多工步组合机床的plc控制系统设计.docx
《多工步组合机床的plc控制系统设计.docx》由会员分享,可在线阅读,更多相关《多工步组合机床的plc控制系统设计.docx(28页珍藏版)》请在冰豆网上搜索。
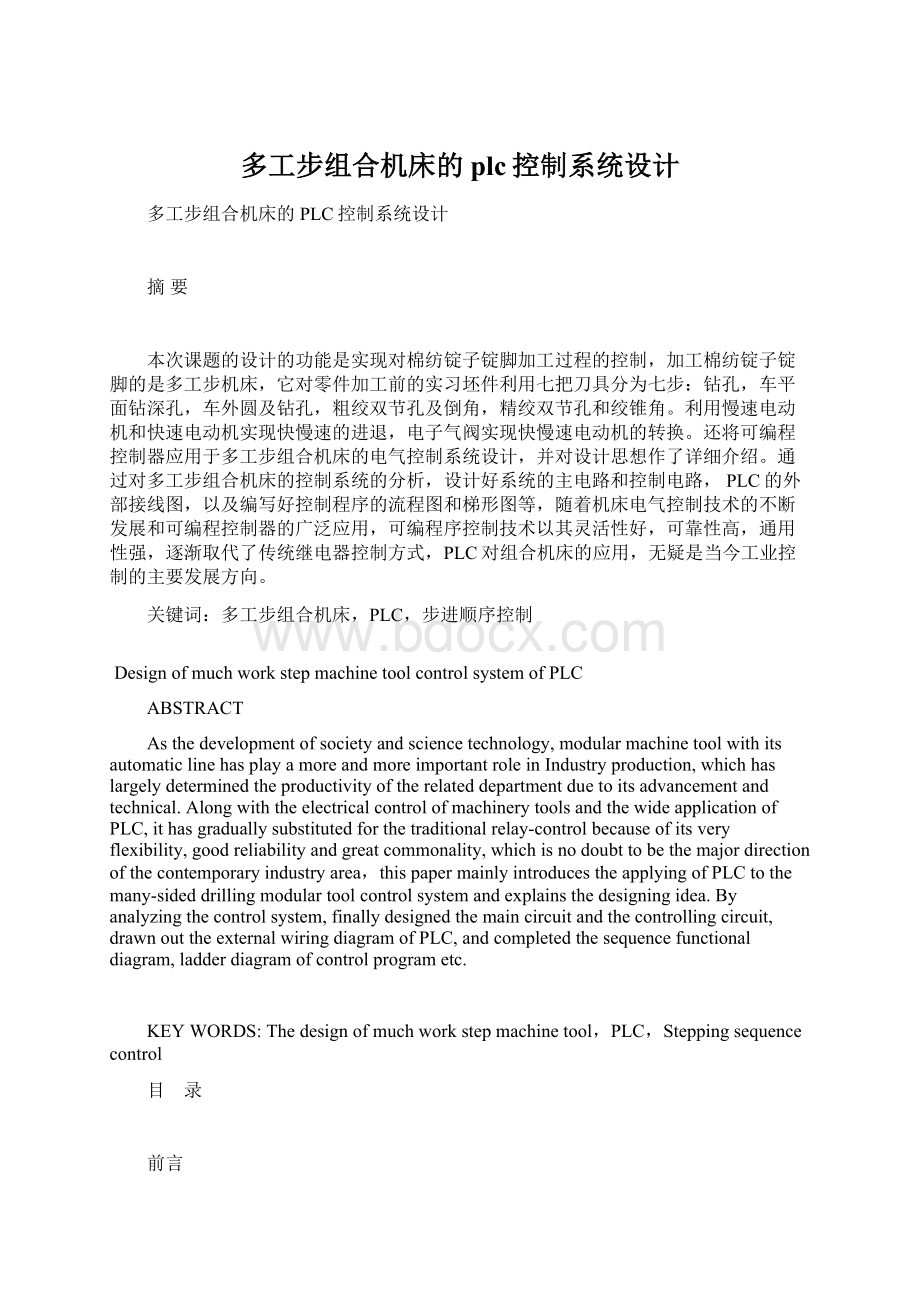
多工步组合机床的plc控制系统设计
多工步组合机床的PLC控制系统设计
摘要
本次课题的设计的功能是实现对棉纺锭子锭脚加工过程的控制,加工棉纺锭子锭脚的是多工步机床,它对零件加工前的实习坯件利用七把刀具分为七步:
钻孔,车平面钻深孔,车外圆及钻孔,粗绞双节孔及倒角,精绞双节孔和绞锥角。
利用慢速电动机和快速电动机实现快慢速的进退,电子气阀实现快慢速电动机的转换。
还将可编程控制器应用于多工步组合机床的电气控制系统设计,并对设计思想作了详细介绍。
通过对多工步组合机床的控制系统的分析,设计好系统的主电路和控制电路,PLC的外部接线图,以及编写好控制程序的流程图和梯形图等,随着机床电气控制技术的不断发展和可编程控制器的广泛应用,可编程序控制技术以其灵活性好,可靠性高,通用性强,逐渐取代了传统继电器控制方式,PLC对组合机床的应用,无疑是当今工业控制的主要发展方向。
关键词:
多工步组合机床,PLC,步进顺序控制
DesignofmuchworkstepmachinetoolcontrolsystemofPLC
ABSTRACT
Asthedevelopmentofsocietyandsciencetechnology,modularmachinetoolwithitsautomaticlinehasplayamoreandmoreimportantroleinIndustryproduction,whichhaslargelydeterminedtheproductivityoftherelateddepartmentduetoitsadvancementandtechnical.AlongwiththeelectricalcontrolofmachinerytoolsandthewideapplicationofPLC,ithasgraduallysubstitutedforthetraditionalrelay-controlbecauseofitsveryflexibility,goodreliabilityandgreatcommonality,whichisnodoubttobethemajordirectionofthecontemporaryindustryarea,thispapermainlyintroducestheapplyingofPLCtothemany-sideddrillingmodulartoolcontrolsystemandexplainsthedesigningidea.Byanalyzingthecontrolsystem,finallydesignedthemaincircuitandthecontrollingcircuit,drawnouttheexternalwiringdiagramofPLC,andcompletedthesequencefunctionaldiagram,ladderdiagramofcontrolprogrametc.
