2台100T锅炉除尘脱硝脱硫技术方案.docx
《2台100T锅炉除尘脱硝脱硫技术方案.docx》由会员分享,可在线阅读,更多相关《2台100T锅炉除尘脱硝脱硫技术方案.docx(65页珍藏版)》请在冰豆网上搜索。
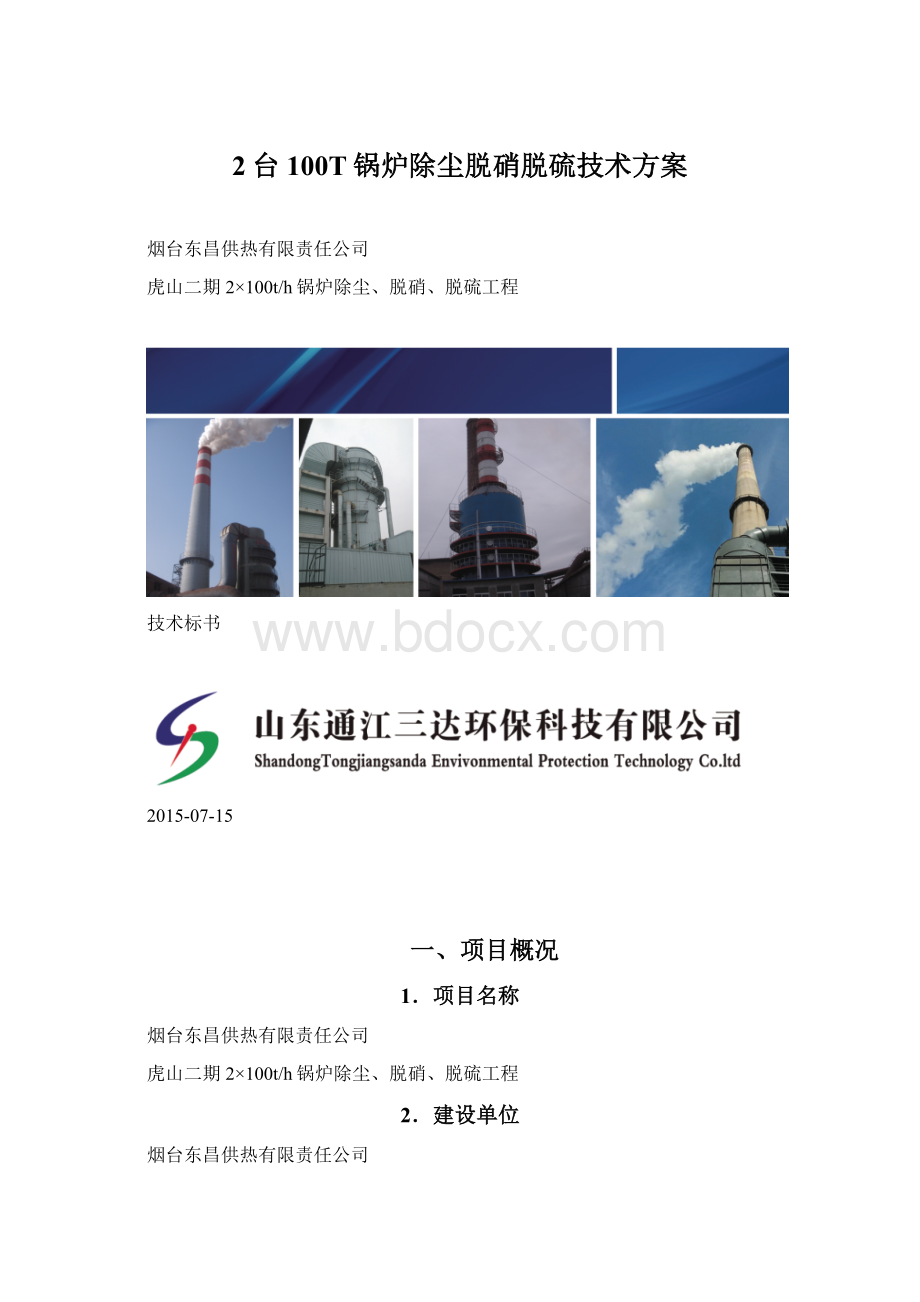
2台100T锅炉除尘脱硝脱硫技术方案
烟台东昌供热有限责任公司
虎山二期2×100t/h锅炉除尘、脱硝、脱硫工程
技术标书
2015-07-15
一、项目概况
1.项目名称
烟台东昌供热有限责任公司
虎山二期2×100t/h锅炉除尘、脱硝、脱硫工程
2.建设单位
烟台东昌供热有限责任公司
3.设计单位
山东通江三达环保科技有限公司
4.项目概况
烟台东昌供热有限责任公司,主要经营供热,位于山东烟台莱山区,
公司现有虎山、金房、莱阳等锅炉脱硫项目,SO2排放高达2000mg/Nm3。
现除尘采用水膜除尘,均没有建设配套脱硫脱硝设施,出口烟气达不到环保要求。
在“十二五”计划中,我国的节能减排工作任重而道远。
面对日益严峻的环保形势,为响应国家有关部门关于烟气脱硫的政策法规,以及从可持续发展和社会及环保效益的角度出发,烟台东昌供热有限责任公司对现锅炉烟气计划建设除尘改造及脱硫脱硝综合环保工程,经处理后外排烟气达到当地环保要求。
根据《山东省区域性大气污染物综合排放标准》中不同时段的标准要求,其中第二时段标准为2015年1月1日至2016年12月31日排放烟气达到:
名称
NOx(mg/m3)
SO2(mg/m3)
烟尘(mg/m3)
第二时段标准
300
200
30
第三时段标准为2017年1月1日至2019年12月31日
名称
NOx(mg/m3)
SO2(mg/m3)
烟尘(mg/m3)
第三时段标准
100(200)
100
20
第四时段即2020年以后达到超低排放标准要求。
名称
NOx(mg/m3)
SO2(mg/m3)
烟尘(mg/m3)
超低排放标准
50
35
10
5.设计思路
为满足不同时期的环保标准,公司拟对现有烟气处理设施进行一系列改造,本技术方案设计思路总体按照超低排放标准设计,采用模块化的设计理一次设计分阶段实施的方式。
1、一期建设投资后,外排烟气达到第三时段排放标准。
即:
烟尘:
20mg/m3SO2100mg/m3NOx(以NO2计)100mg/m3
2、预留二期建设,烟气经处理后达到超低排放标准。
即:
烟尘:
10mg/m3SO235mg/m3NOx(以NO2计)50mg/m3
3、一期建设工艺思路,在锅炉内增加SNCR脱硝设备,SNCR后采用布袋除尘器,脱硫采用氧化镁法脱硫及高压湿式电除尘深度净化装置,即在原有水膜除尘器基础上拆除副塔,将主塔改造为旋流板式脱硫装置,高压湿式电除尘装置。
4、预留高级低温氧化反应器,满足超低排放标准下稳定达标运行,同时降低SNCR运行成本等。
工艺流程简图:
二、设计依据、原则、范围和要求
1.设计依据
(1)《锅炉大气污染物排放标准》GB13271-2001
(2)《锅炉烟尘测试方法》GB/T5468-91
(3)《工业企业噪声控制设计规范》GBJ78-85
(4)《钢结构工程施工质量验收》GB50205-2001
