POY工艺.docx
《POY工艺.docx》由会员分享,可在线阅读,更多相关《POY工艺.docx(14页珍藏版)》请在冰豆网上搜索。
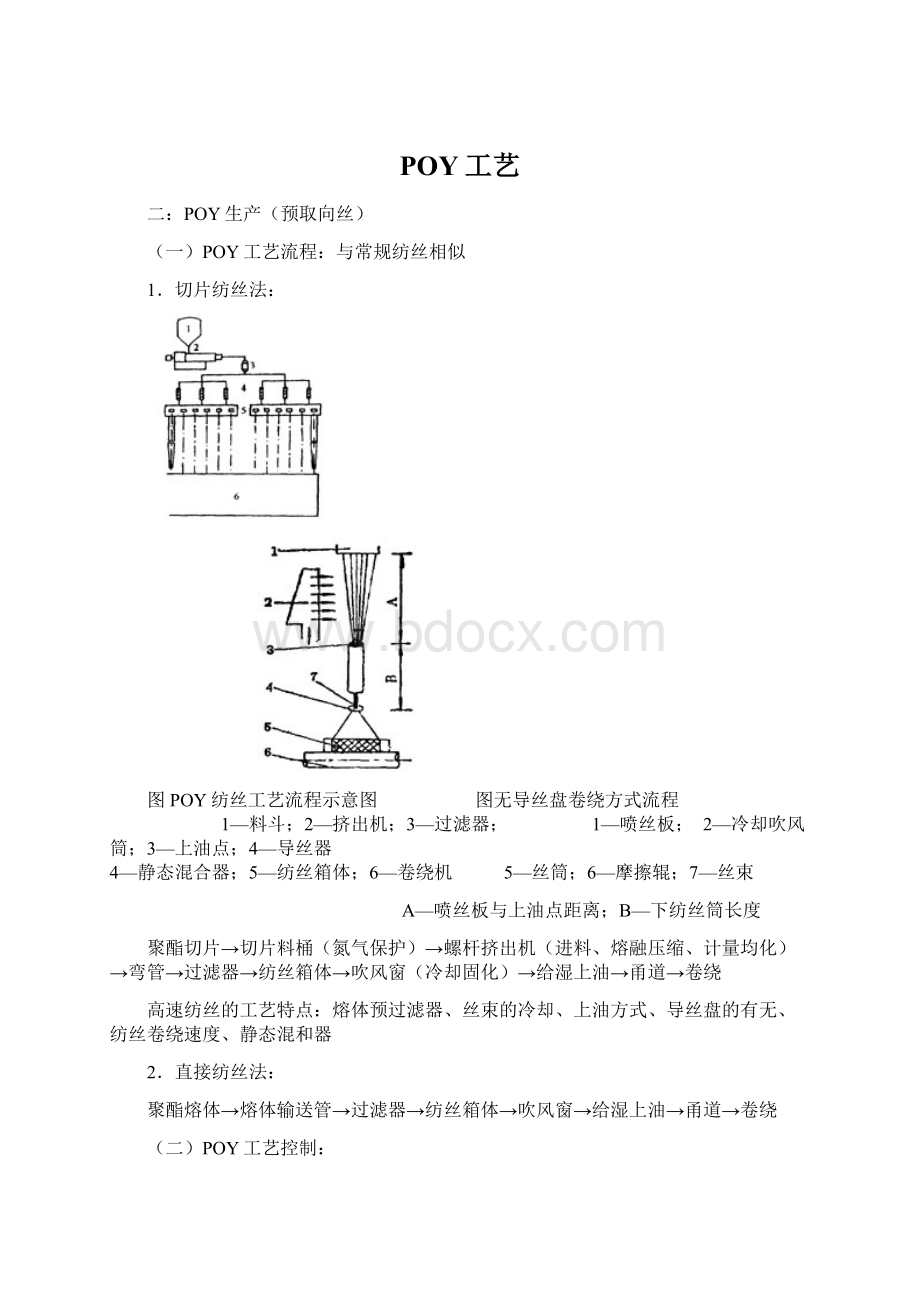
POY工艺
二:
POY生产(预取向丝)
(一)POY工艺流程:
与常规纺丝相似
1.切片纺丝法:
图POY纺丝工艺流程示意图 图无导丝盘卷绕方式流程
1—料斗;2—挤出机;3—过滤器; 1—喷丝板; 2—冷却吹风筒;3—上油点;4—导丝器
4—静态混合器;5—纺丝箱体;6—卷绕机 5—丝筒;6—摩擦辊;7—丝束
A—喷丝板与上油点距离;B—下纺丝筒长度
聚酯切片→切片料桶(氮气保护)→螺杆挤出机(进料、熔融压缩、计量均化)→弯管→过滤器→纺丝箱体→吹风窗(冷却固化)→给湿上油→甬道→卷绕
高速纺丝的工艺特点:
熔体预过滤器、丝束的冷却、上油方式、导丝盘的有无、纺丝卷绕速度、静态混和器
2.直接纺丝法:
聚酯熔体→熔体输送管→过滤器→纺丝箱体→吹风窗→给湿上油→甬道→卷绕
(二)POY工艺控制:
1.对聚酯质量的要求:
*切片的粉屑:
<0.1%;粉屑↑→纺丝喷丝板粘板↑——筛滤除去
*凝胶:
聚酯热降解→纺丝断头↑,深色丝(D丝)——聚合时避免氧渗入(高温、氧作用,金属是聚酯降解的催化剂)
*高结晶聚合物:
高结晶聚合物→熔点↑→纺丝断头——高过滤、螺杆温度提高
*TiO2:
TiO2→聚酯降解催化剂→→→→→→→→→→→→→→
→不溶于三甘醇清洗剂→熔体过滤器滤芯难洗涤→→加入量0.3%
*二甘醇:
<0.76%;二甘醇↑→聚酯熔点↓、分子量↓、黄光↑
2.对切片质量要求(干燥):
*干燥切片含水率:
0.005%;
含水率↑→高速纺丝熔体水解↑(高速纺丝温度=常规纺温度+5~15℃)
→气泡丝→毛丝或断头(高速纺丝速度高,使气泡丝毛丝→或断头)
→飘丝
*干燥切片特性粘度:
0.65±0.1dL/g;
*干燥切片温度:
干燥风温度<185℃;干燥时切片的实际温度<160℃保证除去水分;保证
特性粘度不至于下降过大(可采用加大干燥风量和降低干燥风湿度来提高
干燥效率)
3.纺丝温度:
280--300℃(纺丝速度高→纺线上拉伸倍数↑→要求熔体流动性好
→纺丝停留时间↓→要求熔体流动性好)
纺丝温度↑→聚合物热分解↑→可纺性↓
纺丝温度↓→熔体流变性和均匀性↓→毛丝、断头↑
螺杆挤出机的加热划分成五区或六区,螺杆进料段(第一、二区)、压缩段(第三区)、计量段(第四、五、六区)。
表不同切片的纺丝温度
切片
特性粘度(dL/g)
纺丝温度(℃)
最高纺丝速度
(m/min)
毛丝
断头
可纺性
一区
二区
三区
四区
五区
六区
箱体
熔体温度
A
B
C
0.64
0.69
0.92
285
290
295
290
295
300
292
298
310
292
298
310
292
298
310
292
——
292
298
310
291
295
304
