工业自动化专业毕业设计论文基于PLC的供水控制系统设计.docx
《工业自动化专业毕业设计论文基于PLC的供水控制系统设计.docx》由会员分享,可在线阅读,更多相关《工业自动化专业毕业设计论文基于PLC的供水控制系统设计.docx(21页珍藏版)》请在冰豆网上搜索。
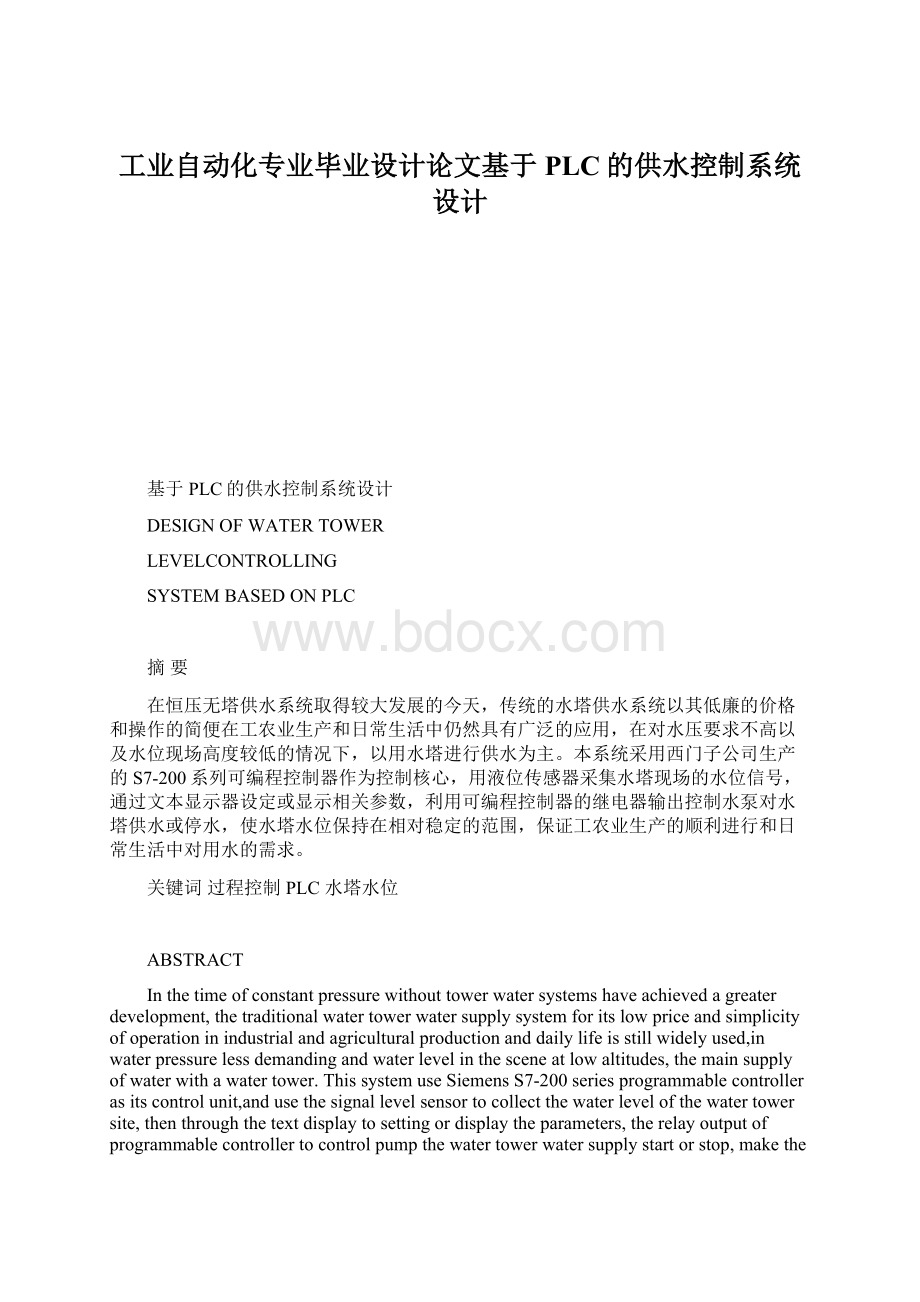
工业自动化专业毕业设计论文基于PLC的供水控制系统设计
基于PLC的供水控制系统设计
DESIGNOFWATERTOWER
LEVELCONTROLLING
SYSTEMBASEDONPLC
摘要
在恒压无塔供水系统取得较大发展的今天,传统的水塔供水系统以其低廉的价格和操作的简便在工农业生产和日常生活中仍然具有广泛的应用,在对水压要求不高以及水位现场高度较低的情况下,以用水塔进行供水为主。
本系统采用西门子公司生产的S7-200系列可编程控制器作为控制核心,用液位传感器采集水塔现场的水位信号,通过文本显示器设定或显示相关参数,利用可编程控制器的继电器输出控制水泵对水塔供水或停水,使水塔水位保持在相对稳定的范围,保证工农业生产的顺利进行和日常生活中对用水的需求。
关键词过程控制PLC水塔水位
ABSTRACT
Inthetimeofconstantpressurewithouttowerwatersystemshaveachievedagreaterdevelopment,thetraditionalwatertowerwatersupplysystemforitslowpriceandsimplicityofoperationinindustrialandagriculturalproductionanddailylifeisstillwidelyused,inwaterpressurelessdemandingandwaterlevelinthesceneatlowaltitudes,themainsupplyofwaterwithawatertower.ThissystemuseSiemensS7-200seriesprogrammablecontrollerasitscontrolunit,andusethesignallevelsensortocollectthewaterlevelofthewatertowersite,thenthroughthetextdisplaytosettingordisplaytheparameters,therelayoutputofprogrammablecontrollertocontrolpumpthewatertowerwatersupplystartorstop,makethewatertowerwaterlevelmaintainedatarelativelystablerange,tomakesurethesmoothprogressoftheindustrialandagriculturalproductionanddailylifeinthedemandforwater.
KEYWORDSprocesscontrolPLCwaterleveloftower
目录
中文摘要I
英文摘要II
1引论1
