压铸产品缺陷的诊断.docx
《压铸产品缺陷的诊断.docx》由会员分享,可在线阅读,更多相关《压铸产品缺陷的诊断.docx(9页珍藏版)》请在冰豆网上搜索。
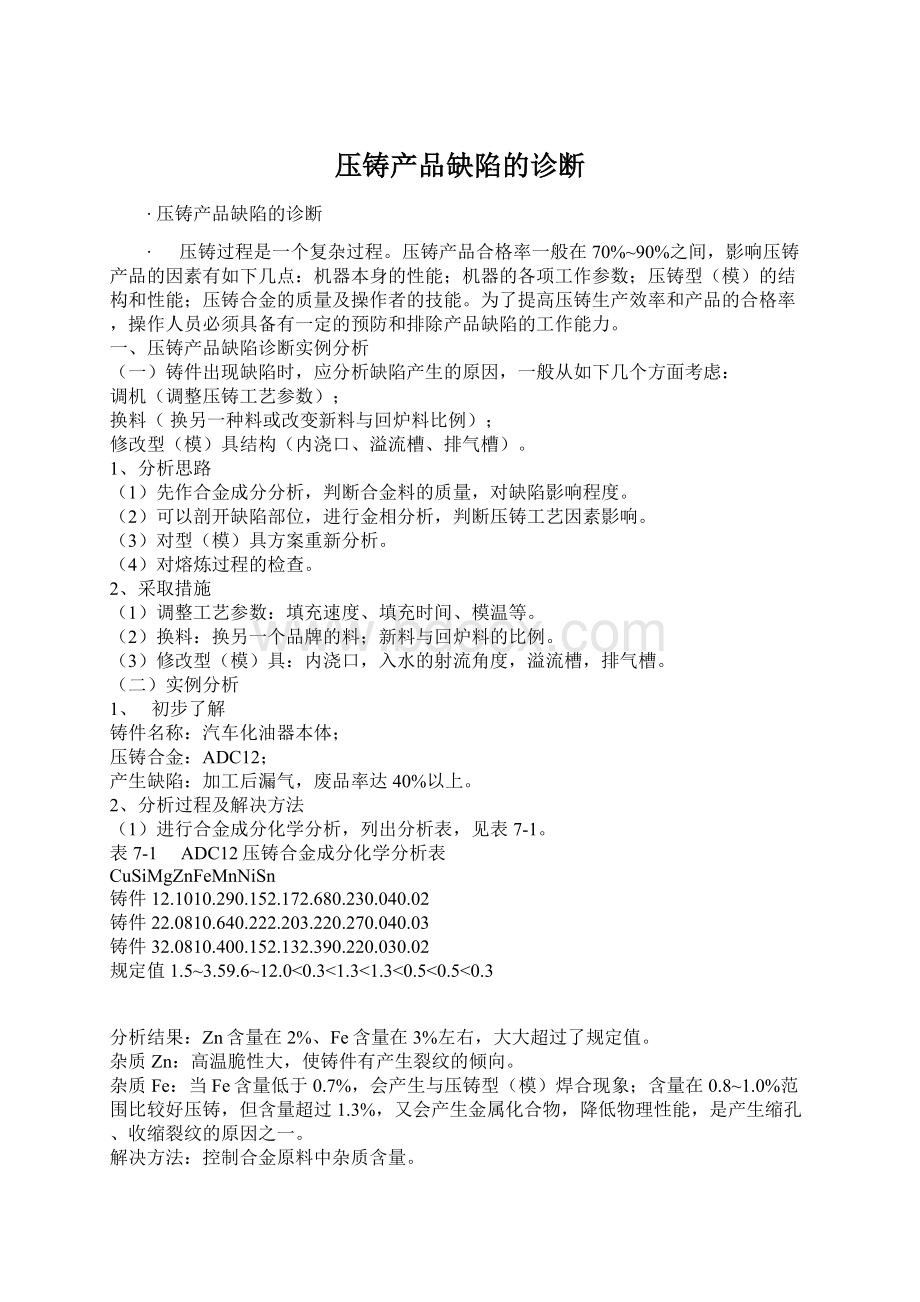
压铸产品缺陷的诊断
∙压铸产品缺陷的诊断
∙ 压铸过程是一个复杂过程。
压铸产品合格率一般在70%~90%之间,影响压铸产品的因素有如下几点:
机器本身的性能;机器的各项工作参数;压铸型(模)的结构和性能;压铸合金的质量及操作者的技能。
为了提高压铸生产效率和产品的合格率,操作人员必须具备有一定的预防和排除产品缺陷的工作能力。
一、压铸产品缺陷诊断实例分析
(一)铸件出现缺陷时,应分析缺陷产生的原因,一般从如下几个方面考虑:
调机(调整压铸工艺参数);
换料( 换另一种料或改变新料与回炉料比例);
修改型(模)具结构(内浇口、溢流槽、排气槽)。
1、分析思路
(1)先作合金成分分析,判断合金料的质量,对缺陷影响程度。
(2)可以剖开缺陷部位,进行金相分析,判断压铸工艺因素影响。
(3)对型(模)具方案重新分析。
(4)对熔炼过程的检查。
2、采取措施
(1)调整工艺参数:
填充速度、填充时间、模温等。
(2)换料:
换另一个品牌的料;新料与回炉料的比例。
(3)修改型(模)具:
内浇口,入水的射流角度,溢流槽,排气槽。
(二)实例分析
1、 初步了解
铸件名称:
汽车化油器本体;
压铸合金:
ADC12;
产生缺陷:
加工后漏气,废品率达40%以上。
2、分析过程及解决方法
(1)进行合金成分化学分析,列出分析表,见表7-1。
表7-1 ADC12压铸合金成分化学分析表
CuSiMgZnFeMnNiSn
铸件12.1010.290.152.172.680.230.040.02
铸件22.0810.640.222.203.220.270.040.03
铸件32.0810.400.152.132.390.220.030.02
规定值1.5~3.59.6~12.0<0.3<1.3<1.3<0.5<0.5<0.3
分析结果:
Zn含量在2%、Fe含量在3%左右,大大超过了规定值。
杂质Zn:
高温脆性大,使铸件有产生裂纹的倾向。
杂质Fe:
当Fe含量低于0.7%,会产生与压铸型(模)焊合现象;含量在0.8~1.0%范围比较好压铸,但含量超过1.3%,又会产生金属化合物,降低物理性能,是产生缩孔、收缩裂纹的原因之一。
解决方法:
控制合金原料中杂质含量。
(2)金相分析
分析结果:
发现基本组织晶体粗大,有铁-锌-硅的化合物,有气孔、缩孔。
解决方法:
合金成分中杂质含量控制,压铸工艺调整。
(3)对合金熔炼过程采取措施
估计金属液中含气量较高,在保温炉内,采用氩气脱气处理15分钟。
(4)对型(模)具方案重新分析
1) 排气不够充分时,可加大排气槽尺寸,加多排气气口。
2) 利用激冷排气块或采用真空压铸法,加大型腔内的空气排放量。
3) 在产生缩孔部位(漏气)增设辅助浇口,以提高铸造压力的传递效果。
