公差分配原则.docx
《公差分配原则.docx》由会员分享,可在线阅读,更多相关《公差分配原则.docx(13页珍藏版)》请在冰豆网上搜索。
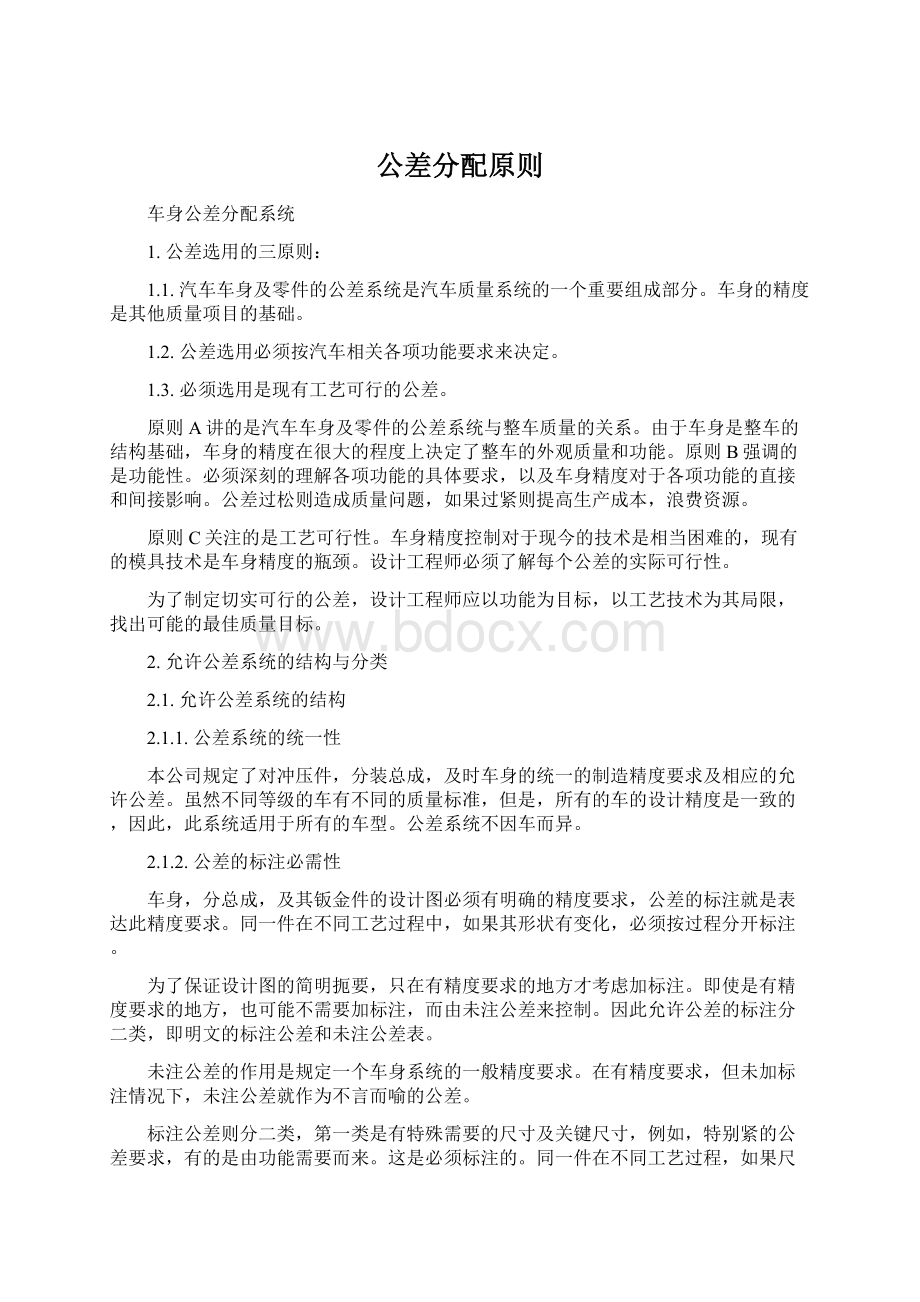
公差分配原则
车身公差分配系统
1.公差选用的三原则:
1.1.汽车车身及零件的公差系统是汽车质量系统的一个重要组成部分。
车身的精度是其他质量项目的基础。
1.2.公差选用必须按汽车相关各项功能要求来决定。
1.3.必须选用是现有工艺可行的公差。
原则A讲的是汽车车身及零件的公差系统与整车质量的关系。
由于车身是整车的结构基础,车身的精度在很大的程度上决定了整车的外观质量和功能。
原则B强调的是功能性。
必须深刻的理解各项功能的具体要求,以及车身精度对于各项功能的直接和间接影响。
公差过松则造成质量问题,如果过紧则提高生产成本,浪费资源。
原则C关注的是工艺可行性。
车身精度控制对于现今的技术是相当困难的,现有的模具技术是车身精度的瓶颈。
设计工程师必须了解每个公差的实际可行性。
为了制定切实可行的公差,设计工程师应以功能为目标,以工艺技术为其局限,找出可能的最佳质量目标。
2.允许公差系统的结构与分类
2.1.允许公差系统的结构
2.1.1.公差系统的统一性
本公司规定了对冲压件,分装总成,及时车身的统一的制造精度要求及相应的允许公差。
虽然不同等级的车有不同的质量标准,但是,所有的车的设计精度是一致的,因此,此系统适用于所有的车型。
公差系统不因车而异。
2.1.2.公差的标注必需性
车身,分总成,及其钣金件的设计图必须有明确的精度要求,公差的标注就是表达此精度要求。
同一件在不同工艺过程中,如果其形状有变化,必须按过程分开标注。
为了保证设计图的简明扼要,只在有精度要求的地方才考虑加标注。
即使是有精度要求的地方,也可能不需要加标注,而由未注公差来控制。
因此允许公差的标注分二类,即明文的标注公差和未注公差表。
未注公差的作用是规定一个车身系统的一般精度要求。
在有精度要求,但未加标注情况下,未注公差就作为不言而喻的公差。
标注公差则分二类,第一类是有特殊需要的尺寸及关键尺寸,例如,特别紧的公差要求,有的是由功能需要而来。
这是必须标注的。
同一件在不同工艺过程,如果尺寸有变化,必须按过程分开标注。
第二类是可标注可不标注的,按未注公差亦无不可,但是标注了会使图简单易读。
这由设计者按具体情况而定。
2.1.3相对公差和绝对公差
绝对公差是那些以整车坐标系统(WorldCoordinateSystem)或以零件坐标系统为基础定义的误差,在CAD系统中,几何特征,通常是点,线,和面,都以此类坐标系统为基础而定义,简明扼要,极为方便。
绝对公差是以此定义为基础而建立的误差系统,因此也简单明了。
然而,此类公差,往往带入了没有必要的精度要求。
相对公差则包括两个或两个以上的点,线,和面,互相之间的关系。
此关系通常是距离,也可以是角度。
例如喇叭在门内板上的安装孔。
其互相之间的距离要控制,以利于安装,相对公差要标明。
然而喇叭与整车的关系则不关键,就让未注公差来管制。
例证请看附录1。
从广义的角度看,所有的距离(长度)和角度上的公差都是相对公差,因此,孔径公差是相对公差。
