挤压模具设计.docx
《挤压模具设计.docx》由会员分享,可在线阅读,更多相关《挤压模具设计.docx(19页珍藏版)》请在冰豆网上搜索。
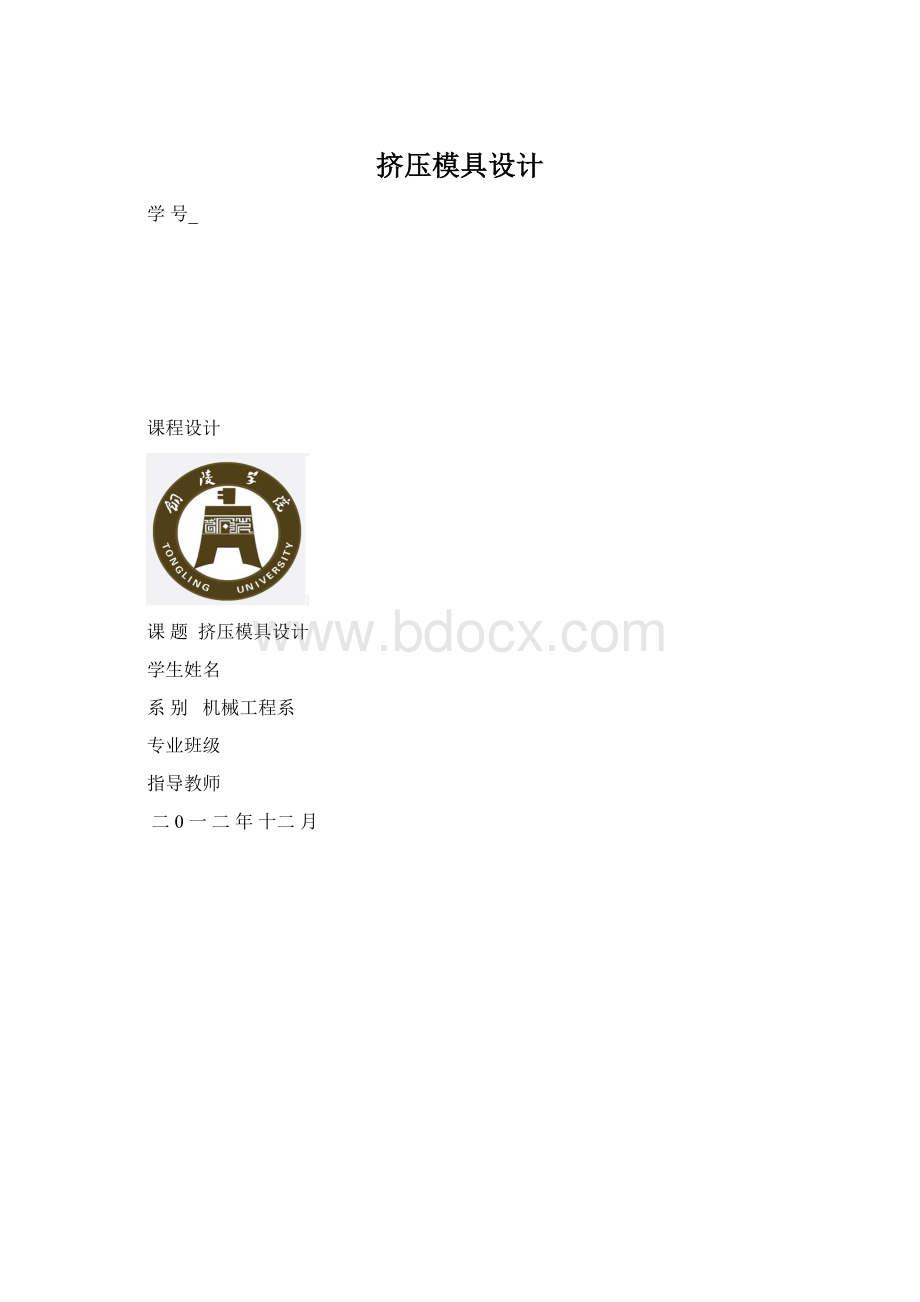
挤压模具设计
学号_
课程设计
课题挤压模具设计
学生姓名
系别机械工程系
专业班级
指导教师
二0一二年十二月
课程设计任务书
机械工程系09材控(1,2)班
指导教师:
。
设计课题:
挤压模具设计
一、设计条件:
在19.6MN挤压机的Φ200mm挤压筒上生产出下列条件的合格型材,设计出相应的型材模具。
1.单模孔模具生产如下图型材。
(1,2,3组同学设计)
2.双模孔生产ф12mm的圆棒材。
(4,5,6组同学设计)
3.三模孔生产ф8mm的圆棒线材。
(7,8,9组同学设计)
4.四模孔生产ф6mm的圆棒线材。
(10,11,12组同学设计)
二、设计内容:
1.模孔布置。
2.设计工作带长度。
3.型材模孔尺寸设计。
4.模子强度校核。
5.画出模具图。
三、设计时间:
2011年12月10日至12月14日
四、设计地点:
实验楼C楼501,502
五、分组情况:
组号
学生安排情况
型材金属种类
1
0910121001----0910121012,0810121039,0810121114
铜及其合金
2
0910121013----0910121023,0810121027
铝及其合金
3
0910121026----0910121036
镁及其合金
4
0910121037----0910121048
铜及其合金
5
0910121049----0910121060
铝及其合金
6
0910121061----0910121072
镁及其合金
7
0910121073----0910121084
铜及其合金
8
0910121085----0910121096
铝及其合金
9
0910121097----0910121108
镁及其合金
10
0910121109----0910121120
铜及其合金
11
0910121121----0910121132
铝及其合金
12
0910121133----0910121140,0906131060,0906121043
镁及其合金
第一章概述
1.1铝及铝合金简介
铝是自然界中分布最广的金属元素,地壳中铝占地壳总量的8.8%(重量),仅次于氧和硅。
铝通常以复杂的硅酸盐形态存在,铝元素在地壳中的含量居金属首位。
原铝在市场供应中统称为电解铝,是生产铝材及铝合金材的原料。
铝是强度低、塑性好的金属,除应用部分纯铝外,为了提高强度或综合性能,配成合金。
铝中加入一种合金元素,就能使其组织结构和性能发生改变,适宜作各种加工材料或铸造零件。
经常加入的合金元素有铜、镁、锌、硅、锰等。
铝合金共有九个系列,其中六系列铝合金代表6063主要含有镁和硅两种元素,故集中了4000系列和5000系列的优点6063是一种冷处理铝锻造产品,适用于对抗腐蚀性、氧化性要求高的应用。
可使用性好,容易涂层,加工性好;其主要特点为密度低,抗拉强度高,延伸率高,疲劳强度好。
其挤压和轧制制品已取得广泛的商业应用。
众所周知,因所含合金元素种类和数量、工艺参数设定、模具设计等因素,以及挤压变形特有的在截面上变形分布不均匀的特点,热挤压合金微观组织通常是非均匀的。