(5)《钢结构设计规范》GB50017-2003
(6)《袋式除尘器安装技术要求与验收规范》JB/T8471-96
(7)《袋式除尘器用滤料及滤袋技术条件》GB12625-90
(8)《除尘机组技术性能及测试方法》GB/T11653-89
(9)《脉冲喷吹类袋式除尘器》GB/T8532-1997
(10)《电器装置安装工程施工技术条件》GBJ232-82
(11)《建筑抗震设计规范》GB5011-2001
(12)《固定式钢斜梯安全技术条件》GB4053.4-93
(13)《固定式工业钢平台》GB4053.4-83
(14)《袋式式除尘器用滤袋框架技术条件》JB/T5917-91
(15)《袋式式除尘器用电磁脉冲阀》JB/T5916-2004
(16)《电气装置安装工程及验收规程》GB50254-6—96
(17)《低压分配和电路设计规范》GBJ54-83
(18)GB150钢制压力容器
(19)GB536液体无水氨
(20)GB2440尿素
(21)GB3836.2爆炸性气体环境用电气设备
(22)GB4208外壳防治等级(IP代码)
(23)GB8978污水综合排放标准
(24)GB12268危险货物品名表
(25)GB12348工业企业厂界噪声标准
(26)GB12358作业环境气体检测报警仪通用技术要求
(27)GB12801生产过程安全卫生要求总则
(28)GB14554恶臭污染物排放标准
(29)GB18218重大危险源辩识
(30)GB50058爆炸和火灾危险环境电力装臵设计规范
(31)GB50160石油化工企业设计防火规范
(32)GB50222建筑内部装修设计防火规范
(33)GB50351储罐区防火堤设计规范
(34)GBZ1工业企业设计卫生标准
(35)GB/T16157固定污染源排气中颗粒物测定与气态污染物采样方法
(36)GB/T20801生产过程安全卫生要求总则
(37)GB/T21509燃煤烟气脱硝技术装备
(38)DL408电业安全工作规程
(39)GB9078工业炉窑大气污染物排放标准
(40)GB18599一般工业固体废物贮存、处置场污染控制标准
(41)GB50016建筑设计防火规范
(42)GB50040动力机器基础设计规范
(43)GB50212建筑防腐蚀工程施工及验收规范
(44)HG23012厂区设备内作业安全规程
(45)HJ/T75固定污染源烟气排放连续监测技术规范(试行)
(46)HJ/T76固定污染源烟气排放连续监测系统技术要求及检测方法(试行)
(47)《建设工程质量管理条例》(中华人民共和国国务院第279号)
(48)《建筑项目(工程)竣工验收办法》(国家计委文件计建设[1990]1215号)
(49)《建筑项目环境保护竣工验收管理办法》(国家环境保护总局令第13号)
(50)《污染源自动监控管理办法》(国家环境保护总局令第28号)
2.设计原则
1、烟气脱硫脱硝工艺成熟、可靠。
烟气脱硫脱硝及辅助设备和附件使用的材料,制造工艺及检验要求均不低于国家有关标准的规定。
2、保证烟气二氧化硫及NOx浓度在一定范围内波动时,脱硫脱硝率满足系统设计要求。
烟气量变动在70~100%时,系统工作正常。
3、采用成熟的脱硫脱硝技术,可以保证脱硫效果满足系统设计的要求和标准。
