AP1000技术手册5.docx
《AP1000技术手册5.docx》由会员分享,可在线阅读,更多相关《AP1000技术手册5.docx(31页珍藏版)》请在冰豆网上搜索。
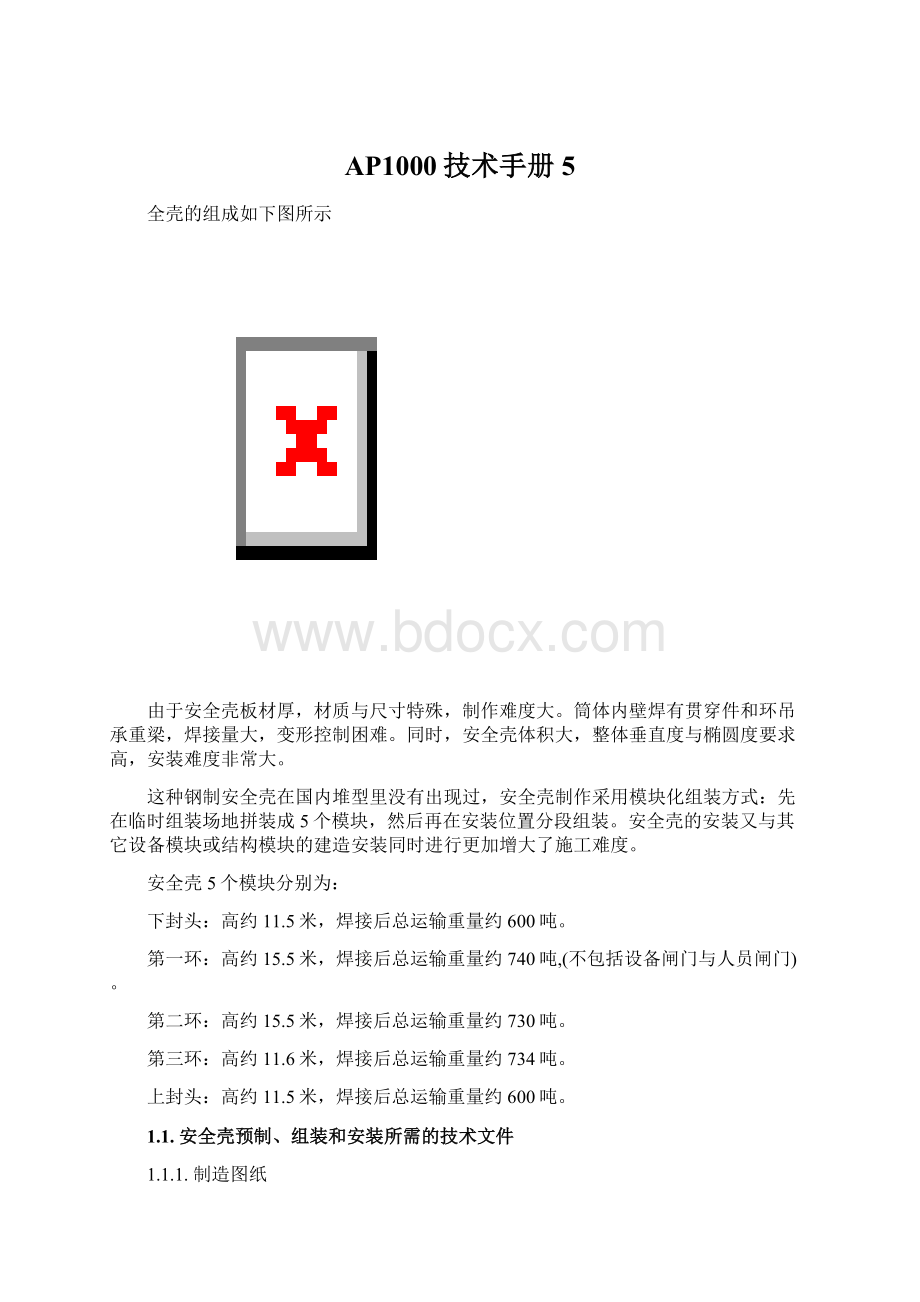
AP1000技术手册5
全壳的组成如下图所示
由于安全壳板材厚,材质与尺寸特殊,制作难度大。
筒体内壁焊有贯穿件和环吊承重梁,焊接量大,变形控制困难。
同时,安全壳体积大,整体垂直度与椭圆度要求高,安装难度非常大。
这种钢制安全壳在国内堆型里没有出现过,安全壳制作采用模块化组装方式:
先在临时组装场地拼装成5个模块,然后再在安装位置分段组装。
安全壳的安装又与其它设备模块或结构模块的建造安装同时进行更加增大了施工难度。
安全壳5个模块分别为:
下封头:
高约11.5米,焊接后总运输重量约600吨。
第一环:
高约15.5米,焊接后总运输重量约740吨,(不包括设备闸门与人员闸门)。
第二环:
高约15.5米,焊接后总运输重量约730吨。
第三环:
高约11.6米,焊接后总运输重量约734吨。
上封头:
高约11.5米,焊接后总运输重量约600吨。
1.1.安全壳预制、组装和安装所需的技术文件
1.1.1.制造图纸
安全壳容器椭圆底封头制造图
安全壳容器环形制造图纸
安全壳容器椭圆顶封头制造图
贯穿件套管和附件图吊车梁和轨道制造图
安全壳临时支撑梁详图
1.1.2.工具图纸
定位设备
1.1.3.材料采购技术规格书
SA738Gr.B;
SA333Gr.B;
STUDBOLT;
TemporaryColumn,
WeldingMaterial.
1.1.4.预制程序
焊接工艺程序(SMAW,GMAW,SAW)
坡口预制程序
安全壳球壳板压制方案
安全壳筒体板卷制方案
安全壳环吊梁预制方案
贯穿件预制方案
热处理工作程序
焊接工艺合格记录清单
修复计划
制造程序流程图
清洁程序
清扫和油漆程序
制造质量计划
材料质量计划
1.1.5.检查和测试程序
超声检查程序
液体渗透检查程序
磁粉检查程序
材料验证程序
焊口X光检查程序
目视检查程序
1.1.6.组装程序
安全壳底封头现场组装程序
安全壳筒体模块现场组装程序
安全壳顶封头现场组装程序
运输程序
吊装程序
1.2.安全壳板的预制
安全壳板预制分为筒体板预制、球面板预制、贯穿件支座预制、设备闸门通道预制、人员闸门预制、环吊梁预制。
安全壳板预制的关键在于安全壳的排版图的绘制。
筒体预制工作包括板材的接收、下料、开坡口、卷板、焊接环吊梁支座、筒体板之间组对、焊后热处理、喷砂除锈、制作运输托架、运输到施工现场等。
球面板预制包括压制成型(对于上、下封头球面板)包括板材的接收、下料、开坡口、喷砂除锈、运输到施工现场等。
所有弧板与球壳板的成形除锈后,刷底漆(底封头除外),留出100mm宽的焊接边界不刷,底封头采用可剥性涂层加以保护。
设备闸门通道、人员闸门、环吊梁的预制包括板材的接收、下料、开坡口、组对、焊接、焊后热处理、喷砂除锈、涂漆、运输到施工现场。
