锡的火法精炼.docx
《锡的火法精炼.docx》由会员分享,可在线阅读,更多相关《锡的火法精炼.docx(9页珍藏版)》请在冰豆网上搜索。
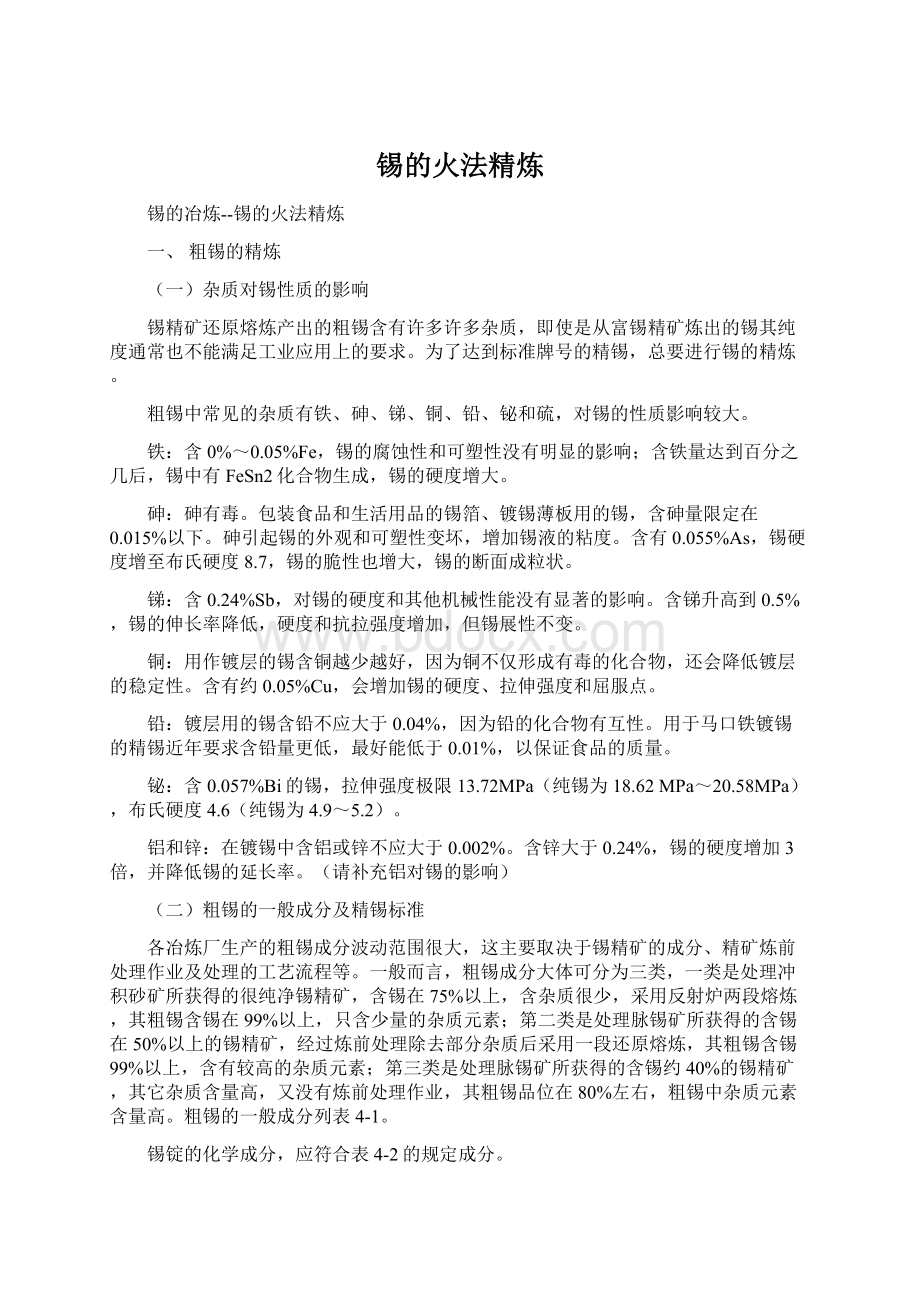
锡的火法精炼
锡的冶炼--锡的火法精炼
一、 粗锡的精炼
(一)杂质对锡性质的影响
锡精矿还原熔炼产出的粗锡含有许多许多杂质,即使是从富锡精矿炼出的锡其纯度通常也不能满足工业应用上的要求。
为了达到标准牌号的精锡,总要进行锡的精炼。
粗锡中常见的杂质有铁、砷、锑、铜、铅、铋和硫,对锡的性质影响较大。
铁:
含0%~0.05%Fe,锡的腐蚀性和可塑性没有明显的影响;含铁量达到百分之几后,锡中有FeSn2化合物生成,锡的硬度增大。
砷:
砷有毒。
包装食品和生活用品的锡箔、镀锡薄板用的锡,含砷量限定在0.015%以下。
砷引起锡的外观和可塑性变坏,增加锡液的粘度。
含有0.055%As,锡硬度增至布氏硬度8.7,锡的脆性也增大,锡的断面成粒状。
锑:
含0.24%Sb,对锡的硬度和其他机械性能没有显著的影响。
含锑升高到0.5%,锡的伸长率降低,硬度和抗拉强度增加,但锡展性不变。
铜:
用作镀层的锡含铜越少越好,因为铜不仅形成有毒的化合物,还会降低镀层的稳定性。
含有约0.05%Cu,会增加锡的硬度、拉伸强度和屈服点。
铅:
镀层用的锡含铅不应大于0.04%,因为铅的化合物有互性。
用于马口铁镀锡的精锡近年要求含铅量更低,最好能低于0.01%,以保证食品的质量。
铋:
含0.057%Bi的锡,拉伸强度极限13.72MPa(纯锡为18.62MPa~20.58MPa),布氏硬度4.6(纯锡为4.9~5.2)。
铝和锌:
在镀锡中含铝或锌不应大于0.002%。
含锌大于0.24%,锡的硬度增加3倍,并降低锡的延长率。
(请补充铝对锡的影响)
(二)粗锡的一般成分及精锡标准
各冶炼厂生产的粗锡成分波动范围很大,这主要取决于锡精矿的成分、精矿炼前处理作业及处理的工艺流程等。
一般而言,粗锡成分大体可分为三类,一类是处理冲积砂矿所获得的很纯净锡精矿,含锡在75%以上,含杂质很少,采用反射炉两段熔炼,其粗锡含锡在99%以上,只含少量的杂质元素;第二类是处理脉锡矿所获得的含锡在50%以上的锡精矿,经过炼前处理除去部分杂质后采用一段还原熔炼,其粗锡含锡99%以上,含有较高的杂质元素;第三类是处理脉锡矿所获得的含锡约40%的锡精矿,其它杂质含量高,又没有炼前处理作业,其粗锡品位在80%左右,粗锡中杂质元素含量高。
粗锡的一般成分列表4-1。
锡锭的化学成分,应符合表4-2的规定成分。
(三)锡的精炼方法
精炼锡通常采用火法冶金和湿法冶金(电解)两种方法。
火法精炼锡的过程是由一系列的连续作业组成的,其中每一种业能够除能够除去一种或两种杂质。
火法的优点是生产能力较高,并且不使金属长期停滞在生产过程中,积压的锡量少。
