管壳式换热器的课程.docx
《管壳式换热器的课程.docx》由会员分享,可在线阅读,更多相关《管壳式换热器的课程.docx(34页珍藏版)》请在冰豆网上搜索。
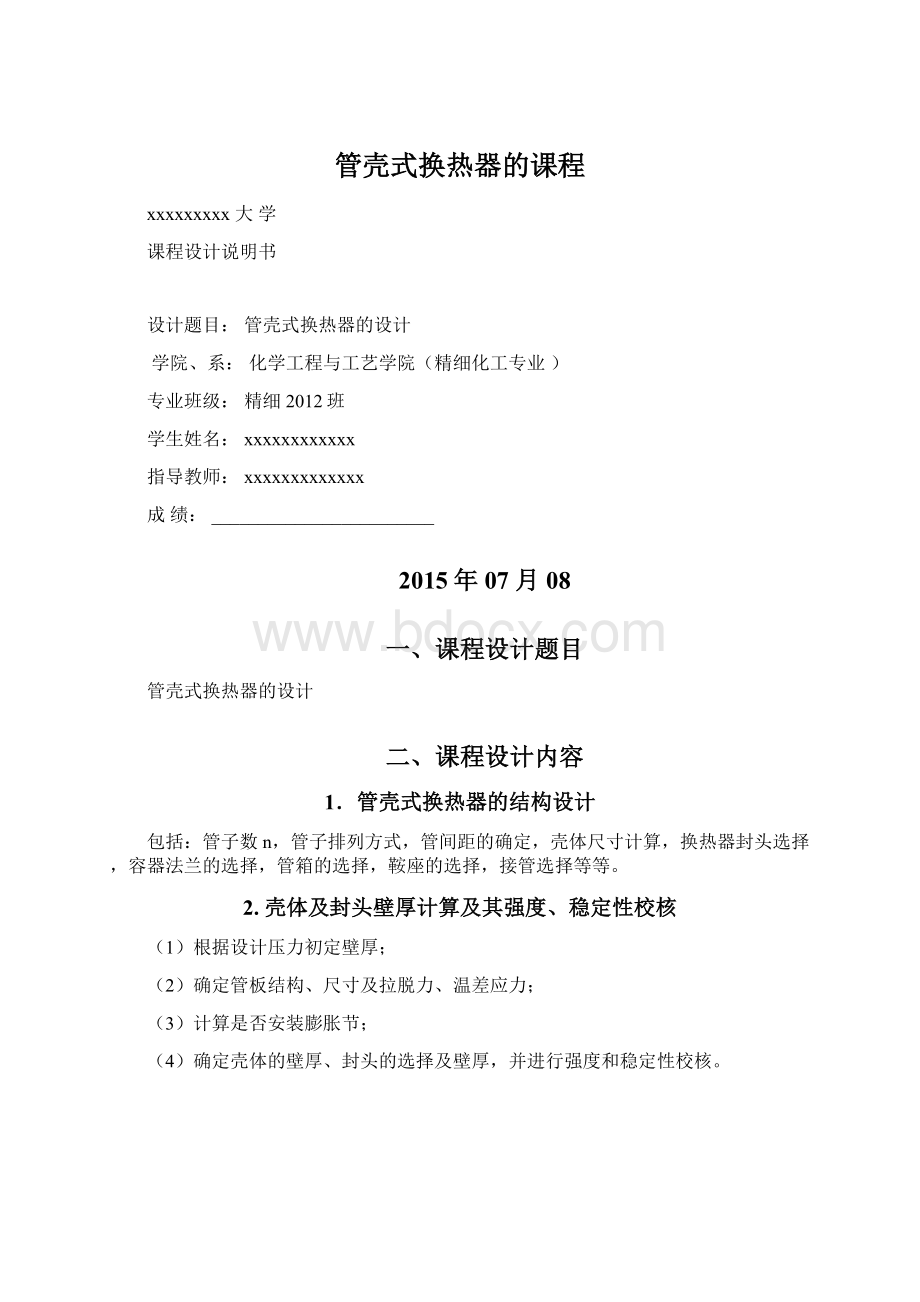
管壳式换热器的课程
xxxxxxxxx大学
课程设计说明书
设计题目:
管壳式换热器的设计
学院、系:
化学工程与工艺学院(精细化工专业)
专业班级:
精细2012班
学生姓名:
xxxxxxxxxxxx
指导教师:
xxxxxxxxxxxxx
成绩:
________________________
2015年07月08
一、课程设计题目
管壳式换热器的设计
二、课程设计内容
1.管壳式换热器的结构设计
包括:
管子数n,管子排列方式,管间距的确定,壳体尺寸计算,换热器封头选择,容器法兰的选择,管箱的选择,鞍座的选择,接管选择等等。
2.壳体及封头壁厚计算及其强度、稳定性校核
(1)根据设计压力初定壁厚;
(2)确定管板结构、尺寸及拉脱力、温差应力;
(3)计算是否安装膨胀节;
(4)确定壳体的壁厚、封头的选择及壁厚,并进行强度和稳定性校核。
3.筒体水压试验应力校核
4.鞍座的选择
5.换热器各主要组成部分选材,参数确定。
6.编写设计说明书一份
7.绘制1号装配图一张。
三、设计条件
(1)气体工作压力
管程:
半水煤气0.7MPa
壳程:
变换气0.475MPa
(2)壳、管壁温差50℃,tt>ts
壳程介质温度为400~220℃,管程介质温度为180~370℃。
(3)由工艺计算求得换热面积为105m2。
(4)壳体与封头材料在低合金高强度钢中间选用,并查出其参数,接管及其他数据根据表7-15、7-16选用。
(5)壳体与支座双面对接焊接,壳体焊接接头系数Φ=0.85
(6)图纸:
参考图7-52,注意:
尺寸需根据自己的设计的尺寸标注。
四、基本要求
1.学生要按照任务书要求,独立完成管壳式换热器设备的机械设计;
2.设计说明书一律采用电子版,1号图纸一律采用CAD绘制;
3.画图结束后,将图纸按照统一要求折叠A4,同设计说明书统一在19周周五早上8:
30答辩.
4.根据设计说明书、图纸、平时表现及答辩综合评分。
五、说明书的内容
1.符号说明
2.前言
(1)设计条件;
(2)设计依据;
(3)设备结构形式概述。
3.材料选择
(1)选择材料的原则;
(2)确定各零、部件的材质;
(3)确定焊接材料。
4.绘制结构草图
(1)换热器装配图
(2)确定支座、接管、人孔、控制点接口及附件、内部主要零部件的轴向及环向位置,以单线图表示;
(3)标注形位尺寸。
(4)写出图纸上的技术要求、技术特性表、接管表、标题明细表等
5.壳体、封头壁厚设计
(1)筒体、封头及支座壁厚设计;
(2)焊接接头设计;
(3)压力试验验算;
6.标准化零、部件选择及补强计算:
(1)接管及法兰选择:
根据结构草图统一编制表格。
内容包括:
代号,PN,DN,法兰密封面形式,法兰标记,用途)。
补强计算。
(2)其它标准件选择。
7.结束语:
对自己所做的设计进行小结与评价,经验与收获。
8.主要参考资料。
【格式要求】:
1.计算单位一律采用国际单位;2.计算过程及说明应清楚;
