OT与IT融合技术架构演进.docx
《OT与IT融合技术架构演进.docx》由会员分享,可在线阅读,更多相关《OT与IT融合技术架构演进.docx(9页珍藏版)》请在冰豆网上搜索。
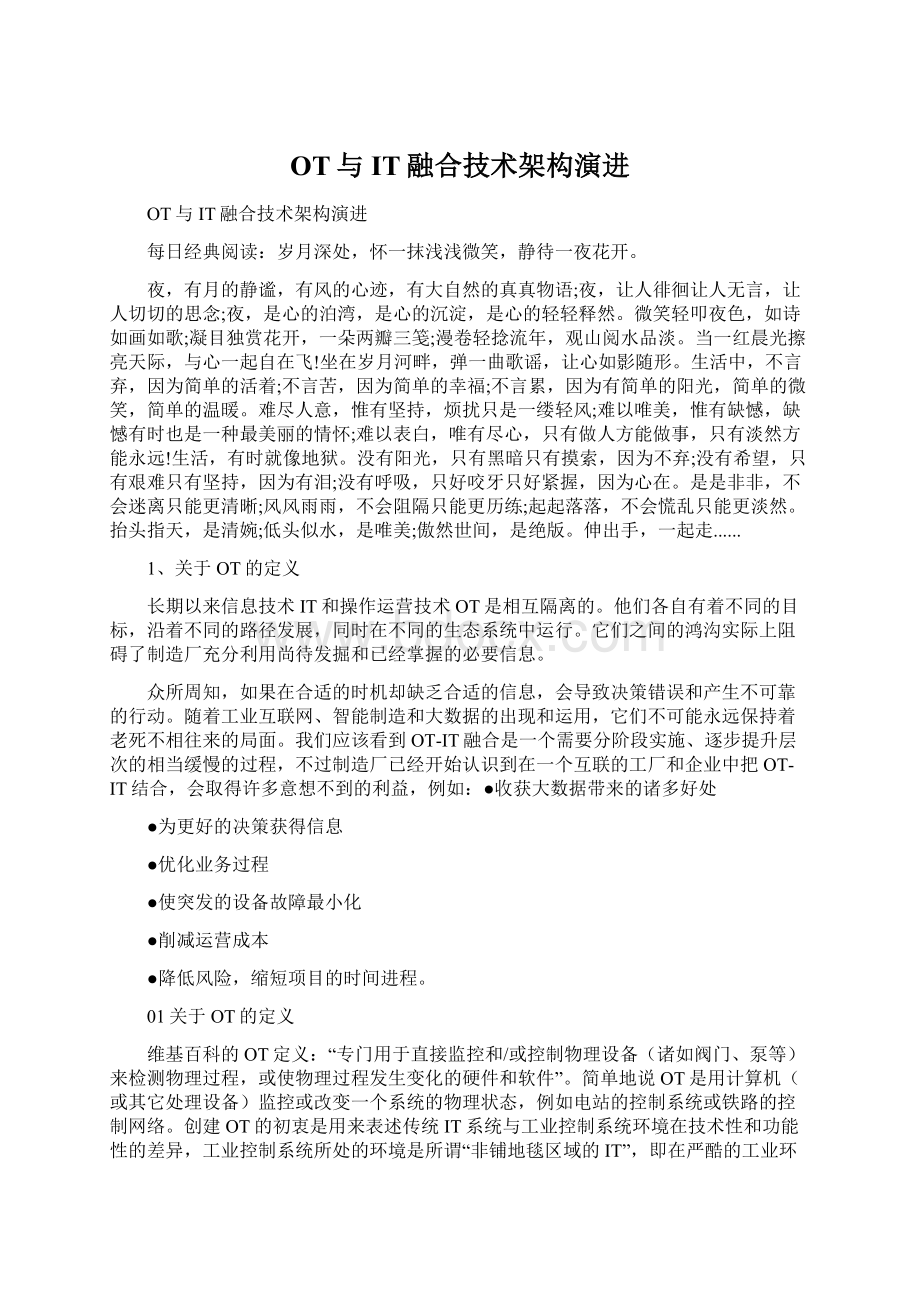
OT与IT融合技术架构演进
OT与IT融合技术架构演进
每日经典阅读:
岁月深处,怀一抹浅浅微笑,静待一夜花开。
夜,有月的静谧,有风的心迹,有大自然的真真物语;夜,让人徘徊让人无言,让人切切的思念;夜,是心的泊湾,是心的沉淀,是心的轻轻释然。
微笑轻叩夜色,如诗如画如歌;凝目独赏花开,一朵两瓣三笺;漫卷轻捻流年,观山阅水品淡。
当一红晨光擦亮天际,与心一起自在飞!
