研磨加工技术四五章.docx
《研磨加工技术四五章.docx》由会员分享,可在线阅读,更多相关《研磨加工技术四五章.docx(32页珍藏版)》请在冰豆网上搜索。
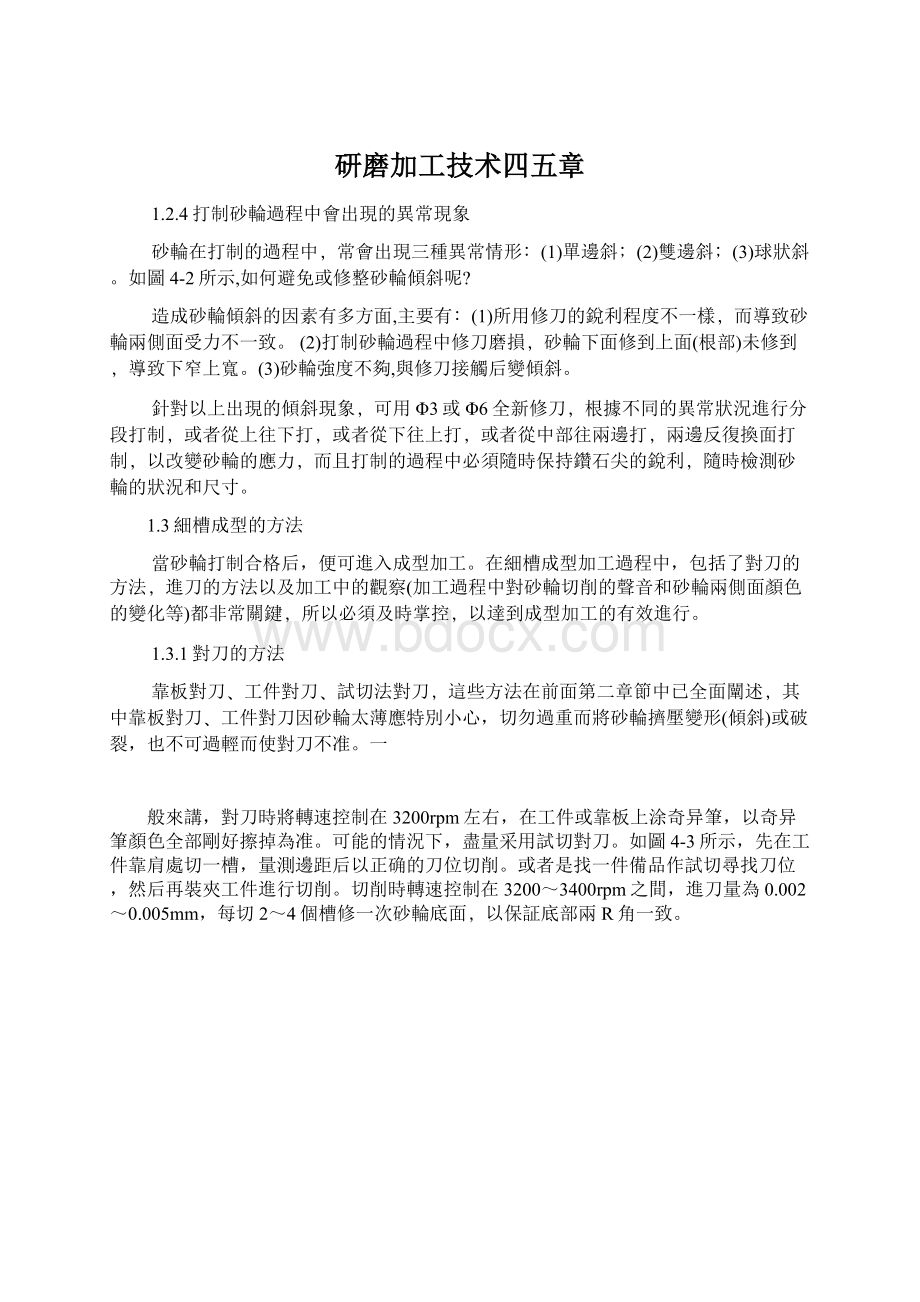
研磨加工技术四五章
1.2.4打制砂輪過程中會出現的異常現象
砂輪在打制的過程中﹐常會出現三種異常情形﹕
(1)單邊斜﹔
(2)雙邊斜﹔(3)球狀斜。
如圖4-2所示,如何避免或修整砂輪傾斜呢?
