挤压模设计4.docx
《挤压模设计4.docx》由会员分享,可在线阅读,更多相关《挤压模设计4.docx(18页珍藏版)》请在冰豆网上搜索。
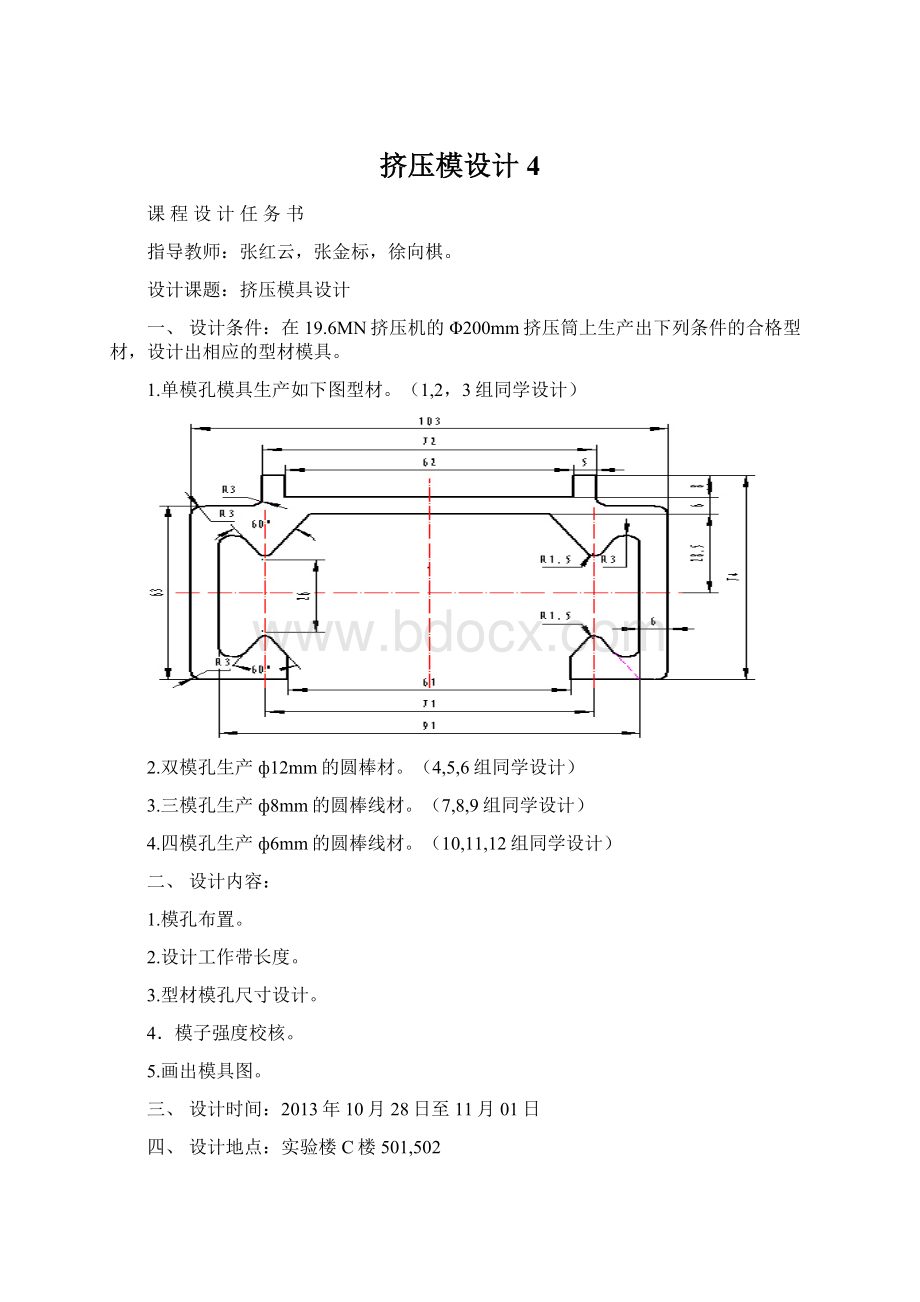
挤压模设计4
课程设计任务书
指导教师:
张红云,张金标,徐向棋。
设计课题:
挤压模具设计
一、设计条件:
在19.6MN挤压机的Φ200mm挤压筒上生产出下列条件的合格型材,设计出相应的型材模具。
1.单模孔模具生产如下图型材。
(1,2,3组同学设计)
2.双模孔生产ф12mm的圆棒材。
(4,5,6组同学设计)
3.三模孔生产ф8mm的圆棒线材。
(7,8,9组同学设计)
4.四模孔生产ф6mm的圆棒线材。
(10,11,12组同学设计)
二、设计内容:
1.模孔布置。
2.设计工作带长度。
3.型材模孔尺寸设计。
4.模子强度校核。
5.画出模具图。
三、设计时间:
2013年10月28日至11月01日
四、设计地点:
实验楼C楼501,502
五、分组情况:
组号
学生安排情况
型材金属种类
1
1010121001----1010121009,1010121158
铜及其合金
2
1010121011----1010121020,1010121056
铝及其合金
3
1010121022----1010121032,1010121155
镁及其合金
4
1010121033----1010121046,1010121154
铜及其合金
5
1010121047----1010121063,1010121152
铝及其合金
6
1010121064----1010121070,1010121150
镁及其合金
7
1010121071----1010121083,1010121149
铜及其合金
8
1010121085----1010121098,1010121148
铝及其合金
9
1010121099----1010121111,1010121147
镁及其合金
10
1010121112----1010121122,1010121146
铜及其合金
11
1010121124----1010121134
铝及其合金
12
1010121136----1010121145
镁及其合金
目录
第一章绪论1
1.1挤压技术简介1
1.2热挤压模具在有色金属生产中的应用1
1.3关于镁及镁合金1
1.4关于挤压模具设计1
第二章坯料选择2
2.1锭坯尺寸选择2
2.2挤压比计算2
2.3锭坯材料选择3
第三章模孔布置4
3.1模孔布置4
3.2模孔尺寸的确定5
3.3模孔工作带长度的确定5
3.4导流模设计5
第四章模具外形尺寸设计7
4.1模具外径D的设计7
4.2模具厚度H7
4.3挤压模结构形式与模具外形锥度7
4.4模具入口处圆角半径的确定7
4.5模具出口部位结构及尺寸8
4.6模具材料的确定9
第五章棒材模强度校核11
第六章绘制模具图12
设计小结14
参考文献15
致谢16
第一章绪论
1.1挤压技术简介