2S7-200可编程控制器3
2.1S7-200可编程控制器的组成3
2.2S7-200可编程控制器的工作原理5
3液位传感器的选型7
3.1液位传感器的分类及选用方法7
3.2静压投入式液位传感器的工作原理7
4硬件方案的设计9
4.1总体方案9
4.1.1控制方案的分析9
4.1.2控制系统的I/O点及地址分配9
4.2PLC系统的选型9
4.2.1CPU模块9
4.2.2扩展模块10
4.2.3文本显示器10
4.3电源的设计10
4.4硬件接线图11
4.5主电路接线图11
4.6元器件清单12
5软件的设计13
5.1程序流程图13
5.2文本显示器的组态13
5.3程序设计17
5.3.1主控制程序17
5.3.2液位显示程序18
5.3.3液位上下限值设定程序18
5.3.4液位上下限设定值限制程序19
结束语22
致谢23
参考文献24
1引论
1.1PLC控制技术的发展过程
20世纪70年代初出现了微处理器,人们很快将其引入可编程控制器,使PLC增加了运算、数据传送及处理等功能,完成了真正具有计算机特征的工业控制装置。
此时的PLC为微机技术和继电器常规控制概念相结合的产物。
个人计算机发展起来后,为了方便和反映可编程控制器的功能特点,可编程序控制器定名为ProgrammableLogicController(PLC)。
20世纪70年代中末期,可编程控制器进入实用化发展阶段,计算机技术已全面引入可编程控制器中,使其功能发生了飞跃。
更高的运算速度、超小型体积、更可靠的工业抗干扰设计、模拟量运算、PID功能及极高的性价比奠定了它在现代工业中的地位。
20世纪80年代初,可编程控制器在先进工业国家中已获得广泛应用。
世界上生产可编程控制器的国家日益增多,产量日益上升。
这标志着可编程控制器已步入成熟阶段。
20世纪80年代至90年代中期,是PLC发展最快的时期,年增长率一直保持为30~40%。
在这时期,PLC在处理模拟量能力、数字运算能力、人机接口能力和网络能力得到大幅度提高,PLC逐渐进入过程控制领域,在某些应用上取代了在过程控制领域处于统治地位的DCS系统。
20世纪末期,可编程控制器的发展特点是更加适应于现代工业的需要。
这个时期发展了大型机和超小型机、诞生了各种各样的特殊功能单元、生产了各种人机界面单元、通信单元,使应用可编程控制器的工业控制设备的配套更加容易。
1.2课题研究现状及意义
我国的水工业科技发展较快,与国际先进水平的差距正在不断缩小,水工业科技体系已初步形成,拥有一支从事水工业基础科学研究、应用研究、产品研制和工程化产业化开发的科技队伍。
但是,在水工业科技领域普遍存在着实用性差、转化率低的情况。
这已成为制约我国水工业产业化发展的关键。
在水工业科技产业化大潮到来之际,认真分析我国水工业科技发展历程,总结我国水工业科技的特点和特长是寻找水工业产业化突破口的关键。
目前,我国的供水自动化系统发展已初有成效。
供水自动化系统主要包括水厂自动化和供水管网调度自动化两个方面。
我国供水行业是推动水科技产业化的龙头。
给水行业是城市基础设施投资的主要方向之一。
在体制上,供水企业体制的变革已成为市场化发展的必然;在技术上,供水行业则面临着关键给水装备国产化、工艺技术成套设备化、自动控制现代化的迫切的技术要求。