坐在岁月河畔,弹一曲歌谣,让心如影随形。
生活中,不言弃,因为简单的活着;不言苦,因为简单的幸福;不言累,因为有简单的阳光,简单的微笑,简单的温暖。
难尽人意,惟有坚持,烦扰只是一缕轻风;难以唯美,惟有缺憾,缺憾有时也是一种最美丽的情怀;难以表白,唯有尽心,只有做人方能做事,只有淡然方能永远!
生活,有时就像地狱。
没有阳光,只有黑暗只有摸索,因为不弃;没有希望,只有艰难只有坚持,因为有泪;没有呼吸,只好咬牙只好紧握,因为心在。
是是非非,不会迷离只能更清晰;风风雨雨,不会阻隔只能更历练;起起落落,不会慌乱只能更淡然。
抬头指天,是清婉;低头似水,是唯美;傲然世间,是绝版。
伸出手,一起走......
1、关于OT的定义
长期以来信息技术IT和操作运营技术OT是相互隔离的。
他们各自有着不同的目标,沿着不同的路径发展,同时在不同的生态系统中运行。
它们之间的鸿沟实际上阻碍了制造厂充分利用尚待发掘和已经掌握的必要信息。
众所周知,如果在合适的时机却缺乏合适的信息,会导致决策错误和产生不可靠的行动。
随着工业互联网、智能制造和大数据的出现和运用,它们不可能永远保持着老死不相往来的局面。
我们应该看到OT-IT融合是一个需要分阶段实施、逐步提升层次的相当缓慢的过程,不过制造厂已经开始认识到在一个互联的工厂和企业中把OT-IT结合,会取得许多意想不到的利益,例如:
●收获大数据带来的诸多好处
●为更好的决策获得信息
●优化业务过程
●使突发的设备故障最小化
●削减运营成本
●降低风险,缩短项目的时间进程。
01关于OT的定义
维基百科的OT定义:
“专门用于直接监控和/或控制物理设备(诸如阀门、泵等)来检测物理过程,或使物理过程发生变化的硬件和软件”。
简单地说OT是用计算机(或其它处理设备)监控或改变一个系统的物理状态,例如电站的控制系统或铁路的控制网络。
创建OT的初衷是用来表述传统IT系统与工业控制系统环境在技术性和功能性的差异,工业控制系统所处的环境是所谓“非铺地毯区域的IT”,即在严酷的工业环境中直接监控和控制生产的IT设备,例如PLC、SCADA、DCS、CNC系统(包括计算机化的机床)、科学设备(如数字式示波器)。
Gartner关于OT的定义:
“直接监控和/或控制工业设备、资产、流程和事件来检测物理过程或使物理过程产生变化的硬件和软件”。
在网上还可以检索到一些其它的定义,但基本离不开上面两种定义的概念。
归纳OT的概念有着以的几点基本内容:
①OT和在工业企业用的IT系统都是为工业企业服务的,这些工业企业是指流程工业,离散制造业、批量制造业等,将其它类型的企业的运营技术纳入OT的概念只是引申,并非原意。
②OT技术是直接对工业的物理过程、资产和事件进行监控和/或对过程、资产和事件实施改变控制的硬件和软件。
直观来看,OT其实就是工业控制系统(PLC、DCS、SCADA等)及其应用软件的总称,但其应用软件显然隐含了工业工程技术(所谓的ET)的丰富内容。
③不直接对工业物理过程、资产和事件进行监控和产生影响的技术,不属于OT的范围。
按照这个概念ERP显然不是OT的范畴,MES/MOM处于IT和OT之间。
④OT技术的承载体是计算机系统或其它的运用计算技术的处理系统。
不过由于OT直接面对工业生产的物理设备和过程,保证其安全稳定运行,按质按量生产产品是其首要的目标,因此长期以来采用专用的系统、网络和软件。
在这个意义上,与IT相比,其开放性和标准化有待于改善和提升。
简而言之,当下的工厂有IT和OT之分。
处理工厂的数据和信息,并以维护所制造产品的质量为目标的团队,就叫IT。
另外的团队控制和分析整个的生产过程以获得进一步的改善,这就是OT。
历史上这两个团队是相互独立的,但一旦它们相互融合会使整个工厂产生显著的改善。
OT与IT融合必然创建提质增效的结果。
