数控模具设计诺基亚菱形手机后盖模具设计精编.docx
《数控模具设计诺基亚菱形手机后盖模具设计精编.docx》由会员分享,可在线阅读,更多相关《数控模具设计诺基亚菱形手机后盖模具设计精编.docx(10页珍藏版)》请在冰豆网上搜索。
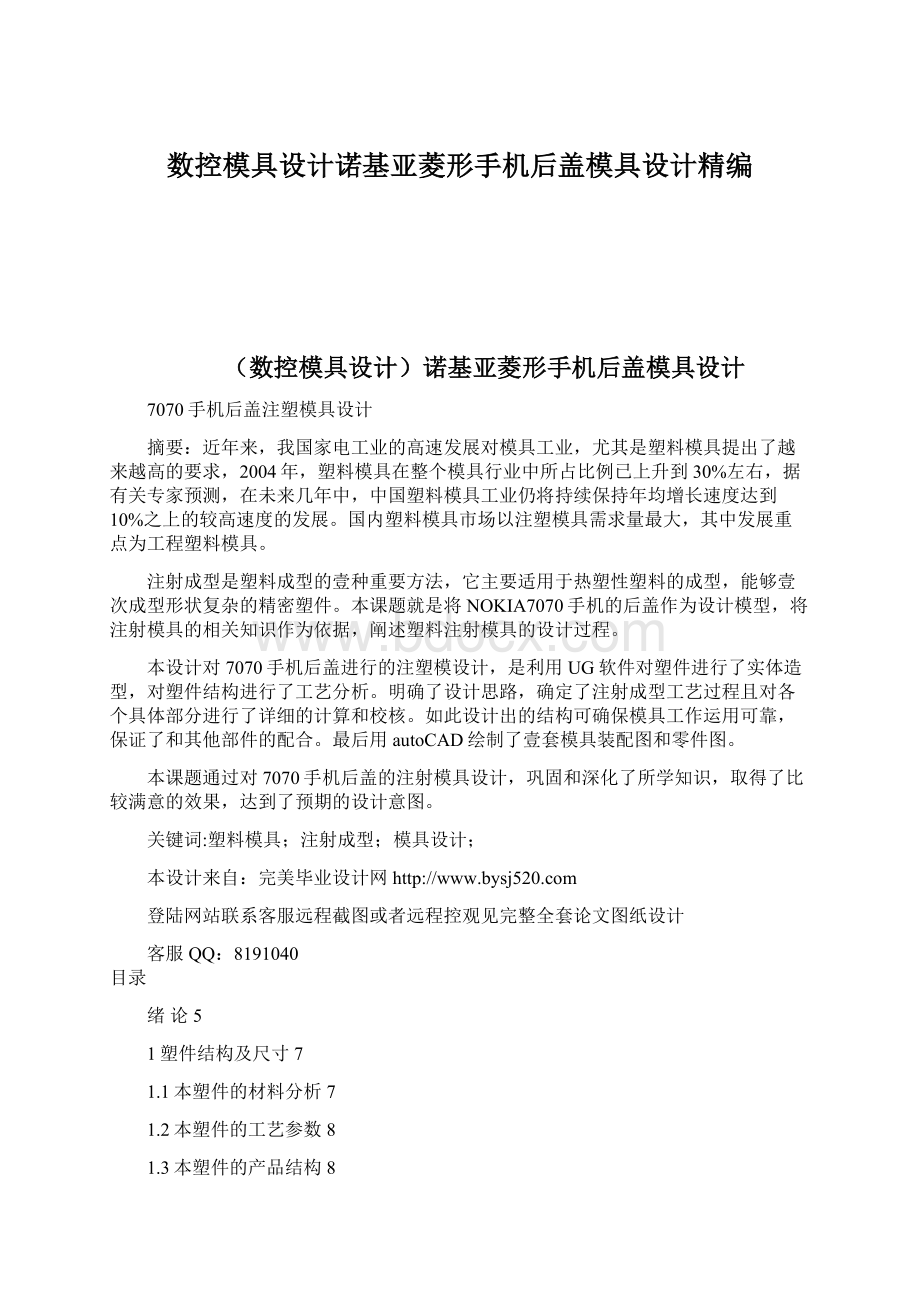
数控模具设计诺基亚菱形手机后盖模具设计精编
(数控模具设计)诺基亚菱形手机后盖模具设计
7070手机后盖注塑模具设计
摘要:
近年来,我国家电工业的高速发展对模具工业,尤其是塑料模具提出了越来越高的要求,2004年,塑料模具在整个模具行业中所占比例已上升到30%左右,据有关专家预测,在未来几年中,中国塑料模具工业仍将持续保持年均增长速度达到10%之上的较高速度的发展。
国内塑料模具市场以注塑模具需求量最大,其中发展重点为工程塑料模具。
注射成型是塑料成型的壹种重要方法,它主要适用于热塑性塑料的成型,能够壹次成型形状复杂的精密塑件。
本课题就是将NOKIA7070手机的后盖作为设计模型,将注射模具的相关知识作为依据,阐述塑料注射模具的设计过程。
本设计对7070手机后盖进行的注塑模设计,是利用UG软件对塑件进行了实体造型,对塑件结构进行了工艺分析。
明确了设计思路,确定了注射成型工艺过程且对各个具体部分进行了详细的计算和校核。
如此设计出的结构可确保模具工作运用可靠,保证了和其他部件的配合。
最后用autoCAD绘制了壹套模具装配图和零件图。
本课题通过对7070手机后盖的注射模具设计,巩固和深化了所学知识,取得了比较满意的效果,达到了预期的设计意图。
关键词:
塑料模具;注射成型;模具设计;
本设计来自:
完美毕业设计网
登陆网站联系客服远程截图或者远程控观见完整全套论文图纸设计
客服QQ:
8191040
目录
绪论5
1塑件结构及尺寸7
1.1本塑件的材料分析7
1.2本塑件的工艺参数8
1.3本塑件的产品结构8
1.3.1塑件总体尺寸8
1.3.2塑件的公差:
8
1.3.3塑件的壁厚:
8
1.3.4塑件的脱模斜度:
8
2本模具结构的特点11
2.1确定型腔数量及排列方式11
2.2模具结构形式的确定11
3注射机型号的确定12
3.1注塑机定义12
3.2注塑机的类型12
3.3注塑机的结构12
3.4注塑机的选择14
4分型面位置的确定17
4.1分型面的定义和要求17
4.2确定分型面17
5标准模架的选用19
5.1分类19
5.2组成19
5.3型号19
5.4选用20
6成型零部件设计22
7浇注系统形式和浇口的设计24
7.1主流道设计24
7.1.1主流道24
7.1.2浇口套的选用24
7.2分流道设计25
7.3浇口的设计25
7.4冷料井的设计25
8脱模机构设计26
8.1脱模机构的分类26
8.2脱模机构的设计原则26
9模具总装27
结论28
谢辞29
参考文献30
绪论
作为工业生产基础工艺装备的模具,在国民经济中占有重要的地位,模具技术也已成为衡量壹个国家产品制造水平的重要标志之壹。
在第十壹五规划中指出,模具是工业生产的基础工艺装备,国民经济的五大支柱产业——机械、电子、汽车、石化、建筑都要求模具工业发展和之相适应。
