有限元分析软件外文翻译.docx
《有限元分析软件外文翻译.docx》由会员分享,可在线阅读,更多相关《有限元分析软件外文翻译.docx(10页珍藏版)》请在冰豆网上搜索。
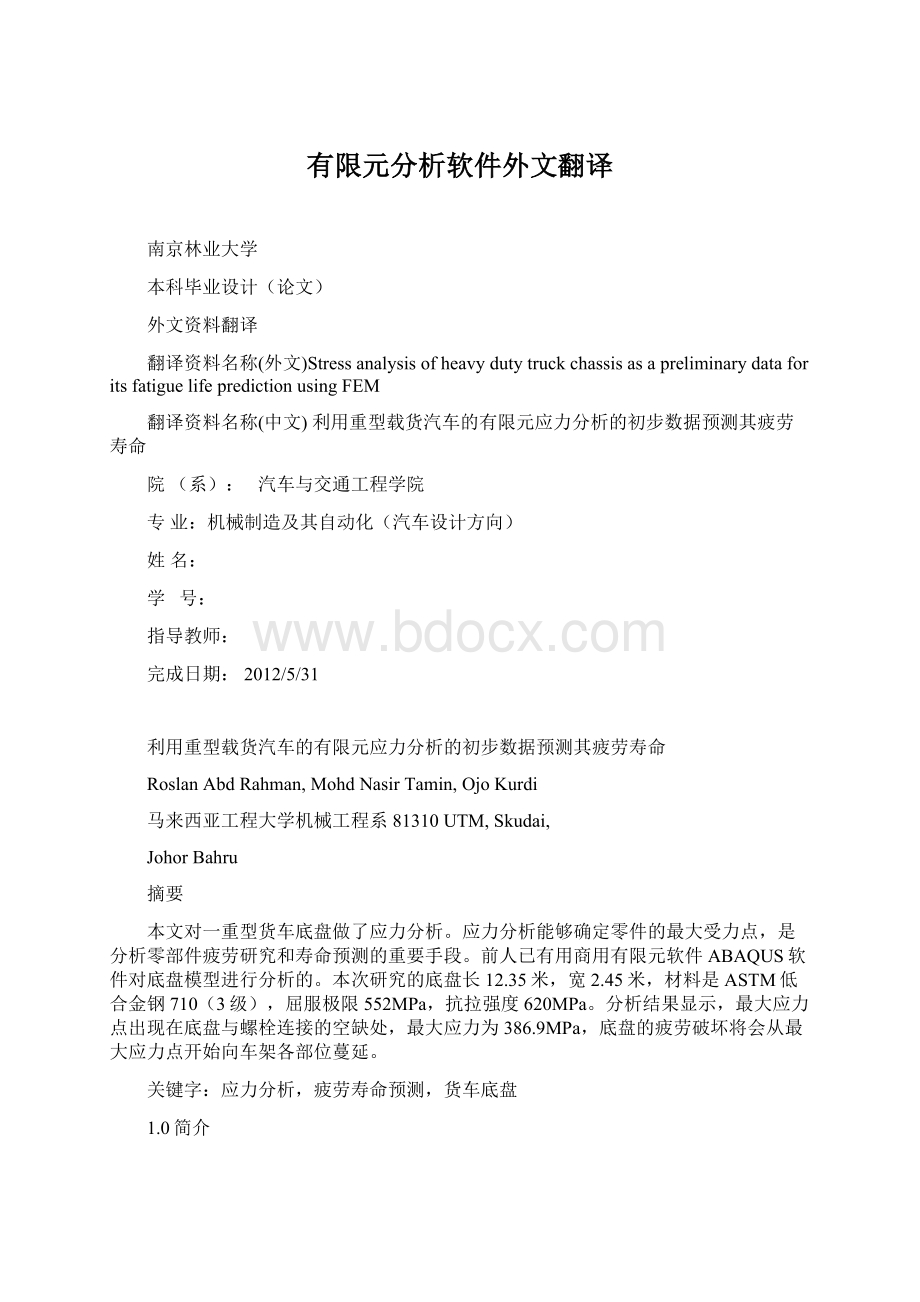
有限元分析软件外文翻译
南京林业大学
本科毕业设计(论文)
外文资料翻译
翻译资料名称(外文)StressanalysisofheavydutytruckchassisasapreliminarydataforitsfatiguelifepredictionusingFEM
翻译资料名称(中文)利用重型载货汽车的有限元应力分析的初步数据预测其疲劳寿命
院(系):
汽车与交通工程学院
专业:
机械制造及其自动化(汽车设计方向)
姓名:
学号:
指导教师:
完成日期:
2012/5/31
利用重型载货汽车的有限元应力分析的初步数据预测其疲劳寿命
RoslanAbdRahman,MohdNasirTamin,OjoKurdi
马来西亚工程大学机械工程系81310UTM,Skudai,
JohorBahru
摘要
本文对一重型货车底盘做了应力分析。
应力分析能够确定零件的最大受力点,是分析零部件疲劳研究和寿命预测的重要手段。
前人已有用商用有限元软件ABAQUS软件对底盘模型进行分析的。
本次研究的底盘长12.35米,宽2.45米,材料是ASTM低合金钢710(3级),屈服极限552MPa,抗拉强度620MPa。
分析结果显示,最大应力点出现在底盘与螺栓连接的空缺处,最大应力为386.9MPa,底盘的疲劳破坏将会从最大应力点开始向车架各部位蔓延。
关键字:
应力分析,疲劳寿命预测,货车底盘
1.0简介
在马来西亚,很多货车的车架寿命都有20多年,20多年架就会有使用安全的问题。
因此,为了确保底盘在工作期间的安全性能,就有必要对底盘作疲劳研究和寿命预测。
利用有限元法作应力分析能够确定受最大应力的关键点,这个关键点是导致底盘疲劳损伤的因素之一。
应力的大小能够预测底盘的寿命,所以可以根据应力分析的结果精确地预测底盘的寿命,应力分析越精确,底盘寿命预测的越合理。
本文是用商用有限元软件ABAQUS软件完成底盘应力分析的。
汽车工业(汽车总成及各部件)在马来西亚的工业中占据非常重要的地位。
随着东盟自由贸易区的贸易自由化发展,当地的汽车制造商和供应商应该顺应汽车及其零部件的世界级标准要求,比如噪声和振动就有相应的标准。
马来西亚的汽车工业主要是依赖于国外的技术,而底盘是实现汽车轻量化的关键结构,所以底盘大多从国外进口。
为了改变这种趋势,有必要建立发展马来西亚自己的底盘设计产业,这是对底盘进行研究的目标。
底盘车架是汽车的装配基体和承载基体,支承着汽车的各个总成及零部件,如车轴,悬架系统,传动系,驾驶室及拖挂部件等,并将它们整合成一部完整的汽车。
货车的底盘经常受到静载荷,动载荷以及周期性载荷。
静载荷主要是车厢质量、货物及乘客,底盘的动载荷是由于货车的运动产生的,而发动机的振动和路面的不平整将会产生周期载荷。
现有的底盘设计通常是基于静载荷的分析,设计的重点是底盘的强度结构设计,以支承施加在底盘上的载荷。
然而货车底盘的受力复杂,包括静载、动载和疲劳破坏方面。
据估计,85%到90%的货车底盘的结构破坏是由疲劳破坏引起的[1]。
因此,货车底盘的动态和疲劳分析是很重要的。
为了获得底盘的动态和疲劳工况的情况,就要确定各个零部件,如发动机、悬架、变速器等的支承点,并对其优化。