优质供水是水工业市场化发展的新增长点,同时要倡导节约用水,提高水的重复利用率,并逐步建立完善的水工业学科体系。
完善的水工业学科体系是水工业产业发展的必要保证。
水塔是确保生活用水、生产用水的重要装备之一。
水塔供水是将水体置于一定的高度,依靠大气压力将水体通过管道送至需水现场,其过程本身并不复杂,但是实现水位的稳定,并且能够自动调节,是一项重要的任务。
本课题之所以选择以水位控制作为研究对象,就是基于我国水工业生产过程中对水位控制的需求,高效并且实用的水位控制系统不仅能为工业生产和日常生活提供良好的用水保证,同时也能起到保护水资源的作用。
1.3课题研究的主要内容
本课题的研究是以西门子公司生产的S7-200系列PLC及其相关产品为基础的,主要进行两个方面的研究:
一是PLC在实际生产中的应用,对模拟信号进行处理及对继电器输出的控制;二是研究水位控制中如何保证水位的稳定,以及通过相关设备对设定的参数进行显示及修改,实现生产过程与人的良好交流。
2S7-200可编程控制器
2.1S7-200可编程控制器的组成
S7-200PLC是德国西门子公司生产的一种小型PLC,其许多功能达到大、中型PLC的水平,而价格却和小型PLC的一样,因此,它一经推出,即受到了广泛的关注。
2.1.1电源
可编程控制器的电源在整个系统中起着十分重要的作用。
如果没有一个良好的、可靠的电源系统是无法正常工作的,因此,可编程控制器的制造商对电源的设计和制造也十分重视。
PLC一般使用220V的交流电源或24V直流电源,内部的开关电源为PLC的中央处理器、存储器等电路提供5V、±12V、24V等直流电源,整体式的小型PLC还提供一定容量的直流24V电源,供外部有源传感器使用。
PLC控制系统示意图如图2-1所示。
图2-1PLC控制系统示意图
2.1.2中央处理单元(CPU)
中央处理单元(CPU)是可编程控制器的控制中枢。
它按照可编程控制器系统程序赋予的功能接收并存储从编程器键入的用户程序和数据;检查电源、存储器、I/O以及警戒定时器的状态,并能诊断用户程序中的语法错误。
当可编程控制器投入运行时,首先它以扫描的方式接收现场各输入装置的状态和数据,并分别存入I/O映象区,然后从用户程序存储器中逐条读取用户程序,经过命令解释后按指令的规定执行逻辑或算数运算的结果送入I/O映象区或数据寄存器内。
等所有的用户程序执行完毕之后,最后将I/O映象区的各输出状态或输出寄存器内的数据传送到相应的输出装置,如此循环运行,直到停止运行。
2.1.3存储器
PLC的存储器包括系统存储器和用户存储器两部分。
系统存储器用来存放由PLC厂家编写的系统程序,并固化在ROM中,用户不能更改。
它使PLC具有基本的功能,能够完成PLC设计者规定的各项工作,。
系统程序的内容主要包括三部分:
系统管理程序、用户指令解释程序和标准程序模块与系统调用管理程序。
用户存储器包括用户程序存储器和用户数据存储器两部分。
用户程序存储器用来存储用户针对具体控制任务用规定的PLC编程语言编写的应用程序。
用户程序存储器根据所选用的存储器单元类型的不同,可以是RAM、EPROM、EEPROM存储器,其内容可以由用户任意修改或增删。
