10级车辆2班液压与气压传动课程设计说明书.docx
《10级车辆2班液压与气压传动课程设计说明书.docx》由会员分享,可在线阅读,更多相关《10级车辆2班液压与气压传动课程设计说明书.docx(10页珍藏版)》请在冰豆网上搜索。
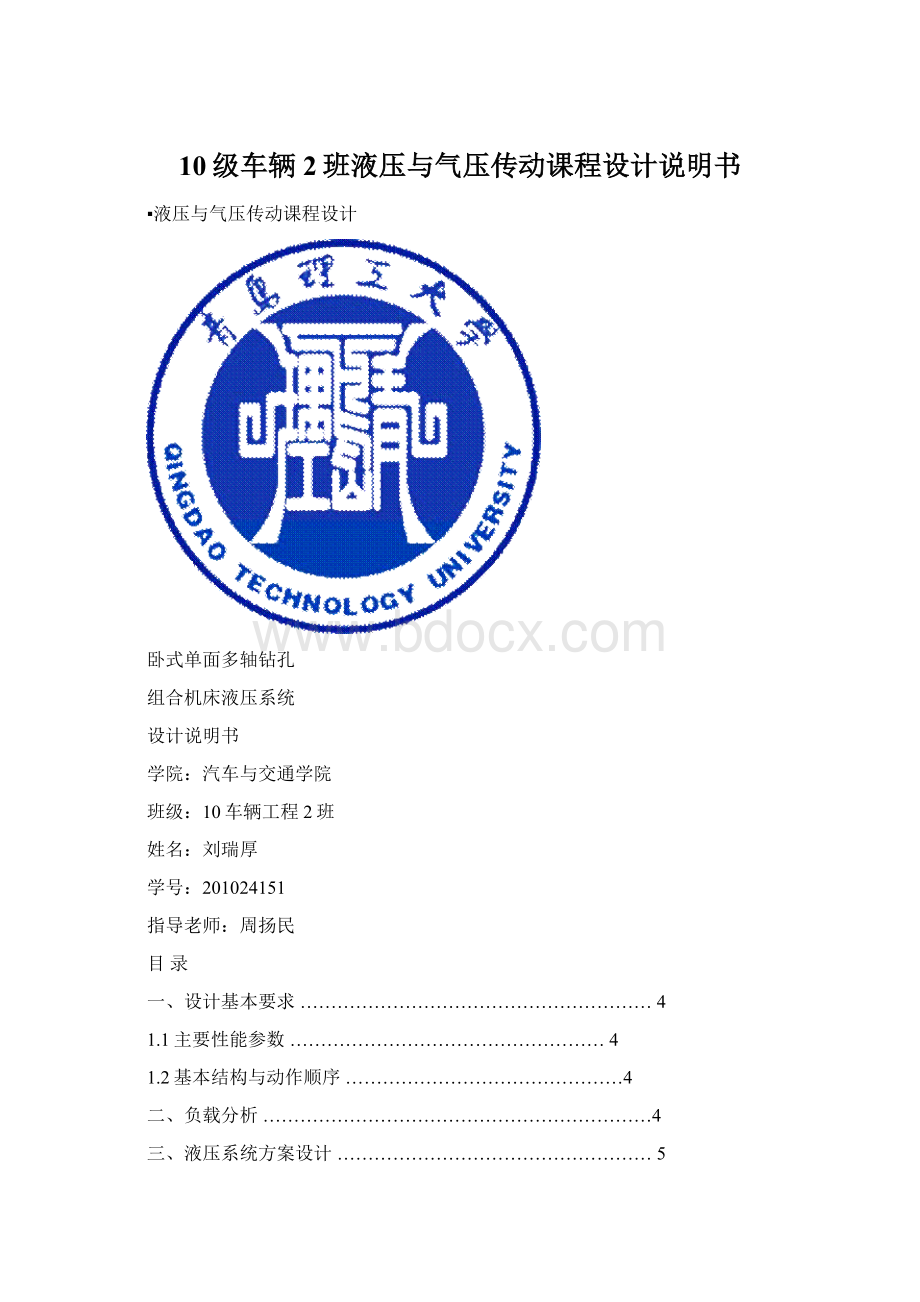
10级车辆2班液压与气压传动课程设计说明书
▪液压与气压传动课程设计
卧式单面多轴钻孔
组合机床液压系统
设计说明书
学院:
汽车与交通学院
班级:
10车辆工程2班
姓名:
刘瑞厚
学号:
201024151
指导老师:
周扬民
目录
一、设计基本要求…………………………………………………4
1.1主要性能参数……………………………………………4
1.2基本结构与动作顺序………………………………………4
二、负载分析………………………………………………………4
三、液压系统方案设计……………………………………………5
3.1确定液压泵类型及调速方式…………………………………5
3.2选用执行元件…………………………………………………5
3.3快速运动贿赂和速度换接回路…………………………………5
3.4换向回路的选择…………………………………………………5
3.5组成液压系统绘原理图…………………………………………5
四、液压系统的参数计算……………………………………………5
(一)液压缸参数计算…………………………………………………5
1.初选液压缸的工作压力…………………………………………5
2.确定液压缸的主要结构尺寸……………………………………5
3.计算液压缸各工作阶段的工作压力、流量和功率……………6
(二)液压泵的参数计算……………………………………………7
(三)电动机的选择…………………………………………………7
1.差动选择…………………………………………………………8
2.工进………………………………………………………………8
3.快退………………………………………………………………8
五、液压元件的选择…………………………………………………9
5.1液压阀及过滤器的选择…………………………………………9
