拨叉的机械加工工艺规程的确定.docx
《拨叉的机械加工工艺规程的确定.docx》由会员分享,可在线阅读,更多相关《拨叉的机械加工工艺规程的确定.docx(6页珍藏版)》请在冰豆网上搜索。
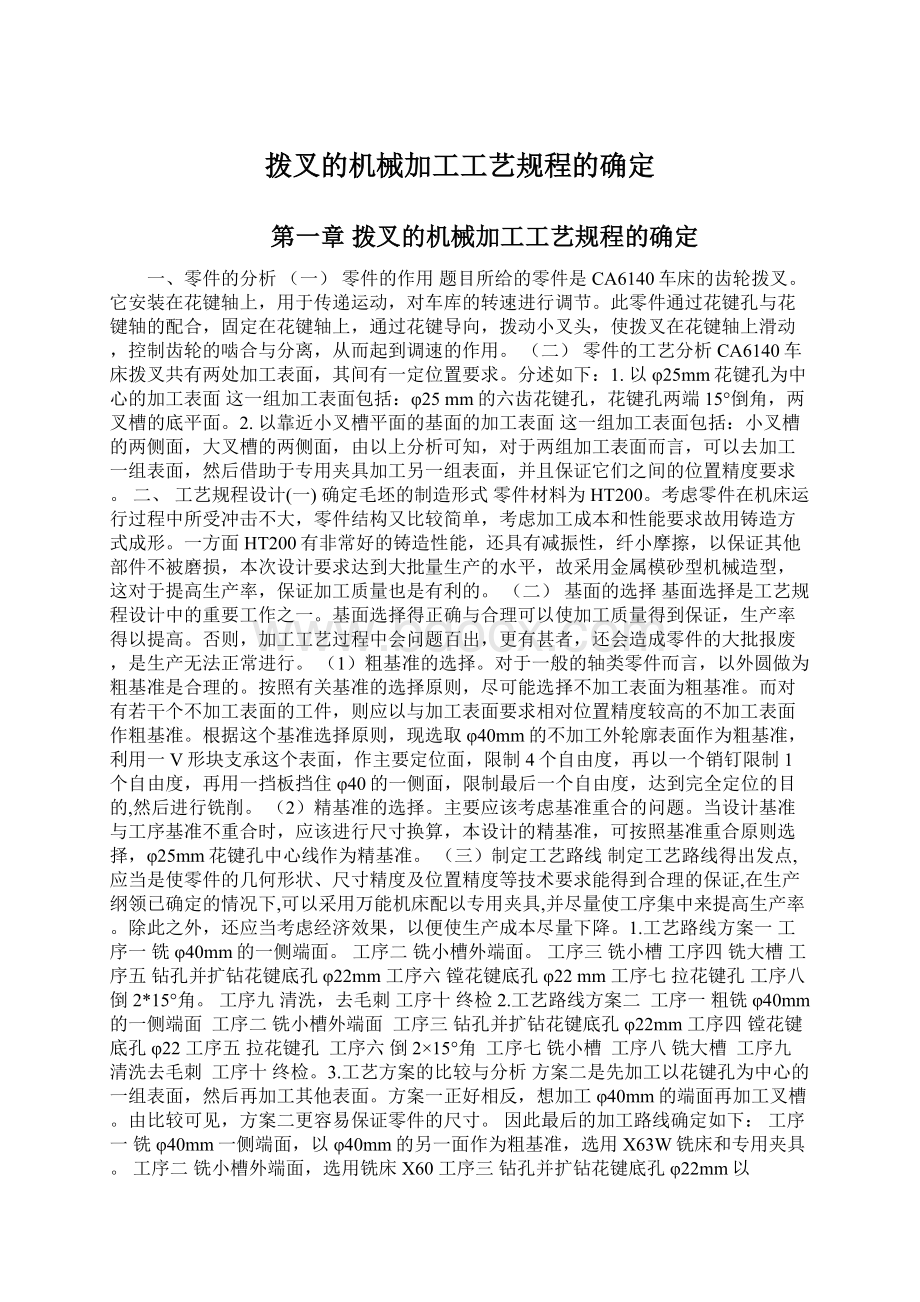
拨叉的机械加工工艺规程的确定
第一章拨叉的机械加工工艺规程的确定
一、零件的分析
(一)零件的作用题目所给的零件是CA6140车床的齿轮拨叉。
它安装在花键轴上,用于传递运动,对车库的转速进行调节。
此零件通过花键孔与花键轴的配合,固定在花键轴上,通过花键导向,拨动小叉头,使拨叉在花键轴上滑动,控制齿轮的啮合与分离,从而起到调速的作用。
(二)零件的工艺分析CA6140车床拨叉共有两处加工表面,其间有一定位置要求。
分述如下:
1.以φ25mm花键孔为中心的加工表面这一组加工表面包括:
φ25mm的六齿花键孔,花键孔两端15°倒角,两叉槽的底平面。
2.以靠近小叉槽平面的基面的加工表面这一组加工表面包括:
小叉槽的两侧面,大叉槽的两侧面,由以上分析可知,对于两组加工表面而言,可以去加工一组表面,然后借助于专用夹具加工另一组表面,并且保证它们之间的位置精度要求。
二、工艺规程设计
(一)确定毛坯的制造形式零件材料为HT200。
考虑零件在机床运行过程中所受冲击不大,零件结构又比较简单,考虑加工成本和性能要求故用铸造方式成形。
一方面HT200有非常好的铸造性能,还具有减振性,纤小摩擦,以保证其他部件不被磨损,本次设计要求达到大批量生产的水平,故采用金属模砂型机械造型,这对于提高生产率,保证加工质量也是有利的。
(二)基面的选择基面选择是工艺规程设计中的重要工作之一。
基面选择得正确与合理可以使加工质量得到保证,生产率得以提高。
否则,加工工艺过程中会问题百出,更有甚者,还会造成零件的大批报废,是生产无法正常进行。
(1)粗基准的选择。
对于一般的轴类零件而言,以外圆做为粗基准是合理的。
按照有关基准的选择原则,尽可能选择不加工表面为粗基准。
而对有若干个不加工表面的工件,则应以与加工表面要求相对位置精度较高的不加工表面作粗基准。
根据这个基准选择原则,现选取φ40mm的不加工外轮廓表面作为粗基准,利用一V形块支承这个表面,作主要定位面,限制4个自由度,再以一个销钉限制1个自由度,再用一挡板挡住φ40的一侧面,限制最后一个自由度,达到完全定位的目的,然后进行铣削。
(2)精基准的选择。
主要应该考虑基准重合的问题。
当设计基准与工序基准不重合时,应该进行尺寸换算,本设计的精基准,可按照基准重合原则选择,φ25mm花键孔中心线作为精基准。
(三)制定工艺路线制定工艺路线得出发点,应当是使零件的几何形状、尺寸精度及位置精度等技术要求能得到合理的保证,在生产纲领已确定的情况下,可以采用万能机床配以专用夹具,并尽量使工序集中来提高生产率。
除此之外,还应当考虑经济效果,以便使生产成本尽量下降。
1.工艺路线方案一工序一铣φ40mm的一侧端面。
工序二铣小槽外端面。
工序三铣小槽工序四铣大槽工序五钻孔并扩钻花键底孔φ22mm工序六镗花键底孔φ22mm工序七拉花键孔工序八倒2*15°角。