许多研究人员都曾研究过货车底盘。
KaraogluandKuralay曾用铆接的连接方式对底盘所有限元应力分析[2]。
研究数据表明,局部增大纵梁的厚度可以减小边梁的应力,如果不能增大变量的厚度,增加接触面的面积也可以减小应力。
Fermeretal用高级疲劳分析软件MSC/Fatigue软件对沃尔沃双燃料车S10做了疲劳寿命分析[3],ConleandChu对复杂的底盘结构的疲劳分析和局部的应力应变分布做了研究[4],Ferreiraetal研究了汽车零部件耐久性的结构优化问题[5],FermérandSvensson研究了工业上焊接的汽车结构的铁基寿命预测问题[6]。
Filhoet.al.考虑到小规模生产的经济可行性,结合适当的动载荷和结构特性对一越野车底盘做了设计分析和优化设计[7]。
研究表明,增大底盘的抗扭刚度,维持车架重心位置不变可以用来优化越野车结构,这样,底盘车架结构的总质量得到优化,结构也跟简单,生产成本也少了。
Cosmeetal利用计算机辅助设计和工程软件代码Pro/E,ADAMSandANSYS模拟了改变设计对货车车架的影响[8]。
Chiewanichakornetal用试验得到的有限元模型,将已破坏的混凝土桥面替换为FRP钢板,分析了桁架桥[9]。
结果数据表明,修复过后,桥的疲劳寿命是修复前钢筋混凝土桥面的两倍,在货车交通研究数据的基础上,桥面载荷及ERP钢板系统的应力范围在无限疲劳寿命范围中,即在其使用期间不会有桁架和地板系统的疲劳破坏现象。
Ye和Moan已经用有限元分析法分析了铝制框加强筋的车架静态和疲劳特性[10],改变车架切割形状和相应的焊接过程,同时得到足够的疲劳强度,这样就能够减小制造成本,并且解决连接问题。
利用铁的疲劳可以确定可能产生疲劳裂纹的关键点,并能预测门铰链系统的寿命[11]。
本次研究中,对重型载货汽车施加静载荷,对其做应力分析,确定产生疲劳裂纹的危险点位置,以此作为该车架的疲劳寿命预测的备用数据。
2.0货车车架的有限元分析
2.1有限元法基本概念
有限元分析法是一种计算机辅助技术,用来获得工程中边值问题的近似解。
简言之,边值问题是一个数学问题,其中一个或是多个应变量必须要满足一个自变量范围已知的微分方程,还要满足特定的边界条件[12]。
有限元法的通俗解释是将一个结构离散成无数个单元(结构碎片),用简单的方法描述每个单元,然后用节点加各个单元重新连接起来,就像这些点是针脚或者点滴粘贴在一起形成各个单元(如图1所示)。
这样就会产生一系列的同步代数方程。
在分析应力时,这些方程式是节点的平衡方程,这样就会有数百甚至数千个这种方程,那么电脑的硬件要求就较高[13]。
图1二维轮齿的网格,所有的节点和单元都在纸平面内
2.2有限元法一般步骤
有限元法可以分析一些物理问题,包括结构分析、流体分析、热传递和其他问题,分析这些问题有些通用的步骤,这些步骤通常包括一些商用有限元分析软件。
主要有三大步骤,即前处理模块、求解模块和后处理模块。
前处理模块要建立模型,这是必要的,如果发生了错误,就不会有完美的计算机有限元求解结果。
这一步骤包括:
定义问题的几何域,所需的单元类型,单元的材料属性,单元的几何性质(长度、面积等等),单元的连通性(网格划分),物理约束(边界条件)和加载。
接下来就是求解,在这一步骤中,以矩阵方式列出的控制代数方程和未知的主变量是合成的,用计算结果回带求得其他派生变量,如反应力,单元应力和热流量。