(5)压铸工艺参数
1) 合理设置慢速压射和快速压射开始点,可以减少金属液包卷气体现象。
修改原来工
艺中快速切换的位置,快速切换位置选择在铸件两侧壁厚部位(产生缩孔处)之前。
2) 浇口速度提高到40~50 m/s。
3) 降低金属液浇注温度:
680℃~690℃ 降 670℃ ± 5℃
4) 降低模温:
200℃ 降 160℃
3、效果:
加工后废品率降低到5%以下。
二、压铸产品缺陷类型、产生原因及解决措施
(一) 流痕和花纹
外观检查:
铸件表面上有与金属液流动方向一致的条纹,有明显可见的与金属基体颜色不
一样无方向性的纹路,无发展趋势,如图7-18所示。
图7-18 流痕
1、 流痕产生的原因有如下几点,查明原因后应及时纠正。
(1)模温过低。
(2)浇道设计不良,内浇口位置不良。
(3)料温过低。
(4)填充速度低,填充时间短。
(5)浇注系统不合理。
(6)排气不良。
(7)喷雾不合理。
2、花纹产生的原因是型腔内涂料喷涂过多或涂料质量较差,解决和防止的方法如下:
(1)调整内浇道截面积或位置。
(2)提高模温。
(3)调整内浇道速度及压力。
(4)适当的选用涂料及调整用量。
(二) 网状毛翅(龟裂纹)
外观检查:
压铸件表面上有网状发丝一样凸起或凹陷的痕迹,随压铸次数增加而不断扩大和延伸,如图7-19所示。
图7-19 网状毛翅
产生原因如下:
1、 压铸型(模)型腔表面有裂纹;
2、 压铸型(模)预热不均匀。
解决和防止的方法为:
1、 压铸型(模)要定期或压铸一定次数后,应作退火处理、消除型腔内应力。
2、 如果型腔表面已出现龟裂纹,应打磨成型表面,去掉裂纹层。
3、 型(模)具预热要均匀。
(三) 冷隔
外观检查:
压铸件表面有明显的、不规则的、下陷线性型纹路(有穿透与不穿透两种)形状细小而狭长,有时交接边缘光滑,在外力作用下有断开的可能,如图7-20所示。
图7-20 冷隔
产生原因如下:
1、 两股金属流相互对接,但未完全熔合而又无夹杂存在其间,两股金属结合力又很薄弱;
2、 浇注温度或压铸型(模)温度偏低;
3、 浇道位置不对或流路过长;
4、 填充速度低。
解决和防止的方法为:
1、 适当提高浇注温度;
2、 提高压射比压缩短填充时间,提高压射速度。
3、 改善排气、填充条件。
(四) 缩陷(凹痕)
外观检查:
在压铸件厚大部分的表面上有平滑的凹痕(状如盘碟)。
产生原因如下:
1、 由收缩引起
(1)压铸件设计不当壁厚差太大;
(2)浇道位置不当;
(3)压射比压低,保压时间短;
(4)压铸型(模)局部温度过高。
2、冷却系统设计不合理;
3、开型(模)过早;
4、浇注温度过高。
解决和防止的方法为:
1、 壁厚应均匀;
2、 厚薄过渡要缓和;
3、 正确选择合金液导入位置及增加内浇道截面积;
4、 增加压射压力,延长保压时间;
5、 适当降低浇注温度及压铸型(模)温度;
6、 对局部高温要局部冷却;
7、 改善排溢条件
(五) 印痕
外观检查:
铸件表面与压铸型(模)型腔表面接触所留下的痕迹或铸件表面上出现阶梯痕迹,如图7-21所示。