投影到某一平面的长度和角度公差也是相对公差。
门与门框的配合公差亦是相对公差。
对称公差也是一种相对公差,无论是尺寸(长度或面积),还是角度,或是位置。
使用相对公差能达到绝大多数功能方面的要求。
将其以绝对公差来表达,势必增加工艺难度,从而提高成本。
因此,尽可能使用相对公差和避免使用绝对公差有其经济意义。
2.2.冲压件的分类与不同状态
冲压件按其功能分为三类,A类是外表面件,其要求最高,其次是B类,主要是结构件。
最后是C类,例如支架之类。
冲压件在安装过程中,随着状态的变化,(单件状态,分总成状态,车身总成状态)误差逐步增加。
下图表达了这个变化。
图1冲压件的分类与不同状态
2.3.面和边缘的分类
面分为外观面,结合面,和一般面。
外观面只有一种级别,即A级。
结合面和一般面分二级,即B级和C级,没有A级。
钣金件的边分二级,即B级和C级,没有A级。
一个件可以有不同级面和边组成。
例如,侧围外板,是B级件,但是其四分板和门框是A级面。
其A柱和B柱是B级面,但是A柱和B柱上的装配面是A级面。
由此可见,执行者的难度在于如何确定面和边的等级。
设计人员必须按功能和工艺的要求来定。
设计人员可以参考所附的钣金件分类例证。
(附录2:
A21分类)
表1是以上几个方面的总结,也是图1的细化。
表1是以上几个方面的总结,也是图1的细化。
3.冲压件,分总成及白车身的允许公差
3.1.冲压件的未注允许公差表
一般位置精度:
(A类件:
±0.5,B类件:
±1.0,C类件:
±1.5)
一般孔中心位置精度:
±0.5
直径轮廓:
(塞规测量)+0.5,-0.0;(最大值/最小值之间的差值,游标卡尺测量)0.15
孔距(孔与孔):
±0.5
工具孔
直径:
+0.2,-0.0
基准到基准:
±0.2
阶梯(搭接)
深度(高度差):
+0.3,-0.0
位置精度:
±1.0
配合面精度:
(B类面:
±0.7,C类面:
±1.0)
翻边宽度:
+1.0,-0.5
一般曲率半径:
±0.5
角度:
±2度
安装孔
直径轮廓(塞规测量):
±0.5
孔距(孔与孔,塑料件装配用):
±0.5
孔距(孔与孔,金属件装配用):
±0.3
一致性
同一批中的五个样品的所有的检点的六个标准值不得超过±1.0毫米。
其平均值的移动较之前一批不得大于±0.3毫米。
对称性
左右手对称件的所有的尺寸差值应在±0.5毫米范围内,所有的位置差应在±0.75毫米内。
3.2.分总成的未注允许公差表
一般位置精度:
(A类件:
±0.7,B类件:
±1.5,C类件:
±2.0)
一般孔中心位置精度:
±0.7
直径轮廓:
(塞规测量)+0.5,-0.0;(最大值/最小值之间的差值,游标卡尺测量)0.15
孔距(孔与孔):
±0.7
工具孔
直径:
+0.2,-0.0
基准到基准:
±0.3
基准孔位置:
±0.5
阶梯(搭接)
深度(高度差):
+0.3,-0.0
位置精度:
±1.5
配合面精度:
(B类面)±1.0;(C类面)±1.5
翻边宽度:
+1.0,-0.5
一般曲率半径:
±0.5
角度:
±2度
安装孔
直径轮廓(塞规测量):
±0.5
孔距(孔与孔,塑料件装配用):
±0.5
孔距(孔与孔,金属件装配用):
±0.3
一致性