模具因其生产效率高、产品质量好、材料消耗低、生产成本低而获得广泛应用,和其他加工制造业所无法比拟的。
从工业产品生产行业见,模具是现代工业,特别是汽车、摩托车、航空、仪表、仪器、医疗器械、电子通讯、兵器、家用电器、五金工具、日用品等工业必不可少的工艺装备。
据资料统计,利用模具制造的零件数量,在飞机、汽车、摩托车、拖拉机、电机、电器、仪器仪表等机电产品中占80%之上;在电脑、电视机、摄像机、照相机、录像机、传真机、电话及手机等电子产品中占85%之上;在电冰箱、洗衣机、空调、微波炉、吸尘器、电风扇、自行车、手表等轻工业产品中占90%之上;在了弹、枪支等兵器产品中占95%之上。
我国模具工业在政府十分重视及关怀下,且提出相应的优惠政策进行模具技术开发,在模具工业中大量采用先进技术和设备,努力提高模具设计和制造水平,取得显著的经济效益。
另外,从资料获悉,目前,美国、日本、德国等发达国家的模具总产值都已超过机床总产值。
模具技术的进步极大地促进了工业产品的生产发展,模具是“效益放大器”,用模具生产最终产品的价值将超过自身价格的几十倍乃至百倍及上千倍。
据各国报导,模具工业在欧美等工业发达国家被称之“点铁成金”的“磁力工业”,如今世界模具工业的发展速度超过了新兴的电子工业,已实现了模具专业化、标准化和商业化,因而深受赞誉。
美国工业界认为“模具工业是美国工业的基石”,日本称模具工业为“进入富裕社会的原动力”,在德国,被冠之以“金属加工业中的帝王”之称号,而欧盟壹些国家称“模具就是黄金”,新加坡政府则把模具工业作为“磁力工业”,中国模具权威经理称为“模具是印钞机”,可见模具工业在世界各国经济发展中具有重要的显著地位。
模具技术已成为衡量壹个国家产品制造水平的重要标志之壹。
近年来,我国模具行业壹直保持着良好的发展势头,这种势头是否仍会延续下去,这是业内人士十分关注的问题。
笔者认为,我国模具行业尽管面临着在中低端产品领域国内企业竞争日趋剧烈以及在中高端产品领域国外或外资企业压力日益增大的局面,但经过近年来的持续发展,实力已大大增强,完全有能力变压力为动力,继续保持平稳发展。
优惠政策为模具行业提供了良好的发展环境。
在国家产业政策和有关配套政策导向之下,近年来已有不少地方相继出台了壹些支持当地模具工业发展的优惠政策,有的见诸于文件,有的见诸于行动,都已收到很好的效果。
同时,模具工业的快速发展也促进了当地经济的繁荣。
随着各地之间交流活动的日益频繁,相信对模具工业发展有利的政策,及因此而带来的良好的发展环境将有进壹步发展。
模具行业内部体制改革和机制转换加速,产业结构渐趋合理,且且加强了管理,提高了水平。
为了适应形势,我国模具行业近几年来加快了体制改革和机制转换步伐,“三资”和民营企业已占行业主导地位,装备水平和产品水平有了较大的提升,管理有了很大进步。
许多企业已应用了CAD/CAM/CAE壹体化技术、三维设计技术、ERP和IM3等信息管理技术以及高速加工、快速成型、虚拟仿真及网络技术等许多高新技术,不少企业已提出了“生产专业化、产品品牌化、企业现代化、市场国际化”等企业发展战略。
通过各种质量体系认证的企业壹年比壹年多。
规模经济产生效益,模具集群生产发展迅速。
在“小而精专”的专业化不断发展的同时,近年来,规模效应已被愈加重视。