1.3.安全壳板的组装
1.3.1.安全壳组装前的准备工作
材料堆放场地规划和建设;上下封头组装用门式起重机设计及安装;组装场地基础设计与建设;组装厂房设计和建造;下封头组装支架设计和制作;安全壳筒体组装支座设计和制作;上封头组装支架设计和制作;安全壳测量支架设计和制作。
1.3.2.安全壳的组装顺序
下封头
↓
第一环
↓
第二环
↓
第三环
↓
上封头
1.3.3.下封头组装和安装流程
下封头组装支架安装;
下封头第一圈板焊支承台和吊耳;
完成后依照编号顺序吊放在组装支架上;
调整间隙,调标高,调整平度后用多功能板固定(用全站仪测量);
点焊,施焊,检测焊接质量和板面变形符合要求;
如此依次完成下封头第一环第二圈板、第三圈的组对和焊接;
移动安装在中心的测量支架到封头外,组装底圈二块极板;
点焊,焊接,检测合格后下封头组对工作完成。
第一环第一圈在下封头上组装,完成后,用油漆在下封头和第一环第一圈的对应点作好标志,吊运第一环第一圈到指定位置调平;
给下封头装调整支柱;
吊运下封头到安装位置;
调整上口水平度到要求值。
下封头外表面焊螺柱
1.3.4.安全壳第一环组装和安装流程
借助全站仪调平下封头上口水平到要求值,用支撑将下封头固定;
第一环第一圈板焊支承台和吊耳;
按编号吊装第一环第一圈板到下封头上口上;
用立柱上专用装置将板稳固.;
调整,第一环第一圈的焊缝间隙到要求值;
点焊,然后将第一圈板焊成一个圆环(不得与下封头焊接);
检测焊接质量应合格,对第一圈板立焊缝进行热处理;
取下稳固装置,吊第一环第一圈,放在预定位置;
在组装位置布置调整垫板,用吊车吊上第一环第一圈放在调整垫板上,借助全站仪调整第一环第一圈水平度到要求值;
给第一环第二圈板焊支撑台和吊耳
吊第二圈板到第一圈板上,
用立柱上的装置稳固
调整间隙到要求值
点焊固定,检测间隙合格后施焊(包括环缝)
检测焊缝质量和热变形在要求范围。
依次做第三圈板和第四圈板的组装。
检测焊缝质量,上口水平度,不圆柱度,合格后完成第一环组装。
还要在第一环上完成第二环第一圈的组装,
给予第一环与第二环第一圈的对中点作出标记,
吊走第二环第一圈,放到规定位置
用吊车将第一环吊装到下封头上,对正基准点
调整间隙,用多功能调节板固定
测量筒身铅直度上口水平度符合要求
点焊,施焊,检测第一环环焊缝质量,筒体铅直度,上口水平度均符合要求后,第一环安装完成。
1.3.5.安全壳第二环组装和安装流程
安全壳组装基础上按照布置图放置垫铁组,调配标准高度;
用吊车将安全壳第二环第一圈吊放在可调垫铁组上;
借助全站仪调整安全壳第二环第一圈到达要求值;
给第二环第二圈板焊支承台和吊耳;
吊放第二圈板到第一圈上,用立柱上装置稳固;
调整间隙到要求值,点焊,焊接;
检测焊接质量和热变形在允许范围内;
依次再完成第三圈板、第四圈板的组装和焊接,第二环组装完成。
在第三环第一圈板的组装第二环上进行。
完成第三环第一圈板的点焊,焊接(不准和第二环焊接),质量和变形检测,用起重机吊起第三环第一圈,放