KEYWORDS:
Thedesignofmuchworkstepmachinetool,PLC,Steppingsequencecontrol
目 录
前言
在机床行业中,多工步机床由于其工步及动作多,控制较复杂,采用传统的继电器控制时,需要的继电器多,接线复杂,因此,故障多,维修困难,费工费时,不仅加大了维修成本,而且影响了设备的工效。
在可编程序控制器问世之前,继电器接触器在工业领域中占主导地位。
继电器接触器控制系统是采用固定接线的硬件实现控制逻辑。
另外,大型控制系统用继电器和接触器控制,使用的继电器数目越多,控制的体积越大,耗电多,且继电器触电为机械触点,工作频率较低,在频繁动作的情况下寿命较短,造成系统故障,系统可靠性差。
为了解决这一问题,早在1968年,美国最大的汽车制造商通用汽车公司,为了适应汽车型号不断翻新,以求在激烈竞争的汽车工业中占有优势,提出要用一种新型控制装置来取代继电器接触器控制装置,并且对未来的新型控制装置做了具体的设想,药把计算机的完备功能以及灵活性、通用性好等优点溶于新的控制装置中,且要求新的控制装置编程简单,使得步熟悉计算机的人员也能很快掌握它的使用技术。
PLC是综合继电器接触器控制的优点及计算机灵活、方便的特点而设计制造和发展的,这就使得PLC具有许多其他控制器所无法相比的特点:
可靠性高,抗干扰能力强;通用性强,使用方便;采用模块化结构,使系统组合灵活方便;编程语言简单、易学,便于掌握;系统设计周期短;对生产工艺改变适应性强;安装简单,调试方便、维护工作量小。
第1章组合机床的设计简介
从本世纪30年代开始,机械加工业企业为了提高生产效率,采用机械化流水作业的生产方式,对不同类型的零件分别组成自动生产线。
随着产品机型的更新换代,生产线承担的加工对象也随之改变,这就需要改变控制程序,使生产线的机械设备按新的工艺流程运行,而传统继电器控制系统是采用固定接线的,体积大,结构复杂,维修不方便,其很难适应当代生产工艺要求。
大型自动生产线的控制系统使用的继电器数量很多,这种有触点的电器工作频率较低,在频繁的动作情况下寿命较短,从而造成系统故障,使生产线的运行可靠性降低。
为了解决这个问题,于1969年美国数字设备公司率先研制出第一台可编程控制器,其在通用汽车公司的自动装配线上试用成功,PLC体积小,最突出优点是可靠性高,平均无故障运行时间可达10万h以上,可大大减少设备维修费用和停产造成的经济损失,当前PLC已经成为在电气控制系统中应用最为广泛的核心装置。
组合机床及其PLC电气控制系统是集机电于一体的综合自动化程度较高的制造技术和成套工艺装备。
它具备经济、高效、高质等优点,因此被广泛应用于工程机械、军工、能源、交通、轻工、家电等行业。
我国传统的组合机床及组合机床电气控制系统主要采用机、电、气、液压控制,它的加工对象主要是生产批量比较大的大中型箱体类和轴类零件(近年研制的组合机床加工连杆、板件等也占一定份额),完成钻孔、扩孔、铰孔,加工各种螺纹、镗孔、车端面和凸台,在孔内镗各种形状槽,以及铣削平面和成形面等。
组合机床的分类繁多,有大型组合机床和小型组合机床,有单面、双面、三面、卧式、立式、倾斜式、复合式,还有多工位回转台式组合机床等;随着技术的不断进步,一种新型的组合机床——柔性组合机床越来越受到人们的青睐,它应用多位主轴箱、可换主轴箱、编码随行夹具和刀具的自动更换,配以可编程序控制器、数字控制等,能任意改变工作循环控制和驱动系统,并能灵活适应多品种加工的可调可变的组合机床。
