课程设计CA6140车床齿轮工艺规程与夹具设计.docx
《课程设计CA6140车床齿轮工艺规程与夹具设计.docx》由会员分享,可在线阅读,更多相关《课程设计CA6140车床齿轮工艺规程与夹具设计.docx(25页珍藏版)》请在冰豆网上搜索。
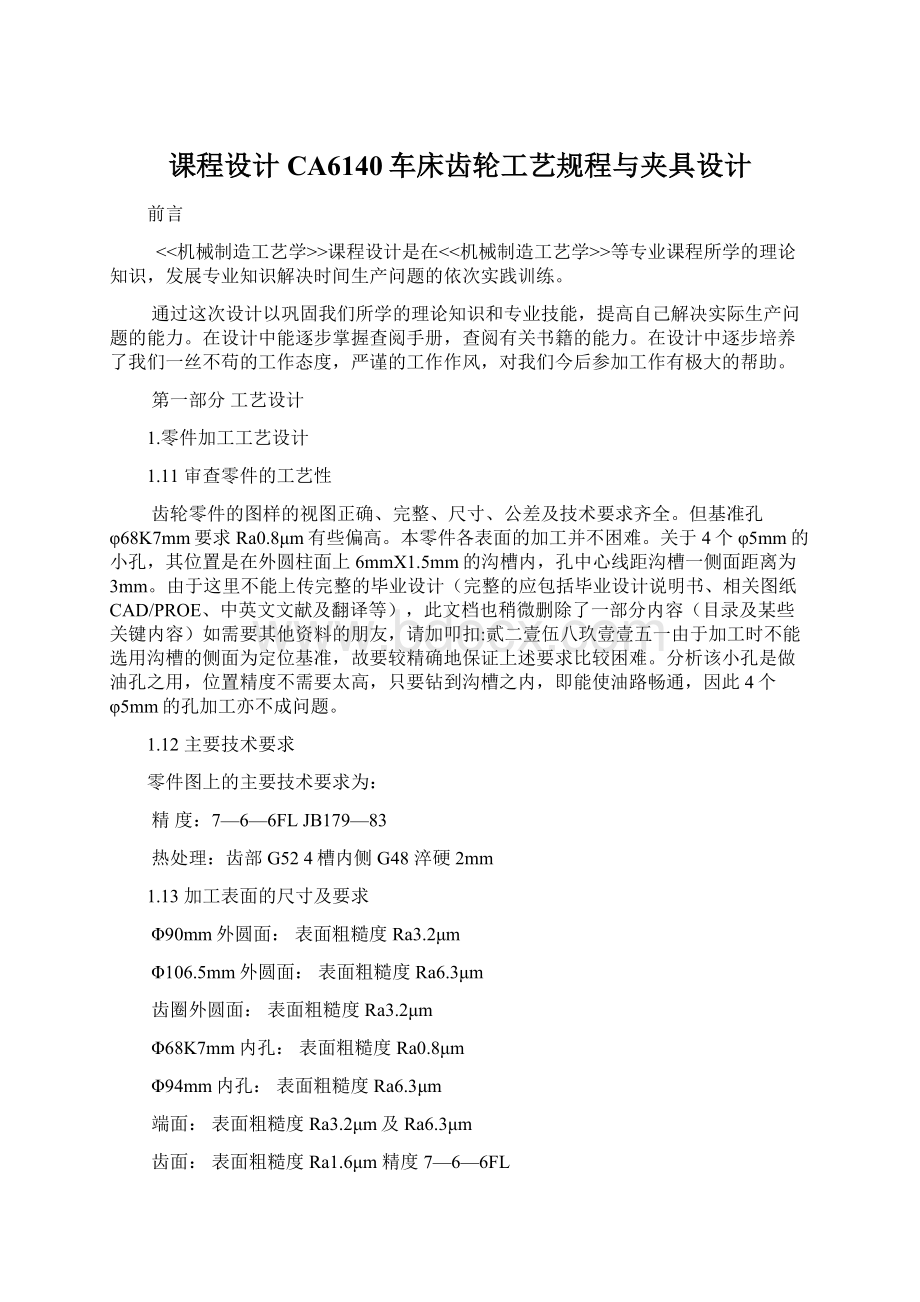
课程设计CA6140车床齿轮工艺规程与夹具设计
前言
<<机械制造工艺学>>课程设计是在<<机械制造工艺学>>等专业课程所学的理论知识,发展专业知识解决时间生产问题的依次实践训练。
通过这次设计以巩固我们所学的理论知识和专业技能,提高自己解决实际生产问题的能力。
在设计中能逐步掌握查阅手册,查阅有关书籍的能力。
在设计中逐步培养了我们一丝不苟的工作态度,严谨的工作作风,对我们今后参加工作有极大的帮助。
第一部分工艺设计
1.零件加工工艺设计
1.11审查零件的工艺性
齿轮零件的图样的视图正确、完整、尺寸、公差及技术要求齐全。
但基准孔φ68K7mm要求Ra0.8μm有些偏高。
本零件各表面的加工并不困难。
关于4个φ5mm的小孔,其位置是在外圆柱面上6mmX1.5mm的沟槽内,孔中心线距沟槽一侧面距离为3mm。
由于这里不能上传完整的毕业设计(完整的应包括毕业设计说明书、相关图纸CAD/PROE、中英文文献及翻译等),此文档也稍微删除了一部分内容(目录及某些关键内容)如需要其他资料的朋友,请加叩扣:
贰二壹伍八玖壹壹五一由于加工时不能选用沟槽的侧面为定位基准,故要较精确地保证上述要求比较困难。
分析该小孔是做油孔之用,位置精度不需要太高,只要钻到沟槽之内,即能使油路畅通,因此4个φ5mm的孔加工亦不成问题。
1.12主要技术要求
零件图上的主要技术要求为:
精度:
7—6—6FLJB179—83
热处理:
齿部G524槽内侧G48淬硬2mm
1.13加工表面的尺寸及要求
Φ90mm外圆面:
表面粗糙度Ra3.2μm
Φ106.5mm外圆面:
表面粗糙度Ra6.3μm
齿圈外圆面:
表面粗糙度Ra3.2μm
Φ68K7mm内孔:
表面粗糙度Ra0.8μm
Φ94mm内孔:
表面粗糙度Ra6.3μm
端面:
表面粗糙度Ra3.2μm及Ra6.3μm
齿面:
表面粗糙度Ra1.6μm精度7—6—6FL
槽:
表面粗糙度Ra3.2μm和Ra6.3μm
Φ5mm小孔:
表面粗糙度Ra2.5μm
1.14零件的材料
零件的材料为45钢
1.2选择毛坯的形状、尺寸、公差
齿轮是最常用的传动件,要求具有一定的强度。
该零件的材料为45钢,轮廓尺寸不大,形状亦不复杂,又属成批生产,做毛坯可采用模锻成型。
零件形状并不复杂,因此毛坯形状可以与零件的形状尽量接近。
