向丰田学习管理生产运营篇修改讲解.docx
《向丰田学习管理生产运营篇修改讲解.docx》由会员分享,可在线阅读,更多相关《向丰田学习管理生产运营篇修改讲解.docx(49页珍藏版)》请在冰豆网上搜索。
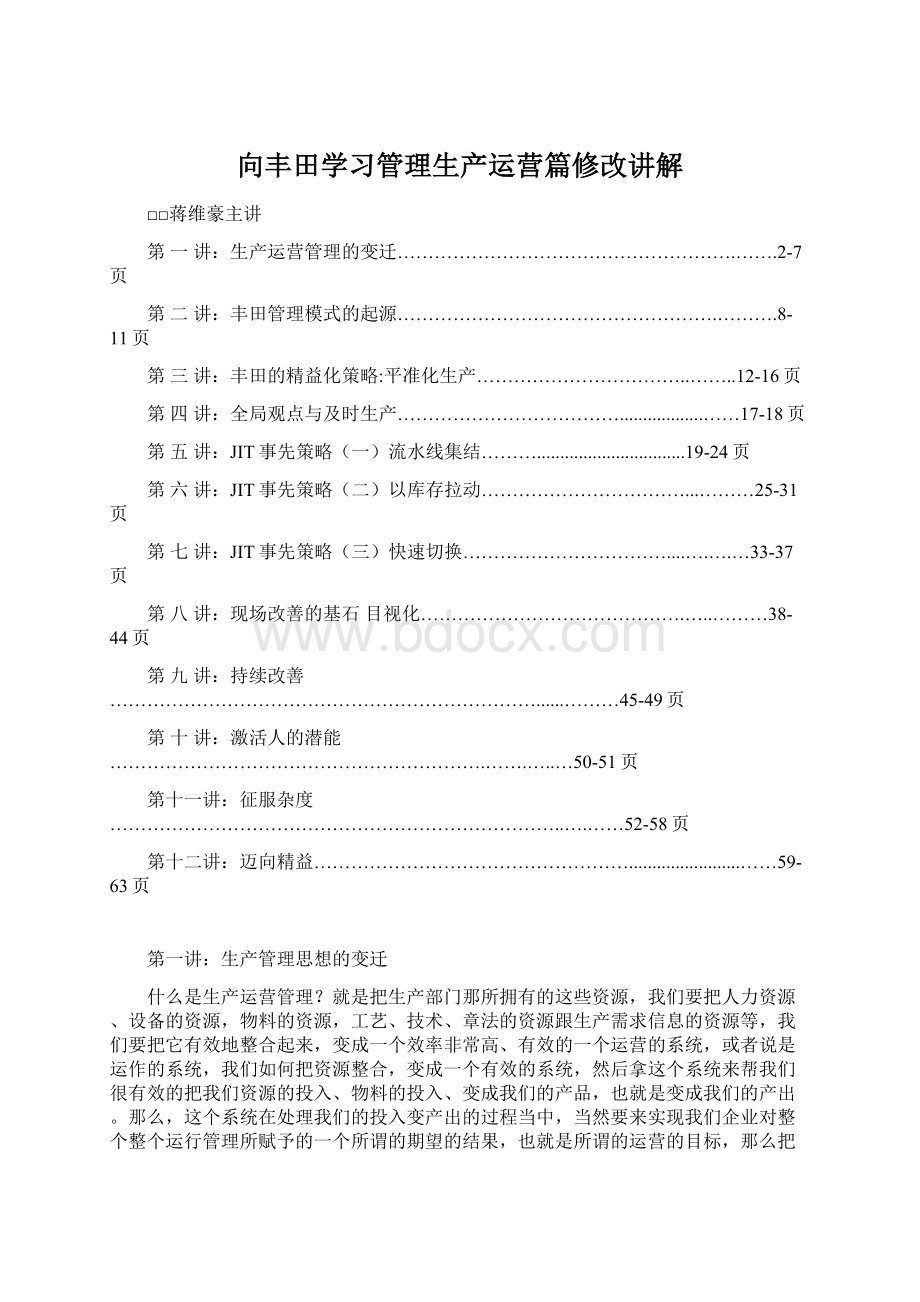
向丰田学习管理生产运营篇修改讲解
□□蒋维豪主讲
第一讲:
生产运营管理的变迁……………………………………………….…….2-7页
第二讲:
丰田管理模式的起源…………………………………………….……….8-11页
第三讲:
丰田的精益化策略:
平准化生产……………………………..……..12-16页
第四讲:
全局观点与及时生产………………………………..................……17-18页
第五讲:
JIT事先策略
(一)流水线集结………................................19-24页
第六讲:
JIT事先策略
(二)以库存拉动……………………………...………25-31页
第七讲:
JIT事先策略(三)快速切换……………………………....….….…33-37页
第八讲:
现场改善的基石目视化…………………………………….…..………38-44页
第九讲:
持续改善……………………………………………………………......………45-49页
第十讲:
激活人的潜能…………………………………………………….…….…..…50-51页
第十一讲:
征服杂度………………………………………………………………..….……52-58页
第十二讲:
迈向精益……………………………………………........................……59-63页
第一讲:
生产管理思想的变迁
什么是生产运营管理?
