晶体硅太阳能电池表面PECVD淀积SiN减反射膜工艺研究讲解.docx
《晶体硅太阳能电池表面PECVD淀积SiN减反射膜工艺研究讲解.docx》由会员分享,可在线阅读,更多相关《晶体硅太阳能电池表面PECVD淀积SiN减反射膜工艺研究讲解.docx(15页珍藏版)》请在冰豆网上搜索。
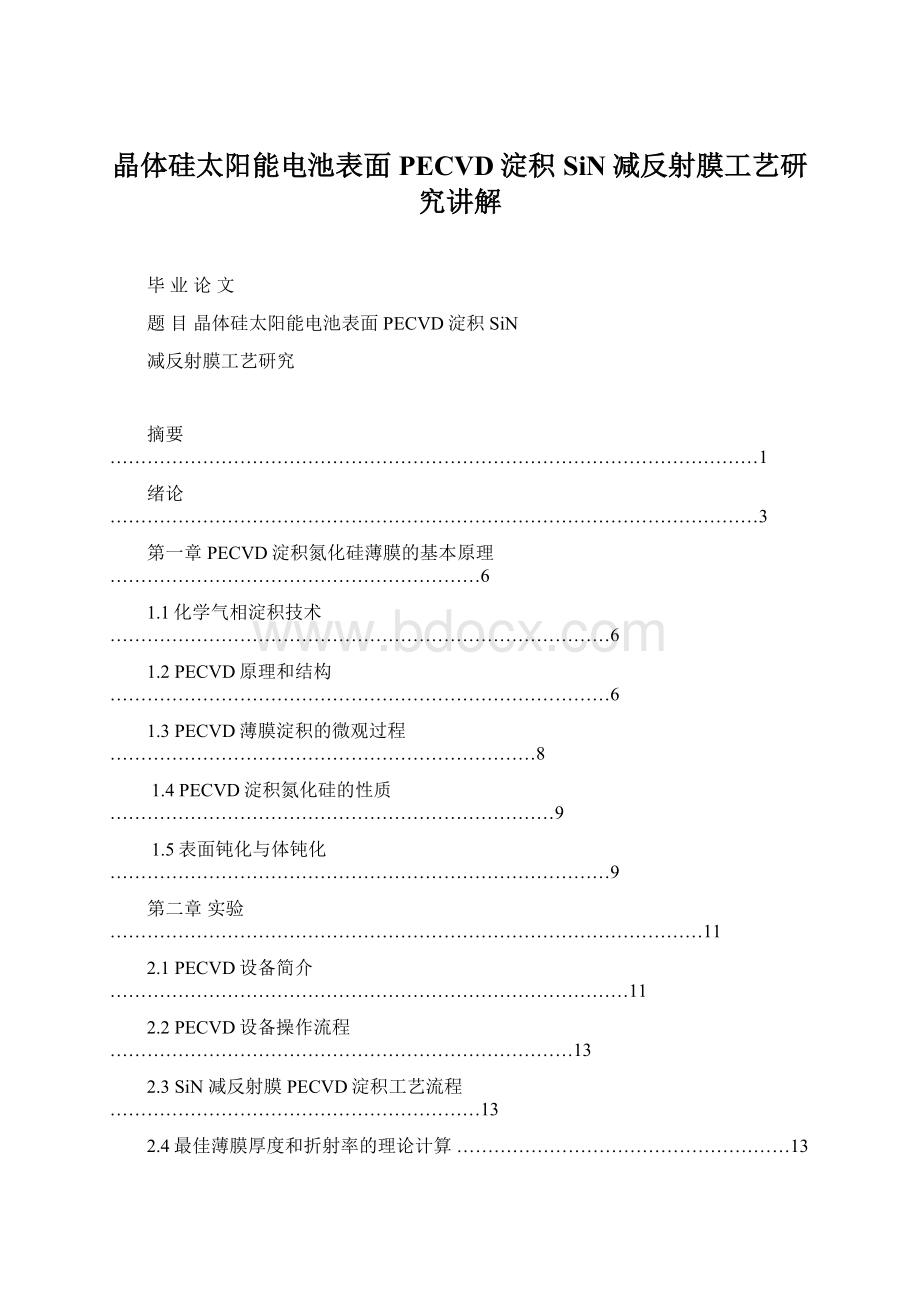
晶体硅太阳能电池表面PECVD淀积SiN减反射膜工艺研究讲解
毕业论文
题目晶体硅太阳能电池表面PECVD淀积SiN
减反射膜工艺研究
摘要……………………………………………………………………………………………1
绪论……………………………………………………………………………………………3
第一章PECVD淀积氮化硅薄膜的基本原理……………………………………………………6
1.1化学气相淀积技术………………………………………………………………………6
1.2PECVD原理和结构………………………………………………………………………6
1.3PECVD薄膜淀积的微观过程……………………………………………………………8
1.4PECVD淀积氮化硅的性质………………………………………………………………9
1.5表面钝化与体钝化………………………………………………………………………9
第二章实验……………………………………………………………………………………11
2.1PECVD设备简介…………………………………………………………………………11
2.2PECVD设备操作流程…………………………………………………………………13
2.3SiN减反射膜PECVD淀积工艺流程……………………………………………………13
2.4最佳薄膜厚度和折射率的理论计算………………………………………………13
2.5理论实验总结……………………………………………………………………………15
结束语……………………………………………………………………………………………16
参考文献…………………………………………………………………………………………17
晶体硅太阳能电池表面PECVD淀积SiN减反射膜工艺研究
摘要
