重焦沥青装置操作规程格式规范.docx
《重焦沥青装置操作规程格式规范.docx》由会员分享,可在线阅读,更多相关《重焦沥青装置操作规程格式规范.docx(52页珍藏版)》请在冰豆网上搜索。
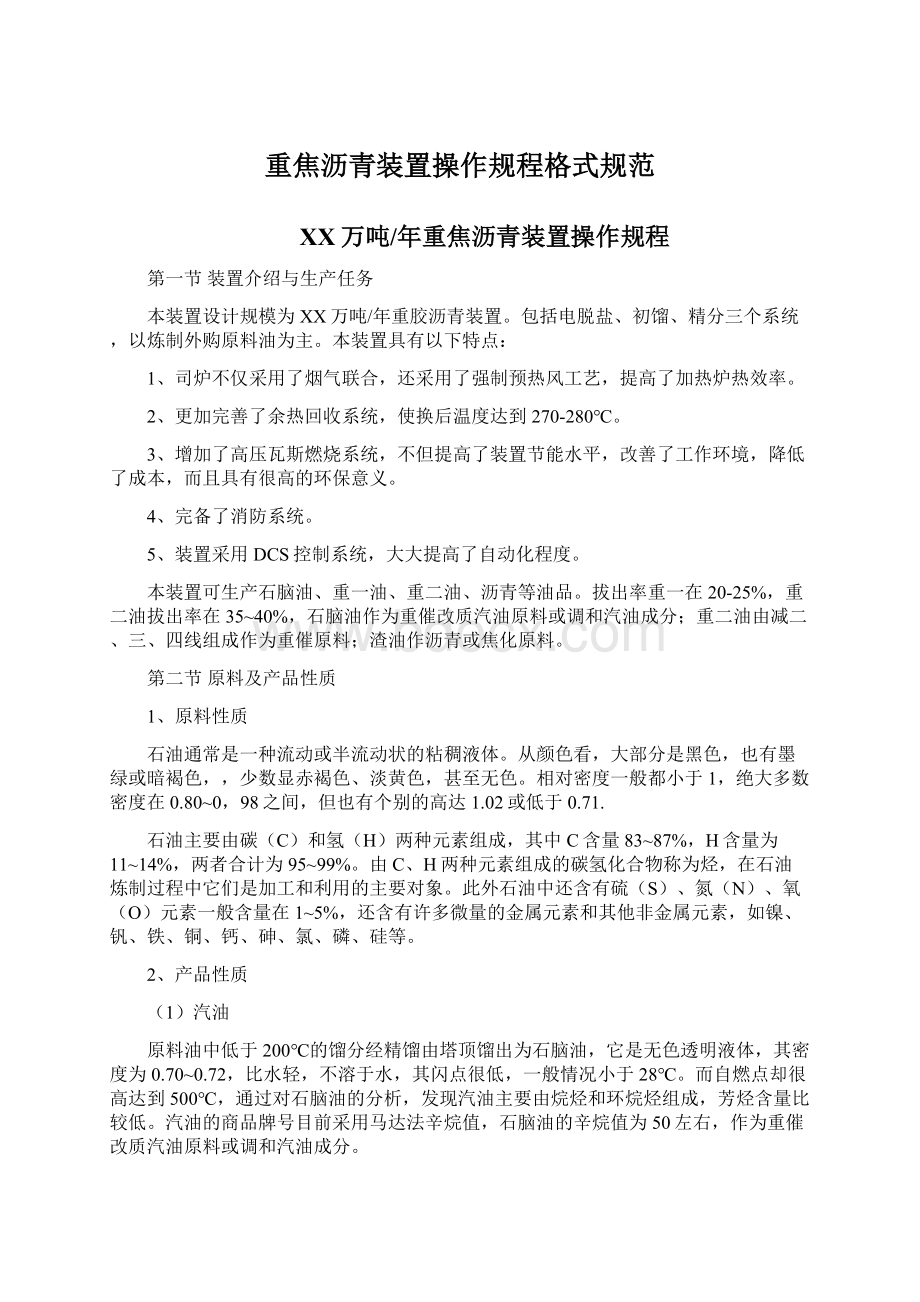
重焦沥青装置操作规程格式规范
XX万吨/年重焦沥青装置操作规程
第一节装置介绍与生产任务
本装置设计规模为XX万吨/年重胶沥青装置。
包括电脱盐、初馏、精分三个系统,以炼制外购原料油为主。
本装置具有以下特点:
1、司炉不仅采用了烟气联合,还采用了强制预热风工艺,提高了加热炉热效率。
2、更加完善了余热回收系统,使换后温度达到270-280℃。
3、增加了高压瓦斯燃烧系统,不但提高了装置节能水平,改善了工作环境,降低了成本,而且具有很高的环保意义。
4、完备了消防系统。
5、装置采用DCS控制系统,大大提高了自动化程度。
本装置可生产石脑油、重一油、重二油、沥青等油品。
拔出率重一在20-25%,重二油拔出率在35~40%,石脑油作为重催改质汽油原料或调和汽油成分;重二油由减二、三、四线组成作为重催原料;渣油作沥青或焦化原料。
第二节原料及产品性质
1、原料性质
石油通常是一种流动或半流动状的粘稠液体。
从颜色看,大部分是黑色,也有墨绿或暗褐色,,少数显赤褐色、淡黄色,甚至无色。
相对密度一般都小于1,绝大多数密度在0.80~0,98之间,但也有个别的高达1.02或低于0.71.
石油主要由碳(C)和氢(H)两种元素组成,其中C含量83~87%,H含量为11~14%,两者合计为95~99%。
由C、H两种元素组成的碳氢化合物称为烃,在石油炼制过程中它们是加工和利用的主要对象。
此外石油中还含有硫(S)、氮(N)、氧(O)元素一般含量在1~5%,还含有许多微量的金属元素和其他非金属元素,如镍、钒、铁、铜、钙、砷、氯、磷、硅等。
2、产品性质
(1)汽油
原料油中低于200℃的馏分经精馏由塔顶馏出为石脑油,它是无色透明液体,其密度为0.70~0.72,比水轻,不溶于水,其闪点很低,一般情况小于28℃。
而自燃点却很高达到500℃,通过对石脑油的分析,发现汽油主要由烷烃和环烷烃组成,芳烃含量比较低。
汽油的商品牌号目前采用马达法辛烷值,石脑油的辛烷值为50左右,作为重催改质汽油原料或调和汽油成分。
(2)重一油
原料油中高于200℃而低于350℃的馏分为重一油,由塔常一、二线馏出。
重一油是棕褐色液体,其相对密度为0.84左右。
我国规定重一油燃料的闪点不低于55℃,安全性虽好,但限制了重一油馏程宽度和重一油来源,重一油馏分中烷烃很高,而环烷烃和芳烃含量较少。
目前我国用十六烷值表示重一油抗爆性。
重一油作为高速重一油机的燃料质量要求较高,按照凝点分为10、5、-10、-20、-35、-50七个牌号,本装置一般生产-10、0、5、10号重一油。
(3)重二油
