4105直角固定冲压模具设计.docx
《4105直角固定冲压模具设计.docx》由会员分享,可在线阅读,更多相关《4105直角固定冲压模具设计.docx(28页珍藏版)》请在冰豆网上搜索。
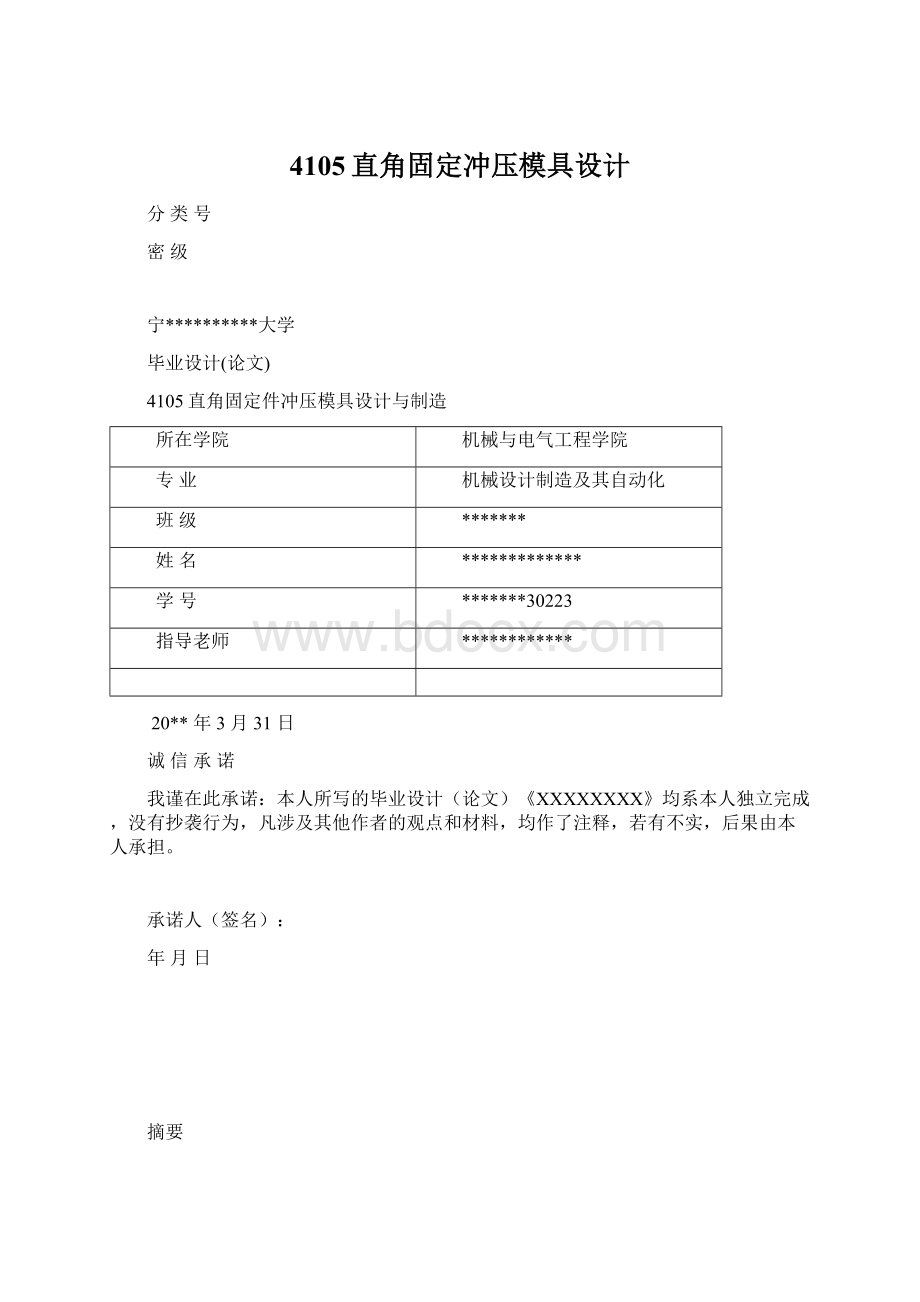
4105直角固定冲压模具设计
分类号
密级
宁**********大学
毕业设计(论文)
4105直角固定件冲压模具设计与制造
所在学院
机械与电气工程学院
专业
机械设计制造及其自动化
班级
*******
姓名
*************
学号
*******30223
指导老师
************
20**年3月31日
诚信承诺
我谨在此承诺:
本人所写的毕业设计(论文)《XXXXXXXX》均系本人独立完成,没有抄袭行为,凡涉及其他作者的观点和材料,均作了注释,若有不实,后果由本人承担。
承诺人(签名):
年月日
摘要
毕业设计是在模具专业理论教学之后进行的实践性教学环节。
是对所学知识的一次总检验,是走向工作岗位前的一次实战演习。
其目的是,综合运用所学课程的理论和实践知识,设计一副完整的模具训练、培养和提高自己的工作能力。
巩固和扩充模具专业课程所学内容,掌握模具设计与制造的方法、步骤和相关技术规范。
熟练查阅相关技术资料。
掌握模具设计与制造的基本技能,如制件工艺性分析、模具工艺方案论证、工艺计算、加工设备选定、制造工艺、收集和查阅设计资料,绘图及编写设计技术文件等。
本设计主要对弯垫板冲压模具进行设计。
结合公司实际生产要求和产品的特点,在厂原有的设计上,对模具进行了改进设计。
本设计对压簧片加工工艺进行了分析,得出了最佳加工方案,在充分保证零件质量与精度的前提下,选择高生产率的加工工艺,降低生产成本,从而有效地节约了材料。
本设计中使用计算机软件进行了辅助设计,在保证高精度的同时简化了传统的繁琐计算过程,使设计更为便捷。
该弯垫板从坯料到完全成形,以前是使用两套模具:
冲孔落料复合模与弯曲模。
所设计的两套模具较为典型,也具有一定的代表性。
本设计的重点与难点是多道工序的结合以及对凸、凹模刃口尺寸的计算,因为它将直接影响零件的质量。
关键词:
冲压模具;级进模;辅助设计;模具结构
Abstract
Graduationdesignisapracticalteachinglinkafterthemoldtheoryteaching.Istolearntheknowledgeofageneralinspection,istoworkbeforeapracticalexercise.Itspurposeistousethetheoryandpracticalknowledgeofthecourse,designacompletemoldtraining,trainingandimprovetheirabilitytowork.Consolidateandexpandthecontentsofthemoldprofessionalcourses,mastermolddesignandmanufacturingmethods,stepsandrelatedtechnicalspecifications.Familiarwithtechnicaldocuments.Masterthebasicskillsofmoulddesignandmanufacturingprocessoftheparts,suchasmoldprocessanalysis,schemedemonstration,processcalculation,processequipmentselection,manufacturingprocess,collectionandaccesstodesigninformation,drawingdesignandthepreparationoftechnicaldocumentsetc..
Thedesignofthebendingplatestampingdiedesign.Combinedwiththeactualproductionrequirementsandthecharacteristicsoftheproduct,intheoriginaldesignofthefactory,themoldwasimproved.Thisdesignhascarriedontheanalysistothepressurespringprocess,theoptimumprocessingscheme,inordertoensurethequalityandprecisionofthepremiseparts,choiceofprocessingtechnologyofhighproductivity,reduceproductioncosts,therebyeffectivelysavingmaterial.Thisdesignusesthecomputersoftwaretocarryontheauxiliarydesign,whileguaranteeingthehighaccuracy,hassimplifiedthetraditionaltediouscomputationprocess,causesthedesigntobemoreconvenient.
Thebendingplateisformedfromblanktofullyformed,andtwosetsofdiesareusedbefore.Thedesignofthetwosetsofmoldismoretypical,butalsohasacertainrepresentation.Thefocusanddifficultyofthisdesignisthecombinationofthemultiprocessandthecalculationofthesizeoftheconvexandconcavedie,becauseitwilldirectlyaffectthequalityoftheparts.
