第一届铸造工艺设计大赛.docx
《第一届铸造工艺设计大赛.docx》由会员分享,可在线阅读,更多相关《第一届铸造工艺设计大赛.docx(17页珍藏版)》请在冰豆网上搜索。
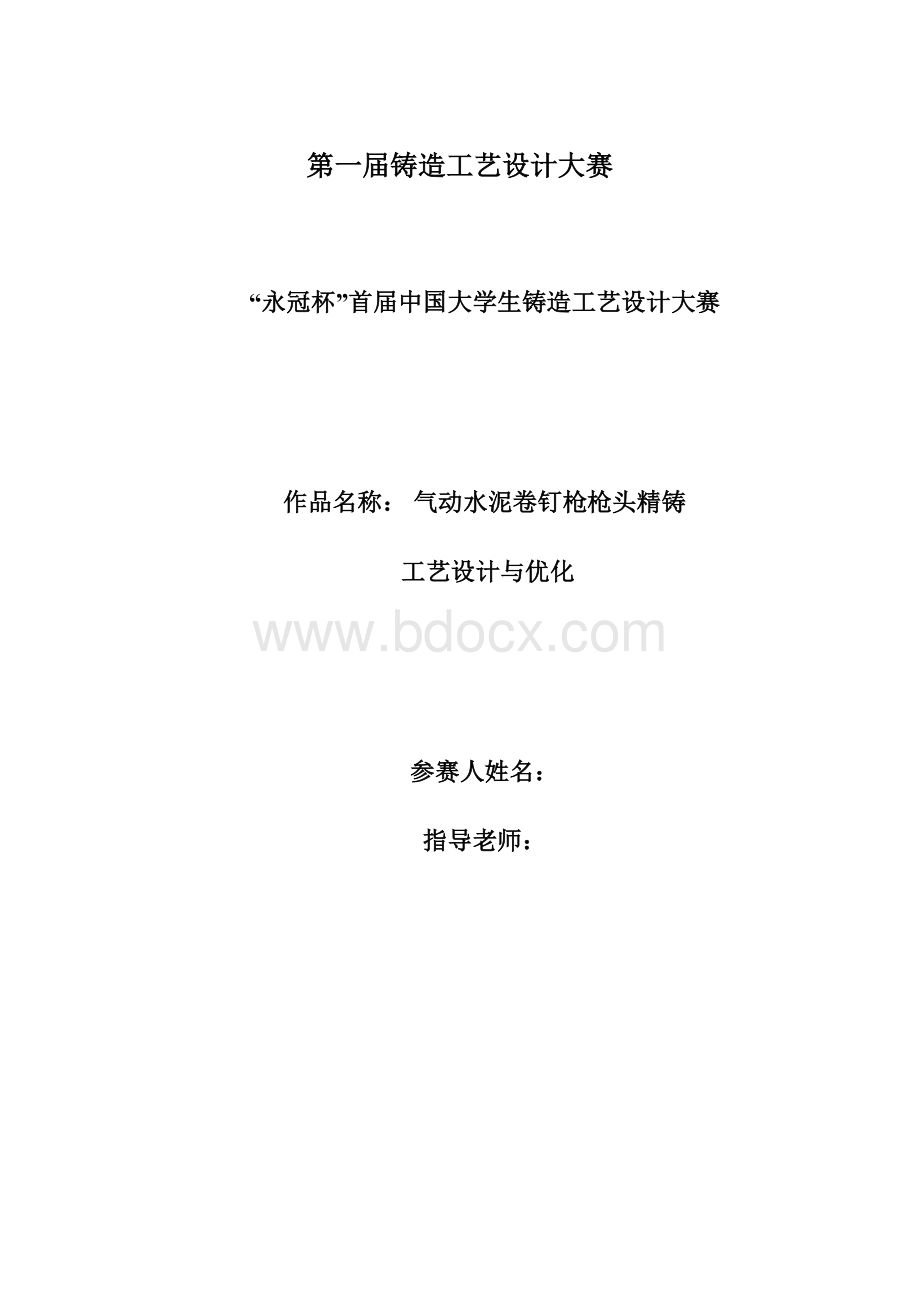
第一届铸造工艺设计大赛
“永冠杯”首届中国大学生铸造工艺设计大赛
作品名称:
气动水泥卷钉枪枪头精铸
工艺设计与优化
参赛人姓名:
指导老师:
气动水泥卷钉枪枪头精铸工艺设计与优化
本次大赛所选零件来自于某精铸企业,由于零件尺寸小,结构复杂,壁厚较小且不均匀,材料为铸钢,故采用熔模铸造工艺进行生产。
首先针对零件的结构进行工艺分析,初步制定工艺方案,然后应用Procast对工艺方案进行数值模拟,根据模拟结果对初始方案进行优化设计,并进行数值模拟。
由模拟结果可知优化方案可以继续被优化,优化之后进行模拟验证,得到最终工艺方案。
1.产品信息
零件名称:
气动水泥卷钉枪枪头
用途:
用于气动水泥卷钉枪枪头(如图1所示)
图1.气动水泥卷钉枪枪头
材质:
ZG40Cr
零件要求:
基本上受力较大,不能出现缩孔缩松。
而且由于是气动工具,法兰端面与气缸配合,所以,气密性要求较高,零件加工后不能出现缩孔缩松。
工艺方法:
熔模铸造
2.产品模型及工艺设计
产品模型见图2.1。
铸件最大长度为100mm,宽度为100mm,壁厚为15mm,位于铸件上部法兰端面,最薄处为3mm,位于铸件中部。
该铸件结构复杂,壁厚不均匀,材料为ZG40Cr。
铸件不允许出现缩孔、缩松,内外表面不允许有气孔、砂眼、夹砂等缺陷,质量要求较高。
浇注系统为顶注式,生产中设计为一模4件,见图2.2。
采用顶注式浇注系统,有利于金属液的充型和补缩,但金属液对型壁冲击力较大,易飞溅,使铸件产生夹渣和气孔等缺陷。
考虑到该铸件高度较低,结果复杂,金属液对型壁的冲击力较小,飞溅倾向小。
浇注位置位于铸件圆形法兰端面,该面为较大平面,易于浇道的清理,对铸件表面质量影响不大。
图2.1产品模型
图2.2工艺方案
3.凝固过程数值模拟流程
Procast模拟流程如图2.1所示。
4.凝固模拟前处理
4.1建立模型及网格划分
为了便于分析,将实际生产时的浇注系统进行简化,取单个铸件进行模拟分析,如图4.1。
首先使用Pro/E软件进行铸件的三维建模。
建模完毕以后,将文件转换为可被Procast接受的文件格式,如STEP(STP)。
将STEP(STP)文件导入Procast软件自带的网格划分工具MeshCAST,进行网格划分的剖分,见图4.2和图4.3。
铸件与型壳总结点数为77511个,总单元体数为343461个。
从图4.2可以看到,零件网格划分比浇注系统部分致密,这是为了保证零件部位模拟的准确性。
图4.1简化模型
图4.2铸件网格模型
图4.3型壳网格模型
4.2热物性参数
模拟中铸件材料为40Cr,其热物性参数主要包括热导率λ、比热C、热焓H、密度ρ等,见表4.1。
这些参数一般均随温度的变化而变化,所以称为变热物性参数。
40Cr的液相线温度为1491℃,固相线温度为1429℃。
耐火材料是制造型壳的主要材料。
型壳的一些主要性能都与耐火材料的物理、化学性质有关。
实际生产及模拟分析时,表面层和加固层的型壳材料分别选为锆英石和莫来石,其材料的物理、化学性质如表4.2所示。
表4.140Cr热物性参数
物性参数
200℃
400℃
600℃