就是把生产部门那所拥有的这些资源,我们要把人力资源、设备的资源,物料的资源,工艺、技术、章法的资源跟生产需求信息的资源等,我们要把它有效地整合起来,变成一个效率非常高、有效的一个运营的系统,或者说是运作的系统,我们如何把资源整合,变成一个有效的系统,然后拿这个系统来帮我们很有效的把我们资源的投入、物料的投入、变成我们的产品,也就是变成我们的产出。
那么,这个系统在处理我们的投入变产出的过程当中,当然要来实现我们企业对整个整个运行管理所赋予的一个所谓的期望的结果,也就是所谓的运营的目标,那么把资源整合起来变成一个有效的系统,让它能够说明我们实现我们的运营目标,这一系列的过程一系列的活动总的加起来成为运营管理。
所谓的管理的活动,再把它一分为四,如下:
第一个我们把它称为策划,策划叫Plan,我们根据我们运营目标,对我们这个运作系统的要求,我们来设计我们实现目标的手段,也就是这个运营系统。
所以呢,对于运营管理要做的第一件事情,当然我们要来思考,我们要来策划,我们的事情,到底应该怎么做。
也就是我们这一套运作的系统。
那么,到底应该如何运作、如何策划,如何设计让它能够非常有效的完成的目标,所以管理的第一动作就是策划Plan。
第二动作就是驱动,叫做DO。
我们要想办法来驱动这个系统,让它动起来。
我们要让设备动起来,我们要让人动起来,那么借由这个整个系统的驱动的过程让这个系统来为我们完成这个所谓的运营目标,完成生产任务,实现运营的目标。
当你把这个系统驱动了以后,可能还不够,我们要来加上第三个动作。
第三个动作成为控制control,我们要持续不断地来追踪,衡量、评价这个运作系统,我们同样都希望它能够我们实现运营目标,所以我们要持续不断地跟进,为现在的成果打分数,来跟原本我们所期望的结果进行比较分析。
第四个动作一般管理上的习惯把改进称为叫做A:
Action。
只要有差异,就要进行纠偏;只要有机会,我们要进行改进。
那么借由我们对一个系统的策划,对于策划好的系统,我们驱动它让它动起来,在执行的过程中,我们不断的监控来达到我们的期望值,有差异有落差我们要进行纠偏,我们系统有不足,我们要不断地来改进,这个PDCA就可以把我们所谓的管理活动一分为四,那么生产运营管理,我们里所当然的也就必须来设定一个标杆。
在目前全世界执行所谓的生产运营管理整个成绩最好的、绩效最高的、展现的最犀利的最有效率的当然是非丰田的管理模式。
丰田,它拥有一套非常扎实的一套管理的章法,借由这套章法它实现了丰田今天基本上已经接近世界第一名的汽车厂的绩效,这门课程,我们将来会借由这个丰田的管理思想,从头开始他们一路积累,如何积累如何发展到最后整合出来这么一套这么完善的一套管理理念,管理章法的整个发展跟实践的过程来做说明。
在丰田汽车生产运营管理模式之前,全球有关生产运营管理的这一套章法在过去这五六十年以来,它的整个发展或者是演变的过程是从二战之后迎来了一个营销学上的猛暴型需求的年代,一夜之间忽然全世界对物资的需求一下子爆炸开来了。
在这种猛暴型的市场需求的大前提之下。
全世界具备生产力的国家管理思想自然而然的朝着所谓追求产量的大目标来发展他们的管理思想,这一过程最为经典的国家就是美国。
它在二战期间,国土的资源没有受战火波及所赐。
二战后美国就能够很快地恢复生产:
很快地就用强大的供给力量。
来供应全球物资的需求,在这么一个大前提下,当时美国的制造业和企业,基本上追求的就是怎么样用最快的方法用最快的速度把这个产品做出来,所以整个管理思想称为产量的时代。
当时美国想到的方法就是延续着以前泰勒的分工的那一套逻辑章法,那么进行细部的分工。
分工分得越细,做起事情来就会越有效率。