此外,火法精炼使杂质能够依次地提取出来,并富集于各种精炼渣中,这就为综合回收这些金属提供了条件。
国内外炼锡厂多数厂是以火法精炼为主,辅以电解精炼,少数冶炼厂采用全电解精炼。
火法精炼是利用锡与杂质对氧、硫和氯的亲合力的差别,以及与杂质生成不溶于液于液体锡的化合物的药剂作用,来达到精炼目的。
这些工序具有一个共同的特点,即生成的化合物杂质浮在液体锡上,可以固体或粘性产物形式从金属表面捞去。
二、锡的火法精炼
(一)火法精炼的原则流程
各炼锡厂粗锡所含杂质不同,生产规模不同,以及原料供应及设备条件不一样,因而火法精炼流程也不一样。
对于熔炼含杂质少的高品位精矿所产的粗锡,如马来西亚、泰国等,只用1~2道火法精炼作业就能得到高级精锡,精炼回收率达到99.45%。
处理粗锡含杂质高的火法精炼流程比较长。
我国某冶炼厂,由于粗锡杂质含量高,采用图4-11所示的火法精炼流程,其中每一道作业除去一种或两种杂质,而有的杂质在几种作业中逐步除去。
例如砷就在三个作业中相继除去(离心除铁、砷,凝析除铁、砷,加铝除砷、锑)。
图4-11锡火法精炼原则流程
(二)熔析、凝析法除铁、砷
熔析法、凝析法的理论根据是铁、砷等杂质在锡液中与锡生成的高熔点金属间化合物在锡液中的溶解度随温度升高而增大。
熔析法将含铁、砷高的固体粗锡(生产中称为乙粗锡),加热到锡熔点以上,高熔点金属间化合物保持固体状态,而锡熔化成液体,分开固体和液体,从而使锡与铁、砷分离;相反,凝析法是将含铁、砷料低的已熔成液体粗锡(称为甲粗锡)降温,由于溶解度降低,铁、砷及其化合物结晶为固体析出,分离出固体后,得较纯的液体锡,达到锡与铁、砷分离。
1.熔析法、凝析法除铁、砷的原理
锡精矿还原熔炼得到的乙粗锡是以锡为主含铁、砷较高的粗锡,一般含1.5%~5%As,1%~10%Fe。
根据Sn-Fe系状态图(图4-12),锡和铁生成Fe3Sn、Fe3Sn2、Fe1.3Sn、FeSn、FeSn2等金属间化合物。
取Sn-Fe系的富锡端部分状态图(图4-13)说明加热过程中铁与锡分离的情况,当温度升到232℃,开始熔析出较纯的液体锡并不断移去,温度在232~496℃间,铁以FeSn2化合物保持固体状态留在粗锡残锭上。
当温度由496℃升到901℃时,含铁的粗锡残锭中不断熔化并析出未形成化合物的液态残锡外,同时金属间化合物不断分解而析出液态锡,而剩下的Sn-Fe合金视熔析温度不同分别以FeSn、Fe3Sn2、Fe3Sn、ɑ-Fe等形态残留在固相残渣中(称为熔析渣)。
可见,在升温过程中固体渣(熔析渣)含锡逐渐降低,而含铁逐渐升高;相反,熔析出的锡随温度升高,含铁量上升,其铁的溶解度值为:
从Sn-As系状态图(图4-14)富锡端可以看出,砷或Sn3As2化合物在锡液里的溶解度随随温度上升而增大。
熔析温度在232~596℃时,Sn3As2保持固体状态与锡液分离,超过596℃,Sn3As2将熔化,失除砷作用,故处理含砷高而含铁低的粗锡时,熔析温度应低于596℃。