用户数据存储器可以用来存放用户程序中所使用期间的ON/OFF状态和数值、数据等。
用户存储器的大小关系到用户程序容量的大小,是反映PLC性能的重要指标之一。
2.1.4输入/输出单元
PLC的输入和输出信号类型可以是开关量、模拟量。
输入/输出接口单元包含两部分:
一部分是与被控设备相连接的接口电路,另一部分是输入和输出的映像寄存器。
输入单元接收来自用户设备的各种控制信号,外部接口电路将这些信号转换成CPU能够识别和处理的信号,并存到输入映像寄存器。
运行时CPU从输入映像寄存器读取输入信息并结合其他元器件最新的信息,按照用户程序进行计算,将有关输出的最新计算结果放到输出映像寄存器。
输出映像寄存器由输出点相对应的触发器组成,输出接口电路将其由弱电控制信号转换成现场需要的强电信号输出,以驱动电磁阀、接触器、指示灯等被控设备的执行原件。
2.1.5扩展接口
扩展接口用于将扩展单元或功能模块与基本单元相连,使PLC的配置更加灵活,以满足不同控制系统的需要。
2.1.6通信模块
为了实现“人—机”或“机—机”之间的对话,有些PLC配有一定的通信接口。
PLC通过这些通信接口可以与显示设定单元、触摸屏、打印机相连,提供方便的人机交互途径;也可以与其他的PLC、计算机以及现场总线网络相连,组成多机系统或工业网络控制系统。
2.2S7-200可编程控制器的工作原理
当可编程控制器投入运行后,其工作过程可分为三部分。
第一部分是上电处理。
机器上电后对PLC系统进行一次初始化,包括硬件初始化,I/O模块配置检查,停电保持范围设定,系统通信参数及其他初始化处理等。
第二部分是扫描过程。
PLC上电处理阶段完成以后扫描工作过程。
先完成输入处理,其次完成与其他外设的通信处理,再进行时钟、特殊寄存器更新。
当CPU处于STOP方式时,转入执行自诊断检查。
当CPU处于RUN方式时,还要完成用户程序的执行和输出处理,再转入执行自诊断检查。
第三部分是出错处理。
PLC每扫描一次,执行一次自诊断检查,确定PLC自身的动作是否正常,如CPU、电池电压、程序存储器、I/O和通信等是否异常或出错。
如检查出异常时,CPU面板上的LED及异常继电器会接通,在特殊寄存器中会存入出错代码;当出现致命错误时,CPU被强制为STOP方式,所有的扫描便停止。
PLC工作过程的中心内容包括三个阶段,即输入采样阶段、用户程序执行阶段和输出刷新阶段。
完成上述三个阶段称作一个扫描周期。
在整个运行期间,可编程控制器的CPU以一定的扫描速度重复执行上述三个阶段。
PLC扫描周期示意图如图2-2所示。
图2-2PLC扫描周期示意图
2.2.1输入采样阶段
在输入采样阶段,可编程控制器以扫描方式依次地读入所有输入状态和数据,并将它们存入I/O映象区中的相应的单元内。
输入采样结束后,转入用户程序执行和输出刷新阶段。
在这两个阶段中,即使输入状态和数据发生变化,I/O映象区中的相应单元的状态和数据也不会改变。
因此,如果输入是脉冲信号,则该脉冲信号的宽度必须大于一个扫描周期,才能保证在任何情况下,该输入均能被读入。
2.2.2用户程序执行阶段
在用户程序执行阶段,可编程控制器总是按由上而下的顺序依次地扫描用户程序(梯形图)。
