基于AMESim的负荷传感与LUDV液压系统的仿真研究解读.docx
《基于AMESim的负荷传感与LUDV液压系统的仿真研究解读.docx》由会员分享,可在线阅读,更多相关《基于AMESim的负荷传感与LUDV液压系统的仿真研究解读.docx(7页珍藏版)》请在冰豆网上搜索。
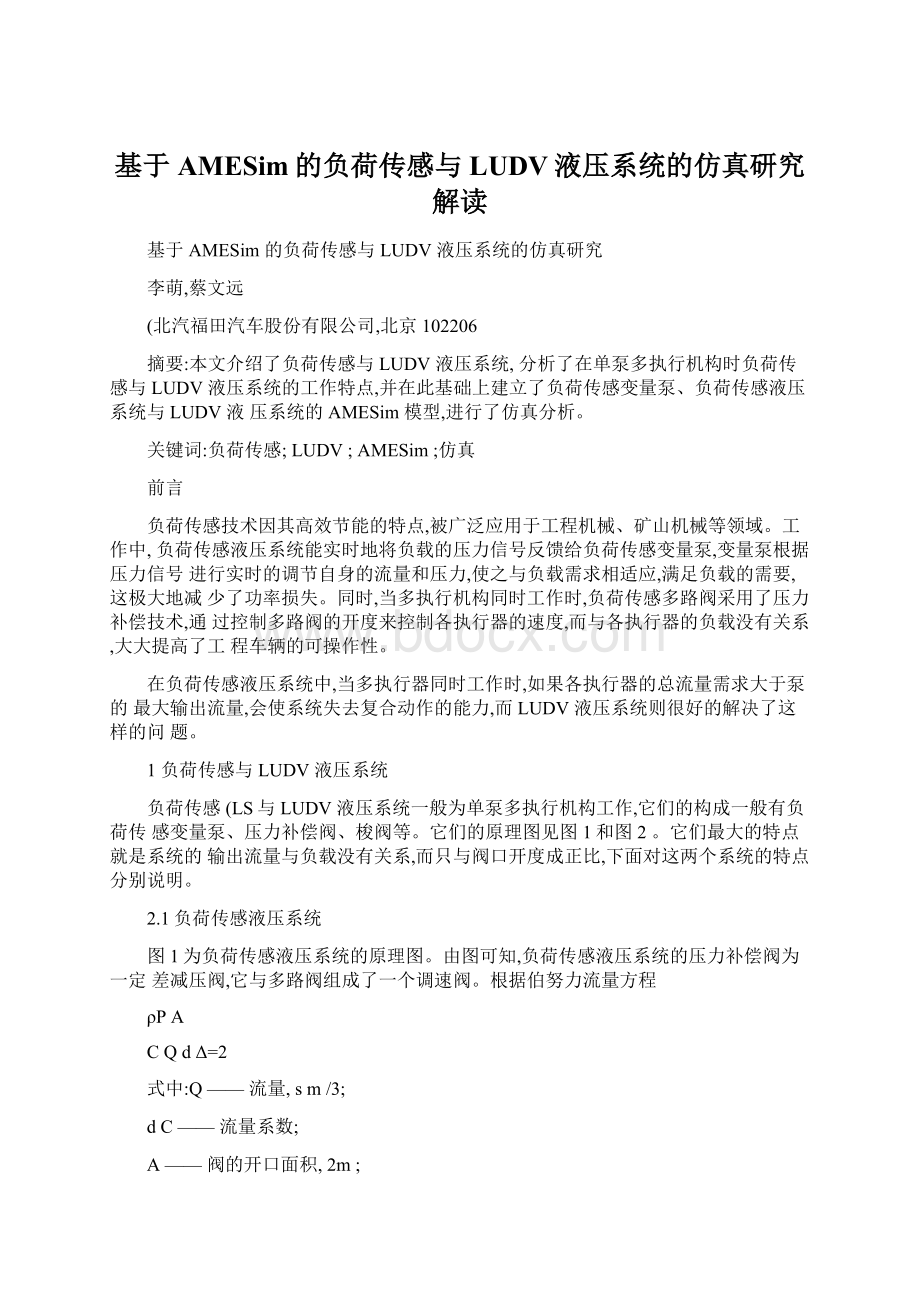
基于AMESim的负荷传感与LUDV液压系统的仿真研究解读
基于AMESim的负荷传感与LUDV液压系统的仿真研究
李萌,蔡文远
(北汽福田汽车股份有限公司,北京102206
摘要:
本文介绍了负荷传感与LUDV液压系统,分析了在单泵多执行机构时负荷传感与LUDV液压系统的工作特点,并在此基础上建立了负荷传感变量泵、负荷传感液压系统与LUDV液压系统的AMESim模型,进行了仿真分析。
关键词:
负荷传感;LUDV;AMESim;仿真
前言
负荷传感技术因其高效节能的特点,被广泛应用于工程机械、矿山机械等领域。
工作中,负荷传感液压系统能实时地将负载的压力信号反馈给负荷传感变量泵,变量泵根据压力信号进行实时的调节自身的流量和压力,使之与负载需求相适应,满足负载的需要,这极大地减少了功率损失。
同时,当多执行机构同时工作时,负荷传感多路阀采用了压力补偿技术,通过控制多路阀的开度来控制各执行器的速度,而与各执行器的负载没有关系,大大提高了工程车辆的可操作性。
在负荷传感液压系统中,当多执行器同时工作时,如果各执行器的总流量需求大于泵的最大输出流量,会使系统失去复合动作的能力,而LUDV液压系统则很好的解决了这样的问题。
1负荷传感与LUDV液压系统
负荷传感(LS与LUDV液压系统一般为单泵多执行机构工作,它们的构成一般有负荷传感变量泵、压力补偿阀、梭阀等。
它们的原理图见图1和图2。
它们最大的特点就是系统的输出流量与负载没有关系,而只与阀口开度成正比,下面对这两个系统的特点分别说明。
2.1负荷传感液压系统
图1为负荷传感液压系统的原理图。
由图可知,负荷传感液压系统的压力补偿阀为一定差减压阀,它与多路阀组成了一个调速阀。
根据伯努力流量方程
ρPA
CQdΔ=2
式中:
Q——流量,sm/3;
dC——流量系数;
A——阀的开口面积,2m;
PΔ——多路阀口前后压差,Pa;
ρ——液体密度,3/mKg。
由公式可知,系统的ρ和dC一般为定值,那么流量只与A和PΔ有关。
如果PΔ为一定植,则系统流量Q与阀的开口面积A成正比,阀口开度增大,流量增大,阀口开度减小,流量减小,与负载没有关系。
由原理图可知,PΔ其实就是压力补偿阀设定的压力,为一定值。
这样系统的流量只与阀口的开度大小成正比,而与负载无关。