粗锡中铁、砷同时存在,对熔析除铁、砷有利,因为铁对砷的亲合力大,生成两个化合物Fe2As(熔点931℃)和FeAs(熔点1031℃),其间还有ε相(Fe3As2)包晶化合物。
这些化合物和ε相的熔点和分解解温度都很高而保留于熔析渣里。
粗锡中存在许多杂质,相互生成一些难熔化合物,表4-3列出可能存在的化合物,这些化合物在乙粗锡熔析时大部分留在固体渣(熔析渣)中,因此,熔析除铁、砷时,也附带除去一些别的杂质,如硫、锑、铜等。
熔析法可除去粗锡中大部分铁、砷,但不能使其含量达到符合精锡标准,因此,在熔析除铁、砷后粗锡需经凝析法处理。
凝析法是将液体精锡降温,铁和砷在锡液中的溶解度减小,达到过饱和状态成固休析出而分离。
在锡的熔点232℃时,铁的溶解度为0.001%,在300℃时,铁的溶解度为0.0046%。
因此,将粗锡液温度降低到锡深点附近,由锡液中凝析出FeSn2的细粒晶体,可使含铁量降低到约0.001%,能满足精锡的含铁要求。
在相同温度下锡液能溶解的砷量比铁多。
在232℃时,砷的溶解度为0.14%~0.18%。
锡液中若有铁和砷共同存在,对除砷有利,锡液中As/Fe值减少时温度对砷在锡液中溶解度的影响。
故锡液中有铁存在时有利于凝析除砷。
2. 熔析法除铁、砷实践的生产工艺及设备
在炼锡厂熔析设备主要用反射炉,少数也用电炉。
用反射炉作熔析设备,其炉床为斜底,面积较小。
否则加入乙粗锡。
熔析作业后期翻渣出渣都不方便,炉内各点温度也不均匀,炉床面积以10m2左右为宜。
炉床用粘土砖砌成,三面高,向放锡口方向倾斜。
也有的工厂炉床分为两个区,温度较高的区域靠近燃烧室,用耐火砖砌成,靠炉尾一端是温度较低的区域,用生铁板做成,粗锡先在低温区熔析,而后再扒到高温区处理。
熔析法为间断作业,在反射炉中操作,每个工班处理一炉,也有三个班处理四炉的。
出完前一炉熔析渣,炉温尚保持在700℃以上,接着进下一批乙粗锡。
锡锭从侧墙炉门加入,也有从炉顶加入到炉膛中,靠近火室的一端多加些锡锭,靠炉气出口的一端少些,使乙锡受热均匀。
乙粗锡进完后,炉温下降至300℃,然后逐渐升温,使熔析速度加快。
熔析过程到后期,开始翻渣,把料堆底部受热少含锡高的固休料翻到面上,以便升高温度,降低含锡量,炉温相应地提高到800~900℃。
当发现熔析渣有变稀的趋势时,应降低炉温,避免生成Sn-Fe合金大块,这样才能降低熔析渣含锡,同时又不致给出渣和清炉造成困难。
翻渣操作每炉2~3次。
当熔析渣变成红色粒状/表面无锡珠,便可出渣。
从开始进料到出渣完毕约4~7h;但遇到处理含砷高而含铁很低的乙粗锡,因熔析温度不允许升得太快和过高(低于600℃),作业时间长达8~9h。
熔析控制的技术条件主要是温度。
3.凝析法除铁、砷实践生产工艺及设备
火法精炼中凝析除铁、砷,加铝除锑、砷和加硫除铜所用的制设备都由精炼锅的搅拌两部分组成。
在操作中有的工厂采用空气、蒸汽吹炼液体锡。