>6000
>6000
5600
很少
无
少
无
无
无
好
好
尚好
4.螺杆挤出机出口压力:
熔体经预过滤器后的压力>7MPa→减去熔体管道压力损失→保证计量泵前的工作压力>2MPa
5.预过滤器压力:
*材质:
粗细海砂(或金刚砂)+金属过滤网
若干层目数不同的金属丝网
烧结金属网
*排列:
上层(粗目);中层(细目);底层少量粗目(支撑作用)——过滤好,可防止熔体对细砂的冲击
*影响:
新的或经清洗过的过滤器入口压力=过滤器出口压力→过滤时间延长→过滤器前后压差=7MPa→清洗过滤器
6.组件压力:
*起初压力:
高压纺丝40MPa,中压纺丝14--30MPa
*终压力:
起初压力+7~8MPa→更换组件
7.喷丝孔:
*孔径:
0.15—0.3mm,均可纺丝
孔径↓(泵供量不变)→熔体细流剪切速度↑、喷丝速度↑→熔体细流表观粘度↓,喷丝头拉伸比↓→高速纺丝有利
→喷丝板孔堵塞↑→换组件率↑
表高速纺丝成品丝单丝纤度与喷丝孔直径的关系
单丝纤度(dtex)
4.4
3.3
1.7
1.1
喷丝孔直径(mm)
0.30
0.27
0.25
0.20
*喷丝板孔径、孔数、泵供量对纺丝工艺和成品丝质量的影响比常规纺小:
喷丝头拉伸倍数决定纤维性质,而高速纺丝的纺速比常规纺高2—3倍,故喷出速度对上述影响小
*喷丝板孔分布排列:
——条件:
喷丝板孔密度小于4.0孔/cm2;喷丝板最小孔距大于4.5mm;喷丝板冷却气流方向4mm宽度内所包含的最多孔数小于10孔;
——设置该条件的原因:
高速纺速大于3000m/min,若喷丝孔板排列较密,尽管加大冷却风速,也会造成丝条迎风和背风侧单丝冷却不匀,产生毛丝和断头,条干不匀;
8.冷却吹风条件:
*吹风速度:
0.3~0.7m/s(比常规纺高)
风速↑→空气湍动↑→飘丝↑→初生纤维条干不匀↑
→冷却效果↑(高速纺卷绕张力大,提高风速不会引起丝束摆动)
风速↓→丝条凝固速度↓→飘丝↑→初生纤维条干不匀↑
风速对预取向丝的双折射、强度、伸长影响小;卷绕性、条干不匀率影响大
*吹风温度:
18~25℃,(在15~35℃,风温对丝条张力和成品丝质量几乎不影响;)
但吹风温度波动→丝条条干不匀↑、染色均匀性↓、毛丝↑、断头↑
*相对湿度:
65%
相对湿度↑→丝条在纺丝时的静电↓、飘丝↓
→比热容和热容量↑→热吸收量↑→冷却风在吸收同样热量时温升低→冷却吹风温度稳定
→操作条件差、设备锈蚀
*密闭区(无风区):
设置密闭区原因:
喷丝板→熔体细流(高分子弹性记忆)→挤出胀大(细流脆弱)→经不起气流冲击
位置:
喷丝板下10cm距离内(比常规纺减少一半)
喷丝板下5~15cm距离内(短纤维)
9.上油:
高速纺纺丝张力大,不利于卷绕成型,故丝条提前集束上油,以减少纺丝张力
*方式:
油嘴(油嘴上油兼有上油和导丝,省去油盘传动机构,避免油剂外溢、腐蚀机台;但油泵发生故障时,丝束脱油不易发现)
*位置:
纺丝吹风窗下(距喷丝板150~170cm)