热变形组织的再结晶晶粒尺寸大小均匀性和第二相的尺寸及位置分布等因素,即合金微观组织的均匀程度,直接影响铝合金的力学性能。
1.2铝及铝合金特性的应用
铝是一种面心六方晶格的金属,具有12个滑移系,塑性很高,抗变形能力很小,可以挤压成形。
许多铝合金包括铸造铝合金、变形铝合金均可最为挤压材料,但是,生产上使用较多的还是一些易挤压的铝合金、镁合金。
对于铝合金来说,可用铝合金挤压时的极限温度范围来说明铝合金的挤压性,这一温度范围是由上限温度和下限温度来决定的。
温挤压工艺是在冷挤压工艺基础上发展起来的一种少无切削的成形技术。
所谓温挤压,是指对坯料在室温以上,再结晶温度一下的某一温度区域进行挤压。
温挤压成形的制件尺寸精度和表面粗糙度要明显优于热挤压,稍逊于冷挤压,具有加工硬化等特征。
正是因为温挤压的这些特点,其适用范围要比冷挤压大得多,凡是冷挤压难以成形的大尺寸,高强度材料都可进行温挤压。
温挤压自20世纪60年代问世以来,随着技术的不断完善,已被广泛用于各种机器零件的成形,是零件少无切削成形的有效手段之一.。
材料在挤压过程中,如挤压模具不是很好或模具挤压铝材过多,铝材表面会产生挤压痕,用手可能触摸其表面不光滑。
因此,在现代化大生产中实施挤压加工技术,其成败的关键是模具,模具设计以及其质量,事关产品的质量、成本。
在挤压设计的过程中挤压工艺条件:
应考虑挤压温度、挤压速度、模具(材料、形状、尺寸等)等多方面的因素。
第二章挤压生产的特点和发展
2.1挤压的特点
2.1.1挤压的优点
作为生产棒及线坯的挤压法具有以下一些优点:
(1)挤压时金属受到强烈的三向压应力,金属可以发挥其最大的塑性。
因此挤压可加工其他方法如轧制或锻造难于加工的金属材料。
挤压时金属可以一次承受很大的塑性变形。
(2)挤压可以生产断面极其复杂,或者变断面的管材和型材。
(3)具有很大的灵活性。
在一台设备上只要更换相应的模具就可以改换生产另一种产品,因此挤压非常适用于生产小批量、多品种和多规格的产品。
(4)产品尺寸精确,表面质量高。
(5)实现生产过程自动化和封闭化比较容易。
2.1.2挤压的缺点
挤压过程中,仍存在一些问题:
(1)金属的固定废料损失大。
在挤压终了是要留有压余和产生挤压缩尾,压余量一般占锭坯重量的10%~15%。
(2)挤压机结构复杂,投资费用高。
(3)加工速度低。
挤压的生产率一般比较低。
(4)由于变形不均,因此沿产品长度和断面上组织性能不均。
(5)挤压时在高温、高压环境下,挤压工具消耗较大,增加成本。
综上所述,挤压法非常适合于生产品种、规格和批数繁多的有色金属棒、线材等。
2.1.3挤压时金属的流动特点应力状态分布
按金属流动特征和挤压力的变化规律,将挤压过程分为三个阶段。
分别是填充挤压阶段,该阶段金属承受挤压杆的作用力,首先充满挤压筒和模孔,挤压力急剧上升。
第二阶段为基本挤压阶段(平流挤压阶段)。
该阶段中心部分首先流动进入变形区,外层流动的较慢,因此存在金属流动不均匀现象。
靠近挤压垫处和模子与挤压筒交界处形成难变形区。
该阶段的挤压力随筒内锭坯长度的缩短、表面摩擦力总量减少,几乎是直线下降。
第三阶段称终了挤压阶段或紊流挤压阶段。
该阶段会产生“缩尾”缺陷,挤压力也会上升。
