20钢液体渗碳工艺及性能分析.docx
《20钢液体渗碳工艺及性能分析.docx》由会员分享,可在线阅读,更多相关《20钢液体渗碳工艺及性能分析.docx(19页珍藏版)》请在冰豆网上搜索。
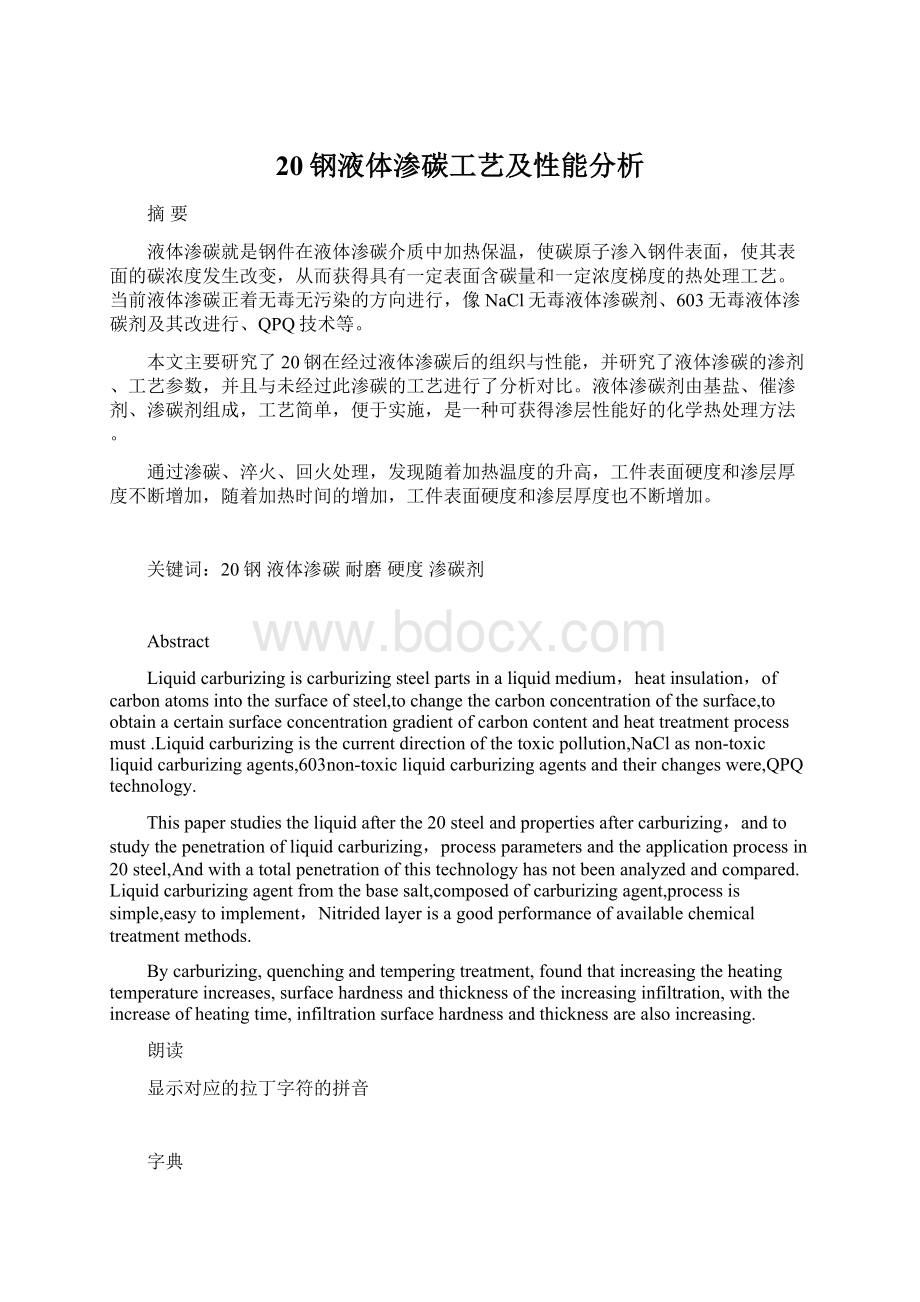
20钢液体渗碳工艺及性能分析
摘要
液体渗碳就是钢件在液体渗碳介质中加热保温,使碳原子渗入钢件表面,使其表面的碳浓度发生改变,从而获得具有一定表面含碳量和一定浓度梯度的热处理工艺。
当前液体渗碳正着无毒无污染的方向进行,像NaCl无毒液体渗碳剂、603无毒液体渗碳剂及其改进行、QPQ技术等。
本文主要研究了20钢在经过液体渗碳后的组织与性能,并研究了液体渗碳的渗剂、工艺参数,并且与未经过此渗碳的工艺进行了分析对比。
液体渗碳剂由基盐、催渗剂、渗碳剂组成,工艺简单,便于实施,是一种可获得渗层性能好的化学热处理方法。
通过渗碳、淬火、回火处理,发现随着加热温度的升高,工件表面硬度和渗层厚度不断增加,随着加热时间的增加,工件表面硬度和渗层厚度也不断增加。
关键词:
20钢液体渗碳耐磨硬度渗碳剂
Abstract
Liquidcarburizingiscarburizingsteelpartsinaliquidmedium,heatinsulation,ofcarbonatomsintothesurfaceofsteel,tochangethecarbonconcentrationofthesurface,toobtainacertainsurfaceconcentrationgradientofcarboncontentandheattreatmentprocessmust.Liquidcarburizingisthecurrentdirectionofthetoxicpollution,NaClasnon-toxicliquidcarburizingagents,603non-toxicliquidcarburizingagentsandtheirchangeswere,QPQtechnology.
