拼板工艺流程及基本要求.docx
《拼板工艺流程及基本要求.docx》由会员分享,可在线阅读,更多相关《拼板工艺流程及基本要求.docx(8页珍藏版)》请在冰豆网上搜索。
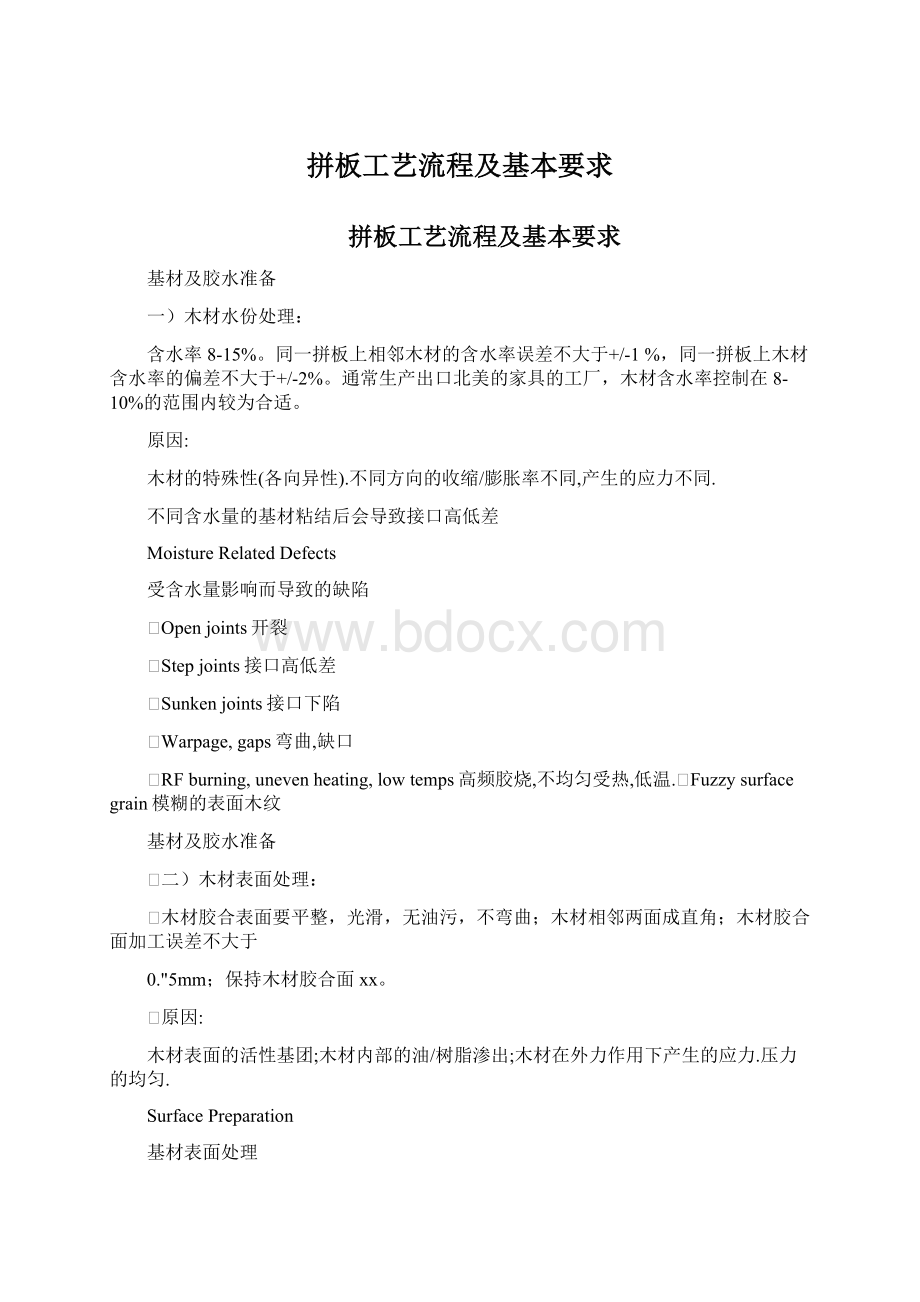
拼板工艺流程及基本要求
拼板工艺流程及基本要求
基材及胶水准备
一)木材水份处理:
含水率8-15%。
同一拼板上相邻木材的含水率误差不大于+/-1%,同一拼板上木材含水率的偏差不大于+/-2%。
通常生产出口北美的家具的工厂,木材含水率控制在8-10%的范围内较为合适。
原因:
木材的特殊性(各向异性).不同方向的收缩/膨胀率不同,产生的应力不同.