另外,近年来组合机床加工中心、数控组合机床、机床辅机(清洗机、装配机、综合测量机、试验机、输送线)等在组合机床行业中所占份额也越来越大。
因此,为适应现代化生产企业的市场要求,为适应组合机床由过去的“刚性”机床结构,向“柔性”化方向发展的趋势,我设计了这套“双面钻孔组合机床的PLC电气控制系统设计”,希望能够满足用户的需求,真正成为刚柔兼备的自动化装备。
1.1组合机床的加工方式
组合机床一般采用多轴、多刀、多工序、多面或多工位同时加工的方式,生产效率比通用机床高几倍至几十倍。
由于通用部件已经标准化和系列化,可根据需要灵活配置,能缩短设计和制造周期。
因此,组合机床兼有低成本和高效率的优点,在大批、大量生产中得到广泛应用,并可用以组成自动生产线。
组合机床一般用于加工箱体类或特殊形状的零件。
加工时,工件一般不旋转,由刀具的旋转运动和刀具与工件的相对进给运动,来实现钻孔、扩孔、锪孔、铰孔、镗孔、铣削平面、切削内外螺纹以及加工外圆和端面等。
有的组合机床采用车削头夹持工件使之旋转,由刀具作进给运动,也可实现某些回转体类零件(如飞轮、汽车后桥半轴等)的外圆和端面加工。
1.2组合机床的发展史
二十世纪70年代以来,随着可转位刀具、密齿铣刀、镗孔尺寸自动检测和刀具自动补偿技术的发展,组合机床的加工精度也有所提高。
铣削平面的平面度可达0.05毫米/1000毫米,表面粗糙度可低达2.5~0.63微米;镗孔精度可达IT7~6级,孔距精度可达0.03~0.02微米。
专用机床是随着汽车工业的兴起而发展起来的。
在专用机床中某些部件因重复使用,逐步发展成为通用部件,因而产生了组合机床。
最早的组合机床是1911年在美国制成的,用于加工汽车零件。
初期,各机床制造厂都有各自的通用部件标准。
为了提高不同制造厂的通用部件的互换性,便于用户使用和维修,1953年美国福特汽车公司和通用汽车公司与美国机床制造厂协商,确定了组合机床通用部件标准化的原则,即严格规定各部件间的联系尺寸,但对部件结构未作规定。
近两年虽然组合机床行业产销呈现上升趋势,但行业内一些企业同样存在负债经营的情况,主要原因是传统的组合机床产品不能满足用户柔性化、高精度、短周期的市场需求,同时组合机床行业一些企业存在现代化管理水平低、人才流失严重、科研成果不能迅速转化为生产力等缺陷。
1.3组合机床部件分类
通用部件按功能可分为动力部件、支承部件、输送部件、控制部件和辅助部件五类。
动力部件是为组合机床提供主运动和进给运动的部件。
主要有动力箱、切削头和动力滑台。
支承部件是用以安装动力滑台、带有进给机构的切削头或夹具等的部件,有侧底座、中间底座、支架、可调支架、立柱和立柱底座等。
输送部件是用以输送工件或主轴箱至加工工位的部件,主要有分度回转工作台、环形分度回转工作台、分度鼓轮和往复移动工作台等。
控制部件是用以控制机床的自动工作循环的部件,有液压站、电气柜和操纵台等。
辅助部件有润滑装置、冷却装置和排屑装置等。
1.4组合机床的发展
为了使组合机床能在中小批量生产中得到应用,往往需要应用成组技术,把结构和工艺相似的零件集中在一台组合机床上加工,以提高机床的利用率。