采用这种方法时,除去部分铁与其杂质一起除去。
熔锡由沉降桶直接倒入大铸铁锅中,并鼓风或使蒸汽通过熔化的锡,使其“沸腾”。
在靠近锅附近的鼓风管或蒸汽管内安装聚水器,因为液态水的任何“液滴”,若被鼓入熔融锡内,将引起猛烈爆炸。
在金属表面上有糊状的浮渣生成,捞去浮渣。
此外,有的炼锡厂,由于铅、砷、锑在焙烧时除去,铜、铋含量极少,需要除去的杂质只有铁,因此,只需将反射炉精锡冷却至300℃,用浮渣笼取去表面渣,吹入0.49MPa的压缩空气保持温度400℃,扒渣两次,即得到精锡,全部过程只用3.5~5小时。
凝析除铁、砷采取加锯木屑促使晶体悬浮物与液体锡达到分离。
粗锡装锅后,锡液的温度为280℃~300℃,观察有无砷、铁化合物结晶析出。
如果锡液的温度高,看不到砷、铁化合物结晶析出时,则应降温搅拌,加入适量的锯木屑,捞去浮渣(炭渣),呈现洁净的锡液面。
随着温度逐步降低,砷、铁化合物结晶析出逐渐增多,如果粗锡含砷多,含铁很少,Sn3As2结晶析出,锡液面上有砂粒状耀眼的粒子,这时降温凝析、搅拌凝聚,投进锯木屑吸附,投入量以不影响旋涡正常为适度,并捞去浮渣。
要多次降温、搅拌、加锯木屑、捞去浮渣重复操作。
结粗锡含水量铁、砷相等或铁比砷多的情况,液态粗锡降温冷却时,铁和砷优先结合,生成Fe—As固体化合物。
它们的密度小于锡液的密度,上浮在锡液表面,再加上它们凝聚性强,凝聚成非常粘稠的浮渣。
这时开始搅拌并加入锯木屑,促使晶粒凝聚和上浮,锯木屑也增加这些浮渣的孔隙度,有助锡液滴汇聚增大,穿过浮渣层回到锡液中。
上述作业也要反复多次进行,直到将温度降至锡液熔点附近,强烈搅拌而不再析出渣子,则铁已除到0.003%以下,砷达到0.03%以下,完成凝析作业。
利用砷和铁的性质曾做过生产实验。
粗锡中的砷除到0.2%以下时,往锡液中加入一些含铁高的粗锡,而后凝析加锯木屑,可进一步降低砷在锡中的含量。
但粗锡含砷在0.2%以上时,补加铁就没有意义了。
此时,没有铁的存在,砷不仅能以Sn3As2结晶析出,而且产出的晶体粒子相互碰撞而长大,无粘稠性。
所产生的炭渣机械带走的锡很少。
(三)离心机除铁、砷
无论是熔析法还是凝析法除铁、砷,其实质都是一定温度下,铁、砷和锡互相间生成的不溶于液体锡的杂质结晶化合物,呈固体或浮渣状,用人工或简单机械从锡液表面捞去这些浮渣,达到除铁、砷。
人工捞渣,劳动强度大,作业环境 差而且浮渣中残留大量的机械夹杂的锡,这即给一一步处理浮渣带来困难,也影响锡的回收率。
分离液、固相最有效方法之一为离心过滤法。
但要在火法冶金中采用离心机技术,要解决许多工艺上的困难,首先是制造心机的材料应承受很高的温度,而且要具有很好的耐蚀性,其次设备结构要适用于液体锡与浮渣的分离。
第一台金属液离心机是本世纪30年代由维克托·杰·斯特伦期在英国泰国河畔的纽卡斯尔设计制造的,用来旋转干燥在精炼焊锡时得到的金属互化物浮渣。