等离子增强化学气相淀积氮化硅减反射薄膜已经普遍应用于光伏工业中,其目的是在晶体硅太阳能电池表面形成减反射薄膜,同时达到了良好的钝化作用。
氮化硅膜的厚度和折射率对电池性能都有重要的影响。
探索最佳的工艺条件来制备最佳的薄膜具有重要意义。
本课题是利用Roth&Rau的SiNA设备进行淀积氮化硅薄膜的实验,介绍了几种工艺参数对薄膜生长的影响,获得了生长氮化硅薄膜的最佳工艺条件,制作出了高质量的氮化硅薄膜。
实验中使用了椭偏仪对样品进行膜厚以及折射率的测量。
关键词:
等离子增强化学气相淀积,氮化硅薄膜,太阳能电池,光伏效应,钝化
ABSTRACT
SiNFilmplasma-enhancedchemicalvapordeposition(PECVD)iswidelyusedinP-Vindustryasanantireflectionthinfilmonthesurfaceofcrystalsiliconsolarcell.Inadditionthisprocesstakesadvantageofanexellentpassivationeffect.BoththethicknessandrefractiveindexoftheSiNfilmmakeimportantinfluencestotheperformanceofsolarcells.Soitisveryimportanttofindthebestprocessparameterstodepositthebestfilm.Inthispaper,theexperimentofSiNfilmdepositionwascompletedwiththeequipmentnamedSiNAproducedbyRoth&Rau.Theinfluenceoftheparameterstothegowthofthefilmwasintroducedbasedontheexperiment,andthebestparameterstoproducethetop-qualitySiNfilmwereobtainted.TheSpectroscopicellipsometrywasusedtotestthethicknessandrefractiveindexofthesamplesduringtheexperiment.