挤压是将金属毛坯放入模具模腔内,在强大压力和一定速度的作用下,迫使金属从模腔中挤出,从而获得所需形状、尺寸以及具有一定力学性能的制品。
因此,挤压加工是利用模具来控制金属流动,使金属体积大量转移来形成零件。
挤压模具是挤压生产中最重要的工具,它的结构形式、各部分尺寸、模具材料、模具的装配形式等,对挤压力、金属流动的均匀性、制品尺寸的稳定性、制品表面质量以及模具自身的使用寿命等都产生极大的影响。
1.2热挤压模具在有色金属生产中的应用
在当代工业制品和生活制品中,有相当部分金属构件的成品或半成品是经过压力加工方法生产而得的。
采用模具加工成形金属构件,具有生产效率高,质量好,节省材料,成本低,以及规格灵活多变等特点,近几年来,在国民经济建设的各个领域中,得到了广泛的应用。
模具是金属压力加工的基础,模具的设计与制造技术是金属压力加工的核心,而模具的质量和使用寿命是决定金属压力加工过程是否经济可行的关键。
模具技术特别是设计制造精密,复杂,大型,寿命长的模具是衡量一个国家工业水平的重要标志之一,因此有“模具是工业之母”之说。
1.3关于镁及镁合金
镁是具有密排六方晶格的金属,滑移系只有3个,与铝、铜相比,镁的塑性是很低的。
冷挤压镁是比较困难,但当加热到200℃以上时,镁的塑性便得到较大的提高。
纯镁中的杂质元素常见得有铝、钠、铁、硅、钾、铜、镍等。
它们的存在使镁的性能发生了不好的改变,因此,镁中应控制这些杂质的含量。
镁及镁合金的强度重量比很高,故使用广泛。
镁及镁合金还具有良好的加工切削性能,并可以进行时效强化。
镁及镁合金的挤压性在室温下很差,但在高温下,却有较好的挤压性能。
一般对其毛坯进行退火处理以减小其变形抗力。
退火后的毛坯在挤压之前仍需进行长时间加热,以保证温度均匀和多相元的溶解,提高其可挤压性,一般加热时间按50mm直径加热1h计算。
镁及镁合金的挤压速度也需要严格的控制,一般不超过30m/min,对于有些难变形合金不能超过0.3~1m/min。
1.4关于挤压模具设计
在挤压设计的过程中挤压工艺条件:
应考虑挤压温度、挤压速度、润滑、模具(种类、形状、尺寸等)、切压余、淬火、冷却、切头切尾等多方面的因素。
其中,选择挤压模外形尺寸、工作带长度、模孔尺寸是最核心的问题,有以下的选择原则:
1)保证产品表面质量原则;
2)保证挤压模强度的原则;
3)保证产品内在质量的原则;
4)经济上的优化原则:
生产成本最低、成材率最大、产量最高。
第二章坯料选择
2.1锭坯尺寸选择
锭坯尺寸选择得是否合理,直接影响到挤压制品的质量、成品率、生产率等技术经济指标。
锭坯尺寸(直径和长度)越大,制品越长,从而使切头尾、切压余的几何损失和挤压周期内的辅助时间所占的比例降低。
对压余所导致的金属几何损失,增大直径或者增加长度对成品率的影响不同。
锭坯体积一定时,增大直径和减短长度使几何损失增加,减小直径增加长度,几何损失减小。
2.1.1锭坯直径选择
选择锭坯直径时,一般应在满足制品断面机械性能要求和均匀性要求的前提下,尽可能采用较小的挤压比。
但是,在挤压外接圆大的复杂形状断面型材时,要考虑模孔轮廓不能太靠近挤压筒壁,以免制品出现分层缺陷。