即外形做成台阶形,内部孔锻出。
1.3定位基准的选择
本零件是带孔的盘状齿轮,孔是其设计基准(亦是装配基准和测量基准),为避免由于基准不重合而产生的误差,应选孔为定位基准,即遵循“基准重合”的原则。
具体而言,即选Φ68K7mm孔及一端面作为精基准。
由于本齿轮全部表面都需加工,而孔作为精基准应选进行加工,因此应选外圆及一端面为粗基准。
外圆Φ117h11表面不平整有飞边等缺陷,定位不可靠,故不能选为粗基准。
1.4零件表面加工方法的选择
本零件的加工面有外圆、内孔、端面、齿面、槽及小孔等,材料为45钢。
参考有关资料,其加工方法选择如下:
(1)Φ90mm外圆面:
为未标注公差尺寸,根据GB1800—79规定其公差等级为IT14,需进行粗车及半精车(见[1]表1.4-6)。
(2)齿圈外圆面:
公差等级为IT11,粗车、精车即可(见[1]表1.4-6)。
(3)Φ106.5mm外圆面:
公差等级为IT12,粗车即可(见[1]表1.4-6)。
(4)Φ68K7mm内孔:
公差等级为IT7,毛坯孔已锻出,为未淬火钢,根据[1]表1.4-7,又是大批量生产,故加工方法采用粗镗、半精镗、拉孔。
(5)Φ94mm内孔:
为未标注公差尺寸,公差等级按IT14,毛坯孔已锻出,只需粗镗即可(见[1]表1.4-7)。
(6)端面:
本零件的端面为回转体端面,尺寸精度都要求不高,表面粗糙度有两种要求。
要求Ra3.2μm的端面经粗车和半精车,要求Ra6.3μm的端面,经粗车即可。
([1]表1.4-8)
(7)齿面:
齿轮模数为2.2,齿数为50,采用AA级单头滚刀滚齿([1]表1.4-16、表1.4-17)。
(8)槽:
槽宽和槽深的公差等级分别为IT13和IT14,采用三面刃铣刀,粗铣、半精铣(参考[1]表1.4-8)。
(9)Φ5mm小孔:
采用复合钻头一次钻出即可。
1.5制订工艺路线
齿轮的加工工艺路线一般是先进行齿坯的加工,再进行齿面加工。
齿坯加工包括各圆柱表面及端面加工。
按照先加工基准面及先粗后精的原则,齿坯加工按下述工艺路线进行:
工序10:
以外圆Φ106.5mm及端面定位,粗车另一端面,粗车外圆Φ90mm及台阶面,粗车外圆Φ117mm,粗镗孔Φ68mm
工序20:
以粗车后的外圆Φ90mm及端面定位,粗车另一端面,粗车外圆Φ106.5mm及台阶面,车6mmX1.5mm沟槽,粗镗孔Φ94mm,倒角。
工序30:
以粗车后的外圆Φ106.5mm及端面定位,半精车另一端面,半精车外圆Φ90mm及台阶面,半精车外圆Φ117mm,半精镗孔Φ68K7,倒角。
工序40:
以外圆Φ90mm及端面定位,拉Φ68K7孔,镗孔内的沟槽,倒角。
