真空碳酸钾脱硫工艺.docx
《真空碳酸钾脱硫工艺.docx》由会员分享,可在线阅读,更多相关《真空碳酸钾脱硫工艺.docx(9页珍藏版)》请在冰豆网上搜索。
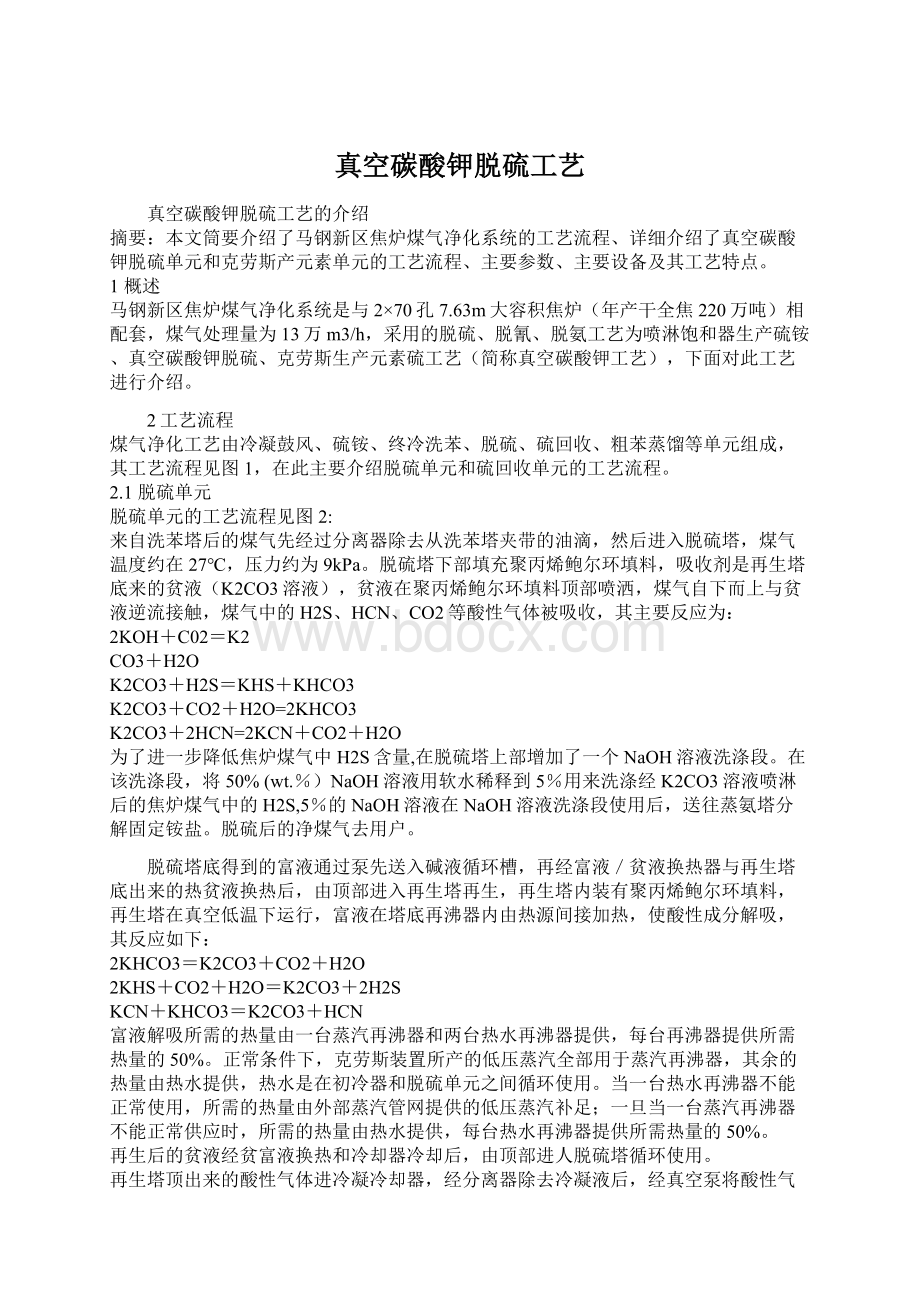
真空碳酸钾脱硫工艺
真空碳酸钾脱硫工艺的介绍
摘要:
本文筒要介绍了马钢新区焦炉煤气净化系统的工艺流程、详细介绍了真空碳酸钾脱硫单元和克劳斯产元素单元的工艺流程、主要参数、主要设备及其工艺特点。
1概述
马钢新区焦炉煤气净化系统是与2×70孔7.63m大容积焦炉(年产干全焦220万吨)相配套,煤气处理量为13万m3/h,采用的脱硫、脱氰、脱氨工艺为喷淋饱和器生产硫铵、真空碳酸钾脱硫、克劳斯生产元素硫工艺(简称真空碳酸钾工艺),下面对此工艺进行介绍。
2工艺流程
煤气净化工艺由冷凝鼓风、硫铵、终冷洗苯、脱硫、硫回收、粗苯蒸馏等单元组成,其工艺流程见图1,在此主要介绍脱硫单元和硫回收单元的工艺流程。
2.1脱硫单元
脱硫单元的工艺流程见图2:
来自洗苯塔后的煤气先经过分离器除去从洗苯塔夹带的油滴,然后进入脱硫塔,煤气温度约在27℃,压力约为9kPa。
脱硫塔下部填充聚丙烯鲍尔环填料,吸收剂是再生塔底来的贫液(K2CO3溶液),贫液在聚丙烯鲍尔环填料顶部喷洒,煤气自下而上与贫液逆流接触,煤气中的H2S、HCN、CO2等酸性气体被吸收,其主要反应为:
2KOH+C02=K2
CO3+H2O
K2CO3+H2S=KHS+KHCO3
K2CO3+CO2+H2O=2KHCO3
K2CO3+2HCN=2KCN+CO2+H2O
为了进一步降低焦炉煤气中H2S含量,在脱硫塔上部增加了一个NaOH溶液洗涤段。
在该洗涤段,将50%(wt.%)NaOH溶液用软水稀释到5%用来洗涤经K2CO3溶液喷淋后的焦炉煤气中的H2S,5%的NaOH溶液在NaOH溶液洗涤段使用后,送往蒸氨塔分解固定铵盐。
脱硫后的净煤气去用户。
脱硫塔底得到的富液通过泵先送入碱液循环槽,再经富液/贫液换热器与再生塔底出来的热贫液换热后,由顶部进入再生塔再生,再生塔内装有聚丙烯鲍尔环填料,再生塔在真空低温下运行,富液在塔底再沸器内由热源间接加热,使酸性成分解吸,其反应如下:
2KHCO3=K2CO3+CO2+H2O
2KHS+CO2+H2O=K2CO3+2H2S
KCN+KHCO3=K2CO3+HCN
富液解吸所需的热量由一台蒸汽再沸器和两台热水再沸器提供,每台再沸器提供所需热量的50%。
正常条件下,克劳斯装置所产的低压蒸汽全部用于蒸汽再沸器,其余的热量由热水提供,热水是在初冷器和脱硫单元之间循环使用。