这类机床常见的有两种,可换主轴箱式组合机床和转塔式组合机床。
组合机床未来的发展将更多的采用调速电动机和滚珠丝杠等传动,以简化结构、缩短生产节拍;采用数字控制系统和主轴箱、夹具自动更换系统,以提高工艺可调性;以及纳入柔性制造系统等。
1.5组合机床在中小批量生产中的应用
组合机床是以通用部件为基础,配以按工件特定外形和加工工艺设计的专用部件和夹具,组成的半自动或自动专用机床。
它一般采用多轴、多刀、多工序、多面或多工位同时加工的方式,生产效率比通用机床高几倍至几十倍。
由于通用部件已经标准化和系列化,可根据需要灵活配置,能缩短设计和制造周期。
因此,组合机床兼有低成本和高效率的优点,在大批、大量生产中得到广泛应用,并可用以组成自动生产线。
组合机床一般用于加工箱体类或非凡外形的零件。
加工时,工件一般不旋转,由刀具的旋转运动和刀具与工件的相对进给运动,来实现钻孔、扩孔、锪孔、铰孔、镗孔、铣削平面、切削内外螺纹以及加工外圆和端面等。
有的组合机床采用车削头夹持工件使之旋转,由刀具作进给运动,也可实现某些回转体类零件(如飞轮、汽车后桥半轴等)的外圆和端面加工。
专用机床是随着汽车工业的兴起而发展起来的。
在专用机床中某些部件因重复使用,逐步发展成为通用部件,因而产生了组合机床。
最早的组合机床是1911年在美国制成的,用于加工汽车零件。
初期,各机床制造厂都有各自的通用部件标准。
为了提高不同制造厂的通用部件的互换性,便于用户使用和维修,1953年美国福特汽车公司和通用汽车公司与美国机床制造厂协商,确定了组合机床通用部件标准化的原则,即严格规定各部件间的联系尺寸,但对部件结构未作规定。
通用部件按功能可分为动力部件、支承部件、输送部件、控制部件和辅助部件五类。
动力部件是为组合机床提供主运动和进给运动的部件。
主要有动力箱、切削头和动力滑台。
为了使组合机床能在中小批量生产中得到应用,往往需要应用成组技术,把结构和工艺相似的零件集中在一台组合机床上加工,以提高机床的利用率。
这类机床常见的有两种,可换主轴箱式组合机床和转塔式组合机床。
组合机床未来的发展将更多的采用调速电动机和滚珠丝杠等传动,以简化结构、缩短生产节拍;采用数字控制系统和主轴箱、夹具自动更换系统,以提高工艺可调性;以及纳入柔性制造系统等。
1.6PLC在组合机床中的应用
目前,PLC在国内外已广泛应用于钢铁、石油、化工、电力、建材、机械制造、汽车、轻纺、交通运输、环保及文化娱乐等各个行业,使用情况大致可归纳为如下几类。
1.开关量的逻辑控制
这是PLC最基本、最广泛的应用领域,它取代传统的继电器电路,实现逻辑控制、顺序控制,既可用于单台设备的控制,也可用于多机群控及自动化流水线。
如注塑机、印刷机、订书机械、组合机床、磨床、包装生产线、电镀流水线等。
2.模拟量控制
在工业生产过程当中,有许多连续变化的量,如温度、压力、流量、液位和速度等都是模拟量。
为了使可编程控制器处理模拟量,必须实现模拟量和数字量之间的A/D转换及D/A转换。
PLC厂家都生产配套的A/D和D/A转换模块,使可编程控制器用于模拟量控制。
3.运动控制
PLC可以用于圆周运动或直线运动的控制。
从控制机构配置来说,早期直接用于开关量I/O模块连接位置传感器和执行机构,现在一般使用专用的运动控制模块。
