通用工艺规则草稿版本41.docx
《通用工艺规则草稿版本41.docx》由会员分享,可在线阅读,更多相关《通用工艺规则草稿版本41.docx(15页珍藏版)》请在冰豆网上搜索。
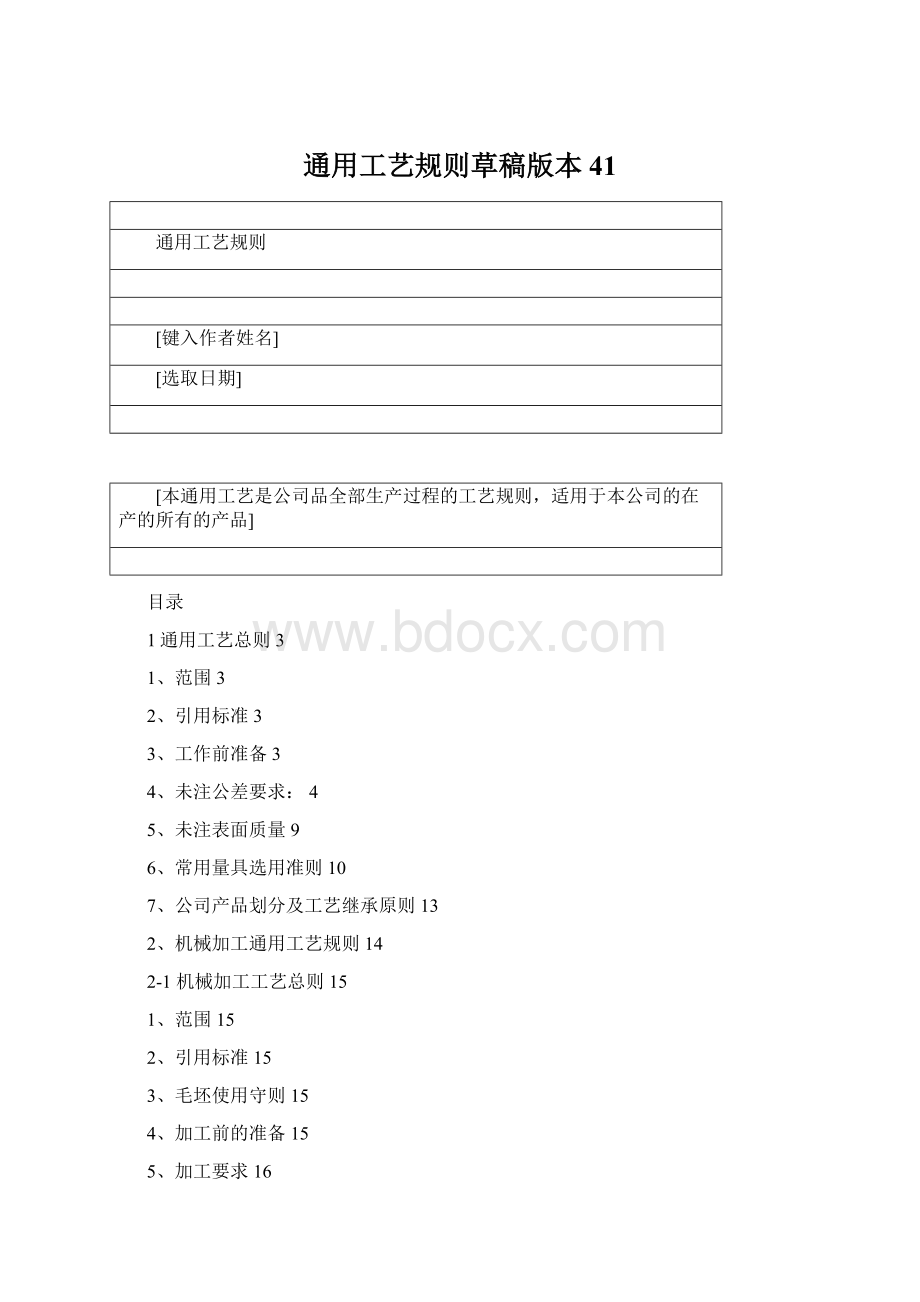
通用工艺规则草稿版本41
通用工艺规则
[键入作者姓名]
[选取日期]
[本通用工艺是公司品全部生产过程的工艺规则,适用于本公司的在产的所有的产品]
目录
1通用工艺总则3
1、范围3
2、引用标准3
3、工作前准备3
4、未注公差要求:
4
5、未注表面质量9
6、常用量具选用准则10
7、公司产品划分及工艺继承原则13
2、机械加工通用工艺规则14
2-1机械加工工艺总则15
1、范围15
2、引用标准15
3、毛坯使用守则15
4、加工前的准备15
5、加工要求16
6、刀具与装夹17
7、加工后处理18
8、工艺路线拟定守则19
9、其它要求19
2-2车削通用加工工艺20
2-3铣削通用加工工艺20
2-4钻削通用加工工艺20
2-5插、刨削通用加工工艺20
3、装配通用工艺规则20
4、热处理通用工艺规则20
5、焊接通用工艺规则20
6、产品后处理通用工艺规则20
1通用工艺总则
1、范围
1.1本通用工艺是公司产品全部生产过程的工艺守则,适用于本公司的在产的所有的产品。
1.2本守则是公司产品制造生产的通用性工艺文件,须与产品设计工艺文件相配合使用,如产品工艺文件有特殊要求时,以产品的工艺文件为准。
2、引用标准
本守则所包含的部分条文引用国家标准和行业标准。
本守则生效时,国家标准的版本均为有效。
所有的标准都可能被修订,当相应的国家标准进行修订时,技术部及各个使用部门应探讨修改本守则的必要性。
JB/T9168.1-1998
3、工作前准备
3.1检查图纸图样、工艺文件、工艺规程等有关技术文件是否齐全。
3.2按照工艺规程准备全部的工艺装备。
对于新装备要先熟悉使用要求和操作方法。
3.3工艺装备要放在指定位置,不得乱放,不得随意拆卸。
3.4检查工艺装备的状态,如采用机床等设备时严格按照使用说明进行维护。
3.5核对量具,保证所有的量具都在正常的精度中。
4、未注公差要求:
根据公司现有加工技术水平和参考国家标准和行业标准,对未注公差按照以下标准执行。
.尺寸未注公差:
尺寸范围(mm)
孔径和内尺寸(μm)
轴径和外尺寸(μm)
长度(μm)
小于等于3
+100/0
0/-100
+50/-50
3至6
+120/0
0/-120
+60/-60
6至10
+150/0
0/-150
+75/-75
10至18
+180/0
0/-180
+90/-90
18至30
+210/0
0/-210
+105/-105
30至50
+250/0
0/-250
+125/-125
50至80
+300/0
0/-300
+150/-150
80至120
+350/0
0/-350
+175/-175
120至180
+400/0
0/-400
+200/-200
180至250
+460/0
0/-460
+230/-230
250至315
+520/0
0/-520
+260/-260
315至400
+570/0
0/-570
+285/-285
400至500
+630/0
0/-630
+315/-315
500至630
+700/0
0/-700
+350/-350
630至800
+800/0
0/-800
+400/-400