在要求位置;
用2600吨吊车将第二环吊装上位;
用多功能调节板调整间隙和固定,点焊,焊接;
检测焊接质量和热变形(包括铅直度,不圆度,不圆柱度),均符合要求后,第二环安装完成。
1.3.6.安全壳第三环组装和安装流程
安全壳组装基础上垫铁组安装;
将第三环第一圈吊放在垫铁组上,调整第三环第一圈水平度到要求值;
给第三环第二圈焊支承台和吊耳;
将第三环第二圈板
按照编号顺序吊装到第一圈上,并用柱上装置稳固
调整间隙,并用多功能板固定;
点焊,焊接,检测焊接质量和热变形应在要求范围内;
同样做第三环第三圈的组对和焊接,检测焊接质量和热变形应在要求范围内;
检测环吊梁尺寸,给环吊梁焊吊耳;
吊装环吊梁,调整环吊梁尺寸和焊接间隙;
点焊,焊接,检测焊缝质量和热变形应在要求范围内,做环吊梁焊缝热处理,调整第三环上口水平度到要求值。
给上封头第一圈板组加组装支撑,给上封头第一圈板焊支承台和吊耳;
按要求顺序吊装上封头第一圈板到第三环上,并用立柱上装置稳固;
调整间隙,并用多功能板固定;
点焊,焊接,检测焊接质量应在规定范围内,热变形不应超过允许范围;上封头第一圈组对完成,吊运走上封头,放到指定位置。
用2600吨吊车将第三环吊装到第二环上,用多功能板调整间隙和固定;点焊,焊接,检测焊接质量,筒体圆度,筒身铅直度符合要求,安全壳筒身安装基本完成。
1.3.7.上封头组装和安装流程
用起重机将上封头第一圈吊放在垫铁组上;
给第二圈板焊支承台和吊耳,吊放上封头第二圈板到组装支撑上,调整间隙,用多功能板固定;
点焊,焊接,检测焊接质量和热变形应在要求范围内;
安装第三圈板支撑和调节器,给第三圈板焊支承台和吊耳,吊放第三圈板到支撑上;
点焊,焊接,检测焊接质量和热变形应在允许范围内;
2600吨吊车将上封头吊装到第三环上,调整间隙,用多功能调节板固定;
点焊,焊接,检测焊接质量和热变形应在允许范围内,上封头组对工作完成,安全壳组装工作基本完成。
1.3.8.安全壳上贯穿安装
安全壳上有许多贯穿件,有的在制造工厂安装,有的在组装厂房安装,其中的设备闸门和人员闸门的开孔必须在第三环焊接完成后进行,用全站仪先放出中心线,再放出孔的位置线;用自动切割机开孔,装门体支撑件;调整位置;点焊,焊接;检测焊接质量和热变形应当在允许范围,贯穿件的角度符合要求。
1.3.9.焊接工艺
采用自动熔化极气体保护焊工艺、埋弧焊工艺等。
所有的自动焊机都采用专用焊机,对焊接轨道、焊接区的防风保护、埋弧焊焊剂的回收等装置进行针对性的设计。
为了保证安装质量,将编制相应的工作程序以对装配焊接顺序进行详细规定以保证装配公差符合要求,并对坡口准备、组对、焊接、检验等工序进行严格的控制,以保证最终的焊接质量。
1.3.10.热处理工艺
所有焊缝焊接前的预热均采用电加热,外敷保温棉。
环吊梁组装焊缝的热处理采用整体气体加热的方式进行。
筒体纵焊缝与环焊缝的热处理均采用局部热处理的方法,用陶瓷电加热片作加热器,加热带外部采用硅酸铝保温棉作保温材料,焊缝的内外表面都布置保温棉。