要我们的经济规模能放得越大,那么我们的成本就能够降低,这个是美国的管理当时的第二个核心思想,追求经济规模的扩大,借此来降低成本。
那么这个管理细想一直影响着整“全世界的生产运营管理的一些基本思想,一直延续到1978年。
因为在1978年,产生了一件事情。
1978年有一位美国的学者他写了一本书叫《日本第一》也称《JapanIsnumber0ne》那这本书的主要的内容是:
在描述日本竟然有责有能力在战后短短的三十年时当中,已经有五十几大类的产品。
它的国际市场份额已经爬升到全世界第一位。
那么就根据这一个过程这个事就写了这本书叫《日本第—》。
《JapanisNumberone》,那么这本书出来了以后对于全世界就好像投下一颗原子弹一样,大家忽然之间眼睛大亮。
开始一窝地来研究日本的一些管理章法。
日本的管理思想之后获得了一个结论日本的产品质量非常好。
那是戴明博士对日本的产品的质量的建立所赐在1947年,戴明博士进入日本之后他们来教日本人怎么样把产品的质量提升上去。
他教日本人怎么样在全球市场的罅缝中求生存,去寻找自己的一个发展的空间。
他教日本人千万不要跟美国的产品正面的交锋,硬碰硬鸡蛋丢石头一点机会都没有,你一定要在美国人照顾不到的市场罅缱里去寻找成长的机会。
那么从罅缝继中开始对美国的产品进行市场的蚕食鲸吞。
可能才未来最关键的是要把产品的斥量提升上去,那么戴明博士在日本很长的一段的时间他持续不断在教日本的企业怎么样提升产品的质量。
当然这么一路的做着做着他总算皇天不负苦心人就把整个日本的很多产品的质量一路的提升了上去。
到了1980年呢,全世界在一窝蜂的观察学习分析,日本成功的原因之后做出了一个结论:
日本的生产企业,他们的生产运作的章法不是只有在追求产量的提升,而是他们在追求产量提升的同时他们在考虑产品的质量的提升,不但把产量做上去同时也要把质量做进去。
在整个生产运营管理的这层领域到了80年代基本上我们就可基本上就是一个质量管理的时代。
全世界只有在一窝蜂的所有的企业在进行质量的提升,开始在他们的生产运作系统加入很多质量控制的方法,质量提升的方法,改变了整个生产的运作运境基本架构。
那么一路走着走着,1980年整个TOM全面质量管理的就好像雨后春笋一样。
很多企业都开始导入所谓的全面质量管理的这一套系统来提升他们的产品的质量。
那么整个管理的思想,就这么走着发展到1989年到1990年代又产生了一件事情那么89年刚好这个日本的泡沫经济破灭了,以后整个它们的经营环境就好像多米诺骨牌一样一个压倒一个产生了一运列的连锁反应,那么当时大家以为我们本来以为日本管理方法有多好看起来也不过尔尔。
结果正在笑话日本整个经济体系崩溃的同时,竟然发现很多的日本的企业冒出了头角。
它不但没有垮,它反而赚钱是越赚越凶,那么所有这些企业,基本上都是以丰田汽车为代表,所以在90年代又开始来研究丰田汽车为什么能够对付得了这样一个经营环境。
它能够经营得这么好,那么在一窝地研究之后,大家又得出了一个结论,丰田汽车之所以能够盈利、能够成长之所以能够生存因为它拥有一套自己的一套管理章法,有自己的一套管理模式。
这一套丰田管理模式不但有能力追求产量的提升,有能力把质量做进去,也有能力把速度做出来,同时也能够把成本降下去。
大家忽然之间才在思考整个生产运作环境,光考虑产量不够,考虑质量也不够,我们还必须考虑成本的降低和速度加快。
所以在90年代之后又掀起了精益生产的一股风潮。
精益的生产这个名词出现了以后,的确国有很多的企业开始导入开始学丰田的这套管理模式。
后来也证明了相应的都职得了相当不错的成绩。
所以在90年代整个生产运作管理系统的章法又被要求整个结构必须产生一次改变。
你必须具备一个好的运作管理运作系统,想要实现运营的目标不但要求产量的提升,质量的提升,而且还要考虑速度的加快跟成本的降低。