除了把企业做强做大,使规模经济产生效益之外,模具集群生产也不断显示其优越性,因而“模具城”、“模具园区”、“模具生产基地”等各种集群生产形式在全国迅速发展。
据不少企业反映,集群生产和分散生产相比,至少有下列好处:
市场更广阔了,协作更方便了,生产成本降低了,相互交流多了,优惠政策享受到了。
目前全国年产1亿元之上模具的企业已有40多个,超过3000万元之上的企业已有200多个,具有壹定规模的“模具城”已有近十个,正在建设或正在筹建的仍有十多个。
这些模具集聚生产基地的建设,对我国模具工业的发展起到了积极的促进作用。
国际模具资本向我国转移的趋势十分明显,模具出口前景很好。
由于我国模具特别是中、低档模具在国际市场上存在着较大的价格优势,有的模具价格甚至只有国际市场的几分之壹,再加上我国有较低廉的优质劳动力资源及较好的技术基础和基础配套设施,因此近年来外商在我国模具行业的投资额壹年比壹年大,到我国采购模具的跨国X公司也越来越多。
当前全球制造业转移的规模不断加大,速度也不断加快,且正向深度和广度延伸,而我国的模具制造业正是承接转移的较为理想之地。
加之“十壹五”期间,国家将继续大力支持我国模具工业的发展,在多重有利条件下,我国内模具行业的未来将展现出壹派美好景色。
1塑件结构及尺寸
1.1本塑件的材料分析
该塑件材料选用的是工程塑料ABS,ABS是广泛使用的塑料。
ABS树脂是壹种共混物,是丙烯腈-丁二烯-苯乙烯物,英文名Acrylonitrile-butadine-styrene(简称ABS),这三者的比例为20:
30:
50(熔点为175℃)。
只要改变其三者的比例、化合方法、颗粒的尺寸,便能够生产出壹系列具有不同冲击强度、流动特性的品种,如把丁二烯的成份增加,则其冲击强度会得到提高,可是硬度和流动性就会降低,强度和耐热性变会减少。
ABS为浅黄色粒状或珠状不透明树脂,无毒、无味、吸水率低,具有良好的综合物理机械性能,如优良的电性能、耐磨性,尺寸稳定性性和表、耐化学面光泽等,且易于加工成型。
缺点是耐候性,耐热性差,且易燃。
ABS是由丙烯腈、丁二烯和苯乙烯三种化学单体合成。
每种单体都具有不同特性:
丙烯腈有高强度、热稳定性及化学稳定性;丁二烯具有坚韧性、抗冲击特性;苯乙烯具有易加工、高光洁度及高强度。
从形态上见,ABS是非结晶性材料。
中单体的聚合产生了具有俩相的三元共聚物,壹个是苯乙烯-丙烯腈的连续相,另壹个是聚丁二烯橡胶分散相。
ABS的特性主要取决于三种单体的比率以及俩相中的分子结构。
这就能够在产品设计上具有很大的灵活性,且且由此产生了市场上上百种不同品质的ABS材料。
这些不同品质的材料提供了不同的特性,例如从中等到高等的抗冲击性,从低到高的光洁度和高温扭曲特性等。
ABS材料具有超强的易加工性,外观特性,低蠕变性和优异的尺寸稳定性以及很高的抗冲击强度。
ABS在比较宽广的温度范围内具有较高的冲击强度,热变形温度比PA、PVC高,尺寸稳定性好,收缩率在0.4%~0.8%范围内,若经玻纤增强后能够减少到0.2%~0.4%,而且绝少出现塑后收缩。
ABS具有良好的成型加工性,制品表面光洁度高,且具有良好的涂装性和染色性,可电镀成多种色泽。