原料油中高于350℃的馏分在下经塔精馏而分离出来,这一部分即为重二油馏分。
也称为高沸点馏分。
重二油呈淡黄色,其相对密度为0.92左右,作为重催原料也有一定的质量要求:
密度≯0.94,残炭≯2%,硫含量≯1,碱性氮500左右,重金属含量低。
(4)沥青
原料油经、塔精馏以后剩余的组分就是沥青,它是黑色的固体,随温度升高逐渐软化而成液体,原料油性质直接影响沥青的质量性能。
第三节生产原理
经过加温,脱水处理含水<1%、温度60~70℃的原料油经原料油泵自罐区引入装置,经换热达到130℃左右,进入电脱盐罐,在罐内注入软化水、破乳剂,借助于破乳剂和高压电场的共同作用将原料油脱盐、水。
经过脱盐、水的原料油经一系列换热,温度达到270℃进入初馏塔进行蒸馏,原料油在初馏塔中精馏,从塔顶馏出汽油馏分,从塔侧馏出重一油,塔底为重油。
为了取得催化裂化原料,需把沸点高于350℃的馏分从重油中分离出来。
如果继续再进行分离,则必须将重油加热到400℃以上,从而导致重油特别是其中的胶质、沥青质等不稳定组分发生严重的分解、缩合等化学反应,这不但影响产品质量,而且会加大设备结焦而缩短生产周期。
为此,将重油送至加热炉加热至360℃左右,然后进入塔,在减压条件下进行蒸馏。
减顶真空度不低于0.096MPa,采用蒸汽抽真空。
从塔顶馏出的主要是裂化油气,又称减顶瓦斯气。
馏分油从各侧线馏出。
塔底产品是沸点很高的沥青,原料油中的绝大部分胶质、沥青质都集中于此。
第四节开工方案
一、开工前的准备工作
(一)、要求
(1)参加开工的人员一定要树立“安全第一”的思想,以科学的态度对待工作,严格按开工方案和有关操作规程进行操作,坚决反对蛮干和急于求成。
(2)开工前操作人员要熟悉各流程、参数、DCS的使用,并做到熟练掌握,并且认真学习和讨论岗位责任制、巡回检查制、安全生产制度、设备维护保养制度、交接班制等规章制度,明确本职工作,认真落实到工作中。
(3)开工前有专人负责装置内的盲板、孔板、安全阀、支撑弹簧销子的装拆,登记工作。
(4)单机试运要在有关科室的领导下,有电工、钳工、操作工参加按有关规程做好试运。
(5)所有参加开工人员,由车间统一组织认真学习一次各消防器材的使用。
(6)各岗位人员必须保持高度警惕,发生事故要沉着、冷静处理。
(二)、全面大检查
联系项目人员、设计院、施工单位、车间人员及各操作工组成联合检查组按工艺流程对设备、管线、机泵、仪表、保温、焊接等进行全面检查验收为顺利开工做好准备。
(1)按工艺流程检查逐台设备、逐条管线、管件、阀门、法兰、放空、人孔、螺栓、是否松动或缺损,压力表、温度表是否齐全,保温是否达到交工要求。
(2)机泵设备要详细检查冷却水、润滑系统等,保证随时可以启动,可以正常运转。
(3)对各仪表进行效验,调校至准确达到开工要求。
(4)对塔内各部件的安装、焊接连接处进行详细检查,并由专人负责,检查完成封人孔。