贯穿件焊缝采用局部热处理的方法,整条焊缝一起进行处理,焊缝的内外表面都布置保温棉。
1.3.11.喷砂与油漆工艺
将CV部件上的标识位置、标识内容和标识数量进行移植和记录。
CV部件推入喷砂室进行喷砂处理。
CV部件喷砂处理后清洁吹扫。
对CV部件进行标识和周边焊缝位置、标识进行保护。
检查CV部件喷砂处理等级、粗糙度、清洁和标识等并进行记录。
CV部件推入喷漆室进行喷底漆。
检查CV部件底漆的湿膜厚度、外观质量并进行记录。
CV部件推入烘干室进行底漆烘干。
检查CV部件底漆的干膜厚度、外观质量并进行记录。
CV部件综合性检查,检查合格后,运送到CV部件存放区存放。
CV部件拼装段完成后,对焊缝位置进行喷砂处理和清洁吹扫。
检查CV拼装段焊缝位置喷砂处理等级、粗糙度、清洁等并进行记录。
进行CV拼装段底漆修补和喷涂底漆。
检查CV拼装段底漆的湿膜厚度、干膜厚度、外观质量并进行记录。
进行CV拼装段面漆喷涂。
检查CV拼装段面漆的湿膜厚度、干膜厚度、外观质量并进行记录。
1.3.12.安全壳安装要求及记录
安全壳内径39.624米,以此为测量直径的基准。
安全壳直径允差100毫米,即最大39.724米,最小39.524米,不允许出现5毫米的台阶。
安全壳筒身高度约42.5米,筒身铅直度最大允差100毫米。
为了在组装过程中进行质量控制,对每项工序进行质量控制。
整个预制、组装和安装过程要进行测试和相应得的记录。
1.4.安全壳组装和安装的主要设施
安全壳组装场地安装三台门式起重机:
一台起重机的起重量50吨,跨度50米,大钩起升高度25米,用于筒体模块的组对工作。
另外利用两台20吨门式起重机,跨度46米,起升高度21米。
组装场地设置52米宽,50米进深的活动厂房,将三台吊车整体组成一片,对安全壳组装、焊接、测量提供了安全和环境保障。
安全壳组装场地起重机安装需70吨以上吊车配合。
安全壳吊装:
最重件740吨,吊装时必须用的吊梁和吊具约重130吨,用2600吨吊车吊装上位。
1.5.安全壳预制、组装、安装工艺特点与难点
1.5.1.板成形特点
板成形质量直接影响着现场拼装的进度和安全壳整体安装质量。
安全壳共有260块弧板拼焊而成,每块板的微小成形误差,将会带来相当大的错口,而增大安装难度。
因此板成形有严格的要求。
板材尺寸偏大,板材厚,其回弹量难以把握,容易造成弧度不合格,校形将是很大的难点,尤其是球壳板,现场根本无法校形。
对于球壳板压制要求更严,既要保证弧度正确,还要保证在压板时不会造成弧面背部不开裂,凹面不起皱,这必须要有相当的技术要领。
1.5.2.焊接与热处理特点与难点
材料特殊,安全壳容器材料为SA738B,属于低合金高强度钢,焊接要求高,易发生裂纹。
安全壳容器尺寸大,板材厚,每个安全壳焊缝的延长米总长度达到3800米以上,消耗焊接材料在30吨以上,焊接量大。
由于安全壳的强度比普通压力容器高,焊接工艺要选择适当。