800℃
1000℃
1200℃
1400℃
1600℃
密度/(kg/m3)
7690
7670
7660
7640
7635
7620
7610
7275
热焓/(KJ/Kg)
70
195
295
580
630
795
930
1310
比热/(KJ/Kg/K)
0.52
0.61
0.75
0.96
0.65
0.66
0.71
0.79
热导率/(W/m/K)
49
42
35
26
28
30
31
24
表4.2制壳所用耐火材料的物理、化学性质
材料名称
分子式
化学性质
熔化温度
(℃)
比重
(g/cm3)
线膨胀系数
a(1/℃)
20~1000℃
导热系数λ
(K/cm·s·℃)
400℃
1200℃
锆英石
ZrO2·SiO2
两性
1810
3.16
4.5x10-6
0.0029
0.0037
莫来石
3AL2O3·2SiO2
弱酸性
1775
4.5
5.1x10-6
0.005
4.3初始条件及边界条件
模拟的初始条件和边界条件与工厂实际生产相同,具体数据如下:
金属液浇注温度为1550℃;型壳焙烧温度为1000℃;浇注时间为3s;重力加速度9.8m/s2。
铸件与型壳的传热系数为300W/m2/K。
型壳与周围空气的传热系数为10W/m2/K。
5模拟分析结果与生产实际结果对比
5.1铸件充型时的固相率分析
图5.1为铸件凝固过程中内部金属液的固相率分布图。
从图5.1中可以看出,当time=42.9s时,铸件左侧金属液通道被隔断。
当time=48.4s时,铸件左侧底部出现了孤立的液相区,将此部位称为1处。
该处金属液凝固时,体积收缩无法得到补缩,易产生缩孔、缩松缺陷。
同样,当time=92.6s时,铸件右侧金属液通道被隔断。
当time=96.9s时,铸件右侧底部出现孤立的液相区,将此部位称为2处。
该处金属液凝固时,体积收缩无法得到补缩,易产生缩孔、缩松缺陷。
(a)time=42.9s
(b)time=48.4s
(c)time=92.9s
(d)time=96.9s
图5.1铸件充型时的固相率变化
5.2模拟结果与实际生产的对比
从模拟结果分析可知,图5.2(a)中铸件左侧两壁相接处即1处,易产生缩孔、缩松缺陷。
而从图5.2(b)中箭头所指部位,实际生产中产生缩松缺陷概率相当大,已达到60%。
由模拟结果分析可知,图5.2(c)中铸件右侧底部即2处,易产生缩孔、缩松缺陷。
对铸件做剖切处理,从图5.2(d)中白线圈处,产生了缩孔缺陷。
可以得出:
此次数值模拟分析结果与实际生产结果基本吻合。
(a)模拟结果1处
(b)实际结果1处
(c)模拟结果2处
(d)实际结果2处
图5.2模拟结果与实际结果对比
6工艺方案改进
6.1方案改进
针对1处缩孔、缩松缺陷,开设补缩浇道困难,则可从其冷却方式入手。
因为在凝固过程,铸件中部薄壁处金属液凝固过快,致使与1处相连的金属液体通道被隔断,无法对该处进行补缩。
可在型壳表面如图6.1红色部位包裹石棉等保温材料,减缓薄壁处的冷却速度,保证补缩通道的畅通。
对于2处缩孔、缩松缺陷,可从浇注系统入手,开设补缩浇道,专门对其补缩,如图6.2。
由于与2处相接的部分为较大平面,且距离直浇道较近,在此处开设分浇道易于清理和补缩。
图5.1包裹石棉
图6.2开设补缩浇道
6.2改进方案边界条件
此次模拟只需改变模拟的边界条件,其他工艺参数如材料设置、初始条件等都不变。
