生产运作管理 实验报告.docx
《生产运作管理 实验报告.docx》由会员分享,可在线阅读,更多相关《生产运作管理 实验报告.docx(13页珍藏版)》请在冰豆网上搜索。
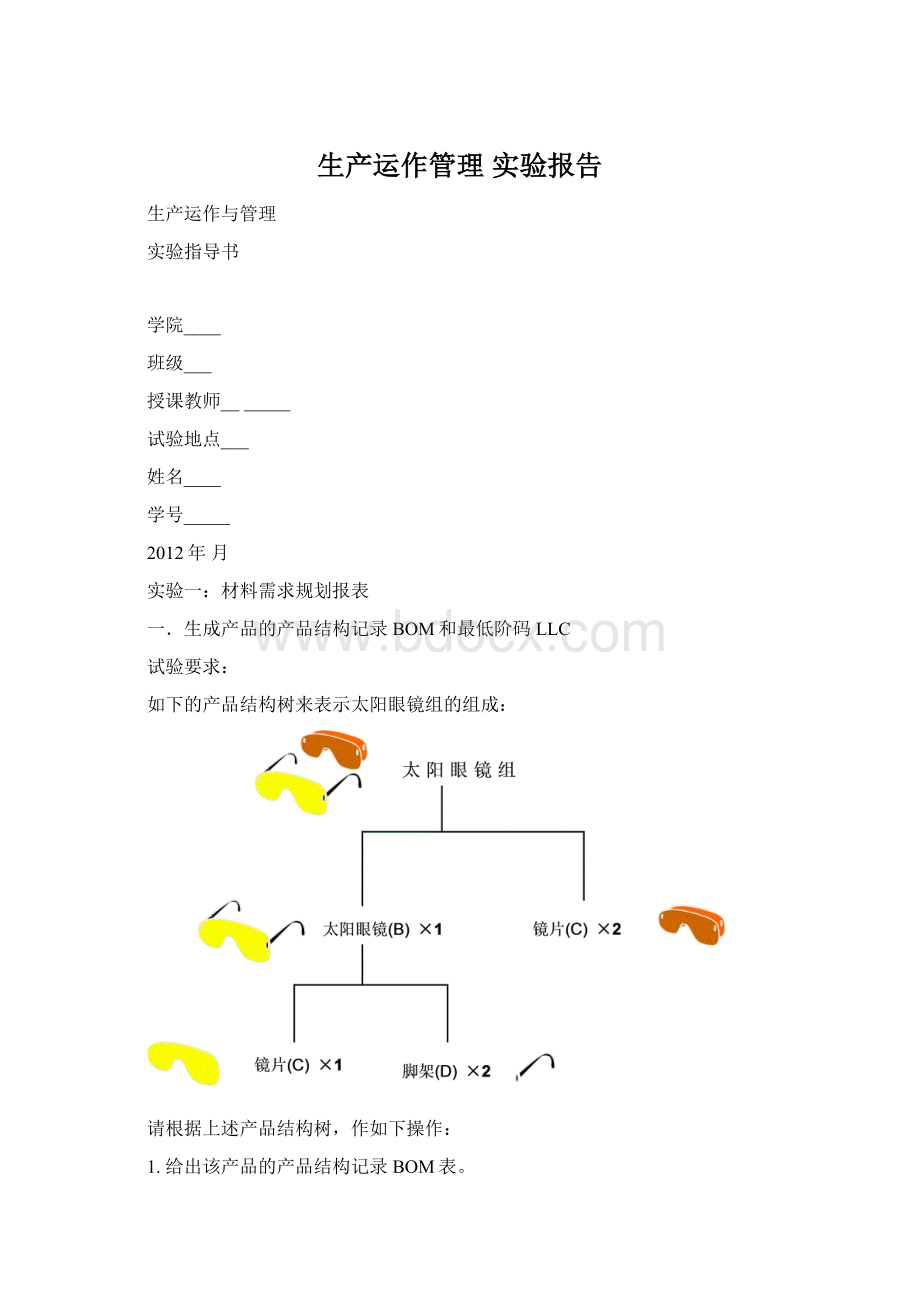
生产运作管理实验报告
生产运作与管理
实验指导书
学院____
班级___
授课教师_______
试验地点___
姓名____
学号_____
2012年月
实验一:
材料需求规划报表
一.生成产品的产品结构记录BOM和最低阶码LLC
试验要求:
如下的产品结构树来表示太阳眼镜组的组成:
请根据上述产品结构树,作如下操作:
1.给出该产品的产品结构记录BOM表。
2.生成该产品的最低阶码LLC。
试验结果:
最低阶码
件号
最低阶码
A
0
B
1
C
2
D
2
材料表(BOM)
父件
子件
单位用量(QP)
A
B
1
A
C
2
B
C
1
B
D
2
\
物料需求计划MRP的处理
已知:
某公司生产多种产品,需要对不同的产品进行材料需求规划。
现在有其中的X、Y产品,其材料主文件(ItemMaster)如表1所示,其产品结构记录(BOM)如表2所示,其主生产排程项目之需求如表3所示。
同时,根据表2,我们可以获得如表4所示的最低码价表。
材料主文件(ItemMaster)
件号
安全库存SS
批量
前置时间LT
X
150
400
1
Y
100
180
1
A
0
180
2
B
0
800
2
C
0
800
3
D
0
400
2
E
0
600
2
表1.