挤压金属上作用的外力有:
挤压杆通过挤压垫给予金属的单位压力,挤压筒壁、模子压缩锥面和工作带给予金属的单位正压力和摩擦力;一定条件下,挤压垫和金属界面上也会出现摩擦力。
挤压时,变形区内金属一般处于三向压缩应力状态,即轴向压应力、径向压应力和周向压应力。
2.2挤压生产的发展
挤压法相对而言,是一种新的金属加工工艺。
直到1894年,制造了第一台可以挤压黄铜的挤压机,才得到发展。
二战以来由于各工业领域的发展,促进了挤压生产的急剧发展。
主要表现在:
(1)挤压机台数和能力在不断地增加,挤压生产线自动化程度不断提高。
(2)挤压技术得到不断创新,解决了许多问题。
(3)产品品种、规格不断扩大。
计算机辅助设计的应用,使人们分析挤压的过程更加容易,因此可以让我们避免一些人为的错误,从而提高材料的利用率。
随着能源危机的日趋严重,人们对环境质量将更加关注,加之市场竞争日益加剧,促使锻件生产向高效、高质、精化、节能节材方向发展。
因此用挤压成形等工艺手段所生产的精化锻件的产量,在市场竞争中将得到较大的发展。
20世纪后期,随着高速发展的工业技术,对挤压复杂断面、高精度、高性能制品的要求,促进了挤压技术向大型化、高精度、多功能、高效节能方向发展,出现了许多新技术和大型先进的挤压机。
世界上最大的立式反向挤压机为350MN,我国最大的卧式挤压机为125MN,新技术的发展如高速挤压、半固态挤压、连续挤压等大大丰富了挤压理论和技术。
目前我国挤压技术、工艺装备、生产规模、产品质量等已经步入一个更高层次的发展阶段,达到国际的先进水平。
第三章挤压工艺设计
3.1挤压工艺分析
3.1.1锭坯材料
6063合金是Al-Mg-Si系列中的典型代表,具有特别优良的可挤压性,是生产棒线材的首选材料。
它的特点是在压力加工的温度-速度条件下,塑性性能和抗腐蚀性高,没有应力腐蚀现象;在焊接时,其抗腐蚀性实际上不降低。
6063合金在热处理时剧烈强化。
合金中的主要强化相是Mg2Si和AlSiFe。
如果6063合金挤压棒线材在退火状态下的抗拉强度为98~117.6MPa,那么在淬火和自然时效后可提高到176.4~196MP,此时相对延长率下降不大;合金在160~170℃下,经过人工时效可以得到更大的强度效果,此时,抗拉强度可提高到269.5~285.2MPa。
但是,在人工时效时,塑性性能急剧下降。
淬火与人工时效之间的时间间隔对6063合金的强化程度有显著的影响,随着间隔时间有15分钟增加到4小时,抗拉强度和屈服强度降低29.4~39.2MPa。
人工时效的保温时间对6063合金半成品的力学性能没有重大影响。
3.1.2锭坯尺寸
锭坯尺寸选择得是否合理,直接影响到挤压制品的质量、成品率、生产率等技术经济指标。
锭坯尺寸(直径和长度)越大,制品越长,从而使切头尾、切压余的几何损失和挤压周期内的辅助时间所占的比例降低。
对压余所导致的金属几何损失,增大直径或者增加长度对成品率的影响不同。
锭坯体积一定时,增大直径和减短长度使几何损失增加,减少直径增加长度,几何损失减少。
选择锭坯的原则如下:
(1)锭坯质量符合要求。
根据金属、制品的技术要求和生产的工艺而定。
(2)根据塑性图可确定适当的变形量。
一般为保证挤压制品断面组织和性能均匀及满足其他技术要求,要求变形程度不小于90%。