距离短→冷却不充分→丝束染色不匀、毛丝断头多、不能稳定卷绕
距离长→丝束张力过大→生头操作难、条干不匀、卷装硬
*上油量:
0.3~0.5%
上油量↓→纤维表面不能均匀形成油膜→摩擦阻力↑→集束性↓→毛丝↑
10.导丝盘的有无
*导丝盘作用:
调节卷绕张力(降低或增加),形成良好卷装
常规纺:
纺丝卷绕速度低→丝束张力<正常卷绕张力→设置导丝盘增加卷绕张力
高速纺:
纺丝卷绕速度高→丝束张力>正常卷绕张力→设置导丝盘降低卷绕张力
无导丝盘高速纺:
纺丝吹风窗下上油→丝束抱成一束→高速行走时与空气摩擦↓→→→丝束张力↓→解决了无导丝盘卷绕的技术问题
→毛丝↓→断头↓
11.纺丝速度(卷绕速度):
3000——3600m/min
纺丝速度↑→>3000m/min→纤维力学性能较好
→1000~2000m/min,产量直线上升→>2500m/min,产量缓慢上升>3000m/min,产量增加微小>3600m/min,产量不再上升
→卷绕机保养费用↑
→卷绕丝取向度↑→剩余拉伸倍数↓→改善了后拉伸条件→防止了较大的加捻张力而造成的毛丝、断头→成品丝均匀性↑
→>4000m/min→取向诱导大量结晶(要避免)
12.高速卷绕成型:
(1)卷绕筒子形式:
直边形(10——20kg)、双锥形
(2)不良卷装:
螺旋边、蛛网丝、表面凹凸、叠圈、卷绕硬度过高或过低、卷绕角过大或过小
图不良卷绕
1—表面凹凸;2—凸肩;3—卷绕角
4—螺旋边;5—蛛网丝;6—叠圈
①螺旋边(鸡爪):
卷绕筒子端面出现开放性螺旋线——后加工退卷不良
高速卷绕→筒管受力→卷绕筒子丝的外层惯性力比内层大→外层制动速度比内层慢→丝层间沿离心力方向产生滑移→卷绕筒子端面出现开放性螺旋线
②蛛网丝:
卷绕筒子端面出现,部分丝脱离正常的卷绕轨迹,由弧变成弦。
——毛丝、断头
③表面凹凸:
卷绕筒子外表面凹凸不平(凸肚:
筒子中间高,两端低;凸肩:
反之)
凸出部分硬度高,凹下部分硬度低。
——条干不匀率、染色不匀率
④叠圈:
卷绕筒子端面,圆圈状高出其它卷绕部分的丝——后加工退卷不良、塌边
⑤卷绕角过大或过小:
卷绕角↑↑→凸肩↑、蛛网丝↑
卷绕角↓↓→凸肚↑、塌边↑
(3)正常卷绕角:
6°35ˊ~7°05ˊ
(4)影响高速卷绕的主要因素:
常规纺:
油剂、卷绕张力、欠喂率
高速纺:
油剂、卷绕张力、超喂率
①卷绕油剂:
油膜强度高、单丝间抱合力好(适应大卷装)、高平滑性、渗透性好(高速时能瞬间均匀附着在丝束的表面))
②卷绕张力:
影响预取向丝的卷绕筒子成型
*范围:
0.1~0.3cN/dtex
33~82.5dtex细特丝(0.2~0.3cN/dtex);82~220dtex(0.15~0.25cN/dtex)
*影响:
卷绕张力↑→卷绕筒子成型不良(螺旋边、蛛网丝、凸边、表面凹凸)、筒子硬度↑↑(后加工退卷困难)
卷绕张力↓→卷绕筒子成型不良(筒子卷绕密度↓↓→脱圈)
*调节:
有导丝盘:
导丝盘圆周速度与卷绕速度差值
无导丝盘:
改变集束点位置;辅助槽辊对摩擦辊的超喂率
③卷绕角:
在卷绕筒子上两层相邻丝条之间的交角,卷绕角6.5~7°
*影响:
卷绕角↓↓→丝束间趋于平行排列堆砌→在摩擦辊接触压力下→丝束向两端移动→筒子端面凸,甚至塌边
卷绕角↑↑→丝束向中间移动→卷绕筒子凸肩,且网络丝↑
④超喂率:
有导丝盘:
导丝盘对摩擦辊的超喂率
无导丝盘:
辅助槽辊对摩擦辊的超喂率
*表示:
超喂率%=
*范围:
1~14%(常用5~8%)
*影响:
超喂率↑→凸肩↑、蛛网丝↑
超喂率↓→凸肚↑、内层塌边
⑤横动导丝器的运动速度(基速)及其干扰振幅、周期:
卷绕筒子的丝层的卷绕=筒子旋转+横动导丝器往复运动
*范围:
干扰振幅、周期:
±1~1.5%,周期3~5s(防止卷绕时相邻丝层间的重叠)
*影响:
干扰振幅↓→卷绕筒子成型不良(脱圈)
干扰振幅↑→蛛网丝↑
⑥摩擦辊与卷绕筒子的接触压力:
卷绕筒子的旋转=摩擦辊与筒子间的摩擦力推动
*摩擦力:
绕底层丝(摩擦系数小);绕满卷丝(摩擦系数大)
*接触压力:
整个卷绕操作分三步:
第一步:
空筒管加速,升速到规定速度,其接触压力(14~16)×105Pa;
第二步:
绕底层丝,降压至(8~10)×105Pa;
第三步:
正常卷绕,升压至(11~13)×105Pa;
*接触压力调节:
压缩空气调节。
四个压力表。
整个卷绕机头压缩空气供气压力、卷绕筒管轴供气压力:
可表示6×105Pa以上
压缩空气压力(两个):
(3~4)×105Pa
(三)高速纺丝卷绕机:
1.设备制造商:
德国巴马格Barmag、日本村田Murata、美国杜邦DuPort、美国婆罗涅Bouligny、意大利凡尔利西那Vallesina、日本帝人、上海二纺机——德国巴马格合资、苏州——巴马格
2.设备特点:
①螺杆挤出机:
卧式螺杆,直径75~200mm,“LTM”销钉型混合头螺杆(Barmag公司)
②熔体预过滤器:
连续熔体过滤器CPF,立式烛形过滤器,过滤精度高(20~25μm),过滤器由两个过滤室组成,三通阀分别与熔体管道接通,可定期切换三通阀,交替使用过滤室。
当过滤器的前后压差=50×105~70×105,则切换过滤室→组件使用周期提高4—6倍(2—3月)
③纺丝箱体:
Barmag公司的SP23型号,2位/箱体,4~8块喷丝板/位
④计量泵:
双碟泵(两个单泵并联,,一根传动轴及一套传动系统,一个入口,两个出口,一个泵可供两个喷丝板的定量输送)
⑤油嘴喷射上油:
氧化铝陶瓷,喷嘴中间有一深2mm、直径0.7mm的小孔,喷嘴两侧呈V字形(导丝:
防止丝束左右晃动)
⑥高速卷绕机:
3000—4000m/min,Barmag公司的SW4SSD、SW46S、SW4RL系列
*导丝系统:
导丝器、吸丝器、切丝器、断丝检测器——断头时,切丝器剪断丝,并吸入废丝箱
*卷绕头:
往复导丝槽筒、辅助槽筒、摩擦辊、导丝器、筒管夹——完成卷绕
⑦纺制细特(旦)和粗特(旦)丝,配有导丝盘:
条干不匀率↓