(5)检查各消防设施是否到位,安全通道是否畅通,消除周围易燃物。
(6)保证水、电、汽、风的供应。
(7)检查各伴热线的畅通情况,并对各伴热线的给汽点及放空点做好详细记录。
(8)检查各回流的工作情况。
(9)对原料油罐进行检尺,并做好原料油的化验分析。
(10)联系各有关车间人员做好开工的配合工作。
(三)、吹扫试压
1、试压前关闭安全阀手阀,关闭所有阀门逐条试压。
2、所有工艺管线、冷却设备、容器用蒸汽试压至最大设计压力并逐一检查。
3、常压试压方案:
引蒸汽至各个注汽点放尽存水见汽;
(1)试压范围:
初馏塔、汽提塔、初顶冷却器、机泵、回流罐、入塔管线、空冷机。
(2)标准:
0.2~0.25MPa。
(3)所具备的条件:
各管线已吹扫贯通,装好试压压力表。
(4)试压步骤:
①关闭下列阀门:
初底泵的出口阀门、安全阀、注氨阀、注水阀。
除注汽以外的所有蒸汽阀门、初顶水冷器出、入口阀门。
②打开以下阀门:
所有侧线泵的入口阀,塔底泵、初顶汽油泵的入口阀、所有塔壁的侧线及回流阀、冷却器的放空阀。
③给汽点:
汽提塔,初底泵及各侧线泵的入口、回流泵的出口,塔顶放空见汽后,关闭塔顶放空阀,回流罐脱水见汽后关闭放空阀。
④打开初底泵放空阀、容器放空阀见汽畅通后关闭。
⑤试压:
缓慢开启严防管线及容器内水击,压力升至0.25MPa时,关闭各注汽阀,用回流罐放空控制压力,严禁超压。
⑥检查:
组织人员对所有试压的内容进行详细检查,对漏点进行登记和标记,处理完成后再试压直至合格后泄压。
4、减压试压方案
(1)试压范围:
塔、炉、转油线、减顶冷却器、抽真空系统、水封罐、与塔相连的各泵的入口管线、各回流换热器及入塔管线。
(2)标准:
0.2~0.25MPa。
(3)试压步骤:
①关闭下列阀门:
所有系统的出口阀门、冷却器水阀、瓦斯放空阀、所有非给汽点阀门、所有除塔顶放空、水封罐顶放空以外的所有放空线阀门。
②打开下列阀门:
减一、二、三、四线泵的入口阀、侧线回流阀、塔顶放空阀、给汽阀及大气腿放空阀。
③给汽点:
塔底注汽点、泵出入口,塔顶放空见汽后关闭,打开塔底及所有机泵容器放空放凝结水见汽后关闭,以此关闭除塔底放空以外的所有放空阀。
④关闭各给汽点用塔底注气和塔底放空控制压力0.25MPa。
⑤检查:
压力平稳后,组织人员对系统进行全面检查,做好漏点记录,处理完后再试压,直不漏为止,注意减顶冷却器大气腿是否畅通。
⑥泄压:
试压完毕后,打开塔底放空及水封罐大气腿放空要缓慢,关闭给汽点泄压。
5、原料油系统及各外送冷换设备、管线试压
(1)试压注意事项:
给汽前先脱水,缓慢给汽,防止冲坏塔内设备,试压完成后,泄压速度不可太快,试压期间要参照多处压力表,防止压力表失灵,组织好人员,专人给汽,专人看表,专人排空。
(2)吹扫详细流程
首先引净化风入装置串入蒸汽管网,吹扫时各流量表、调节阀走副线。
A、常压系统
①石脑油泵入口注风→分两路:
a路→EC8008/1.2.3.4(塔顶水冷器)→空冷机→塔放空。