造成砂輪傾斜的因素有多方面,主要有﹕
(1)所用修刀的銳利程度不一樣﹐而導致砂輪兩側面受力不一致。
(2)打制砂輪過程中修刀磨損﹐砂輪下面修到上面(根部)未修到﹐導致下窄上寬。
(3)砂輪強度不夠,與修刀接觸后變傾斜。
針對以上出現的傾斜現象﹐可用Φ3或Φ6全新修刀﹐根據不同的異常狀況進行分段打制﹐或者從上往下打﹐或者從下往上打﹐或者從中部往兩邊打﹐兩邊反復換面打制﹐以改變砂輪的應力﹐而且打制的過程中必須隨時保持鑽石尖的銳利﹐隨時檢測砂輪的狀況和尺寸。
1.3細槽成型的方法
當砂輪打制合格后,便可進入成型加工。
在細槽成型加工過程中,包括了對刀的方法﹐進刀的方法以及加工中的觀察(加工過程中對砂輪切削的聲音和砂輪兩側面顏色的變化等)都非常關鍵﹐所以必須及時掌控﹐以達到成型加工的有效進行。
1.3.1對刀的方法
靠板對刀﹑工件對刀﹑試切法對刀﹐這些方法在前面第二章節中已全面闡述﹐其中靠板對刀﹑工件對刀因砂輪太薄應特別小心,切勿過重而將砂輪擠壓變形(傾斜)或破裂,也不可過輕而使對刀不准。
一
般來講,對刀時將轉速控制在3200rpm左右,在工件或靠板上涂奇异筆,以奇异筆顏色全部剛好擦掉為准。
可能的情況下,盡量采用試切對刀。
如圖4-3所示,先在工件靠肩處切一槽,量測邊距后以正确的刀位切削。
或者是找一件備品作試切尋找刀位,然后再裝夾工件進行切削。
切削時轉速控制在3200~3400rpm之間,進刀量為0.002~0.005mm,每切2~4個槽修一次砂輪底面﹐以保証底部兩R角一致。
1.3.2進刀方法以及注意事項﹕
進刀時特別強調上下進刀和左右走刀的協調性。
通常進刀的方法有兩種﹕傳統進刀法和深切緩進法。
(1)傳統進刀法
在加工前﹐首先確認工件的細槽需不需要粗切。
一般情況下﹐對于0.3mm以下的槽不必粗切﹐對于0.3mm以上的槽則要視其切削寬度、數量及切削深度而決定是否粗切。
粗切時槽兩邊的留量至關重要﹐
如果粗切后槽兩邊余量不等﹐精切時則會使砂輪底部兩R角磨損不一致﹐從而使砂輪兩則受力不均均﹐槽切斜(如圖4-4所示)
不需粗切的工件﹐加工時也要注意砂輪兩R角磨損是否一樣。
在切削過程中﹐及時修整砂輪底部相當重要。
砂輪底部修整的好壞直接影響工件的加工品質。
一般情況下﹐修整砂輪底部時﹐機台轉速必須控制在2800-3000rpm之間﹐每次進刀0.001-0.003mm﹐前后手柄要均勻搖出﹐以保証砂輪底部粗細均勻。
當發現砂輪底部兩R角不一致時﹐可把砂輪R角磨損較大的那一邊底部修整稍細些﹐磨損較小的那邊修整稍粗些﹐以調整砂輪兩邊的切削力與砂輪的磨損﹐達到控制兩R角的目的。
切削過程中,砂輪轉速要控制在3000-3300rpm之間,Z軸進刀量在0.005-0.003mm﹐
(2)深切緩進法
a.如圖4-5所示,對于此種深槽
的加工﹐
采用深切緩進法加
工(簡稱一刀過加工法)。
一刀
過
切削此槽具有一定的難度。
首
先是機台的精度和機台額定轉
速﹐其次是加工技朮和砂輪打制。
在現有機台JL-618額定轉
速(3600rpm)限定的情況下﹐加工比較困難,我們只有將機台馬達轉速提升到3600
--7200rpm之間﹐以此來增大砂輪切削線速度﹐增強切削力﹐達到良好的切削效果。
(磨床變頻器是可以調節砂輪轉速的﹐通常狀況僅設定為3600rpm﹐如果要提升則必須經相關部門的允許)。
使用時從安全方面考慮﹐砂輪前面必須裝上防護罩﹐并且明確標示該機台的最高轉速。
特別強調﹕經升速后的機台﹐在常規加工中﹐必須注意使用轉速不得超過3600rpm。
b.成型砂輪修好以后﹐先在工件表面對刀歸零﹐然后將砂輪下降6.50mm﹐底部留0.020~0.030mm余量。
切削時機台轉速控制在4200rpm左右為宜。
c..慢慢移動左右導軌手柄﹐從右向左移動﹐利用聽聲器掌握砂輪切削工件所受到阻力大小來調節移動手柄的速度。