同一批中的五个样品的所有的检点的六个标准值不得超过±1.5毫米。
其平均值的移动较之前一批不得大于±0.5毫米。
对称性
左右手对称件的所有的尺寸差值应在±0.75毫米范围内,所有的位置差应在±1.5毫米内。
3.3.整车的允许公差
根据图1,测量点的公差按照其所在面而定。
如果是A面公差是±1.0毫米,如是B面,公差为±2.0毫米,C面上的点则是±2.0毫米。
B面与C面没有差别了。
这是因为B件大都为结构件,与其他件关系密切,也就是被制约。
相对而言,C件比较自由,由其他件传递过来的误差要少一些。
两者就变得很接近了。
通常,如果测量点位于夹具的控制点上,其公差可以更紧一些。
因为,车身按由外向内的装配方式,误差被推往车内,外面的误差较之车内误差要小一些。
这和实际情况相一致。
3.4.工艺装配缝的允许公差
装配缝的允许公差是建立在装配面公差的基础上的。
因此,其公差可以由装配面的公差用统计学方法推算。
实际应用时,其顺序则相反,是由装配缝的要求来定装配面的级别。
例如,粘接缝要求相对高,两装配面都应是B级。
缝最宽处应小于1.5毫米。
点焊枪有压合作用,装配缝的允许公差可略为宽松一点。
其中,对头接相对要求紧一点,搭接则相对松一些。
具体地说,假如两边都是10毫米的翻边,装配缝最宽处应小于2.0毫米。
搭接缝应小于3.0毫米。
如果一边是翻边,另一边不是翻边,装配缝最宽处应小于2.5毫米
3.5.允许公差标注
一般公差
标准车身和手工提样的允许公差标准车身是由标准白车身及与其相配的门和盖组合而成。
这是样车过程后期的定型车。
数模将根据此车来改动和定型,内外饰也将以此为根据来改动。
在本规范2.1款中,本公司规定了不同等级的车有相同的设计精度,但是不同等级的车有不同的试制精度。
等级高的车,较之等级低的车,其试制精度要求会相应的高。
为了实现高精度,其模具及冲压件的精度也会相应的高。
一旦达到其试制精度,模具的改动就停止了。
如果功能性建造的认可通过,数模的改动就开始了。
显然,等级高的车,其数模改动会相对地少。
4.1标准车身的允许公差(试制精度)
4.1.1I级
95%的测点应在±1.5毫米以内;其中95%的焊装控制点。
应在±1.0毫米以内。
门/盖与框之间的缝,寛误差±0.5毫米,寛均度0.75毫米/300毫米,平度±0.5毫米。
4.1.2II级95%的测点应在±2.0毫米以内;其中95%的焊装控制点。
应在±1.25毫米以内。
门/盖与框之间的缝,寛误差±0.75毫米,寛均度1.0毫米/300毫米,平度±0.75毫米。
4.1.3III级
95%的测点应在±2.5毫米以内
其中95%的焊装控制点。
应在±1.5毫米以内。
门/盖与框之间的缝,寛误差±1.0毫米,寛均度1.5毫米/300毫米,平度±1.0毫米。
4.2手工提样的允许公差
在一般情况下,标准车身是由手工提样的钣金件装配的,而手工提样的钣金件的制作时,拉伸模已经完成调试或基本完成调试,打孔及修边模尚未完成。
因此,形状误差应该与全模提样相当。
但是,因为基准孔不是冲压模制作的,测量的形状误差也可能略微偏高。
如果采用数控激光切割机,手工提样的钣金件的误差与全模提样的误差应当相当接近。
4.生产车身的允许公差