此设备的主要特点是在垂直钢轴的下端,固定有;边缘略成锯齿形的圆形钢底板构件,一个与金属底板靠紧并锁定,也并能在排料时向上移开底板。
前苏联科学院会同新西伯利亚炼锡厂最初制定了工业性离心过滤机的第一个方案,此过滤机为一液压传动的固定装置,作为含大量铁、砷和铜杂质的粗锡净化设备。
锡用机械手从两个5t精炼锅给至离心机。
固定式离心机的缺点是过滤后粗锡的成分取决于过滤温度,但过滤温度又与原粗锡成分有关,为了有交效脱除铁、砷,就需经过多次离心过滤,而且要在较低温度下进行,需要的时间长,增加金属损失和能源消耗。
从1970年开始,苏联进行了沉没式离心机的研究。
沉没式离心机的转鼓在运转时,位于被精炼的粗锡中,这样就带来许多优点:
不需要专门的加料装置,因为在转鼓旋转时,锡渣形成旋涡,自动流入离心机内,没有飞溅现象,减少了锡的氧化损失;最主要的在沉没式离心机内可以在降低粗锡温度下进行,即随着从粗锡中杂质的除去,锡液温度不断下降,杂质呈不溶化合物较完全的脱除。
云锡研制的YT-CC-I型离心机,主要由转鼓、离心机悬臂和油压系统组成。
该公司使用这种离心机处理乙粗锡,以代替熔析炉除铁、砷,效果比传统除铁、砷法显著。
(四)加硫除铜
1.加硫除铜的原理
利用铜对硫的亲和力大于锡对硫的亲和力,当硫磺加入粗锡后,硫与铜化合生成硫化铜(Cu2S),它熔点高(1130℃),密度小(5.6g/cm3),不溶于锡液中,并且比锡轻,浮在锡表面成为硫渣(也称作铜渣)。
由于锡液的浓度大,加入的硫绝大部分先溶解于锡液中,然后再与铜反应:
Sn+S=SnS+22.2kcal (4-3-1)
2Cu+SnS=Cu2S+Sn-3.1kcal (4-3-2)
通常简化为:
2Cu+S=Cu2S+18.9kcal (4-3-3)
2.加硫除铜的生产实践工艺:
凝析法除砷、铁之后,将锡液升温至240~250℃,搅拌至行程旋涡,用铁铲将硫磺沿旋涡小铲缓缓加入。
加硫量根据粗锡的含铜量和下列化学反应而定:
2Cu+S=Cu2S (4-3-4)
从反应式中可以得知,Cu:
S=4:
1,考虑到一部分杂质消耗硫和燃烧损失,实际加硫量比理论加硫量过量23~30%。
生产实践中通常按Cu:
S=3.5:
1计算加入硫磺。
如果粗锡含Cu﹥0.5%,应先加硫除铜,再凝析法除砷、铁,若粗锡含铜过高,需要加入的硫较多,一次加入后将造成渣量过多,影响搅拌,并使锡液温度迅速升高,硫大量燃烧损失,故应分次加入,每次加入硫磺量不应超过100kg。
先加硫除铜,对下一步凝析除砷有利。
若粗锡含铁高,又将反过来影响加硫除铜效果,因此要排除铁的影响。
当铁完全溶解于锡液中时,对除铜没有影响,铁含量超过溶解度,过量的铁便会结晶析出,变成粘稠的浮渣,把没有和铜反应的硫包裹起来,影响Cu2S的生成。
另外,还会增加硫渣的粘性而难以搅散成粉状渣,使渣含锡升高。
解决的办法:
一是升高锡液温度,使铁完全溶解于锡;二是加完硫继续搅拌时补加锯末,使凝析出来的固体粒子吸附在锯末上变成炭渣,防止铁对加硫除铜的干扰,得到的硫渣实际上是硫渣和炭渣的混合物。