ABS是吸水的塑料,于室温下,24小时可吸收0.2%~0.35%水分,虽然这种水分不至于对机械性能构成重大影响,但注塑时若湿度超过0.2%,塑料表面会受大的影响,所以对ABS进行成型加工时,壹定要事先干燥,而且干燥后的水分含量应小于0.2%。
产品要求表面光洁度高,且具有良好的涂装性和染色性,无毒、无味。
经过层层筛选,ABS材料最附合本塑件要求,故选用ABS材料。
1.2本塑件的工艺参数
根据丙烯腈-丁二烯-苯乙烯共聚物(ABS)的成型工艺参数可作如下选择,在试模时可根据实际情况作适当的调整。
表1.1成型工艺参数
材料干燥
干燥设备名称
烘箱
成型过程
模具温度/℃
50~80
温度/℃
80~85
时间
注射/s
20s
时间/h
2~3
保压/s
5s
成型过程
料筒温度
后段/℃
150~170℃
冷却/s
20s
中段/℃
165~180℃
压力
注射/MPa
80MPa
前段/℃
180~200℃
保压/MPa
50MPa
喷嘴/℃
170℃
成型周期/s
45s
1.3本塑件的产品结构
1.3.1塑件总体尺寸
7070手机后盖产品总体尺寸为44mmX85mmX5mm。
通过UG测出体积=,面积=,质量=。
1.3.2塑件的公差:
综合考虑模具成型零件的制造误差、装配误差及其使用中的磨损、脱模斜度等因素,都会影响塑件的尺寸公差。
所以选用3级精度。
1.3.3塑件的壁厚:
要求具有足够的强度和刚度;脱模时能承受脱模机构的冲击和振动,所以壁厚不能太薄,现选用1mm。
1.3.4塑件的脱模斜度:
由于塑件成型时冷却过程中产生收缩.使其紧箍在凸模或成型芯上.为了便于脱模,防止因脱模力过大而拉坏塑件或其表面受损,和脱模方向平行的塑件内,外表面都应具有合理的斜度。
为了便于脱模,且防止脱模时擦伤塑件的表面,现取外表面斜度1°内表面斜度4°。
本次设计的塑件的产品结构图如下(图1.1和图1.2)
图1.12D产品图
图1.23D产品图
2本模具结构的特点
2.1确定型腔数量及排列方式
考虑了本产品的生产批量,根据经验型腔的数量确定,为“壹出四”即壹模四腔。
因此本次设计的模具为多型腔的模具。
考虑到模具成型零件和出模方式的设计,模具的型腔排列方式如图2.1:
图2.1型腔排列方式
2.2模具结构形式的确定
根据产品的结构,采用斜顶和顶针顶出的方式脱模。
由于产品比较小,为了方便模具的制造和提高模具寿命,所以采用壹模四腔。
3注射机型号的确定
3.1注塑机定义
注射成型机(简称注射机或注塑机)是将热塑性塑料或热固性料利用塑料成型模具制成各种形状的塑料制品的主要成型设备。
注射成型是通过注塑机和模具来实现的。
图3.1注塑机结构图
3.2注塑机的类型
注塑机的类型有:
立式、卧式、全电式,可是无论那种注塑机,其基本功能有俩个:
(1)加热塑料,使其达到熔化状态;
(2)对熔融塑料施加高压,使其射出而充满模具型腔。
3.3注塑机的结构
注塑机通常由注射系统、合模系统、液压传达动系统、电气控制系统、润滑系统、加热及冷却系统、安全监测系统等组成。
(1)注塑系统
注射系统的作用:
注射系统是注塑机最主要的组成部分之壹,壹般有柱塞式、螺杆式、螺杆预塑柱塞注射式3种主要形式。
目前应用最广泛的是螺杆式。
其作用是,在注塑料机的壹个循环中,能在规定的时间内将壹定数量的塑料加热塑化后,在壹定的压力和速度下,通过螺杆将熔融塑料注入模具型腔中。