由于安全壳焊缝数量多,焊缝结构较为复杂,焊接量大,会产生很大的收缩变形,而由于板材厚,一旦在焊接过程中产生超过规定的焊接变形,很难采用机械的方法进行矫正,因此在安装焊接过程中需要采用合理的焊接工艺,采用合理的装配焊接顺序,以控制焊接变形,保证组装和安装的尺寸要求。
焊接的质量要求高,所有筒体焊缝都要进行100%的射线检验。
核电基地又是台风的多发区,风大而且空气潮湿,野外施工对焊接质量有着很大的影响。
为了保证工期,必须要为安全壳的预制拼装设计一个相对封闭的厂房,此厂房既要承受现场16级台风又要保证将大模块顺利地运出。
对于厚度在45mm以上的大型钢制容器焊接,需要焊前预热,还需相应的热处理工艺,情况都较为复杂,远比已建的秦山一、二期核电站的钢衬里焊接难度大。
1.5.3.运输与吊装特点与难点
模块组装完后,最大模块近40米直径,15.5m高,重达800吨。
模块吊装时内部不允许有任何防变形加固设施,如何将这么大的模块从临时组装场地运输并吊装到就位点而不发生变形,将是起重业重要的一项课题。
2.模块预制、运输和组装、安装
2.1.模块的制造要求
2.1.1.对于模块及其内部结构的吹扫和油漆要求
◆结构碳钢
碳钢板的吹扫符合SSPCSP-10并且在预制前涂3mils厚的无机富锌硅酸底漆
所有安装在电站的最终暴露于空气的要涂上无机富锌底漆,表面涂上高密度环氧或环氧酚(干膜厚4.0to8.0)
◆不锈钢
所有不锈钢都不涂油漆
◆模块预制
所有需要涂漆的模块在从预制商处,运输前都要涂上面漆。
◆管道和元件-碳钢
按照材料,保温,供货商的涂层的系统要求等,指定每个模块的涂层。
在现场将子模块组装成模块,完成焊接和补漆工作,在模块上涂上聚氨环氧树脂(干膜5mils)
2.1.2.保温
安装在系统元件和设备上的保温是为了减少热损失和减少在冷冻水系统管道支撑上的冷凝,以及按照系统技术规格书或工艺和仪表图纸提供人员的保护。
2.1.3.测试
编制所有模块的测试程序,确保符合模块设计的技术规格书,满足模块接收准则。
在模块运输前,要最大程度上进行测试和记录模块质量。
按照程序SNT-TC-1A测试人员是有资格和通过认证的。
通知测试日期,提供测试的设备和材料以使西屋或他的代表能见证测试。
2.1.4.记录
按照ANSI/ASMENQA-1-核电站的质量保证要求,生成质量保证记录并且得以维护。
这些记录最少将包括的模块设计包,模块设计报告,模块测试接收报告和模块预制要求。
2.2.模块的预制
2.2.1.预制要求
AP1000设计中模块准备完全使用工厂预制的方法,并在厂内进行组装让后整体运输。
如果部分模块的尺寸超出运输要求,可以对其分解并进行标记,安装临时螺栓或销钉以简化现场安装时所需的准备工作,另外还要尽量减少现场焊接的操作。
2.2.2.预制流程
技术准备/技术交底→领料→下料→标识→坡口→预制面板/型钢结构→子模块组对→焊接→检验→表面处理(酸洗/抛光及喷砂防腐)→成品维护→组件运输→交付现场组装
2.3.模块的运输
安全壳模块(包括底封头、三个环、顶封头),直径都近40米,最高模块为15.5米,最重模块达740吨。