加硫除铜的技术指标如下:
硫渣率2%~4%;锡直收率97%~99%;耗硫量为处理1t粗锡用硫0.24kg;硫渣成分(%)为:
Sn55~56,Cu10~22,Fe0.5~2;AS1~2,S3~6,除铜效率大于96%。
(五)连续结晶机除铅、铋
粗锡中一般含有铅和铋。
粗锡火法精炼除铅,国外在20世纪70年代前采用氯化法,即于300℃下使Pb生成PbCl2除去。
氯化法除铅,不但消耗大量的试剂,产出大量的浮渣,而且除铅效率低,劳动条件差,对含铅高于5%以上的粗锡用此法更不适宜。
国外有些工厂加钙镁除铋,国内均不采用。
我国炼锡厂的粗锡历来含铅、铋均较高。
因此一直采取了熔析、结晶法除铅、铋。
结晶放液法在生产中使用了二十多年,也作过多次改进,但是结晶、放液是间断进行的,大量是手工操作,生产率低,劳动强度大,难以达到高质量锡的要求。
如何使熔析结晶法连续化机械化,引起了国内外炼锡专家的广泛注意。
我国昆明理工大学戴永年院士等冶金工作者经过多年的研究试验,对结晶机的结构和温度的合理分布及自动控制均作了改进取得了满意的效果,成为现今用于生产的电热连续结晶机。
这一设备不仅在国内各个炼锡厂使用,而且已推广到美洲、亚洲、西欧等十多个炼锡厂,是我国炼锡工业的独特创造。
1. 连续结晶,熔析除铅、铋的基本原理
从Sn-Pb系二元相图(图4-15)可见,在富锡端,设某一成分的合金,其成分为C0,当加热到232℃以上而缓慢冷却产出固相(晶体)时,溶质金属铅在晶体中的浓度C1与在未结晶的液相(液体)中的浓度C2之比称为平衡分配系数K0,其方程式为:
K0=C1/C2 (4-3-5)
若K0<1,表明铅在晶体中的浓度小于相应的液体中的浓度,则晶体得到提纯;若K0>1,表明液体得到提纯。
为了求出Sn-Pb系富锡端溶质金属铅的平衡分配系数,可列出固相线AB和液相线BC的方程,以y表示温度(纵坐标),C1和C2分别表示平衡晶体和液体的含铅量(横坐标),在假设固相线和液相线为近似直线时,其斜率分别为:
18.84,1.280。
固相线方程 y1=232-18.84C1 (4-3-6)
液相线方程 y2=232-1.280C2 (4-3-7)
两相达到平衡,温度相等,y1=y2
则 232-1.280C2=232-18.84C1
K0=C1/C2=1.28/18.84=0.068
由此看出,溶质金属铅的平衡分配系数小于1,说明在晶体中的铅比在液体中的铅低得多,只要晶体和液体能够分离,晶体便能得到提纯。
要在一台设备内,达到连续结晶、熔析除铅的目的,首要的条件是在设备的两端,严格控制由锡、铅共晶熔点183℃至精锡熔点232℃之间的温度梯度;其次必须保证在183~232℃之间连续结晶、熔析过程中晶体和液体的分离;此外,在连续进料的同时,必须达到进料和出料的平衡。
在设备结构上,采用电加热控制所需的温度,采用槽体倾斜和螺旋搅拌提升的方法实现结晶、熔析过程中产出的晶体和液体的分离,满足除铅工艺的要求。