这一步骤要进行矩阵计算,数值积分,方程求解,这些都是由软件自动解决的。
最后是后处理模块,对结果进行分析和评估。
在这一部中,可以完成的操作包括按单元应力的大小分类,检查平衡,计算安全因素,绘制结构的变形形状,以动画的形式显示模型,以不同的颜色显示温度的分布。
大型软件都会有一个前处理模块和后处理模块来完成分析,这两个模块都可以和其他的软件相同。
前期处理和后期处理根据不同的项目会有各自的程序。
2.3货车的定义和分类
货车是一种重型机动车辆,是用来承载货物的。
货车的另一种定义是用来牵引的激动车辆。
对货车的其他定义将根据货车的类型变化,例如自动倾卸卡车的货物可以作清空处理,车前端的平台末端就可以有空气作用被升起,此时载荷通过重力施加。
房车或拖车有两种分类,一种是根据重量分类,由美国政府定的从1级到8级,如表1和表2所示;第二种是更为广泛的分类:
轻型载重汽车;中型载重汽车和重型载重汽车。
表1货车分类及等级
重量等级
最小总质量额定值/磅
最大总质量额定值/磅
VIUS分类
一般分类
1级
6000
轻型
轻型
2级
6001
10000
轻型
轻型
3级
10001
14000
中型
轻型
4级
14001
16000
中型
中型
5级
16001
19500
中型
中型
6级
19501
26000
轻型-重型
中型
7级
26001
33000
重型-重型
重型
8级
33001
重型-重型
重型
表2制造商的货车分类
分类
等级
总质量额定值
参考车型
轻型
1
0-27kN(0-6000磅)
卡车,救护车,运钞车
2
27-45kN(6001-10000磅)
3
45-62kN(10001-14000磅)
中型
4
62-71kN(14001-16000磅)
市运货车,饮料运货车,拖吊车,校车
5
71-87kN(16001-19500磅)
6
87-116kN(19501-26000磅)
7
116-147kN(26001-33000磅)
重型
8
147kN及以上(33000磅及以上)
卡车拖拉机,水泥搅拌车,自动倾卸卡车,消防车,城市公交客车
注:
总质量额定值:
制造商指定的质量作为一辆车的最大装载质量(货车加货物)。
2.4货车车架模型
该模型如图2所示。
模型长12.35m,宽2,45m,材料为ASTM低合金钢710(3级),屈服极限552MPa,抗拉强度620MPa。
车架的其他属性见表3。
表3货车车架的材料属性
弹性模量E(Pa)
密度ρ(kg/m3)
泊松比
屈服极限(MPa)
抗拉强度(MPa)
207×109
7800
0.3
550
620
图2货车底盘模型
2.5加载
货车模型承受来自车身和货物的静载荷,该车的最大装载质量为36000kg,假设由最大载质量求得一个总的压力,将这个压力平均的分配到货物和底盘上表面的接触面上,具体的加载如图3所示,底盘上表面的压强为67564.6N/m2。
图3静载荷(压强为67564.6N/m2)
2.6边界条件
本模型有3个边界条件。
第一个施加在底盘前端,第二和第三个边界条件在底盘的后端,如图4所示。
第一个边界条件是固定的(约束有轴的平移自由度,释放所有轴的旋转自由度),底盘与驾驶室的接触条件如图5(a)所示。
车架与车轴间由弹簧连接,将货物和底盘的重量传递到车轴上,所以第二个边界条件施加在底盘与弹簧上端连接的地方。
第二个边界条件如图5所示,平移自由度只约束在轴2上,所有轴的旋转自由度都释放。