(四)纺丝卷绕异常现象
1.纺丝异常现象
异常现象
产生原因
解决方法
1.飘单丝
1.熔体含水率过高
2.聚酯特性粘数不匀
3.喷丝板板面和喷丝孔不洁,有细丝
4.组件压力扁低
5.组件过滤层击穿
6.熔体温度过高
1.调整切片于燥工艺,降低干切片含水率
2.调整各区温度,增加螺杆挤出机混合效果
3.铲洁板面或更换组件
4.增加过滤层压力
5.更换组件
6.降低箱体、熔体温度
2.并丝
1.熔体温度过高
2.侧吹风冷却情况不佳
3.泵供量过大
4.喷丝板板面不洁
5.喷丝孔有弯头丝
1.降低螺杆各区及箱体、熔体温度
2.增加侧吹风风速或降低风温
3.适当降低泵供量
4.更换组件或铲洁板面
5.更换组件,修整喷丝孔
3.注头丝和硬头丝
1.新装组件的预热温度不够
2.熔体温度过低
3.侧吹风冷却过快
4.熔体与喷丝板剥离性能不良
1.提高组件预热箱温度和延长预热时间
2.整高熔体温度
3.降低侧吹风风速
4.喷涂硅油、铲洁板面
4.集束不良
1.组件组装不佳
2.侧吹风风速过大
3.冷却凝固点飘移
4.POY油剂不好
1.改变组件组装工艺
2.调整侧吹风风速
3.改善冷却凝固条件
4.提高油剂浓度或更换油剂品种
5.毛丝
1.熔体含水、合杂量高
2.喷丝孔,喷丝板板面不清洁
3.导丝器有擦伤或角度不对
4.熔体特性粘数低
5.喷丝头拉伸过大
1.干燥切片,提高预过滤器或组件过滤效果
2.铲洁板面或更换组件
3.更换导丝器或改变导丝器角度
4.降低熔体温度或切片干燥温度
5.降低纺丝速度,增加吐出量
6.丝条晃动过大
1.侧吹风风速过大或d小
2.卷绕间向纺丝室倒回风
3.低分子升华物堵塞侧吹风网
1.调整侧吹风风速
2.正确控制纺丝室和卷绕间的风压
3.清刷则吹风过滤网
7.干切片与无油丝的特性粘数降过大
1.干切片含水率高
2.螺杆挤出机各区及熔体温度偏高
3.熔体停留时间过长
4.螺杆转速过快
1.改变干燥工艺条件,提高干燥效果
2.降低熔体温度,调整螺杆挤出机各区温度
3.改用浅槽螺杆或提高纺丝吐出量
4.降低螺杆转速
8.纤度偏差
1.计量泵吐出量异常
2.组件漏浆
3.计量泵转速过高或过低
4.飘单丝或单丝断裂
5.计量泵之前压力不足
6.分丝错误
1.检查计量泵运转状态,校验计量泵
2.紧固组件、顶紧螺栓或更换组件
3.调整计量泵转速
4.按照排除飘单丝的方法处理
5.提高计量泵泵前压力
6.认真分丝,集束上油,不分错单丝
9.强度偏差
1.原料切片特性粘数波动
2.干切片含水率波动
3.熔体温度过高或过低
1.加强切片混料和按批号投料
2.稳定切片干燥工艺,提高干燥效率
3.调整熔体温度
10.纤度偏差
1.熔体温度过低,引起伸度偏低
2.无油丝特性粘数被动
3.干切片含水率高,切片干燥温度过高
1.提高熔体温度
2.改变纺丝、干燥工艺条件
3.提高切片干燥效率,降低切片干燥温度
11.含油不均匀
1.上油嘴部分被阻塞
2.上油泵转速不合适
3.油剂浓度波动
4.油剂浓度过高
