第4章 制 气.docx
《第4章 制 气.docx》由会员分享,可在线阅读,更多相关《第4章 制 气.docx(17页珍藏版)》请在冰豆网上搜索。
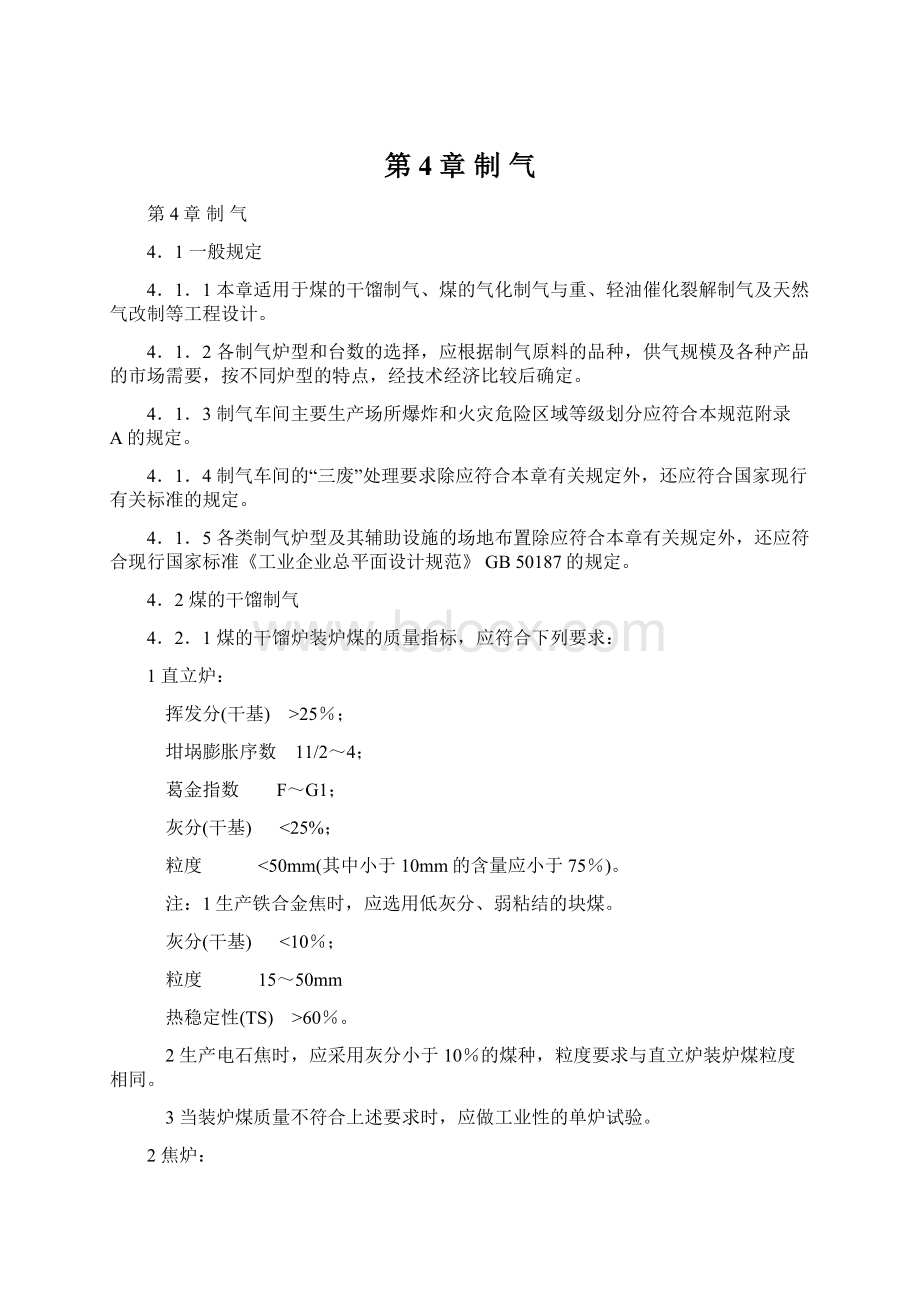
第4章制气
第4章制气
4.1一般规定
4.1.1本章适用于煤的干馏制气、煤的气化制气与重、轻油催化裂解制气及天然气改制等工程设计。
4.1.2各制气炉型和台数的选择,应根据制气原料的品种,供气规模及各种产品的市场需要,按不同炉型的特点,经技术经济比较后确定。
4.1.3制气车间主要生产场所爆炸和火灾危险区域等级划分应符合本规范附录A的规定。
4.1.4制气车间的“三废”处理要求除应符合本章有关规定外,还应符合国家现行有关标准的规定。
4.1.5各类制气炉型及其辅助设施的场地布置除应符合本章有关规定外,还应符合现行国家标准《工业企业总平面设计规范》GB50187的规定。
4.2煤的干馏制气
4.2.1煤的干馏炉装炉煤的质量指标,应符合下列要求:
1直立炉:
挥发分(干基) >25%;
坩埚膨胀序数 11/2~4;
葛金指数 F~G1;
灰分(干基) <25%;
粒度 <50mm(其中小于10mm的含量应小于75%)。
注:
1生产铁合金焦时,应选用低灰分、弱粘结的块煤。
灰分(干基) <10%;
粒度 15~50mm
热稳定性(TS) >60%。
2生产电石焦时,应采用灰分小于10%的煤种,粒度要求与直立炉装炉煤粒度相同。
3 当装炉煤质量不符合上述要求时,应做工业性的单炉试验。
2焦炉:
挥发分(干基) 24%~32%;
胶质层指数(Y) 13~20mm;
焦块最终收缩度(X) 28~33mm;
粘结指数 58~72;
水分 <10%;
灰分(干基) ≤11%;
硫分(干基) <1%;
粒度(<3mm的含量) 75%~80%。
注:
1指标仅给出范围,最终指标应按配煤试验结果确定。
2采用焦炉炼制气焦时,其灰分(干基)可小于16%。
3采用焦炉炼制冶金焦或铸造焦时,应按焦炭的质量要求决定配煤的质量指标。
4.2.2采用直立炉制气的煤准备流程应设破碎和配煤装置。
采用焦炉制气的煤准备宜采取先配煤后粉碎流程。
4.2.3原料煤的装卸和倒运应采用机械化运输设备。
卸煤设备的能力,应按日用煤量、供煤不均衡程度和供煤协议的卸煤时间确定。
4.2.4储煤场地的操作容量应根据来煤方式不同,宜按10~40d的用煤量确定。
其操作容量系数,宜取65%~70%。
4.2.5配煤槽和粉碎机室的设计,应符合下列要求:
1配煤槽总容量,应根据日用煤量和允许的检修时间等因素确定;
2配煤槽的个数,应根据采用的煤种数和配煤比等因素确定;
3在粉碎装置前,必须设置电磁分离器;
4粉碎机室必须设置除尘装置和其他防尘措施,室内含尘量应小于10mg/m3;
排入室外大气中的粉尘最高允许浓度标准为150mg/m3;
5粉碎机应采用隔声、消声、吸声、减振以及综合控制噪声等措施,生产车间及作业场所的噪声A声级不得超过90dB。
4.2.6煤准备流程的各胶带运输机及其相连的运转设备之间,应设连锁集中控制装置。