5.2油管的选择………………………………………………………9
5.3油箱容积的确定…………………………………………………9
六、验算液压系统性能………………………………………………10
(一)压力损失的验算及泵压力的调整……………………………10
1.工进时的压力损失验算及泵压力的调整……………………10
2.快退时的压力损失验算及大流量泵卸载压力的调整…………10
3.局部压力损失…………………………………………………11
(二)液压系统的发热和温升验算…………………………………11
七、个人总结……………………………………………………………12
八、参考文献……………………………………………………………12
油压机液压系统设计说明书
一、设计基本要求
(一)、基本结构与动作顺序
卧式单面多轴组合机床主要由工作台、床身、单面动力滑台、定位夹紧机构等组成,加工对象为铸铁变速箱体,能实现自动定位夹紧、加工等功能。
工作循环如下:
工件输送至工作台—自动定位—夹紧—动力滑台快进—工进—快退—夹紧松开—定位退回—工件送出。
(其中工作输送系统不考虑)
(二)、主要性能参数
1.轴向切削力F1=24000N;
2.滑台移动部件质量m=510kg;
3.加减速时间△t=0.2s;
4.静摩擦系系数fs=0.2,动摩擦系数fd=0.1,采用平导轨;
5.快进行程l1=200mm;工进行程l2=100mm,工进速度30~50mm/min
6.工作台要求运动平稳,但可以随时停止运动,两运动滑台完成各自循环时互不干扰,夹紧可谓并能保证。
二、负载分析
负载分析中,暂不考虑回油腔的被压力,液压缸的密封装置产生摩擦阻力在机械效率中加以考虑。
因工作部件是卧式放置,重力的水平力为零,这样需要考虑的力有:
切削力,导轨摩擦力和惯性力。
导轨的正压力等于动力部件的重力,设导轨的静摩擦力Fs,动摩擦力为Fd,则
Fs=fsFN=0.2*15000=3000N
Fd=fdFN=0.1*15000=1500N
Fm=m*△V/△T=1531N
如果忽略切削力引起的颠覆力矩对导轨摩擦力的影响,并设液压缸的机械效率ηm=0.95,
则液压缸在各工作阶段的总机械负载可以算出,见表1-1.