同时考虑到这个生产目标。
这个生生产运作系统才是一个好的运作系统。
我们中国的改革开放,基本上真正开始跑起来动起来应该80年代末期之后的事情那么早期整个深圳特区的改革开放作为模板。
积累了成就之后,那开始向沿海一线的开放,中国在改革开放的早期就好像一战之后产生了一个猛晕型的市场需求的是一样。
因为在改革开放的时候把很多的物质的需求开放了,老百姓可以自己选择想要的东西了。
所以就好像整个市场需求一夜之间爆发出来。
中国的企业在20世纪90年代末基本上就是停留在所谓的追求产量的时代,只要产品做的出来就能够把人民币换回来。
国内的企业就这么一个简单的追求产量的一个管理章法。
一直到1994年,可能是因为国家宏观调控的关系,也可能是因为这个IS09000进行第二次的改版。
改版完了以后在我们中国红红火火地做了一次宣传。
所以在1994年之后中国的企业好像家家户户都必须搞一张IS09000的1张证书。
没有这张证书就好像企业搞不下去一样。
结果在94年之后昵中国才正式被宣布进入产量加质量的越个运作逻辑章法。
在90年代大家因为导入IS09000的这一套质量管理体系。
对整个生产运作的章法就比较成熟了一点。
同时考虑了产量,也考虑了质量,那这一套运作的运境。
就这么一直维持到了2004年又产生了一次地动山摇的改变。
因为中国在2001年12月11号宣布要加入WT0,加入WT0就是当时我们向全世界关贸总协的成员的国家,我做出了一些承诺请关贸总协的国家先对我们中国开放你们的市场,那么你给我们中国五年的时间改造。
我们希望在五年之后,也就是2006年的12月11号的那一天开始。
那我们中国的整个市场将全面的对全世界开放。
等我五年的时间就好,那么我也是循序渐进一路地改进,比如说我的关税会一路一路不断的住下降,这是有时间表的。
那么这个过程就在2001年我们决定加入WT0之后等干已经宣布中国的整个市场的经营的形式将会在2006年的年底变成全球化的竞争。
在90年代之后日本泡沫经济破灭了以后造成全球经济的一次衰退。
在90年代之后,全球就已经陷入一个微利竞争的时代。
利润很微薄,整个企业经营管理过程只要稍一步小心就会亏损。
所以在微利竞争时代的大前提之下大家才想到丰田这套管理模能够同时追求产量提升,质量提升,最重要是它能够把成本将下去,把速度做出来。
所以它能够有效的去面对微利竞争的时代。
那么中国加入WT0等于也就代表说在2006年中国的市场必定会和全球一样进入这个时代。
只不过整个微利竞争的时间到来提前了两年。
在2004年下半年可能是因为汽车价格大崩盘的关系。
整个汽车价格一路地下划造成对一级二级汽车厂跟一级二级供应链那么也产生整个价格的下滑的效应,结果这个大环境的影响很不幸是这个汽车价格下滑零部件下滑,结果整个所有的原材辅料、钢铁上涨、石油化学工业的产品上涨,甚至有很多农产品棉花上涨、面料上涨。
所以造成整个国内的制造业的生产成本一路开始的上涨。
中国就等于提前在2004年的下半年就已宣布进入了微利竞争的时代。
到了2004年大家忽然之间才恍然大悟,我们必须重新改变我们生产运作逻辑的章法。
我们的生产运作环境改变的过程前前后后花了五六十年的时间慢慢地变从二战之后到了1980年才产生第一次的转变向质量的转变。
一直到了90年代才产生第一二次的向成本跟速度的转变。
可是我们中国的企业被要求在短短的的十几年当中,必须而从质量转变成产量加质量。
到2004年之后开始又变成时产量加质量加成本加速度所以整个运作运统的变革的速度要求加快。
毫无疑问给管理者带来了一个很强大的—个变革的压力,那么整个管理思想借这么一路的演变下来之后。
因为对目标要求产生改变,所以生产运作章法手段当然也必须跟着变。
