氧气顶吹转炉炼钢工艺.docx
《氧气顶吹转炉炼钢工艺.docx》由会员分享,可在线阅读,更多相关《氧气顶吹转炉炼钢工艺.docx(35页珍藏版)》请在冰豆网上搜索。
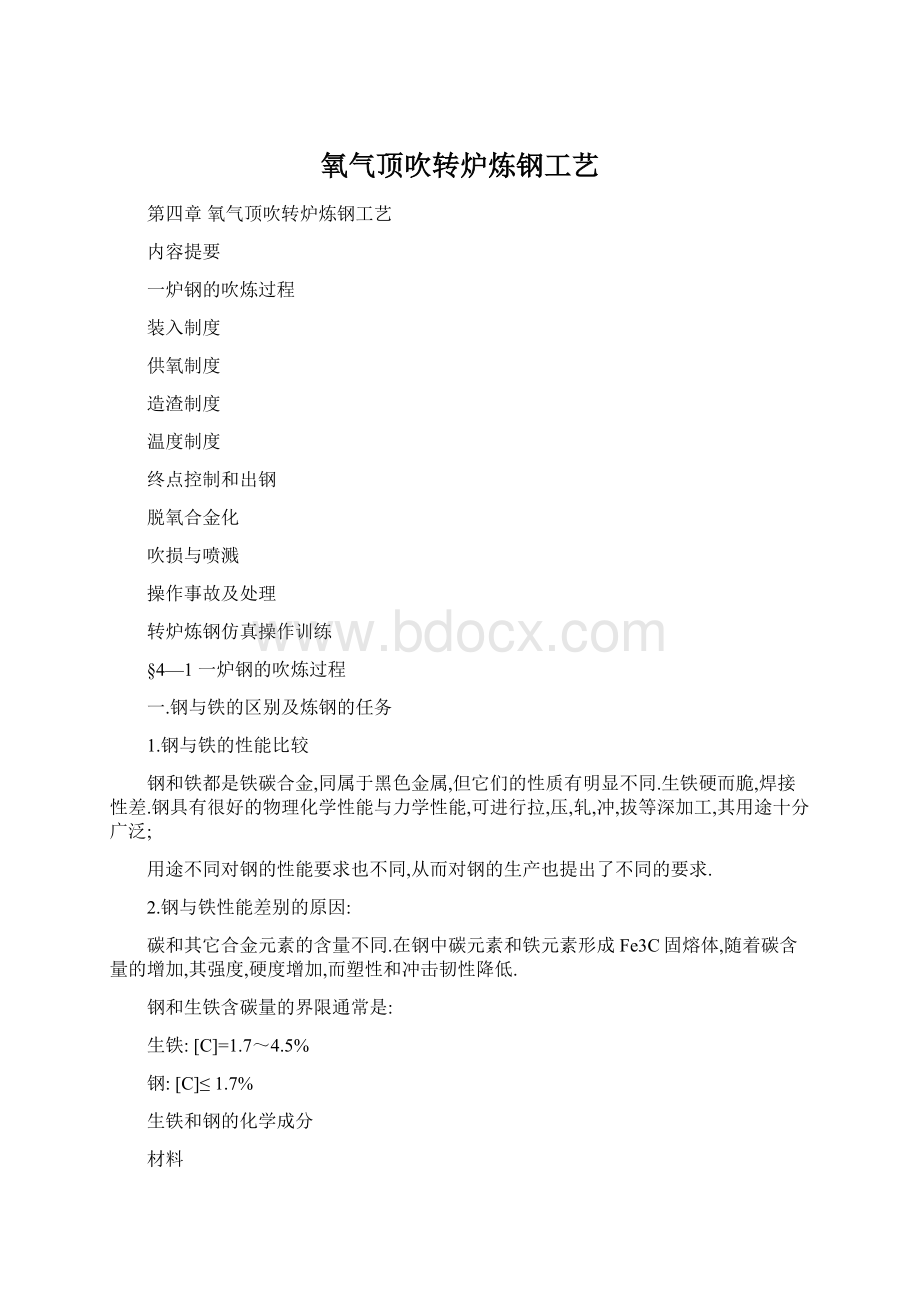
氧气顶吹转炉炼钢工艺
第四章氧气顶吹转炉炼钢工艺
内容提要
一炉钢的吹炼过程
装入制度
供氧制度
造渣制度
温度制度
终点控制和出钢
脱氧合金化
吹损与喷溅
操作事故及处理
转炉炼钢仿真操作训练
§4—1一炉钢的吹炼过程
一.钢与铁的区别及炼钢的任务
1.钢与铁的性能比较
钢和铁都是铁碳合金,同属于黑色金属,但它们的性质有明显不同.生铁硬而脆,焊接性差.钢具有很好的物理化学性能与力学性能,可进行拉,压,轧,冲,拔等深加工,其用途十分广泛;
用途不同对钢的性能要求也不同,从而对钢的生产也提出了不同的要求.