工序50:
以Φ68K7孔及端面定位,滚齿,齿部淬火G52。
4个槽与4个小孔的加工安排在最后,考虑定位方便,应先铣槽后钻孔。
工序60:
以孔Φ68K7及端面定位,粗铣4个槽,4槽内侧淬火G48淬硬2mm。
工序70:
以孔Φ68K7、端面及粗铣后的一个槽定位,半精铣4个槽。
工序80:
以孔Φ68K7、端面及一个槽定位,钻4个小孔。
工序90:
钳工去毛刺。
工序100:
终检。
1.6确定工序机械加工余量、工序尺寸及公差
①本零件各圆柱表面的工序加工余量、工序尺寸及公差
加工表面
工序双边余量/mm
工序尺寸及公差/mm
粗
半精
精
粗
半精
精
Φ117h11外圆
2.5
1.5
—
Φ118.50-0.54
Φ1170-0.22
—
Φ106.50-0.4外圆
3.5
—
—
Φ106.50-0.4
—
—
Φ90外圆
2.5
1.5
—
Φ91.5
Φ90
—
Φ94孔
5
—
—
Φ94
—
—
Φ68K7孔
3
2
1
Φ65+0.190
Φ67+0.0740
Φ68+0.009-0.021
②确定轴向工序尺寸。
本零件各工序的轴向尺寸如下图:
a.确定各加工表面的工序加工余量
工序
加工表面
总加工余量
工序加工余量
Ⅰ
1
2
Z11=1.3
2
2
Z12=1.3
Ⅱ
3
1.7
Z32=1.7
4
1.7
Z42=1.7
5
1.7
Z52=1.7
Ⅲ
1
2
Z13=0.7
2
2
Z23=0.7
b.确定工序尺寸L13、L23、L5及L6。
该尺寸在工序20、工序30中应达到零件图样的要求,L13=64+0.50mm,L5=6mm,L6=2.5mm,L23=20mm。
c.确定工序尺寸L12、L11、L21。
这些尺寸只与加工余量有关,则
L12=L13+Z13=(66+0.7)mm=64.7mm
L11=L12+Z32=(64.7+1.7)mm=66.4mm
L21=L23+Z13-Z23=(20+0.7-0.7)=20mm
d.确定工序尺寸L3。
尺寸L3需解工艺尺寸链才能确定,工艺尺寸链如下图所示。
图中L7为未标注公差尺寸,其公差等级按IT14,查公差表得公差值为0.27mm,则L7=120-0.43mm。
根据尺寸链计算公式有
L7=L13-L23-L3
L3=L13-L23-L7=(64-20-12)mm=32mm
T7=T13+T23+T3(L7为封闭环)
由于T13=0.5mm,T7=0.43mm,不能满足尺寸公差的关系式,必须减小其公差。
现按加工方法的经济精度确定偏差,则L13=64mm,L23=20mm,L3作调整尺寸,L7=120-0.43mm求得L3=32+0.250mm.