Keyword:
Stampingdie,progressivedie,aideddesign
第1章、绪论
1.1.课题来源和研究意义
本设计题目由实习单位提供,经系指导老师审核通过的。
本设计题目涉及的主要内容是对冲压模的设计,研究目的是在厂原有的基础上,对模具进行改进设计,提高产品质量与效益。
在二十世纪中期甚至更早,国外就已经出现很多对模具及模具工业的高度评价与精辟的比喻。
例如:
“模具是美国工业的基石”(美国);“模具是促进社会繁荣富强的原动力”(日本);“模具工业是金属加工的帝王”(德国);“模具是黄金”(东欧)等。
在二十世纪未,中国人才开始认识到其极端重要性,作出了科学的评价:
“模具工业是现代工业之母”(中国)。
制造行业在2000年以后,行业的特点正在发生这改变,从机器时代变革至现在的信息技术的时代。
在2001年入世以后,世界多地的商家开始在进入中国,机遇挑战并存,随着日渐激烈的竞争中,对商家的快速市场反应能力增加了考验,以面对不断改变的商机,并对柔性制造提出了最新的要求,更好的发展。
现今,全世界模具工业年总产值约为650亿美元,其中亚洲地区占到全世界一半的总产值。
而在亚洲,最高属于日本,年产值达200亿美元上下。
美国的年产值为50亿美元。
中国也在后来居上,现在已经达到70亿美元。
然而,产值并不等同于技术质量。
虽然我们国家在冲压模具的数量,质量,技术等各个领域都取得了长足的进步,但与世界先进的水平相比仍是有着很大的差距。
每年依然需要大量进口高精度,寿命长的高级模具。
而技术含量低的模具已供过于求,市场利润空间狭小。
近五年来,平均每年进口模具约为11.2亿美元,2003年就进口了近13.7亿的模具,这还未包括随设备和生产线作为附件带进来的模具。
这表示中国大陆模具业的发展潜力仍然很巨大。
这就是这次研究的意义。
1.2.国内外在该方向的研究现状及分析
在世界上大多数国家和地区,模具及模具工业早已成为了一个行业,有专门的行业组织机构指导和推动模具工业的发展。
比如日本有“型技术协会”,台湾地区有“台湾模具工业同业公会”,我国有“中国模具工业协会”,各省市均有其分会。
模具行业已成为一个大行业
,仅我国的模具企业已达到了数万家之多。
近年来,我国冲压模具水平已有很大提高。
大型冲压模具能生产的单套最高重量的模具达到了50多吨,另外要求更高的多工位级进模也可以生产了。
其模具精度,使用寿命都得到了大幅的提升。
对于各种要求的精冲模领的设计制造中也达到了相当高的水准。
我国模具CAD/CAM技术的发展已有20多年历史。
由原华中工学院和武汉733厂于1984年共同完成的精冲模CAD/CAM系统是我国第一个自行开发的模具CAD/CAM系统。
华中工学院和北京模具厂等在1986年共同完成的冷冲模CAD/CAM系统是我国自行开发的第一个冲裁模CAD/CAM系统。
上海交通大学开发的冷冲模CAD/CAM系统也于同年完成。
21世纪开始,CAD/CAM技术逐渐普及,现在具有一定生产能力的冲压模具企业基本都有了CAD/CAM技术,其中部分骨干重点企业还具备各CAE能力。
模具CAD/CAM技术能明显减少模具设计与制造周期,降低生产成本,提升产品质量,已成为大家的共识。
在“八五”、九五“期间,已有一大批优秀的模具企业推广普及了计算机绘图技术,数控加工的使用频率也越来越多,并持续引进了相当数量CAD/CAM系统。
如以色列公司的Cimatron,日本HZS公司的CRADE及space-E,美国CV公司的CADSS,美国EDS的UG,美国ParametricTechnology公司的Pro/Engineer,英国DELCAM公司的DOCT5还引进了AutoCADCATIA等软件及法国Marta-Daravision公司用于汽车及覆盖件模具的Euclid-IS等专用软件。
国内汽车覆盖件模具生产企业普遍采用了CAD/CAM技术/DL图的设计和模具结构图的设计均已实现二维CAD,较多的企业已经向三维过渡,总图生产逐步代替零件图生产。