第三个边界条件施加在底盘孔的内表面和螺栓的外表面的接触面处,在ABAQUS软件中,这种接触是相互作用的,本文中的相互作用是面与面之间的摩擦作用。
此时,螺栓所在的轴的平移自由度和旋转自由度都为零,称为固定约束。
假定螺栓都是刚性元件,故螺栓选用杨氏模量很高的材料。
图4模型的约束
图5实物的约束
注:
a——第一个边界条件,b、c——第二个边界条件,d——第三个边界条件
3.0分析结果及讨论
在等效应力云图中,最大应力点在底盘开孔的地方,即与螺栓接触的地方,如图6所示,最大应力为386.9MPa,最大应力点在86104单元和16045节点上。
底盘开孔处的内表面与非常坚硬的螺栓接触。
第三个边界条件也是固定约束,因此会产生一个很大的应力。
基于静态安全系数理论,取安全系数为1.43,由安全系数公式得:
安全系数=极限应力/许用应力
(1)
图6等效应力云图及最大应力点
Vidosic建议根据结构的载荷和材料选取一些安全系数,对于一些常用的材料,当载荷很容易确定时,安全系数可以取1.5到2。
基于分析结果,为了得到底盘精确的安全系数值,有必要减小最大应力值,因此对底盘结构进行修改以提高安全系数,尤其是在临界点区。
底盘的位移和最大位移点如图7所示,最大位移为4.995mm,位于底盘中部,最大的偏转在第一个边界条件和第二个边界条件的中部。
为了验证分析结果,最大应力发生在第一个边界条件和第二个边界条件之间,这一部分可以近似的简化为一维的简支梁结构,在其中点施加集中力载荷,用施加在中点的集中力代替均匀分布在梁上的压力,这一力的大小等于压强的大小乘以受到压力的所有面的面积,求得结果与分析结果近似。
计算求得的结果表明,这个简支梁的应变点在梁的中部,大小为:
(2)
图7应变分布云图及最大应变点位置
模拟结果的最大应变值为4.99mm,比数值分析计算结果大11.2%。
4.0结论
从数值分析可以看出,应力关键点出现在与螺栓连接的底盘孔处,最大应力值是很重要的,因为安全系数低于推荐值。
由于疲劳破坏是从最大应力点开始的,可以断定,这一关键点是一些破坏的起源。
因此,要注意减少这一点上的应力值,这是很重要的。
分析得到的最大挠度的位置与受均布载荷的简支梁的最大变形位置一致。
参考文献
[1]MSC.Fatigue,2003.[Encyclopedia].LosAngeles(CA,USA):
MacNeal,SchwendlerCorporation.
[2]Karaoglu,C.andKuralay,N.S.,2000.StressAnalysisofaTruckChassiswithRivetedJoints,ElsevierSciencePublishersB.V.Amsterdam,theNetherlands,Vol.38,1115-1130.
[3]Fermer,M.,McInally,G.andSandin,G.,1999.FatigueLifeAnalysisofVolvoS80Bi-FuelusingMSC/Fatigue,WorldwideMSCAutomotiveConference,Germany.
[4]Conle,F.A.andChu,C.C.,1997.FatigueAnalysisandtheLocalStress-strainApproachinComplexVehicularStructures,InternationalJournalofFatigue.