4、工程场地布置能满足系统设备用地要求。
5、脱硫产物不会产生二次污染。
6、氧化风机压头和风量可靠,以保证脱硫后的亚硫酸盐完全氧化成硫酸盐。
7、整个脱硫系统中与有腐蚀性的介质接触的部件和设备有防腐措施。
8、采购的设备为国内、国际知名品牌。
9、催化剂满足高灰分要求,选择科学合理的技术参数。
10、工艺设计尽可能节约能源和水源,应设计节能技术及设备,尽可能降低系统的投资与运行费用。
在设备及管道运行中溢流、冲洗和清扫过程中产生的废水应回收重复利用于环保设施。
11、装置区域环境噪声满足GB12348-1990《工业企业厂界噪声标准》Ⅱ类标准,设备运转噪声小于85分贝(离设备1米处测量)。
12、模块化的设计理念,满足不同时期的环保要求。
3.设计范围
采用“SNCR脱硝装置+布袋除尘器+湿式氧化镁法脱硫+深度净化湿式电除尘组合工艺”对现有烟气治理装置进行改造。
3.1锅炉烟气脱硝技术
3.2锅炉烟气除尘改造
3.3锅炉烟气脱硫及深度净化装置
4.厂址自然条件
(1)气温:
年平均气温12.5℃
(2)多年极端最高气温38℃
(3)多年极端最低气温-13.1℃
(4)降雨量:
年平均降雨量750mm
5.工程模式
实施设计、制造、安装、调试和上岗人员培训的工程服务模式。
三、设计参数
1.锅炉主要参数
名称
锅炉型号
烟气量
引风机风压
除尘形式
出力
虎山锅炉
DHL70-1.6/130/70-AII
165000m3/h
3290Pa
水膜除尘
70MW
(1)锅炉额定热功率:
100t/h
(2)锅炉运行负荷为90%时(燃煤发热值为:
5000大卡):
燃煤量:
13t/h;烟气量:
165000m³/h
(3)锅炉出口烟气温度:
170℃
(4)锅炉设计风压:
3041.41Pa
(5)引风机实际压力:
3290Pa
(6)引风机最大风量:
254670m³/h
SO2浓度为1000--2000mg/m3
入口烟气NOX为400mg/m3
改造除尘后颗粒物为50mg/m3
2.燃烧煤种参数
项目
符号
单位
检验结果
炭
C
%
36.9
氢
H
%
3.29
氧
O
%
15.91
氮
N
%
0.63
灰分
A
%
11.85
固定碳
FC
%
49.37
全硫
TS
%
1
3.烟气主要参数
锅炉处理烟气量:
165000m3/h
省煤器后烟气温度:
170℃
入口烟气SO2浓度:
2000mg/m3
入口烟气NOX400mg/m3
除尘后颗粒物30mg/m3
3.设计目标值
SO2脱除效率:
98%
SO2排放浓度:
≤35mg/Nm3
NOX排放浓度:
≤50mg/Nm3
烟气出口雾滴含量:
≤25mg/Nm3
烟气出口颗粒物浓度:
≤10mg/Nm3
镁硫比(Mg/S):
1.05
液气比(L/Nm3):
2
系统阻力:
≤1200Pa
漏风率:
≤3%
可利用率:
≥98%
设计条件下年可运行时间:
≥8000小时
脱硫系统采用的脱硫剂为氧化镁粉,粒径≥200目,含水率≤2%,纯度≥80%。
四、工艺方案设计
1.设计思路
◆脱硝采用SNCR(预留高级低温氧化装置)脱硝。
SNCR工艺是一种不用催化剂,在800-1050℃范围内还原NOx的方法。