工序九清洗,去毛刺工序十终检2.工艺路线方案二工序一粗铣φ40mm的一侧端面工序二铣小槽外端面工序三钻孔并扩钻花键底孔φ22mm工序四镗花键底孔φ22工序五拉花键孔工序六倒2×15°角工序七铣小槽工序八铣大槽工序九清洗去毛刺工序十终检。
3.工艺方案的比较与分析方案二是先加工以花键孔为中心的一组表面,然后再加工其他表面。
方案一正好相反,想加工φ40mm的端面再加工叉槽。
由比较可见,方案二更容易保证零件的尺寸。
因此最后的加工路线确定如下:
工序一铣φ40mm一侧端面,以φ40mm的另一面作为粗基准,选用X63W铣床和专用夹具。
工序二铣小槽外端面,选用铣床X60工序三钻孔并扩钻花键底孔φ22mm以φ40mm的外圆柱面的基准,选用Z525钻床及专用夹具。
工序四镗φ22mm花键底孔,以φ40mm的外圆柱面为基准,选用TT40金刚镗床及专用夹具工序五拉花键孔φ25mm选用L6110。
工序六倒角2*15°双侧。
采用150°锪钻。
工序七铣小槽,以φ22mm内圆柱面为基准,选用铣床X60。
工序八铣大槽以φ22mm内圆柱面为基准,选用铣床X60工序九清洗去毛刺。
工序十终检。
工序改进后,工作效率和加工精度都大大提高了。
以上过程详见机械加工工艺过程综合卡片。
(四)机械加工余量、工序尺寸及毛坯尺寸的确定”CA6140车床拨叉”;零件材料为HT200,硬度190~210HB,毛坯重量1kg,生产件数为4000件,类型大批量,铸造毛坯,采用金属砂型机械造型。
据以上原始资料及加工路线,分别确定各加工表面的机械加工余量、工序尺寸及毛坯尺寸如下:
1.花键孔外端面的加工余量(计算长度为70mm,精度选择IT12,偏差为)①查《工艺手册》表2.2~2.5,CT为8-10取CT为9级。
MA:
G,再查《工艺手册》表2.2-4,加工余量为3.0mm再查《工艺手册》表2.2-1铸件尺寸公差值为2.2mm②粗加工后精铣余量查《工艺手册》表2.3-21为1.0mm铣削公差按加工精度ITB级,因此可知本工序的加工尺寸偏差为:
-0.046mm毛坯名义尺寸:
70+3=73mm毛坯最大尺寸:
73+1.5=74.5mm毛坯最小尺寸:
73-0.7=72.3mm精铣后最大尺寸:
70+1=71mm精铣后最小尺寸:
70-0.3=70.7mm2.花键孔(6-φ25*φ22*φ6)要求花键孔的外径定心,故采用拉削加工。
内孔尺寸为φ22见图样参照《工艺手册》表2.3-9确定孔的加工余量分配:
钻孔:
φ22mm扩钻:
φ21.8mm镗孔:
φ22mm拉花键孔:
6-φ25*φ22*φ6花键孔要求外径定心,拉削时的加工余量参照《工艺手册》表2.3-19取2z=1mm3.小槽端面,要求该面的中心线的距离为27mm,粗糙度值Ra:
3.2,故采用粗铣后精铣,精铣的加工余量为1mm4.小槽:
查《工艺手册》表2.3-22槽长:
40mm,槽宽:
8mm,槽深:
8mm粗铣后半精铣:
2.0mm半精铣后精铣:
0.7mm5.大槽:
查《工艺手册》表2.3-22槽长:
40mm槽宽:
18mm槽深:
23mm工序间余量可查得:
粗铣后半精铣余量:
3.0mm半精铣后精铣余量:
1mm(五)确立切削用量及基本工时工序一:
铣花键孔的一侧端面,保证长度尺寸为70mm。
粗糙度值Ra3.2um参考《切削手册》表3.3,Fz=01.5-0.3切削速度:
参照切削手册确定v=15-21m/min取v=20m/min刀具采用变速钢镶齿三面刃铣刀φ63mm齿数Z=16则:
=先采用X63w铣床,根据机床使用说明书《工艺手册》表4.2-39取=118r/min则实际的切削速度为:
当=118r/min时,工作台每分钟进给量:
查《工艺手册》4.2-39则=75m/min,故直接选用该值。
切削加工时:
查《工艺手册》表6.2-7铣削机动时间的计算公式:
当主偏角Kr<90°时L1=0.5(d-)++(1-2)=7L2=1-3取L2=2mmtm==0.6min精铣时为减少辅助时间,采用相同的机床及转速切深为:
1mm。
切削工时同样为:
0.6min
工序二:
铣小槽外端面,该工序采用花键孔定位,保证长度为27mm
粗糙度值:
Ra=3.2um,参考切削手册表3.3。
Fz=0.25-0.3mm/z,切削速度参照切削手册取:
v=20m/min,刀具采用高速钢三面刃铣刀φ63mm齿数z=16则:
=现采用X63w铣床=118r/min。
故实际的切削速度:
当=118r/min时,工作台进给量fm=75mm/min,切削工时:
tm==0.6min本工序与第一道工序基本相同,有利于提高机床的使用效率,提高生产率。
工序三:
钻孔并扩钻花键底孔1钻孔φ20刀具:
标准麻花钻,圆柱粗锥柄φ20mm零件材料为HT200查手册可得硬度HBS200查表《切削手册》表7.9进给量f=0.13-0.17mm/r根据零件的相关尺寸,本道工序选用机床为Z525再根据机床说明书选取:
f=0.5mm/r切削速度:
根据《切削手册》查得:
v=20m/min所以:
根据Z525钻床的说明书取:
=272r/min故实际的切削速度为:
切削工时:
《工艺手册》表6.2-5钻削机动时间的计算公式tm=由零件的工艺尺寸可知:
l=70mmL1=ctgkr+(1-2)=18mml2=1-4取L2=1mm,tm==0.7min故本工序的机动工时为:
tm=0.7min2扩钻φ21.8mm采用刀具:
φ21.8专用扩孔钻机床仍然选用Z525进给量为:
f=01.3-0.17mm/r机床说明书机床Z525的进给范围0.1-0.81mm/r取f=0.8mm/r机床主轴转速选取n=272r/min切削速度为:
机动工时:
查《工艺手册》表6.2-5钻削机动时间的计算公式:
tm=由零件图可知:
l=70mmL1=ctgkr+1=2.6L2=2-4mm取L2=2mm故切削工时:
tm==0.4min由以上计算可知本工序的机动工时为:
Tm=tm1+tm2=0.7+0.4=1.1min
工序四:
精镗φ22mm花键底孔由于孔的直径比较小,又属于是精加工,故:
选用机床:
T740金刚镗床单边余量为:
z=0.1mm一次镗去全部余量ap=0.1mm进给量f=0.1mm/r根据相关手册,确定金刚镗床的切削速度为v=100m/min
二、由于T740金刚镗床主轴转速为无级调速,故以上转速可以作为加工工时使用的转速。
切削工时:
查《工艺手册》表6.2-1车削和镗削机动时间计算公式:
tm=L=70mmL1=+(2-3)=3mmL2=3mmtm==0.5min工序五:
拉花键孔机床选择:
L6110卧式拉床刀具选择:
矩形齿花键拉刀,拉刀总长760mm单面齿升:
根据有关手册,确定拉花键孔时花键拉刀的单面齿升为0.06mm/s切削工时:
t=式中:
Zb:
单面余量1.5mm(由φ22拉削至φ25)L:
拉削长度:
70mmη:
考虑校准部分的长度系数取1.2k:
考虑机床返回行程系数取k=1.4z:
拉刀同时工作齿数Z=p:
拉刀齿距p=(1.25-1.5)=12mm所以拉刀同时工作齿数Z==6则t==0.14min工序六倒角2*15°双面,采用150°锪钻为缩短辅助时间,取倒角时的主轴转速与扩孔时相同。
机床:
Z525272r/m
手动进给,切削工时较短。
工序七铣小槽该槽的尺寸为:
槽长40mm槽宽槽深8mm加工余量:
粗铣后半精铣2.0mm偏差:
+0.09mm精铣后精铣0.7mm偏差:
+0.03mm1.粗铣小槽机床选择:
X60铣床刀具选择:
高速钢直柄立铣刀d=6mmz=3查《工艺手册》根据X60机床说明书,选择进给量45mm/minF=45mm/min主轴转速选择为1120r/min则实际切削速度为:
切削工时:
查《工艺手册》表6.2-7铣削机动时间的计算公式:
tm=L1=0.5d+2=5mL2=2mtm==1min2.精铣由于是在同一机床进行加工,可选用相同的进给量及主轴转速刀具:
高速钢直柄立铣刀d=8mmz=6所以所用机动工时基本相同t=1min工序八铣大槽槽长40mm槽宽18mm槽深23mm1.粗铣机床:
X63卧式铣床刀具:
细齿直柄立铣刀铣刀直径d=16mmZ=6铣削速度v=20-25m/minf=0.10-0.05mm/齿则:
:
根据机床使用说明书取=375r/min工作台的进给量fm应为:
Fm=fznw=0.1*6*375=225mm/min切削工时:
tm==0.2min2.精铣精铣时由于是在同一机床进行加工,可选用相同的进给量及主轴转速所以tm=0.2min
第二章铣断双体的专用夹具设计为了提高劳动生产率,保证加工质量,降低劳动强度,需要设计加用专用夹具。
经过与老师协商,决定设计第八道工序中——粗铣半精铣,及精铣大槽的铣床夹具。
本夹具将用于X63立式铣床。
刀具为直柄立铣刀。
(一)问题的提出在给定的零件中,对本步加工的定位需要基准孔和平面保证垂直度,定位要求比较高。
因此,本步的重点应在保证垂直度上。
还应考虑如何提高生产率。
(二)夹具设计1.定位基准的选择出于定位简单和快速的考虑,选择∮22mm孔为基准,即以一面上一心轴(自由度限制数:
4)配合以一菱形销(自由度限制数:
1)及支承钉(自由度限制数:
1)使工件完全定位。
再使用钩行压板进行卡紧。
2.切削力和卡紧力计算刀具为直柄立铣刀∮9mm,齿数为4。
F=CF=119,ap=1.5mm,XF=1.0,Fz=0.1mm,yF=0.75,ae=23mm,uF=0.85,d0=9mm,WF=-0.13,Qf=0.73,Z=4取系数K1=1.2,K2=1.2,K3=1.0,K4=1.0。
K=K1K2K3K4=1.44则实际夹紧力为F’=K1*K2*K3*K4*F=1012N由于夹紧力方向和立铣刀的方向一致,不许用太大的夹紧力,因此本夹具安全工作。