CA01模块,长29米,宽25米,高11米,重达450吨。
CA20模块长也有21米,重达700吨。
这类模块超大尺寸,不可能放在吊车吊装范围内进行组装,为此必须在主干道附近布置大型模块的组装场地,采用大吊车直接带载行走。
2.4.模块的组装
2.4.1.模块组装要求
所有的模块预制组件在连接成较大的单体组件时,其单体组件的尺寸应符合图纸和技术文件要求。
在单体组件的尺寸未检查确认前,不能进行最终的焊接,其在现场组对均采用点焊的方式固定。
被组对的模块预制组件尺寸应尽可能精确对中,焊接过程中应保证构件不变形。
焊接端部最大错边应不大于设计及规范要求的值。
保证对中且允许留在完工焊缝内的定位焊缝应由合格的焊工进行焊接;
不去除的定位焊缝应由使用与第一道打底焊缝相同或相当的焊材进行焊接;
其起弧或收弧处应用打磨或其他方法进行加工使之可以理想地熔入最终焊缝;
凡开裂的定位焊缝应去除。
定位组装完成后,必须重新检查定位的尺寸是否改变,如WPS要求,还应预热(碳钢)。
所有的与结构模块构件相关的焊接工作都应在结构模块组对、焊接及调整完成后进行。
同时还应特别注意模块构件之间的间隙控制,必须严格按照《模块组装手册》中的技术标准的要求执行,以保证组装完成的结构模块符合图纸要求。
2.4.2.
模块组装工艺流程
2.5.模块的安装
模块现场安装工作范围包括:
技术准备、安装施工准备、安装现场准备、吊装/运输、模块安装校正、最终就位精调/固定、模块焊接以及模块的最终移交放行等项工作环节。
3.主设备安装
主设备安装包括两部分内容:
反应堆设备安装和主回路设备安装
3.1.工作范围
3.1.1.反应堆设备安装
反应堆设备包括压力容器、堆内构件、堆顶部件;
其中:
堆内构件应包括:
上部堆内构件、下部堆内构件、堆内构件吊具、导向管组件;
堆顶部件包括:
顶盖本体、顶盖支撑架、CRDM耐压壳、线圈组件、通风罩组件、电缆桥架、抗震支撑组件、顶盖吊具、热电偶柱组件、顶盖螺栓拉伸机;
3.1.2.主回路设备安装
蒸汽发生器安装,包括蒸汽发生器垂直与侧向支撑、蒸汽发生器本体。
稳压器安装,包括稳压器垂直与侧向支撑、稳压器本体、支撑的二次预埋件。
主泵安装,包括主泵泵内件、主泵电机、主泵的最终调整。
主管道,包括主冷却剂管道热段、冷段。
蒸汽发生器安装,包括蒸汽发生器垂直与侧向支撑、蒸汽发生器本体。
稳压器安装,包括稳压器垂直与侧向支撑、稳压器本体、支撑的二次预埋件。
主泵安装,包括主泵泵内件、主泵电机、主泵的最终调整。
主管道,包括主冷却剂管道热段、冷段。
3.2.工艺流程
CA04模块安装就位
↓
压力容器腔室保温层安装
↓
压力容器支承块安装
↓
CV第3环焊接
压力容器吊装并最终调整、定位
↓
↓
环吊可用
主管道吊入腔室临时贮存
↓
↓
IHP顶盖组件组装
SG垂直支撑吊装就位
↓
SG吊装,就位
波动管移入房间
↓
↓
堆内构件吊具组装
主管道焊接
稳压器吊装就位
↓
↓
↓
下部堆内构件在存放架上就位并组装
