AD15数控车床Z向进给系统的开发与设计.docx
《AD15数控车床Z向进给系统的开发与设计.docx》由会员分享,可在线阅读,更多相关《AD15数控车床Z向进给系统的开发与设计.docx(19页珍藏版)》请在冰豆网上搜索。
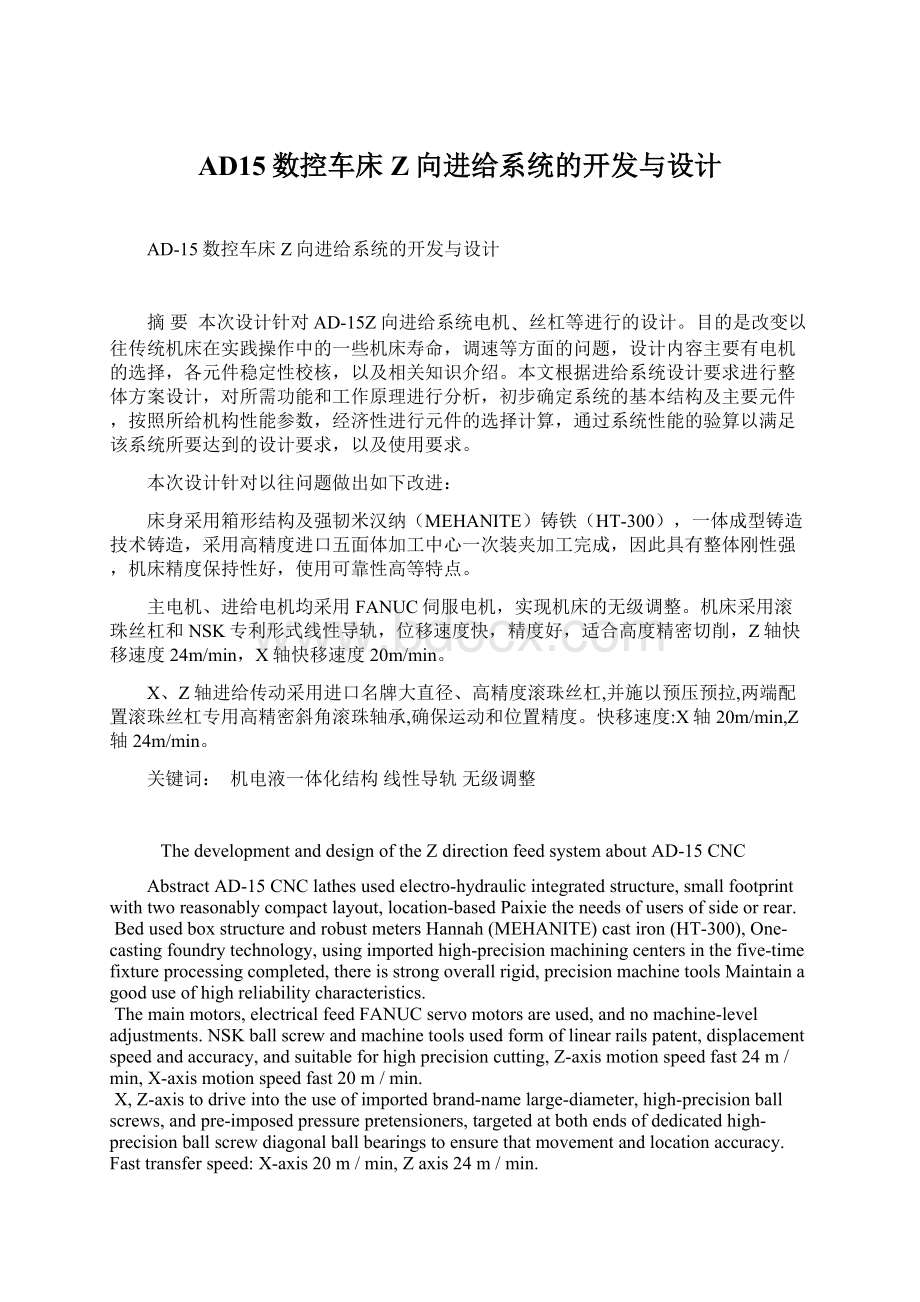
AD15数控车床Z向进给系统的开发与设计
AD-15数控车床Z向进给系统的开发与设计
摘要本次设计针对AD-15Z向进给系统电机﹑丝杠等进行的设计。
目的是改变以往传统机床在实践操作中的一些机床寿命,调速等方面的问题,设计内容主要有电机的选择,各元件稳定性校核,以及相关知识介绍。
本文根据进给系统设计要求进行整体方案设计,对所需功能和工作原理进行分析,初步确定系统的基本结构及主要元件,按照所给机构性能参数,经济性进行元件的选择计算,通过系统性能的验算以满足该系统所要达到的设计要求,以及使用要求。
本次设计针对以往问题做出如下改进:
床身采用箱形结构及强韧米汉纳(MEHANITE)铸铁(HT-300),一体成型铸造技术铸造,采用高精度进口五面体加工中心一次装夹加工完成,因此具有整体刚性强,机床精度保持性好,使用可靠性高等特点。
主电机、进给电机均采用FANUC伺服电机,实现机床的无级调整。
机床采用滚珠丝杠和NSK专利形式线性导轨,位移速度快,精度好,适合高度精密切削,Z轴快移速度24m/min,X轴快移速度20m/min。
X、Z轴进给传动采用进口名牌大直径、高精度滚珠丝杠,并施以预压预拉,两端配置滚珠丝杠专用高精密斜角滚珠轴承,确保运动和位置精度。
快移速度:
X轴20m/min,Z轴24m/min。
关键词:
机电液一体化结构线性导轨无级调整
ThedevelopmentanddesignoftheZdirectionfeedsystemaboutAD-15CNC
AbstractAD-15CNClathesusedelectro-hydraulicintegratedstructure,smallfootprintwithtworeasonablycompactlayout,location-basedPaixietheneedsofusersofsideorrear.
BedusedboxstructureandrobustmetersHannah(MEHANITE)castiron(HT-300),One-castingfoundrytechnology,usingimportedhigh-precisionmachiningcentersinthefive-timefixtureprocessingcompleted,thereisstrongoverallrigid,precisionmachinetoolsMaintainagooduseofhighreliabilitycharacteristics.
Themainmotors,electricalfeedFANUCservomotorsareused,andnomachine-leveladjustments.NSKballscrewandmachinetoolsusedformoflinearrailspatent,displacementspeedandaccuracy,andsuitableforhighprecisioncutting,Z-axismotionspeedfast24m/min,X-axismotionspeedfast20m/min.