在冲压成型CAE软件方面,除了引进的软件外,湖南大学、华中科技术大学、吉林大学、等都已研发了较高水平的具有自主知识产权的软件,并已在实践中得到成功应用,产生了良好的效益。
快速原型(RP)传统的快速经济模具相结合,快速制造大型汽车覆盖件模具,解决了原来低熔点合金模具靠样件浇铸模具,模具精度低、制件精度低和制造难等一系列问题,实现了以三维CAD模型作为制模依据的快速模具制造。
它意味着RPM应用于汽车身大型覆盖件试制模具已取得了成功。
围绕着大型覆盖件模具、汽车车身试制的快速制造,这些年来也涌现出一些新的快速成型的方法。
比如,目前已开始在生产中应用的无模多点成型及激光冲击和电磁成型等。
它们都表现出了减少成本、提升效率的优势。
1.3.本课题研究的主要内容
1.直角固定件冲裁工艺方案;
2.直角固定件模具总体方案设计;
3.模具各零件尺寸计算;
4.模具总装配图与零件图绘制。
1.4.本章小结
本章从国内外当今模具的发展状况这个角度介绍了课题的研究意义,及主要的设计方案的过程,在此基础上提出课题设计的任务。
第2章、4105直角固定件加工工艺综合分析
2.1.直角固定件加工工艺要求
直角固定件零件图如图2-1所示,材料为30#钢,优质碳素结构钢,材料厚度
=1.5mm,已知年产量为大批量生产。
要求表面无划痕、冲口无毛刺、弯曲无裂纹。
设计其冲压模,确定冲压工艺方案。
(30#钢材质抗拉强度约是450-600MPa,抗剪强度约是360-480MPa,具有良好的塑性,其冲裁、成形加工性较好。
)
图2-1直角固定件零件图
2.2.零件图分析
该件为折形弯曲的产品,尺寸精度要求不高,由冲裁和弯曲即可成形。
冲压难点在于多
道工序在一副模具里实现,即采用连续冲压的方法,同时要保证产品不能变形。
最好是采用中间载体来设计模具,先冲两边的废料,中间连接部分做载体,最后切断,产品脱离模具,整个工艺流畅,可以提高生产效率。
2.3.冲压件经济性和先进性分析
冲压是该件最好的加工方法。
由于批量较大,为提高生产率,宜采用复杂一点的多工位级进模设计。
2.4.工艺方案的确定
方案一:
首先整体落料,再冲孔,最后进行弯曲;
方案二:
落料,弯曲,最后进行冲孔;
方案三:
落料冲孔复合,最后进行弯曲。
方案四:
冲侧刃,冲孔,切废料,弯曲,最后切断,产品掉下。
上述三方案的综合比较见下表:
表2-1 冲压工艺方案比较表
项 目
方案一,二
方案三
方案四
模具数量
三套
二套
一套
制件质量
有回弹,可控制
有回弹,不易控制
形状尺寸精度较好,有回弹,可控制
生产率
较低
较高
较高
模具寿命
结构简单,寿命不长
结构复杂,生产效率高,比较合理
根据上表比较,选定方案三。
由于冲压件弯曲尺寸精度均为IT12,方案四回弹可控制,对其影响不大。
同时,采用这样的方案,在提高生产率的同时也很好地保证弯曲与外形尺寸精度。
2.5.本章小结
本章分析了压簧片整体加工工艺性,对其工艺性进行审查,并对冲压件进行了经济性与先进性分析,最后确定工艺方案。
第3章、级进模的设计
3.1.冲压件的工艺分析
该产品落料,弯曲等工序结合,结构较为简单,整个形状由直线与圆弧组成。
由零件图可知,该件的经济精度为IT14,符合冲裁精度要求,精度要求能够在冲裁加工中得到保证,一次冲压成形。
其尺寸要求、生产批量等情况,也均符合冲裁的工艺要求。
材料为30#。
该工件的弯曲内圆角半径为1mm,大于最小弯曲半径rmin=0.5t=0.5×1.2=0.6mm,故该工件形状、尺寸、精度在计算展开尺寸时可以按中心层不变原则计算。
3.1.1.弯曲件回弹值的计算
(1)
时属于小变形程度,而
时属于大变形程度。
此零件的r/t=1/1.0=1,属于大变形程度,圆角半径回弹小,不必计算,只计算凸模角度。
因为
,由文献[1,表5-5]得到:
计算凸模的中心角:
(3-1)
其中
凸模的圆角部分的中心角,(
);
工件的中心角,(
)。
(2)工件回弹问题的解决:
当工件精度要求不高或校正弯曲时,生产中常采取调整凸、凹模间隙的方法解决工件回弹问题。
3.2.排样
根据产品形状,弯曲R角和材料厚度的比例大于0.5,所以无法按小R角计算公式计算,只能根据材料中性层不变的原则计算展开尺寸:
L=38,由于材料在弯曲时R角处材料会有所延长,所以根据经验,本次课题展开尺寸按
38.8计算和设计模具,展开图如下:
此尺寸还需要经过实际生产来调节,结合产品形状和模具结构情况,决定采用直排的排样方案,如下图3-1所示:
个
图3-1 排样图
由文献[1,表3-17]可知:
中间搭边载体尺寸为22×38.8=853.6mm2,冲压件面积为853.6-3.14×36-3.14×9-(16×22-16×12)=552.3mm2,
所以一个进距的材料利用率为:
1×552.3÷853.6×100%=64.7%(3-1)
3.3.计算冲压力(根据工步计算冲压力)
3.3.1.冲导正孔力
P1=Lt
=1
(3.14
4)
1.5
480=9.043KN
3.3.2.冲废料力
P2=Lt
=1
56.2
1.5
480=40.464KN
3.3.3.冲废料力
P3=Lt
=1
63.25
1.5
480=45.54KN
3.3.4.弯曲力的计算
(1)弯曲力
P4=cLt
=0.8
(22+22)
1.5
600=31.68KN
式中
P—弯曲力
c--系数,取0.5-0.8
L--弯曲件长度(mm)
t--板料厚度(mm)
--材料抗拉强度(MPa)
3.3.5.卸料力
P5=KrP1
由文献[3,表3-8]:
取Kr=0.04,故
P5=0.04×(7.234+32.371+36.432+25.344)=4.1KN
3.3.6.顶件力
由文献[3,表3-8],取Kp=0.045,故
PtKp
=0.045×(7.234+20.16+32.371+36.432+25.344+4.1)=4.8KN
总冲压力
P0=P1+P2+P3+P4+P5+P6=111.4KN
初步选择400KN冲床。
3.4.确定模具压力中心
图3-2冲裁力分析图
以中间圆圆心为原点,建立如上图3-2所示坐标系XOY。
采用解析法求压力中心,求YG,XG
F1——冲导正孔F3=Ltσb,得F3=7.234KN
F2——切废料力F5=Ltσb,得F5=32.371KN
F3——切废料力F6=Ltσb,得F6=36.432KN
F4——弯曲力F7=cLt
,得F7=25.344KN
Y1——F1到X轴的力臂Y3=13
X1——F1到Y轴的力臂X3=70
Y2——F2到X轴的力臂Y4=-12.2
X2——F2到Y轴的力臂X4=28
Y3——F3到X轴的力臂Y5=11.55
X3——F3到Y轴的力臂X5=14
Y4——F4到X轴的力臂Y6=-16.2
X4——F4到Y轴的力臂X6=-14
根据合力距定理:
YG=(Y1F1+Y2F2+Y3F3......)/(F1+F2+F3……)
XG=(X1F1+X2F2+X3F3…..)/(F1+F2+F3……)
YG——F冲压力到X轴的力臂;YG=8.6328
XG——F冲压力到Y轴的力臂;XG=-2.0907
所以本次设计的模具压力中心为(8.6238,-2.0907)。
3.5.计算凸、凹模刃口尺寸
3.5.1.冲孔凸、凹模刃口计算
对冲孔采用凸、凹模分开的加工方法,其凸、凹模刃口部分尺寸计算如下:
冲Φ6mm、Φ12mm孔,由文献[3,表3-5]可知:
Zmin=0.06,Zmax=0.15,
Zmax-Zmin=0.15-0.06=0.09mm
由文献[1,表3-13]得凸凹模制造公差:
=0.02mm,
=0.03mm
校核:
Zmax-Zmin=0.09mm,
+
=0.05mm
满足Zmax-Zmin≧
+
的条件。
由文献[1,表3-12]得因数x=0.5,则
dp1=(5.95+0.5×0.1)=6.0
工件尺寸:
Φ12mm。
查表得,X=0.5。
根据查表知,尺寸10mm的公差为Δ=0.46。
根据公式
得:
d
=(12+0.5×0.46)
=12.23
mm
冲孔凹模尺寸按凸模实际尺寸配做,保证双边间隙为(0.15+0.06)/2=0.10mm,具体零件尺寸看零件图。
3.5.2.落料凸、凹模刃口计算
凸、凹模刃口尺寸的计算原则