生产运作管理可以从资源角度来切入,也可以从结果的角度来切入。
从资源角度来切入,谈的是人员管理、物料管理、设备管理。
从资源的角度来谈应该怎么管理。
也可以从结果的角度来谈管理,可以谈质量管理、生产管理、成本管理、交期管理,不管是从哪个角度切入到最后都必须进入一个整个运作系统。
一个质量管理为了保证最终产品的质量,我们是不是到最后我们会发现最终产品的质量跟我们整个产品到底是怎么做出来的这一套章法有关,它跟设计有关,跟技术有关系,跟采购有关系,当然也会跟我们的整个生产制造的过程产生关系。
为了控制产品质量我们就必须回到整个运作系统里来寻找质量的变异点来控制好这些变异点,来保证最终产品的质量这个叫做质量管理。
成本管理也一样,成本到底应该如何降低,要回归到产品到底是什么做的。
从这个证作系统里面去寻找核心,才能够找到成本降低的机会。
交期管理也必须在回归整个运作系统里头来观察和识别和时间有关系的参数,对时间有关系的参数我们进行改善、进行控制能够保证我们交货时间能够缩短,保证我们能够准时的把货支付出去。
所以在谈生产管理不管从哪个角度切入,从资源角度切入,从结果的角度来切入,到最后你都必须要进入整个运作管理的系统。
事实上就是整个生产管理的核心。
第二讲:
丰田管理的模式的起源
目前在整个生产运作管理最好的这个企业当然就是日本的丰田汽车。
它能够持续不断地每年获得非常稳定的利润,比如说2005年赚了103个亿的美金。
相对世界第一大的汽车厂美国通用汽车2005年亏损,2006年也一样。
丰田汽车又增长到了140个亿的美金。
美国通用汽车还是一样亏损。
我们了解到丰田它确实有一套非常犀利的生产运作的管理章法值得我们去学。
大野耐一在1945年进入了丰田汽车之后,他很快就发现丰田汽车的一些生产运作管理上的不合理地方。
比如说他看到了当时丰田的汽车他们有个3个车间,这3个车间生产的计划的排程非常不合理。
当时丰田汽车只有在生产卡车,一个月大概需要五百部的卡车的这种需求量所以他们的生产计划投放方式就把一个月要做的五百部卡车的生产指令投放在第一个车间。
我们假设我们第一个车间说它叫零件车间,那么它这个生产指令投放给他,那么它就是把五百部卡车所需要的材料开始生产这五百部卡车,可能忙了十天之后把所有五百部卡车所需要的所有零件做好了后才把它转绐第二个间。
我们假设把第二个车间叫做部件的组装车间,部件车间又等到材料过来了以后开始组装它的部件。
那就结果月中11号材料进来了,我们开始加班加点忙起来,必须赶在20号之前把所有的部件组装完成。
也许我们说20号五百部卡车的部件全部组装完成了整个成批的转给总装厂,总装厂到了21号才开始有活干。
才开始这个组装它的五百部的卡车。
因力零件跟部件那个时侯才全部到开始讲行组装。
那个时候大野耐一说“这个生产计划排程的方法太不科学了,这个叫蛇吞蛋,我们丰田吞下去了五百部卡车的大巨蛋,结果消化不良。
花了三十天的时间才做完,因为移动批量太大,因为我们转换的时间延迟太长。
”要等到五百部卡车的所有零件全部完成有办去向下移交,因为你不成套我部件无法组装,部件也一样一定要到五百部卡车的所有部件全部成套了完成了才把它整批的转交给总装车间。
你不成套我也一样没有办法组装,这个大野耐一就采取了一个做法他下了一个命令把这五百部卡车干均地分配给一个月当中的二一十五个工作天,五百部除以二十五天就每天二十部卡车,所以我指令下的方法从1号开始的工作天的每一天你第一个车间只能生产二十部卡车所要用的零件,只要做出这个零件之后你就必须马上把它当天转给二十部卡车的部件的组装。
第2天把二十个卡车所需要的部件组装完成了以后必须当天把它转移绐第3个车间。
也就是总装车间,总装车间日到了第3天。