4.2.7每座直立炉顶层的储煤仓总容量,宜按36h用煤量计算。
辅助煤箱的总容量,应按2h用煤量计算。
储焦仓的总容量,宜按一次加满四门炭化室的装焦量计算。
焦炉的储煤塔,宜按两座炉共用一个储煤塔设计,其总容量应按12~16h用煤量计算。
4.2.8煤干馏的主要产品的产率指标,可按表4.2.8采用。
表4.2.8煤干馏的主要产品的产率指标
主要产品名称
直立炉
焦炉
煤气
350~380m3/t
320~340m3/t
全焦
71%~74%
72%~76%
焦油
3.3%~3.7%
3.2%~3.7%
硫铵
O.9%
1.O%
粗苯
O.8%
1.00%
注:
1直立炉煤气其低热值为16.3MJ/m3;
2焦炉煤气其低热值为17.9MJ/m3;
3直立炉水分按7%的煤计;
4焦炉按干煤计。
4.2.9焦炉的加热煤气系统,宜采用复热式。
4.2.10煤干馏炉的加热煤气,宜采用发生炉(含两段发生炉)或高炉煤气。
发生炉煤气热值应符合现行国家标准《发生炉煤气站设计规范》GB50195的规定。
煤干馏炉的耗热量指标,宜按表4.2.10选用。
表4.2.10煤干馏炉的耗热量指标[kJ/kg(煤)]
加热煤气种类
焦炉
直立炉
适用范围
焦炉煤气
2340
-
作为计算生产消耗用
发生炉煤气
2640
3010
焦炉煤气
2570
-
作为计算加热系统设备用
发生炉煤气
2850
-
注:
1直立炉的指标系按炭化室长度为2.1m炉型所耗发生炉热煤气计算。
焦炉的指标系按炭化室有效容积大于20m3炉型所耗冷煤气计算。
2水分按7%的煤计。
4.2.11加热煤气管道的设计应符合下列要求:
1 当焦炉采用发生炉煤气加热时,加热煤气管道上宜设置混入回炉煤气装置;当焦炉采用回炉煤气加热时,加热煤气管道上宜设置煤气预热器;
2应设置压力自动调节装置和流量计;
3必须设置低压报警信号装置,其取压点应设在压力自动调节装置的蝶阀前的总管上。
管道末端应设爆破膜;
4应设置蒸汽清扫和水封装置;
5加热煤气的总管的敷设,宜采用架空方式。
4.2.12直立炉、焦炉桥管上必须设置低压氨水喷洒装置。
直立炉的荒煤气管或焦炉集气管上必须设置煤气放散管,放散管出口应设点火燃烧装置。
焦炉上升管盖及桥管与水封阀承插处应采用水封装置。
4.2.13炉顶荒煤气管,应设压力自动调节装置。
调节阀前必须设置氨水喷洒设施。
调节蝶阀与煤气鼓风机室应有联系信号和自控装置。
4.2.14直立炉炉顶捣炉与炉底放焦之间应有联系信号。
焦炉的推焦车、拦焦车、熄焦车的电机车之间宜设置可靠的连锁装置以及熄焦车控制推焦杆的事故刹车装置。
4.2.15焦炉宜设上升管隔热装置和高压氨水消烟加煤装置。
4.2.16氨水喷洒系统的设计,应符合下列要求:
1低压氨水的喷洒压力,不应低于0.15MPa。
氨水的总耗用量指标应按直立炉4m3/t(煤)、焦炉6~8m3/t(煤)选用;
2直立炉的氨水总管,应布置成环形;
3低压氨水应设事故用水管;
4焦炉消烟装煤用高压氨水的总耗用量为低压氨水总耗用量的3.4%~3.6%,其喷洒压力应按1.5~2.7MPa设计。