X,Z-axistodriveintotheuseofimportedbrand-namelarge-diameter,high-precisionballscrews,andpre-imposedpressurepretensioners,targetedatbothendsofdedicatedhigh-precisionballscrewdiagonalballbearingstoensurethatmovementandlocationaccuracy.Fasttransferspeed:
X-axis20m/min,Zaxis24m/min.
Keywords:
Electro-hydraulicintegrationofnon-lineartrack-adjustment
引言…………………………………………………………………1
第一章机床概况……………………………………………………3
1.1机床规格与用途…………………………………………………3
1.2加工范围与刀具干涉……………………………………………3
第二章Z向进给系统的部分元件设计……………………………5
2.1滚珠丝杠相关的计算……………………………………………5
2.2确定滚珠丝杠副预紧力…………………………………………6
2.3确定滚珠丝杠副支撑用的轴承代号,规格………………………6
2.4转动惯量的计算…………………………………………………6
2.5电机扭矩计算……………………………………………………7
第三章进给系统整体校核………………………………………10
3.1计算进给牵引力…………………………………………………10
3.2计算最大动负载…………………………………………………10
3.3传动效率计算……………………………………………………10
3.4刚度验算………………………………………………………11
3.5各元件受力变形…………………………………………………11
3.6稳定性校核………………………………………………………12
第四章润滑系统与冷却系统……………………………………13
4.1润滑系统…………………………………………………………13
4.2冷却系统…………………………………………………………14
第五章机床的结构及调整………………………………………………16
5.1主轴结构…………………………………………………………15
5.2.刀架的调整………………………………………………………15
5.3.皮带张紧的调整…………………………………………………15
5.4.尾座的结构和调整………………………………………………16
5.5.液压卡盘的使用和调整……………………………………………17
结论…………………………………………………………………18
致 谢…………………………………………………………………19
参考文献………………………………………………………………20
引言
数控机床是数字控制机床的简称,是一种装有程序控制系统的自动化机床。
该控制系统能够逻辑地处理具有控制编码或其他符号指令规定的程序,并将其译码,从而使机床动作并加工零件。
与普通机床相比,数控机床有如下特点:
加工精度高,具有稳定的加工质量;
可进行多坐标的联动,能加工形状复杂的零件;
加工零件改变时,一般只需要更改数控程序,可节省生产准备时间;
机床本身的精度高、刚性大,可选择有利的加工用量,生产率高(一般为普通机床的3~5倍);
机床自动化程度高,可以减轻劳动强度;
对操作人员的素质要求较高,对维修人员的技术要求更高。
数控机床一般由下列几个部分组成:
主机,他是数控机床的主题,包括机床身、立柱、主轴、进给机构等机械部件。
他是用于完成各种切削加工的机械部件。
数控装置,是数控机床的核心,包括硬件(印刷电路板、CRT显示器、键盒、纸带阅读机等)以及相应的软件,用于输入数字化的零件程序,并完成输入信息的存储、数据的变换、插补运算以及实现各种控制功能。