如可驱动步进电机或伺服电机的单轴或多轴位置控制模块。
世界上各主要PLC厂家的产品几乎都有运动控制功能,广泛用于各种机械、机床、机器人、电梯等场合。
4.过程控制
过程控制是指对温度、压力、流量等模拟量的闭环控制。
作为工业控制计算机,PLC能编制各种各样的控制算法程序,完成闭环控制。
PID调节是一般闭环控制系统中用得较多的调节方法。
大中型PLC都有PID模块,目前许多小型PLC也具有此功能模块。
PID处理一般是运行专用的PID子程序。
过程控制在冶金、化工、热处理、锅炉控制等场合有非常广泛的应用。
5.数据处理
现代PLC具有数学运算(含矩阵运算、函数运算、逻辑运算)、数据传送、数据转换、排序、查表、位操作等功能,可以完成数据的采集、分析及处理。
这些数据可以与存储在存储器中的参考值比较,完成一定的控制操作,也可以利用通信功能传送到别的智能装置,或将它们打印制表。
数据处理一般用于大型控制系统,如无人控制的柔性制造系统;也可用于过程控制系统,如造纸、冶金、食品工业中的一些大型控制系统。
6.通信及联网
PLC通信含PLC间的通信及PLC与其它智能设备间的通信。
随着计算机控制的发展,工厂自动化网络发展得很快,各PLC厂商都十分重视PLC的通信功能,纷纷推出各自的网络系统。
新近生产的PLC都具有通信接口,通信非常方便。
7.PLC控制的数控滑台结构
一般组合机床自动线中的数控滑台采用步进电机驱动的开环伺服机构。
采用PLC控制的数控滑台由可编程控制器、环行脉冲分配器、步进电机驱动器、步进电机和伺服传动机构等部分组成,伺服传动机构中的齿轮Z1、Z2应该采取消隙措施,避免产生反向死区或使加工精度下降;而丝杠传动副则应该根据该单元的加工精度要求,确定是否选用滚珠丝杠副。
采用滚珠丝杠副,具有传动效率高、系统刚度好、传动精度高、使用寿命长的优点,但成本较高且不能自锁。
8.控制系统的软件结构
软件结构根据控制要求而设计,主要划分为五大模块:
即步进电机控制模块、定位控制模块、数据拨盘输入及数据传输模块、数码输出显示模块、元件故障的自动检测与报警模块。
第2章可编程控制器的概述
2.1可编程控制器的基本概念
可编程控制器(ProgrammableController)是计算机家族中的一员,是为工业控制应用而设计制造的。
早期的可编程控制器称作可编程逻辑控制器,简称PLC,它主要用来代替继电器实现逻辑控制。
随着技术的发展,这种装置的功能已经大大超过了逻辑控制的范围,因此,今天这种装置称作可编程控制器,简称PC。
但是为了避免与个人计算机的简称混淆,所以将可编程控制器简称PLC。
2.2可编程控制器的由来
在60年代,汽车生产流水线的自动控制系统基本上都是由继电器控制装置构成的。
当时汽车的每一次改型都直接导致继电器控制装置的重新设计和安装。
随着生产的发展,汽车型号更新的周期愈来愈短,这样,继电器控制装置就需要经常地重新设计和安装,十分费时,费工,费料,甚至阻碍了更新周期的缩短。
为了改变这一现状,美国通用汽车公司在1969年公开招标,要求用新的控制装置取代继电器控制装置,并提出了十项招标指标,即:
1.编程方便,现场可修改程序;
2.维修方便,采用模块化结构;
3.可靠性高于继电器控制装置;
4.体积小于继电器控制装置;
5.数据可直接送入管理计算机;