Keywords:
PECVD,SiNfilm,solarcell,photovoltaiceffect,passivation
第一章绪论
从2003年开始,全球化石能源的缺乏引发了能源价格不断攀升,可再生能源也因此得到了更多的重视,太阳能光伏行业迎来了发展的春天。
1.1太阳能光伏产业发展现状和未来
人类历史上从未有如2009年底哥本哈根会议那样的事件,会使“节能减排”、“低碳”等字眼如此深入人心,全球经济的发展方向和导航标也已然转向了低碳经济。
太阳能作为一种清洁的可再生能源,是未来低碳社会的理想能源之一,当下正越来越受到世界各国的重视。
CSIA最新研究报告称[1],目前太阳能电池主要分为单晶硅电池、多晶硅电池和薄膜电池三种。
单晶硅电池技术成熟,光电转换效率高,但其生产成本较高,技术要求高;多晶硅电池成本相对较低,技术成熟,但光电转换效率相对较低;而薄膜电池成本低,发光效率高,但目前其在技术稳定性和规模生产上均存在一定的困难。
随着技术的进步,未来薄膜电池会有更好的发展前景在各国政府的大力支持下,太阳能光伏产业得到了快速的发展。
2006年至2009年,太阳能光伏电池产量的年均增长率为60%。
由于受到2008年金融危机的影响,2009年前两个季度光伏电池产量的增长速度有所放缓,但随着2009年下半年市场需求的复苏,2009年全年的太阳能电池产量达到了10431MW,比2008年增长42.5%。
目前太阳能光伏发电的成本大约是燃煤成本的11—18倍,因此目前各国光伏产业的发展大多依赖政府的补贴,政府的补贴规模决定着本国的光伏产业的发展规模。
目前在政府的补贴力度上,以德国、西班牙、法国、美国、日本等发达国家的支持力度最大。
2008年,西班牙推出了优厚的光伏产业补贴政策,使其国内光伏产业出现了爆发式发展的态势,一度占据了世界光伏电池产量的三分之一强。
2009年德国光伏组件安装量高达3200MW,占全球安装量的50.4%。
目前,中国已形成了完整的太阳能光伏产业链。
从产业布局上来看,国内的长三角、黄渤海、珠三角及中西部地区已形成各具特色的区域产业集群,并涌现出了无锡尚德、江西赛维、天威英利等一批知名企业。
截止到2009年年底,全球太阳能电池累计安装量已达到24.5GWp,而中国太阳能电池产量为9300MW,占全球总产量的40%以上,已成为为全球太阳能电池生产第一大国。
1.2晶体硅太阳能电池技术的发展
晶体硅太阳电池是光伏行业的主导产品[2],占市场份额的90%,尤其是多晶硅太阳电池的市场份额已远超过单晶硅电池的市场份额,自从六十年代太阳能电池作为能源应用于宇航技术以来,太阳能电池的技术得到非常迅速的发展,单晶硅太阳能电池的转换效率已接近25%(单晶硅电池理论上极限转换效率为27%),多晶硅太阳能电池的转换效已接近近20%。
由于太阳能光伏电池的高制造成本使得它的发展和应用受到了一定的影响[3]。
而如果太阳能光发电的成本能够下降到10美分/千瓦时,将有巨大的经济效益!
所以现在所有的光伏企业以及研究机构都在努力研究更加先进的太阳能电池制作工艺和寻找更好更加廉价的电池材料,以达到提高转化效率,降低成本的目的。
对晶体硅电池的研究应遵循以下工艺原则,即低成本、大批量和高效化。
薄片化具有双重目的。
薄片化可以降低成本,同时薄片电池可以降低载流子的体内复合从而提高光电转化效率。
目前硅片厚度已普遍地从370μm降到240μm,很多厂家已减薄到220μm,仍能保持较高的成品率。
现在已开始试制200μm的薄硅片产品。
所以不断减薄硅片厚度,同时又保持高的成品率、产率和转化效率可以大幅降低成本。
预计到不久的将来薄片电池可以做到100μm[4]。
大片化符合大批量的原则,目前多数光伏企业已能批量生产六英寸和八英寸晶圆硅片。
而根据预测,中国有可能在未来156×156(mm)单晶硅片生产上,占有让国际光伏圈内不可小视的一席之地。
因为中国有批量生产8吋单晶炉设备的厂家,很多硅片厂家也在上8吋单晶生产线,这些都将大大促进中国光伏产业的发展。
然而,在次展望中国光伏产业发展的未来,道路坎坷但前景不可估量。
通过设计优化太阳电池生产工艺和电池结构,已经研制出了许多高效电池。
其中包括PESC电池(发射结钝化太阳电池)、表面刻槽绒面PESC电池、背面点接触电池(前后表面钝化电池)和PERL电池(发射结钝化和背面点接触电池)。
由这些电池设计和工艺制造出的电池的转换效率均高于20%,其中保持世界记录(24.7%)的单晶硅和多晶硅电池(19.8%)的转换效率均是由著名的澳大利亚新南威尔斯大学设计的PERL电池实现的。
但由于工艺复杂,应用于工业生产成本过高。
以硅片为载体的光伏电池制造技术,其理论极限效率为29%。
近年来由于一系列新技术的突破,硅太阳能电池转换效率产业化水平单晶16%~18%、多晶15%~17%,按目前的晶体硅电池效率路线图与电池技术,提升效率的难度已经非常大。
因此有人预言硅电池的市场生命周期,但产品市场生命力的决定因素是其性价比,就如半导体集成电路一样近一个世纪了仍然离不开硅基,晶体硅太阳能电池作为光伏发电主要材料的现状不会改变,市场主导地位将继续延续!