(主要靠加工經驗和手感來控制)。
當砂輪完全搖過了工件后﹐再以0.002-0.005mm的進刀量把深度尺寸6.532加工到位。
深切緩進法加工注意事項﹕
(1)在加工的過程中要注意砂輪的寬度(磨損)和強度的變化﹐每次裝夾切削的實際寬度不得超過1.00mm。
(2)手柄在移動過程中要緩慢而均勻﹐不能撞擊工件﹐以免砂輪破裂。
(3)工件裝在正角器上加工為宜﹐這樣可以隨時取下工件量測﹐隨時掌握當前的加工狀況。
再次裝夾復位性好。
(4)砂輪前面必須裝上防護罩,以免砂輪破裂傷人。
1.4案例解析
(1)
---典型細槽的加工
1.4.1案例工件的特點﹕
(1)槽易切斜。
(2)齒頭部極易彈動﹐導致頭部倒角。
(3)屬薄齒深槽加工類,宜采用深切緩進法加工(一刀過切法)。
下圖4-6所示為工件加工藍圖(簡圖).
1.4.2解決方案
為解決以上加工難點,必須要有一個合理的加工制程與加工參數。
以下加工方案為實際生產中多次摸索總結的經驗。
加工制程為﹕RMGF1ESGF2QC
(1)RM備料加工:
選用深冷熱處理VIKING材料(此為易變形,易斷齒工件的特別要
求﹐材料經此方法處理后﹐其內部組織較穩定﹐能有效控制工的變形﹐
切削性龍好
)。
備料呎寸為45.25mm*22.55mm*1.76mm。
(2)GF1第一次研磨加工
a.粗磨厚度,留0.05mm餘量,長度及寬度各留0.1mm餘量。
b.用60J砂輪粗切段差,依外形留量,並如圖4-7預留寬度為2mm的站腳。
c.用100J砂輪粗切背部17個0.70
*0.70
的頂針槽,砂輪寬度打至
0.5mm,槽側面單邊留0.1mm餘量,底部依
外形留量。
d.精磨六面體,外形呎寸到位,並使工件變形控制在0.005mm以內。
e.用120J砂輪將寬度打至0.710mm精加工背部
頂針槽,並清角至0.03mm以內,再用此砂輪將靠
肩3.00-0.01呎寸到位。
f.選用100J砂輪精成型側視圖頭部各斷差
及斜面,並使19.350mm呎寸及站腳處的底部
尺寸1.335mm到位,以便於去站腳時不碰傷成
型面。
(3)ES放電加工﹕加工頭部導入斜面21.5*1.60
。
(4)GF2第二次研磨加工
a.首先將工件主視圖頭部兩邊斷差加工完成,然后將工件裝於正角器上,總體裝夾誤差不得超過0.002mm。
b.
打成型砂輪0.250+0.01(0.500-0.250-0.01)﹐打制方法參考第四章第一節細槽砂輪的修制。
+0
-0.003
c.精切槽先在工件上奇異筆水,砂輪轉速選用3300~3400rpm,側面在已切過的最邊齒部分對刀,深度呎寸用工件表面對刀來保證,每切5個槽將砂輪底部修掉0.05mm,直到切完,無需清角。
修砂輪底部時轉速應調為2200~2300rpm,以保持砂輪的銳利。
d.去站角,使1.335呎寸到位。
(5)QC檢驗并交生管包裝出貨。
1.4.3參考資料:
(1)細深槽砂輪切削參數對照表:
細深槽砂輪切削參數對照表
砂輪寬度(mm)
0.5~0.4
0.4~0.3
0.3~0.28
0.28~0.25
0.25~0.20
0.20~0.18
最大切削長度(mm)
20
15
10
5
1.8
1.5
切削深度(mm)
3.5
3.6
4.5
3.9
3.9
3
排屑間隙(mm)
0.3
0.3
0.3
0.3
0.3
單件長度(mm)
1.0
2.0
0.8
0.8
0.4
0.25
砂輪型號
120J/180J
180J/320J
320J/500I
320J/500I
320J/500I
500I
轉速(rpm)
3300
3300
3300~3400
3400
3400
3500
最大進刀量(mm)
0.01
0.01
0.005
0.005
0.003
連續進刀
注:
本表數據是近期內研磨現有工件所列出的經驗值,僅供參考。
(1).