3.所有标准件均要写明标记或代号;4.设计说明书目录要有序号、内容、页码;
5.设计说明书中与装配图中的数据一致。
如果装配图中有修改,在说明书中要注明变更;
6.书写工整,字迹清晰,层次分明;7.设计说明书要有封面和封底,均采用A4纸,装订成册。
六、主要参考资料
1.《化工设备机械基础课程设计指导书》.化学工业出版.2005.1
2.《化工设备机械基础》第五版刁与玮王立业编著2003.3;
3.《化工单元过程与设备设计》匡国柱史启才主编;
4.《化工制图》华东化工学院制图教研室编人民教育出版社1980;
5.《化工设备机械基础》参考资料;
6.《钢制压力容器》GB150-1998;
7.《钢制塔式容器》JB4710-1992;
8.GB151-1999《管壳式换热器》1999年;
9.《压力容器安全技术监察规程》国家质量技术监督局1999年。
管壳式换热器的结构设计
序言
课程设计理论是学生理论联系实际的一次很好的机会,本次实验就管壳式换热器进行一次课程设计,掌握并了解在工业生产中节能、高效、环保等概念。
换热设备在炼油、石油化工以及在其他工业中使用广泛,它适用于冷却、冷凝、加热、蒸发和废热回收等各个方面。
其中,管壳式换热器虽然在换热效率、设备的体积和金属材料的消耗量等方面不如其他新型的换热设备,但它具有结构坚固、弹性大、可靠程度高、使用范围广等优点,所以在各工程中仍得到普遍使用。
管壳式换热器的结构设计,是为了保证换热器的质量和运行寿命,必须考虑很多因素,如材料、压力、温度、壁温差、结垢情况、流体性质以及检修与清理等等来选择某一种合适的结构形式。
对同一种形式的换热器,由于各种条件不同,往往采用的结构亦不相同。
在工程设计中,除尽量选用定型系列产品外,也常按其特定的条件进行设计,以满足工艺上的需要(得到适合工况下最合理最有效也最经济的便于生产制造的换热器等等)。
1前言
1.1概述
1.1.1换热器的类型
管壳式换热器是最典型的间壁式换热器,历史悠久,占据主导作用,主要有壳体、管束、管板、折流挡板和封头等组成。
一种流体在管内流动,其行程称为管程;另一种流体在管外流动,其行程称为壳程。
管束的壁面即为传热面。
其主要优点是单位体积所具有的传热面积大,传热效果好,结构坚固,可选用的结构材料范围宽广,操作弹性大,因此在高温、高压和大型装置上多采用列管式换热器。
为提高壳程流体流速,往往在壳体内安装一定数目与管束相互垂直的折流挡板。
折流挡板不仅可防止流体短路、增加流体流速,还迫使流体按规定路径多次错流通过管束,使湍流程度大为增加。
列管式换热器中,由于两流体的温度不同,使管束和壳体的温度也不相同,因此它们的热膨胀程度也有差别。
若两流体温差较大(50℃以上)时,就可能由于热应力而引起设备的变形,甚至弯曲或破裂,因此必须考虑这种热膨胀的影响。
1.1.2换热器
换热器是化工、石油、食品及其他许多工业部门的通用设备,在生产中占有重要地位。
由于生产规模、物料的性质、传热的要求等各不相同,故换热器的类型也是多种多样。
按用途它可分为加热器、冷却器、冷凝器、蒸发器和再沸器等。
根据冷、热流体热量交换的原理和方式可分为三大类:
混合式、蓄热式、间壁式。
热体,将热量由热流体传给冷流体。