在扫描每一条梯形图时,又总是先扫描梯形图左边的由各触点构成的控制线路,并按先左后右、先上后下的顺序对由触点构成的控制线路进行逻辑运算,然后根据逻辑运算的结果,刷新该逻辑线圈在系统RAM存储区中对应位的状态;或者刷新该输出线圈在I/O映象区中对应位的状态;或者确定是否要执行该梯形图所规定的特殊功能指令。
即,在用户程序执行过程中,只有输入点在I/O映象区内的状态和数据不会发生变化,而其他输出点和软设备在I/O映象区或系统RAM存储区内的状态和数据都有可能发生变化,而且排在上面的梯形图,其程序执行结果会对排在下面的凡是用到这些线圈或数据的梯形图起作用;相反,排在下面的梯形图,其被刷新的逻辑线圈的状态或数据只能到下一个扫描周期才能对排在其上面的程序起作用。
在程序执行的过程中如果使用立即I/O指令则可以直接存取I/O点。
即使用I/O指令的话,输入过程影像寄存器的值不会被更新,程序直接从I/O模块取值,输出过程影像寄存器会被立即更新,这跟立即输入有些区别。
2.2.3输出刷新阶段
当扫描用户程序结束后,可编程控制器就进入输出刷新阶段。
在此期间,CPU按照I/O映象区内对应的状态和数据刷新所有的输出锁存电路,再经输出电路驱动相应的外设。
这时,才是可编程控制器的真正输出。
3液位传感器的选型
3.1液位传感器的分类及选用方法
液位传感器是一种测量液位的压力传感器。
分为两类:
一类为接触式,包括单法兰静压/双法兰差压液位变送器、浮球式液位变送器、磁性液位变送器、投入式液位变送器、电动内浮球液位变送器、电动浮筒液位变送器、电容式液位变送器、磁致伸缩液位变送器、侍服液位变送器等。
第二类为非接触式,分为超声波液位变送器、雷达液位变送器等。
选择合适的液位传感器,首先要知道被测量的介质的情况,比如是否具有腐蚀性,其次还要知道被测量介质的高度、被测量介质所在容器的安装方式,以及是否要带现场显示等。
3.2静压投入式液位传感器的工作原理
静压投入式液位传感器如图3-1所示。
图3-1静压投入式液位传感器
静压投入式液位传感器适用于石油化工、冶金、电力、制药、供排水、环保等系统和行业的各种介质的液位测量。
精巧的结构,简单的调校和灵活的安装方式为用户轻松地使用提供了方便。
4~20mA、0~5V、0~10mA等标准信号输出方式由用户根据需要任选。
利用流体静力学原理测量液位,是压力传感器的一项重要应用。
采用特种的中间带有通气导管的电缆及专门的密封技术,既保证了传感器的水密性,又使得参考压力腔与环境压力相通,从而保证了测量的高精度和高稳定性。
静压投入式液位传感器的工作原理为:
当液位变送器投入到被测液体中某一深度时,传感器迎液面受到的压力公式为:
(3-1)
其中:
为变送器迎液面所受压力,
为被测液体密度,
为当地重力加速度,
为液面上大气压,
为变送器投入液体的深度。
同时,通过导气不锈钢将液体的压力引入到传感器的正压腔,再将液面上的大气压
与传感器的负压腔相连,以抵消传感器背面的
,使传感器测得压力为:
,显然,通过测取压力
,可以得到液位深度。
在实际应用中,水塔的水位高度一般在5米,并且现场情况不复杂,不需要太高的安全等级及技术要求,使用普通的静压投入式液位传感器可以满足系统的设计要求。
据此,可选用BPY800系列液位变送器,该传感器将扩散硅充油芯体封装在不锈钢壳体内,前端防护帽起保护传感器膜片的作用,也能使液体流畅地接触到膜片,防水导线与外壳密封连接,通气管在电缆内与外界相连,内部结构防结露设计。