产品结构记录(BOM)
父件
子件
单位用量(QP)
X
B
2
X
C
1
B
D
0.25
Y
A
1
Y
C
1
A
B
1
A
E
1
表2.
生产排程项目之需求
期别
1
2
3
4
5
6
7
8
9
10
11
12
X
100
400
300
200
100
200
300
100
100
400
300
200
Y
100
200
100
200
100
200
100
200
100
200
100
200
表3.
最低阶码
父件
最低阶码
X
0
Y
0
A
1
B
2
C
1
D
3
E
2
表4.
完成从“项目X”到“项目E”7张材料需求规划的空白报表。
在每张表格中,根据具体的情况,对独立需求、已分配量、计划收到三个手工输入的变量设置了必要的参数。
上述由人工干预而获得的数据,在报表中,以红色斜体标识。
表格中的LT、SS、LS数值来源于材料主文件(ItemMaster)。
而现有库存的起始数值为经统计后由人工填入的各组件的在库量。
试验要求:
1.根据产品结构记录(BOM),生成产品X和Y的产品结构。
产品结构用Word文档撰写,采用“MS组织结构图”对象工具来完成。
(格式如下)
2.根据已知的材料主文件(ItemMaster)、产品结构记录(BOM)、主生产排程项目之需求、最低码价表,生成完整的“项目X”到“项目Y”的材料需求规划报表。
其独立需求的数值直接调用主生产排程项目之需求。
3.根据已知的材料主文件(ItemMaster)、产品结构记录(BOM)、主生产排程项目之需求、最低码价表,结合上述生成的项目X”到“项目Y”的材料需求规划报表,产生完整的“项目A”到“项目E”5张材料需求规划报表。
4.材料需求规划报表中的所有数据均需通过相应的公式来获得,没有可以直接键入数值的单元格。
在公式的引用中,本实验题用到如下几个函数:
max()、if()、offset(),请通过查阅Excel的HELP文件获得相关的解释。
5.实验的结果直接完成在实验2_2.xls文件中。
请在进行实验前,先备份文件。
试验原理:
总需求=独立需求+相关需求+已分配量
现有库存=上期库存+计划收到+计划投产-总需求
净需求量的计算:
“上期库存+计划收到-总需求”的值和“安全库存”比较,如果小于“安全库存”,说明就有净需求。
计划投产的计算:
有“净需求”就会产生“计划投产”。
把计算求得的“净需求”和“批量”值进行比较,取其中较大的值作为实验中的“计划投产”。
计划交付的计算
根据“提前期”,使用OFFSET函数来获得“计划交付”值。
1.计算毛需求G(t)
毛需求=独立需求+非独立需求/相关需求
=独立需求+上层物料计划订单的投入数量×物料单中每一个组装件的用量
2.计算净需求N(t)
预计可用量=现有库存量+计划入库数量-安全库存
即A(t)=H(t-1)+S(t)-SS
式中A(t)——第t周预计可用量
H(t-1)——第t周初现有库存量,亦即第t-1周末的实际库存量
S(t)——第t周计划收到以前的订货量
SS——安全库存量
净需求=毛需求量-(现有库存量+计划入库数量-安全库存)
即N(t)=G(t)-A(t)=G(t)-[H(t-1)+S(t)-SS]
3.产生计划订单
当净需求存在时,产生物料的计划生产订单和计划采购订单。
计划订单包括两种:
计划订单收到(数量、时间)和计划订单发出(数量、时间)。
确立计划订单的下达日期和数量分为三步:
(1)确立计划订单收到量P(t)。
当净需求量≤生产批量或采购批量,即N(t)≤Q时,
计划订单收到量=生产批量或采购批量,即P(t)=Q;
当净需求量>生产批量或采购批量,即N(t)>Q时,
计划订单收到量=净需求量,即P(t)=N(t)。
当有计划订单收到时,第t+1期的库存预计可用量为A(t+1)=A(t)+P(t)-G(t)。
(2)考虑提前期,计算何时下达订单。
计划订单发出量=计划订单收到量;
计划订单发出时间=计划订单收到时间-提前期。
即R(t-LT)=P(t)
式中R(t-LT)——第t-LT周计划订单发出量,亦即第t-LT周时应该投入的量;
