汽车底盘制造度质量指标体系规划报告.docx
《汽车底盘制造度质量指标体系规划报告.docx》由会员分享,可在线阅读,更多相关《汽车底盘制造度质量指标体系规划报告.docx(38页珍藏版)》请在冰豆网上搜索。
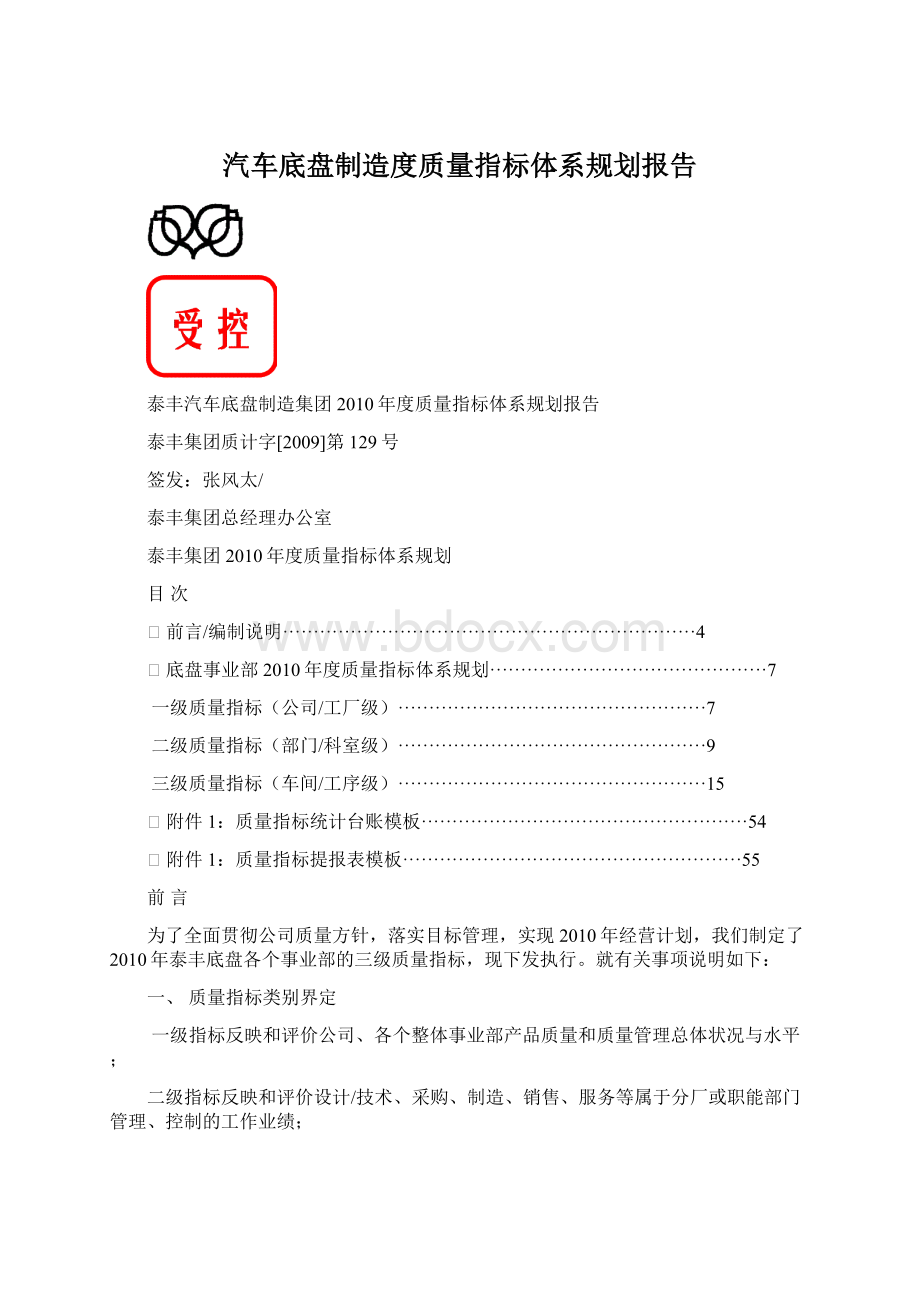
汽车底盘制造度质量指标体系规划报告
泰丰汽车底盘制造集团2010年度质量指标体系规划报告
泰丰集团质计字[2009]第129号
签发:
张风太/
泰丰集团总经理办公室
泰丰集团2010年度质量指标体系规划
目次
Ø前言/编制说明···································································4
Ø底盘事业部2010年度质量指标体系规划·············································7
一级质量指标(公司/工厂级)··················································7
二级质量指标(部门/科室级)··················································9
三级质量指标(车间/工序级)··················································15
Ø附件1:
质量指标统计台账模板·····················································54
Ø附件1:
质量指标提报表模板·······················································55
前言
为了全面贯彻公司质量方针,落实目标管理,实现2010年经营计划,我们制定了2010年泰丰底盘各个事业部的三级质量指标,现下发执行。
就有关事项说明如下:
一、质量指标类别界定
一级指标反映和评价公司、各个整体事业部产品质量和质量管理总体状况与水平;
二级指标反映和评价设计/技术、采购、制造、销售、服务等属于分厂或职能部门管理、控制的工作业绩;
三级指标反映和评价科室、车间/工序/工位等执行/操作层面完成/实现工作、生产任务,达到的质量水平。
二、质量指标制定原则
1)一级质量指标是实物、管理综合性指标;二级质量指标采取考察产品实物质量与工作质量并重原则;三级质量指标以考察所达到的产品实物质量水平为主;
2)质量指标的设置必须覆盖主要业务环节内容,突出重点/关键/特殊工序,突出管理、控制重点/难点,特别是顾客(主机厂、市场)抱怨、投诉、关注的焦点问题,明确改进/改善的方向;
3)确实有必要设置,而因目前暂无历史数据无法确定具体数值的质量指标,作为观察指标项目列入;
4)在原始数据记录、采集和提报的规范性得到保证的前提下,尽可能采用量化指标(数值型、比例型);如果获得数据全面、完整、准确,尽可能采用比例型指标(百/千分率、PPM等);不能定量或定量有困难的质量指标,则采用综合评级的定性方法(A级、B级、C级),必要时根据级别打分(百分制)
5)沿用2009年的质量指标,则以2009年实际统计指标完成值为依据和参考,在维持现有质量水平基础上,适度考虑质量提升空间,同时还应考虑到其它相关因素影响(例如:
旺季/淡季等)确定2010年各个季度的目标值;
6)动态管理,及时完善。