注:
1直立炉水分按7%的煤计;
2焦炉按干煤计。
4.2.17直立炉废热锅炉的设置应符合下列规定:
1每座直立炉的废热锅炉,应设置在废气总管附近;
2废热锅炉的废气进口温度,宜取800~900℃,废气出口温度宜取200℃;
3废热锅炉宜设置1台备用;
4废热锅炉应有清灰与检修的空间;
5废热锅炉的引风机应采取防振措施。
4.2.18直立炉排焦和熄焦系统的设计应符合下列要求:
1直立炉应采用连续的水熄焦,熄焦水的总管,应布置成环形。
熄焦水应循环使用,其用水量宜按3~4m3/t(水分为7%的煤)计算;
2排焦传动装置应采用调速电机控制;
3排焦箱的容量,宜按4h的排焦量计算;
采用弱粘结性煤时,排焦箱上应设排焦控制器;
4排焦门的启闭,宜采用机械化装置;
5排出的焦炭运出车间以前,应有大于80s的沥水时间。
4.2.19焦炉可采用湿法熄焦和干法熄焦两种方式。
当采用湿法熄焦时应设自动控制装置,在熄焦塔内应设置捕尘装置。
熄焦水应循环使用,其用水量宜按2m3/t(干煤)计算。
熄焦时间宜为90~120s。
粉焦沉淀池的有效容积应保证熄焦水有足够的沉淀时间。
清除粉焦沉淀池内的粉焦应采用机械化设施。
大型焦化厂有条件的应采用干法熄焦装置。
4.2.20 当熄焦使用生化尾水时,其水质应符合下列要求:
酚≤0.5mg/L;
CN-≤0.5mg/L;
CODcr≈350mg/L。
4.2.21焦炉的焦台设计宜符合下列要求:
1每两座焦炉宜设置1个焦台;
2焦台的宽度,宜为炭化室高度的2倍;
3焦台上焦炭的停留时间,不宜小于30min;
4焦台的水平倾角,宜为28°。
4.2.22焦炭处理系统,宜设置筛焦楼及其储焦场地或储焦设施。
筛焦楼内应设有除尘通风设施。
焦炭筛分设施,宜按筛分后的粒度大于40mm、40~25mm、25~10mm和小于10mm,共4级设计。
注:
生产冶金、铸造焦时,焦炭筛分设施宜增加大于60m或80mm的一级。
生产铁合金焦时,焦炭筛分设施宜增加10~5mm和小于5mm两级。
4.2.23筛焦楼内储焦仓总容量的确定,应符合下列要求:
1直立炉的储焦仓,宜按10~12h产焦量计算;
2焦炉的储焦仓,宜按6~8h产焦量计算。
4.2.24储焦场的地面,应做人工地坪并应设排水设施。
4.2.25独立炼焦制气厂储焦场的操作容量宜按焦炭销售运输方式不同采用15~20d产焦量。
4.2.26 自产的中、小块气焦,宜用于生产发生炉煤气。
自产的大块气焦,宜用于生产水煤气。
4.3煤的气化制气
4.3.1本节适用于下列炉型的煤的气化制气:
1煤气发生炉;两段煤气发生炉;
2水煤气发生炉;两段水煤气发生炉;
3流化床水煤气炉。
注:
1煤气发生炉、两段煤气发生炉为连续气化炉;水煤气发生炉、两段水煤气发生炉、流化床水煤气炉为循环气化炉。
2鲁奇高压气化炉暂不包括在本规范内。
4.3.2煤的气化制气宜作为人工煤气气源厂的辅助(加热)和掺混用气源。
当作为城市的主气源时。
必须采取有效措施,使煤气组分中一氧化碳含量和煤气热值等达到现行国家标准《人工煤气》GB13612质量标准。