它赋予工厂的管理者监控运行和过程的能力大为增强,甚至可以预测到可能发生的任何意想不到的事件,未雨绸缪。
它会加速生产节拍或速度、使能源和时间的消耗最小化,以及降低监控资产的成本。
下图1是从近年新进且在IIoT领域发展很好的美国InductiveAutomation公司的白皮书《IIoT:
CombiningtheBestofOTandIT》中的截图。
直观地指出OT包括机械装备、物理成套设备以及对它们践行监控和控制的工业硬件和软件。
OT和IT的范围
OT专业人员偏好使用PLC、DCS、RTU、HMI、SCADA,以及嵌入式计算技术。
而IT包括用于企业管理的硬件、软件、网络、通信技术以及存贮、处理和向企业各个部门传输信息的系统。
IT专业人员擅长联网技术,非常熟悉快速扩展网络规模、云基础架构、基于web的部署和诸如SQL、Java及Python等技术。
在解决问题的工作和思维方式上OT和IT也往往不同。
IT采用自顶而下的方法,惯于从总体需求出发,然后划分为若干的子部件,且针对子部件提出和开发解决方案。
这种解决问题的思路,不仅仅能了解问题的所在,而且也很好地给出了解决问题的方法。
OT人员习惯于自下而上的思路,从个别的部件出发构建复杂的系统。
例如SCADA系统要从工厂层面的不同生产过程采集数据,OT人员必须面对如何从不同的专用系统中把数据集成起来。
而且OT人员环绕着以任务为关键的高风险系统工作,他们最关注的一定是安全(物理安全、功能安全和信息安全)。
这也就是为什么互联网和局域网的联接不能在OT范围直接运用的根源。
随着智能装备、大数据和工业互联网的引入,OT和IT人员都面临需要解决存取工业数据同样的问题。
偏偏在企业中OT和IT处在不同的层面,从解决问题的观点来看,它们相互之间并不真正了解对方的需求。
IT人员并不理解为什么OT仍然要使用传统的设备,采用专用的昂贵的解决方案去处理问题。
OT人员或许对SQL数据库或者对现今在IT中运用的信息安全协议的宽度并不深度了解。
即使存在这些差异,而现在正好存在这样的机会让OT和IT相互融合,通过提升各自的能力,从而形成一种真正具有颠覆性的技术。
在工业3.0的时代,OT和IT保持着彼此相互的分割。
而为了满足今天的数据密集型的环境和进入工业4.0,企业必须将OT和IT交汇融合匹配。
2、充分运营IIoT
促使OT-IT融合
怎样把老一辈在工厂生产管理的经验和积累的知识,通过数字化转型成为“数字原生”的知识财富,并被年青一代继承和发展,这一挑战也可理解为OT与IT交汇融合,使得OT和IT各自的“神经突触”紧紧相连,从而为创造更多价值提供保证。
图5是日本横河利用工业互联网IIoT实现流程工业的OT和IT融合的解决方案。
原来在本企业内各个工厂积累了丰富的控制、管理和优化的经验,形成了一套以生产任务优先的解决方案。
不过这些解决方案充其量体现了操作运营管理和控制的局部优化的系统思维。
如果在一个企业中有许多的工厂,它们各自的局部优化运营也需要服从于该企业的全局优化运营。
从社会大生产的全局而言,一个企业只不过是这一大生产链条中的一环,与其生产的上游和下游存在着诸多的关联因素。
因此一个企业的IIoT不仅仅要服务于该企业各个工厂间的生产协调和优化,还必然要为企业与企业间的优化协调服务。
在横河的方案中,边缘设备的解决方案作为IIoT的一部分,执行过程优化和分析功能;并通过与云基的解决方案的通信,实现企业间供应链的协调和优化,同时还通过远程解决方案实现各种工程化、运营和维护的需求。
横河的IIoT的解决方案包括:
●实施提高效率,使产出最大化;●进行过程数据分析,使生产性能最优化;●实现云端库存管理,提高库存的可视化和协调能力,以优化供应链;●运用实时的过程数据共享服务,远程监控过程数据,从而达到设备运转时间最大化的目的;●提供运营管理目标服务,实现云基的性能跟踪和管理;●通过区域能源管理协调,利用云计算使区域能源成本最低;●集中的过程数据管理系统采集和利用海量的过程数据以改善运营效率和安全;●工厂或过程仿真,使用CPS对相关工厂或过程进行近期行为的预测;●对重要设备进行振动检测,以改善状态检测的效率,达到降低成本的要求;●运营人工智能分析阀门的“purePV”,预测空蚀现象;●利用IIoT采集的数据和分析,①确保过程的安全运行和信息安全,防止突发事件的发生和来自外界的信息攻击;②杜绝非计划停车的可能性,以改善可用性和可靠性;③为消除人为的出错,而导致的人因可靠性失控。
3、ET必须纳入
由于在制造业中集成产品和流程设计的重要性大为增加,促使企业的数字化转型要求工程技术ET(engineeringtechnology)纳入IT-OT的融合进程中。
在ARC给出的概念中,ET包括了数字模型的建模技术,形成了流程工艺工程师必须与IT软件开发人员一起工作,工业安全专家必须与IT信息安全专家协同,自动化专家必须与IT数据科学家协同的局面。
在制造业中由于智能设备的复杂度增加,相应的软件推动IT和OT紧密的集成,于是创造了在原有的知识上获得新的洞察和观察视角的机会。
只是在IIoT的数字化数据环境中,将ET工程技术中那些为建立虚拟模型的技术纳入OT-IT融合的进程和交换中,这才能真正发挥作用。
或许过去ET已经被隐含在OT-IT的融合中,但是它的作用被低估了。
在现在和将来的工作环境必须改变这种观念,原因在于建模工具已成为管理决策或技术决策中的基础和必备的环节。
如图4所示,由于ET需要利用IT来改善OT,所以ET处于IT和OT的中间。
随着获取实际状态和对实际状态进行可视化的技术不断在改进,ET为用户提供更好了解资产在实际运用中的能力。
在这三个领域之间的关系应该超越“和平共存”,而通过合并融合,最终产生大于其各自部分总和的结果。
在虚拟环境下对新产品、新系统,甚至新的生产工厂进行设计和测试,将会创造一种令人耳目一新的效果,特别是从成本的视角来看可以获得前所未有的增益。
虚拟模型可以在资产整个生命周期中将IT/ET/OT联系起来,仅从资产管理的角度来评价,可以取得在一个问题发生之前就能预测,并能够以优化的速度和成本对可能发生的问题进行维护。
举例来说,制药行业由于具有对制造过程进行合规验证的要求,一旦不合规就会影响其声誉。
当验证的要求发生变化,接下去就要改变控制规程,如果能在专业的规程实践的指导下运用制造IT自动地保证所需要结果的一致性,问题就容易解决。
还有一个依靠资产信息进行能源管理的案例。
加拿大最大的集成能源公司SuncorEnergy,其运营卓越管理系统(OEMS)和数字化转型平台的基础就是资产信息。
从2004
年开始OEMS的目标就是有效和高效率地改善工厂的可靠性、风险管理和环境的可持续发展。
为了获得良好的效果,资产信息必须是完整的、可存取的、适时的和可信赖的。
良好的资产信息提供了按许可证运行来改善风险管理、减少非计划停车和非计划降低运行速度、提高生产率、削减供应链成本,以及削减资产投运的调试时间。
Suncor公司从企业的视角设计资产信息系统,首先设置四大支柱:
标准和过程、内容、人与企业文化、技术工艺,先对所采集的五花八门的信息按一定的数据格式加以标准化,接着按照工业标准建立工具,并按业务情况和实例加以提升。
建立一种可管理的结构确保呈现和显示来自所有业务单位的数据。
除非标准和业务情况和实例已经被批准,是不允许客制化的。
过程按不同的人员即工程师、操作人员、维护人员予以实现。
4、怎样可以实现OT-IT融合
IT和OT的融合可不是一件轻而易举的任务。
即使是在提出IT/OT融合概念的美国,现在还在艰难地探索,至少在当下还不存在非常成熟的模式。
这里暂不涉及技术细节,更
多从