(2).
1.4案例解析
1.4.1案例工件的特點﹕
槽底有一斜面﹐導致砂輪切削過程中易斜﹐工件槽底部易產生倒錐,傷到右側面。
(如圖4-8)
1.4.2原因分析
如圖4-8,由于成型砂輪打成單斜面加工時﹐
工
件斜面對砂輪產生一個反作用力F﹐該力有一水平分力F1﹐使砂輪向右傾斜﹐從而使切出的槽出現側錐異常。
1.4.3解決方案
應用此成型砂輪加工深槽時,應考慮切削時的受力情
況,避免因受力不均而導致刀具(砂輪)變形,出現加工異常。
具體步驟﹕
(1)首先將頭部斷差成型完成。
(2)再用直槽砂輪在斷差面對刀﹐后向下切削﹐切入深度到斜部停止。
(如圖4-9)
圖4-9
(3)將砂輪兩邊打成對稱斜度﹐繼續往下切削﹐直至槽底尺寸。
(4)將砂輪打成單斜面﹐并將工件另一邊斜面去掉。
第二節薄小齒的成型研磨
2.1薄小齒的特性
從字面上就清楚其特殊性在于薄和小。
薄﹐
導致工件強度不足﹐極易變形﹐切削成型時易
彈動﹐齒頭部易倒角。
小﹐導致難于裝夾定位﹐
推毛刺費時﹐如右圖4-10所示(工件外形尺寸為
2.5*0.801*9.0,且齒頭部較薄為0.26mm)為典型的
薄小齒。
2.2薄小齒的加工方法及注意事項
2.2.1薄小齒加工的著想點
在實際加工中如何針對薄小齒的具體特性(太小不易裝夾﹐太薄
易于彈動等等)而加以克服﹐最終達成藍圖的要求﹐這是在加工之前首先要考慮的。
當然還有是否對下工段(放電、線切割等工段)產生不良影響也很重要﹐這一點將在第五章講述。
2.2.2薄小齒加工方法﹕
薄小齒的加工關鍵在于對工件齒部的分析﹐克服其問題點,通常情況有以下几種方法﹕
(1)多利用先一體成型加工再切片加工﹐一體加工要求盡可能多的完成加工步驟和部位。
以減少切片后帶來更多的麻煩。
在砂輪的選擇和打制上沒有太多的特殊要求。
經過多年的加工經驗﹐運用砂輪的側面加工比用砂輪的底部加工效果要好﹐多運用把斷差齒改成槽類齒的加工模式。
(2)齒強度不足,多采用加強邊和嵌入式加工的方法.