2.钢与铁性能差别的原因:
碳和其它合金元素的含量不同.在钢中碳元素和铁元素形成Fe3C固熔体,随着碳含量的增加,其强度,硬度增加,而塑性和冲击韧性降低.
钢和生铁含碳量的界限通常是:
生铁:
[C]=1.7~4.5%
钢:
[C]≤1.7%
生铁和钢的化学成分
材料
化学成分%
C
Si
Mn
P
S
炼钢生铁
3.5~4.0
0.6~1.6
0.2~0.8
0.0~0.4
0.03~0.07
碳素镇
静钢
0.06~1.50
0.1~0.37
0.25~0.80
≤0.045
≤0.05
沸腾钢
0.05~0.27
≤0.07
0.25~0.70
≤0.045
≤0.05
4.炼钢的基本任务:
⑴脱碳;
将铁水中的碳大部分去除,同时随着脱碳的进行,产生大量CO气泡,在CO排出过程中,搅拌熔池促进化渣,同时脱除[H],[N]和夹杂.
⑵去除杂质(去P,S和其它杂质);
铁水中[P],[S]含量高,而钢中[P]会造成"冷脆",[S]造成"热
脆".通常大多数钢种对P,S含量均有严格要求,炼钢必须脱除P,S等有害杂质.
⑶去除气体及夹杂物;
在炼钢过程中通过熔池沸腾(碳氧反应,底吹惰性气体搅拌)脱除H],[N]和非金属夹杂物.
⑷脱氧合金化;
在炼钢过程中因为脱碳反应的需要,要向钢液中供氧,就不可避免地使后期钢中含有较高的氧,氧无论是以液体形态还是以氧化物形态存在于钢中都会降低钢的质量,所以必须在冶炼后期或出钢过程中将多余的氧去除掉.
在冶炼过程中,铁水中的Si,Mn大部分氧化掉了,为了保证成品钢中的规定成分,要向钢水中加入各种合金元素,这个过程与脱氧同时进行,称为合金化.
⑸升温(保证合适的出钢温度).
铁水温度一般在1250~1300℃,而钢水的出钢温度一般在1650℃以上,才能顺利浇注成铸坯,因此炼钢过程也是一个升温过程.
5.完成炼钢各项任务的基本方法
⑴氧化
为了将铁水等炉料中的硅,锰,碳等元素氧化掉,可以采用"吹氧"方法,即直接喷吹氧气,或加入其它氧化剂,如铁矿石,铁皮等.
⑵造渣
为了去除炉料中的P,S等杂质,在炼钢过程中加入渣料(石灰,白云石,熔剂等),形成碱度合适,流动性良好,足够数量的炉渣,一方面完成脱除P,S的任务,同时减轻对炉衬对侵蚀.
⑶升温
转炉主要是依靠碳,硅,锰等元素氧化放出等热量,以及铁水的物理热实现升温.