多孔模挤压时,除上述因素外,还应考虑各模孔间的最小距离,既保证各模孔间流动速度均匀,又要考虑挤压模的强度。
用以挤压棒材的锭坯一般为实心圆锭坯。
计算锭坯直径时,应综合考虑挤压筒直径、锭坯直径偏差量、加热膨胀后仍能顺利进入筒内等因素。
按填充系数计算:
(2-1)
式中:
Dp锭坯外径;
D0挤压筒直径;
c填充系数,c=1.07~1.15。
由设计条件知,D0=200mm,取c=1.10,得Dp=190mm。
2.1.2坯料长度计算
在实际生产中,坯料一般是圆柱形的,在挤压有色金属时,坯料长度L0为直径的2.5~3.5倍。
则
L0=(2.5~3.5)Dp(2-2)
计算得L0=(2.5~3.5)190mm=475~669mm,取L0=500mm。
2.2挤压比计算
在挤压生产中,金属的变形量大小常用挤压比或加工率()来表示。
挤压比是指挤压成形前锭坯充满挤压筒时的断面积与挤成形后制品断面积总和之比值,以表示:
(2-3)
式中:
Dt挤压筒直径;
dk棒材直径;
n同时挤压制品的根数或模孔数。
由条件可知,Dt=200mm;dk=6mm;n=4,计算得
。
2.3锭坯材料选择
从表2-1中热挤压各种金属材料时工艺参数值,可以选择镁及合金中MB2作为锭坯的材料。
综上,选择190500mm的MB2镁合金进行挤压。
表2-1热挤压各种金属材料时工艺参数值
金属材料
挤压温度/℃
挤压比
流出速度/(ms-1)
单位及压力/MPa
镁及
镁合金
纯镁
MB2,MB5,MB7
镁铝合金
350~440
300~400
300~420
≤100
10~(50~80)
10~80
0.25~0.50
0.016~0.16
0.008~1.25
≤800
≤1000
第三章模孔布置
3.1模孔布置
采用多孔棒材模时,金属流动要比单孔模均匀,故可减少中心缩尾形成的几率。
但是,如果模孔排列不当,会使挤出的制品长短不齐,增加几何废料,恶化表面质量;如果模孔靠近挤压筒边缘,也会使制品表面产生起皮、分层等缺陷。
此外,多模孔过于靠近挤压筒边缘时由于内侧金属供应量大、流动速度快,而外侧由于金属供应量不足,流动速度慢,会造成制品出现外侧裂纹;当模孔太靠近挤压筒中心时,外侧金属供应量大于内侧,则制品易出现内侧裂纹。
图3-1所示,表示了模孔分布对制品长度的影响,从而了解模孔位置布置的重要性,故应将多孔模模孔的理论重心均匀地分布在距模具中心和挤压边缘有适当距离的同心圆周上。
多模孔的同心圆直径D心与挤压筒直径Dt之间的关系可以按以下经验公式来确定:
D心
D心=
(3-1)
式中:
D心多孔模模孔断面中心分布的同心圆直径;
Dt挤压筒内径;
n模孔数目(n2);
经验系数,一般取2.5~2.8;n值较大时取下限,挤压筒内径大时取上限,一般取2.6。
根据上式,取=2.51,计算,D心=
。
D心通过上式求出后,还必须考虑节约模具钢材和工模具规格的系列化及互换性(如模垫、导路的通用性等),再对D心进行必要的调整。
3.2模孔尺寸的确定
模孔尺寸的确定主要考虑挤压制品的金属成分、断面形状、尺寸偏差、各部位几何形状特点和型材的冷却收缩量、张力矫直时的断面收缩量等因素的综合影响来进行设计或计算确定。