经过功能性建造的认可后,数模以及设计的目标值应按测量值的中值做响应的修改。
修改后一年,车身的质量应达到:
以一百辆为单元:
95%的测点应在±1.5毫米以内。
所有的相对精度应在±1.0毫米以内。
6.工艺空间的作用
设计工艺空间的首要目的是为防止钣金件之间的干涉。
换而言之,工艺空间可以用来吸收钣金件尺寸误差。
因此,工艺空间的功能和滑动平面理论相似。
7.工艺空间的分类
7.1.钣金件之间的装配关系的分类
钣金件之间的装配关系主要可以分为对接(buckjoint)和叠接(lapjoint),如图1和图2所示。
对接对于尺寸要求高,模具成本和制造成本都会相对高。
叠接则恰好相反,会提供一个误差的消除面,即所谓的滑动平面。
车身设计人员应尽量多采用滑动平面以提高工艺性。
但是,许多情况下必须采用对接时为了减少干涉的可能性,就需要采用工艺空间。
7.2.对接的工艺缝
在对接的情况下,钣金件的误差值会叠加。
当钣金件被定位情况下,装配面之间的干涉就可能发生,冲压件有可能不能放入夹具。
即使放下了,焊接后的反弹和尺寸误差也难避免。
因此工艺缝就有必要。
一个典型例子是底板和侧围之间的工艺缝,如图三和图四所示。
另外类似的例子就是横梁和防火墙。
(请查阅附录1)
图3车身底板与侧围之间的工艺缝
图4车身底板与侧围装配面
7.3.嵌入接的工艺缝
如图5所表示,嵌入接是两个U型截面的冲压件的嵌入接合。
工艺缝宽通常定为0.5毫米
图5U型截面件的嵌入接合。
7.4.台阶搭接的工艺间隙
如图六所示,台阶搭接应有1毫米的工艺间隙,以防干涉的发生。
图6搭接面件的接合
7.5.压边的工艺空间
如图七所示,压边的工艺空间是为了给内板在外板里移动的自由。
图7压边的工艺空间。
8.工艺空间的允许公差和尺寸
与表面缝不同,工艺空间,包括工艺缝和工艺间隙,本身并不设定和标注公差,而是由形成此空间的实体的面或边的公差所决定。
例如,工艺缝的允许公差是建立在两装配面公差的基础上的。
因此,缝的公差可以由装配面的公差用统计学方法估算。
估算的工艺空间允许公差通常会是范围的绝对值大于工艺空间的名义值。
例如,0.7±1.5。
这表明工艺空间可能是负值,换而言之,干涉可能发生。
设计人员应考虑对接区域的软硬状态。
如果硬度高,应考虑适当加大工艺空间。
但过大的工艺空间会增加车身尺寸误差的可能性。
工艺空间的尺寸考虑的基础是几个方面:
第一是允许公差的尺寸,第二则是其工艺性。
以搭接面为例,假如工艺空间设定较大,叠加的边也必须加宽。
9.工艺空间对于车身尺寸的影响和对策
工艺空间的作用是减少干涉从而减少车身尺寸误差。
但是工艺空间本身可能会引人新的误差。
为了防止这一点,设计师应考虑应有措施。
如图八所示,如能设定滑动平面,先焊滑动平面,将两个件的距离固定下来,工艺缝焊接会由局部变形来完成,(如图九所示)从而不影响车身尺寸。
图8梁之间的接合
图9工艺缝的局部变形。
10.工艺空间的标注
工艺空间的设定在三维数模即应标明。
为了让出空间,必需选定被缩小的零件和响应的尺寸。
装配图应明确标注工艺空间的尺寸,伴随以“工艺缝”字样,其公差则不标。
附录1工艺空间例证
附录1-图1车身底板与侧围之间的工艺缝
附录1-图2车身底板与侧围之间的工艺缝的位置
附录1-图3横梁和纵梁之间的工艺缝的位置