4.3.3气化用煤的主要质量指标宜符合表4.3.3的规定。
表4.3.3气化用煤主要质量指标
指标项目
煤气发生炉
两段煤气发生炉
水煤气发生炉
两段水煤气发生炉
流化床水煤气炉
粒度(mm)
-
-
-
-
-
1无烟煤
6~13,13~25,25~50
-
25~100
-
O~13
2烟煤
-
20~40,25~50,30~60
-
20~40,25~50,30~60
其中1以下<10%,大于13<15%
3焦炭
6~10,10~25.25~40
-
25~100
-
质量指标
-
-
-
-
-
1 灰分(干基)
<35%(气焦)
<25%(烟煤)
<33%(气焦)
25%(烟煤)
-
<24%(无烟煤)
-
<24%(无烟煤)
-
<35%(各煤)
2 热稳定性(TS)+6
>60%
>60%
>60%
>60%
>45%
3抗碎强度(粒度大于25mm)
>60%
>60%
>60%
>60%
-
质量指标
-
-
-
-
-
4灰熔点
>1200℃(冷煤气)
>1250℃
>1300℃
>1250℃
>1200℃
(ST)
>1250℃(热煤气)
-
-
-
-
5全硫(干基)
<1%
<1%
<1%
<1%
<1%
6挥发分(干基)
-
>20%
<9%
>20%
-
7罗加指数(R.I)
-
≤20
-
≤20
<45
8自由膨胀序数(F.S.I)
-
≤2
-
≤2
-
9煤的化学反应性(a)
-
-
-
-
>30%(1000℃时)
注:
1发生炉入炉的无烟煤或焦炭,粒度可放宽选用相邻两级。
2两段煤气发生炉、两段水煤气发生炉用煤粒度限使用其中的一级。
4.3.4煤场的储煤量,应根据煤源远近、供应的不均衡性和交通运输方式等条件确定,宜采用1O~30d的用煤量;当作为辅助、调峰气源使用本厂焦炭时,宜小于1d的用焦量。
4.3.5 当气化炉按三班制时,储煤斗的有效储量应符合表4.3.5的要求。
表4.3.5储煤斗的有效储量
备煤系统工作班制
储煤斗的有效储量
一班工作
20~22h气化炉用煤量
二班工作
14~16h气化炉用煤量
注:
1备煤系统不宜按三班工作。
2用煤量应按设计产量计算。
4.3.6煤气化后的灰渣宜采用机械化处理措施并进行综合利用。
4.3.7煤气化炉煤气低热值应符合下列规定:
1煤气发生炉,不应小于5MJ/m3。
2两段发生炉,上段煤气不应小于6.7MJ/m3;
下段煤气不应大于5.44MJ/m3。
3水煤气发生炉,不应小于10MJ/m3。
4两段水煤气发生炉,上段煤气不应小于13.5M/m3;
下段煤气不应大于10.8MJ/m3。
5流化床水煤气炉,宜为9.4~11.3MJ/m3。
4.3.8气化炉吨煤产气率指标,应根据选用的煤气发生炉炉型、煤种、粒度等因素综合考虑后确定。
对曾用于气化的煤种,应采用其平均产气率指标;对未曾用于气化的煤种,应根据其气化试验报告的产气率确定。
当缺乏条件时,可按表4.3.8选用。
表4.3.8气化炉煤气产气率指标
原料
产气率(m3/t)(干基)
煤气发生炉
两段煤气发生炉