该方法以炉膛为反应器,可通过对锅炉进行改造实现。
其中反应最适宜温度800-950℃(该项目炉膛温度为850~900℃,因此只适用于喷淋氨水)。
因为炉膛温度、NOx的分布在炉膛对流断面上是经常变化的,如果喷入控制点太少或锅炉整个断面上喷氨不均匀,则会出现较高的氨逸出量。
若喷入还原剂不充分反应,则泄漏的NH3不仅会使烟气中的飞灰沉积在锅炉尾部的受热面上,而且遇到SO3会发生铵盐,可能造成空气预热器堵塞和腐蚀。
为保证脱硝反应能以最少的喷NH3量达到最好的还原效果,选用合适的喷射器,分层布置,使NH3与烟气良好地混合,达到脱硝目的。
根据现场实际
◆除尘改造采用布袋除尘器,改造后出口颗粒物低于30mg/Nm3
◆脱硫采用氧化镁法脱硫,脱硫率高达98%以上,出口SO2排放浓度低于35mg/Nm3
◆深度除尘采用深度净化装置—高压静电湿式除尘(雾)器,用于捕集脱硫净化湿烟气中的细粉尘、酸雾及汞等,能有效去除烟气中的氨、铵盐、SO3酸雾、PM2.5、细小液滴、汞等重金属,使出口烟气处于酸雾几乎被全部去除的比较“干”的状态,有效地降低了SO3酸雾冷凝对烟囱造成的腐蚀速度,实现烟气高度清洁排放出口颗粒物低于10mg/Nm3
◆模块化的设计理念,不同模块有不同的作用,本技术方案预留高级低温氧化反应器。
随着环保标准的提高,不需要拆除改造原有,直接增加催化剂制备车间即可。
2.除尘技术方案
袋式除尘器是一种干式滤尘装置。
滤料使用一段时间后,由于筛滤、碰撞、滞留、
扩散、静电等效应,滤袋表面积聚了一层粉尘,这层粉尘称为初层,在此以后的运动过程中,初层成了滤料的主要过滤层,依靠初层的作用,网孔较大的滤料也能获得较高的过滤效率。
LCMD长袋低压脉冲袋式除尘器是集合国内先进技术为一体,处理风量大、过滤风速低、清灰效果好、除尘效率高、运行可靠、维护方便、占地面积小的单元组合式除尘设备。
该设备技术先进,质量稳定,广泛应用于电力、冶金、建材、化工等行业的锅炉、烟气除尘及物料回收、粉尘治理。
产品优点:
⑴除尘效率高,一般在99%以上,除尘器出口气体含尘浓度在数十mg/m3之内,对亚微米粒径的细尘有较高的分级效率。
⑵处理风量的范围广,小的仅1min数m3,大的可达1min数万m3,既可用于工业炉窑的烟气除尘,减少大气污染物的排放。
⑶结构简单,维护操作方便。
⑷在保证同样高除尘效率的前提下,造价低于电除尘器。
⑸采用玻璃纤维、聚四氟乙烯、P84等耐高温滤料时,可在200℃以上的高温条件下运行。
⑹对粉尘的特性不敏感,不受粉尘及电阻的影响。
3.脱硝技术方案
SNCR脱硝技术即选择性非催化还原(SelectiveNon-CatalyticReduction,以下简写为SNCR)技术,是一种不用催化剂,在850~1100℃的温度范围内,将含氨基的还原剂(如氨水,尿素溶液等)喷入炉内,将烟气中的NOx还原脱除,生成氮气和水的清洁脱硝技术。
在合适的温度区域,且氨水作为还原剂时,其反应方程式为:
4NH3+4NO+O2→4N2+6H2O(1
然而,当温度过高时,也会发生如下副反应:
4NH3+5O2→4NO+6H2O
(2)
SNCR烟气脱硝技术的脱硝效率一般为30%~80%,受锅炉结构尺寸影响很大。