由于型壳1处部位包裹石棉,见图4.1红色部位,此处型壳传热速度比周围部位要慢,则该部分石棉与空气之间的换热系数为3W/m2/K,而其它部分与空气之间的换热系数仍为10W/m2/K。
6.3改进方案模拟结果与原方案模拟结果比较
图6.3为改进方案模拟结果与原方案模拟结果对比图,其中图6.3(a)、(c)为原方案模拟结果,图6.3(b)、(d)为改进方案模拟结果。
由图6.3(a)箭头和圆圈标示处可知,当time=42.9s时,原工艺方案的铸件由于薄壁处优先凝固,致使中部金属液体通道被割断,即模拟过程中出现断流现象,产生孤立液相区。
而从图6.3(b)箭头和圆圈标示处可知,当time=50s时,在1处并没有出现孤立的液相区,主要是因为改进方案中包裹石棉的部位,冷却慢,基本达到顺序凝固。
由图6.3(c)箭头和圆圈标示处可知,当time=92.9s时,原工艺方案的铸件在2处出现孤立的液相区。
而从图6.3(d)箭头和圆圈标示处可知,当time=102s时,优化方案的铸件从底部自下而上顺序凝固,在2处并没有出现孤立的液相区。
由以上两种方案的对比分析可知,采用优化方案,1处和2处的孤立液相区明显消失,缩孔、缩松倾向得到有效的控制,这也说明优化工艺措施是合理有效的。
(a)time=42.9s
(b)time=50s
(c)time=92.9s
(d)time=102s
原方案
改进方案
图6.3优化工艺结果与原始工艺结果对比
6.4试验验证及生产应用
基于数值分析的改进工艺措施,进行熔模铸造工艺试验,对改进后的模拟结果进行验证。
图6.4为试验方案所增加的保温石棉及增设的补缩浇道。
图6.5为优化工艺后的铸件。
从图6.5(a)可以看出,1处部位缩孔、缩松明显消失,表明在型壳表面包裹石棉,确实能够减缓铸件该部位冷却速度,保证其周围补缩通道的畅通。
同样,从图6.5(b)剖面图,可以看出缺陷2处的缩孔、缩松被消除,表明开设补缩通道确实有效,能够对该部分进行补缩。
该厂采用优化方案,铸件废品率由原来的60%减少到8%,大大减少企业生产成本。
图6.4(a)型壳包裹石棉
图6.4(b)增加的补缩浇道
图6.4改进方案
图6.5(a)表面质量
图6.5(b)内部质量
图6.5改进方案生产的铸件
7工艺方案优化
7.1方案优化
图7.1.1补缩浇道补缩作用的分析
由模拟分析结果可知:
改进工艺方案中所加的补缩浇道并没有起到补缩的作用,而是起了蓄热,调节铸件温度场的作用,使铸件达到顺序凝固,因此可以对工艺继续优化,即改变补缩浇道的结构。
如图7.1.2所示,将补缩浇道改为贴片,即在原补缩浇道下端所在部位增加一个贴片。
改进方案
优化方案
图7.1.2优化方案
7.2优化方案数值分析
图7.2优化方案数值分析
由图7.2优化方案数值分析结果可以看出:
优化方案中的贴片在铸件凝固过程中起了蓄热,调节铸件温度场,使铸件达到顺序凝固的作用,因此优化方案合理,这也说明了改进方案中补缩浇道的作用是蓄热,调节铸件温度场。
7.3试验验证及生产应用
图7.3优化方案生产的铸件
对基于数值分析的优化工艺措施进行熔模铸造工艺试验,对优化后的模拟结果进行验证。
图7.3为按优化工艺方案生产的铸件。
图7.3中的剖面图可以看出缺陷2处的缩孔、缩松被消除,表明优化方案有效,贴片的作用明显。
优化方案节省了材料的用量,节约了熔炼的成本,降低了去除浇口的难度。
因此优化方案既降低了成本又提高了生产效率。