800至1000
+900/0
0/-900
+450/-450
1000至1250
+1050/0
0/-1050
+525/-525
1250至1600
+1250/0
0/-1250
+625/-625
1600至2000
+1500/0
0/-1500
+750/-750
2000至2500
+1750/0
0/-1750
+875/-875
2500至3150
+2100/0
0/-2100
+1050/-1050
.未注倒角尺寸:
(mm)
尺寸
倒角X45°
小于等于5
0.2
5至30
0.5
30至100
1
100至250
2
250至500
3
500至1000
4
大于1000
5
.未注倒圆尺寸:
(mm)
台阶差尺寸(有台阶)
尺寸(无台阶)
倒圆半径
小于等于4
3至10
0.4
4至12
10至30
1
12至30
30至80
2
30至80
80至260
4
80至140
260至630
8
140至200
630至1000
12
大于200
大于1000
20
.倒角和倒圆半径的公差:
(mm)
倒角和倒圆半径
公差
0.5至3
+0.2/-0.2
3至6
+0.5/-0.5
6至30
+1/-1
30至50
+2/-2
.未注角度公差:
短边长度值(mm)
公差
小于等于10
+1°/-1°
10至50
+30'/-30'
50至120
+20'/-20'
120至400
+10'/-10'
大于400
+5'/-5'
.未注形状和位置公差:
直线度、平行度和平面度(mm)
长度范围
公差
小于等于10
0.05
10至30
0.1
30至100
0.2
100至300
0.4
300至1000
0.6
1000至3000
0.8
圆跳动、同轴度(mm)
长度范围
公差
小于等于10
0.2
10至30
0.2
30至100
0.2
100至300
0.2
300至1000
0.2
1000至3000
0.2
垂直度(mm)
长度范围
公差
小于等于100
0.4
100至300
0.6
300至1000
0.8
1000至3000
1
对称度(mm)(键槽除外)
长度范围
公差
小于等于100
0.6
100至300
0.6
300至1000
0.8
1000至3000
1
键槽对称度(mm)
长度范围
公差
小于等于1
0.015
1至3
0.02
3至6
0.025
6至10
0.03
10至18
0.04
18至30
0.05
30至50
0.06
.螺钉孔和螺栓孔中心距:
(mm)
规格
螺钉孔中心距公差
螺栓孔中心距公差
M2至M6
+0.12/-0.12
+0.25/-0.25
M8至M10
+0.25/-0.25
+0.50/-0.50
M12至M18
+0.30/-0.30
+0.75/-0.75
M20至M24
+0.50/-0.50
+1/-1
M27至M30
+0.60/-0.60
+1.25/-1.25
M36至M42
+0.75/-0.75
+1.5/-1.5
M48
+1/-1
+2/-2
M56至M72
+1.25/-1.25
+2.5/-2.5
大于M80
+1.5/-1.5
+3/-3
5、未注表面质量
5.1产品表面质量衡量采用表面粗糙度评定,如图纸和技术文件无特殊说明,一律默认选择
作为评定参数。
表面粗糙度的标注方法参考国标。
5.2粗糙度公司执行标准:
非机械加工表面(锻造、铸造、气割)
:
50-70µm
粗加工表面
:
25µm
精加工表面
:
12.5µm
5.3技术文件中无特殊说明粗糙度可按照下表标准目视判定,判定采用互判及必须经过技术人员确认方可认定有效。
如有特殊要求及判定产生异议时必须采用仪器测量。
表面粗糙度
/µm
特征
目视标准
50-100
粗糙
明显可见刀痕
25
粗糙
可见刀痕
12.5
粗糙
微见刀痕
6.3
半光
可见加工痕迹
3.2
半光
微见加工痕迹
1.6
半光
看不清加工痕迹
0.800
光
可辨认加工痕迹方向
0.400
光
微辨认加工痕迹方向
0.200
光
不可辨认加工痕迹方向
0.100
最光
暗光泽面
0.050
最光
亮光泽面
0.025
最光
雾状镜面
0.008
最光
镜面
目视判定标准
6、常用量具选用准则
6.1为保证零件几何公差的要求,尺寸测量要按照下表确定足够的安全裕度,所选量具的不确定度必须小于安全裕度的90%。
安全裕度及计量器具不确定度的允许值单位mm
工件公差
安全裕度
计量器具不确定度最大允许值
大于
至
0.009
0.018
0.001
0.0009
0.018
0.032
0.002
0.0018
0.032
0.058
0.003
0.0027
0.058
0.100
0.006
0.0054
0.100
0.180
0.010
0.009
0.180
0.320
0.018
0.016
0.320
0.580
0.032
0.029
0.580
1.000
0.060
0.054
1.000
1.800
0.100
0.090
千分尺和游标卡尺的不确定度单位mm
尺寸范围
计量器具
分度值0.01外径千分尺
分度值0.01外径千分尺
分度值0.02游标卡尺
分度值0.05游标卡尺
大于
至
不确定度
0
50
0.004
0.008
0.020
0.050
50
100
0.005
100
150
0.006
150
200
0.007
0.013
200
250
0.008
0.100
250
300
0.009
300
350
0.010
0.020
/
350
400
0.011
/
400
450
0.012
/
450
500
0.013
0.025
/
500
600
/
0.030
/
600
700
/
/
700
1000
/
/
0.150
指示表的不确定度单位mm
尺寸范围
计量器具
分度值为0.001的千分表(0级在全程范围内,1级在0.2范围内),分度值为0.002千分表(在一转的范围内)
分度值为0.001、002、0.005的千分表(1级在全程范围内),分度值为0.01的百分表(0级在任意1mm内)
分度值为0.01mm的百分表(0级在全程范围内,1级在任意1mm内)
分度值为0.01的百分表(1级在全程范围内)
大于
至
不确定度
25
0.005
0.010
0.018
0.030
25
40
40
65
65
90
90
115
115
165
0.006
165
215
215
265
265
315
6.2测量仪器显示尺寸必须位于工件极限尺寸缩小安全裕度后的尺寸范围内。
如测量尺寸
,安全裕度为0.006,按照不确定度选择分度值为0.01mm的外径千分尺,千分尺测量上限为34.944mm,测量下限为34.984mm。
6.3使用量具前必须看清该量具是否在有效期内;在使用过程中量具若造成磕碰,必须交计量室重新修理、检定;在使用结束后,必须将量具擦拭干净,放入量具盒。