Thispaperstudiestheliquidafterthe20steelandpropertiesaftercarburizing,andtostudythepenetrationofliquidcarburizing,processparametersandtheapplicationprocessin20steel,Andwithatotalpenetrationofthistechnologyhasnotbeenanalyzedandcompared.Liquidcarburizingagentfromthebasesalt,composedofcarburizingagent,processissimple,easytoimplement,Nitridedlayerisagoodperformanceofavailablechemicaltreatmentmethods.
Bycarburizing,quenchingandtemperingtreatment,foundthatincreasingtheheatingtemperatureincreases,surfacehardnessandthicknessoftheincreasinginfiltration,withtheincreaseofheatingtime,infiltrationsurfacehardnessandthicknessarealsoincreasing.
朗读
显示对应的拉丁字符的拼音
字典
Keywords:
20steelliquidcarburizingwearhardnesscarburizingagent
摘要····································································Ⅰ
Abstract································································Ⅱ
第1章绪论····························································1
1.1项目的发展背景··················································1
1.2项目发展趋势和研究意义··········································1
第2章材料分析························································2
2.1材料分析························································2
2.1.120钢的成分特点············································2
2.1.220钢的用途················································2
第3章20钢液体渗碳的实验仪器和内容····································4
3.1实验原理························································4
3.2实验仪器························································4
3.2.1加热设备和检测设备········································4
3.2.2显微硬度测试原理··········································6
3.2.3观察金相的步骤············································6
3.2.4渗碳层深度的测量··········································7
3.3实验药品························································8
3.4具体工艺及参数的确定············································8
3.4.1预先热处理工艺确定········································8
3.4.1.2正火温度············································8
3.4.1.1正火时间············································8
3.4.2液体渗碳热处理工艺确定····································9
3.4.2.1盐浴配方············································9
3.4.2.2液体渗碳工艺参数····································9