设计落料模需要先确定凹模刃口尺寸,拿凹模做基准,间隙取在凸模上;设计冲孔模先确认凸模刃口尺寸,拿凸模做基准,间隙取在凹模上。
间隙是影响模具寿命的各种因素中占最主要的一个。
冲裁过程中,凸模与被冲的孔之间,凹模和落料件之间的均有磨檫,而且间隙越小,磨檫越严重。
在现实生产作业中受到制造误差与装配精度的限制下,凸模不可能绝对垂直于凹模平面,而且间隙不会绝对均匀分布,合理的间隙均可使凸模、凹模侧面与材料间的磨檫减小,并缓减间隙不均匀的不利影响,从而提高模具的使用寿命。
冲裁间隙对冲裁力的影响:
虽然冲裁力随冲裁间隙的增大有一定程度的降低,但是当单边间隙介于材料厚度5%~20%范围时,冲裁力的降低并不明显(仅降低5%~10%左右)。
因此,在正常情况下,间隙对冲裁力的影响不大。
冲裁间隙对斜料力、推件力、顶件力的影响:
间隙对斜料力、推件力、顶件力的影响较为显著。
间隙增大后,从凸模上斜、从凸模孔口中推出或顶出零件都将省力。
一般当单边间隙增大到材料厚度的15%~25%左右时斜料力几乎减到零。
冲裁间隙对尺寸精度的影响:
间隙对冲裁件尺寸精度的影响的规律,对于冲孔和落料是不同的,并且与材料轧制的纤维方向有关。
通过以上分析可以看出,冲裁间隙对断面质量、模具寿命、冲裁力、斜料力、推件力、顶件力以及冲裁件尺寸精度的影响规律均不相同。
因此,并不存在一个绝对合理的间隙数值,能同时满足断面质量最佳,尺寸精度最佳,冲裁模具寿命最长,冲裁力、斜料力、推件力、顶件力最小等各个方面的要求。
在冲压的实际生产过程中,间隙的选用主要考虑冲裁件断面质量和模具寿命这两个方面的主要因素。
但许多研究结果表明,能够保证良好的冲裁件断面质量的间隙数值和可以获得较高的冲模寿命的间隙数值也是不一致的。
一般说来,当对冲裁件断面质量要求较高时,应选取较小的间隙值,而当对冲裁件的质量要求不是很高时,则应适当地加大间隙值以利于提高冲模的使用寿命。
根据冲模在使用过程中的磨损规律,设计落料模时,凹模基本尺寸应取接近或等于零件的最小极限尺寸;设计冲孔模时,凸模基本尺寸则取接近或等于冲孔件的最大极限尺寸。
按冲件精度和模具可能磨损程度,凸、凹模磨损留量需保证在公差范围内的0.5-1.0之间。
磨损量用xΔ表示,其中Δ为冲件的公差值,x为磨损系数,其值在0.5-1.0之间,与冲件的制造精度有关,可按下列关系选取:
零件精度IT10以上X=1;零件精度IT11-IT13X=0.75;零件精度IT14X=0.5。
不管落料还是冲孔,冲裁间隙一律采用最小合理间隙值(Zmin)。
选择模具制造公差时,一般冲模精度较零件高3-4级。
对于形状简单的圆形、方形刃口,其制造偏差值可按IT6-IT7级选取;对于形状复杂的刃口尺寸制造偏差可按零件相应部位公差值的1/4来选取;对于刃口尺寸磨损后无变化的制造偏差值可取冲件相应部位公差值的1/8并冠以(±);若零件没有标注公差,则可按IT14级取值。
零件尺寸公差与冲模刃口尺寸的制造偏差应按“入体”原则标注单向公差,即:
落料件上偏差为零,只标注下偏差;冲孔件下偏差为零,只标注上偏差。
如果零件公差是依双向偏差标注的,则应换算成单向标注。
磨损后无变化的尺寸除外。
对外轮廓的落料,由于形状较复杂,故采用配合的加工方法。
其凸、凹模刃口部分尺寸计算如下:
当以凹模做基准件时,凹模磨损后,刃口尺寸有的增大,有的减小。
增大尺寸有:
6,28,3,它在冲孔凸模上相当于落料凹模尺寸,故按一般落料凹尺寸公式计算。
由文献[1,表3-13]得因数x为:
对3、17,12,△
0.50时,所以有
6d=(6.1-0.5×0.2)=6
3d=(3.05-0.5×0.1)=3
28d=(28.15-0.5×0.3)=28
由文献[1,表3-4]得Zmin=0.06mm,凸模尺寸按凹模实际尺寸配做,保证双边间隙为(0.15+0.06)/2=0.10mm,具体零件尺寸看零件图。
3.5.3.弯曲工作部分尺寸计算
(1)凸模圆角半径
由于此件圆角半径(r=1mm)较小,凸模圆角半径可取R1=2.2,R2=3.2。
(2)凹模圆角半径
凹模圆角半径不能过小,以