b路→汽油阀组→回流→塔
↘→出装置至成品放空。
②顶循抽出注风→泵→顶循--原料油换热器(E8001/1.2)→回流阀组→塔放空。
初侧油馏出注风→汽提塔→泵→初侧--原料油换热器(E8003/1.2)→水冷器(EC8004/1.2)→重一油缓冲罐→成品罐前放空。
原料油泵注风→初顶循--原料油换热器(E8001/1.2)→重一--原料油换热器(E8002/1.2)分两路:
a路、→初侧--原料油换热器(E8003/1.2)→减二--原料油换热器二换(E8004/1.2)→减三--原料油二换(E8005/1.2)
b路、→减二--原料油换热器(E8006/1.2)→沥青--原料油五换(E8007/1.2)
两路合二为一后→电脱盐罐出分两路:
a路、→沥青--原料油四换(E8008/1.2)→减二--原料油一换(E8009/1.2)→减四--原料油二换(E8010/1.2)
b路、→减三--原料油二换(E8011/1.2)→沥青--原料油换热器三换(E8012/1.2)→减三--原料油一换(E8013/1.2)
两路合二为一后→沥青--原料油二换(E8014/1.2)→减四--原料油一换(E8015/1.2)→沥青--原料油一换(E8016/1.2)→初馏塔→塔底放空
⑤初底泵注风→加热炉→减压塔放空。
B、减压系统
①减一抽出注风→泵→减一--原料油换热器(E8002/1.2)→水冷器(EC8003)→回流→塔放空,另一路至成品罐前放空。
②减二抽出注风→减二--原料油一换(E8009/1.2)→减二--原料油二换(E8004/1.2)→减二--原料油三换(E8006/1.2)→水冷器(EC8002/1.2)→回流→塔放空,另一路至成品罐前放空。
③减三抽出注风→减三--原料油一换(E8013/1.2)→减三--原料油二换(E8011)→减三--原料油三换(E8005/1.2)→水冷器(EC8001/1.2)→回流→塔放空,另一路与减二混合至成品罐前放空。
减四抽出注风→减四--原料油一换(E8015/1.2)→减四--原料油二换(E8010/1.2)→回流→塔放空,另一路与减二、三混合至成品罐前放空。
减底泵注风→沥青--原料油一换(E8016/1.2)→→沥青--原料油二换(E8014/1.2)→沥青--原料油三换(E8012/1.2)→沥青--原料油四换(E8008/1.2)→沥青--原料油五换(E8007/1.2)→成品放空
塔注风(塔顶)→一级水冷(EC8005)→一级冷凝分液罐→二级水冷(EC8006)→二级冷凝分液罐→三级水冷(EC8007)→三级冷凝分液罐→水封罐放空
C、司炉
①蒸汽注风→炉前汽包→过热蒸汽→各注汽点前放空
②燃油泵注风→炉前火嘴处放空,另一路经循环线至燃油罐放空。
(3)试压时将风改为蒸汽,从一点给汽逐条管线试压压力控制1.2~1.5MPa,切净水严防水击,损坏设备、管线。