若用A表示模孔长度,则用以下算式对棒材模进行计算:
A=A0(1+k)(3-2)
式中:
A0棒材断面的名义尺寸,圆棒A0为直径;
k模孔裕量系数,见表3-1。
由表3-1查得,k=1.0~1.2,取k=1.1,则A0=6mm,A=6(1+1.1%)mm=6.1mm。
表3-1不同金属模孔裕量系数k/%
金属种类
孔裕量系数k
紫铜
1.5
黄铜
1.0~1.2
青铜
1.7
L1~L7,LF2,LF3,LF21,LD2,LD31等
1.0~1.2
LF5,LY11,LY12,LD5,LD8,LC4等
0.7~1.0
MB1,MB2,MB15
1.0~1.2
高镁合金
1.0~1.2
3.3模孔工作带长度的确定
棒材模的工作带长度是决定棒材尺寸精度和表面质量的基本参数。
工作带过长,容易在其表面粘结金属,使制品表面出现部分毛刺、麻面等缺陷;工作带过短,不能稳定地控制棒材,常易出现椭圆等缺陷,同时,由于工作带易磨损,致使模具寿命缩短。
棒材模的工作带长度可根据被挤压金属的不同有不同的选择。
在挤压铝、镁合金圆棒时,模孔的工作带长度可根据棒材的直径确定如下表3-2所示。
由于挤压制品棒材直径40,所以模孔工作带长度取值范围为2~3mm,则取模孔工作带长度为2mm。
表3-2模孔工作带长度经验值表
棒材直径/mm
模孔工作带长度/mm
40
2~3
40~70
4
70~120
5
130~280
6~8
3.4导流模设计
由于挤压制品的挤压比过大,为保证锭坯的顺利挤压,采用导流模。
导流模的基本结构形式有两种:
一种是将导流模和型材模分开制造,然后再组装成一个整体使用;另一种是直接将导流模和型材模加工成一个整体。
为了提高模具的利用率,选择导流模和型材模分开的结构。
导流模的设计原则是有利于金属预分配和调整金属流速。
一般来说导流模的轮廓尺寸比型材的外形轮廓尺寸大6~15mm;导流腔的深度按照挤压筒大小不同一般取15~25mm;导流孔的入口最好做成3°~15°导流角,导流模腔各部位采用圆滑过渡。
则导流模的尺寸设计为轮廓尺寸比型材的外轮廓尺寸大15mm,导流模的深度为20mm,导流角为5°,结构如图3-2所示。
第四章模具外形尺寸设计
模具的外形尺寸主要是根据挤压机吨位大小和挤压模的强度以及装配模具的相关部件结构等因素来确定,同时应当考虑模具的系列化、标准化,便于使用和管理。
4.1模具外径D的设计
为了便于制造和更换,模具外径可标准化与系列化。
模具外径尺寸标准化、系列化的必要性有三个方面:
减少模具设计与制造的工作量,降低产品成本,缩短生产周期,提高生产效率;
通用性大,互换性强,只需要配备几种规格的模支撑和模架,可节约模具钢材,容易备料,便于维修和管理;
标准化有利于提高产品的尺寸精度。
因此,对于一台挤压机来说,模具外径最好根据挤压机配备各种规格的挤压筒,有1~3中规格为宜。
表4-1所示为棒材模具外形尺寸。
因设计条件为在19.6MN挤压机的200mm挤压筒上生产6mm的圆棒线材,所以取模具的外圆直径D1为198mm。
表4-1棒材模具外形标准尺寸
挤压机能力/MN
挤压筒直径/mm
D1/mm
H/mm
7.35