[5]Ferreira,W.G.,Martins,F.,Kameoka,S.,Salloum,A.S.andKaeya,J.T.,2003.StructuralOptimizationofAutomotiveComponentsAppliedtoDurabilityProblems,SAETechnicalPapers.
[6]Fermér,M.andSvensson,H.,2001.IndustrialExperiencesofFE-basedFatigueLifePredictionsofWeldedAutomotiveStructures,Fatigue&FractureofEngineeringMaterialsandStructures24(7),2001,489-500.
[7]Filho,R.R.P.,Rezende,J.C.C.,Leal,M.deF.,Borges,J.A.F.,2003.AutomotiveFrameOptimization,12thInternationalMobility
[8]Cosme,C.,Ghasemi,A.andGandevia,J.,1999.ApplicationofComputerAidedEngineeringintheDesignofHeavy–DutyTruckFrames,InternationalTruck&BusMeeting&Exposition,Detroit,Michigan,November15–17.
[9]Chiewanichakorn,M.,Aref,A.J.,Allampalli,S.,2007.DynamicandFatigueResponseofaTrussBridgewithFiberReinforcedPolymerDeck,InternationalJournalofFatigue,29,1475–1489.
[10]Ye,N.andMoan,T.,2007.StaticandFatigueAnalysisofThreeTypesofAluminiumBox-Stiffener/WebFrameConnections,InternationalJournalofFatigue,29,1426–1433.
[11]Bekah,S.,2004.FatigueLifePredictioninaDoorHingeSystemUnderUni-AxialandMultiaxialLoadingCondition,MasterThesis,RyersonUniversity,Toronto,Ontario,Canada.
[12]Hutton,David,V.,2004.FundamentalofFiniteElementAnalysis,McGrawHill,NewYork.
[13]Cook,Robert,D.,1995.FiniteElementModelingforStressAnalysis,JohnWilley&Sons,Inc,NewYork.
[14]Juvinall,R.C.andMarshek,K.M.,2006.FundamentalMachineComponentDesign,JohnWilley&Son,Inc.,USA.
[15]Vidosic,J.P.,1957.MachineDesignProject,RonaldPress,NewYork.