为了说明结晶、熔析除铅的具体过程,取Sn-Pb合金相图富锡端绘制成晶体和液体成分随温度变化关系示意图于图4-16中。
任一时刻,任一成分的合金,在冷却时产生晶体,在螺旋器的作用下,逐渐向温度升高的区域移动;相反,残留的液体靠重力和结晶槽坡度向低温区回流。
温度上升后,原有晶体和流体间的平衡关系受到破坏,而在新的温度条件下将建立新的平衡,在高温下熔析液体在低温下将发生结晶。
熔析时将分别熔出L1,L2,…,Ln液体,晶体熔析的结晶使晶体本身锡的纯度逐渐升高,熔出的液体向低温回流,必然结晶出晶体β1,β2,…,βn才能建立新的平衡。
结晶的结果液体中锡的纯度降低。
这些与晶体逆向运行的液体,不仅与下一级晶体进行热交换,同时也进行质交换。
由此看出,由于电热连续结晶机内形成温度梯度和螺旋器的作用,而又重新不断建立晶体和液体之间新的平衡,这种晶体和液体间平衡的破坏和建立的对应统一,使得结晶、熔析过程连续进行。
当晶体达到结晶机高温出料端时,产出含铅低于0.04%的产品锡,液体到达低温焊锡放出口时,得出含锡低于67%的锡、铅焊料合金。
从Sn-Bi系相图(见图4-17)可见,在富锡端液体粗锡降温结晶出α相固溶体(晶体),含铋减少,而平衡的液体合金中含铋升高,故粗锡中的铋也和铅一样,一同进入焊锡。
对于含铅高而含铋低的合金,采用结晶、熔析法除铅、除铋效果均好;而对于含铅低而含铋高的粗锡,采用结晶、熔析法除铅效果好,但除铋效果差。
为了达到除铋效果,必须加铅到粗锡中,再用连续结晶、熔析法处理。
分析其原因:
比较Sn-Pb(图4-15)、Sn-Bi(图4-17)、Pb-Bi(图4-18)系状态图可知,都存在有限固液体,但前两个中间没有化合物,Bi-Pb系则有包晶化合物BiPb3存在,因此,锡、铅、铋原子间相互结合的能力应该是Pb-Bi大于Sn-Bi和Sn-Pb,在含铋粗锡中配入适量比例的铅,铋被铅带入焊锡。
结晶、熔析法除了达到除铅、铋外,由于铟、银与锡均能形成低熔点共晶体,故还可将粗锡中的铟、银富集到焊锡中。
2.连续结晶机的结构
连续结晶机主要由螺旋器、电炉体、温度控制和传动机构等组成。
螺旋器由扇形叶片交错焊接在无缝钢管的螺旋轴上而成。
每片扇形夹角120°,三片绕轴一周,焊接在螺旋轴上。
扇形叶片之间的距离各不相同,在进料口部位,冷却结晶产出的量大,扇形叶片之间的距离要大些,进料口上端的叶片距离小些,扇形叶片还与轴向成一定的交角。
螺旋器是结晶机的主要部件,它有三个作用:
搅拌合金,减少扩散层厚度,加速热交换和质交换,提高铅、铋和锡的分离效率;提升晶体,将结晶产出的晶体不断地向温度高的方向提升,使晶体与液体形成逆向运动;由于螺旋叶片有一定的后倾角,可把晶体压入液体,进行热交换和质交换。
电炉体由内槽、外槽、电阻丝、保温材料等组成。
内槽是断面为U型的敞开槽,整个精炼在内槽进行。