⑷加入脱氧剂和合金料
通过向炉内或钢包内加入各种脱氧剂和合金料的方法,完成脱氧及合金化的任务.
二.金属成分和炉渣成分的变化规律
1.Si在吹炼前期(一般在3~4分钟内)即被基本氧化.
在吹炼初期,铁水中的[Si]和氧的亲和力大,而且[Si]氧化反应为放热反应,低温下有利于此反应的进行,因此,[Si]在吹炼初期就大量氧化.
[Si]+O2=(SiO2)(氧气直接氧化)
[Si]+2[O]=(SiO2)(熔池内反应)
[Si]+(FeO)=(SiO2)+2[Fe](界面反应)
2(FeO)+(SiO2)=(2FeO·SiO2)
随着吹炼的进行石灰逐渐溶解,2FeO·SiO2转变为2CaO·SiO2,即SiO2与CaO牢固的结合为稳定的化合物,SiO2活度很低,在碱性渣中FeO的活度较高,这样不仅使[Si]被氧化到很低程度,而且在碳剧烈氧化时,也不会被还原,即使温度超过1530℃,[C]与[O]的亲和力也超过[Si]与[O]的亲和力,终因(CaO)与(SiO2)结合为稳定的2CaO.SiO2,[C]也不能还原(SiO2).
硅的氧化对熔池温度,熔渣碱度和其他元素的氧化产生影响:
[Si]氧化可使熔池温度升高;
[Si]氧化后生成(SiO2),降低熔渣碱度,熔渣碱度影响脱磷,脱硫;
熔池中[C]的氧化反应只有到[%Si]P0.
⑵喷嘴前氧压P0:
其选用应考虑以下因素:
A.氧气流股出口速度要达到超音速(450~530cm∕s),即M=1.8~2.1.
B.出口的氧压应稍高于炉膛内气压.
通常P0=0.784~1.176MPa.
⑶出口氧压P:
应稍高于或等于周围炉气的压力.
通常P=0.118~0.125MPa.
六.枪位及其控制
所谓枪位,是指氧枪喷头端面距静止液面的距离,常用H表示,单位是m.
目前,一炉钢吹炼中的氧枪操作有两种类型,一种是恒压变枪操作,一种是恒枪变压操作.比较而言,恒压变枪操作更为方便,准确,安全,因而国内钢厂普遍采用.
1.枪位的变化X围和规律
关于枪位的确定,目前的做法是经验公式计算,实践中修正.
一炉钢冶炼中枪位的变化X围可据经验公式确定:
H=(37~46)P×D出
式中P——供氧压力,MPa;
D——喷头的出口直径,mm;
H——枪位,mm.
具体操作中,枪位控制通常遵循"高-低-高-低"的原则:
⑴前期高枪位化渣但应防喷溅.
吹炼前期,铁水中的硅迅速氧化,渣中的(SiO2)较高而熔池的温度尚低,为了加速头批渣料的熔化(尽早去P并减轻炉衬侵蚀),除加适量萤石或氧化铁皮助熔外应采用较高的枪位,保证渣中的(FeO)达到并维持在25~30%的水平;否则,石灰表面生成C2S外壳,阻碍石灰溶解.当然,枪位亦不可过高,以防发生喷溅,合适的枪位是使液面到达炉口而又不溢出.
⑵中期低枪位脱碳但应防返干.
吹炼中期,主要是脱碳,枪位应低些.但此时不仅吹入的氧几乎全部用于碳的氧化,而且渣中的(FeO)也被大量消耗,易出现"返干"现象而影响S,P的去除,故不应太低,使渣中的(FeO)保持在10~15%以上.
⑶后期提枪调渣控终点.
吹炼后期,C-O反应已弱,产生喷溅的可能性不大,此时的基本任务是调好炉渣的氧化性和流动性继续去除硫磷,并准确控制终点碳(较低),因此枪位应适当高些.