采用SNCR技术,目前的趋势是用尿素代替氨作为还原剂。
SNCR脱硝原理
在850~1100℃范围内,NH3或尿素还原NOx的主要反应为:
NH3为还原剂:
4NH3+4NO+O2→4N2+6H2O
尿素为还原剂:
NO+CO(NH2)2+1/2O2→2N2+CO2+H2O
SNCR脱硝系统组成:
SNCR(喷氨)系统主要由卸氨系统、罐区、加压泵及其控制系统、混合系统、分配与调节系统、喷雾系统等组成。
SNCR系统烟气脱硝过程是由下面四个基本过程完成:
接收和储存还原剂;在锅炉合适位置注入稀释后的还原剂;
还原剂的计量输出、与水混合稀释;还原剂与烟气混合进行脱硝反应。
SNCR脱硝反应器的具体安装位置根据锅炉及现场实际确定,常规工艺流程如下:
4.脱硫技术方案
4.1氧化镁法脱硫法
锅炉烟气由引风机送入吸收塔预冷段,冷却至适合的温度后进入吸收塔,往上与逆向流下的吸收浆液反应,脱去烟气中的硫份。
吸收塔顶部安装有除雾器,以除去净烟气中携带的细小雾滴。
净烟气经过除雾器降低烟气中的水分后排入烟囱。
粉尘与脏东西附着在除雾器上,会导致除雾器堵塞、系统压损增大,需由除雾器冲洗水泵提供工业水对除雾器进行喷雾清洗。
吸收过程发生的主要反应如下:
Mg(OH)2+ SO2→ MgSO3+ H2O
MgSO3 + SO2+ H2O → Mg(HSO3)2
Mg(HSO3)2 + Mg(OH)2→ 2MgSO3 + 2H2O
吸收了硫分的吸收液落入吸收塔底,吸收塔底部主要为氧化、循环过程。
氧化过程,由曝气鼓风机向塔底浆液内强制提供大量压缩空气,使得造成化学需氧量的MgSO3氧化成MgSO4。
这个阶段化学反应如下:
MgSO3 + 1/2O2→ MgSO4
Mg(HSO3)2 + 1/2O2→ MgSO4 + H2SO3
H2SO3 + Mg(OH)2→ MgSO3 + 2H2O
MgSO3 + 1/2O2→ MgSO4
循环过程即是将落入塔底的吸收液经浆液循环泵重新输送至吸收塔上部吸收区。
塔底吸收液pH由自动喷注的20%氢氧化镁浆液调整,而且与酸碱计连锁控制。
当塔底浆液pH低于设定值时,氢氧化镁浆液通过输送泵自动补充到吸收塔底,在塔底搅拌器的作用下使浆液混合均匀,至pH达到设定值时停止补充氢氧化镁浆液。
20 %氢氧化镁溶液由氧化镁粉加热水熟化产生,或直接使用氢氧化镁,因为氧化镁粉不纯,而且氢氧化镁溶解度很低,就使得熟化后的浆液非常易于沉积,因此搅拌机与氢氧化镁溶液输送泵必须连续运转,避免管线与吸收塔底部产生沉淀。
4.2氧化镁-氧化镁湿法脱硫工艺流程
主要包括:
烟气系统;循环水、工艺水系统;脱硫剂制备系统;副产品回收系统;控制系统等。
详见工艺流程图。
4.3镁法脱硫优点
a.技术成熟。
氧化镁脱硫技术是一种成熟度仅次于钙法的脱硫工艺,氧化镁脱硫工艺在世界各地都有非常多的应用业绩,其中在日本已经应用了100多个项目,台湾的电站95%是用氧化镁法,另外在美国、德国等地都已经应用,并且目前在我国部分地区已经有了应用的业绩。
b.原料来源充足。
在我国氧化镁的储量十分可观,目前已探明的氧化镁储藏量约为160亿吨,占全世界的80%左右。