e.确定工序尺寸L4。
工序尺寸L4亦需解工艺尺寸链才能确定。
工艺尺寸链如下图所示。
图中L8为零件图样上要求保证的尺寸33。
其公差值按公差等级IT13查表为0.39mm,L8=32mm。
解工艺尺寸链,其中L13=64mm,L8为封闭环。
得L4=31mm。
f.确定工序尺寸L11、L12、L21。
按加工方法的经济精度IT12及偏差入体原则,得L11=66.4mm,L12=64.7mm,L21=20mm。
g.确定铣槽的工序尺寸。
半精铣可达到零件图样的要求,则该工序尺寸:
槽宽16+0.280mm,槽深15mm。
粗铣时,为半精铣留有加工余量:
槽宽双边余量为2mm,槽深余量为2mm。
则粗铣的工艺尺寸:
槽宽为13mm,槽深13mm。
1.7选择机床设备及工艺装备
工序
机床设备
夹具
量具
切削刀具
工序10
CA6140
三爪自定心卡盘
游标卡尺
YT5900偏刀YT5镗刀
工序20
CA6140
三爪自定心卡盘
YT5900偏刀YT5450外圆车刀YT5镗刀切槽刀
工序30
CA6140
三爪自定心卡盘
游标卡尺深度百分尺外径百分尺内径百分尺
YT15900偏刀YT5镗刀倒角刀
工序40
卧式内拉床
CA6140
三爪自定心卡盘
圆柱塞规
拉刀切槽刀倒角刀
工序50
Y3150
心轴
公法线百分表
AA级单头滚刀滚齿
工序60
X6132
铣床夹具
游标卡尺
高速钢错齿三面刃铣刀(Φ125)
工序70
X6132
铣床夹具
游标卡尺
高速钢错齿三面刃铣刀
工序80
Z518
钻床夹具
高速钢麻花钻Φ5`锪钻
2.填写工艺文件
按以上确定的工艺规程填写机械加工工艺卡和工序卡
第二部分夹具的设计
1.设计任务
设计加工孔Φ5的钻床夹具
2.确定定位方案、选择定位元件
孔Φ5需要限制6个自由度,完全定位。
3.夹紧机构的选择与设计
夹紧机构有斜楔行夹紧机构、螺旋夹紧机构、偏心夹紧机构、铰链夹紧机构、联动夹紧机构等。
该孔加工为钻孔加工,钻孔的冲击力较大,震动较大,所以不适合偏心夹紧机构、斜楔行夹紧机构。
联动夹紧机构的结构比较复杂,这里选择螺旋夹紧机构。
4.对刀装置的选择
在加工中要确定孔的位置。
选用钻套对刀,选择GB2262-1991钻套。
5.夹具在机床上的定位与夹紧
夹具用支撑架可限制6个自由度,使用紧固螺旋夹紧。
专题论文
夹具在现代工程技术中的应用
李超
(黑龙江科技学院哈尔滨市150027)
摘要:
本文主要介绍了固定夹具、随行夹具、组合夹具、通用夹具、成组夹具等现代制造工程中常用夹具的结构特点及应用。
明确了现代机床夹具的发展方向以及现代制造业对夹具设计制造的基本要求。
关键词:
随行夹具、组合夹具、通用夹具、成组夹具
Abstract:
Thistextmainlyintroducedfixedfixture,withgo
fixture,theassemblyfixture,ingeneralusefixtureandbecomethesetfixtureetc.modernproductionthestructurecharacteristicsandapplicationoftheincommonusefixtureintheengineering.Explicitbasicrequestofthedevelopmentdirectionandmodernmanufacturingindustryofthemodernenginebedfixturetothefixturedesignproduction.