水煤气发生炉
两段水煤气发生炉
流化床水煤气炉
灰分含量
无烟煤
3000~3400
-
1500~1700
-
-
15%~25%
烟煤
-
2600~3000
-
800~11OO
18%~25%
焦炭
3100~3400
-
1500~1650
-
900~1000
13%~21%
气焦
2600~3000
-
1300~1500
-
25%~35%
4.3.9气化炉组工作台数每1~4台宜另设一台备用。
4.3.10水煤气发生炉、两段水煤气发生炉,每3台宜编为1组;流化床水煤气炉每2台宜编为1组;合用一套煤气冷却系统和废气处理及鼓风设备。
4.3.12循环气化炉的煤气缓冲罐宜采用直立式低压储气罐,其容积宜为O.5~1倍煤气小时产气量。
4.3.13循环气化炉的蒸汽系统中应设置蒸汽蓄能器,并宜设有备用的蒸汽系统。
4.3.14煤气排送机和空气鼓风机的并联工作台数不宜超过3台,并应另设一台备用。
4.3.15作为加热和掺混用的气化炉冷煤气温度宜小于35℃,其灰尘和液态焦油等杂质含量应小于20mg/m3;气化炉热煤气至用气设备前温度不应小于350℃,其灰尘含量应小于300mg/m3。
4.3.16采用无烟煤或焦炭作原料的气化炉,煤气系统中的电气滤清器应设有冲洗装置或能连续形成水膜的湿式装置。
4.3.17煤气的冷却宜采用直接冷却。
冷却用水和洗涤用水应采用封闭循环系统。
冷循环水进口温度不宜大于28℃,热循环水进口温度不宜小于55℃。
4.3.18废热锅炉和生产蒸汽的水夹套,其给水水质应符合现行的国家标准《工业锅炉水质标准》GB1576中关于锅壳锅炉水质标准的规定。
4.3.19 当水夹套中水温小于或等于100℃时,给水水质应符合现行的国家标准《工业锅炉水质标准》GB1576中关于热水锅炉水质标准的规定。
4.3.20煤气净化设备、废热锅炉及管道应设放散管和吹扫管接头,其位置应能使设备内的介质吹净;当净化设备相联处无隔断装置时,可仅在较高的设备上装设放散管。
设备和煤气管道放散管的接管上,应设取样嘴。
4.3.21放散管管口高度应符合下列要求:
1高出管道和设备及其走台4m,并距地面高度不小于10m;
2厂房内或距厂房10m以内的煤气管道和设备上的放散管管口,应高出厂房顶4m。
4.3.22煤气系统中应设置可靠的隔断煤气装置,并应设置相应的操作平台。
4.3.23在电气滤清器上必须装有爆破阀。
洗涤塔上宜设有爆破阀,其装设位置应符合下列要求:
1装在设备薄弱处或易受爆破气浪直接冲击的位置:
2离操作面的净空高度小于2m时,应设有防护措施;
3爆破阀的泄压口不应正对建筑物的门或窗。
4.3.24厂区煤气管道与空气管道应架空敷设。
热煤气管道上应设有清灰装置。
4.3.25空气总管末端应设有爆破膜。
煤气排送机前的低压煤气总管上,应设爆破阀或泄压水封。
4.3.26煤气设备水封的高度,不应小于表4.3.26的规定。
表4.3.26煤气设备水封有效高度
最大工作压力(Pa)
水封的有效高度(mm)
<3000
最大工作压力(以Pa表示)×0.1+150,但不得小于250