其资源主要分布在辽宁、山东、四川、河北等省,其中辽宁占总量的84.7%,其次是山东莱州,占总量的10%,其它主要是在河北邢台大河,四川干洛岩岱、汉源,甘肃肃北、别盖等地。
因此氧化镁完全能够作为脱硫剂应用于电厂的脱硫系统中去。
c.脱硫效率高。
在化学反应活性方面氧化镁要远远大于钙基脱硫剂,并且由于氧化镁的分子量较碳酸钙和氧化钙都比较小。
因此其它条件相同的情况下氧化镁的脱硫效率要高于钙法的脱硫效率。
一般情况下氧化镁的脱硫效率可达到95-98%以上,而石灰石/石膏法的脱硫效率仅达到90-95%左右。
d.投资费用少
由于氧化镁作为脱硫本身有其独特的优越性,因此在吸收塔的结构设计、循环浆液量的大小、系统的整体规模、设备的功率都可以相应较小,这样一来,整个脱硫系统的投资费用可以降低20%以上。
e.运行费用低。
决定脱硫系统运行费用的主要因素是脱硫剂的消耗费用和水电汽的消耗费用。
氧化镁的价格比氧化钙的价格高一些,但是脱除同样的SO2氧化镁的用量是碳酸钙的40%;水电汽等动力消耗方面,液气比是一个十分重要的因素,它直接关系到整个系统的脱硫效率以及系统的运行费用。
对石灰石石膏系统而言,液气比一般都在15L/m3以上,而氧化镁在7 L/m3以下,这样氧化镁法脱硫工艺就能节省很大一部分费用。
同时氧化镁法副产物的出售又能抵消很大一部分费用。
f.运行可靠。
镁法脱硫相对于钙法的最大优势是系统不会发生设备结垢堵塞问题,能保证整个脱硫系统能够安全有效的运行,同时镁法PH值控制在6.0-6.5之间,在这种条件下设备腐蚀问题也得到了一定程度的解决。
总的来说,镁法脱硫在实际工程中的安全性能拥有非常有力的保证。
5.高压静电湿式除尘(雾)技术
高压静电湿式除尘器为脱硫塔塔内安装方式,是利用高压脉冲直流电、电场驱动烟气内微细烟尘,使其加速沉降于阳极表面,以除去烟气中的尘粒,是对吸收塔机械除尘器过滤后残留的液滴和烟尘进行二次捕捉、净化的设备。
主要用于捕集脱硫净化湿烟气中的细粉尘、酸雾及汞等,能有效去除烟气中的氨、铵盐、SO3酸雾、PM2.5、细小液滴、汞等重金属,使出口烟气处于酸雾几乎被全部去除的比较“干”的状态,有效地降低了SO3酸雾冷凝对烟囱造成的腐蚀速度,实现烟气高度清洁排放出口颗粒物低于10mg/Nm3
6.技术方案特点
6.1独特的预处理室技术
一是对烟气降温、润湿除尘,使烟气温度降至露点左右,使烟气中的二氧化硫转化为亚硫酸;二是,创造良好的脱硫反应时间与温度;三是增加烟气的停留时间减少烟气带水问题。
将原水膜除尘器主塔改造为预处理室,同时作为后期预留高级低温氧化脱硝的反应器。
6.2高效喷射旋流曝气脱硫塔
应用旋风除尘、惯性分离等原理设计的高效喷射旋流曝气除尘脱硫塔,高效旋流曝气脱硫塔为圆柱形塔体,塔外有高效射流器,塔内安装有高负荷旋流装置和高效深度除雾装置。
脱硫工作时,烟气由塔壁切向进入,形成旋转气流上升,烟气通过旋流筒的导向作用使烟气呈旋转上升。
经二次扩散,使得气体里所含的二氧化硫散发,并与上部两层喷淋的脱硫浆液充分接触,从而增大气液间的接触面积;液滴被气流带动旋转,产生的离心力强化气液间的接触,最后液滴被甩到塔壁上沿壁流下,经过溢流装置到下层塔板上,再次被气流雾化而进行气液接触。
如上所述,液体在与气体充分接触后得到有效分离,避免雾沫夹带,其气液负荷比常用塔板大一倍以上。