当蓄热体与热流体接触时,从热流体处接受热量,蓄热体温度升高后,再与冷流体接触,将热量传给冷流体,蓄热体温度下降,从而达到换热的目的。
此类换热器结构简单,可耐高温,常用于高温气体热量的回收或冷却。
其缺点是设备的体积庞大,且不能完全避免两种流体的混合。
工业上最常见的换热器是间壁式换热器。
根据结构特点,间壁式换热器可以分为管壳式换热器和紧凑式换热器。
管壳式换热器包括了广泛使用的列管式换热器以及夹套式、套管式、蛇管式等类型的换热器。
其中,列管式换热器被作为一种传统的标准换热设备,在许多工业部门被大量采用。
列管式换热器的特点是结构牢固,能承受高温高压,换热表面清洗方便,制造工艺成熟,选材范围广泛,适应性强及处理能力大等。
这使得它在各种换热设备的竞相发展中得以继续存在下来。
使用最为广泛的列管式换热器把管子按一定方式固定在管板上,而管板则安装在壳体内。
因此,这种换热器也称为管壳式换热器。
常见的列管换热器主要有固定管板式、带膨胀节的固定管板式、浮头式和U形管式等几种类型。
1.2设计的目的与意义
换热器是将热流体的部分热量传递给冷流体的设备,以实现不同温度流体间的热能传递,又称热交换器。
换热器是实现化工生产过程中热量交换和传递不可缺少的设备。
换热设备在炼油、石油化工以及在其他工业中使用广泛,它适用于冷却、冷凝、加热、蒸发和废热回收等各个方面。
其中,管壳式换热器虽然在换热效率、设备的体积和金属材料的消耗量等方面不如其他新型的换热设备,但它具有结构坚固、弹性大、可靠程度高、使用范围广等优点,所以在各工程中仍得到普遍使用。
管壳式换热器的结构设计,是为了保证换热器的质量和运行寿命,必须考虑很多因素,如材料、压力、温度、壁温差、结垢情况、流体性质以及检修与清理等等来选择某一种合适的结构形式。
1.3管壳式换热器的发展史
为了满足电厂对在较高压力下运行的大型换热器(如冷凝器和供水加热器)的需要,在20世纪初,提出了壳管式换热器的基本设计。
经过长期的运用,使设计变得相当成熟和专业化。
壳管式换热器发展的早期阶段,出现的最大量的严重问题,不是在传热方面(这可以由实践经验粗略的估算),而是各种部件,特别是管板材料的强度计算问题,还有在制造技术和工程实施中的许多有关的其他问题,如管和管板的连接,法兰和接头管的焊接等。
在20世纪20年代,壳管式换热器的制造工艺得到相当圆满的发展,这主要是由于几个主要制造商努力的结果。
制造设备的传热面积可达500m2,即直径约750mm、长6m,用于急剧增长的石油工业。
在30年代,壳管式换热器的设计者,根据直接经验和在理想管束上的实验数据,建立了很多正确的设计原则。
水-水和水-气换热器的设计,大概与现今的设计差不多。
因为污垢热阻起很大的作用,壳侧流动的粘性流是一个困难的问题,而且,60年代以前的他们的了解很少。
随着壳管式换热器的应用稳步增长,以及对在各种流程条件下性能预计的精度要求越来越高,这造就40年代直至50年代研究活动的激增。
研究内容不仅包括壳侧流动,而且相当重要的还有真实平均温差的计算、结构件特别是管板的强度计算。
多年来发展起来的壳管式换热器,由于其结构坚固并能适应很大的设计和使用条件的变化,已成为最广泛使用的换热器。