3.定位误差分析本工序采用一定位轴,一菱形销,一支承钉定位,工件始终靠近定位轴的一面,菱形销和支承钉平行于夹具体平面达到一定垂直度,定位元件心轴与平面有较高的精度要求,取过盈配合,从而保证定位垂直要求。
4.夹具设计及操作的简要说明夹具的卡紧力大小要求不高,可使用手动夹紧。
使用螺纹螺母和钩形压板进行夹紧,保证效率。
夹具体上有对刀块,可使夹具在一批零件的加工前很好地对刀(与塞尺配合使用),同时,夹具体低面上的一对定位键可使整个夹具在机床工作台上有正确的安装的位置,以便于铣削加工。
结论
伴随这篇毕业论文的收笔,我的毕业设计业近尾声了。
在2013年4月到5月中,我一直为此忙碌着,学习、生活基本都是以此为中心。
收集材料、设计方案、、确定、修改、综合等等,时间过的简单而紧凑。
经过3个月的毕业设计,我的理论知识又一次得到了巩固,同时动手能力也有了很大的提高:
1.运用机械制造工艺及有关课程的知识,结合生产实习中学到的实践知识。
独立地分析和解决工艺问题。
具有设计一些中等零件的能力。
2.能根据被加工零件技术要求,运用夹具设计的基本原理和方法,并学会拟定夹具的设计方案。
3.熟悉与机械有关手册和资源网站,能快速查询并得到所需的数据和信息。
4.大大提高了自己的制图、识图能力。
通过设计,培养了我综合运用理论和专业知识的技能,让我熟悉了一般
机零件的加工工艺过程,具备了设计夹具的能力。
对于本课题而言,我认为自己已经基本达到了设计目的,但是也存在着缺陷与不足。
但即使如此,在我的毕业设计的整个过程中,以上的结果已经令我受益匪浅了。
在这三个月里,我经历很多,得到了许多。
在其中我走过很多的弯路,尝到很多的失败,也经历过设计成功的喜悦。
我想我得到的并不仅仅是书本上的知识,更是一个人工作研究的心境,态度和经验。
我明白了一个大学专科毕业生对待自己的专业,对待自己的工作应该抱着一种什么态度;一个人对待专业知识上的困难,应该如何解决;一个人应该如何面对成功与失败;一个人如何与周围的人交流等等。
对于我来说,这些都是无价的。
我想在这三个月中我努力着,只是为了将自己的想法一点点的实现,虽然回避了一些困难,尽管有些问题直到现在都未能解决,虽然我三个月的成就在专家眼里看来是如此的幼稚,但我感觉到自己值得这样做,这一切已经足够的令我感到欣慰了。
毕业设计的完成,毕业论文的写作对于我来说是第一次,我欧诺个其中学到了很多,这个过程就是一个学习的过程。
再过一些时间,我要踏上工作岗位了,那也是一个长期的学习过程。
我将鼓足勇气。
在自己专业的这条道路上走的更远,走的更加的出色。
致谢
感谢导师刘卫旗工程师的关心、指导和教诲。
刘卫旗工程师追求真理、献身科学、演绎律己、宽己待人的崇高品质对学生将是永远的鞭策。
本人在毕业设计期间都是刘卫旗工程师全面。
具体的指导下进行的。
刘卫旗工程师渊博的知识、敏锐的的思维、明主而严谨的作风,是学生受益匪浅,终生难忘。
感谢我的学友和朋友及老师们的关心和帮助。
参考文献
[1]肖继德、陈宁平主编。
《机床夹具设计》第2板。
机械工业出版社,2007.2
[2]孙丽媛主编。
《机械制造工艺及专用夹具设计指导》。
冶金工业出版社,2001.12
[3]周昌治、扬忠鉴等。
《机械制造工艺学》。
重庆大学出版社,2006.12
[4]李益民主编。
《机械制造工艺设计简明手册》。
机械工业出版社,2004.7