图7-21 印痕
产生原因如下:
1、由顶出元件引起
(1)顶杆端面被磨损;
(2)顶杆调整长短不一致;
(3)压铸型(模)型腔拼接部分和其他部分配合不好;
2、由拼接或活动部分引起
(1)镶拼部分松动;
(2)活动部分松动或磨损;
(3)铸件的侧壁表面,由动、定模互相穿插的镶件所形成。
解决和防止的方法为:
1、 顶杆长短要调整到适当位置;
2、 紧固镶块或其他活动部分
3、 设计时消除尖角,配合间隙调整适合;
4、 改善铸件结构使压铸型(模)消除穿插的镶嵌形式,改进压铸型(模)结构;
(六)粘附物痕迹
外观检查:
小片状及金属或非金属与金属的基体部分熔接,在外力的作用下剥落小片状物,
剥落后的铸件表面有的发亮、有的为暗灰色。
产生的原因如下:
1、 在压铸型(模)型腔表面有金属或非金属残留物;
2、 浇注时先带进杂质附在型腔表面上。
解决和防止的方法为:
1、 在压铸前对型腔压室及浇注系统要清理干净,去除金属或非金属粘附物;
2、 对浇注的合金也要清理干净;
3、 选择合适的涂料,涂层要均匀。
(七)分层(夹皮及剥落)
外观检查或破坏检查:
在铸件局部有金属的明显层次。
产生的原因如下:
1、 型(模)具刚性不够在金属液填充过程中,模板产生抖动;
2、 在压射过程中冲头出现爬行现象;
3、 浇道系统设计不当。
解决和防止的方法为:
1、 加强型(模)具刚度,紧固型(模)具部件,使之稳定;
2、 调整压射冲头与压室的配合,消除爬行现象;
3、 合理设计内浇道。
(八)摩擦烧蚀
外观检查:
压铸件表面在某些位置上产生粗糙面。
产生的原因如下:
1、由压铸型(模)引起的内浇道的位置方向和形状不当;
2、由铸造条件引起的内浇道处金属液冲刷剧烈部位的冷却不够。
解决和防止的方法为:
1、改善内浇道的位置和方向的不善内浇当之处;
2、改善冷却条件,特别是改善金属液冲刷剧烈部位;
3、对烧蚀部分增加涂料;
4、调整合金液的流速,使其不产生气穴
5、消除型(模)具上的合金粘附物。
(九)冲蚀
外观检查:
压铸件局部位置有麻点或凸纹。
产生的原因如下:
1、 内浇道位置设置不当;
2、 冷却条件不好。
解决和防止的方法为:
1、 内浇道的厚度要恰当;
2、 修改内浇道的位置、方向和设置方法;
3、 对被冲蚀部位要加强冷却。
(十)裂纹
外观检查:
将铸件放在碱性溶液中,裂纹处呈暗灰色。
金属基体的破坏与裂开呈直线或波浪线形,纹路狭小而长,在外力作用下有发展趋势。
1、铝合金铸件裂纹,如图7-22所示:
图7-22 铝合金铸件裂纹
产生的原因:
(1)合金中铁含量过高或硅含量过低;合金中有害杂质的含量过高,降低了合金的可塑性;铝硅合金、铝硅铜合金含锌或含铜量过高;铝镁合金中含镁量过多;
(2)留模时间过短,保压时间短;铸件壁厚有剧烈变化之处;
(3)局部包紧力过大,顶出时受力不均。
解决和防止的方法:
(1)正确控制合金成分,在某些情况下:
可在合金中加纯铝锭以降低合金中含镁量;或在合金中加铝硅中间合金以提高硅含量。