1.7提高管壳式换热器传热能力的措施
管壳式换热器的传热能力是由壳程换热系数、管程换热系数和换热器冷、热介质的对数平温差决定的,因此,提高管壳式换热器传热能力的措施包括以下几点。
1、提高管壳式换热器冷、热介质的平均对数温差
2、合理确定管程和壳程介质
3、采用强化管壳式换热器传热的结构措施
1.8设计思路、方法
1.8.1换热器管形的设计
管子外形有光管、螺纹管。
相同条件下,采用螺纹管管束比光管管束能增加换热面积2倍左右。
同时,由于螺纹管的螺纹结构能有效破坏流体边界层,有效提高了换热器的传热能力。
当壳程介质易结垢时,由于外螺纹管束沿轴向的胀缩作用使换热管外壁的硬垢脱落,具有良好的自洁作用,能够有效防止管束外壁的结垢,减小换热器壳程热阻,提高换热器的传热能力。
1.8.2换热器管径的设计
由于小直径换热管具有单位体积传热面积大,换热器结构紧凑,金属耗量少,传热系数高的特点,在换热器结构设计中,对于管程介质清洁、不易结垢的介质,采用小管径管束能有效增加换热面积。
相同条件下,采用Φ19mm管束比采用Φ25mm管束能提高传热面积30%~40%,节约金属20%以上。
1.8.3换热管排列方式的设计
管子的排列方式有等边三角形、正方形和同心圆排列等,对于壳程介质不易结垢或可用化学方法清洗污垢的介质,采用三角形排列可使换热器的外径减小15%;对于需要机械清洗的管束,管子排列应采用正方形;对于小于300mm的换热器,为使管束排列紧凑,可采用同心圆排列。
1.8.4管、壳程分程设计
管程分程设计。
当需要的传热面积很大,换热管长度太长(对卧式换热器管长比壳径比超过6~10,立式换热器超过4~6时),采用单管程换热器使管程流速很低时,可采用管程分程的办法来提高管程换热介质的流速。
因为决定管程介质的流态的雷诺数Re与管程介质流速成正比,为提高换热器管程换热系数k,可采用管程分程的办法提高管程换热系数。
壳程分程设计。
为了提高换热器传热能力,且不使换热管太长,壳程利用横向折流板或纵向折流板分程。
壳程分程可增加对壳程换热介质的扰动,使壳程换热介质流速增加,流程加大,换热介质横向冲刷扰动加大,提高换热器传热能力。
1.8.5折流板的结构设计
折流板的结构设计包括型式的确定,形状的设计,缺口高度设计和折流板间距设计。
换热器壳程折流板可分为横向折流板和纵向折流板,由于壳程加装纵向折流板在制造工艺上较困难,而且造成壳程压降增加,因此一般采用壳程加装横向折流板。
壳程加装横向折流板后,壳程换热介质雷诺数Re≥100时,壳程介质即达湍流,能有效提高换热器的传热能力,横向折流板常采用弓形和盘-环形,弓形折流板加工、制造和组装较方便,使用最普遍,盘-环形折流板主要用于小型换热器中。
在换热器结构设计中,合理设计折流板间距是保证壳程换热介质的压力降满足设计要求的关键。
1.8.6管、壳程进、出口的设计
管程进、出口管的设计。
管程进、出口管径在考虑管程压降允许的条件下,通过计算确定管径,其计算公式为ρω2<3300(ρ为管程介质密度,kg/m3;ω为管程介质进、出口流速,m/s)。
为保证管程流体的均匀分布,充分发挥换热管的换热性能,管程进、出口应设置在换热器管程的底部和顶部。
对换热器的使用寿命影响较大,特别是壳程换热介质流速较高或介质中含有固体颗粒。