⑷终点前降枪点吹破坏泡沫渣.
接近终点时,降枪点吹一下,均匀钢液的成分和温度,同时降低炉渣的氧化铁含量并破坏泡沫渣,以提高金属和合金的收得率.
2.枪位的调节
⑴开吹前必须了解的情况
A.喷嘴的结构特点及氧气总管氧压情况;
B.铁水成分,主要是Si,P,S的含量;
C.铁水温度,包括铁水罐,混铁炉或混铁车内存铁情况及铁水包的情况;
D.炉役期为多少,是否补炉,相应的装入量是多少,上炉钢水是否出净,是否有残渣;
E.吹炼钢种及其对造渣和温度控制的要求;
F.上一班操作情况,并测量熔池液面高度.
⑵枪位的调节
生产条件千变万化,因此具体操作中还应根据实际情况对枪位进行适当的调节.
A.铁水温度:
若遇铁水温度偏低,应先压枪提温,而后再提枪化渣,以防渣中(FeO)积聚引发大喷,即采用低-高-低枪位操作.
铁水温度高时,碳氧反应会提前到来,渣中∑(FeO)降低,枪位可稍高些,以利成渣.
B.铁水成分:
铁水硅,磷高时,若采用双渣操作,可先低枪位脱硅,磷,倒掉酸性渣;若单渣操作,由于石灰加入量大,应较高枪位化渣.铁水含锰高时,有利于化渣,枪位则可适当低些.
C.装入量变化:
炉内超装时,熔池液面高,枪位应相应提高,否则,不仅化渣困难而且易烧坏氧枪.
D.炉内留渣:
采用双渣留渣法时,由于渣中(FeO)高,有利于石灰熔化,因此吹炼前期的枪位适当低些,以防渣中(FeO)过高引发泡沫喷溅.
E.供氧压力:
高氧压与低枪位的作用相同,故氧压高时,枪位应高些.
F.废钢中生铁块多导热性差,不易熔化,应降低枪位,以防吹炼后期没有完全熔化.
G.炉龄
a开新炉,炉温低,应适当降低枪位;
b炉役前期液面高,可适当提高枪位;
c炉役后期装入量增加,熔池面积增大,不易化渣,可在短时间内采用高低枪位交替操作以加强熔池搅拌,利于化渣.
H.渣料
a石灰质量差和加入量多,则渣量大,枪位应相应提高;
b使用活性石灰成渣快,整个过程枪位都可以稍低些;
c铁矿石,氧化铁皮和萤石用量多时,熔渣容易形成,同时流动性较好,枪位可适当低一些.
I.钢种
炼高碳钢时,由于脱磷困难,应采用较高的枪位,特别是在吹炼后期.同理,在吹炼含磷很低的钢种时,应采用较高枪位.
七.恒压变枪操作的几种模式
由于各厂的转炉吨位,喷嘴结构,原材料条件及所炼钢种等情况不同,氧枪操作也不完全一样.现介绍如下几种氧枪操作方式.
1.高—低—高的六段式操作
开吹枪位较高,及早形成初期渣;二批料加入后适时降枪,吹炼中期炉渣返干时又提枪化渣;吹炼后期先提枪化渣后降枪;终点拉碳出钢.
2.高—低—高的五段式操作
五段式操作的前期与六段式操作基本一致,熔渣返干时可加入适量助熔剂调整熔渣流动性,以缩短吹炼时间,见下图.
3.高一低一高一低的四段式操作
在铁水温度较高或渣料集中在吹炼前期加入时可采用这种枪位操作.开吹时采用高枪位化渣,使渣中含(FeO)量达25~30%,促进石灰熔化,尽快形成具有一定碱度的炉渣,增大前期脱磷和脱硫效率,同时也避免酸性渣对炉衬的侵蚀.在炉渣化好后降枪脱
高—低—高五段式操作示意图
碳,为避免在碳氧化剧烈反应期出现返干现象,适时提高枪位,使渣中(FeO)保持在10~15%,以利磷,硫继续去除.在接近终点时再降枪加强熔池搅拌,继续脱碳和均匀熔池成分和温度,降低终渣(FeO)含量.