→
下部堆内构件在压力容器内安装,调整并焊接
波动管焊接
↓
CA31模块安装
上部堆内构件在存放架上就位并组装
→
上部堆内构件安装
↓
堆内构件吊出
主泵泵内件及密封安装
↓
↓
与压力容器相关的系统冲洗
主泵电机的安装
压力容器内部清洁
↓
堆内构件重新吊入,压力容器顶盖就位,主螺栓拉伸
↓
CRDM抗震拉杆的安装
↓
堆顶电缆托和电缆桥架的安装
↓
反应堆冷态试验
↓
压力容器管口保温安装
↓
压力容器顶盖圆周保温层的安装
↓
主管道保温层安装
↓
安装热电偶(ET)
↓
反应堆热态试验
3.3.安装工序
3.3.1.压力容器安装
CA04模块安装
↓
堆腔内保温层安装
↓
压力容器支承块安装
↓
压力容器吊装就位
↓
压力容器垫板的加工、安装
↓
压力容器最终调整、定位
3.3.2.堆内构件安装
环吊可用、换料水池清洁
↓
堆内构件吊具组装、上下部堆内构件贮存架组装
↓
堆内构件在存放架上就位
↓
下部堆内构件第一次吊入并安装U形块
↓
二次试装并对中
↓
第三次吊入并最终安装
↓
上部堆内构件第一次吊入压力容器
↓
上部堆内构件在存放架上的安装工作
↓
上部堆内构件最终安装
3.3.3.堆顶部件安装
环吊可用、换料水池清洁
↓
压力容器顶盖贮存架的安装
↓
压力容器顶盖吊装在贮存架上就位
↓
CRDM耐压壳组件安装
↓
CRDM线圈组件的安装
↓
CRDM位置指示器组件的安装
↓
CRDM通风罩组件的安装
↓
CRDM抗震支撑环和支撑板的安装
↓
压力容器顶盖吊具组装
↓
压力容器顶盖就位安装
↓
CRDM抗震拉杆的安装
↓
堆顶电缆托和电缆桥架的安装
3.3.4.蒸汽发生器安装
CA01就位,腔室刷漆完毕
↓
主管道移入腔室,穿入压力容器腔室,临时固定
垂直支撑的吊装、调整、固定
↓
蒸汽发生器吊装准备
↓
蒸汽发生器翻转竖立
↓
蒸汽发生器吊入腔室初就位
↓
测量,蒸汽发生器垫板加工、安装
↓
蒸汽发生器最终就位
↓
固定下部纵向支撑
↓
蒸汽发生器与主管道焊接
↓
安装阻尼器
↓
开启蒸汽发生器人孔并检查
↓
在热试状态下测量各支撑处的间隙
3.3.5.稳压器安装
稳压器腔室就位,腔室刷漆完成,波动管移入
↓
安装四个垂直支撑
↓
稳压器吊装准备
↓
稳压器在厂房外翻转竖立
↓
稳压器降至腔室内
↓
测量标高等,加工垫铁
↓
稳压器最终固定
↓
安装并调节水平支撑限制器
↓
养生后检查、螺杆加载
↓
在热试状态下测量各支撑处的间隙
3.3.6.主泵安装
主管道焊接完成
↓
设备的引入
↓
吸入口环的安装
↓
电机组件的组装
↓
叶轮的安装
↓
电机组件与泵壳的对接
↓
定子下端盖的安装
↓
主法兰螺栓的拉伸
↓
附件与管件的安装
↓
检查清场
3.3.7.主管道安装
蒸汽发生器吊入前,将主管道引入
↓
蒸汽发生器最终就位
↓
主管道热段采用激光对中
↓
主管道热段与压力容器、蒸汽发生器焊接20%
↓
主管道冷段采用激光对中
↓
主管道冷段与压力容器、蒸汽发生器焊接20%
↓
完成所有焊缝
↓
焊接后检