BPY800型内置微型信号处理电路,可进行远程传输,具有良好的稳定性和可靠性。
考虑到水位的高度,选择测量范围为0~8米的型号即可,传输信号选用4~20mV标准电信号。
其基本参数如表3-1所示。
表3-1静压投入式液位传感器技术参数
测量范围
0~8mH₂O
供电范围
12~36VDC
输出信号
4~20mA
介质温度
-30~70℃
环境温度
-40~85℃
长期稳定性
≤0.1F·S/年
4硬件方案的设计
4.1总体方案
4.1.1控制方案的分析
水塔的一般蓄水深度为5米,将静压投入式液位传感器通过电缆线放入水塔底部,用于检测水位的深度。
以西门子S7-200系列可编程控制器作为控制核心,将液位传感器检测到的液位信号,通过模拟量输入模块输入CPU,与存储的液位上下限信号相比较。
当液位信号低于液位下限时,输出点置位,给主电路接触器的线圈通电,接通电源,启动电动机,带动水泵给水塔供水;当液位信号高于液位上限时,输出点复位,主电路接触器线圈失电,接触器断开,电动机停止,水泵停止供水。
液位信号的显示和液位上下限设定的修改通过文本显示器进行。
4.1.2控制系统的I/O点及地址分配
控制系统的I/O点及地址分配如表4-1。
表4-1输入输出信号代码和地址编号表
名称
代码
地址编号
液位高度信号
B
AIW0
水泵起停
QA1
Q0.0
4.2PLC系统的选型
4.2.1CPU模块
CPU模块的主要特点和技术规范:
(1)供电电压:
直流24V和交流220V两种供电电源电压。
(2)输出方式:
输出类型有晶体管(DC)和继电器(DC/AC)两种输出方式。
(3)集成电源:
主机集成有24V直流电源,可以直接用于传感器和执行机构的供电。
(4)高速计数:
它可以用普通输入端子捕捉比CPU扫描周期更快的脉冲信号,进行高速计数,输入脉冲频率可达200kHz。
(5)脉冲输出:
2路最大可达100kHz的高频脉冲输出,可以驱动步进电动机和伺服电动机以实现准确定位任务。
(6)集成模拟电位器:
可以用模块上的电位器来改变它对应的特殊寄存器中的数值,可以实时更改程序运行中的一些参数,如定时器/计数器的设定值和过程的控制参数等。
(7)实时时钟:
可用于对信息加注时间标记,记录机器运行时间或对过程进行时间控制。
根据对硬件的分析及输入输出点的分配可以知道,系统共有开关量输出点1个、模拟量输入点1个。
选用的CPU模块需要扩展单元。
参照西门子S7-200PLC产品目录及市场实际价格,选用主机为CPU222(AC/DC/继电器8输入/6输出)一台。
4.2.2扩展模块
由于本系统有一个模拟量输入,根据各扩展模块的特点,可以选择模拟量输入扩展模块EM231(24VDC模拟量输入,4输入),该模块可以用来连接标准的电流信号和电压信号。
通过液位传感器从现场采集的4~20mA可以和该扩展模块连接。
EM231模块的配置开关SW1、SW2、SW3分别设置为ON、ON、OFF(ON为接通,OFF为断开),此时,EM231模块满量程输入为0~20mA,满足液位传感器输出信号的要求。
4.2.3文本显示器
文本显示器,又名终端显示器,是一种单纯以文字呈现的人机互动系统。