责任单位应及时将实施过程中出现的问题反馈质量部,质量部及时与集团公司沟通。
如有必要,则将组织评审、讨论之后对相关内容进行调整、修订。
三、相关要求
1)本质量指标体系是集团公司年度质量指标总体规划,各个事业部应按照质量指标“全员挂钩”的指导原则,此为依据,逐级进行月度分解,并要求分解到每一个员工,实现“人人有指标”,将分解计划和月度考核结果报集团公司备案;各单位应建立质量指标统计台账;(格式模板参见附件1),
2)各个部门应指定专门负责采集、汇总、统计、提报质量指标原始数据的人员,每月3日之前填报完毕并上报;部门负责人对于数据的真实性、准确性负责;(格式模板参见附件2)
3)各种质量指标统计相关的原始数据必须保留以备查考;
4)质量指标作为考核指标时,相关数据需要经过责任单位的确认、复核,允许申诉;涉及到自身利益的指标时,应遵循利益回避的原则,其它部门参与确认(相关单位部门会签确认);观察项目暂不纳入考核;
5)必要时由质量部组织对质量指标进行评审,以决定是否对于指标设置进行调整,是否采信、采纳有关意见。
一、底盘事业部2010年度质量指标体系规划
底盘事业部
一级质量指标(公司/工厂级)
序号
质量指标名称
指标含义及统计方式/方法、评定/判定标准
责任主体
2009年
实际值
2010年目标值(季度)
提报单位
备注
一
二
三
四
1
质量事故、重大/批量质量问题
[次]
●特大质量事故(下列情形之一):
1质量问题导致被一次索赔/损失≥1万元
2质量问题导致被取消供货资格;
3质量问题导致长时间停线停产;
4质量问题人员伤亡/重大财产损失、导致诉讼,媒体曝光,信誉/形象严重损坏
事业部领导、相关部门
13186系列车架因螺栓设计问题发生1次
0
0
0
0
销售公司
生产部
质量部
问题定性:
可由专题会讨论决定;承担责任/考核比例可视具体情况划分确定
●重大质量事故(下列情形之一):
1质量问题导致被一次索赔/损失≥5千元
2质量问题导致被停供、批量退货;
3质量问题导致停线停产≥4小时;
4质量问题导致批量返工损失≥1千元
5短时间内重复发生的批量问题
≥5千元质量索赔次数:
车架8次,油箱7次,传动轴15次
2
产品出厂合格率[%]
●公式:
合格台数/出厂待检总台数×100%
●采用底盘公司主导产品合格率的加权平均值
车架合格率×0.7+油箱合格率×0.1+
传动轴合格率×0.1+中央制动器合格率×0.1
事业部领导、相关部门
96.36%
96.4
96.5
96.6
96.7
质量部
产品加权平均09年出厂合格率公式(1-市场反馈不合格台数/出厂总台数)*100
3
工序平均下线合格率[%]
●工序平均下线合格率=
∑各工序下线合格率/工序数量×100%
事业部
92.43%
92.5
93.2
93.3
93.5
质量部
油箱厂
传动轴
4
关键尺寸合格率[%]
●提供数据:
欧曼、奥铃、欧马克、欧Ⅴ等
车架
65-75%
75%
75%
76%
76%
主机厂
以欧曼为基准
5
外观质量等级率[评级]
●提供数据:
欧曼、奥铃、欧马克、凯马等
车架、油箱
/
待定
待定
待定
主机厂
质量部
一季度积累数据
6
Audit评分限值
●提供数据:
欧曼、奥铃、欧马克、欧Ⅴ等
车架
100-120
≤90
≤90
≤90
≤90
根据主机厂
以欧曼为基准
7
市场三包期内维修费用[元]