它就有足够的零件跟部件可以开始进行它的组装任务,所以可能第3天结束之后二十部的卡车就出来了。
从第3天之后的每一天都能够出来二十部的卡车。
这一个降低移动批量,蛇吞蛋把蛋变小了之后,创造出来的出来的第一效果就是它的生产周期缩短了,半成品库存降低,成品库存降低、资金流入的速度加快了。
这就叫做降低生产批量带来的效果。
假设冲压车间100个零件装成1箱,它的整个生产批量是一百个产品需要一百分钟才能够完成这一批,也就是一百分钟之后这一东西才有可能转移下一道工序,下一道工序它也一样每一个加工时间需要一分钟,它当然也就是需要一百分钟的时间才能够把这批东西生产完成。
移动批量越大,代表为了等待它成为一批的我们把它叫批量等待时当然就越长。
在一个产品假如你有相当多的零部件必须要生产,那么品种越多等待的时间就可能会越多,生产周期也会延长到一定程度。
所以大野耐一进入丰田汽车之后他的第一件改善就是蛇吞蛋把蛋变小,就是降低了它的整个生产跟移动的批量之后就马上取得了一个效果。
第一个降低移动批量带来的好处第二个降低移动批量带来的好处
所以后来大野耐一尝到了这个甜头,所以它的整个生产跟移动的批量。
他搅尽脑汁想尽办法持续不断的一直想办法在压缩他的移动批量。
当然他到最后做到了把整个移动的批量降到只有一个,这个就是在精益生产里我们所称为叫单件流,叫0nePieceFlow做每道工序集结起来合并起来之后,我做完一我就往下交一个,就把批量等待的时间全部把清除掉。
我们可以想象当批量等待的时间只有一个的时候,那么我们的成本周期可以缩短了什么程度。
那么我们的整个生产的效益,市场的反应可以提升到什么程度。
我们考虑用什么方法来降低我们的移动批量呢,必须要大批量的搬运,大批量的移动,生产的批量越太,可能它的生产成本越经济。
可能是因力某一些设备,它是共用设备。
所谓共同设备就代表它可能必须要同时生产很多不同的产品,所以第一个产品生产完了以后,你要更换模具,要更换工装治具,要重新调整这台设备才能够生产第二种产品。
我们把这个称作切换,那么很可能是因力你生产的切换时间太长,每次切换要2个小时,生产的整个过程中你舍不得在很短的时间之内又进行第二次的切换,前面所说的这个产品,那么生产的这个产品就真的就是生产上所需要的吗?
那么这个事实上我们都会发现,通常很多企业就是基于切换时间太长所以它会把生产批量放得很大,产生的批量等待时间,生产批量放大,可能生产出来的这个批量不是眼前所需要的,可能两千个拿去用,很可能有四千个是留下来当成库存留着以后慢慢地用。
那么你可以想象为了切换,把批量加大再来产生第二个问题,后面就有第一个第二个第三个第四个第五个产品在后面排队。
假如你是以每天生产一个产品来做生产计划那你可以想象你后面有多少产品它要排队排多少天。
结果这一天所生产出来的这一批产品口只有一小部分是你眼前迫切所需要使用的,另外有一小部分可能是摆起来以后要用的就产生了很多的余量库存,很可能是因为切换时间太长。
所以你的生产批量必须要放大。
大野耐一当时为了降低移动批量所想到的一些解决方法:
第一个我们讲缩短距离,假设所有的工段距离很远,那么当然第一个工段做好了的东西必须要搬到第二个工段,就会产生了一个搬运的需求,你当然而然就会考虑搬运的成本,所以搬运批量当然要放大。
在这种情况之下,只要生产跟生产的环节周期被缩短,只要生产的环节跟生产周期环节之间的搬运距离能够被摆脱搬运效率的制约,只要距离够短,左手能够交给右手。
那么当外我们的整个移动的批量就能够降到变成只有一件,我们叫做单件流。
我们可以尽可能有一些工装用具,可以借吊挂系统生产搬运作业,就能够打破必须大批量移动时间。
其它企业也有在2个车间做了一个重力的滑道,我东西做好了以后一放它自然而然就能够滑到下一道工段。