(3)提高成品率,减少几何废料损失。
采取长度大的锭坯,挤压棒材时,锭坯的长度是其直径的1.5-3倍。
(4)满足设备能力和挤压工具的强度。
(5)保证锭坯可以顺利地送入挤压筒中,为此,锭坯与挤压筒要有足够的间隙,见表3-3。
(6)采用润滑挤压的挤压机,对锭坯表面要求质量高。
表3-1筒、锭间隙选择
挤压机
挤压筒直径
mm
间隙值,mm
类型
吨位,MN
卧式
—
≤100
1~3
1~5
100~300
5
≥300
10
立式
6
75~120
1~2
由上表可得,锭坯的直径为190mm,锭坯长度为380mm。
下图3-1用是ProE绘制的锭坯实体图:
图3-1锭坯实体图
3.2挤压的生产方案
3.2.1挤压方法的确定
挤压是将金属毛坯放入模具模腔内,在强大压力和一定速度的作用下,迫使金属从模腔中挤出,从而获得所需形状、尺寸以及具有一定力学性能的制品。
(1)按挤压材料的温度分为冷挤压、温挤压和热挤压。
冷挤压:
挤压时不加热坯料多用于生产管材、棒材和简单实心型材,冷挤压时,包括挤压碳素钢在内,一般在加工前要进行预先软化退火,在各道冷挤压工序之间往往也要进行退火处理,在冷挤压以前要进行磷化处理。
优点:
冷挤压是少切削和无切削工艺,节约原材料,生产率高,产品强度高,精度高,表面光洁。
但是冷挤压需要的变形力大,因此对模具材料提出了很高的要求,从而限制了冷挤压零件的尺寸范围。
温挤压:
是指对坯料在室温以上,再结晶温度一下的某一温度区域进行挤压。
适用一般材料变形尺寸或者零件尺寸较大,以致冷挤压设备不足,打算连续生产。
缺点:
温挤压与冷挤压相比,需要增加加热装置,产品尺寸精度与表面粗糙度虽与冷挤压较接近,但是还是差点,由于坯料需要加热,使劳动条件较冷挤压差。
但是坯料的变形抗力减少使得成型压力机的吨位也可以减少,如果控制合适,模具的寿命也比冷挤压时要高。
温挤压坯料在较低的温度范围内加热,使氧化,脱碳大大减少,所以产品的尺寸精度较高,表面粗糙度值降低。
热挤压:
热挤压是在加工前将坯料加热到金属再结晶温度以上的某一温度区域进行挤压的。
优点:
可使材料变形抗力降低,从而降低了对模具材料和挤压设备的要求,使固定资产投入大大减少,同时扩大了挤压零件的尺寸范围,使得一些低塑性的合金和难变形材料也可以采用挤压工艺。
与普通锻造件相比,挤压件加工余量小,通常单边余量只给0.5~2.5mm。
热挤压件有良好的力学性能。
热挤压件的表面质量和尺寸精度较模锻件高,其表面粗糙度可达Ra3.2尺寸精度可以达6~7级。
但是由于加热产生氧化,脱碳及热膨胀等问题,降低了产品尺寸精度和表面质量,因而一般都需要经过切削加工才能作为最后的产品。
由于使用冷挤压加工前要进行预先软化退火,并且需要的变形力比较大大,温挤压的温度不好控制,产品尺寸精度与表面粗糙也比较低,所以不采用,但是热挤压就不同,挤压所需要的变形力相对较小,产品尺寸精度也较高,挤压件加工余量小,所以综合分析采用热挤压方法
(2)根据金属流动方向与挤压轴运动方向之间关系分正挤压和反挤压。
正挤压是挤压生产中应用最广泛的一种方法,主要特点是挤压时金属流动方向与挤压轴的运动方向一致。
在挤压过程中挤压筒固定不动,锭坯在挤压轴压力的作用下沿着挤压筒内壁向前移动,使得锭坯表面与挤压筒内壁发生激烈的摩擦并引起锭坯的温度升高。
正向挤压的生产特点是:
制品的尺寸范围广大,灵活性大,自动化简单,投资费用少,易于分离残料;同时,摩擦产生的温度使锭坯的温度不均匀,导致金属流动不均匀。
为了避免由于金属流动不均匀造成的制品产生裂纹等缺陷必须降低挤压速度,从而导致生产效率低下,挤压残料较厚。
反挤压是挤压时金属的流动方向与挤压轴的运动方向相反,使挤压过程中的锭坯表面与挤压筒内壁之间无相对运动,改变了金属在挤压筒内流动的力学条件,减少了所需的挤压力,降低了变形的不均匀性。
反挤压生产的特点:
可减少总挤压力的30%~40%适合于应挤压生产,金属的流动性能较好,从而使挤压制品的组织和性能均匀,但由于受到挤压轴,挤压模的限制,使得挤压制品的表面质量欠佳,而且对锭坯表面质量要求严格,分离残料困难。
正向挤压机已使用于所有挤压过程挤压各种制品,在挤压条件相同时,反向挤压机相对可节能20~40%,制品质量、成品率和生产率均较高。
但是,由于制品规格受工具强度限制,对锭坯表面质量要求高,操作较复杂,因此正向挤压使用广泛。
(3)挤压机的选择
单动挤压机无独立穿孔系统,因此适用于挤压实心的型材和棒材。
双动挤压机具有独立的穿孔系统,一般用来挤压管材。
卧式挤压机的操作、监测和维护均较方便,普遍使用于所有规格、各种制品的挤压。
但是卧式挤压机容易失调。
长期使用过程中的磨损、变形,各种零部件的热膨胀,可以导致主要挤压工具的失稳。
立式挤压机一般生产中小型管材。
本设计中挤压棒线材可以采用正向挤压的卧式挤压机。
3.2.2挤压时的温度-速度选择
(1)锭坯的温度:
6063铝允许加热温度范围在320℃到550℃之间,为了保证制品的组织性能,挤压时锭坯的加热温度不宜过高,应尽量降低挤压温度。
这里取480℃。
(2)挤压筒的温度:
模具的成分多为合金模具钢钢,由于导热性差,为避免产生热应力,挤压前挤压筒要预热,为保证挤压制品的质量,并且具有良好的挤压效应,挤压筒温度可取400℃~450℃。
(3)挤压温度:
随着加热温度的增高,金属的塑性提高,更易于变形。
但是金属坯料的加热温度必须控制在一定的范围内。
因为金属坯料的加热温度过高,不仅会产生严重的氧化和脱碳,而且还可能出现过热和过烧现象。
热挤压的温度范围只从挤压开始到挤压终止温度之间的一段温度间隔。
此温度范围应保证被挤压金属坯料具有足够的塑性,较低的变形抗力和较为理想的金相组织。
热挤压中一般根据金属材料的种类、化学成分和产品零件图的性能要求等确定金属坯料的加热温度和挤压温度范围。
本设计挤压筒温度为450℃,挤压锭坯温度控制在480℃左右。
(4)挤压速度:
挤压速度低,金属热量逸散较多,致使挤压制品尾部出现加工组织。
挤压速度高,锭坯与工作内壁接触时间短,热量传递来不及进行,有可能形成区内的绝热挤压过程,使金属的出口温度越来越高,导致制品表面裂纹。
实际生产中,挤压速度常受到挤压温度的制约,挤压温度高时,必须在较低速度下进行挤压;在较低温度挤压时,才允许提高挤压杆速度考虑金属与合金的可挤压性,制品质量要求及设备的能力限制,本设计的挤压速度取1.5~1.8m/min。
第四章挤压工模具设计
4.1模具材质的选取
对于热挤压模具,由于工作环境十分恶劣,在挤压生产中长时间的承受高温、高压、强摩擦及循环载荷的冲击作用,导致模具使用寿命低且损耗大,通常模具费用占挤压生产成本的10%到15%。