Keyword:
Withgofixture,theassemblyfixture,ingeneralusefixtureandbecomesetfixture
1绪论
在机械制造业中,为了保证产品的质量,改善工人的作业条件,提高劳动生产率,在产品的制造工艺过程中,除了使用机床等设备外还需要夹具、刀具、量具等多种工艺装备,所以从广义上说,夹具是一种保证产品的加工质量,提高工艺过程效率的工艺装备,但同时也是机床的辅助装置,近年来,随着先进制造技术的发展,新型机床的出现,夹具的设计、制造也产生了很大的变化。
现代科学技术的高速发展和社会需求的不断变化,使得多品种,中小批量生产逐渐占优势,因此,在大批量生产中有着长足优势的专用夹具逐渐暴露出它的不足,因而为适应多品种、中小批量生发展了组合夹具、通用可调夹具和成组夹具,由于数控技术的发展,数控机床在机械制造工程中有了广泛的应用,数控机床夹具也随之发展起来,并在现代机床夹具中占有了一定的地位。
现代机床夹具虽然各具特色,但它们的定位、夹紧的原理以及组成都是和传统夹具相同的。
夹具组成和工作原理:
夹具主要有定位元件、夹紧元件和装置、对刀及导向元件、夹具体和连接元件组成。
夹具就是用来装夹工件的,装夹就是将工件在机床和夹具中进行定位和夹紧的过程,定位是为了确定工件在机床或夹具中的正确位置,夹紧是为了定位后将工件压紧、夹牢,是其在加工过程中保持定位位置的不变,这样工件在切削力、重力、离心力、和惯性力的作用下就能保证定位时所获得位置不变。
2专题正文
2.1固定夹具和随行夹具在自动线上的应用
自动线夹具的种类主要有固定夹具和随行夹具两大类。
1、固定夹具用于工件直接运输的生产自动线上,通常要求工件具有良好的定位和输送基面,例如箱体零件、轴承环等。
这类夹具和一般机车夹具相似,在结构上具有自动定位、夹紧装置,设计原则上应保证工件输送方便,夹紧、定位可靠与切屑的顺利排除。
2、随行夹具随行夹具用于工件间接输送的自动线,主要适用于工件形状复杂、没有合适的输送基面,或者随有合适的输送基面,但属于易磨损的非铸材料工件,使用随行夹具可以避免表面划伤与磨损。
工件装在随行夹具上,自动线的输送机构带着随行夹具依次输送到自动线的各个加工位置上,各个加工位置的机床的上都有一个相同的机床夹具来定位和夹紧该随行夹具,所以,自动线上应有许多随行夹具在机床的加工位置上进行加工,另有一些要进入装卸工位,卸下加工好的工件,装好待加工的毛坯件,这些随行夹具也等待送入机床工作位置进行加工的指令,就这样不停地循环工作。
随行夹具在自动线上的输送和返回系统是生产自动线设计的一个十分重要的环节,随行夹具的返回方式有垂直下方返回,垂直上方返回、斜上方或斜下方和水平返回方式。
根据随行夹具的尺寸、返回系统的占地面积、输送装置的复杂程度操作、和机床刚性等因素来选择不同的随行夹具的返回系统。
图
(1)是垂直上方返回的系统图。
图
(1)随行夹具的垂直返回系统
其中1、随行夹具2、随行夹具输送器3、7、升降台4、推杆5、倾斜返回轨道6、限位器。
如图
(2)所示为活塞加工自动线的随行夹具,工件以止口端面和两半圆定位在随行夹具1的环形布置的10个定位块6和定位销2、4上定位,但不夹紧。
待随行夹具到达加工位置时,将工件和随行夹具一起夹紧在机床夹具上。
随行夹具上的T型槽在T型输送轨道上移动,到达加工位置时,机床夹具的定位销插入随行夹具的定位套5的孔中实现定心,盖板3防止切屑落入定位孔中。
采用这种夹紧方法必须保证工件在随行夹具的运送过程中不出现任何位移。
图
(2)活塞加工自动线上的随行夹具
1、随行夹具2、4、定位销5、定位套6、定位块
由于随行夹具在生产自动线中不断地流动,因此在随行夹具中大多采用螺旋夹紧机构来夹紧工件,因为螺旋夹紧机构自锁性能好,在随行夹具的输送过程中不容易松动。