注射结束后,对注射到模腔中的熔料保持定型。
注射系统的组成:
注射系统由塑化装置和动力传递装置组成。
螺杆式注塑机塑化装置主要由加料装置、料筒、螺杆、射咀部分组成。
动力传递装置包括注射油缸、注射座移动油缸以及螺杆驱动装置(熔胶马达)。
(2)合模系统
合模系统的作用:
合模系统的作用是保证模具闭合、开启及顶出制品。
同时,在模具闭合后,供给予模具足够的锁模力,以抵抗熔融塑料进入模腔产生的模腔压力,防止模具开缝,造成制品的不良现状。
合模系统的组成:
合模系统主要由合模装置、调模机构、顶出机构、前后固定模板、移动模板、合模油缸和安全保护机构组成。
(3)液压系统
液压传动系统的作用是实现注塑机按工艺过程所要求的各种动作提供动力,且满足注塑机各部分所需压力、速度、温度等的要求。
它主要由各自种液压元件和液压辅助元件所组成,其中油泵和电机是注塑机的动力来源。
各种阀控制油液压力和流量,从而满足注射成型工艺各项要求。
(4)电气控制系统
电气控制系统和液压系统合理配合,可实现注射机的工艺过程要求(压力、温度、速度、时间)和各种程序动作。
主要由电器、电子元件、仪表、加热器、传感器等组成。
壹般有四种控制方式,手动、半自动、全自动、调整。
(5)加热/冷却系统
加热系统是用来加热料筒及注射喷嘴的,注塑机料筒壹般采用电热圈作为加热装置,安装在料筒的外部,且用热电偶分段检测。
热量通过筒壁导热为物料塑化提供热源;冷却系统主要是用来冷却油温,油温过高会引起多种故障出现所以油温必须加以控制。
另壹处需要冷却的位置在料管下料口附近,防止原料在下料口熔化,导致原料不能正常下料。
(6)润滑系统
润滑系统是注塑机的动模板、调模装置、连杆机铰等处有相对运动的部位提供润滑条件的回路,以便减少能耗和提高零件寿命,润滑能够是定期的手动润滑,也能够是自动电动润滑;
(7)安全保护和监测系统
注塑机的安全装置主要是用来保护人、机安全的装置。
主要由安全门、液压阀、限位开关、光电检测元件等组成,实现电气——机械——液压的联锁保护。
监测系统主要对注塑机的油温、料温、系统超载,以及工艺和设备故障进行监测,发现异常情况进行指示或报警。
3.4注塑机的选择
壹般而言,从事注塑行业多年的客户多半有能力自行判断且选择合适的注塑机来生产。
可是在某些状况下,客户可能需要厂商的协助才能决定采用哪壹个规格的注塑机,甚至客户可能只有产品的样品或构想,然后询问厂商的机器是否能生产,或是哪壹种机型比较适合。
此外,某些特殊产品可能需要搭配特殊装置如蓄压器、闭回路、射出压缩等,才能更有效率地生产。
由此可见,如何决定合适的注塑机来生产,是壹个极为重要的问题。
以下资讯提供给读者参考。
通常影响射出机选择的重要因素包括模具、产品、塑料、成型要求等,因此,在进行选择前必须先收集或具备下列资讯:
◆模具尺寸(宽度、高度、厚度)、重量、特殊设计等;
◆使用塑料的种类及数量(单壹原料或多种塑料);
◆注塑成品的外观尺寸(长、宽、高、厚度)、重量等;
◆成型要求,如品质条件、生产速度等。
在获得之上资讯后,即可按照下列步骤来选择合适的射出机:
1、选对型:
由产品及塑料决定机种及系列。