当一台热水再沸器不能正常使用,所需的热量由外部蒸汽管网提供的低压蒸汽补足;一旦当一台蒸汽再沸器不能正常供应时,所需的热量由热水提供,每台热水再沸器提供所需热量的50%。
再生后的贫液经贫富液换热和冷却器冷却后,由顶部进人脱硫塔循环使用。
再生塔顶出来的酸性气体进冷凝冷却器,经分离器除去冷凝液后,经真空泵将酸性气体送至硫回收工段。
新碱(KOH)贮存于槽中,并通过计量泵向循环碱液槽中补充。
软水用于循环碱液系统的补水,补入循环碱液槽内。
为了调整循环碱液中盐的含量,部分溶液必须外排。
废液可以排放到已有的煤气净化装置里。
2.2硫回收单元
从再生塔顶来的酸汽(含有H2S,HCN和少量的NH3及CO2)送入一个带特殊燃烧器的克劳斯炉,见图3。
在克劳斯炉燃烧室内加入主空气,使约1/3的H2S燃烧生成SO2,SO2再与2/3的H2S反应生成元素硫,反应热可使过程气维持在1100℃左右,当酸汽中H2S含量较低时,尚需补充少量煤气。
在燃烧室和催化床中同时发生HCN和NH3的分解反应。
为达到尽可能高的H2S转化率,通过在催化床后部加入辅空气来调整H2S/SO2。
克劳斯炉内发生以下反应:
H2S+3/2O2=SO2+H2O
2H2S+SO2=3/xSX+2H2O
2NH3=N2+3H2
2HCN+2H2O=N2+2CO2+3H2
由克劳斯炉排出的高温过程气,经废热锅炉冷却,安装在废热锅炉出口处的迷宫式分离器将冷凝出来的液态硫磺分离,回收的热量生产120℃,0.15MPa的低压蒸汽。
由废热锅炉排出的过程气仍含有H2S与SO2,使其进入克劳斯反应器,进一步使H2S与SO2反应趋于完全,主反应如下:
2H2S+SO2=3/xSX+2H2O
为达到克劳斯反应器进口温度的要求,将部分克劳斯炉出来的热过程气掺入冷却后的过程气中,热过程气量通过废热锅炉的中央管来控制。
克劳斯反应器出来的过程气经硫冷凝器冷却,再经分离器分离出液硫,经硫封槽汇入液硫贮槽贮存,定期用泵抽出送至硫结片机生产固体硫磺,装袋称量外销。
废热锅炉带有一个外置汽包,外置汽包内装有换热管束,将克劳斯反应器出来的热过程气冷却到约140℃。
冷却后的尾气(温度约为140℃、压力约为0.02MPa)送入初冷器前荒煤气管道里。
废热锅炉所产蒸汽用于再生塔的蒸汽再沸器。
废热锅炉所需软水由外部送来,首先进入锅炉供水处理槽,槽内通入直接蒸汽加热,进行蒸吹除氧,为使锅炉供水符合标准,由试剂泵向水中加入化学试剂。
经处理后的软水用泵抽出,进人废热锅炉。
克劳斯炉装有火焰监视器,并设有安全关闭机构,当出现酸汽、空气流量太小,煤气、空气压力过低或锅炉液位过低等不正常状态时,克劳斯炉将自动关闭,酸汽送往初冷器前煤气管道。
3主要参数
3.1煤气净化指标
焦炉煤气净化前后的H2S,HCN含量见
表1
焦炉煤气净化前后的H2S、HCN含量