11.76~14.7
19.6
34.3
49
122.5
196
85,95
115,130
170,200
270,320,370
300,360,420,500
420,500,650,800
650,800,1100
113,132
148
198
230,330
270,306,360,420
300,420,570,670,880
570,670,900,1000
16,32
32,50,70
40,60,80
60,80
60,80
60,80,120,150
80,120,150,200
3
3
3
3
6
6,10
10,15
4.2模具厚度H
模具厚度H应根据被挤压合金的变形抗力(即挤压力)的大小来考虑。
在保证模具组件(模具、模垫、垫环等)有足够的强度的条件下,模具的厚度应尽量减薄,规格应尽量减少。
但为了安装和调整方便,模具的厚度尺寸应尽量可能系列化,便于管理和使用,一般模具的厚度按下述数值(单位:
mm)选用:
20,25,30,40,50,60,70,80,90,100,110
在挤压机设计时,通常选取单位压力为1000MPa时的挤压筒直径Dt作为基本参数来确定模具的厚度,其关系为:
H=(0.12~0.22)Dt(4-1)
将Dt=200mm带入式中,得到H=24~44mm,考虑标准化及强度等因素,将H放大,取H=80mm。
4.3挤压模结构形式与模具外形锥度
挤压模具的外形结构根据其安装方式的不同可以有不同的结构形式,卧式挤压机上用的挤压模有圆柱形、带正锥和带倒锥三种形式。
带正锥的挤压模在操作时逆着挤压方向放到模支承中,为了便于装卸,锥度不能太小,否则,人工取模困难;但如果锥度过大,则可能出现在模座靠紧挤压筒时,挤压模容易从模支承中脱落出来,故正锥的锥度在130~4范围内选取。
带倒锥的挤压模在操作时顺着挤压方向装入模支承中,其锥度为3~10,一般取6左右,为了便于机械加工挤压模的外形锥度,一般在锥体上有一段长10mm左右的圆柱部分。
由表4-1查得,=3,因此,应选择带正锥的挤压模,如4-1所示。
4.4模具入口处圆角半径的确定
入口圆角半径r选取与金属的强度、挤压温度和制品的断面尺寸、模具结构有关。
根据生产经验,r值可在表4-2所列数值范围内选取。
由于锭坯材料为镁合金,入口处圆角半径r取值范围为1~3mm,则取r=1mm。
模具入口处圆角是指被挤压金属进入工作带时,模具工作端面与工作带表面间形成的拐角r入。
这个角若为尖棱角时,在挤压过程中则易开裂或压秃、压堆,从而改变模孔尺寸,导致难以保证挤压制品的尺寸精度,因此必须采用过渡圆角半径r。
制作入口圆角半径r,还可以防止低塑性合金在挤压时产生表面裂纹,减小金属在流入模孔时的非接触变形。
但是,圆角增大了接触磨损面积,可能会引起及压力增加。
表4-2模具入口处圆角半径/mm
金属种类
铝合金
紫铜、黄铜
白铜
镍合金
镁合金
钢、钛合金
入口处圆角半径r
0.40~0.75
2~5
4~8
10~15
1~3
3~8
4.5模具出口部位结构及尺寸
模具的出口部分是保证成形制品能顺利通过模具并确保表面质量的重要通道。