(2)提高型(模)具温度;改变铸件结构,调整抽芯机构或使推杆受力均力;
(3)加大拔模斜度,局部使用强力脱模剂;
(4)增加留模时间、增加保压时间。
2、镁合金铸件裂纹,如图7-23所示:
图7-23 镁合金铸件裂纹
产生的原因:
合金中铝硅含量高;型(模)具温度低;铸件壁厚薄变化剧烈;顶出和抽芯时受力不均匀。
解决和防止的方法:
合金中加纯镁以降低铝硅含量;型(模)具温度要控制在要求的范围内;改进铸件结构,消除厚薄变化较大的截面;调整好型芯和推杆,使之受力均衡。
3、铜合金铸件裂纹
产生的原因:
(1)黄铜中锌的含量过高(冷裂)或过低(热裂);硅黄铜中硅的含量高;
(2)开型(模)时间晚,特别是型芯多的铸件。
解决和防止的方法:
(1)保证合金的化学成分,合金元素取其下限:
硅黄铜在配制时,硅和锌的含量不能同时取上限;
(2)提高型(模)具温度;适当控制调整开型(模)时间。
(十一)欠铸及轮廓不清晰
外观检查:
金属液充满型腔,铸件表面有不规则的孔洞、凹陷或棱角不齐,表面形状呈自然液流或液面相似,如图7-24所示:
图7-24 欠铸及轮廓不清晰
产生的原因如下:
1、 内浇道宽度不够或压铸型(模)排气不良;
2、 合金流动性差;
3、 浇注温度低或压铸型(模)温度低,压射速度低;
4、 压射比压不足;
5、 压铸型(模)腔边角尺寸不合理、不易填充;
6、 喷雾不合理。
解决和防止的方法:
1、 改进内浇道,改进排气条件,适当提高压铸型(模)温度和浇注温度;
2、 提高压射比压和压射速度;
3、 注意喷雾的位置。
(十二)变形
外观检查或测量和划线:
铸件翘(弯)曲、超出图样尺寸公差要求。
产生的原因如下:
1、 铸件结构不合理,各部收缩不均匀;
2、 留模时间太短;
3、 顶出过程铸件偏斜;
4、 铸件刚性不够;
5、 堆放不合理或去除浇道方法不当。
解决和防止的方法:
1、 改进铸件结构、使壁厚均匀;
2、 不要堆叠存放,特别是大且面薄的铸件;
3、 时效或退火时不要堆叠入炉;
4、 必要时可以进行整形。
(十三)飞翅
外观检查:
铸件分型面处或活动部分突出过多的金属薄片,如图7-25所示。
图7-25 飞翅
产生的原因如下:
1、 压射前机器的调整、操作不合适;
2、 压铸型(模)及滑块损坏,闭锁元件失效;
3、 镶块及滑块磨损;
4、 压铸型(模)强度不够造成变形;
5、 分型面上杂物未清理干净;
6、 锁型(模)力小。
解决和防止的方法:
1、 检查合型(模)力及增压情况;
2、 调整增压机构使压射增压峰值降低;
3、 检查压铸型(模)强度和闭锁元件;
4、 检查压铸型(模)损坏情况并修理;
5、 清理分型面防止有杂物;
6、 增大锁型(模)力。
(十四)夹渣(渣孔)
外观检查或探伤及金相检查:
铸件上有不规则的明或暗孔,孔内常被熔渣充塞。
金相检查时,在低倍显微镜下呈暗黑色;在高倍显微镜下亮而无色。
产生的原因如下:
1、金属中有夹渣或型腔中有非金属残留物,在压射前未被清除;
2、金属液表面上的熔渣未清除;
3、将熔渣及金属同时浇注到压室。