2.3案例解析
(1)
---加強邊
2.3.1案例工件的特點
如圖4-11所示,當研磨加工最后一個齒時,由于余量過少導致切削過程中彈動而將齒彈斷。
2.3.2解決方案
針對最後一個齒易彈斷的狀況,將齒
邊加寬以增大其強度。
如圖4-12方式備料(RM)﹐當工件上
a<3.0mm時﹐c尺寸的備料需在正常留留量的情況下外加3mm余量。
當工件上a>3.0mm時則正常備料。
2.3案例解析
(2)
---化零為整的加工方法
2.3.1案例工件的特點﹐如圖4-13﹕
工件數量多,外形极小且尺寸精度高﹐推毛刺費時,裝夾不便,剛性不足,齒部尺寸難以保証。
2.3.2傳統加工方法
加工步驟:
下整料→成型主視圖→切片、磨厚度0.801→成型右視圖0.26尺寸→去站角→完工處理→品檢。
缺點:
成型右視圖0.26及6.00尺寸難以保証精度。
去毛剌費時,裝夾困難,剛性不足。
圖4-14
2.3.3改善歷程一:
加工步驟:
下整料→成型主視圖→切槽成型右視圖(整塊)→切片、抓邊距、磨厚度→品檢。
(1)優點:
推毛剌費時,裝夾困難,剛性不足問題均得以解決。
OK率有較大的提升。
圖4-15
(2)缺點:
齒部倒角仍然存在。
2.3.4改善歷程二(圖4-16):
加工步驟:
下整料→成型主視圖→隔位切槽法(即一個槽隔一個槽加工,注意隔位加工時,第一批槽要完全加工好后方可進入第二批槽加工,同時降低切槽速度)→切片、抓邊距、磨厚度→品檢。
圖4-16
經過此次加工﹐圓滿地解決了用傳統方法加工產生的所有問題。
此案例的成功為微小工件的製作提供了一條可行的新思路。
2.3案例解析(3)
---薄齒嵌入式加工
3.3.1案例工件的特點﹕
如右圖4-17所示﹐此細長薄齒易傾斜,又
因工件整體體積較大,無法用下整料加工即無
法用案例
(2)的方式解決.
3.3.2解決方案:
採用連體拼合加工的運用,將薄斷差
轉化為薄齒。
同時將傳統的底面
加工
改善為側面成型進行加工。
但此工件
一個方向即0.46mm尺
寸成型好后,對
於0.24mm的尺
寸仍然須用砂輪底部去成型。
為
了克服齒部彈動,特將齒嵌入一
治具中,即所謂的嵌入式加工。
此
方法解決薄齒加工齒易彈動問題非常有效。
3.3.3具體加工方案如下:
(1)RM備料
備料時將左右兩件下在一塊,如圖4-18所示,呎寸為26.0mm*17(7.8*2+1.40)mm*1.9mm。
(2)G研磨工段
a.
+0
-0.01
先成型右視圖。
六面體粗磨,粗切0.8mm斷差
並留站角,頭部0.24mm的斷差先不要粗切
(如圖4-19所示)。
精磨六面體呎寸
到
位并加工2.99靠肩呎寸到位。
此
過程一定要保證厚度尺寸一致.
b.成形主視圖頭部:
用120J泰
利砂輪把25.00mm、1.75mm、
0.15mm、
1.6.01mm以及0.20mm
各呎寸成型到位。
因為是左右體,加工時可對稱加工兩邊各呎寸。
各呎寸到位后,打制寬約為0.80+0-0.01mm的砂輪,如圖4-20所示,垂直切下去,底部切至27.85mm。
0.46mm呎寸用0.80mm的砂輪對刀后一次到位,然後加工頭部0.20mm呎寸。
頭部成型
好后,根據工件實際寬度,換算
呎寸后打制成型砂輪寬度為X加
工2.1mm×3.01mm的呎寸。
(3)用80J砂輪把圖4-20中工件
頭部的
陰影部份去掉。
(4)成型右視圖頭部(如圖4-21加工草圖)
(1)在加
(2)工右
視圖頭部前,要先加工三套治具,如
圖4-22所示。
a.先加工兩塊厚度分別為0.34~0.58與1.295~1.535的擋塊﹐然后根據工件的實際尺寸再在上面加工几個0.47寬的小槽﹐用于切斷時卡住0.46尺寸的齒。
b.再據圖面尺寸加工一根厚為0.340的薄片﹐用于精切A面段
差時墊在B面上﹐避免加工時由于B面懸空而造成彈動。
圖4-21
圖4-22
斷差具體加工步驟為﹕
a.用治具2卡住工件頭部0.46尺寸齒上﹐切出B面0.34尺寸的斷差。
b.加工B面上頭部0.20*5°的倒角。