通过对系统原理图的分析还可以得知,如果工作系统需求的流量超过泵供油能力的极限时,最高负荷回路上的执行元件速度会迅速降低甚至停止,压力油大部分或全部流向低负载执行机构,从而使工作机构失去复合动作的协调能力。
2.2LUDV液压系统
图1LS液压系统原理图图2LUDV液压系统原理图负荷传感变量泵
压力补偿器多路阀开口
梭阀
负荷传感变量泵
压力补偿器多路阀开口
梭阀
从上面系统的原理图可知,负荷传感液压系统是阀前压力补偿,LUDV液压系统是阀后压力补偿,负荷传感液压系统的压力补偿阀是基于定差减压阀,而LUDV液压系统的压力补偿是基于比例溢流阀。
LUDV液压系统中,根据压力补偿阀的受力平衡可以得到如下的关系式:
moPPP+′=
式中:
oP——多路阀出口压力,Pa;
P′——压力补偿阀弹簧的设定产生的开启压力,Pa;
mP——梭阀输出的最高压力,Pa。
则多路阀的前后压差opPPP−=Δ
式中pP——泵的出口压力,Pa。
根据负荷传感泵的特点可知
lsmpPPPΔ+=
式中lsPΔ——变量泵中负荷敏感阀的压力设定值,Pa。
则PPPls′−Δ=Δ
由于lsPΔ和P′都是定值,则多路阀的前后压差PΔ为定值。
这种控制形式与泵的流量饱和与否没有关系,流向各支路执行器的流量只与其控制阀的开口度成正比。
如果泵能提供的最大流量小于各执行器需求流量的总和,则流向各支路的流量以泵的最大流量为基础,按照各支路控制阀的开口度成正比例分配,不会使各执行机构失去复合动作的协调能力。
3AMESim系统建模与仿真
AMESim(AdvancedModelingandSimulationEnvironmentforSystemsEngineering是世界著名的工程系统高级建模与仿真平台,它提供了一个系统级工程设计的完整平台,使得用户可以在单一的平台上建立复杂的一维多学科领域的机电液一体化系统模型,并在此基础上进行仿真计算和深入的分析。
AMESim采用物理模型的图形化建模方式,软件中提供了丰富的应用元件库,用户可以采用基本元素法按照实际物理系统来构建自定义模块或仿真模型,
从而使用户从繁琐的数学建模中解放出来,而将更多的精力投入到实际物理模型
本身的研究。
其应用领域包括:
燃料喷射系统;悬挂系统;车辆动力学;制动系
统;润滑系统;动力操纵系统;冷却系统;传动系统;变量阀压力脉动;液压元
件;阀/管路;系统控制;液压回路;机械系统等。
AMESim有40多个应用库,本文应用了其中的液压库、HCD库、机械库、信号库等建立了系统的模型,并进行了仿真分析。
3.1负荷传感变量泵建模与仿真
根据负荷传感变量泵原理图,搭建了变量泵的模型,并设置模型各个模块相应的参数,使负荷传感变量泵的基本参数为:
排量为100rcm/3,LSPΔ为24bar,容积效率η为0.98,切断压力为254bar。