表1-1液压缸各运动阶段负载
运动阶段
计算公式
机械负载F/N
起动
F=Fs/ηm
3157.9N
加速
F=(Fm+Fd)/ηm
3190.52N
快进
F=Fd/ηm
1578.94N
共进
F=(Fl+Fd)/ηm
29674.23N
快退
F=Fd/ηm
1578.94N
三、液压系统方案设计
1.确定液压泵类型及调速方式
参考同类组合机床,选用双叶泵供油·调速阀进油调速的开式回路,溢流阀作定压阀。
为防止钻孔通时滑台突然失去负载向前冲,回油路上设置背压阀,初定背压值Pb=0.8MPa
2.选用执行元件
因系统动作循环要求正向快进和工作,反向快退,且快进、快退速度相等,因此选用单活塞杆液压缸,快进时差动连接,无杆腔面积A1等于有杆面积A2的两倍。
3.快速运动回路和速度换接回路
根据本例的运动方式和要求,采用差动连接与双泵供油两种快速运动回路来实现快速运动。
既快进时,由大小泵同时供油,液压缸实现差动连接。
4.换向回路的选择
本系统对换向的平稳性没有严格的要求,所以选用电磁换向回路。
为便于实现差动连接,选用了三位五通换向阀。
为提高换向的位置精度,采用死档板和压力继电器的行程终点返程控制
5.组成液压系统绘原理图
将上诉所选定的液压回路进行组合,并根据要求作必要的修改补充,即组成如图所示的液压系统图。
为便于观察调整压力,在液压泵的进口处、背压阀和液压缸无杆腔进口处设置测压点,并设置多点压力表,这样只需一个压力表即能观测各点压力。
电磁铁动作顺序
IY
2Y
3Y
快进
+
-
-
工进
+
-
+
快退
-
-
-
停止
-
+
-
四、液压系统的参数计算
(一)液压系统的参数计算
1.初选液压缸的工作液压力
参考同类型组合机床,初定液压缸的工作压力为P1=40*105Pa
2确定液压缸的主要结构尺寸
本例要求动力滑台的快进|、快退速度相等,现采用活塞杆固定的单杆式液压缸。
快进时采用差动连接,并取无杆腔有效面积A1等于有杆腔有效面积A2的两倍,即A1=2A2,为了防止在钻孔钻通时滑台突然向前冲,在回油路中装有背压阀,按表8-1,初选被压Pb=8*105Pa
由表1-1可知最大负载为工进阶段的负载F=29674.23N
A1=F/P1-0.5Pb=8.24cm²
D=10.24cm
由A1=2A2可知活塞杆直径
d=0.707D=7.24CM
按国标将所计算的D与d值分别园整到相近的标准直径,以便采用标准的密封转置
D=10cmd=7cm
按标准直径算出
A1=3.14*D²/4=78.5cm²
A2=3.14*(D²-d²)=40cm²
按最低工进速度验算液压缸尺寸,查产品样本,调速阀最小稳定流量qmin=0.05L/min,因工进速度v=0.05m/min为最小速度,则由式,
A≥qmin/vmin=
本例A1=6.36cm2》10cm2,满足最低速度的要求。
3.计算液压缸各工作阶段的工作压力、流量和功率
根据液压缸的负载图和速度图以及液压缸的有效面积,可以算出液压缸工作过程各阶段的压力、流量和功率,在计算工进时背压按pb=5x105Pa代入计算公式和计算结果列于下表中。
工作循环
计算公式
负载F
进油压力pa
回油压力pb
所需流量
输入功率P
N
Pa
Pb
L/min
kw
差动快进
Pj=
1578.94
9.3×105
11.5×105
23.1
0.358
工进