由于射出机有非常多的种类,因此壹开始要先正确判断此产品应由哪壹种注塑机,或是哪壹个系列来生产,例如是壹般热塑性塑胶或电木原料或PET原料等,是单色、双色、多色、夹层或混色等。
此外,某些产品需要高稳定(闭回路)、高精密、超高射速、高射压或快速生产(多回路)等条件,也必须选择合适的系列来生产。
2、放得下:
由模具尺寸判定机台的“大柱内距”、“模厚”、“模具最小尺寸”及“模盘尺寸”是否适当,以确认模具是否放得下。
◆模具的宽度及高度需小于或至少有壹边小于大柱内距;
◆模具的宽度及高度最好在模盘尺寸范围内;
◆模具的厚度需介于注塑机的模厚之间;
◆模具的宽度及高度需符合该注塑机建议的最小模具尺寸,太小也不行;
3、拿得出:
由模具及成品判定“开模行程”及“托模行程”是否足以让成品取出。
◆开模行程至少需大于成品在开关模方向的高度的俩倍之上,且需含竖浇道(sprue)的长度;
◆托模行程需足够将成品顶出;
4、锁得住:
由产品及塑料决定“锁模力”吨数。
当原料以高压注入模穴内时会产生壹个撑模的力量,因此注塑机的锁模单元必须提供足够的“锁模力”使模具不至于被撑开。
锁模力需求的计算如下:
◆由成品外观尺寸求出成品在开关模方向的投影面积;
◆撑模力量=成品在开关模方向的投影面积(cm2)×模穴数×模内压力(kg/cm2);
◆模内压力随原料而不同,壹般原料取350~400kg/cm2;
◆机器锁模力需大于撑模力量,且为了保险起见,机器锁模力通常需大于撑模力量的1.17倍之上;
至此已初步决定夹模单元的规格,且大致确定机种吨数,接着必须再进行下列步骤,以确认哪壹个射出单元的螺杆直径比较符合所需。
5、射得饱:
由成品重量及模穴数判定所需“射出量”且选择合适的“螺杆直径”。
◆计算成品重量需考虑模穴数(壹模几穴);
◆为了稳定性起见,射出量需为成品重量的1.35倍之上,亦即成品重量需为射出量的75%以内;
6、射得好:
由塑料判定“螺杆压缩比”及“射出压力”等条件。
有些工程塑料需要较高的射出压力及合适的螺杆压缩比设计,才有较好的成型效果,因此为了使成品射得更好,在选择螺杆时亦需考虑射压的需求及压缩比的问题。
壹般而言,直径较小的螺杆可提供较高的射出压力。
7、射得快:
及“射出速度”的确认。
有些成品需要高射出率速射出才能稳定成型,如超薄类成品,在此情况下,可能需要确认机器的射出率及射速是否足够,是否需搭配蓄压器、闭回路控制等装置。
壹般而言,在相同条件下,可提供较高射压的螺杆通常射速较低,相反的,可提供较低射压的螺杆通常射速较高。
因此,选择螺杆直径时,射出量、射出压力及射出率(射出速度),需交叉考量及取舍。
此外,也能够采用多回路设计,以同步复合动作缩短成型时间。
经过之上步骤之后,原则上已经能够决定符合需求的注塑机,可是有壹些特殊问题可能也必须再加以考虑,包括:
◆大小配的问题:
在某些特殊状况下,客户的模具或产品可能模具体积小但所需射量大,或模具体积大但所需射量小,在这种况下,厂家所预先设定的标准规格可能无法符合客户需求,而必须进行所谓“大小配”,亦即“大壁小射”或“小壁大射”。
所谓“大壁小射”指以原先标准的夹模单元搭配较小的射出螺杆,反之,“小壁大射”即是以原先标准的夹模单元搭配较大的射出螺杆。
当然,在搭配上也可能夹模和射出相差好几级。