每月三包维修费用(零部件、人工、工时、差旅、正常/日常索赔)
15-18万
/
待定
待定
待定
售后服务部
相关部门
观察项目
一季度积累数据
8
季度内审检查、评价[项]
根据内审计划进行,不符合项目
待定
待定
待定
质量部
观察项目
一季度积累数据
底盘事业部
二级质量指标(部门/科室级)
部门
质量指标名称
指标含义及统计方式/方法、评定/判定标准
2009年
实际值
2010年目标值(季度)
提报单位
备注
一
二
三
四
技术部
1)新产品(包括产品改进)项目完成(要求进度达成)率[%]
●项目完成(要求进度达成)率:
=
到期项目中实际完成项目数/到期项目总数×100%
●数据来源、提报、统计方式:
包括根据月初的开发(改进)计划进行中的项目,加上根据主机厂的要求随时补充增加的开发项目,到月底,项目负责人将交付物提交主管领导审核,判定是否完成并合格,结果提交统计员。
涉及其它部门的项目,需进行会签,必要时应组织评审。
正在进行中项目,也应纳入统计:
按照统计周期中,该项目是否应达到规定进度,视为完成或未完成
未统计
100%
100%
100%
100%
技术部
样件获得主机厂的认可,即可视为完成
2)新产品开发成功率[%]
●项目开发成功率:
=
完成批量生产准备的新产品中认定为开发成功项目数/完成批量生产准备的新产品项目总数×100%
●数据来源、提报、统计方式:
开发成功的认定:
新开发的产品,通过了试制、试验、试装、小批量试生产验证等环节,OTS获得了主机厂认可(通过PPAP)。
设备、工装、材料、工艺等达到工业化实施的要求。
完成批量生产准备。
统计方法同上。
~25%-30%
100%
100%
100%
100%
技术部
技术部
3)现场技术问题处理:
包括各类质量问题[%]
及时性,有效性[评级]
●质量部组织生产部等相关部门对当月处理涉及技术部的问题处理情况进行评审,给出综合评级
——A级:
处理迅速、及时,措施得当,有效,未对生产及交货发生影响;
——B级:
能够控制平息事端,未对生产、交货产生影响或仅有轻微影响;
——C级:
反应迟钝,处理不当/未做处理,影响正常生产供货,发生投诉
~C
≮B
≮B
≮B
≮B
生产部
质量部
生产部、技术部提出问题清单
4)工艺纪律检查[评级]
●例行的检查计划及其实施记录,后续整改的跟踪落实情况记录,等;月末根据评审结论确定给出综合评级:
(质量部、生产部等参与评审)
——A级:
圆满完成计划,发现重大问题或隐患,提出整改措施有效,督促实施得力;
——B级:
基本完成计划,有实施记录,发现了一些问题并有整改行为,效果一般;
——C级:
未做,或完成情况未达到一般要求
~C
≮B
≮B
≮B
≮B
技术部
根据检查得分确定级别
5)技术文件规范完成率[%]
●技术部提交当月编制/下发的技术文件清单,组织质量部、采购部、生产部等相关单位(包括基层科室)就技术文件(技术通知单(包括转发的)、更改单等)的及时性、准确性、完整性、适宜性、合理性、可操作性等方面逐一进行全面评审,得出合格与否的结论,计算规范性合格率。
●技术文件规范完成率:
=
认定为完成规范的技术文件数/当月计划规范的技术文件总数×100%
●必要时,由技术部提交材料,质量部门组织评审
~70%
90%
90%
90%
90%
技术部
评审的内容包括技术要求/时间节点,符合实际情况,发放范围,反馈/回执,跟踪落实,有无低级错误等方面