解决和防止的方法:
1、 仔细去除金属表面的熔渣;
2、 遵守金属熔炼舀取工艺规程。
(十五)硬点
机械加工过程中或加工后外观检查或金相检查:
铸件上有硬度高于金属基体的细小质点或块状物,使刀具磨损严重、加工后常常显示出不同亮度。
1、非金属硬点产生的原因及解决和防止的方法
(1)由于混入了合金液表面的氧化物而产生非金属硬点,解决和防止的方法为:
铸造时不要把合金液表面的氧化物舀入勺内;清除铸铁坩埚表面的氧化物后,再涂上
涂料;消除勺子等工具上的氧化物;使用与铝不产生反应的涂料;
(2)由于混入了合金液与涂料的反应生成物,而产生非金属硬点。
应该用与铝合金不发
生反应的涂料。
(3)金属液中产生了复合化合物,如Al 、Mn 、Fe 、Si组成的化合物。
应注意:
在铝
合金中含有Mn 、Fe等元素时应勿使偏析;并保持清洁;用干燥的去气剂除气,但铝合金含镁时要注意补偿。
(4)金属液中铝硅合金含Si高;铝合金在半液态下浇注;硅游离存在,或者铝硅合金Si
高于11.6%且Cu 、Fe含量亦高。
解决和防止的方法为:
铝合金含Cu 、Fe多时,应使含Si量降到10.5%以下;适当的提高浇注温度,以避免使Si析出。
(5)由于金属锭不纯或粘附了油污,熔炼工具不干净而夹带异物,而产生非金属硬点。
应
注意检验金属锭的纯度,加强原料,回收料的清理,不得粘上油、砂、尘土等异物;注意清理干净坩埚,熔炼工具上面的铁锈及氧化物。
3、 金属硬点产生的原因及解决和防止的方法:
(1)、混入了未溶解的硅元素原料而产生金属性硬点。
解决和防止的方法为:
1)熔炼硅合金时,不要使用硅元素粉末;
2)调整合金成分时,不要直接加入硅元素,必须采取中间合金;
3)熔炼温度要高,时间要长,使硅充分溶解。
(2)、混合了促进初生硅结晶生长的原料而产生金属性硬点,生产中应注意:
缩小铸造温度波动范围,使之经常保持熔融状态;加冷料时要防止合金锭块使合金凝固;尽量减少促进粗晶硅易于生长的成分。
(3)、混入了生成金属件化合物结晶物质而产生金属性硬点,生产中应注意:
1)减少温度波动范围,不使合金液的温度过高或过低;
2)控制合金成分杂质含量的同时,注意勿使增加杂质;
3)对能产生金属间化合物的材料要在高温下熔炼、为防止杂质增加,应一点一点的少量加入。
4、 偏析性硬点产生的原因是由于急冷,使容易偏析的成分析出成为硬点,在压射时应注意:
合金液浇入压室后,应立即压射填充;尽可能不含有Ca 、Mg 、Na等易引起急冷效应的合金成分。
Ca应控制在0.05%以下。
(十六)脆性
外观检查或金相检查:
合金晶粒粗大或极小,使铸件易断裂或碰碎。
产生的原因如下:
1、 合金过热太大或保温时间过长;
2、 激烈过冷,结晶过细;
3、 铝合金含有锌铁等杂质太多;
4、 铝合金中含铜超出规定范围。
解决和防止的方法为:
1、 合金不宜过热;
2、 提高型(模)具温度,降低浇注温度;
3、 严格控制合金成分在允许的范围内。
(十七)渗漏
通过试压试验,压铸件漏水或渗水。
产生的原因如下:
1、 压力不足;