为保证换热器的使用性能,可在壳程入口加装防冲板,对介质冲刷起到缓冲的作用,保护管束不受冲击;为避免壳程入口流速过高,壳程介质流速有一定的限制:
ρω2<2200。
1.9选材方法
1.9.1管壳式换热器的选型
管壳式换热器有三种类型,分别为固定管板式换热器、浮头式换热器、U形管式换热器和填料函式换热器。
1、固定管板式:
固定管板式换热器主要有外壳、管板、管束、封头压盖等部件组成。
固定管
图1-1固定管板式换热器
板式换热器的结构特点是在壳体中设置有管束,管束两端用焊接或胀接的方法将管子固定在管板上,两端管板直接和壳体焊接在一起,壳程的进出口管直接焊在壳体上,管板外圆周和封头法兰用螺栓紧固,管程的进出口管直接和封头焊在一起,管束内根据换热管的长度设置了若干块折流板。
这种换热器管程可以用隔板分成任何程数。
固定管板式换热器结构简单,制造成本低,管程清洗方便,管程可以分成多程,壳程也可以分成双程,规格范围广,故在工程上广泛应用。
壳程清洗困难,对于较脏或有腐蚀性的介质不宜采用。
当膨胀之差较大时,可在壳体上设置膨胀节,以减少因管、壳程温差而产生的热应力。
固定管板式换热器的特点是:
旁路渗流较小;造价低;无内漏。
在相同的壳体直径内,排管较多,比较紧凑;壳侧层清洗困难,加上膨胀节的方法不能照到管子的相对移动。
比较适合温差不大或温差大而壳层压力不高的场合。
固定管板式换热器的缺点是,壳体和管壁的温差较大,易产生温差力,壳程无法清洗,管子腐蚀后连同壳体报废,设备寿命较低,不适用于壳程易结垢场合。
2、浮头式换热器:
其两端管板只有一端与壳体完全固定,另一端课相对于壳体作某些移动,该端称之为浮头。
此种换热器的管束不受壳体的约束,壳体与管束之间不会因为膨胀量的不同而产生热应力。
而且在清洗和检修时,仅将管束从壳体中抽出即可。
图1-2浮头式换热器
特点:
该种换热器结构复杂、笨重,造价比固定管板式要高出约20%,材料的消耗量较大,浮头的端盖在操作中无法检查,所以安装时要特别注意其密封,以免发生内漏,且管束和壳体间隙较大,设计时避免短路。
该种换热器比较适合管壳壁间温差较大,或易于腐蚀和易于结垢的场合。
3、U型管式换热器
仅有一个管板,管子两端均固定于同一管板上。
图1-3U型管式换热器
这类换热器的特点是:
管束可以自由伸缩,不会因为管壳之间的温差而产生热应力,热补偿性能好;管程为双管程,流程较长,流速较高,传热性能好;承压能力强;管束课从壳体内抽出,便于检修和清洗,造价便宜。
但是管内清洗不变,管束中间分布的管子难以更换,管板中心部分布管不紧凑,管子数目不能太多。
仅适用于管壳壁温相差较大,或壳程截止易于结垢而管程介质不易结垢,高温高压腐蚀性强的情形。
4、填料函式换热器
此类换热器的管板也仅有一端与壳体固定,另一端采用填料函密封。
特点为它的管束也可以自由膨胀,所以管壳间不会产生热应力,且管程与壳程都能清洗。
造价较低、加工制造简便,材料消耗较少。
填料密封处于泄露,故壳程压力不能过高,也不宜用于易挥发、易燃、易爆、有毒的场合。
综上可知,换热器的使用场合、使用目的、换热介质物性等因素的不同,决定了管壳式换热器的结构型式。