例:
马钢一钢厂95T转炉氧枪操作
A.全程枪位:
高—低—高式或高—高—低式
过程枪位:
要力求稳定,尽量少波动,每次动枪波动X围≯200mm.
补吹枪位:
必须按最低枪位控制(1.1m).
B.高枪位:
1.7~2.0m;
基本吹炼枪位:
1.4~1.7m;
拉碳枪位:
1.2~1.4m;吹炼中,高碳钢拉碳枪位应提高0.1~0.2m.
例:
马钢一钢厂95T转炉开吹枪位的确定
(a)铁水Si>0.70%时渣量大,易喷溅,枪位应比正常情况下低0.1~0.2m;铁水Si,P含量低,特别是Si1%),P,S较高,或生产优质钢时采用.
倒渣时机:
这是双渣法操作的关键.选择在渣中含P量最高,含铁量最低的时刻,以获得高脱磷率和低铁损的效果.同时,应在Si已氧化完毕,炉渣已基本化好,P在渣钢之间的分配已接近平衡时进行.
生产实践证明,顶吹转炉在吹炼时间25%左右,复吹转炉为30%左右时倒渣脱磷率最高;若是因铁水硫高而采用双渣法,则应在吹炼10min左右倒渣.
注意:
倒渣前1分钟适当提枪或加些熔剂改善炉渣的流动性,以便于倒渣操作.
3.双渣留渣法
定义:
将上一炉的终渣(高碱度,高温度和较高(FeO)含量)部分地留在炉内,并在吹炼中途倒出部分炉渣再造新渣的操作方法.
特点:
初渣早成而前期的去硫及去磷效率高,总去硫率可达60%~70%,总去磷率更是高达95%,适合于吹炼中,高磷铁水.
注意:
装料时应先加一批石灰稠化所留炉渣,而且兑铁水时要缓慢进行,以防发生爆发性碳氧反应而引起喷溅.若上一炉钢终点碳过低,不宜进行留渣操作.
应当指出,顶吹转炉虽能将高磷铁水炼成合格的钢,但技术经济指标较差,与吹炼中,低磷铁水相比,每吨钢的金属料消耗高30~100kg,石灰多用40~100kg,炉龄大幅降低;产量也仅为吹炼低磷铁水时的70%~80%;另外,单渣法生产稳定,操作简单,便于实行计算机控制.因此,对于含硅,磷及硫较高的铁水,入炉前进行预处理使之达到单渣法操作的要求,不仅技术上可行而且工艺上经济合理.
七.渣料的加入方法
关于渣料的加入,关键是要注意渣料的分批和把握加入的时间.
1.渣料分批加入
目的:
渣料应分批加入以加速石灰的熔化(否则,会造成熔池温度下降过多,导致渣料结团且石灰块表面形成一层金属凝壳而推迟成渣).
批次:
单渣操作时,渣料通常分成两批:
第一批1/2~2/3及白云石全部(冶炼初期炉衬侵蚀最严重);第二批1/2~1/3.
2.加料时间
⑴第一批渣料在开吹的同时加入.
⑵第二批渣料,一般是在硅及锰的氧化基本结束,头批渣料已经化好,碳焰初起的时候(30吨的转炉开吹6min左右)加入(如果加入过早,炉内温度还低且头批渣料尚未化好又加冷料,势必造成渣料结团难化;反之,如果加入过晚,正值碳的激烈氧化时期,渣中的(∑FeO)较低渣料亦难化.问题的关键是正确判断炉况,头批渣料化好的标志是:
火焰软且稳定,炉内发出柔和的嗡嗡声,喷出物为片状,落在炉壳上不粘贴;未化好的情况是:
炉口的火焰发散且不稳定,炉内发出尖锐的吱吱声,喷出物是金属火花和石灰粒).