驱动装置,他是数控机床执行机构的驱动部件,包括主轴驱动单元、进给单元、主轴电机及进给电机等。
他在数控装置的控制下通过电气或电液伺服系统实现主轴和进给驱动。
当几个进给联动时,可以完成定位、直线、平面曲线和空间曲线的加工。
辅助装置,指数控机床的一些必要的配套部件,用以保证数控机床的运行,如冷却、排屑、润滑、照明、监测等。
它包括液压和气动装置、排屑装置、交换工作台、数控转台和数控分度头,还包括刀具及监控检测装置等。
编程及其他附属设备,可用来在机外进行零件的程序编制、存储等。
自从1952年美国麻省理工学院研制出世界上第一台数控机床以来,数控机床在制造工业,特别是在汽车、航空航天、以及军事工业中被广泛地应用,数控技术无论在硬件和软件方面,都有飞速发展。
数控机床的伺服进给系统由伺服进给系统、伺服驱动系统、机械传动系统及执行部件。
而Z向进给系统主要包括:
Z向伺服电机、联轴器、轴承、滚珠丝杠及Z向滑台
本次设计主要解决以下问题:
(1)提高系统机械结构的传动刚度、稳定性。
(2)采用低而稳定的摩擦传动副。
(3)惯量匹配。
(4)提高传动件的刚度、负载能力。
一、机床概况
1.1机床规格与用途
本机床属于半闭环控制系统的全功能数控车床,适宜中、小型轴、套、盘类零件的内、外圆柱面、圆锥面、圆弧面、端面和螺纹面的加工,特别适应于精密零件的加工。
工艺适应性强,效率高,精度高,加工质量稳定,可降低对工人熟练程度的要求。
编程容易,操作简单,可广泛适用于汽摩配件、家电、液压气动、轴承、仪器仪表、五金阀门等制造业零件的批量加工,是理想的中小型机械加工设备。
1.机床的加工范围
最大回转直径440mm
最大切削直径300mm
最大切削长度500mm
最大棒料直径52mm
2.主轴
主轴速度范围(无级)45~4500rpm
主轴通孔直径62mm
主轴端部型式A2-6
3.刀架
刀架型号CLT-100-8T
刀架工位数8
换刀时间0.72秒
刀杆截面尺寸25mm×25mm
1.2加工范围与刀具干涉
图2加工范围图
图3刀具干涉图
第二章:
Z向进给系统的部分元件设计
2.1滚珠丝杠相关的计算
机床定位精度0.020mm,重复定位精度0.010mm,由于考虑到加工精度,实际上切削力由下面经验公式计算。
外圆主切削力F
(N)按经验公式估算:
F
=0.67F=0.6*4850=2910N
1滚珠丝杠副的导程P
P=V/i*n=20/(1*3000)≈10mm(2-1)
V-Z向快移速度;n-Z向电机最高转速。
传动比i=1
所以所选丝杠的导程必须是7mm以上,可选8和10
2载荷与转速
丝杠轴向载荷:
F=F1+T+f(P1+P2)=2910+2+0.005(1900+1900)=2931N(2-2)
F2=Fg=0.005*200*9.8=9.8N
滚动直线导轨摩擦系数f=0.005T=2
平均载荷为:
Fm=(2F+F2)/3=1954.3N
最大进给时,丝杠转速为3000/10=300r/min,最小进给时,为1r/min,平均
转速n=(2*300+1)/3=200.3r/min
丝杠的平均寿命取Lh=20000小时。
3确定允许的最小螺纹底径
丝杠允许的最大轴向变形量:
<(1/3~1/4)重复定位精度<(1/3~1/4)0.007=0.002
<(1/4~1/5)定位精度<(1/4~1/5)0.016=0.004
取
=0.002mm
丝杠支承形式为两固定d=5mm,两个固定支承之间的距离L=788mm
4确定滚珠丝杠规格代号
根据PhCmd,选择内循环垫片式预紧螺母形式FFZD4012-4
Ph=12mmCm=36.5KNd=32.7mm刚度值0.909N/mm