6.成本可与继电器控制装置竞争;
7.输入可以是交流115V;
8.输出为交流115V,2A以上,能直接驱动电磁阀,接触器等;
9.在扩展时,原系统只要很小变更;
10.用户程序存储器容量至少能扩展到4K。
1969年,美国数字设备公司(DEC)研制出第一台PLC,在美国通用汽车自动装配线上试用,获得了成功。
这种新型的工业控制装置以其简单易懂,操作方便,可靠性高,通用灵活,体积小,使用寿命长等一系列优点,很快地在美国其他工业领域推广应用到1971年,已经成功地应用于食品,饮料,冶金,造纸等工业。
这一新型工业控制装置的出现,也受到了世界其他国家的高度重视。
1971日本从美国引进了这项新技术,很快研制出了日本第一台PLC。
1973年,西欧国家也研制出它们的第一台PLC。
我国从1974年开始研制。
于1977年开始工业应用。
2.3可编程控制器的特点
2.3.1可靠性高
1.所有的I/O接口电路均采用光电隔离,使工业现场的外电路与PLC内部电路之间电气上隔离。
2.各输入端均采用R-C滤波器,其滤波时间常数一般为10~20ms.
3.各模块均采用屏蔽措施,以防止辐射干扰。
4.采用性能优良的开关电源。
5.对采用的器件进行严格的筛选。
6.良好的自诊断功能,一旦电源或其他软,硬件发生异常情况,CPU立即采用有效措施,以防止故障扩大。
7.大型PLC还可以采用由双CPU构成冗余系统或有三CPU构成表决系统,使可靠性更进一步提高。
2.3.2丰富的I/O接口模块
PLC针对不同的工业现场信号,如:
•交流或直流;
•开关量或模拟量;
•电压或电流;
•脉冲或电位;
•强电或弱电等。
有相应的I/O模块与工业现场的器件或设备,如:
•按钮
•行程开关
•接近开关
•传感器及变送器
•电磁线圈
•控制阀
可直接连接。
另外为了提高操作性能,它还有多种人-机对话的接口
模块;为了组成工业局部网络,它还有多种通讯联网的接口模块,等等。
2.3.3采用模块化结构
为了适应各种工业控制需要,除了单元式的小型PLC以外,绝大多数PLC均采用模块化结构。
PLC的各个部件,包括CPU,电源,I/O等均采用模块化设计,由机架及电缆将各模块连接起来,系统的规模和功能可根据用户的需要自行组合。
2.3.4编程简单易学
PLC的编程大多采用类似于继电器控制线路的梯形图形式,对使用者来说,不需要具备计算机的专门知识,因此很容易被一般工程技术人员所理解和掌握。
2.3.5安装简单,维修方便
PLC不需要专门的机房,可以在各种工业环境下直接运行。
使用时只需将现场的各种设备与PLC相应的I/O端相连接,即可投入运行。
各种模块上均有运行和故障指示装置,便于用户了解运行情况和查找故障,由于采用模块化结构,因此一旦某模块发生故障,用户可以通过更换模块的方法,使系统迅速恢复运行。
2.4可编程控制器的工作原理
最初研制生产的PLC主要用于代替传统的由继电器接触器构成的控制装置,但这两者的运行方式是不相同的:
继电器控制装置采用硬逻辑并行运行的方式,即如果这个继电器的线圈通电或断电,该继电器所有的触点(包括其常开或常闭触点)在继电器控制线路的哪个位置上都会立即同时动作。
PLC的CPU则采用顺序逻辑扫描用户程序的运行方式,即如果一个输出线圈或逻辑线圈被接通或断开,该线圈的所有触点(包括其常开或常闭触点)不会立即动作,必须等扫描到该触点时才会动作。