如下图3为负荷传感变量泵的AMESim模型。
AMESim有一个超级元件(supercomponent的功能,可以把复杂的系统封装,用一个简单的图标来代替,图标放在自己定义的应用库中,可以方便的取用。
图4便为封装后的变量泵模型,简单直观。
搭建如下图5简单的系统,验证变量泵的模型的正确性。
下列系统各元件的基本参数为:
电机转速2000r/min,变量节流口直径为8mm,控制信号10s使节流口面积从最大变为0,10s到15s保持0;节流口的直径4设置为5mm。
仿真时间为15s,通讯间隔为0.01s。
泵输出流量的仿真结果见图6。
节流口两端的压差24bar,见图7。
经分析,仿真结果与预期一致,变量泵模型正确。
图3变量泵模型图4封装后变量泵模型
3.2负荷传感与LUDV液压系统建模与仿真
根据原理图搭建负荷传感与LUDV液压系统的AMESim模型,见图8和图9。
对于负荷传感液压系统,设置参数如下:
可变节流阀1和可变节流阀2的最大通径为5mm;控制信号1在0—1秒内的值为0.5,1—5秒内的值为1;控制信号2在0—1秒的值为0,1—3秒为0.8,3—5秒为1;压力补偿阀1和压力补偿阀2的P
Δ为10bar;负载1为100000N,负载2为300000N;流量系数0.7;仿真时间5秒,通讯间隔0.01秒。
现在计算一下在两个节流阀都完全打开的情况下,系统能正常工作的饱和流量是多大,按此可以计算出给系统提供饱和流量时,泵的最低转速。
据公式
ρP
ACQdΔ
=2
图5图6流量曲线图7节流阀口前后压力
按照给定的已知条件可得Q=80L/min,则泵的转速为ω=80≈817r/min。
100*10−3*0.98把电机的转速分别设为1500r/min、500r/min、100r/min,做三次仿真,分析结果。
对于LUDV液压系统,设置压力补偿的相关参数,使节流阀前后的压差ΔP为10bar,与负荷传感液压系统一致,其余参数设置与负荷传感液压系统的参数设置一致,进行仿真分析,其结果与负荷传感液压系统相比较,进行分析。
负载1负载2节流阀1控制信号1节流阀2控制信号2压力补偿阀1压力补偿阀2图8LS液压系统仿真模型负载1负载2压力补偿阀2压力补偿阀1节流阀1控制信号1节流阀2控制信号2图9LUDV液压系统仿真模型-6-
仿真结果见图10~图13。
图10负荷传感液压系统节流阀1的流量图11负荷传感液压系统节流阀2的流量图12LUDV液压系统节流阀1的流量图13LUDV液压系统节流阀2的流量下面对仿真结果进行分析。
当电机转速为1500r/min时,变量泵能提供足够的流量,负荷传感液压系统与LUDV液压系统的两个支路的节流口的流量在仿真的三个阶段的数值见下表:
表11500r/min时,负荷传感系统仿真结果0—1s节流口1流量(L/min)节流口2流量(L/min)1—3s40323—5s4039.9200-7-
表21500r/min时,LUDV系统仿真结果0—1s节流口1流量(L/min)节流口2流量(L/min)1—3s39.531.53—5s39.439.2200从表中看到,当流量足够时,负荷传感液压系统与LUDV液压系统基本没有什么区别,且通过节流口的流量与节流口的开度大小成正比。
当电机转速为500r/min时,负荷传感液压系统与LUDV液压系统的两个支路的节流口的流量在仿真的三个阶段的数值见下表:
表3500r/min时,负荷传感系统仿真结果0—1s节流口1流量(L/min)节流口2流量(L/min)表41—3s4093—5s409200500r/min时,LUDV系统仿真结果0—1s节流口1流量(L/min)节流口2流量(L/min)1—3s27.321.73—5s24.624.419.80电机转速500r/min时,当两节流阀同时开到最大时,泵提供的流量已不能满足系统需要,由于负荷传感系统支路1的负载小于支路2的负载,所以流量优先得到满足。
而同样条件的LUDV液压系统,流过节流口1和节流口2的流量仍然与它们的开口度的大小成正比,与负载没有关系。
当电机转速为100r/min时,泵提供的流量严重不足,由图11可知,负荷传感液压支路2的流量几乎为零,液压油全部流向低负载的支路1。
而LUDV液压系统的流量依然按照各支路节流口开度大小进行正比例分配。
4结论本文介绍了负荷传感液压系统以及LUDV液压系统,分析了它们的共同点以及区别,LUDV液压系统是与负载压力无关的流量分配系统,在单泵多执行机构系统中,各支路的流量分配除了与各支路的负载压力无关外,还与泵所能提供的最大流量没有关系,只与控制各支路的多路阀的开度有关,这样在多执行机构进行复合动作时,不会因为泵的流量不足而失去复合动作的协调能力。
本文简要介绍了AMESim的功能,建立了负荷传感泵、负荷传感液压系统、LUDV液压-8-
系统的AMESim模型,对负荷传感泵进行了超级模块封装,并对系统模型进行了仿真。
通过对仿真结果的详细分析,验证了负荷传感变量泵、负荷传感液压系统、LUDV液压系统的特点。
参考文献:
1.张海涛,何清华等.LUDV负荷传感系统在液压挖掘机上的应用.建筑机械,(10)2004.谢英俊.多执行器负载敏感系统的分流控制发展综述.机床与液压,(3)2001.2.顾临怡,3.张新海,何清华等.挖掘机负荷传感液压系统中的压力补偿,工程机械,2005(7).祁晓野.AEMSim系统建模和仿真—从入门到精通.北京航空航天大学出版社.4.付永领,2006.-9-