2.2确定滚珠丝杠副预紧力
Fp﹥1/3*Fmax=1/3*2811≈937N(2-3)
取预紧力Fp=1370N
2.3确定滚珠丝杠副支撑用的轴承代号,规格
轴承承受的轴向载荷F=Fmax=2811N
F预紧力﹥F/3=937N
则滚珠丝杠支撑形式采用NSK系列,型号:
30TAC62BDFPN7B
2.4转动惯量的计算
丝杠轴向载荷产生的摩擦力矩T
Tm=5.97KN预加载荷的预紧力矩Tp=0.614KN
1.回转运动件的转动惯量:
JR=md2/8=πρd4l/32(kg.m2)(2-4)
其中:
d—直径(m);
l—长度(m);
ρ—钢的密度=7800kg/m2
这样,d=0.05m,l=1.823m。
那么,由上式可以得出:
JR=πρd4l/32=π×7800×0.054×1.823/32≈0.00175kg.m2。
直线运动件向丝杠折算的惯量:
JL=M×[P/(2π)]2(kg.m2)
其中:
M—质量(Kg,主要包括溜板、床鞍、刀架等);
P—丝杠螺距(m)。
直线运动件质量M=800kg,丝杠螺距P=0.01m。
那么,由上式可以得出:
JL=800×[0.01/(2π)]2≈0.0001kg.m2。
2.联轴器的转动惯量
联轴器为外购件,根据联轴器样本在(上海席特传动)可以查出
Jw=2.17*0.00001kg.m2。
3.轴承的转动惯量
(2-5)
4.折算至电机轴上的总惯量为:
J=JR+JL+Jw+J4(2-6)
=0.0087+0.002+0.004+0.0023
≈0.012kg.m2。
2.5电机扭矩计算
在实际设计当中我们通常分两步走,一是计算快速空载启动时所需的最大扭矩,再一个就是计算机床重切时所需的最大扭矩,哪一个数大就以哪一个数作为选择电机的依据。
1.折算至电机轴上的最大加速力矩为:
Tamax≈2πnmax×J/(60ta)(N.m)(2-7)
其中:
Vmax—要求Z向快移速度15m/min,丝杠螺距为0.01m
则:
nmax=15/0.01=1500r/min
J—折算至电机轴上的系统总惯量≈0.017;
ta—加速时间(s),ta≈3/Ks,
Ks—系统增益,取Ks=20s-1,则ta≈3/Ks=0.15s。
那么,由上式可以得出:
Tamax≈2πnmax×J/(60ta)
=2π×1500×0.017/(60×0.15)
≈12.5N.m。
2.折算至电机轴上的摩擦力矩为:
Tf=F0×P/(2πηi)(N.m)(2-8)
其中:
F0—导轨摩擦力N,F0=Mf,而f—摩擦系数f=0.018(TSF软带—淬火钢,油润滑)
所以,F0=M·g·f=800×9.8×0.018=98.5N;
P—丝杠螺距,0.01m;
η—传动链总效率,滚珠丝杠副η=0.98;
i—齿轮降速比,无齿轮减速,i=1。
那么,由上式可以得出:
Tf=F0×P/(2πηi)=141.12×0.01/(2π×0.98×1)
=0.158N.m。
3.折算至电机轴上的由丝杠予紧引起的附加摩擦力矩为:
T0=P0×P×(1-η02)/(2πηi)(2-9)
其中:
P0—滚珠丝杠予加载荷为Fz/3=6180/3=1750N
η0--滚珠丝杠副未予紧时的传动效率0.9。
那么,由上式可以得出:
T0=P0×P×(1-η02)/(2πηi)
=3456.8×0.01×(1-0.92)/(2π×0.98×1)
≈1.07N.m
快速空载启动时所需的最大扭矩为:
T=Tamax+Tf+T0=17.8+0.229+1.07≈14.6N.m。
4.重切时所需扭矩计算:
重切时的切削负载转矩:
T切=Fz×P/(2π)(2-10)
其中:
Fz—Z向进给力为2308.7N.