29674.23
41.9×105
8×105
0.942
0.022
快退
1578.94
13.8×105
5×105
24
0.552
(二)液压泵的参数计算
由表二可知工进阶段液压缸压力最大,若取进油路总压力损失∑△p=,压力继电器可靠动作需要压力差为5×105Pa,则液压泵最高工作压力可按式算出
Pp=Pl+∑△p+5×105=(41.9+5+5)×105=51.9×105Pa
因此泵的额定压力可取Pr》(1.1×0.942+2.5)L/min=3.536L/min,快进快退时液压缸所需的最大流量是23L/min,则泵的总流量为qp=1.1×24L/min=26.4L/min,即大流量泵的流量qp2=qp-qp1=(26.4-3.536)=22.86L/min
根据上面计算的压力和流量,查产品样本,选用YB-E/6型的双联叶片泵,该泵额定压力为16MPa,额定转速1000r/min。
(三)电动机的选择
系统为双泵供油系统,其中小泵1的流量qp1=(4×10-3/60)m3/s=0.0667×10-3m3/s,大泵流量q2=(12×10-3/60)m3/s=0.2×10-3m3/s。
差动快进、快退时两个泵同时向系统供油;工进时,小泵向系统供油,大泵卸载。
下面分别计算三个阶段所需要的电动机功率P。
1.差动快进
差动快进时,大泵2的出口压力油经单向阀11后与小泵1汇合,然后经单向阀2,三位五通阀4进入液压缸大腔,大腔的压力P1=Pj=9.3×105Pa,查样本可知,小泵的出口压力损失△p1=9×105Pa,大泵出口到小泵出口的压力损失△p2=9×105Pa,于是计算可得小泵的出口压力Pj1=13.8×105Pa(总效率=0.5),大泵出口压力Pj1=15.3×105Pa(总效率=0.5)
电动机效率
2.工进
考虑到调速阀所需最小压力差△p1=5×105Pa。
压力继电器可靠动作需要压力差△p2=5×105Pa.因此工进时小泵的出口压力Pj1=P1+△p1+△p2=51.9×105Pa。
而大泵的卸载压力取Pp2=2×105Pa。
(小泵的总效率=0.565,大泵的总效率=0.3)。
电动机效率
3.快退
类似差动快进分析知:
小泵的出口压力pp1=17.2×105Pa(总效率=0.5);大泵出口压力pp2=18.7×105Pa(总效率=0.5)电动机效率
综合比较,快退时所需功率最大。
据此查样本选用Y901-6异步电动机。
功率kw
额定转速r/min
电流A
效率%
净重kg
1.1
910
3.15
73.5
25
五、液压元件的选择
1.液压阀及过滤器的选择
根据液压阀在系统中的最高工作压力与通过该阀的最大流量,可选出这些元件的型号及规格。
本例中所有阀的额定压力都为63×105Pa,额定流量根据各阀通过的流量,确定为10L/min,25L/min和63L/min,所有元件的规格型号列于表三中,过滤器按液压泵额定流量的两倍选取吸油用线隙式过滤器。
序号
元件名称
最大通过流量/L.min-1
型号
1
2
3
4
5
6
7
8
9
10
11
12
13
14
15
16
17
18
19
20
2.油管的选择
根据选定的液压阀的连接油口尺寸确定管道尺寸。
液压缸的进、出油管按输入、排出的最大流量来计算。
由于本系统液压缸差动连接快进快退时,油管内通油量最大,选用内经为20mm.