6.4不准将量具放在床头箱及机床导轨上;不准将量具当作工具使用;不准在量具盒内放其他杂物;不准将几把量具混放在一起;不准使用无合格证的量具。
6.5常用量具使用注意事项:
6.5.1外径千分尺
使用前必须检查零位,如果不在零位,应送计量室调零。
由于灰尘、碎屑、油会引起几个微米的误差,因此被测物必须用汽油或柔软 的布、纸来擦拭干净,然后进行测量。
测量时,被测物必须轻轻地与测量头接触,若碰劲过大,应退回一点重来。
6.5.2百分表和千分表
使用前应将百分表测量面、测杆擦净。
使用百分表前,应将测头压缩使指针至少转过1/6圈。
应当先考察指示值的稳定性后再使用,在零位上,将测杆以快速地或缓慢地往下移,这时看一下指示值的变化情况,当指示值变化0.3刻度以上时,就要考虑下列问题:
a.支架的固紧是否松动;b.百分表装卡的夹紧部分是否松了;c.若无前两种情况,那么百分表本身有问题,请交计量检定人员处理。
6.5.3杠杆百分表和杠杆千分表
保持清洁、量面及转轴处请勿擦油。
当表安装于测量工位上之后,应拨动测量头,察看表针示值稳定情况,旋转表盘对准所需“零位”,即可进行测量。
在使用时,注意使测量头的轴线垂直于被测量尺寸线,假若由于某些原因、测量头轴线不可能达到要求时,则需将所读的数乘以cosα(α—测量头轴线与被测面之夹角)加以修正
7、公司产品划分及工艺继承原则
2、机械加工通用工艺规则
2-1机械加工工艺总则
1、范围
1.1本守则规定公司各种切削加工应共同遵守的基本规则,适合公司内各种切削加工。
1.2本守则是公司产品制造生产的通用性工艺文件,须与产品设计工艺文件相配合使用,如产品工艺文件有特殊要求时,以产品的工艺文件为准。
2、引用标准
本守则所包含的部分条文引用国家标准和行业标准。
本守则生效时,国家标准的版本均为有效。
所有的标准都可能被修订,当相应的国家标准进行修订时,技术部及各个使用部门应探讨修改本守则的必要性。
JB/T9168.1-1998
3、毛坯使用守则
4、加工前的准备
4.1操作者接到加工任务后,首先要检查加工所需的产品图样、工艺规程和有关技术资料是否齐全。
4.2要看懂、看清工艺规程,产品图样及其技术要求,有疑问之处应找有关技术人员问清后再进行加工。
4.3按产品图样或(和)工艺规程复核工件毛坯或半成品是否符合要求,发现问题应及时向有关人员反映,待问题解决后才能进行加工。
4.4按工艺规程要求准备好加工所需的全部工艺装备,发现问题及时处理。
对新夹具、模具等,要先熟悉其使用要求和操作方法。
4.5加工所使用的工艺装备应放在规定的位置,不得乱放,更不能放在机床导轨上。
4.6工艺装备不得随意拆卸和更改。
4.7检查加工所用的机床设备,准备好所需的各种附件,加工前机床要按规定进行润滑和空运转。
5、加工要求
5.1为了保证加工质量和提高生产率,应根据工件材料、精度要求和机床、刀具、夹具等情况,合理选择切削用量。
加工铸件时,为了避免表面夹砂、硬化层等损坏刀具,在许可的条件下,切削深度应大于夹砂或硬化层深度。
5.2对有公差要求的尺寸,在加工时应尽量按其中间公差加工。
5.3工艺规程中未规定表面粗糙度要求的粗加工工序,加工后的表面粗糙度Ra值应不大于25μm。
5.4铰孔前的表面粗糙度Ra值应不大于12.5μm。
5.5精磨前的表面粗糙度Ra值应不大于6.3μm。
5.6粗加工时的倒角、倒圆、槽深等都应按精加工余量加大或加深,以保证精加工后达到设计要求。
5.7图样和工艺规程中未规定的倒角、倒圆尺寸和公差要求应按照本守则总则中未注尺寸的要求规定。