6、单机试运及水联运
吹扫试压完成后为了清除各管线、塔、容器内的杂物及焊渣,所以要引水入装置进行水联运,水联运的同时联系电工、机修对逐台机泵进行单机试运行,确保各机泵能运转正常,性能良好。
(1)关闭所有与塔连通的阀门,从装置内引水至各管网、设备进行水冲洗。
在冲洗初期待管线内杂物、泥沙、焊渣冲洗干净后,打开与塔连通的阀门,塔内进水,待达到一定液位后开启机泵进行系统内循环。
(2)在水联运初期各仪表、调节阀走副线,并且各管线、容器放空点及时放空排凝以防赃物太多堵塞管线,水联运24小时后投用各仪表、调节阀、浮球联系仪表调校至准确。
(3)水冲洗完成后打开放空放尽存水,并引净化风入装置,逐条管线、各个设备容器内进行吹扫,吹净其内的所有存水。
二、原料油开工方案
(一)具备的条件
联系化验室分析原料油比重、水份、馏程,新鲜水、循环水、仪表风、电、蒸汽引入装置,两炉达到点火条件,启用下列仪表:
初馏塔、减压塔、汽提塔、汽油回流罐、燃油罐液位显示,原料油进装置流量表及调节阀、各个温度显示;联系罐区备足原料油及产品油接受情况,原料油及沥青用蒸汽贯通确保畅通;钳工、电工、仪表三修必须现场待命;准备好消防器材及消防蒸汽胶带,通知消防车待命。
(1)改好原料油开路流程,重油投用伴热线。
(2)所有流量表全走副线,待开工正常后再投用,流程改好后全面检查,该关闭的阀门全部关闭,确保万无一失。
(3)司炉岗位检查两炉情况、燃油循环及温度、燃油系统火嘴情况确保能正常使用、准备好点火用具。
(4)原料油进炉、两塔之前要暖炉、暖塔,并且试压。
(5)所有的机泵加入规定的润滑油,机泵冷却水正常循环,密封水畅通,所有机泵打开入口阀门,关闭出口及连通阀,用泵出口放空阀排空脱水,压力表装好打开手阀,机泵盘车灵活,所有机泵达到备用标准。
(二)引油流程
引油时要先从原料油罐经过原料油泵将65~70℃的原料油加压0.5~0.8MPa进入装置,新装置开工时初期量要小控制在50t/h,换热器两支温差控制在10℃以内,开路循环时原料油要回至其它空罐,这样有利于计算装置内存油,在循环期间每2小时取原料油样做含水一次,含水低于1%后改闭路循环点火升温,炉出口温度控制在10℃/h升温,升至150℃为一个脱水期,此时密切注意机泵上量情况,同时各塔液位控制在30%左右,以防汽化沸至上层塔盘或集油箱。
如机泵汽化不上量,炉出口要快速升至200℃,过脱水关,此时可以恒温12小时。
当炉出口升至250~280℃时,恒温12小时,同时组织保运人员对各人孔、阀门、法兰进行一次热紧,在升温过程中炉升温要快,以提高拨出率,降低负荷;各侧线馏出至泵放空,见油后将各侧线油打入换热器内,至各外送阀组前排净水,各回流至回流阀组前排净水,以备需要时打回流,控制温度不能超高。