3.4.3渗后热处理工艺确定········································9
3.5总体实验步骤···················································10
3.5.1渗前预处理步骤············································10
3.5.2渗前准备阶段··············································11
3.5.3渗碳步骤··················································11
3.5.4渗后热处理················································11
3.5.5渗层的检测················································12
3.6渗碳后缺陷及控制···············································12
第4章20钢液体渗碳后的组织与性能······································14
4.1.液体渗碳后的硬度数据及曲线·····································14
4.1.1液体渗碳后的硬度数据······································14
4.1.2液体渗碳后的硬度曲线······································14
4.1.320钢液体渗碳后的金相组织··································16
4.2实验结果分析···················································17
4.2.1硬度分析··················································17
4.2.1.1渗碳温度对比········································17
4.2.1.2渗碳时间对比········································17
4.2.2渗层分析··················································17
4.2.2.1渗碳温度对比········································17
4.2.2.2渗碳时间对比········································17
4.2.3金相分析···················································17
4.2.4渗碳与未渗的对·············································17
4.2.4.1金相分析············································18
4.2.4.2硬度分析············································18
结论····································································19
致谢····································································20
参考文献·······························································21
第1章绪论
本课题研究的是20钢进行液体渗碳的工艺及渗碳后的性能分析。
1.1项目发展背景
宋元时期开始,古代工匠除了采用百炼钢技术以外,还采用了熟铁和生铁合炼的技术。
“团钢”和“灌钢”技术,实际上都属于液体渗碳制钢法。
北宋的沈括在《梦溪笔谈》中描述了团钢的制备方法,是“用‘柔铁’盘屈之,乃以‘生铁’陷其间,泥封炼之,锻令相入”。
液体渗碳与固体渗碳比较,有渗速快、渗层厚度均匀和产品质量稳定等的优点。
具有冶炼生铁坚实基础的中国古人独创了以熔融生铁为渗碳剂的液体渗碳方法,极大地推进了我国古代的钢铁制造业。
液体渗碳究竟始于何时,目前尚不清楚,很有可能《吴越春秋》描绘的“三百人鼓橐装炭,金铁乃濡”就是液体渗碳的开端。
采用液体渗碳方法制取“灌钢”的技术可能很早,西晋的张协有“楚之阳剑,欧冶所营,乃炼乃烁,万辟千灌”。
这里所谓“灌”,可能指的是“灌钢”,到宋代,灌钢流行全国,已经取代炒钢和百炼钢,成为当时主要的炼钢方法。
这是我国古代热处理技术的一项独创性的成就[1]。
在化学热处理方面,液体渗碳方法在制钢方面又有了很大进展,这时采用所谓的“生铁淋口”技术,生产的钢材被称为“苏钢”。
宋应星在《锤锻》篇中提及采用液体渗碳法对锄具进行表面处理的工艺。
锄用“熟铁锻成,熔化生铁淋口,入水淬健,即成刚劲。