模具出口部位又称为模孔空刀,也是指模具出口端尺寸大于模具工作带对应的模孔部分。
模孔空刀既要保证模具工作带强度,又要便于模具的加工制作,同时使制品能顺利导出模孔而不刮伤其表面。
若模具空刀尺寸过大,会大大削弱工作带强度,引起工作带过早变形和压塌,明显降低模具的使用寿命。
因此,对于圆形管、棒挤压模来说,可按以下方式选取:
空刀直径:
d1=d+(3~5)(4-2)
式中:
d模孔直径(即模孔长度)。
由公式(4-2)得d=6.1mm,则d1=6.1+(3~5)mm=9.1~11.1mm,取d1=10mm。
一般情况下,对于模孔形状的挤压模,模孔空刀可选用比模孔边线扩大距离h1可取1.5~2.5mm的形式。
因此模具出口部位结构,如图4-2所示,尺寸为模孔空刀比模孔边线扩大距离h1为1.95mm,空刀直径为10mm。
4.6模具材料的确定
模具的寿命不仅与挤压工艺、模具设计制造工艺过程有关,而且还与模具的材质选择有重要的关系。
对于热挤压模具的材质,必须具备以下条件:
(1)具有足够的高温强度。
即模具能承受高温、高压作用,不发生屈服变形和断裂,保证挤压制品获得所需尺寸精度。
(2)具有良好的抗磨损性能。
即在高温、强摩擦的挤压条件下,模具材料能抵抗金属制品长时间的、高速的、激烈的摩擦作用,而不过早出现磨损,尤其对模具工作带表面更显重要。
(3)具有足够高的抗疲劳性。
在挤压过程中,模具能承受周期性循环载荷作用而不发生断裂损坏,因此,模具材料必须具备良好的抗冲击韧性。
(4)具有良好的导热性能。
热挤压模具处于高温挤压变形过程中,由变形金属产生的大量变形热及模具与变形金属之间产生的摩擦热,直接传递给模具导致温度升高,为防止模具局部出现“过烧”现象,模具材料应具有良好的导热性能,能向外快速地散发热量。
(5)具有良好的热处理淬透性和可氮化性。
即模具材料在热处理过程中,应保证模具的强度、力学性能均匀一致。
同时,模具在使用过程中,可多次进行表面氮化处理,提高模具表面强度的耐磨性。
除此之外,模具材料还应具有良好的抗回火稳定性,良好的抗腐蚀性,较低的膨胀系数,良好的工艺制造性能,以及价格的合理性等。
由表4-3,可选取4Cr5MoSiV1作为模具的材料。
4Cr5MoSiV1模具钢,是近年来国内外广泛用于热挤压制品的一种模具材料,其特点是:
具有良好的抗疲劳性能和综合机械力学性能,同时又具有良好的热处理淬透性。
表4-3热挤压模具材料选择
挤压件材料
模具材料
硬度(HRC)
铝、镁合金
4Cr5MoSiV1
47~51
4Cr5MoSiV
铜和铜合金
4Cr5MoSiV1
42~44
4Cr3Mo3SiV
5Cr4W2Mo2SiV
3Cr2W8V
4Cr4W4Co4V2Mo
钢
4Cr5MoSiV14Cr
44~48
3Mo3SiV
3Cr2W8V
第五章棒材模强度校核
对于多孔棒材模,需要对模孔之间和模孔与模具外径圆周之间的危险断面进行强度校核。
多孔棒材模的剪切强度计算公式如下:
≤
(5-1)
式中:
Q模具上承受的总压力,一般取Q=0.8P,有时为了安全起见,可取Q=P;
P挤压机的公称压力;
rx各模孔均布的同心圆半径;