其特征将会是向着高效率、大尺寸、超薄化、长寿命方向发展。
随着我们对半导体材料与光伏技术研究的不断深入,必将会不断诞生一些突破性的技术来巅覆传统、提升太阳能电池的效率、降低系统发电成本,实现光伏发电从补充能源向主流能源的跃进!
只是以前这些技术都由国外企业与机构产生。
可以预见通过中国广大“光伏人”的努力,今后这些革命性的技术突破将会在我们中国本土企业与科研机构中产生!
1.3本课题的主要内容
目前众多光伏企业都采用PECVD的方法在太阳能电池表面淀积一层氮化硅减反射薄膜。
这除了可以大大减少光线的反射率外,它还起到了良好的表面钝化和体钝化效果,达到了提高电池的光电转换效率和短路电流的目的。
而氮化硅稳定的化学性质起到了抗腐蚀和阻挡金属离子的目的,能够为电池提供长期的保护。
所以,高质量的氮化硅薄膜对提高电池性能和质量都有重要作用。
本课题主要讨论其中的PECVD淀积氮化硅减反射薄膜工艺。
然后通过实验的方法对淀积薄膜的工艺条件进行研究,根据实验结果对工艺条件进行分析比较,从而获得最佳的工艺参数。
第一章PECVD淀积氮化硅薄膜的基本原理
用PECVD的方法在晶体硅太阳能电池表面淀积氮化硅减反射薄膜因为具有良好的减反射作用,同时达到了良好的表面及体钝化效果。
其低温工艺又有效的控制了生产成本,而且保证了较高的产率(15000片/12h)。
这些优点使得它受到了大多数光伏企业的青睐。
1.1化学气相淀积技术
半导体工艺中要使用到许多薄膜淀积技术[5]。
根据不同的用途,需要使用不同的方法来淀积薄膜。
如栅极氧化膜和场氧化膜均需要用热氧化的方式,因为只有通过热氧化的方式才能提供具有最低界面陷阱密度的高品质氧化膜。
介电薄膜主要用来做分立器件或集成电路中金属层绝缘隔离和保护层。
用化学气相淀积的二氧化硅或氮化硅可以用来做介质膜。
CVD(ChemicalVaporDeposition)技术是使用加热、等离子体或紫外线等各种能源,使气态物质经化学反应(热解或化学合成)形成固态物质淀积在衬底上的方法。
它与真空蒸发和溅射技术并列,是应用较为普遍的一种薄膜淀积技术。
它有以下特点:
(1)淀积温度低;
(2)可以淀积各种电学和化学性质都符合要求的薄膜;
(3)均匀性好;
(4)操作简便,适于大量生产;
几种比较流行的CVD技术的基本工艺条件对比如下:
APCVD—常压CVD,700-1000℃;
LPCVD—低压CVD,~750℃,~0.1mbar;
PECVD—300-450℃,~0.1mbar(1bar=1×105Pa)。
通过对比可以看出PECVD的一个基本特征是实现了薄膜淀积工艺的低温化(<450℃)。
因此带来的好处是:
(1)节省能源,降低成本;
(2)提高产能;
(3)减少了高温导致的硅片中少子寿命衰减。
1.2PECVD原理和结构
PECVD技术原理是利用低温等离子体作能量源,样品置于低气压下辉光放电的阴极上,利用辉光放电(或另加发热体)使样品升温到预定的温度,然后通入适量的反应气体,气体经一系列化学反应和等离子体反应,在样品表面形成固态薄膜。
PECVD方法区别于其它CVD方法的特点在于等离子体中含有大量高能量的电子,它们可以提供化学气相淀积过程所需的激活能。
电子与气相分子的碰撞可以促进气体分子的分解、化合、激发和电离过程,生成活性很高的各种化学基团,因而显著降低CVD薄膜淀积的温度范围,使得原来需要在高温下才能进行的CVD过程得以在低温实现。