因此,延长模具寿命,降低模具成本,一直是挤压生产过程中人们最关心的一个重要问题。
模具寿命不仅与挤压工艺、模具制造工艺过程有关,而且还与模具的材质选择有重要的关系。
模具材料必须具备以下条件:
足够的高温强度、良好的抗磨损性能、足够高的抗疲劳性、良好的导热性能以及良好的热处理淬透性和可氮化性;这些是模具材料选择的首选条件。
热挤压模具中,主要是含碳量为0.3%—0.5%的钢中,添加W,Mo,V,Cr,Ni的合金元素的高合金亚共析钢。
添加上述合金元素,可提高模具的高强度、耐热性、抗热磨损的性能。
目前,我国用于热挤压生产的模具材料,基本上是3Cr2W8V,4Cr5MoSiV1登高温耐热钢。
对于3Cr2W8V模具钢,其特点是较好的高温强度,但存在较高的脆性和热裂行,不适合用于挤压断面形状复杂的铝合金制品挤压模具;所以采用3Cr2W8V模具钢对于挤压简单型面的棒线材较适用。
4.2挤压模具尺寸设计
根据挤压机的结构、用途以及所生产的制品类别的不同,挤压工具的组成和结构形式也不同。
挤压工具一般包括:
挤压模、挤压垫、挤压杆和挤压筒。
模子是挤压生产中最重要的工具。
它的结构形式、各部分的尺寸,以及所用的材料和加工处理,对挤压力、金属流动均匀性、制品尺寸的精度、表面质量及其使用寿命都有极大的影响。
模子根据模孔的剖面形状,可以分为七种:
平模、流线模、双锥模、锥模、平锥模、碗形模和平流线模。
模子的主要参数,如图4-1所示。
4.2.1模角
模角是模子的基本参数之一,它是指模子的轴线与其工作断面间所构成的夹角。
当模角
等于
,其特点是在挤压时,可以形成较大的死区,从而可以获得优良的制品表面。
但是,如果死区发生在断裂时,则会在制品表面引起起皮或分层。
同时平模的挤压力也较大,特别是在挤压高温和高强度的合金时,模孔会因塑性变形而变小。
平模多用于挤压铝合金棒、型材和铜合金、镍合金等的管材与棒材。
故本设计中采用模角为
的平模。
4.2.2工作带长度
工作带又称定径带,是用于稳定制品尺寸和保证制品表面质量的关键部分。
工作带的长短直接影响到制品的质量,倘若工作带过短,则模子易磨损,同时会压伤制品表面导致出现压痕和椭圆等缺陷,制品的形状不容易保证;如果工作带过长,又极易在其上粘结金属,使制品表面上产生划伤、毛刺、麻面等缺陷,而且挤压力将升高。
因此根据实践得挤压铝及铝合金时,工作带长度不会超过15~20mm,本设计中取为15mm。
4.2.3工作带直径
模子工作带直径与实际所挤压出制品直径并不相等。
在设计时应保证在冷状态下不超过所规定的偏差范围,同时又能最大限度的延长模子的使用期限。
通常是用裕量系数
来考虑各种因素对制品尺寸的影响。
表4-1为挤压不同金属与合金时的模孔裕量系数
的值。
表4-1裕量系数
合金
值
含铜量不超过65%的黄铜
紫铜、青铜及含铜量大于65%的黄铜
纯铝、防锈铝及镁合金
硬铝和锻铝
0.014~0.016
0.017~0.020
0.015~0.020
0.007~0.010
对于棒材,按标准规定只有负偏差。
在挤压铜合金一类温度较高的材料时,因模孔会逐渐变小,所以工作带直径的设计应使开始的一批棒材的直径接近其名义尺寸。
随着模孔变小,挤压棒材的实际直径接近最大的负偏差。
挤压棒材的模孔直径dg可用下列式计算:
式中:
—棒材的名义直径;