有的厂二批料分小批多次加入以利熔化,但最后一小批料必须在终点前3~4分钟加入
八.石灰,白云石加入量的确定
加入炉内的渣料主要是石灰和白云石,还有少量的萤石或氧化铁皮等熔剂.
1.石灰加入量的确定
⑴首先根据铁水的硅,磷含量和炉渣碱度计算
A.铁水含磷较低([P]<0.3%)时,
(kg∕t铁)
%CaO有效—石灰中的有效CaO,
%CaO有效=(%CaO)石灰-R×(%SiO2)石灰
废钢,生铁块也应根据上式计算需补加的石灰量.
例:
B.铁水含磷较高([P]≥0.3%)时,
(kg∕t铁)
⑵其次,当加入含(%SiO2)的辅助原料时(如:
矿石,白云石萤石,菱镁矿等),应补加石灰.
例:
铁矿石中SiO2的含量为8%,碱度按3.0控制,石灰的有效氧化钙为80%,则每kg矿石补加石灰量=8×3.0/80=0.3(kg)
⑶石灰加入总量
废钢中含有一定量的Si,但成分通常不知,一般按每吨废钢补加石灰15~20kg.
2.白云石用量的确定
白云石的加入量应根据炉渣要求的饱和MgO含量来确定.通常渣中MgO含量控制在8%~10%,除了加入的白云石含有MgO外,石灰和炉衬也会带入一部分.
理论用量W(kg/t)=
实际加入量W/=W-W灰-W衬
3.熔剂的用量
萤石用量:
尽量少用或不用,部标要求≤4kg/t.
矿石用量:
铁矿石及氧化铁皮也具有较强的化渣能力,但同时对熔池产生较大的冷却效应,其用量应视炉内温度的高低,一般为装入量的2~5%.
4.计算举例
例题1:
1t金属料中铁水占85%,废钢占10%,生铁块占5%,每T金属料加矿石5kg,萤石3kg,铁水带渣比为0.5%,石灰熔化率为85%,各原材料成分列在下表中.炉渣碱度为3.5.计算:
1t金属料所需石灰加入量为多少
原料
成分
铁水
废钢
生铁块
铁水带渣
石灰
矿石
萤石
[%Si]
0.50
0.10
1.40
%CaO
37.5
83
%SiO2
36
2.5
6.0
5.0
解:
石灰加入量
铁水带渣量为:
1000×85%×0.5%=4.25(kg)
铁水带渣带入的SiO2应考虑铁水渣中CaO相当的SiO2量:
辅助原料及铁水带渣需补加石灰量(kg)
)
例题2:
用轻烧白云石作为调渣剂其成分如下表:
原料
成分
石灰
轻烧白云石
炉衬
%CaO
%SiO2
%MgO
83
2.5
4.09
50
2.0
37
77
计算条件:
终渣成分要求(MgO)=9.66%,渣量为金属装入量的8.2%,炉衬侵蚀量是装入量的0.05%,其它条件同上述例题.
解题思路:
终渣(MgO)来源:
A.加入的轻烧白云石.
C.石灰中的MgO.
D.炉衬被侵蚀下来的MgO.
⑴计算轻烧白云石加入量
由例题1计算的结果是不加轻烧白云石时石灰加入量为68.39kg∕t.
石灰带入MgO量:
68.39×4.09%=2.80(kg)
炉衬蚀损带入MgO量:
1000×0.05%×77%=0.385(kg)
根据1t装入量计算终渣MgO量:
1000×8.2%×9.66%=7.92(kg∕t)
⑵计算轻烧白云石需补加石灰量
⑶计算轻烧白云石相当的石灰量
石灰加入总量=68.39-8.62+1.21=60.98(kg)
例题3:
某转炉铁水装入量为100t,铁水含Si:
0.4%,P:
0.1%.采用单渣法造渣,终渣碱度为3.5,每炉加矿石3000kg,为保证渣中MgO,每炉加轻烧白云石2500kg.