那么:
T切=Fz×P/(2π)=2308.7×0.01/(2π)≈4.3N.m
重切时的摩擦力矩
Tf切=(M×g+Fy)×f×P/(2π)
其中:
Fy—Y向切削分力=0.4Fz=2134.7N.
那么:
Tf切=(M×g+Fy)×f×P/(2π)
=(800×9.8+2160.5)×0.018×0.01/(2π)
=0.193Nm。
重切时所需扭矩为:
T=T切+Tf切++T
=5.5+0.287+1.07≈4.38N.m
5.结论
通过以上计算可知,电机扭矩应大于19.1Nm,惯量应满足1≤J/J
≤4,在β伺服电机系列中符合条件且最为合适的电机应该是α12/3000i,该电机额定扭矩12Nm,转动惯量0.012kgm,
1≤J/J
=0.017/0.012≈1.4≤4可以胜任AD-15数控车床Z向伺服驱动工作。
第三章:
进给系统整体校核
3.1计算进给牵引力Fm(N)
进给导轨为矩形导轨,拖板底面采用贴塑处理:
Fz=4850N;
G—移动部件的重量,取值8000N;
f'—导轨上的摩擦系数,取值范围是0.03~0.05,取值0.05
K—考虑颠覆力距影响的实验系数,取值1.1。
F
=1.1×3456.8+0.05(8642+2160.5+8000)(3-1)
故:
F
=2376.55+1004.94=3458.27N
3.2计算最大动负载C
C=
f
F
(3-2)
L=60×n×T/10
n=1000.V
/L
式中L
—滚珠丝杠导程,初选L
=10mm;
V
—最大切削力下的进给速度,可取最高进给速度的
(1/2~1/3),此处V
=2m/min;
T—使用寿命,按25000h;
fw—运转系数,按一般运转取1.2~1.5,此取1.5;
L—寿命、以10
转为1单位。
计算得:
n=1000.V
/L
=1000×2/10=200r/min
L=60×n×T/10
=60×200×25000/10
=30
C=
f
F
=
×1.5×4742.61=17362N
所选丝杠为银泰FDWC50其额定载荷Ca=57900N>17362N
由此可知所选丝杠满足需要。
3.3传动效率计算
银泰滚珠丝杠的传动效率很高,大于90%,是高效率的传动部件,符合使用要求。
3.4刚度验算
滚珠丝杠的支撑方式草图如下图所示,最大牵引力为4742.61N,支撑间距L=1600mm,丝杠螺母及轴承均进行预紧,预紧力为最大轴向负荷的1/3。
3.5各元件受力变形
1.丝杠的拉伸变形量
:
根据最大牵引力为4742.61N,D0=50mm,L0=10mm可算出:
△L=
=
=1.17×10-4mm,(3-3)
式中:
Fm—工作负载,既进给率引力,(N);Fm=4742.61N
E—材料弹性模数,对钢E=20.6×104(N/mm);
F—滚珠丝杠截面积(按内径计算);
F=3.14×25
=1962.5
L
—滚珠丝杠的导程(mm);
=
×L=1.17×10-5×1600=2.2×10
mm(3-4)
由于两端均采用角接触推力球轴承,且丝杠又进行了预拉伸,故其拉压刚度可以提高4倍。
其实际变形量
为:
=0.25×
=5.5×
mm
2.滚珠与螺纹滚道间接触变形
=0.0013
(3-5)
F
—轴向工作负载kgf;
d0—滚珠直径mm;
Fy—预紧力Kgf;
Z
—滚珠数量Z
=Z×圈数×列数=24.72×2×2.5=123.6
Z—一圈的滚珠数;Z=3.14×50/6.35=24.72
=0.0013
=0.0013
=0.00094mm