当温度升至300℃以上时,开启抽真空系统,开启时要注意,首先,蒸汽要排净水见汽,然后依次开启三级抽子蒸汽阀门约1/4,二级抽子蒸汽阀门约1/5,一级抽子蒸汽阀门约1/6,慢慢提真空度,稳定一段时间后再慢慢依次开启蒸汽阀门直至全开,瓦斯气进加热炉,当顶温达到90℃以上时开减一打回流,此时严格控制顶温不能超高;初顶温度达到90℃时开启空冷机。
(1)引油流程:
原油在罐内脱水、加温至60~80℃后由原料油泵加压至1.0MPa,进入装置,进换热器:
→顶循/原料油(E8001/1.2)→重一--原料油换热器(E8002/1.2)分两路:
a路:
→初侧--原料油换热器(E8003/1.2)→重二--原料油换热器二换(E8004/1.2)→重三--原料油换热器三换(E8005/1.2)
b路:
→重二--原料油换热器三换(E8006/1.2)→沥青--原料油五换(E8007/1.2)
两路合二为一后→(两支温差控制在5℃,压力差控制在0.5~0.9MPa±0.05MPa,开工期间暂时不投用电脱)电脱盐罐进行脱水处理。
脱后原油再分两路:
a路:
→沥青--原料油四换(E8008/1.2)→重二--原料油一换(E8009/1.2)→重四--原料油二换(E8010)换至225℃
b路:
→重三--原料油二换(E8011/1.2)→沥青--原料油换热三换(E8012/1.2)→重三--原料油一换(E8013/1.2)换至254℃
两路合二为一后→沥青--原料油二换(E8014/1.2)→重四--原料油一换(E8015/1.2)→沥青--原料油一换(E8016/1.2)→初馏塔→加热炉炉(温度250~270℃温差不超过5℃)→塔
(2)联系罐区,在原料油进装置流量表处注汽扫至罐区,直至扫通。
(3)打开原料油泵泵体放空,将管线内的水、汽放空,见油为止,开启原料油泵送油。
(4)原料油经过电脱前后一系列换热器进初馏塔,塔底见油后,启动塔底液位调节系统,液位高于50%时停原料油泵,静止20分钟,从塔底放空阀切水,见油为止,继续引油。
(5)启动初底泵,控制好初底液位。
(6)当减压塔见液位时,启动塔底液位调节系统,液位高于50%时停原料油泵,静止20分钟,从塔底放空阀切水,见油为止,继续引油。
(7)启动减底泵,控制好减底液位。
(8)原料油由减底泵送至渣油线,再经过污油线进入事先量好的空原料油罐内,此时为开路循环,取样分析整个原料油系统含水低于1%时,关闭污油线阀门,将原料油改至开工循环线进入原料油循环系统,此时为闭路循环。
(9)注意事项:
①、引油前一定要改好流程,所有放空阀,扫线阀关死,严防跑、串、憋、漏现象发生。
②、原料油进装置后,油到哪里,仪表就启用到哪里。
③、在原料油进装置过程中,一定要把(特别是塔底泵)换热器、调节阀、电脱及其它有关副线,各设备跨线都要打开一下,将存水顶净。
④、改闭路循环(塔底要保持较高液位),关掉原料油泵,利用塔底泵进行闭路循环。
⑤、联系化验室分析原料油含水,闭路循环无问题,含水合格后,即可点炉升温。
(三)点火升温
1、点火准备工作