固定管板式换热器结构简单、紧凑、造价低,每根换热管可以单独清洗和更换,在外形尺寸相同的条件下,与浮头式和U形管式换热器相比,换热面积大。
由于固定管板式换热器的壳程清洗困难和适应热膨胀能力差,决定了固定管板式换热器适用于换热介质清洁,壳程压力不高,换热介质温差不大的场合。
浮头式换热器由于管束的热膨胀不受壳体的约束,而且可拆卸抽出管束,检修更换换热管、清理管束和壳程污垢方便,因此,浮头式换热器应用最广泛,在油田储运集输系统中,60%~70%的换热器为浮头式换热器。
U形管换热器具有良好的密封性能,并具有检修、清洗方便的特点。
对于换热器换热介质工作压力高,管、壳程介质密封要求严的场合,为确保换热器管、壳程的密封,换热器管束的设计一般采用U形管结构的换热器。
1.9.2流径的选择
在具体设计时考虑到尽量提高两侧传热系数较小的一个,使传热面两侧传热系数接近;在运行温度较高的换热器中,应尽量减少热量损失,而对于一些制冷装置,应尽量减少其冷量损失;管、壳程的决定应做到便于清洗除垢和修理,以保证运行的可靠性。
参考标准:
1、不洁净和易结垢的流体宜走便于清洗管子,浮头式换热器壳程便于清洗。
2、腐蚀性的流体宜走管内,以免壳体和管子同时受腐蚀,而且管子也便于清洗和检修。
3、压强高的流体宜走管内,以免壳体受压,其中冷却介质循环水操作压力高,宜走管程。
4、饱和蒸气宜走管间,以便于及时排除冷凝液,且蒸气较洁净,冷凝传热系数与流速关系不大。
5、被冷却的流体宜走壳程,便于散热,增强冷却效果。
6、需要提高流速以增大其对流传热系数的流体宜走管内,因管程流通面积常小于壳程,且可采用多管程以增大流速。
7、粘度大的液体或流量较小的流体,宜走壳程,因流体在有折流挡板的壳程流动时,由于流速和流向的不断改变,在低Re(Re>100)下即可达到湍流,以提高对流传热系数。
8、若两流体的温度差较大,传热膜系数较大的流体宜走壳程,因为壁温接近传热膜系数较大的流体温度,以减小管壁和壳壁的温度差。
综合考虑以上标准,确定半水煤气应走壳程,变换气走管程。
1.9.3材质的选择
管壳式换热器的材料应根据操作压强、温度及流体的腐蚀性等来选用。
在高温下一般材料的机械性能及耐腐蚀性能要下降。
同时具有耐热性、高强度及耐腐蚀性的材料是很少的。
目前常用的金属材料有碳钢、不锈钢、低合金钢、铜和铝等;非金属材料有石墨、聚四氟乙烯和玻璃等。
根据实际需要,可以选择使用不锈钢材料。
1.9.4管程结构
换热管管板上的排列方式有正方形直列、正方形错列、三角形直列、三角形错列和同心圆排列,如下图所示。
(a)正方形直列 (b)正方形错列 (c)三角形直列
(d)三角形错列 (e)同心圆排列
图1-4换热管管板上的排列方式
正三角形排列结构紧凑;正方形排列便于机械清洗。
对于多管程换热器,常采用组合排列方式。
每程内都采用正三角形排列,而在各程之间为了便于安装隔板,采用正方形排列方式。
管板的作用是将受热管束连接在一起,并将管程和壳程的流体分隔开来。
管板与管子的连接可胀接或焊接。
2壳体直径的确定与壳体壁厚的计算
2.1管径
换热器中最常用的管径有φ19mm×2mm和φ25mm×2.5mm。
小直径的管子可以承受更大的压力,而且管壁较薄;同时,对于相同的壳径,可排列较多的管子,因此单位体积的传热面积更大,单位传热面积的金属耗量更少。