3.支撑滚珠丝杠轴承的轴向接触变形δ
为更好的承受轴向力,两组均采用日本的NSK精密角接触球轴承,型号:
30TAC62BDFPN7B
δ
=0.0024
(3-6)
—轴承滚动体直径(mm)
Z—轴承滚动体数目
根据以上计算:
δ=δ1+δ2+δ3=0.0055+0.00094+0.003=0.00944mm<1/2(定位精度)=0.016
故符合要求。
3.6稳定性校核
计算临界负载FK(N)
FK=
(3-7)
=2×9.8596×20.6×106×26.04/16002
≈4132N
式中:
E—材料弹性模量,钢:
E=20.6×106N/cm;
I—截面惯性矩(cm)丝杠:
I=πd14/64=26.04,
d1为丝杠内径;
L—丝杠两支承端距离(cm);
f—丝杠支承方式系数,因为丝杠的一端固定,一端半固定f2=2.00
nk=57900/4132=14.01>[nk]
(一般[nk]=2.5~4)
因此滚珠丝杠不会产生失稳。
第四章:
润滑系统
4.1润滑系统:
为保证机床正常运转和延长使用寿命,机床所有相互摩擦的零件均需经常地、及时地给予润滑。
主轴轴承采用永久性脂润滑,润滑脂选用高级锂基润滑脂。
纵向和横向的滚珠丝杠副和滚动直线导轨副自动集中润滑泵供油。
自动集中润滑泵安装在机床底座左端面,应定期检查润滑油箱油位情况并及时补油。
润滑油应使用纯净的30号机械润滑油,其粘度为27×10-6~33×10-6m2/s(50℃),用户可按机床工作条件在上述范围内适当调节。
尾座体顶面、刀架顶面和液压卡盘卡盘体上分别有油杯,通过油杯加注润滑油,润滑油牌号为30号机械润滑油。
每班至少要润滑两次。
为保证机床正常运转和延长使用寿命,机床所有相互磨擦的零件均需经常地、及时地给予润滑。
对于导轨、轴承和其它活动部位来说,润滑油是非常的重要,请根据下表所建议牌号,定期添加或更换润滑油。
本公司不负责因使用不正确的润滑油而引起的功能异常。
润滑部分
润滑方式
润滑频率
建议使用油牌号
主轴箱
黄油(内封)
(无须)
ISOFLEX-NBU15
卡盘
黄油(注射)
每日一次
ZL-1号脂
刀塔
黄油(内封)
(无须)
RETINAXAM
润滑泵(X轴和Z轴滚珠丝杠、尾座和导轨)
压力润滑
间歇润滑
32号润滑油
油压系统
——
半年一次
32号润滑油
1、润滑标准
2、主轴
主轴箱仅包含主轴而无齿轮与其他活动零件。
主轴箱中的主轴轴承采用高级锂基润滑脂作永久润滑。
具有耐高/低温(-60°C至130°C)高速(10000rpm),和较强的作业寿命的特性,不须作定期添加或更换。
3、刀塔
刀塔是以黄油作为润滑,不须加添其他润滑油。
此为永久性而不须更换。
4、卡盘
卡盘使用黄油作为润滑,补充黄油于卡盘的滑道槽每天一次。
5、集中润滑
纵向和横向的滚珠丝杠副、滚动直线导轨副和尾座主轴套筒采用自动集中润滑泵供油。
润滑泵应定期检查润滑油箱油位情况并及时补油。
润滑油应使用纯净的32号机械润滑油,其粘度为27×10-6-33×10-6m2/s(50°),用户可按机床工作条件在上述范围内适当调节
4.2冷却系统:
机床床身下面配置有单独的冷却箱,冷却泵安装在冷却箱上。
操作者按下操作面板上冷却启动按钮,水泵转动并将冷却液经过橡胶软管输送至液压刀架,冷却液从刀架刀盘上处于加工工位的喷嘴中喷出。
第五章:
机床的主轴及尾座
5.1主轴结构
图9主轴结构图
主轴采用前后双支撑结构,配合大直径高精密圆柱滚子轴承及高速角接触滚珠轴承,前端固定、后端浮动支撑,可承