引重催来干起进高压瓦斯分液罐,启用压控表,使压力控制在0.5MPa。
将对流室过热蒸汽给汽,并将出口放空压力控制在0.2MPa,初顶水冷器给水,空冷机启动。
改好塔上流程。
2、点火升温
(1)稳定原料油两支流量,点司炉火嘴,升温速度控制20℃/h。
(2)严格控制炉出口两支温度,温差不超过5℃。
如果温差大可用两支流量调节,但总量不变。
(3)当塔底温度升至150℃,此时为塔底脱水期,塔底泵极易抽空,此时应及时调节运转机泵或更换备用泵。
(4)加热炉出口升至250℃,恒温12小时,热紧。
(5)在升温过程中,如塔底液位低,为确保循环量,可启动原料油泵补油。
(6)加热炉出口升至320℃,恒温12小时。
3、改正常
全装置无问题后,可改开路。
启动原料油泵进油,同时各成品外送罐区。
4、开侧线
(1)改开路后,温度以100℃/h,加热炉出口升至365℃。
(2)在初馏塔底处,汽提蒸汽放空排凝,待过热蒸汽>300℃,炉出口高于350℃时,塔底可缓慢给汽。
(3)初顶温度升至90℃时,回流罐底部切水(严防回流带水)。
启动汽油回流泵及塔顶温度控制系统,向塔顶打回流,并视空冷器情况调节水冷器上水,使汽油冷后温度<40℃.
(4)塔顶建立回流,加热炉出口升至365℃,当初侧有液位时可启动泵外送,出侧线油走不合格线,颜色正常后改进成品罐
(5)开侧线前,水冷器给水。
开侧线后,视冷后温度高低决定是否走副线并适当调节上水;初侧油冷后控制<50℃
(6)初顶回流满足后,回流罐汽油液位升高时,汽油即可外送。
(7)及时联系化验室取样化验,待产品合格后,外送罐区。
(8)控制好冷后温度,严格控制塔底液位及塔顶温度,严防发生冲塔事故。
(9)塔全部稳定后,视塔内负荷情况,慢慢提加工量,并适当调节回流量。
(10)开注水、氨、缓蚀剂。
(11)注意事项
①、启动泵时一定要检查好流程,决不能出现失误。
②、各流量表、调节阀走副线,待正常后再投用,顶循打回流时,阀组前脱净水。
③、各机泵启动前排空,见油后启动泵
④、改开、闭路时要有专人负责,动作协调避免出现抽空、憋压现象。
(五)开工
1、准备工作
(1)改好系统流程,各侧线给蒸汽暖管线、塔。
(2)重顶水冷器给水,水封罐上满水建立水封。
2、开工程序
(1)炉继续升温至395℃。
(2)塔进料达300℃时,为了减轻塔负荷,可稍微开启抽真空系统,同时打开侧线馏出阀门。
(3)加热炉出口温度达到395℃时,塔顶温度会持续升高,重一有油后,也可启动向塔顶打回流。
(4)开侧线泵时,必须先从泵出口放空,放净管线及泵内存水,防止泵抽空。
开侧线后,注意注意调节各冷后温度,严防凝线。
(5)塔顶回流满足后,重一应该已建立液位,可暂时不外送,留作重二、三补油用。
(6)顶温度基本稳定,重二、三有油时,可启动泵往侧线打回流,并适当减小塔顶回流。
(7)开抽子时,蒸汽首先要放净存水,先缓慢开启三级抽子,待真空度达到最大值时再依次开启二级、一级。