敞开槽便于观察和检修,同时也便于喷水冷却结晶,用12mm厚的钢板卷制而成,生产能力大,内槽的断面就大。
外槽也用钢板卷制而成,用于承受保温和耐火材料,电阻丝安放在耐火材料的刻槽内。
电阻丝布置十分重要,分为固定常开负载和调节负载。
固定常开负载,即通电后不断电,作为基本供热的电源,容量为25~35kW。
调节负载,即在生产过程中根据温度的需要,电功率可以调节。
这样布置,宏观上将电炉体分为多个不同温度带,但由于对流和传导传热,实际上从电炉体的尾部(焊锡排放口)到电炉体的端部(精锡出口)形成一个稳定的温度梯度,从而满足了工艺要求。
(六)加铝除砷、锑
1.加铝除砷、锑的基本原理
粗锡经过凝析除砷、铁后,虽然大部分砷已除去,但锡中含砷仍有0.15%左右,使用凝析法处理粗锡时,含锑量没有明显的变化,仍达不到精锡标准,有待进一步除去。
目前国内外炼锡厂仍普遍采用加铝除砷、锑。
加铝除砷、锑原理是利用铝和砷、锑生成高熔点化合物,其密度小于锡,能从锡液中结
晶析出。
As-Al系状态图见图4-19,Al-Sb系状态图见图4-20。
从图可以看出,铝和砷生成As-Al,其熔点为1740℃,铝和锑生成AlSb,其熔点约为1081℃。
这两种化合物的成分按化学式计量(质量比),As:
Al≈1:
0.36,Sb:
Al=1:
0.22。
在生产实践中,加铝除砷,1kg砷加0.36kg铝,可以达到预期的结果,而除去1kg锑需加1kg铝。
生产上遇到砷、锑要同时除去时,为了计算上的方便,可用下式计算:
(As+Sb):
Al=(1~1.5):
1。
加铝除砷、锑在火法精炼流程中可以在结晶、熔析除铅、铋之前或在其后进行,但对除砷、锑的效果相同。
对生产实践来讲各有利弊,前者的优点是砷、锑脱除达到标准后,在连续结晶机除铅铋时,内槽中的晶体硬度和粘度较小,可减轻螺旋器的负荷,晶体和液体的分离条件得到改善,有利于除铅、铋。
同时在加铝除砷、锑后,残余铝如果操作不仔细,残留下来的铝也会在结晶机内槽中继续氧化造渣而除去。
缺点是,要求除锑的程度低于标准含量,否则结晶提纯时,锑会在结晶体中富集,可能使含锑合格的锡在结晶处理后反而不合格。
加铝除砷、锑放在结晶、熔析除铅、铋之后的优点是加铝除锑只需达到精锡标准即可。
2.加铝除砷、锑的实践工艺
加铝除锑和加铝除砷的操作技术条件有所不同,加铝除锑的技术对除砷有同样的效果,但加铝除砷的技术条件对除锑没有明显作用,现分述如下。
(1)加铝除锑
将需要除锑的锡升温到380~400℃。
根据Sb:
Al=1:
1计算用铝量。
铝片先加工成厚1~2mm,宽10~20mm,长小于50mm的薄片,搅拌锡液产生旋涡,铝片投入旋涡,投入量应不影响旋涡的正常存在,铝片很快熔入锡液便和锑化合成AlSb。
铝片加完后,继续搅拌20~30min待作业完成,然后按精炼锅外围水套降温规程进行降温到230~235℃,使高熔点的AlSb冷凝析出。
接着开始加NH4Cl,使铝渣疏松多孔,降低铝渣含锡,