2、 浇注系统设计不合理或铸件结构不合理;
3、 合金选择不当;
4、 排气不良。
解决和防止的方法为:
1、 提高压射比压;
2、 尽量避免后加工;
3、 改进浇注系统和排气系统;
4、 选用良好合金。
(十八)气孔
解剖后外观检查或探伤检查:
气孔具有光滑的表面,形状呈圆形或椭圆形。
产生的原因如下:
1、 一速距离过短,一速过快,在料液内卷气;
2、 横浇道设计不合理;
3、 内浇口位置不合理;
4、 分型面选择不当;
5、 排气不良;
6、 料液含气量高;
7、 料液杂质含量高;
8、 喷舞量和位置不当;
9、 横温过高;
10、料温过高;
11、冷却系统设计不合理;
12、合型(模)过早。
解决和防止的方法为:
1、 使用干燥而干净的添加剂,不使合金过热并很好排气,改善金属导入方向;
2、 降低压射速度;
3、 在保证填充良好的情况下,尽可能增大内浇道截面积;
4、 排气槽部位要设置合理并有足够的排气能力。
(十九)气泡
解剖后外观检查或探伤检查:
铸件接近表面有气体集聚,有时看到铸件表面鼓泡。
产生的原因如下:
1、 由卷入气体引起:
型腔气体没有排出,被包在铸件中;涂料产生的气体卷入铸件中;
2、 由合金气体引起:
合金内吸有较多气体,凝固时析出留在铸件内。
解决和防止的方法为:
1、善内浇道、溢流槽排气道的大小和位置;改善填充时间和内浇道处流速;提高压射压力;在气孔发生处设型芯;尽量少用涂料;
2、清除合金液中的气体和氧化物;炉料要管理好,避免被尘土油类污染。
(二十)缩孔缩松
解剖后外观检查或探伤检查:
缩孔表面呈暗色并不光滑,形状不规则的孔洞、大而集中的为缩孔,小而分散的为缩松。
产生的原因如下:
1、缩孔是压铸件在冷凝过程中,内部补偿不足而造成的孔穴,由于浇注温度过高、压射比压低、铸件在结构上有金属积聚的部位和截面变化剧烈,内浇道较小而产生;
2、型(模)具温度过高;
3、保压时间短。
解决和防止的方法:
1、改变铸件结构消除金属积聚及截面变化大处;
2、在可能条件下降低浇注温度;
3、提高压射比压;
4、适当改善浇注系统,使压力更好地传递;
5、降低模温;
6、提高保压时间。
(二十一)粘模拉伤
外观检查:
压铸合金与型壁粘连而产生拉伤痕迹,在严重的部位会被撕破。
产生的原因如下:
1、合金浇注温度高;
2、型(模)具温度太高;
3、涂料使用不足或不正确;
4、型(模)具某些部位表面粗糙;拔模斜度制作过小或倒拔。
5、浇道系统不正确使用合金正面冲击型壁或型芯;
6、型(模)具材料使用不当或热处理工艺不正确,硬度不足。
7、铝合金含铁量太少(<0.6%)ZCuZn40Pb2含锌低或有偏析;
8、填充速度太高。
解决和防止的方法为:
1、 降低浇注温度;
2、 型(模)具温度控制在工艺范围内;
3、 消除型腔粗糙的表面;
4、 检查涂料品种或用量是否适当;
5、 调整内浇道防止金属液正面冲击;
6、 校对合金成分、使铝合金含铁(Fe)量在要求的范围内;
7、 检查型(模)具材料及热处理和硬度是否合理;
8、 适当降低填充速度。