●严格执行公司的资料保密制度,确保公司文件、图纸、资料的安全。
观察项目
采购部
1)采购产品入厂交验批次合格率[%]
●采购产品入厂交验批次合格率:
=
入厂交验合格批次/入厂交验总批次×100%
●数据来源、提报、统计方式:
质量部外检统计、汇总,月初提报。
~90%
98%
98%
98%
98%
质量部
外检
偏差回用,让步接收的件也计入
2)采购计划完成率[%]
(采购产品按期到位率);
●采购计划完成率:
=
采购计划项目完成项次/采购计划总项次×100%
采购部月初提报上个月的采购计划的完成情况,生产部会签。
●因采购不及时、准确耽误生产计划的重大事件,以项次计算
●生产任务临时调整等情况发生的紧急采购,也列入统计范围
100%
/
待定
待定
待定
采购部
生产部
观察项目
生产部
1)产品一次交验合格率[%]
●产成品一次交验合格率:
=
一次交验合格批次/交验总批次×100%
●数据来源、提报、统计方式:
质量部内检(终检)统计、汇总,月初提报。
~92%
/
待定
待定
待定
质量部
终检
一季度积累数据
2)生产计划完成率[%]
●生产计划完成率:
=
实际完成数/生产计划数×100%
●数据来源、提报、统计方式:
生产部统计、汇总,月初提报。
未统计
/
待定
待定
待定
生产部
一季度积累数据
3)工装完好率[%]
及时维护
●工装完好率:
=
工装完好数/检查工装数×100%
●数据来源、提报、统计方式:
生产部每月定期组织所有工装完好性检查,工装管理员记录、统计
造成严重后果的,单独记录、提报,考核
未统计
/
待定
待定
待定
生产部
一季度积累数据
设备部
1)设备维护保养计划的制订与实施
计划完成率[%]
●制订月度设备维护保养计划,跟踪其落实、执行记录,月末组织评审,并根据评审结论确定给出综合评级:
(生产部、质量部等参与评审)
——A级:
计划覆盖全面、考虑周到,执行到位,记录规范;效果理想
——B级:
基本完成计划,且有实施记录,没有设备问题或轻微问题
——C级:
发生因未按期及时维护保养,或不当造成酿成设备事故耽误生产的情况
100%
≮B
≮B
≮B
≮B
设备部
一季度积累数据
3)设备完好率[%]
及时维护
●设备完好率:
=
设备完好数/检查设备数×100%
●数据来源、提报、统计方式:
动力部每月定期组织所有设备完好性检查,设备管理员记录、统计
造成严重后果的,单独记录、提报,考核
未统计
/
待定
待定
待定
设备部
一季度积累数据
质量部
1)重大、批量质量问题处理的及时性、有效性
质量事故[评级]
●汇总当月所有内部与外部的质量问题处理情况,月末组织评审,并根据评审结论确定给出综合评级:
(相关部门等参与评审)
——A级:
反应迅速,处理及时,措施有效;遏制了事态扩大,避免更大损失和影响的;
——B级:
事态基本得到控制,个别地方未做到位,但未导致严重后果;
——C级:
反应迟钝,处理不及时,措施不当;造成事态扩大
~B
≮B
≮B
≮B
≮B
质量部
逐一评价,可结合打分的方法
2)质量改进项目推进、
完成率[评级]
●汇总当月所有质量改进项目进展情况,月末组织评审,并根据评审结论确定给出综合评级、评分:
(相关部门等参与评审)
——A级:
项目完成计划工作量的大部分(80%)以上,重点项目全部完成;
——B级:
项目完成计划工作量的70%以上,重点项目全部完成;
——C级:
项目完成计划工作量的70%以下,重点项目全部完成
~C
≮B
≮B
≮B
≮B
质量部
逐一评价,可结合打分或计算百分率的方法
3)已整改问题重复发生
项次[次]
●前期已整改的问题,又重复出现。
汇总当月所有已整改又重复发生的问题,月末组织评审,界定责任。
按照项次计算
未统计
≯1
≯1
0
0
质量部
一季度积累数据
4)外协产品合格率[%]
●参照:
采购产品入厂交验批次合格率
~90.0%
≮90
≮90
≮90
≮90
质量部
5)生产过程合格率[%]
●参照:
工序平均下线合格率
~78%
≮94.0
≮94.0
≮94.5
≮94.5
质量部
6)产品出厂合格率[%]
●参照:
产品平均出厂合格率
~96.7%
≮97.0
≮97.0
≮97.5
≮97.5
质量部
8)零部件入厂错、漏检(批次)[次]
●当月(季度)零部件入厂检验错、漏检次数
未统计
/
待定
待定
待定
质量部
一季度积累数据
9)生产过程的错、漏检
(项次率%)
●终检发现的不合格项次/下线总件数×100%
~4%
3.5%
3.5%
3.0%
3.0%
质量部
10)Audit评审计划完成改进情况
~90%
100%
100%
100%
100%
质量部
11)质量项目完成、改进、关闭项次[项次]
●当月(季度)质量问题的完成、改进、关闭项次
~60%
/
待定
待定
待定
质量部
一季度积累数据
12计量器具、检测仪器按期送检率[%]
●按期送检率=规定周期内实际送检计量器具数量/规定周期内应送检计量器具数量×100%
~95%
/
待定
待定
待定
质量部
一季度积累数据
综合部
培训计划完成率
培训的次数/培训计划的次数
人员顶岗计划
有第二岗位的人员/所有的职工人数
人员流动率
人员的进厂人员和离厂人员的总计/当月在职人员
销售公司
3)产品按期交付率[%]
●产品按期交付率=按期交付次数/交付总次数×100%
未统计
/
待定
待定
待定
销售公司
一季度积累数据
4)产品退货率[%]
停供/限供次数[次]
●产品退货率=产品退货次数/交付总次数×100%
●停供/限供按照实际发生的情况记录,月底汇总
未统计
/
待定
待定
待定
销售公司
一季度积累数据
5)顾客满意度[%]
[评级]
●根据调查结果
未统计
/
待定
待定
待定
销售公司
一季度积累数据
销售计划完成率
●计划数/完成数
产品及时交付率
●要求未按时到货的次数/总的交货次数
投诉处理及时率
●要求未按时解决的次数/投诉次数
物管部
1)零部件发错项次[次]
●当月(季度)零部件发错项次
未统计
/
待定
销售公司
一季度积累数据
2)先进先出执行情况
●按采购件入库及生产日期执行先进先出
未统计
/
待定
车间
使用部门
一季度积累数据
车队
1)配送计划未完成项次
(逆指标)[次]
●当月(季度)配送计划未完成数量,信息反馈
未统计
/
待定
待定
待定
销售公司
一季度积累数据
2)产品转运过程中发生的磕碰、损坏项次[次]
●当月(季度)零部件在转运过程中发生的磕碰、损坏总数,根据信息反馈
未统计
/
待定
待定
待定
销售公司
一季度积累数据
底盘事业部
三级质量指标(车间/工序级)
分厂
车间/工序
质量指标名称
指标含义及统计方式/方法
评定/判定标准
2009年
实际值
2010年目标值(季度)