而随行夹具在机床夹具常采用“一面两孔”的定位方式,利用随行夹具的周边进行夹紧。
随行夹具的底面既是定位基面又是输送基面。
所以必须有一定的耐磨性以保证定位准确,并能长久地保持精度。
随行夹具在自动线上循环输送,它同时也带着切屑和切削液进入各个加工位置,因而也影响了随行夹具的精确定位,所以必要采取一定的防护措施,常在自动线末端或返回输送带上设置清洗工位。
随行夹具多采用“一面两孔”的统一定位方法,又需要成批制造,因此实现随行夹具的结构的通用化有十分重要的意义,但自动线加工对象各不相同,要使整个随行夹具的结构通用化困难较大,为此可以将随行夹具分为通用底板和专用结构两部分。
这样不但使随行夹具结构通用化,而且也使自动线的机床夹具、随行夹具的输送装置结构通用化,从而提高整个自动线的通用化程度,缩短自动线的设计制造周期,降低制造成本。
2.2组合夹具的应用
组合夹具在夹具元件高度标准化、通用化、系列化的基础上发展起来的一种夹具。
这种夹具我国是从20世纪50年代后期开始使用的,到60年代得到了发展。
组合夹具由一套预先制造好的,具有各种形状、功用、规格、和系列尺寸的标准元件和组件组成,如基础件、支承件、定位件、导向件、压紧件、紧固件等。
根据工件的加工要求,利用这些标准元件和组件组装成不同的夹具。
图三是钻斜孔的组合夹具,其中图a是工件,在其上钻Φ3斜孔。
工件以背面在支承件上定位,底面则支承在一定位销和一定盘上。
根据斜角要
图(3)a工件图
图(3)b钻斜孔组合夹具
1、基础件2、支承件3、定位件4、导向减5、压紧件6、紧固件
求,按正弦定理可以计算出定位销轴线和定位盘轴线间的垂直与水平距离尺寸,工件右端则由挡销定位。
斜孔加工需要有确定钻摸板上钻套轴线位置的工艺孔,在此组合夹具中可利用定位盘兼作工艺辅助基准,计算出定位盘
轴线到钻套轴线的水平距离尺寸。
按此尺寸要求调整钻模板,即可保证斜孔轴线47和18两个位置尺寸。
对多品种、中小批量生产,使用专用夹具是不经济的。
但对一些加工质量要求高的关键零件,不采用夹具又难以保证加工质量,采用组合家具就可以解决这一问题,特别是对于新产品试制和产品对象经常变换不定的生产,采用组合夹具不会因试制后产品改型或加工对象变换造成原来使用的夹具报废。
采用组合夹具即能保证产品加工质量,提高效率,又能节约使用夹具的费用,充分发挥了组合夹具的优势。
由于夹具设计、制造劳动量在整个生产准备工作中占有较大的比例。
采用组合夹具后不需要专门的设计制造夹具,节约了设计和制造夹具所需要的工时、材料和制造费用,缩短了生产准备周期。
2.3通用可调夹具和成组夹具的应用
专用夹具和组合夹具各有优缺点,如果将这两种夹具的优势结合起来,既能发挥专用夹具精度高的优点,又能发挥组合夹具成本低的特点,这就发展了通用可调夹具。
其原理是通过调节或更换装在通用底座上的某些可调节或可更换元件,以装夹多种不同类的夹具的工件;而成组夹具则是根据成组工艺的原则,针对一组相似零件而设计的有通用底座和可调节或可更换元件的夹具。
从结构上看二者十分相似,都具有通用底座固定部分和和可调节和更换部分,但是二者的设计原则不同。
在设计时通用可调夹具的应用对象不明确,只提出了一个大概的加工规格和范围;而成组夹具是根据成组工艺,针对某一零件的加工而设计的,它的应用对象是十分明确的。
如图4-57是通用可调铣床夹具的可换前口的调整图,其通用底座可以固定在铣床的工作台上,而钳口可以根据不同的加工要求进行设计和更换。
2.4夹具在数控机床上的应用
数控机床的特点是在加工时,机床、刀具、夹具和工件之间应有严格的坐标位置,所以数控机床夹具在机床上应相对数控机床的坐标原点具有严格的坐标位置,以保证所装夹的工件处于规定的坐标位置上。
为此数控机床夹具常采用网格状的固定基础板,并将它长期固定在数控机床的工作台上,板上加工出有准确孔心距位置的一组定位孔和一组紧固螺孔,它们成网络分布。