已知:
石灰:
CaO:
91.6%SiO2:
1.6%
矿石:
SiO2:
8%
轻烧白云石:
MgO:
35%CaO:
55%SiO2:
2%
计算石灰加入量(单位kg,保留整数).
解:
⑴计算未加白云石时石灰加入量
⑵计算轻烧白云石需补加石灰量
⑶计算轻烧白云石相当的石灰量
⑷计算石灰加入总量
石灰加入总量=5454+203-1599=4085(kg)
九.渣量计算
渣量可以用元素平衡法计算.由铁水炼成钢,各元素一部分被氧化,一部分残留在钢中.如果知道某一元素在钢中的数量,该元素其余部分全部进入了熔渣,则通过这个元素在渣中的百分含量,就可以计算出熔渣的数量.
Mn和P两元素,从渣料及炉衬中的来源很少,其数量可以忽略不计.因而可以用Mn或P的平衡来计算渣量.
例:
渣量计算(单渣法)
装入量MnPFe
装(kg)%kg%kg%kg
入铁水280000.401120.2056
料废钢40000.50200.020.8
数铁矿石10000.3030.101.056.0560
据小计13557.8560
(MnO)%[%Mn](P2O5)%[%P]
终
点钢水0.120.03
数炉渣3.302.562.861.25
据
金属装入量28000+4000+560=32560kg
出钢量(按装入量的90%计算)
32560×90%=29304kg
钢水中Mn量29304×0.12%=35.16kg
钢水中P量29304×0.03%=8.79kg
进入渣中Mn量135-35.16=99.84kg
进入渣中P量57.8-8.79=49.01kg
用Mn平衡法
熔渣占装入量的百分比
用P平衡法
熔渣占装入量的百分比
习题:
1名词解释:
泡沫渣,单渣法双渣法双渣留渣法
2造渣方法如何选择采用双渣法操作时,倒渣的时间应如何掌握
3石灰加入量如何计算渣料如何加入
4影响石灰溶解的因素有哪些
5炉渣严重泡沫化的原因是什么如何控制泡沫渣
6.吹炼过程中为什么会出现炉渣"返干"现象
§4—5温度制度
氧气转炉的温度制度包括两方面的内容:
一是准确控制终点温度,二是恰当控制冶炼过程温度.
温度对于转炉吹炼过程既是重要的热力学参数,又是重要的动力学参数.它既对各个化学反应的反应方向,反应程度和各元素之间的相对反应速度有重大影响,又对熔池的传质和传热速度有重大影响.因此,为了快而多地去除钢中的有害杂质,保护或提取某些有益元素,加快吹炼过程成渣速度,加快废钢熔化,减少喷溅,提高炉龄等,都必须控制好吹炼过程温度.此外,对各钢种都有其要求的出钢温度.出钢温度过低会造成回炉,短锭,包底凝钢及钢锭的各种低温缺陷和废品;过高则会造成跑漏钢,钢锭上涨,粘模及钢锭的各种高温缺陷和废品,并影响炉衬和氧枪的寿命.
一.转炉温度控制的目标及温度控制内容
1.目标
希望吹炼过程中均衡升温,吹炼终点时钢水的温度和化学成分同时命中钢种要求的X围.
2.内容
⑴确定合适的钢种出钢温度;
⑵确定熔池富裕热量的数值,选择冷却剂并确定其冷却效果和加入量;
⑶掌握影响熔池温度变化的因素,及进行温度控制操作.
二.热量来源与热量支出
1.热量来源
氧气转炉炼钢的热量来源主要是铁水的物理热和化学热.物理热是指铁水带入的热量,它与铁水温度有直接关系,化学热是铁水中各元素氧化后放出的热量,它与铁水化学成分直接相关.