文本显示器可以执行一下任务:
查看用户菜单和画面的层级;显示由S7-200CPU生成的报警;修改指定的程序变量;强制或取消强制I/O点;设置时间和日期;查看CPU状态。
在本设计中,需要应用文本显示器显示液位画面,并修改程序中设置的液位上下限值,选用西门子公司生产的TD200可以满足设计要求。
4.3电源的设计
4.3.1供电电源
可编程控制器一般使用市电(220V,50Hz)。
本设计采用的CPU使用交流供电,顾选用的供电电源为220V交流电,可以直接从电网中接入。
4.3.2S7-200内部直流电源
每个S7-200CPU模块均提供一个24V直流传感器电源和一个5V直流电源。
因为选用的液位传感器使用的是12~36VDC供电,故可直接使用CPU上的24V直流电源供电。
4.4硬件接线图
根据硬件方案,接线图如图4-1所示。
图4-1控制系统PLC及扩展模块接线图
4.5主电路接线图
主电路接线图如图4-2所示。
图4-2主电路接线图
4.6元器件清单
综合分析整个系统,所用到的元器件包括控制系统的组成器件、供水系统的构成及相关的执行机构,还有一些起辅助作用的器材。
元器件清单如表4-2所示。
表4-2元器件清单
元器件名称
数量
西门子S7-200CPU222AC/DC/继电器
1台
西门子S7-200EM231AI4×12位
1台
西门子TD-200文本显示器
1台
BPY800型液位传感器
1个
水泵
1台
接触器
1个
空气开关
1个
电源线
若干根
TD/CPU电缆
1根
连接线
若干根
5软件的设计
5.1程序流程图
系统的工作流程图如图5-1所示。
图5-1程序流程图
5.2文本显示器的组态
使用STEP7-Micro/WIN的文本显示向导对TD200进行组态。
启动STEP7-Micro/WIN,选择“工具”→“文本显示向导”菜单命令,显示出“简介”对话框,使用“下一步”按钮显示如图5-2所示的“选择TD型号和版本”对话框。
图5-2选择TD型号和版本
选择TD2003.0版,使用“下一步”按钮,显示如图5-3所示的“标准菜单和更新速率”对话框,不启用密码保护、实时时钟、强制等功能,更新速率选择默认“尽可能快”。
然后选择语言和字符集,设置为“中文”。
图5-3选择标准菜单和更新速率
完成上述组态以后,单击“用户菜单”图标开始为画面创建用户菜单,在框内输入“液位”,选择“添加屏幕”。
如图5-4所示。
图5-4选择添加液位显示屏幕
在表示TD设备文本显示区域的绿色区域中输入文本“液位:
”,并把此屏幕设为默认显示屏幕,然后单击插入“插入PLC数据”按钮,将变量嵌入文本信息中。
液位显示屏幕如图5-5所示。
图5-5液位显示屏幕
对嵌入画面文本中的PLC数据进行配置,包括“数据地址”、“数据格式”和“小数点右侧位数”等,液位数据的存储地址为“VD0”,数据格式为“实数”小数点右侧位数为“2”。
在显示屏幕中插入PLC数据如图5-6所示。
将“允许用户编辑此数据”前面的勾取消,此设定状态下用户无法编辑该变量。
图5-6在显示屏幕中插入PLC数据
同样,按照上述方法对液位上限和液位下限的屏幕进行组态,其中,液位上限值的地址为VD8,液位下限的地址为VD4,两者“小数点右侧位