第三讲:
丰田的精益化策略:
平准化生产
在1945年大野耐一到了丰田汽车之后,他看到整个看到整个汽车生产计划不合理,那么他就把整个月计划改成日计划。
车间的生产计划因此大幅度提升。
之前有太多的批量等待的时间被延误了,造成三大车间彼此之间忙闲不均。
他尝到这个甜头后在思考整个降低移动批量的过程。
把一个月所需的生产需要分配到25个工作天之内,每一天只要生产二十部的卡车。
这种概念逐步的被定义成新的管理的理念,叫做平准化的生产。
大野耐一发现他只要能够把一个月当中的这个生产任务平均分配给每一天,那么每一天只生产20多辆的卡车。
他的整个思想系统能够做一个很合理的配置。
后来的丰田汽车就有了一级配套厂,二级配套厂。
那么每一天生产的数量假如都能维持非常稳定的数量,代表每天给一级供应商的需求指令也非常的平均。
每一天你既然要做20部卡车,就帮我生产20多部的部件,一级配套厂,二级配套厂,这很可能三台设备五个人工人形成一个小的工作组就能够跟丰田汽车进行专门的配套。
所以一级供应商因此被平准话了以后,能够合理话,同时,整个资源利用率提升到最高。
能够给整个供应链带来利用率的提升。
在1949年,大野耐一进入丰田汽车之后,做了第一个改善所形成的管理上的思维概念。
有2个利处,第一个就是想办法来降低移动批量,可以缩短生产周期,可以降低半成品的库存能够释放流动资金,能够借此来提高市场的放应速度。
第二把每个月的需求分配给每一个工作天,代表生产资源的配置,那么能够用最合理,有能够帮助我的一级、二级供应商,让他们每一天都有非常稳定的订单。
整个生产资源的配置也一样。
能够整个资源的利用率也能够提升到最高。
一般制造业最大的痛苦就是我们借来的订单的数量很不稳定。
有时月初订单全部涌进来,造成我们必须加班加点,可是很可能到了月终或者月底,前面的订单全部生产完成了,新的订单没有进来。
造成生产资源产生闲置。
一般的企业可能有淡旺季之分,每一年的旺季跟淡季差异很大,自然而然就必须要根据整个需求的最高峰来配置你的设备资源和人力资源,只是很少有这么好的运气能够让你的每一天的资源够能够让你的生产任务非常的饱满。
当最高峰过去的时候整个生产掉到了谷底,那个时候,你为了要让你的设备,让你的人力资源有活可以干。
对资源的配置对一般的企业是非常困难的事情。
然而当大野耐一思考到了平准化的这种生产计划排程的方法能够给他的供应商带来合理化的好处,所以他就坚定了这种管理话细想,这种计划的思想。
如何做好平准化生产呢?
首先你必须要有策略性的选择,比如说你有一百个产品,你可能把每一件产品的销售量、需求量先进行一个统计的分析,分析完后排这个排行榜。
精益变革的过程本来就是由点而线,由线而面的一个逐步发展的过程。
第一要选定平准化要生产的产品,思考平均每个月大概需要需要多少数量,再平均分配。
假设要生产1000个这样的产品。
可以建立一个成品的缓冲库存,我先准备好两千个成品的缓冲库存。
每天只要生产400个来填补这些库存,用缓冲库存来面对市场的需求的波动。
然后用平准化的生产方法每天400个来填补缓冲过程。
第二件事情建立成品的“缓冲厍存”。
缓冲库存建立好了以后,我们就按照每一个月平均需要10000个,把它平均分配到每一天二十五天,每一天变成只要400个,生产计划就可以按照每一天需要400个来进行整个生产流水线的设计,所以我们为了要设计这一条所谓的平准化的生产线,每一天大概就是生产出来400个产品。
大野耐一在这个时候他就想到了一点,他创造了一个名称叫节拍时间,他把一天需要400个产品,把它平均分配到一天的标准工作时间里面去。
他把每一分钟生产出来的一个产品的这一个分钟叫节拍时间。
节拍时间算出来