微波PECVD是在400℃,1.5×10-1mbar的低温低压情况下,利用高频(频率是2.45GHz)电磁辐射使反应气体等离子体化,等离子体可看成由高能电子20eV、低能粒子0.3eV和中性气体0.05eV组成。
从宏观上看这种等离子体的温度不高,但其内部却处于受激发状态,其电子能量足以使气体分子键断裂,它们可以提供化学气相淀积过程所需要的激活能Ea。
电子与气相分子的碰撞可以促进气体分子的分解、化合、激发和电离过程,生成活性很高的各种化学基团,因而显著减低了CVD薄膜淀积的温度范围。
SiN薄膜的淀积过程发生的化学反应式如下:
3SiH4→SiH3
+SiH22-+SiH3-+6H+(3.1)
2NH3→NH2-+NH2-+3H+(3.2)
总反应式:
3SiH4+4NH3→Si3N4+12H2↑(3.3)
如今,PECVD技术已经发展到比较成熟的阶段,出现了基于不同等离子体激发原理的PECVD设备。
国内已经生产出了较为稳定的可用于生产和研究的设备。
以下介绍两种基本的PECVD设备结构[8],[9]。
直接式—基片位于一个电极上,直接接触等离子体(激发源:
低频放电10-500kHz或高频13.56MHz),如图1.1所示。
直接式PECVD易于产生均匀浓度的等离子体,有利于沉积均匀的薄膜,且具有低的针孔密度,适合于制作集成电路工艺的介电层以及器件保护层。
图1.1直接式PECVD结构
间接式—基片不接触激发电极(激发源:
2.45GHz微波激发等离子),如图1.2所示。
间接式PECVD的特点:
在微波激发等离子的设备里,等离子产生在反应腔之外,然后由石英管导入反应腔中。
在这种设备里微波只激发NH3,而SiH4直接进入反应腔。
间接PECVD的沉积速率比直接的要高很多,这对大规模生产尤其重要。
图1.2间接式PECVD结构
1.3PECVD薄膜淀积的微观过程
如图1.3所示,工艺腔中的等离子基团先在电池表面形成沉积核心,接着其他离子由于电荷吸引等作用在硅片表面不断的聚集、生长,这种过程的同时还伴随着薄膜扩张,兼并等过程的发生,最后形成均匀的SiNx减反射膜。
成膜过程经历了成核阶段,成长阶段,扩张阶段和成形阶段。
图1.3薄膜生长微观过程
1.4PECVD淀积氮化硅的性质
在太阳能电池表面淀积减反射薄膜可以大大减少光线反射。
SiO2、TiO2、SiNx等都可以作为减反射膜[6]。
传统太阳能电池是用TiO2作为减反射膜的,其折射率虽然接近晶体硅太阳电池最佳光学减反射膜的理论值,但是它对半导体没有表面钝化功能,SiO2的折射率(1.4)太低,光学减反射效果不好,而且不能起到阻挡Na+离子的作用。
与之相比,SiNx具有以下优势:
优良的表面钝化效果;
高效的光学减反射性能;
低温工艺(有效降低成本);
含氢SiNx:
H可以对衬底提供体钝化;
卓越的抗氧化和绝缘性能,良好的阻挡钠离子、掩蔽金属和水蒸汽扩散的能力;
良好的化学稳定性,除氢氟酸和热磷酸能缓慢腐蚀外,其它酸与它基本不起作用。
1.5表面钝化与体钝化
太阳能电池是一种少数载流子工作器件,当光照射到一个P型半导体的表面上,光在材料内的吸收产生电子与空穴对。
在这种情况下,电子是少数载流子,它的寿命定义为从其产生到其与空穴复合之间所生存的时间。
少数载流子在电池内的寿命决定了电池的转换效率。