d棒材直径;
n多孔模的模孔数;
[]模具材料允许的抗剪切强度,在400℃时,4Cr5MoSiV1钢取[]=(0.5~0.6)b,b由表5-1查得,则[]=(0.5~0.6)1360MPa=680~816MPa,取[]=816MPa;
H模具允许的最小厚度。
由上式可得到:
(5-2)
根据设计条件及计算,已知P=19.6MN,rx=
,H=80mm,d=6mm,n=4,则有
,H≥77.5mm,则校核通过,设计合理。
表5-1常用挤压工具钢及其机械性能
牌号
试验温度℃
力学性能
b
MPa
0.2
MPa
%
%
ak
HB
kJ/m2
热处理制度
4Cr5MoSiV1
650
20
400
450
500
550
600
1630
1360
1300
1200
1050
825
1575
1230
1135
1025
855
710
5.5
6
7
9
12
10
45.5
49
52
56
58
67
290
1050℃淬火,625℃在油中回火2小时
第六章绘制模具图
模具入口端
模具出口端
模具侧面
设计小结
在两周的实习中,遇到了很多的问题,在此之中我学会了和搭档去讨论研究结果,体会到了团队合作的重要之处。
学会运用所学知识,应用知识找出问题,并去解决问题。
同时也知道老师对于学生的指导意义。
对挤压模具设计有了比较详细的认识和理解。
同时也意识到在设计生产的时候所要解决的诸多问题,在许多方面比我们想象的要严格要求。
从坯料的选择到模孔的布置、模具的尺寸设计、模具强度的校核以及导流模的设计、到最后校核成功、完成电子档及绘制AutoCAD图纸等一系列的工序;都有着非常多的问题需要我们去解决。
在课程设计的过程中,我们不仅巩固了现在所学的模具设计的这门课程,同时将过去所学的基础专业课的到了巩固和运用。
还学会了对文档、表格的编辑以及对AutoCAD及ProE绘图软件的运用熟练程度的进一步提升。
也知道有时候书本所涉及的不足,学会去寻找资料并找到我们所需要的资料;以及综合各种资料分析出其中的相同于不同选择相对较好的资料,运用于我们的设计。
对于中挤压模具设计这个课题,我知道了在模孔布置时要考虑到产品的截面形状、尺寸、产品类型、是否是多模孔挤压等等。
在模具尺寸设计时要先计算预选尺寸,之后再根据标准准选取模具尺寸。
我们在设计的时候同时要考虑后面设计所需要哪些参数以及顺序而不是一味的只知胡乱计算。
同时校核时要考虑方方面面,同时要认真和细心,因为它所包含的内容较多。
在查阅资料时要考虑是否具有可行性等一系列问题。
在绘制轧辊图时我们要温习AutoCAD绘图软件的使用,同时在绘图时要考虑如何把图简单直观的展现出来;虽然有时很多方法都可行,但是我们要严格的要求自己,越完美越好。
参考文献
[1]樊刚.热挤压模具设计与制造基础[M].重庆:
重庆大学出版社,2001
[2]马怀宪.金属塑性加工学——挤压、拉拔与管材冷轧.[M].北京:
冶金工业出版社,1991
[3]余桂英,等.机械制图[M].大连:
大连理工大学出版社,2006
[4]余桂英,等.AutoCAD2006中文版实用教程[M].大连:
大连理工大学出版社,2006