不同含水量的基材粘结后会导致接口高低差
MoistureRelatedDefects
受含水量影响而导致的缺陷
lOpenjoints开裂
lStepjoints接口高低差
lSunkenjoints接口下陷
lWarpage,gaps弯曲,缺口
lRFburning,unevenheating,lowtemps高频胶烧,不均匀受热,低温.lFuzzysurfacegrain模糊的表面木纹
基材及胶水准备
l二)木材表面处理:
l木材胶合表面要平整,光滑,无油污,不弯曲;木材相邻两面成直角;木材胶合面加工误差不大于
0."5mm;保持木材胶合面xx。
l原因:
木材表面的活性基团;木材内部的油/树脂渗出;木材在外力作用下产生的应力.压力的均匀.
SurfacePreparation
基材表面处理
lAllsurfacingshouldoccuramax.24hoursaheadofgluing
基材表面处理应在用胶前24小时之内进行.
lEnsurethattoolingissharptoavoidbeatingdownwoodfibers
保持工具锋利以避免毛面.
用50号或更细砂纸,以避免毛面.
lPlaning-Avoidsnipes,unevensurfaces,tear-out,&chatter刨光:
避免表面有洞,不平和表面磨损.
lMoulder-AvoidglazingJointer-Avoidsnipes&tear-out
打腻子:
避免表面太光滑.
lSawing-Avoidsawscratches&snipes
锯切:
避免锯切产生划痕xx.
lOptimumsurfacequalityyieldsintimatesubstratecontact&thinglueline.
最佳质量打饿表面会达到基材紧密相接和胶线细密的效果.
木材表面经加工处理后应尽快用胶.木材本身的大小变化会导致夹合压力不均和接口开裂.
基材及胶水准备
l三)胶水与固化剂的混合:
l胶水与固化剂的混合比100:
15(重量比)。
胶水与固化剂的配比的任何改变都会影响胶合效果,请与胶水供应商保持联系。
胶水与固化剂必须充分搅拌均匀。
通常电动搅拌分钟,人工搅拌2分钟。
l混合好的粘合剂应在其活性期内使用完毕。
通常胶水的活性期为45-60分钟(工作环境温度为25ºC,相对湿度在50-65%时)。
在工作环境温度高于35ºC,同时相对湿度较低时,胶水的活性期将大大缩短。
l原因:
固化剂的量应保证充分且均匀的交联;使用前胶水不应固化.
胶水涂布
l一)胶水涂布量:
l木材胶合面胶水涂布应均匀,胶水涂布量通常为150-300克/平方米,硬木应双面涂胶(每面~150克/平方米),其它木材的胶水涂布量~220-300克/平方米。
通常在合适的压力下胶缝挤出的胶水呈连续小珠滴状时,表示涂布量合适。
胶水涂布的方式通常为手工涂布和机器辊涂。
l根据不同的气候条件,调整胶水的涂布量.在温度高且空气湿度低时,要适当增加涂部量.
胶水涂布
l二)胶合面的陈化时间(通常指木材涂胶后至加压完成时的这段时间):
l通常不大于10分钟。
吸水性能强的木材(通常为软木)其陈化时间要尽可能缩短,一般为4-6分钟;吸水性能弱的木材(如硬木,油性材)其陈化时间要相应延长,一般为6-10分钟;在工作环境温度高于35ºC,同时相对湿度较低时,其陈化时间要相应缩短.
l原因:
水份的挥发,木材的吸收;胶水的流展,对木材的渗透.
压合
l胶合面应保持有足够的压力和足够的时间,且
压力应保持均匀,夹具应间隔8-11英寸,离板材边
缘不超过2-3英寸.建议板宽不超出3英寸
l一)压力:
软木3-8公斤/平方厘米;硬木6-12
公斤/平方厘米。
.
l二)时间:
l~45分钟,工作环境温度大于30ºC时。
l~60分钟,工作环境温度为25-30ºC时。
l~90分钟,工作环境温度为15-25ºC时。
l~150分钟,工作环境温度为10-15ºC时。
l原因:
胶水对木材的渗透,木材的应力,充分接触;胶水的固化程度.
压合
l高密度木材需较长加压时间.
l具有环孔的木材需较长的加压时间.
l含水率低的木材胶水固化速度较快.
l高湿度环境下需较长加压时间.
l低温条件下需较长加压时间.
l增加胶水的开放和闭合时间需较长的加压时间.
l挤出的胶水应沿板边呈均匀的小颗粒状.
l窄木条应放臵在板材中间一达到均匀压力.
养生
l在大多数情况下,拼板卸压后养生时间应不低于24小时。
如工作环境温度较高而空气湿度较低以及拼板在烘房内进行处理时,养生时间可相应缩短。
l原因:
养生不足可能产生的缺陷:
接口高低差;胶缝下陷(明显的胶线);强度不足抵抗外力的影响,端部开裂.
粘好的板材应至少放臵24小时后才能进行表面处理.光滑的表面
需放臵更长时间.热压和高频胶合的板材可较快进行下一步的加工
其它
l要保持包装桶的密封,以防止胶水/固化剂与空气和水份接触,以免胶水/固化剂受到污染和失效.
l胶水应放臵在阴凉通风处,避免阳光直接照射.