又因塔板上液层薄,开孔率大而使压降较低,比达到同样效果的一般旋流板塔的压降约低50%,因此,综合性能优于常用的旋流板塔。
由于装置内部提供了良好的气液接触条件,气体中的SO2被碱性液体吸收的效果好;采用较低的液气比。
高效喷射旋流脱硫塔内装有高效深度净化电除雾装置,解决出口烟气带水的危害。
6.3两段双循环脱硫技术:
采用两段多级脱硫层空间,在不同的段采用不同的PH值脱硫剂,对烟气进行高效脱硫。
6.4电除雾技术
针对现有脱硫技术存在的缺点,塔顶增设电除雾技术原因分析
⏹脱硫后的排烟温度仅50℃左右,虽然对烟囱进行了防腐,但防腐效果较差,烟囱低温SO3腐蚀严重。
⏹脱硫后的烟气中含有大量水雾、硫酸雾及微细气溶胶,这些物质在烟囱附近飘落,气温低时易形成“尘雨”或“小雪花”。
“景观”污染非常严重。
⏹湿式静电除雾器能有效去除烟气中的氨、铵盐、SO3酸雾、PM2.5、细小液滴、汞等重金属,去除率可达90%以上,使出口烟气处于酸雾几乎被全部去除的比较“干”的状态,有效地降低了SO3酸雾冷凝对烟囱造成的腐蚀速度,并且大大降低了烟气的浑浊度,并具有SO2联合脱除的效果,出口含尘量降低至10mg/l,实现烟气高度清洁排放。
7.几个关键难题的解决
7.1系统不结垢、堵塞
解决系统不结垢堵塞的关键技术
1)空塔喷淋具有自清洁能力,塔体不结垢、不堵塞;
2)设置有pH值自控能力,保证系统pH值符合规程运行;
3)钙法采用控制CaSO3、Ca(HSO3)2比例,达到既保证脱硫效率又可避免结垢的最佳配置;
4)采用自动供浆,管道中流体流动设计无死角。
7.2系统不带水
湿式脱硫除尘系统最怕带水和结露,带水结露会带来烟道、烟囱及风机的腐蚀和破坏,这是用户最关注的问题之一。
解决带水结露问题,我们采用以下几项专有技术:
一是设计高效的凝并惯性除雾器,保证除雾效率达到99%以上;
二是塔顶设计深度净化装置,使出口烟气处于酸雾几乎被全部去除的比较“干”的状态,有效地降低了SO3酸雾冷凝对烟囱造成的腐蚀速度,并且大大降低了烟气的浑浊度,实现烟气高度清洁排放。
7.3脱硫系统腐蚀、磨蚀问题
烧结烟气中含有HF、HCL、SO2等强酸性气体以及重金属离子粉尘,这些物质溶于水后形成强酸并使将液中含有氯离子和重金属离子,对设备腐蚀较为严重,对此采用如下方案解决:
一是对处于“干—湿”界面的设备选用非金属材料;
二是吸收塔内的冲洗管道等制作成分段式,用法兰连接,部分腐蚀部分更换,无需一处腐蚀整根更换,从而减少运行成本,且方面便检修。
7.4耗水量低
循环湿式脱硫系统的主要耗水量在烟气带走水量,本设计保证烟气含湿量在5%以下,耗水量是进口空塔技术的1/2~1/4以下。
7.5免维修的耐高温防腐设计
本设计主体设备(吸收传质塔、除雾器等)、烟道均选用碳钢防腐,系统出现故障时,允许高温气体在系统中流动半小时到一小时,给操作和维修人员有足够的应急处理时间。
更重要的是提高了系统的安全可靠性,降低了系统的联锁控制保护要求。
7.6适应烟气在一定范围内的变动
本设计适应烟气含硫在800-1000mg/Nm3内调节脱硫剂用量。
五、工艺流程及工艺说明
1.工艺流程(见附件)
2.工艺流程说明
根据锅炉烟气特点,我公司针对SO2采用湿法(氧