网络基础板预先调整好相对数控机床的坐标位置。
利用基础板上的定位孔可以安装各种夹具,当加工零件的对象发生变化时,只需要改变网络板上的相应的夹具就可以了。
生产中也经常常立方固定基础板。
它安装在数控机床工作台的转台上,其四面都有分布的定位孔和紧固螺孔,上面可安装各类夹具的底版。
当加工对象变换时,只需转台转位,便可以迅速转换到加工新的零件用的夹具上,十分方便。
数控机床的夹紧装置要求结构简单紧凑、体积小、采用机动夹紧方式,以满足数控加工的要求。
近十年来国内外常采用高压(10-25MPa)小流量液压夹紧系统,由于压力较高,可省去中间增力机构。
工件液压采用小直径(Φ10-50mm)单作用液压缸,结构紧凑,而零部件设计成单元式结构,在夹具底座上变换安装位置十分容易。
数控机床夹具实质上是通用可调夹具和组合夹具的结合和发展,它的固定基础板部分和可换部分的组合是通用可调夹具组成原理的应用,而它的元件和组件高度标准化和组合化,又是组合夹具标准元件的演变和发展。
3结束语
总之,现代工程技术中所经常使用的夹具逐渐向着标准化、可调化、组合化、精密化、模块化、高效自动化的方向发展着,但是在定位、夹紧以及组成原理等方面和常用的普通夹具是没有什么差别的。
4经济性与资源分析
经济性是机械产品的一个重要指标之一,在产品产品的整个生命周期内,包括原材料制备、设计、制造、包装、运输、使用、回收或再生过程,都应该始终贯彻经济性原则,尽量地节约能源和资源,降低生产成本,提高劳动省生产率。
在该夹具的设计过程中,在满足夹具使用要求的前提下,充分地考虑了夹具的经济性,利用了现有的资源,主要体现在以下几个方面。
(1)合理地选择了各部分零件的材料,充分地发挥了它们的性能。
以不至于大材小用,造成材料的浪费。
如夹具底座比较大,形状复杂,要求精度高,加工比较困难,选用铸铁材料HT20-40。
因为铸铁可以研磨角度面,达到要求精度;铸铁材料的刚性比较好,还可以吸收拉削过程中产生的震动。
分度销主要承受剪切力,所以材料选用40Cr,热处理 HRC33-38,韧性好。
(2)夹具整体结构尽量紧凑、合理。
为保障零件的加工精度,提高生产效率,在夹具上设计了很多辅助机构,在夹具的设计过程中,对这些辅助机构作了合理的布局,把它们放在合理的位置,避免了整个夹具的体积庞大,造成资源的浪费。
并且该夹具的分度和夹紧机构均采用了液压机构,有行程开关控制,降低了工人的劳动强度,提高了生产率,而且便于实现自动化。
(3)在加工设备的选择时,在能满足加工要求的条件下选用了现有的卧式拉床L6120、移动安装座及辅助液压系统,其中移动安装座起到了连接拉床和夹具的作用,相当于转接头,更有利于夹具的安装。
(4)尽量把夹具中部件模块化,以节约资源,扩大夹具的适用范围,更有利于以后的回收、利用。
在该夹具的分度装置的设计过程中,将分度装置设计成端齿盘和分度盘两部分,一方面是为了便于加工,另一方面是为了扩大夹具的适用范围,如在拉削53个榫槽的发动机涡轮盘时,就可以将分度盘换成53个分度销的分度盘,在调整部分辅助装置的位置就可以了。
参考文献
1狄瑞春、潘晓红主编.机械制造工艺学.浙江大学出版社.2004:
175-209
2华茂发主编.机械制造技术.机械工业出版社.2004:
298-305
3寒秋实主编.机械制造技术基础.机械工业出版社.2005:
142-322
4王先奎主编.机械制造工艺学.机械工业出版社.2003:
90-157
5王隆太主编.先进制造技术.机械工业出版社.2003:
112-156
附录1中文译文
柔性制造系统
介绍对制造系统和先进的制造业的技术的讨论,对定义制造系统这一术语是用的。
一个制造系统可以被定义为一系列的把原材料转换成有用的形式和