c.將工件反轉裝夾并將治具3墊在B面下面,然后用治具1卡住工件頭部0.46尺寸齒上﹐加工A面﹐保証尺寸0.24。
d.加工A面上頭部0.20*5°的倒角。
(5)去站角并加工1.075mm、1.6mm呎寸到位。
(6)切片加工7.800呎寸到位。
以上三種治具在研磨界運用非常普遍,主要是將薄齒嵌入治具槽
中以免加工時齒部彈動,原理雖簡單,但非常實用。
第三節超薄工件的成型研磨
3.1.超薄工件的特性
薄﹐易變形﹐六面体難于研磨,加工難度大。
單純是控制變形對于超薄工件來說沒有什么特殊性﹐本節主要講述由于工件太薄而導致其加工工序不能按傳統的方式加工﹐而必須采用异于傳統方法的其他方法加工。
3.2.超薄工件的加工方法及注意事項
3.2.1超薄工件加工的著想點:
超薄工件具有所有薄工件的難以修正變形的特點,然而本節所講的超薄工件其難度不只是在變形上,而是如何繞過變形問題,對工件其他部位進行有效加工,最終保証品質。
3.2.2.超薄工件的加工方法
1)充分運用第一章所講的修變形之方法,盡量減小工件的變形量
但有一點須注意,通常留站腳修變形的方法不适用,因為留站腳導致薄片部份懸空,熱量難以傳遞而更不容易修正變形。
2)多采用薄體部份最後加工,且不分粗精加工,一次到位的方式。
研磨此種工件﹐一般將工件外形尺寸做到下公差,避免加工厚度方向薄体尺寸時,由于砂輪對工件的擠壓而使工件內部組織產生細微變化﹐從而導致外形尺寸增大現象。
此值的變化程度一般在0.003mm以內,有時會因材質內部組織不同﹐此值會增加到0.007mm左右。
所以﹐我們在加工完工件后,一定要全檢外形尺寸﹐以免尺寸有增大超差現象。
3.3超薄工件案例解析
(1)
3.3.1案例工件的特點﹕
(1)太薄﹐厚度僅有0.15mm﹐加工面積大(如圖4-22)
圖4-23
此工件的加工方法有2種
方法一
1)將其厚度加工到1.000mm后抓正角﹐研磨六面體尺寸40.000至39.998﹐10.000尺寸研磨至9.997mm.
2)加工5.00mm与6.00mm的槽。
3)研磨厚度1.000mm到要求值0.15mm。
a.首先在水磨上兩面對稱去余量﹐控制變形。
當厚度磨到
0.30mm
以下時要特別注意﹕第一﹐砂輪的轉速不宜過高,一般控制在2800rpm以下﹔第二﹑y軸進刀要緩慢而均勻。
當厚度磨到只有0.05mm余量時﹐再半精修砂輪﹐這時將砂輪轉速控制在2000-2400rpm﹐進刀量為0.005mm,y軸走刀相對減慢。
當磨到余量只有0.01mm時﹐換用JL-618手搖磨半精磨一刀,Z軸進刀量單邊0.002mm,Y軸進刀要緩慢﹐轉速控制在1800轉/分,整個過程必須保証砂輪鋒利。
b.精磨精磨時首先要修砂輪底部﹐把轉速提升到2400轉/分。
砂輪底部對好刀后﹐Z軸下降0.005mm﹐前后手柄搖動速度要慢﹐來回3次﹐把砂輪底部修細一些來精磨厚度尺寸﹐保証其尺寸与光潔度。
精磨時﹐砂輪轉速應控制在1700轉/分﹐待尺寸ok后﹐將轉速提升到2000轉/分﹐兩面各空走一刀﹐使其光潔度更好。
一面加工ok后,翻面研磨另一面時﹐一定要將平台和工件擦拭干淨﹐使工件基准面與平台完全密合﹐如果一旦有灰塵或毛刺未去干淨﹐很容易使工件產生翹角變形。
所以研磨超薄工件時一定要注意這一點。
4)切頭部0.200mm槽打制0.200mm砂輪﹐砂輪ok后將工件裝
在正角器上,在工件側面對刀加工成
型0.200mm細槽,直到工件ok為
止。
方法二﹕
1)將工件厚度加工到1.000mm后抓正角﹐研磨六面體尺寸40.000至39.998﹐10.000尺寸研磨至9.997mm。
2)加工5.00mm与6.00mm的槽。
3)將工件加工成如圖4-23所示形狀圖4-23
4)切頭部0.200mm槽打制0.200mm砂輪﹐砂輪ok后將工件裝在正角器上,在工件側面對刀加工成型0.200mm細槽,直到工件ok為
止。
5)取下工件將毛刺去干淨后研磨厚度尺寸到位,方法步驟同上述方法一之步驟(3).