5.8凡下工序需进行表面淬火、超声波探伤或滚压加工的工件表面,在本工序加工的表面粗糙度Ra值不得大于6.3μm。
5.9在本工序后无去毛刺工序时,本工序加工产生的毛刺应在本工序去除。
5.10在大件的加工过程中应经常检查工件是否松动,以防因松动而影响加工质量或发生意外事故。
5.11当粗、精加工在同一台机床上进行时,粗加工后一般应松开工件,待其冷却后重新装夹。
5.12在切削过程中,若机床—刀具—工件系统发出不正常的声音或加工表面粗糙度突然变坏,应立即退刀停车检查。
5.13在批量生产中必须进行首件检查,合格后方能继续加工。
5.14在加工过程中,操作者必须对工件进行自检。
5.15检查时应正确使用测量器具。
使用量规、千分尺等必须轻轻用力推入或旋入,不得用力过猛;使用卡尺、千分尺、百分表、千分表等时事先应调好零位。
6、刀具与装夹
61刀具的装夹
6.1.1在装夹各种刀具前,一定要把刀柄、刀杆、导套等擦拭干净。
6.1.2刀具装夹后,应用对刀装置或试切等检查其正确性。
6.2工件的装夹
6.2.1在机床工作台上安装夹具时,首先要擦净其定位基面,并要找正其与刀具的相对位置。
6.2.2工件装夹前应将其定位面、夹紧面、垫铁和夹具的定位、夹紧面擦拭干净,并不得有毛刺。
6.2.3按工艺规程中规定的定位基准装夹,若工艺规程中未规定装夹方式,操作者可自行选择定位基准和装夹方法。
选择定位基准应按以下原则:
a)尽可能使定位基准与设计基准重合;
b)尽可能使各加工面采用同一定位基准;
c)粗加工定位基准应尽量选择不加工或加工余量比较小的平整表面,而且只能使用一次;
d)精加工工序定位基准应是已加工表面;
e)选择的定位基准必须使工件定位夹紧方便,加工时稳定可靠。
4.2.4对无专用夹具的工件,装夹时应按以下原则进行找正:
a)对划线工件应按划线进行找正;
b)对不划线工件,在本工序后尚需继续加工的表面,找正精度应保证下工序有足够的加工余量;
c)对在本工序加工到成品尺寸的表面,其找正精度应小于尺寸公差和位置公差的三分之一;
d)对在本工序加工到成品尺寸的未注尺寸公差和位置公差的表面,其找正精度应保证本守则总则中对未注尺寸公差和位置公差的要求。
6.2.5装夹组合件时应注意检查结合面的定位情况。
6.2.6夹紧工件时,夹紧力的作用点应通过支承点或支承面。
对刚性较差的(或加工时有悬空部分的)工件,应在适当的位置增加辅助支承,以增强其刚性。
6.2.7夹持精加工面和软材质工件时,应垫以软垫,如紫铜皮等。
6.2.8用压板压紧工件时,压板支承点应略高于被压工件表面,并且压紧螺栓应尽量靠近工件,以保证压紧力。
7、加工后处理
7.1工件在各工序加工后应做到无屑、无水、无脏物,并在规定的工位器具上摆放整齐,以免磕、碰、划伤等。
7.2暂不进行下道工序加工的或精加工后的表面应进行防锈处理。
7.3用磁力夹具吸住进行加工的工件,加工后应进行退磁。
7.4凡相关零件成组配加工的,加工后需做标记。
7.5各工序加工完的工件,经检查合格后方能转往下道工序。
8、工艺路线拟定守则
9、其它要求
9.1工艺装备用完后要擦拭干净(涂好防锈油),放到规定的位置或交还工具库。
9.2产品图样、工艺规程和所使用的其它技术文件,要注意保持整洁,严禁涂改。
2-2车削通用加工工艺
2-3铣削通用加工工艺
2-4钻削通用加工工艺
2-5插、刨削通用加工工艺
3、装配通用工艺规则
4、热处理通用工艺规则
5、焊接通用工艺规则
6、产品后处理通用工艺规则