为了消除二者之间由于运行方式不同而造成的差异,考虑到继电器控制装置各类触点的动作时间一般在100ms以上,而PLC扫描用户程序的时间一般均小于100ms,因此,PLC采用了一种不同于一般微型计算机的运行方式,这样在对于I/O响应要求不高的场合,PLC与继电器控制装置的处理结果上就没有什么区别了。
当PLC投入运行后,其工作过程一般分为三个阶段,即输入采样、用户程序执行和输出刷新三个阶段。
完成上述三个阶段称作一个扫描周期。
在整个运行期间,PLC的CPU以一定的扫描速度重复执行上述三个阶段。
2.4.1输入采样阶段
在输入采样阶段,PLC以扫描方式依次地读入所有输入状态和数据,并将它们存入I/O映象区中的相应得单元内。
输入采样结束后,转入用户程序执行和输出刷新阶段。
在这两个阶段中,即使输入状态和数据发生变化,I/O映象区中的相应单元的状态和数据也不会改变。
因此,如果输入是脉冲信号,则该脉冲信号的宽度必须大于一个扫描周期,才能保证在任何情况下,该输入均能被读入。
2.4.2用户程序执行阶段
在用户程序执行阶段,PLC总是按由上而下的顺序依次地扫描用户程序(梯形图)。
在扫描每一条梯形图时,又总是先扫描梯形图左边的由各触点构成的控制线路,并按先左后右、先上后下的顺序对由触点构成的控制线路进行逻辑运算,然后根据逻辑运算的结果,刷新该逻辑线圈在系统RAM存储区中对应位的状态;或者刷新该输出线圈在I/O映象区中对应位的状态;或者确定是否要执行该梯形图所规定的特殊功能指令。
即,在用户程序执行过程中,只有输入点在I/O映象区内的状态和数据不会发生变化,而其他输出点和软设备在I/O映象区或系统RAM存储区内的状态和数据都有可能发生变化,而且排在上面的梯形图,其程序执行结果会对排在下面的凡是用到这些线圈或数据的梯形图起作用;相反,排在下面的梯形图,其被刷新的逻辑线圈的状态或数据只能到下一个扫描周期才能对排在其上面的程序起作用。
2.4.3输出刷新阶段
当扫描用户程序结束后,PLC就进入输出刷新阶段。
在此期间,CPU按照I/O映象区内对应的状态和数据刷新所有的输出锁存电路,再经输出电路驱动相应的外设。
这时,才是PLC的真正输出。
第3章系统设计的总体方案
3.1系统总体设计思路及方案的确定
实现对加工棉纺锭子锭脚多工步机床控制有两种方法,一个是利用传统的继电器的途径实现;一个是利用可编程控制器编程途径实现。
两者都有各自的优缺点。
具体利用哪一种途径,需要对目的系统进行详细和全方位的分析。
设计时思维对象是具体的继电器,利用各种功能的继电器实现控制电路。
在利用PLC实现时,有两两种途径在实现的方法上也不相同。
在利用传统继电器实现时,主要利用经验法,种方法,一个是利用定时和基本指令组合实现。
一个是利用步控指令实现。
用基本逻辑指令实现较复杂的顺序控制,其梯形图比较复杂,而且不太直观。
步控指令使复杂的顺序控制程序能够方便地实现。
采用传统的继电器控制时,需要的继电器多,接线复杂,因此,故障多,维修困难,费工费时,不仅加大了修理成本,而且影响了设备的工效;采用PLC实现无需复杂的接线,而且实现起来方便,不费时。
无需大量继电器,只需PLC芯片,基本无修理成本。
3.2组合机床电气控制系统构成
上面分析过了实现加工棉