”可以看出,该工艺是将锄具在熔化生铁中渗碳,目的是使其表面成为高碳钢,经淬火后得到马氏体而强化。
从近代起,尽管仍有地方生产“灌钢”或“苏钢”,如在安徽的芜湖、湖南的湘潭、四川的重庆、威远等地人们还在使用这一传统技术,但在全国范围内,这一传统的液体渗碳制钢法不再成为制钢主要手段[2]。
1.2项目发展趋势和研究意义
液体渗碳方法以其渗入速度快,渗层均匀,工件变形小,且可直接淬火,设备简单,成本低廉等优点,并且在操作中具有很大的机动性,在盐浴中可以装入或取出任何单独的零件而不影响其余的零件,因此可以不停止生产过程而在不同的零件上得到不同深度的渗碳层,这一点是其他渗碳工艺无法达到的。
正因如此,液体渗碳工艺在国外工业发达国家仍在广泛应用着。
但是液体渗碳盐浴中的渗剂是采用氰盐,或是反应生成物中含有氰根,其毒性大,对人体、环境危害极大。
因此围绕液体渗碳的盐浴组成,渗剂的选用、改进等问题进行了多年的研究[1]。
当前液体渗碳正着无毒无污染的方向进行,像NCL无毒液体渗碳剂、603无毒液体渗碳剂及其改进行、QPQ技术等。
第2章材料分析
2.1材料分析
2.1.120钢的成分特点
1.特性该钢属于优质碳素钢,冷挤压、淬硬钢。
该钢强度低,韧性、塑性和焊接性均好。
抗拉强度为253~500MPa,伸长率≥24%。
20钢特性与15钢基本相仿,但强度稍高[3]。
正火可促进该钢球化,细化大块状先共析铁素体,改进小于160HBS毛坯的切削性能。
该钢零件工艺路线为:
下料→锻造模坯→退火→机械粗加工→冷挤压成型→再结晶退火→机械精加工→渗碳→淬火、回火→研磨抛光→装配。
2.未热处理态,硬度≤156HBS。
3.20钢的化学成分如表2-1[3]:
表2-120钢的化学成分(GB\T699-1988)
元素
C
Si
Mn
Cr
P
S
Ni
Cu
含量W%
0.17~0.24
0.17~0.37
0.35~0.65
≤0.25
≤0.035
≤0.035
≤0.25
≤0.25
4.相变点温度(近似值)Ac1=735℃,Ac3=855℃,Ar3=835℃,Ar1=680℃
5.正火规范温度920~950℃,出炉空冷。
硬度131~156HBS。
6.冷压毛坯软化处理规范温度700~720℃,保温时间8~15h,再以50~100℃/h的冷速,随炉降至温度≤550~600℃,出炉空冷。
处理前硬度≤143HBS,软化后硬度≤131HBS。
7.淬火规范温度910℃±10℃,10%NaCl盐水冷。
2.1.220钢的用途
20钢适用于制造汽车、拖拉机及一般机械制造业中建造不太重要的中小型渗碳、碳氮共渗等零件,如汽车上的手刹蹄片、杠杆轴、变速箱速叉、传动被动齿轮及拖拉机上凸轮轴、悬挂均衡器轴、均衡器内外衬套等;在热轧或正火状态下用于制造受力不大,而要求韧性高的各种机械零件;在重、中型机械制造业中,如锻制或压制的拉杆、钩环、杠杆、套筒、夹具等。
在汽轮机和锅炉制造业中多用于压力≤6N/平方,温度≤450℃的非腐化介质中工作的管子、法兰、联箱及各种紧固件;在铁路、机车车辆上用于制造十字头、活塞等铸件[
20钢依靠自身的材料特性硬度不会超过40HRC,作为工程结构钢,它具有足够的强度和良好的焊接性,成形工艺性及一定的耐蚀性。
当然20钢也可以作为机器零件用钢,这种材料主要承受拉、压、弯、扭、冲击、疲劳应力,且往往是几种载荷同时作用,可以是恒载或变载,作用力的方向可以是单向或反复的,工作环境是大气、水、和润滑油,温度在室温到100℃范围之间,机械零件要求有良好的服役性能,有足够的强度、塑性、韧性和疲劳强度等。
20钢淬火后生成低碳马氏体,为这些应用奠定了基础,相对于中碳和高碳钢来说,淬火后,低碳马氏体具有更好的韧性。
表面经强化处理后可使这种材料具有更好的综合性能,这种强化处理包括钢的化学热处理,比如渗碳、渗氮、碳氮共渗、渗硼、磞氮共渗等,经过这些处理后其表层可达到理想硬度,而心部的韧性高于中高碳钢,这样的性能在机器零件中应用十分广泛。
而单纯的20钢只能应用于不太重要的小型零件,这就决定20钢一般不直接使用,而是先进行表面强化处理[4]。
第3章20钢液体渗碳的实验仪器和实验内容
3.1实验原理
液体渗碳就是在液体介质中进行的渗碳。
它可分为两类:
一类是加有氰化物的盐浴,另一类是不加氰化物的盐浴。
因氰化物有剧毒,顾前类盐浴以不采用。
本实验用不加氰化物的盐浴,这种盐浴的组成大体上可分为:
一是加热介质,即NaCl和KCl;二类是催渗剂,即Na2CO3,即尿素和木炭粉。
这种盐浴在渗碳时的反应是
3(NH2)2CO3+Na2CO3→2NaCNO+4NH3+2CO2(3-1)4NaCNO→2NaCN+Na2CO3+CO+2[N](3-2)2NaCNO+O2→Na2CO3+CO+2[N](3-3)2CO→CO2+[C](3-4)由以上反应可以看出:
①虽然是液体渗碳,但渗碳反仍然是在钢件表面的气相反应
②原材料虽然无毒,但反应的结果仍使盐浴中含有NaCN(0.5%);③盐浴还有一定的渗氮功能[4]。
3.2实验仪器
本次实验的设备均来自学校实验室,包括试样加工设备、加热设备和检测设备。
3.2.1加热设备和检测设备