LT——生产提前期或采购提前期。
(3)利用计划订单计算同一周期更低一层相关项目的毛需求。
4.计算其他层的需求
上层物料的计划订单产生了对下层物料的需求。
计算下层物料的需求时首先考虑是否还有其他要处理的需求,其次考虑层次码,如果存在需求分解则返回第一步进行毛需求计算。
否则停止处理。
试验结果:
项目X的MRP(0阶)
LT=
1
LS=
400
SS=
150
周
1
2
3
4
5
6
7
8
9
10
11
12
独立需求
100
400
300
200
100
200
300
100
100
400
300
200
相关需求
0
0
0
0
0
0
0
0
0
0
0
0
已分配量
0
0
0
0
0
0
0
0
0
0
0
0
总需求
100
400
300
200
100
200
300
100
100
400
300
200
计划收到
400
0
40
0
0
0
0
0
0
0
0
0
现有库存
200
500
500
240
440
340
540
240
540
440
440
540
340
净需求量
0
50
0
110
0
10
0
10
0
110
10
0
计划投产
0
400
0
400
0
400
0
400
0
400
400
0
计划交付
400
0
400
0
400
0
400
0
400
400
0
0
项目Y的MRP(0阶)
LT=
1
LS=
180
SS=
100
周
1
2
3
4
5
6
7
8
9
10
11
12
独立需求
100
200
100
200
100
200
100
200
100
200
100
200
相关需求
0
0
0
0
0
0
0
0
0
0
0
0
已分配量
0
0
0
0
0
0
0
0
0
0
0
0
总需求
100
200
100
200
100
200
100
200
100
200
100
200
计划收到
180
0
40
0
0
0
0
0
0
0
0
0
现有库存
180
260
240
180
160
240
220
120
100
180
160
240
220
净需求量
0
40
0
120
40
60
0
180
100
120
40
60
计划投产
0
180
0
180
180
180
0
180
180
180
180
180
计划交付
180
0
180
180
180
0
180
180
180
180
180
0
项目A的MRP(1阶)
LT=
2
LS=
180
SS=
0
周
1
2
3
4
5
6
7
8
9
10
11
12
独立需求
0
0
0
0
0
0
0
0
0
0
0
0
相关需求
180
0
180
180
180
0
180
180
180
180
180
0
已分配量
0
0
0
0
0
0
0
0
0
0
0
0
总需求
180
0
180
180
180
0
180
180
180
180
180
0
计划收到
180
0
40
0
0
0
0
0
0
0
0
0
现有库存
180
180
180
40
40
40
40
40
40
40
40
40
40
净需求量
0
0
0
140
140
0
140
140
140
140
140
0
计划投产
0
0
0
180
180
0
180
180
180
180
180
0
计划交付
0
180
180
0
180
180
180
180
180
0
0
0
项目C的MRP(1阶)
LT=
3
LS=
800
SS=
0
周
1
2
3
4
5
6
7
8
9
10
11
12
独立需求
10
10
10
10
10
10
10
10
10
10
10
10
相关需求
580
0
580
180
580
0
580
180
580
580
180
0
已分配量
0
0
0
0
0
0
0
0
0
0
0
0
总需求
590
10
590
190
590
10
590
190
590
590
190
10
计划收到
180
0
40
0
0
0
0
0
0
0
0
0
现有库存
500