煤气指标
H2S含量(mg/m3)
HCN含量(mg/m3)
粗焦炉煤气
<7600
<1500
净焦炉煤气
<200
<300
3.2主要技术操作指标
脱硫塔进口煤气温度27℃
脱硫塔操作压力9kPa
再生塔内温度67一72℃
再生塔操作压力一20kPa
K2CO3溶液循环量150一160m3/h
3.3化学试剂及公辅介质消耗指标
脱硫单元和硫回收单元的化学试剂及公辅介质消耗指标见表2:
表2化学试剂及公辅介质消耗指标
项目
消耗指标
项目
消耗指标
50%KOH溶液
770kg/d
软水
7.5m3/h
50%NaOH溶液
270kg/h
热水
1000m3/h
循环冷却水
1300m3/h
低压蒸汽
9t/h
低温冷却水
270m3/h
电力
760kW
4主要设备
脱硫塔2座(DN5000,H=22600,材质Q235一A)、再生塔2座(DN5400,H=27600,材质Q235一A)、克劳斯装置2套、抽真空系统2套。
5工艺特点
5.1脱硫采用真空解吸法再生
该工艺富液再生采用真空解吸法,操作温度为67一72℃,脱硫和再生系统均在低温低压下运行,腐蚀弱,对设备材质要求不高,吸收塔、再生塔及大部分设备材质为碳钢,使整个装置投资减少。
5.2煤气净化效果好
该脱硫工艺属干湿式吸收法,正常工况下,脱硫效率可达95%以,脱氰效率可达80%,且在脱硫塔上部增加了一个NaOH溶液洗涤段,进一步降低了煤气中H2S含量,可使净煤气中H2S含量降到200mg/m3耐以下,满足环保和一般冶金燃气的质量要求。
5.3硫磺转化率高、质量优
硫回收采用酸汽部分燃烧法与催化转化的克劳斯工艺流程,H2S的转化率达96%,所得产品固体硫磺的纯度高达99.5%,是优质化工原料。
5.4余热利用
本工艺设置废热锅炉及贫富液换热器,最大限度地利用过程气及贫液的余热,节省了能源,提高了整个装置的热效率。
再生塔的热源为废热锅炉所产的蒸汽或初冷器所产的热水,不需外加蒸汽;贫液与富液进行热交换,既降低了贫液的温度,又提高了富液的温度,节约了冷却水和蒸汽消耗。
5.5环境保护好
本工艺产生的克劳斯尾气返回吸煤气管道,不污染大气,而尾气中剩余H,S还可继续回收,可燃成分也得到利用。
NTsize=3>5.6系统运行的可靠性和稳定性好
该工艺脱氨与脱硫相互独立,工序之间的适应性较好,对公用介质(蒸汽和低温水)的要求相对较低,遇有停电、停汽、停水等特殊情况时,系统恢复生产的时间较短,系统运行的可靠性和稳定性好。
河南安阳钢铁公司焦炉煤气脱硫脱氰项目(正在建设)
(绿色援助计划示范工程项目选登)
新华社信息北京12月4日电
实施单位:
河南安阳钢铁集团公司
项目概况:
2000年2月24日国家计委、原国家冶金工业局、河南省计
委与日本新能源产业技术综合开发机构(NEDO)在北京签订了基本协议书,
由河南安阳钢铁集团公司与新日本制铁株式会社共同实施。
技术特点:
本项目采用真空碳酸盐法脱硫技术,具有以下特点:
1、脱硫工
艺是一独立单元,与“AS”法比较,控制系统简便、易于掌握。
2、真空碳酸
盐法脱硫所需碳酸钠溶液可循环使用,耗量少,真空解析减少脱硫废液的产生,
克劳斯法生产硫磺产品纯度比国内“HPF”法生产的纯度高,达99.99
%。
而且无熔硫过程中的废气污染,操作环境好。
3、真空碳酸盐法脱硫是用低
温进行吸收液的再生,故不会产生腐蚀,主要设备采用碳钢制作,很少部分采用
不锈钢。
4、“AS”法脱硫对相应的工序及外部条件要求苛刻。
而真空碳酸盐
法脱硫工艺操作范围弹性大,便于操作。
5、该工艺采用循环氨水余热再生,无
需消耗蒸汽,运行费用低。
(
真空碳酸钾法与HPF法工艺的比较
-
在炼焦过程中,煤中大约30%的硫进入煤气中,致使焦炉煤气中的硫化氢含量一般在4~10g/m3。
当煤气作为燃料燃烧时,会生成大量硫氧化物,严重污染大气。
同时,在轧钢过程中,使用含硫量较高的煤气将影响钢材的质量,制约高附加值优质钢材的开发和生产。
所以选择合理、有效的焦炉煤气脱硫工艺显得尤为重要。
对于脱硫脱氰工艺方案的选择,应遵循国家相关的节能减排和循环经济政策,并根据工程项目的总体需求,达到技术先进、节能降耗、清洁生产的最佳组合。
目前我国已经建成的煤气净化系统中具有代表性的湿法脱硫工艺有以下几种:
1)湿式氧化工艺:
TH法、FRC法、ADA法、HPF法。
2)湿式吸收工艺:
单乙醇胺法(索尔菲班法)、氨硫联合洗涤法(AS法)、真空碳酸盐法。
近年来,采用比较多的是真空碳酸钾法脱硫工艺配合WSA制酸工艺和HPF法脱硫制硫磺工艺,我们根据工程设计和生产实践,对上述两种工艺进行比较。
1 两种脱硫工艺的比较基准
1)两种脱硫工艺的设汁条件一致,处理煤气量6.5万m3/h;
2) HPF法脱硫制硫磺工艺位于煤气鼓风机后;
3)真空碳酸钾法脱硫工艺布置在洗苯后,配套WSA制酸工艺;
4)真空碳酸钾法脱硫工艺投资包括利用煤气作为热源所带来的增加投资;
5)两种工艺方案所配套粗苯装置的设备、管道材质等装备水平和自动控制水平相同。
2 两种脱硫工艺的综合比较
两种脱硫工艺的产品、原材料及消耗比较见表1,工艺综合对比见表2,估算投资及生产费用见表3、表4。
表1 两种脱硫工艺的产品、原材料及消耗
项 目
HPF法脱硫配套制硫磺
真空碳酸钾法脱硫配套WSA制酸
原料及辅助材料
PDS催化剂,t/a
20
-
液氨,t/a
-
127
V2O5催化剂(一次装填量),m3
-
38