试样是使用实验室切割器和砂轮进行加工的,在此不再赘述。
加热设备为SX2.5-12箱式炉、SX-G07130节能箱式电阻炉和坩埚,SX2.5-12箱式炉额定加热温度为1000℃,主要用于实验室作化学分析、加温、热处理、物理测定和一般小型钢件热处理时加热之用。
由铁铬铝合金丝绕制成螺旋状的加热元件穿于内炉衬上、下、左、右的丝槽中。
炉内为密封式结构,电炉的炉口砖,炉门砖采用轻质耐火材料,内炉与炉壳之间用耐火纤维、膨胀珍珠岩制品砌筑为保温层。
SX-G07130节能箱式电阻炉额定加热温度为1000℃,加热原理和构造与SX2.5-12箱式炉相似,不同的是它是由数字显示温度和保温时间,能手动设置加热步骤,然后自动执行命令,而且它的精度更高,升温平稳,清洁性也相对较好,适用于温度变化对实验结果影响较大的热处理。
检测设备为MDS倒置金相显微镜、HXD-1000TMC/LCD显微硬度计及图象分析系统和全洛氏硬度计TH320。
如图3-1MDS倒置金相显微镜用于观察分析材料的金相显微组织,具有高性能无限远光学系统、完善的观察功能、先进的图像采集分析系统,可进行自动智能管理、控制操作、图像分析并生成报告。
如图3-2HXD-1000TMC/LCD显微硬度计及图象分析系统用于测定精密零件、金属组织及渗碳等硬化层的显微硬度,完成硬化层深度测量及曲线绘制,能够进行数据测量、统计分析、报告存储打印。
还可用于观察和拍摄金相显微组织。
包括机体、升降工作台、物镜压头转塔、自动加载机构、摄像照明系统、测微目镜系统、控制系统、图象分析系统等。
如图3-3TH320全洛氏硬度计为集洛氏硬度实验机、表面洛氏硬度实验机、塑料洛氏硬度实验机一体的多功能硬度计,采用洛氏(ROCKWELL)测量原理,可直接进行洛氏硬度测量、表面洛氏硬度测量、塑料洛氏硬度测量,并可以将洛氏硬度值转换为HB、HV、HLD、HK、σb值。
适用于碳钢、合金钢、铸铁、有色金属及工程塑料等材料的硬度检测,具有测试精度高,测量范围宽,主实验力自动加卸载,测量结果数字显示并自动打印或与外部计算机通讯等特点。
可广泛应用于计量、机械制造、冶金、化工、建材等行业的检测、科研与生产[5]。
图3-4为坩埚。
图3-1MDS倒置金相显微镜图3-2HXD-1000TMC/LCD显微硬度计及图象
分析系统
图3-3全洛氏硬度计TH320图3-4坩埚
3.2.2显微硬度测试原理[5]
本次实验选择的实验参数为:
500gf的试验力,试验力保持时间5s,放大倍率40倍。
显微硬度是一种压入镀层硬度,反映被测物体对抗另一硬物体压入的能力。
测量仪器是显微硬度计,它实际上是一台设有加负荷装置且带有目镜测微器的显微镜。
测定时,将试样置于显微硬度计的载物台上,通过加负荷装置对四棱锥形的金刚石压头加压。
金刚石压头压入试样后,在试样表面上产生一个菱形凹坑,测量凹坑对角线长度,根据所加负荷及凹坑对角线长度就可计算出所测物质的显微硬度值。
由于所用金刚石压头的形状不同,显微硬度又分为维氏(Vickers)显微硬度和努普(KnooP)硬度两种。
维氏显微硬度是用对象为136°的金刚石四棱锥作压入头,其值按下式计算:
(3-5)
式中HV——维氏硬度;
α——正方形四棱角锥体,二相对面夹角(规定为136°);
p——荷重,g;
d——凹坑对角线长度,μm。
努普硬度是用对棱角为170°30′,和130°的金刚石四棱锥作压入头,其值按下式计算:
(3-6)
式中HK10—努普硬度;
α——正方形四棱角锥体,二相对面夹角(规定为170°30′);
β——相对于短对角线的夹角(规定为130°);
p——荷重,g;
L——凹坑对角线长度,μm。
3.2.3观察金相的步骤
金相显微组织观察是为了更好的分析和研究试样经热处理后的组织变化。
制备显微试样包括磨光,抛光及浸蚀三个步骤。
1.磨光
磨光可用手工和机械两种方法。
手工磨光:
试样是在不同号数的金相砂纸上进行磨光。
砂纸号数有240#,400#,600#,800#,1000#,1200#六种,其中240#最粗,1200#最细。
首先在粗的砂纸上进行磨光,当看到划痕时,把试样转换90度再磨,直到在同一张砂纸上看不到划痕时,换下一号砂纸,顺序进行。
磨光过程中磨削压力不要过大,用力要均匀,避免出现圆角。
试样磨好后在抛光机上进行抛光。
机械磨光:
一般是在预磨机上进行,即把砂纸用水玻璃粘住预磨盘上进行使用,试样也从粗砂纸到细砂纸依次进行磨光。
然后在抛光机上抛光。
本次实验使用手工磨光法。
2.抛光
抛光的目的是除去试样表面的细磨痕,最后得到一个光亮的镜面。
抛光在抛光机上进行。
抛光机是由电机和水平抛盘(直径200~250mm)两部分组成。
抛光盘上铺有固紧的抛光布。
抛光过程中,隔一段时间把,抛光液洒在抛光盘上,抛光液是由抛光粉和水组成的悬浮液。
抛光粉一般有氧化铝,氧化铬,氧化镁等。
抛光时压力不宜过大,抛光时间取决于试件表面磨光的质量,一般为5~15分钟。
抛光后,试件磨面应光亮无痕。
之后先用清水冲洗,再用无水乙醇清洗磨面,然后用吹风机吹干表面。
3.显微试样的浸蚀
金相试样抛光后,在显微镜下只能观察到光亮的表面和夹杂物,石