瓦斯气由朝天放空,改进加热炉。
(六)、岗位注意事项
1、严格按工艺要求,控制好原料油进装置流量。
2、加热炉出口360℃,两支温差<5℃
3、各液位控制50±10%,入炉量要均匀,严禁偏流。
4、各回流量要根据产品质量适当调节,但要避免回流过大或过小。
5、回流罐注意切水,以免回流带水。
6、调节时幅度要小,微调,缓调以免出现大的波动。
(七)开工正常后的各操作参数
A类指标:
司炉出口:
495±1℃
B类指标:
初顶压力:
≤0.05MPa塔顶压力:
﹣0.098MPa液位:
50±5%
产品质量控制:
汽油干点≤205℃重一油凝点:
10~﹣15℃沥青软化点:
>48℃
注剂量:
破乳剂300~500ppm注水量6~8%缓蚀剂50ppm初顶注水量1t/h
三、正常操作
(一)、常压岗位操作法
1、塔的操作要点
塔的操作主要包括塔顶压力和塔顶、侧线温度,塔底液位的控制,使操作平稳的关键就是控制好塔的物料平衡、热量平衡和压力平衡,使其维持在一个最佳稳定操作条件。
塔的正常操作可分为:
1按物料平衡要求、质量要求,调节好各侧线量。
2塔顶、中段、顶循环回流取热分配均匀。
3塔顶温度控制平稳。
4塔顶压力控制平稳,并注意诸多因素对压力的影响,及时调节。
5维持顶回流温度的恒定,防止回流带水。
6保持顶循回流、中段回流量的稳定及入塔温度平稳。
7保证塔底液位正常,液位指示平稳。
8保证塔底注汽量合适。
2、影响塔顶温度的因素及调节方法。
(1)影响因素:
①、原料油换后温度升高,顶温升高。
②、司炉出口温度升高,顶温升高。
③、原料油含水量增加,顶温升高。
④、原料油变轻,顶温升高。
⑤、顶回流带水,顶压升高,顶温升高。
⑥、顶回流温度升高,顶温升高。
⑦、各回流量增加或减少,顶温降低或升高。
⑧、顶回流量太大出现淹塔时,顶温出现周期性的大幅度波动。
⑨、侧线温度升高,顶温升高。
⑩、塔底注汽量增大,顶温升高。
(2)调节方法:
①、换热温度升高时,相应调节炉出口温度。
②、适当降低炉出口温度。
③、视塔顶压力情况调节顶温,若带水严重加强脱水。
④、相应提高各回流取热,来改变塔顶负荷,使塔内汽液相负荷达到均匀。
⑤、若回流带水引起超温、超压时,应加强回流罐切水,消除波动因素。
⑥、视其具体原因回流调节及时相应的降低温度。
⑦、降低顶回流量。
⑧、主要是侧线抽出量增大,而引起顶温升高,这时应降低侧线抽出量但不能大幅度调节。
此时应调节中段回流。
⑨、要控制在一定温度内,不能超温及波动太大,注意平稳操作调节。
⑩、、塔底注汽量要合适,达到汽提的目的,并要注意汽提蒸汽的温度、压力以及是否带水。
3、侧线温度的影响因素。
①、顶温升高,侧线温度升高。
②、炉出口温度升高,侧线温度升高。
③、侧线抽出量减少会使该侧线及下侧线温度下降。
④、进料量减少,侧线温度下降。
⑤、注汽量增加会使侧线温度升高。
⑥、原料油性质变化,会使侧线温度发生变