所以,在管程结垢不很严重以及允许压力降较高的情况下,采用φ19mm×2mm直径的管子更为合理。
如果管程走的是易结垢的流体,则应常用较大直径的管子。
标准管子的长度常用的有1500mm,2000mm,2500mm,3000m,4500,5000,6000m,7500mm,9000m等。
换热器的换热管长度与公称直径之比一般为4~25,常用的为6~10
由于小直径的管子可以承受更大的压力,而且管壁较薄;同时,对于相同的壳径,可排列较多的管子,因此单位体积的传热面积更大,单位传热面积的金属耗量更少。
所以,在管程半水煤气结垢不很严重以及允许压力降较高的情况下,采用
φ19mm×2mm直径的管子更为合理。
选用Φ19×2的无缝钢管,材质为20号钢,管长4.5m。
强度校核:
Pc=0.7MPa,Do=19mm
φ=1(无缝钢管)取腐蚀余量
故该无缝钢管在0.7MPa压力下满足强度要求。
最大安全使用压力为6.73MPa
2.2管子数n
2.3管子排列方式,管间距的确定
采用正三角形排列,由《化工设备机械基础》表7-4查得层数为11层,查表7-5取管间距a=25mm.
2.4换热器壳体直径的确定
式中
b-正六角形对角线上的管子数,查表7-4,取b=23
l-最外层管子的中心到壁壳边缘的距离,取l=0.5do+10=19.5
查表2-5,圆整后取壳体内径
由于换热器的换热管长度与公称直径之比一般为4~25,常用的为6~10。
故符合范围
2.5换热器壳体壁厚计算及校核
材料选用Q245R钢板,计算壁厚为:
式中:
为计算压力,取
=1.0Mpa;
;
=0.85;[
]t=91Mpa(设壳壁温度为400°C)
将数值代入上述厚度计算公式,可以得知:
查《化工设备机械基础》表4-11取
;
查《化工设备机械基础》表4-9得
3.90+1.2+0.3=5.4mm
查表4-13圆整后取
1.校核水压实验强度
,
则
而
可见
,所以水压试验强度足够
该壳体采用Q245R钢6mm厚的钢板制造。
2、强度校核
设计温度下的计算应力
﹥
最大允许工作压力
故强度足够。
2.6拉杆
立杆的直径与数量,查《化工设备机械基础》表7-10,根据壳体的直径得出。
壳体直径/mm
拉杆直径/mm
拉杆数量/mm
600
10
6
安排拉杆需减少6根,故实际管数n=437-6=431根,材料Q235-AF钢
拉杆螺母为AM108级外径为17.77厚度为4
垫圈为A10-100HV外径为20厚度为2
3换热器封头的选择及校核
上下封头均选用标准椭圆形封头,根据GBT25198-2010《压力容器封头》标准,封头为DN600×6,查曲面高度
,直边高度
,材料选用Q245R钢。
所以,封头的尺寸如下图:
4容器法兰的选择
材料选用12Cr2Mo1根据NBT47023-2012长颈对焊法兰选用DN600,PN1.0Mpa的榫槽密封面长颈对焊法兰。
查法兰尺寸如下表:
表4-1法兰尺寸
所以,选用的法兰尺寸如下图:
图4-1容器法兰
5管板
管板除了与管子和壳体等连接外,还是换热器中的一个重要的受压器件。
5.1管板结构尺寸
查《换热器设计手册》得固定管板式换热器的管板的主要尺寸:
表5-