總之,只要我們掌握正确的加工方法﹐并在加工中合理選用加工參數﹐對待超薄工件的加工就不是一件難事。
1.3案例解析
(2)
---薄沖子成型
3.3.1案例工件的特點﹕
此工件為薄片沖子,材質是SKD11,極易
變形。
加之頭部有曲面成型,如果按照傳
統的方法加工則難於保證尺寸及控制變形。
3.3.2傳統方法一:
圖4-24
(1)下板料---成型主視圖,在薄片處留2—3個站腳,修變形----切片----疊加成型頭部曲面視圖----去站腳----完工處理
圖4-25
(2)問題點﹕
加工過程中有三點會產生變形和難以控制變形,第一點是因留有站
腳,使工件懸空而變形難以修復且費時;第二點是切片易產生變形;第三點是去站腳易產生變形。
所以此方法不可取。
3.3.3傳統方法二:
(1)下板料---成型主視圖,修變形----切片----疊加成型頭部曲面視圖(運用專用相嵌治具)---完工處理
(2)問題點:
雖然減少了因去站腳而帶來的變形,但切片后厚度加工卻變得非常困難,加之成型曲面要用專用治具,效率太低。
故此方法也不可取。
3.3.4解決方案:
(1)成型頭部曲面視圖----切片---最後成型薄體部份,一次到位---完工處理
圖4-27
(2)成型薄體部份時,須用CBN砂輪在水磨上一段一段的從頭部向后部切削,保持砂輪鋒利且小量進刀以控制工件變形。
第四節NCR程式的應用
4.1.NCR程式原理
NCR程式主要利用圓与圓相切,圓与線相切,切點唯一的原理而制成的,在研磨適用於砂輪外R對工
件曲面的加工。
面是由線構成的,線
又是由點構成的,即無數個點排在
一起,則構成了線,無數條線排在一
起則構成了面。
NCR程式就是先把
一個曲面分解成無數條線,再用一個正切面切這些無數條線,即得一條曲線,程式最根本的原理是在平面坐標中,將這條曲線細分成點,求出每點對應基點(原點)的坐標值(圖4-28).
4.1.1在運用NCR程式加工工件時﹐當砂輪與工件相切﹐因所成型工件形狀不同﹐而形成以下几種形式(如圖4-29示)﹕
4.1.2.NCR程式以突出以上5種形
式來合理選擇參數,利用電腦算
出砂輪
(1)与工件所形成曲面若干個切點座標的。
(1)据特定的參數最多可組成:
有單一凹圓
弧面、平面、凸圓弧面三种形式並存的曲面,也可依單一的兩种或一种形式存在。
(2)每個NCR程式只能表示出一段簡單曲面,當加工復雜曲面時,用多個NCR程式曲面相接便可完成。
(2)
4.2.NCR程式參數的含意
4.2.1砂輪截面半徑:
程式用砂輪外R的截面半徑(簡稱砂輪半徑)。
a.設定時盡可能接近頂圓半徑,但不可為零。
b.砂輪半徑必須小於或等于底圓半徑。
c.因加工曲面不同也可把砂輪打制
成
R、
R、R接斜面等(如圖4-31a、b)
4.2.2底圓半徑:
工件凹弧半徑
工件上凹圓永遠是底圓,且不可為“零”。
4.2.3.頂圓半徑:
工件凸弧半徑。
工件凸圓永遠是頂圓,可為零。
4.2.4.高度:
過底圓最低水平切點到頂圓最
高水平切點兩水平線間的垂直距離。
4.2.5.X初始值:
程式的第一個切點橫座標值。
a.單一程式一般設定為零。
b.相接程式前一個程式終止點是
后一個程式的初始點.。
4.2.6.Y初始值:
程式的第一個切點縱座標。
a.單一程式一般設定為零。
b.相接程式前一個程式終止點是后一個程式的初始點。
4.2.7.切線角:
底圓和頂圓的外公切線与水平線組成的夾角。
a.當底圓和頂圓相切時切線角程式
輸入值為零。
b.適用範圍0°~90°(如圖4-32a、b、c)
4.2.8.步角:
程式每步中過砂輪半徑圓心做
垂線,
與過切點做直線的夾角。
a.正負值判定:
与始角、切線角相同,与終角相反。
b.適用範圍-90°~90°
c.步角為電腦自行設定可不做輸入。
4.2.9.始角:
底圓初始點向圓心連線與圓心垂線所形成的夾角。
a.以底圓圓心做垂線為零點,程式運行方向為負值反