3000~10000
最大工作压力(以Pa表示)×0.1×1.5
>lO000
最大工作压力(以Pa表示)×0.1+500
注:
发生炉煤气钟罩阀的放散水封的有效高度应等于煤气发生炉出口最大工作压力(以Pa表示)乘0.1加50mm。
4.3.27 生产系统的仪表和自动控制装置的设置应符合下列规定:
1宜设置空气、蒸汽、给水和煤气等介质的计量装置;
2宜设置气化炉进口空气压力检测仪表;
3宜设置循环气化炉鼓风机的压力、温度测量仪表;
4宜设置连续气化炉进口饱和空气温度及其自动调节;
5宜设置气化炉进口蒸汽和出口煤气的温度及压力检测仪表;
6宜设置两段炉上段出口煤气温度自动调节;
7应设置汽包水位自动调节;
8应设置循环气化炉的缓冲气罐的高、低位限位器分别与自动控制机和煤气排送机连锁装置,并应设报警装置;
9应设置循环气化炉的高压水罐压力与自动控制机连锁装置,并应设报警装置;
10应设置连续气化炉的煤气排送机(或热煤气直接用户如直立炉的引风机)与空气总管压力或空气鼓风机连锁装置。
并应设报警装置;
11应设置当煤气中含氧量大于1%(体积)或电气滤清器的绝缘箱温度低于规定值、或电气滤清器出口煤气压力下降到规定值时,能立即切断高压电源装置,并应设报警装置;
12应设置连续气化炉的低压煤气总管压力与煤气排送机连锁装置。
并应设报警装置;
13应设置气化炉的加煤的自动控制、除灰加煤的相互连锁及报警装置;
14循环气化系统应设置自动程序控制装置。
4.4重油低压间歇循环催化裂解制气
4.4.1 重油制气用原料油的质量,宜符合下列要求:
碳氢比 (C/H)<7.5;
残炭 <12%;
开口闪点 >120℃;
密度 900~970kg/m3。
4.4.2原料重油的储存量,宜按15~20d的用油量计算,原料重油的储罐数量不应少于2个。
4.4.3重油低压间歇循环制气应采用催化裂解工艺,其炉型宜采用三筒炉。
4.4.4重油低压间歇循环催化裂解制气工艺主要设计参数宜符合下列要求:
1 反应器液体空间速度:
0.60~0.65m3/(m3·h);
2反应器内催化剂层高度:
O.6~0.7m;
3燃烧室热强度:
5000~7000MJ/(m3·h);
4加热油用量占总用油量比例:
小于16%;
5过程蒸汽量与制气油量之比值:
1.0~1.2(质量比);
6循环时间:
8min;
7每吨重油的催化裂解产品产率可按下列指标采用:
煤气:
1100~1200m3(低热值按21MJ/m3计);
粗苯:
6%~8%;
焦油:
15%左右;
8选用含镍量为3%~7%的镍系催化剂。
4.4.5重油间歇循环催化裂解装置的烟气系统应设置废热回收和除尘设备。
4.4.6重油间歇循环催化裂解装置的蒸汽系统应设置蒸汽蓄能器。
4.4.7每2台重油制气炉应编为1组,合用1套冷却系统和鼓风设备。
冷却系统和鼓风设备的能力应按1台炉的瞬时流量计算。
4.4.8煤气冷却宜采用间接式冷却设备或直接一间接一直接三段冷却流程。
冷却后的燃气温度不应大于35℃,冷却水应循环使用。
4.4.9空气鼓风机的选择,应符合下列要求:
1 风量应按空气瞬时最大用量确定;
2风压应按油制气炉加热期的空气废气系统阻力和废气出口压力之和确定;
3每1~2组炉应设置1台备用的空气鼓风机;
4空气鼓风机应有减振和消声措施。
4.4.10油泵的选择,应符合下列要求:
1流量应按瞬时最大用量确定;
2压力应按输油系统的阻力和喷嘴的要求压力之和确定;
3每1~3台油泵应另设1台备用。
4.4.11输油系统应设置中间油罐,其容量宜按1d的用油量确定。
4.4.12煤气系统应设置缓冲罐,其容量宜按0.5~1.0h的产气量确定。
缓冲气罐的水槽,应设置集油、排油装置。
4.4.13在炉体与空气系统连接管上应采取防止炉内燃气窜入空气管道的措施。
并应设防爆装置。
4.4.14油制气炉宜露天布置。
主烟囱和副烟囱高出油制气炉炉顶高度不应小于4m。
4.4.15控制室不应与空气鼓风机室布置在同一建筑物内。
控制室应布置在油制气区夏季最大频率风向的上风侧。
4.4.16油水分离池应布置在油制气区夏季最小频率风向的上风侧。
对油水分离池及焦油沟,应采取减少挥发性气体散发的措施。
4.4.17重油制气厂应设污水处理装置。
污水排放应符合现行国家标准《污水综合排放标准》GB8978的规定。
4.4.18 自动控制装置的程序控制系统设计,应符合下列要求:
1 能手动和自动切换操作;
2能调节循环周期和阶段百分比;
3设置循环中各阶段比例和阀门动作的指示信号;
4主要阀门应设置检查和连锁装置。
在发生故障时应有显示和报警信号,并能恢复到安全状态。
4.4.19自动控制装置的传动系统设计,应符合下列要求:
1传动系统的形式应根据程序控制系统的形式和本地区具体条件确定;
2应设置储能设备;
3传动系统的控制阀、自动阀和其他附件的选用或设计,应能适应工艺生产的特点。
4.5轻油低压间歇循环催化裂解制气
4.5.1 轻油制气用的原料为轻质石脑油,质量宜符合下列要求:
1相对密度(20℃)O.65~0.69;
2初馏点>30℃;终馏点<130℃;
3直链烷烃>80%(体积分数),芳香烃<5%(体积分数),烯烃<1%(体积分数);
4总硫含量1×10-4(质量分数),铅含量1×10-7(质量分数);
5碳氢比(质量)5~5.4;
6高热值47.3~48.1MJ/kg。
4.5.2原料石脑油储存应采用内浮顶式油罐,储罐数量不应少于2个,原料油的储存量宜按15~20d的用油量计算。
4.5.3轻油低压间歇循环催化裂解制气装置宜采用双筒炉和顺流式流程。
加热室宜设置两个主火焰监视器,燃烧室应采取防止爆燃的措施。
4.5.4轻油低压间歇循环催化裂解制气工艺主要设计参数宜符合下列要求:
1反应器液体空间速度:
0.6~0.9m3/(m3·h);
2反应器内催化剂高度:
O.8~1.0m;
3加热油用量与制气用油量比例,小于29/100;
4过程蒸汽量与制气油量之比值为1.5~1.6(质量比);有CO变换时比值增加为1.8~2.2(质量比);
5循环时间:
2~5min;
6每吨轻油的催化裂解煤气产率:
2400~2500m。
(低热值按15.32~14.70MI/m3计);
7