拼板质量的影响因素
胶水搅拌均匀性的影响及反映
l主剂与固化剂的配比及搅拌均匀性;
l合适的配比:
100:
15
l固化剂低:
胶水不能充分交联,交联程
l度低,影响胶合性能。
l固化剂高:
胶水活性期短;胶层较硬。
l胶水混合不均匀:
颜色深浅不一,胶水
l胶联程度及固化速度不一致,胶线开裂率高。
胶水活性期的影响及反映:
l胶水的活性期与其使用的工作环境有密切的关系:
温度高且相对湿度低时,胶水的活性期短;反之胶水的活性期则长。
lGW-1505/H-66的适用活性期:
l20-25Cº,55-60%时:
〈60min;
l25-30Cº,55-60%时:
〈45min;
l35-40Cº,55-60%时:
〈30min;
l超过适用活性期的胶水反映为:
发泡,流动性很差,胶水的粘合力明显下降。
继续使用对拼板质量的影响极大:
木破率低,耐水/热性能差,胶线厚且明显。
涂布方法,涂布量及其均匀性的影响及反映
l硬木(如:
红橡,白橡,xx硬xx):
l宜双面涂胶,每面涂布量>150g/m²
l软木特别是吸附性能强的木材:
胶水涂布量在>250g/m²;
l其它木材:
胶水涂布量在220g-280/m²。
l涂胶量不足时:
胶缝无胶水挤出或不能形成xx
l续的泪水状胶滴。
胶层缺胶对拼板质量的影响……
OPENTIME的影响及反映
l硬木(如:
红橡,白橡,xx硬xx)特别是
l吸附性能弱的木材:
6-10min;吸附性能差的木材,需要较长的陈化时间以形成较多的胶钉。
l软木(如杉木,新鲜的松木等)特别是吸附性能强的木材:
4-6min,以免胶水被木材过度吸收。
l过长的陈化时间,会产生过厚的胶线以及造成胶层缺胶(胶水过多地被木材吸收),不能形成足够的胶膜。
木材含水率及其分布的均匀性的影响及反映
l适合的木材含水率为:
7-15%,但以8-12%为最佳。
l同一拼板上木材含水率的差异不大于2%,同一拼板上相邻木条的含水率的差异不大于1%。
l含水率变化过大时:
木材在干燥收缩及吸湿(水)膨胀时产生的应力不同,容易造成木材或胶线开裂,尤其是硬木等应力较大(变形较大)的木材,以及产生板材弯曲和接口高低差等缺陷。
木材表面加工质量的影响及反映
l木材胶合表面要平整,光滑,无油污,不弯曲;木材相邻面成直角;木材胶合面加工误差不大于
0."5mm。
l木材相邻面不成直角或加工误差过大时:
l1)容易造成拼板时压力不均(部分过大压力或部分没有压力),也容易造成木材压匮或部分缺胶而影响拼板质量。
l2)木材内部应力较大,拼板在卸压后在应力的作用下,容易造成胶线开裂。
拼板养生期的影响及反映
l拼板卸压后养生24小时再进行下道工序的加工。
l卸压后拼板的胶合强度呈逐渐上升趋势,在168小时后达到最高;在一般情况下,拼板卸压后养生24小时后胶合强度才能足以抵抗外力(切削,成型及砂光等机械加工)的影响。
l养生时间不足时:
在后续加工处理过程中受外力的作用容易造成胶线开裂及出现接缝下陷。
现象,原因及对策
l一)端部开裂:
l木材含水率过高且不均匀:
l拼板前检查和控制木材含水率(+/-1%)
l端部胶水涂布量不足:
l增加胶水涂布量(220-300g/m2)
l木材加工精度不够(如切削时产生的啃头,刀痕等):
l加工误差应不大于
0."2mm
l压力不足,不均:
l提高压力,并使压力均匀,特别是拼板两端的压力(软木:
3-8kg/cm2;硬木:
6-13kg/cm2)
现象,原因及对策
l二)胶线呈海绵状,胶线厚:
开口及闭口xx时间过长:
减少装配时间。
l压力不够:
增加压力。
l压合时间太短:
增加保压时间。
l三)出现光亮胶线:
l压力不够:
增加压力。
l四)白色胶线(粉化):
l木材,胶水及车间温度太低:
提高温度。
现象,原因及对策
l五)接口高低差:
l木材含水率不均匀:
检查/控制含水率。
l不同切向的板材混杂:
板材木纹应相配。
l六)接头下陷:
l粘合后养生时间不足:
增加养生时间。
l七)板材过度弯翘:
l木材含水率不正确/不均匀:
检查/控制含水率。
l板材宽度过大:
板材宽度不应超过3英寸。
l八)紫色/黑色污点:
l铁污染:
检查及避免铁的来源。