因此要提高电池的转换效率,就必须设法减少少数载流子在电池内的复合,从而增加少数载流子的寿命。
影响少数载流子寿命的因素有:
体内复合、表面复合和电极区复合。
正常的SiNx的Si/N之比为0.75,即Si3N4。
但是PECVD淀积氮化硅的化学计量比会随工艺不同而变化,Si/N变化的范围在0.75-2左右。
除了Si和N,PECVD的氮化硅一般还包含一定比例的氢原子,即SixNyHz或SiNx:
H。
而H可与Si形成H-Si键,所以可通过H钝化来降低表面复合和体内复合。
减少电极区的复合可采用将电极区的掺杂浓度提高,从而降低少数载流子在电极区的浓度。
减少载流子在此区域的复合。
如图1.4显示半导体表面的悬挂键[7]。
由于晶体结构在表面突然中断,因此在表面区域产生了许多局部的能态,或是产生-复合中心,这些称为表面态(surfacestates)的能态,会大幅度增加在表面区域的复合率。
图1.4半导体表面悬挂键
由于PECVD氮化硅中含有大量的氢原子,可以很好的填补表面悬挂键,从而达到良好的表面钝化效果,大大降低了表面态密度,从而显著增加短路电流。
因为半导体内部总是存在许多缺陷,所以存在一定的内部悬挂键。
而在后面的烧结工艺中,氮化硅减反射膜中存在的大量的氢被驱赶到半导体内部,复合掉体内的悬挂键,从而达到了很好的体钝化效果。
1981年,Hezel和Schorner首先将等离子增强化学气相淀积(PECVD)SiNx:
H薄膜的技术引入晶体硅太阳电池的制作工艺中,随后便成功地开发出了转化效率为15%~15.8%的MIS-IL太阳电池。
自此,用PECVD法沉积的SiNx:
H作为晶体硅太阳电池的光学减反射及钝化膜,引起了人们极大的兴趣,出现了PESC、PERC、PERL等新型结构的高效太阳电池。
最近几年的发展说明,PECVD法淀积的SiNx:
H是获得高效晶体硅太阳电池最有效的手段之一。
第二章实验
本实验利用SINA系统进行了薄膜淀积实验,并使用SE400型椭偏仪对薄膜的厚度和折射率进行测量,实验所用硅片为6英寸抛光单晶硅片。
2.1PECVD设备简介
图2.1为Roth&RauAG生产的SINA系统,它是专门利用PECVD过程来淀积氮化硅薄膜的系统[10]。
SiNA系统是一个模块化的在线生产系统,主要用于太阳电池减反射薄膜的淀积。
图2.1SINA系统外观
图2.2SINA系统示意图
图2.2为SINA系统示意图。
SINA系统有三个腔体,分别是进料腔,反应腔(包括预热、淀积和冷却三部分)和出料腔。
各腔体直接有闸门阀隔开。
除了腔体,其它主要部分包括真空泵系统,真空监测系统,气体供应系统,等离子体源(微波发生器),冷却水系统,硅片传送系统和衬底加热系统等。
薄膜淀积发生在工艺腔中,图2.3为工艺腔的结构图。
工艺腔包括气源供给装置,共轴外部等离子体传导,石英管和内部导体,磁控系统。
载着硅片的石墨框从工艺腔上部流过。
石英管内部导体两端连接微波源,石英管起到保护导体的作用。
磁控系统可降低沿石英管方向的等离子体浓度不均匀性,还起到了在气源波动时稳定等离子体浓度和降低远离微波源处的等离子体浓度衰减。
使得薄膜更加均匀[11]。
图2.3工艺腔结构图
2.2PECVD设备操作流程
(1)开启设备总电源开关,主控微机自动启动,SINA主控程序自动运行;各系统自动复位。