90
80
330
140
350
340
550
360
570
780
590
580
净需求量
0
0
470
0
450
0
250
0
230
20
0
0
计划投产
0
0
800
0
800
0
800
0
800
800
0
0
计划交付
0
800
0
800
0
800
800
0
0
0
0
0
项目B的MRP(2阶)
LT=
2
LS=
800
SS=
0
周
1
2
3
4
5
6
7
8
9
10
11
12
独立需求
0
0
0
0
0
0
0
0
0
0
0
0
相关需求
800
180
980
0
980
180
980
180
980
800
0
0
已分配量
0
0
0
0
0
0
0
0
0
0
0
0
总需求
800
180
980
0
980
180
980
180
980
800
0
0
计划收到
180
0
40
0
0
0
0
0
0
0
0
0
现有库存
400
580
400
260
260
80
700
520
340
160
160
160
160
净需求量
220
0
540
0
720
100
280
0
640
640
0
0
计划投产
800
0
800
0
800
800
800
0
800
800
0
0
计划交付
800
0
800
800
800
0
800
800
0
0
0
0
项目E的MRP(2阶)
LT=
2
LS=
600
SS=
0
周
1
2
3
4
5
6
7
8
9
10
11
12
独立需求
相关需求
180
0
180
180
180
0
180
180
180
180
180
0
已分配量
0
0
0
0
0
0
0
0
0
0
0
0
总需求
180
0
180
180
180
0
180
180
180
180
180
0
计划收到
180
0
40
0
0
0
0
0
0
0
0
0
现有库存
100
360
0
220
180
180
0
180
180
180
180
180
0
净需求量
0
0
140
0
0
0
180
0
0
0
0
0
计划投产
0
0
600
0
0
0
600
0
0
0
0
0
计划交付
600
0
0
0
600
0
0
0
0
0
0
0
项目D的MRP(3阶)
LT=
2
LS=
400
SS=
0
周
1
2
3
4
5
6
7
8
9
10
11
12
独立需求
相关需求
200
0
200
200
200
0
200
200
0
0
0
0
已分配量
0
0
0
0
0
0
0
0
0
0
0
0
总需求
200
0
200
200
200
0
200
200
0
0
0
0
计划收到
180
0
40
0
0
0
0
0
0
0
0
0
现有库存
200
380
0
240
200
200
0
200
200
0
0
0
0
净需求量
0
0
160
0
0
0
200
0
0
0
0
0
计划投产
0
0
400
0
0
0
400
0
0
0
0
0
计划交付
400
0
0
0
400
0
0
0
0
0
0
0
实验二
一、实验名称
生产流水线AGV小车、自动堆垛机的操作
二、实验目的
1.了解加工流水线的运作
2.观察AGV小车的行程路线及原理
3.学会操作自动堆垛机进行入库、出库
三、实验内容
1.开启流水线开关,产品在链轮的带动下向前运动,当到达工作台时,加工人员可以踩下踏板使产品停止运动并取下产品进行加工,加工完毕后再放回流水线进行后续加工。
在这个过程中时间的把握很重要,时间停顿太久会对生产线造成干扰甚至破坏。
2.流水加工完成后,产品到达末端,对AGV小车的到达进行判断上,并装夹在小车上,小车按照设定的路线行进到堆垛机处准备入库。
3.在计算机上设置使堆垛机复位,选择入库命令,输入产品的条形码,根据货架所标的号码选择入库位置的序号,生成入库程序后由自动堆垛机执行,把产品放到所设位置入库。
同样的方法也可以实现产品的出库。
流水线生产提高了生产效率及设备利用率,堆垛机的使用代替了劳动力,将科技运用到实际生活中实现自动化,安全性得到了提高。