3.油箱容积的确定
中压系统的油箱容积一般取液压泵额定流量的5~7倍,本设计取6倍,故油箱容积为
V=7×23=161L
六、验算液压系统性能
(一).压力损失的验算及泵压力的调查
1.工进时管路中流量仅为0.942L/min因此流量很小,所以沿程损失和局部损失都很小,可忽略不计,这时进油路只考虑调速阀的压力损失△P1=5×105Pa,回油路上只有背压阀的流量损失。
小流量泵的调整压力应等于工进时液压泵的工作压力p1加上加上进油路的压差△P1,并考虑压力续电器动作需要,则Pp=P1+△P1+5×105Pa=(41.9+5+5)=51.9×105Pa
2.快退时的压力损失验算及大流量泵卸载压力调整
因快退时,液压缸无杆腔的回油量是进油量的两倍,其压力损失比快进时要大,因此必须计算快退时的进油路与回油路的压力损失,以便确定大流量泵的卸载压力。
已知快退时进油路和回油路油管长度均为L=1.8m,油管直径d=0.02m,通过的流量进油路q1=23L/min=0.384×10-3m³,回油路q2=46L/min==0.768×10-3m³,。
液压系统选用N32号液压油,假定最低工作温度为15℃,由手册可得运动的粘度ν=1.5st=1.5cm²/s,油的密度ρ=900kg/m³,液压系统元件采用集成块式的配置形式。
雷诺数Re=(V×d)/ν,其中V表示平均流速,d表示内径,ν表示粘度。
而V=q/A,q表示流量,A表示面积。
所以雷诺数Re=(4×q)/(3.14×d×ν)=(1.2732×q)/(d×ν)。
则进油路的雷诺数Re=(1.2732×0.384×10-3×104)/(20×10ˆ-3×1.5)=163〈2300
回油路雷诺数Re=(1.2732×0.768×10-3×104)/(20×10-3×1.5)=326〈2300
(2)沿程压力损失由公式△Pf=(64×L×ρ×g×V²)/(Re×d×2g)=(64×L×ρ×V²)/(Re×d²)算的。
其中进油路V=(4q1)/(3.14×d²)=1.22m/s
进油路的压力损失由公式得∑Pf1=0.24×105pa
在回油路,流速为进油路的两倍,即V=2.44m/s。
则在回油路的压力损失∑Pf2=0.47×105pa
(二)液压系统的发热和升温验算
在整个工作循环中,工进阶段占用的时间最长,所以主要大热应该在共进阶段,所以按共进时验算系统的升温。
共进时液压泵的输入功率P1=746w
共进时液压缸的输出功率P2=f×v=29674.23×0.12/60=59.3w
系统的发热效率φ=P1-P2=746-59.3=686.7w=0.6867Kw
已知油箱的容积V=7×23=161L,由公式(9-22)可知散热面积为A=0.065³≈1.92m²
假定通风良好,取油箱散热系数Cr=0.015Kw/(m²·℃)
由公式△T=φ/(Cr×A)=0.6867/(0.015×1.92)≈23.8℃
假设环境温度T2=25℃,则平衡温度
T1=T2+△T=25+23.8℃=48.8℃
七、个人总结
通过本次液压课程设计,让我很好的锻炼了理论联系实际,与具体项目、课题相结合开发、设计产品的能力。
既让我们懂得了怎样把理论应用于实际,又让我们懂得了在实践中遇到的问题怎样用理论去解决。
回顾起此课程设计,至今我仍感慨颇多,从理论到实践,在这段日子里,可以说得是苦多于甜,但是可以学到很多很多的东西,同时不仅可以巩固了以前所学过的知识,而且学到了很多在书本上所没有学到过的知识。
通过这次课程设计使我懂得了理论与实际相结合是很重要的,只有理论知识是远远不够的,只有把所学的理论知识与实践相结合起来,从理论中得出结论,才能真正为社会服务,从而提高自己的实际动手能力和独立思考的能力。
在设计的过程中遇到问题,可以说得是困难重重,但可喜的是最终都得到了解决。
同时,我也发现了设计知识上的许多不足并进行了及时补充,学会了如何发现问题、解决问题,学会了如何利用手头的资料进行知识的扩充,学会了团队配合精神。
设计过程中,对团队精神的进行了考察,让我们在合作起来更加默契,在成功后一起体会喜悦的心情。
果然是团结就是力量,只有互相之间默契融洽的配合才能换来最终完美的结果。
此次设计我明白了思路即出路,有什么不懂不明白的地方要及时请教或上网查询,只要认真钻研,动脑思考,动手实践,就没有弄不懂的知识,收获颇丰。
八、参考文献
1.《液压与气压传动工程手册》.李壮云主编.电子工业出版社.2007
2.《液压与气压传动系统应用与维修》.罗洪波.曹坚主编.北京理工大学出版社.2009
3.《机械制造工艺及设备设计手册》.李云主编.北京.机械工业出版社
4.《液压系统设计图》.周士昌主编.北京.机械工业出版社
5.《机械设计零件手册》.液压分册