—裕量系数,取为0.020。
代入数据得:
4.2.4模孔出口直径
模子的出口直径一般应比工作带直径大3~5mm,因过小会划伤制品的表面。
对型材挤压模来说,为了保证工作带部分的抗剪强度,工作带模孔与出口处的过渡部分可用圆弧连接,本设计中取4mm,因此出口直径为12.16mm。
4.2.5入口圆角半径r
在工作带模孔入口设有圆角半径r,可以防止低塑性合金在挤压时产生表面裂纹和减轻金属在进入工作带时所产生的非接触变形,同时也是为了减轻在高温下挤压时模子的入口棱角被压颓而很快改变模孔尺寸用的,以保证制品尺寸精度。
入口圆角半径的选用与被挤压金属的强度、挤压温度、制品断面尺寸有关。
对于铝合金不应有你入口圆角,而要求保持锐利的角度,一般取
。
本设计中入口圆角半径为0.5mm。
4.2.6模子的外形尺寸D和H
(1)模子的外圆直径和厚度主要是根据其强度和标准系列化来考虑的。
它与所挤压的型材类型、难挤压程度及合金的性质有关。
根据经验,对于棒材,其模子外径
等于
的(1.25~1.45)倍,
为一般挤压棒材的外接圆最大直径,通常等于挤压筒内径的(0.8~0.85)倍;即:
式中:
—为挤压筒内径,根据设计要求取200mm。
带入数据:
故本设计中D取200mm。
(2)模子厚度H应根据被挤压合金的变形抗力(即挤压力)的大小来考虑的。
在保证模具组件(模具、模垫、垫环等)有则够的强度的条件下,模具的厚度应尽量减薄,规格应尽量减少。
但为了安装和调试方便,模具厚度应尽可能系列化,便于管理和使用,一般模具的厚度按下述数值(单位:
mm)选用:
20,25,30,40,50,60,70,80,90,100
本设计中模子厚度H取50mm。
(3)模子的外形形状可分正锥体与倒锥体两种配合形式,正锥体用于型材棒材模,倒锥体一般用于管材模。
正锥体模在操作时顺挤压方向放模支持中,为了便于安分和取出,锥度一般为
的范围内。
如果角度小,人工取模困难,但是角度也不能太大,否则在模座靠紧挤压筒时,模子容易由模支持中弹出来。
本设计中模具的外形锥度
β为
。
(4)下图是用ProE绘制的挤压模实体图:
图4-2挤压模实体图
4.2挤压垫设计
挤压垫是用来防止高温的锭胚直接与挤压杆接触,消除其断面磨损和变形的工具。
垫片的外径比挤压筒内径小
值。
太大,可能形成局部脱皮挤压,从而影响制品质量,特别是挤压管材时不能有效的控制针的位置,以致造成管子偏心。
但是
也不能太小,以防止挤压筒内衬套摩擦加速其磨损。
因此,确定合适的
值对于提高生产效率,减少停机时间,减轻劳动强度,保护挤压筒和挤压轴前端,提高工具使用寿命都十分重要。
值与挤压筒内径有关:
卧式挤压机取0.5~1.5mm;立式挤压机取0.2mm脱皮挤压取2.0~3.0mm铸锭表面质量不佳的可选取更大些。
管材挤压垫的内孔不能太大,否则对针的位置起不到校正的作用。
还可能使被挤压的金属倒流抱住穿孔针。
垫的厚度可等于其直径的0.2~0.7倍。
故挤压垫直径取198mm,其厚度取50mm。
4.3挤压筒设计
挤压筒是所有挤压工具中最贵重的部件,是容纳锭坯,承受挤压杆传给锭坯的压力,并同挤压杆一起限制锭坯受压后只能从模孔挤出的挤压工具。
挤压筒一般由两层或三层以上的衬套以过盈热配合组装在一起构成的。
将挤压筒制成多层的原因是:
使筒壁中的应力