提报
单位
备注
一
二
三
四
车架
轻卡铆接
工序合格率[%]
工序工废损失[元]
●工序合格率=
当班检验合格数量/该工序该班次当班生产数量×100%
●工序工废损失=
该工序在统计周期之内所发生的工费损失之和
●质量部过程检验员当班统计上报,月末汇总
92.50﹪
93.20﹪
92.50﹪
92.70﹪
质量部
工序工废损失为观察项目,一季度积累数据
轻卡油压
93.90﹪
94.50﹪
94.00﹪
94.20﹪
轻卡平板
93.0﹪
93.20﹪
93.10﹪
93.50﹪
轻卡随行钻
98.80﹪
99.00﹪
98.90﹪
99.00﹪
涂装车间
99.10﹪
99.30﹪
99.30﹪
99.30﹪
重卡铆接
90.20﹪
91.00﹪
90.80﹪
91.00﹪
重卡平板
91.20﹪
92.00﹪
92.00﹪
92.50﹪
重卡随行钻
92.00﹪
92.80﹪
92.20﹪
92.80﹪
重卡油压
91.00﹪
91.50﹪
91.50﹪
91.70﹪
剪板车间
96.20﹪
96.40﹪
96.10﹪
96.50﹪
分装焊车间
98.80﹪
99.00﹪
98.90﹪
99.00﹪
冲压车间
97.00﹪
97.20﹪
97.10﹪
97.30﹪
散件车间
94.50﹪
94.80﹪
94.50﹪
94.80﹪
油箱
滚焊/包边
产品渗漏比率[%]
产品渗漏比率=当月(季度)退回产品渗漏数量/当月发出总数
~1.4﹪
1.39﹪
1.38﹪
1.35﹪
1.30﹪
质量部
观察项目
产品报废比率[%]
产品报废比率=当月(季度)退回产品报废数量/当月发出总数
~0.7﹪
0.69﹪
0.67﹪
0.63﹪
0.060﹪
观察项目
传动轴
车轴承孔
工序合格率[%]
工序工废损失[元]
●当班检验合格数量/该工序该班次当班生产数量×100%
●质量部过程检验员当班统计上报,月末汇总
~95﹪
95.50﹪
95.50﹪
96.00﹪
96.00﹪
质量部
工序工废损失为观察项目,一季度积累数据
铣花键
~95﹪
95.50﹪
95.50﹪
96.00﹪
96.00﹪
磨花键外圆
~98﹪
98.50﹪
98.50﹪
99.00﹪
99.00﹪
调质处理
~99﹪
99.50﹪
99.50﹪
99.55﹪
99.55﹪
高频处理
~98﹪
99.00﹪
99.00﹪
99.50﹪
99.50﹪
动平衡
动平衡不合格
●根据当月市场反馈、退回,统计问题项次
数次
0
0
0
0
平衡块焊接
平衡块脱落
数次
0
0
0
0
手刹制动器
总成
产品出厂合格率[%]
(产品出厂总数—市场反馈不合格数量)/产品出厂总数×100%
99.0﹪
99.2﹪
99.2﹪
99.4﹪
99.4﹪
质量部
工序工废损失为观察项目,一季度积累数据
冲压
工序合格率[%]
工序工废损失[元]
●当班检验合格数量/该工序该班次当班生产数量×100%
●质量部过程检验员当班统计上报,月末汇总
99.2﹪
99.4﹪
99.4﹪
99.6﹪
99.6﹪
焊接
99.5﹪
99.6﹪
99.6﹪
99.8﹪
99.8﹪
组装
99.2﹪
99.4﹪
99.4﹪
99.6﹪
99.6﹪
附件1:
质量指标统计台账
指标名称
指标类型
○相对比例○定性评级
○绝对数值○
数据提供
被考核
单位
序号
(统计)月份
比例型