KOH(48%),t/a
-
201
产品
硫磺(含硫90%),t/a
3249
-
硫酸(98%),t/a
-
8697
动力消耗
循环水(32~45℃),m3/h
180
410
冷冻水(16~23℃),m3/h
125
285
纯水,m3/h
-
9
工业水,m3/h
2
-
生活水,m3/h
-
0.5
蒸汽消耗量(未扣除自产蒸汽量),t/h
4.3
2.5
自产蒸汽(5.8MPa),t/h
-
4
焦炉煤气耗量,m3/h
-
2
压缩空气,m3/h
7020
-
装机容量,kW
1923
1986
操作容量,kW
1256
1217
其中10kV总容量,kW
1500
-
10kV操作容量,kW
1000
-
注:
①真空碳酸钾法循环水用量已扣除利用煤气热量带来的初冷器用水量减少。
②未计HPF法造成的硫按产量的减少。
表2 两种脱硫工艺的综合对比
项 目
HPF法脱硫配套制硫磺
真空碳酸钾法脱硫配套WSA制酸
脱硫脱氰效率
一般
较高
净煤气合格的可靠性
一般
可靠
蒸汽用量
较少
少,可结余蒸汽
冷却水耗量
较少
较多
电力耗量
二者相当
环保
不符合环保要求
符合环保要求
设备数量和总重
少,总重小
多,总重大
操作难易
较难
较易
产品品质
低
高
操作费用
高
低
投资
低
高
表3 两种脱硫方法工艺部分的投资估算(万元)
项 目
HPF法脱硫配套制硫磺
真空碳酸钾法脱硫配套WSA制酸
国内设备费
3533
5263
国内安装及材料费
756
1317
引进设备费
-
2500
引进专利和基本设计费
-
1250
合计
4289
10330
3 结论
由上述比较可知,虽然真空碳酸钾法脱硫及WAS制酸工艺一次性投资高,但脱硫脱氰效率优于HPF法脱硫及制硫磺工艺,经济效益、环保效果也比较好。
真空碳酸钾法脱硫脱氰工艺为中冶焦耐公司在吸收国外先进经验和生产实践的基础上,与高等院校合作开发的有自主知识产权的脱硫工艺技术。
此工艺已在梅山化工焦炉易地大修配套煤气净化工程中得到应用,目前生产操作稳定,净化后煤气中硫化氢含量达到设计要求。
表4 两种脱硫方法工艺部分的生产费用
项 目
单位
HPF法脱硫配套制硫磺
真空碳酸钾法脱硫配套WSA制酸
设备折旧费和维修费
万元/年
428.9
1033
原料消耗费
万元/年
300
315
动力消耗费
万元/年
4448
932
工人工资
万元/年
7.5
-
产品产值
万元/年
162
1566
生产费用
万元/年
5022.4
714
运行成本
元/km3煤气
78.02
11.09
注:
运行成本为水、电、蒸汽等的年耗量乘以各自的单价后,再除以本系统的年煤气处理量。
(注:
可编辑下载,若有不当之处,请指正,谢谢!
)