(2)开启真空泵系统,将反应腔抽至9.9×10-3mbar;
(3)打开总反应气源阀(SiH4和NH3),打开氮气供应阀;
(4)打开冷却水供应阀;
(5)打开参数输入界面,并输入工艺参数,并在实验中改变需要改动的参数;
(6)点击START按钮,系统自动运行;
(7)装片完成并确认后,石墨框被自动放置到进片传送带上。
打开跟踪界面,屏幕显示如图2.2,由此可以跟踪观察硅片的位置;
(8)镀膜完成后,石墨框自动传至卸片台,卸片完成并确认后,石墨框通过返框传送带自动传回装片台。
2.3SiN减反射膜PECVD淀积工艺流程
由人工将硅片装入6×6的石墨框中,放片时应注意片子的位置,不能翘片、斜片等,否则会引起镀膜不均匀。
石墨框在传送带的带动下进入进料腔,接着一号门关闭,真空泵将进料腔抽成真空,红外加热器(加热器1)对硅片迅速加热到400℃,加热时间十几秒。
因为是迅速预加热,加热器1的温控不太稳定,有5℃的浮动。
硅片达到预定温度后,进入沉积腔的第一部分——加热腔,二号腔门关闭,进料腔充氮气到一个大气压,等待下一批硅片的进入。
在加热腔中,温度稳定在400℃的值保持不变,加热器2为普通加热装置,但控温系统好,使硅片保持恒温。
工艺腔中,充满着被功率3000W微波辐射电离的反应气体,如前所述,等离子体中充满着活性基团。
在石墨框移动进入到工艺腔后,沉积反应在硅片上发生,氮化硅薄膜慢慢沉积形成。
镀膜完成以后,石墨舟载着镀膜完成的硅片进入冷却腔,用18~22℃冷却水冷却硅片,稳定薄膜性质。
三号腔门打开,石墨舟进入处于处于真空状态的出料腔。
在出料腔中,冷却水继续对硅片降温,以便在出料后人工取片。
三号门关闭后,真空泵对腔体充氮气至一个大气压后,四号腔门打开出片。
在下料区,人工取片,装盒,流入下一个工序。
经过以上工艺步骤,可以在硅片上做出均匀的呈深蓝色减反膜。
图2.4为在石墨框中的镀膜电池片。
图2.4石墨框中的镀膜电池片
2.4最佳薄膜厚度和折射率的理论计算
图2.5中显示了四分之一波长减反射膜的原理[12]。
从薄膜下表面返回到薄膜上表面的反射光与从上表面的反射光相位相差180度,所以前者在一定程度上抵消了后者。
这样就减少了光能的反射部分能量而更多的能量则进入到半导体中。
假设光线垂直入射,分析如下:
由于反射存在半波损失,所以上、下表面的反射光光程差为:
=(2n1d1+λ/2)-λ/2=2n1d1(2.1)
两光干涉相消时:
=2n1d1=(2k+1)λ/2(k=0,1,2……)(2.2)
取k=0时,得
n1d1=λ/4(2.3)
图2.5薄膜的减反射与增反射对比原理图
如图2.6所示,太阳光在波长λ=600nm处能量最强,所以减反射膜参数应该使600nm的
图2.5薄膜的减反射与增反射对比原理图
光线反射最小。
另外,折射率反映了薄膜的致密性和结构均匀性,同时也影响了薄膜的减反射能力。
根据公式n12=n0n2(n0=1为空气折射率,n2=3.85为本征硅折射率),解得氮化硅薄膜折射率n1=1.92。
但是考虑到组件生产时封装材料的影响,n1取2.02。
将λ和n1的值代入到式2.3中,可以得到厚度d1=75nm,实际中取70nm~80nm。
图2.6AM1.5的能量分布
2.5理论实验总结
根据2.4节的理论最佳减反射薄膜参数(厚度d=70~80nm,折射率n=2.02),通过理论实验得到较优化的工艺参数