1.桶桶上油嘴孔
2.调整上油泵转速
3.严格分析油剂浓度,调整上油量
4.降低油剂浓度
12.凸肩
1.卷绕张力过大
2.摩擦辊与卷绕筒子接触压力太高
1.增大卷绕角
2.降低摩擦辊与卷绕筒子间的接触压力
13.螺旋边
1.卷绕筒管与中间丝层滑动
2.落丝时,筒管制动速度过快
3.筒管夹与摩擦辊未校水平,使卷绕筒
子与摩擦辊接触不良
1.降低卷绕张力
2.增大卷绕角
3.摩擦辊与筒管校成平行
14.蛛网丝
1.横动导丝器每次换向时不在同一位置
2.卷绕张力太高
3.卷统角大大
4.横动导丝器松动或损坏
5.摩擦辊与筒管夹未校水平
6.筒管夹转动不灵或筒管有跳动
7.摩擦辊表面磨损
8.横动导丝器干扰振幅大高
1.调换横动导丝器,修正横动凸轮槽换向点
2.降低卷绕张力,增大欠喂率
3.减小卷绕角
4.调换横动导丝器
5.校正摩擦辊与筒管夹,增加其转动灵活性
6.除会筒管夹中可能带人的废丝,更换筒管
7.修理或更换摩擦辊
8.减小横动导丝器干扰振幅
15.表面凹凸
1.卷绕张力太高
2.卷绕角过大
1.降低卷绕张力
2.减小卷绕角
16.表面丝层脱圈
1.丝不能贴附于筒子两端的表面上
2.上油量过高
1.减小卷绕角
2.减少上油量
17.叠圈
1.横动导丝器的速度、干扰振幅和周期过小,导丝棒或导丝器与丝接触部分表面损坏
2.摩擦辊中部表面磨损
3.筒管夹转动不良
1.增大横动导丝器速度、干扰振幅和周期。
调换导丝器或导丝棒
2.检查摩擦辊表面
3.校正筒管的灵活性
POY品种
264dtex/36根
120dtex/24根
螺杆挤出机各区温度(℃)
C1
C2
C3
C4
C5
C6
278
280
282
285
286
288
276
278
281
283
285
—
螺杆挤出机测量头温度(℃)
联苯温度(℃)
预过滤器后压力(105Pa)
组件熔体压力(105Pa)
组件熔体温度(℃)
计量泵转速(r/min)
泵供量(g/min)
油剂(FT621)浓度(%)
油泵转速(r/min)
288
289
80
200
288
31
88
12
40
285
286
70
170
285
14
40
12
18
组件组装条件
喷丝板孔径(mm)
密封圈(铝质)
分配板
过滤网(不锈钢)
海砂(40目,g)
海砂(24目,g)
过滤网(不锈钢)
密封圈(铝质)
扭力矩(Nm)
0.28
1
1
(320目+60目)×1
30
加满
(250目+60目)×1
1
60
0.22
1
1
(320目+60目)×1
15
加满
(250目+60目)×1
1
60
侧吹风
风速(m/s)
风温(℃)
相对湿度(%)
0.5
22±1
65±5
0.3
22±1
65±5
纺丝张力(mN)
卷绕速度(m/min)
卷绕角(o)
横动次数(DS/min)
横动振幅(±%)
落丝时间(min)
280
3300
7.59
1293.7
0.6
175
270
3200
7.59
1293.7
0.6
380