在炼钢温度下,各元素氧化放出的热量各异,它可以通过各元素氧化放出的热效应来计算确定.例如铁水温度1200℃,吹入的氧气25℃,碳氧反应生成CO时:
[C]1473+{O2}298={CO}1473ΔH1473K=-137520J/mol
则1kg[C]氧化生成CO时放出的热量为137520/12≈11300kJ/kg.
现以100kg金属料为例,计算各元素的氧化热能使熔池升温多少.
设炉渣量为装入金属料的15%,炉衬吸热为装入金属料的10%,计算热平衡公式如下:
Q=∑MCT
式中Q—1kg元素氧化放出的热量,kJ/kg;
M——受热金属液,炉衬和炉渣重量,kg;
C——各物质比热,已知钢液CL为0.84~1.0kJ/kg·℃,炉渣和炉衬的CS为1.23kJ/kg·℃.
计算在1200℃时C—O反应生成CO时,氧化1kg碳可使熔池温度升高数为:
℃
1kg元素是100kg金属料的1%,因此,根据同样道理和假设条件,可以计算出其它元素氧化1%时使熔池的升温数.
碳完全燃烧生成CO2时其发热量最高,使熔池升温数最大,其次是磷和硅.但是碳大部分没有完全燃烧,因此,在氧气转炉吹炼中采用双流氧枪,可有助于CO进一步燃烧生成CO2,使转炉热效率提高.
哪些元素是转炉炼钢的主要热源,不仅要看其热效应大小,还要视其氧化总量的多少而定.例如,在1400℃时,硅氧化0.5%,碳氧化3%,则分别使熔池升温数为71℃和249℃,可见碳氧化产生的总热量要比硅的总热量多得多.
2.热量支出
热量支出主要包括:
钢水物理热;炉渣物理热;炉气物理热;烟尘物理热;渣中金属铁珠物理热;喷溅金属物理热;矿石分解热;废钢物理热(见热平衡表).其中,钢水的物理热约占70%,这是一项主要的支出,熔渣带走的热量大约占10%,它与渣量的多少有关.因此在保证去除P,S的条件下,采用最小的渣量.渣量过大不仅增加渣料的消耗,也增加热量的损失,所以要求铁水进行预处理,这样既可实现少渣操作;同时在吹炼过程中也可减少喷溅,缩短吹炼时间,减少炉与炉的间隔时间,减少热损失,提高转炉的热效率.转炉热效率提高以后,可以提高废钢比.
3.转炉炼钢的热平衡
指炼钢过程的热量来源与支出之间的平衡关系(见热平衡表).
为了准确的控制转炉的吹炼温度,需要知道铁水中各成分氧化反应放出的总热量;这些热量除了把熔池加热到出钢温度外,富余多少热量需要加多少冷却剂这要经过热平衡计算才能得出,具体物料平衡,热平衡计算参看教材中物料平衡与热平衡计算内容.
热平衡表的分析:
根据转炉吹炼过程中热量的收入与支出,作出热平衡计算列出热平衡表,得出
氧气转炉热工特点如下:
⑴热量收入主要是铁水的物理热和化学热;
⑵尚有大量的富余热量,必须加入冷却剂;
⑶元素氧化放热中,C,Si,P都是重要的发热元素,其中碳占有主要地位(占氧化总放热的一半以上).
⑷转炉热效率为60~70%左右.
转炉总热效率计算公式如下:
总热效率=×100%
在转炉炼钢过程中,真正有用的热量占整个热量收入的70%左右,在热量的利用上还是有一定潜力的,应努力提高热效率.
三.出钢温度的确定
出钢温度的高低受钢种,锭型和浇注方法的影响.
1.出钢温度的确定依据:
⑴保证浇注温度高于所炼钢种凝固温度20~30℃(小炉子偏上限,大炉子偏下限).
⑵考虑出钢过程和钢水运输,镇静时间,钢液吹氩时的降温,一般为80~120℃.
⑶考虑