重轨质量及发展战略研究.docx
《重轨质量及发展战略研究.docx》由会员分享,可在线阅读,更多相关《重轨质量及发展战略研究.docx(17页珍藏版)》请在冰豆网上搜索。
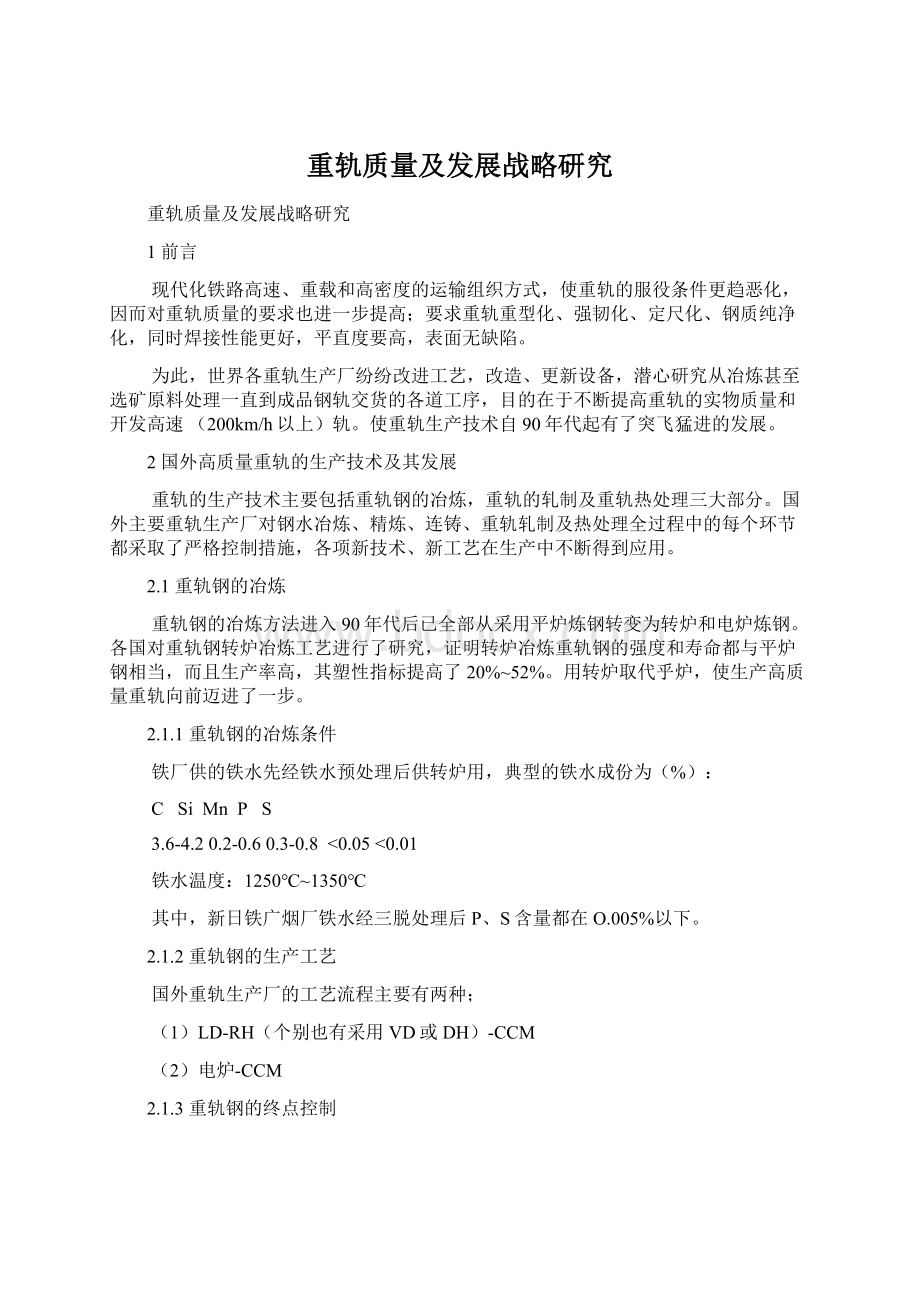
重轨质量及发展战略研究
重轨质量及发展战略研究
1前言
现代化铁路高速、重载和高密度的运输组织方式,使重轨的服役条件更趋恶化,因而对重轨质量的要求也进一步提高;要求重轨重型化、强韧化、定尺化、钢质纯净化,同时焊接性能更好,平直度要高,表面无缺陷。
为此,世界各重轨生产厂纷纷改进工艺,改造、更新设备,潜心研究从冶炼甚至选矿原料处理一直到成品钢轨交货的各道工序,目的在于不断提高重轨的实物质量和开发高速(200km/h以上)轨。
使重轨生产技术自90年代起有了突飞猛进的发展。
2国外高质量重轨的生产技术及其发展
重轨的生产技术主要包括重轨钢的冶炼,重轨的轧制及重轨热处理三大部分。
国外主要重轨生产厂对钢水冶炼、精炼、连铸、重轨轧制及热处理全过程中的每个环节都采取了严格控制措施,各项新技术、新工艺在生产中不断得到应用。
2.1重轨钢的冶炼
重轨钢的冶炼方法进入90年代后已全部从采用平炉炼钢转变为转炉和电炉炼钢。
各国对重轨钢转炉冶炼工艺进行了研究,证明转炉冶炼重轨钢的强度和寿命都与平炉钢相当,而且生产率高,其塑性指标提高了20%~52%。
用转炉取代乎炉,使生产高质量重轨向前迈进了一步。
2.1.1重轨钢的冶炼条件
铁厂供的铁水先经铁水预处理后供转炉用,典型的铁水成份为(%):
CSiMnPS
3.6-4.20.2-0.60.3-0.8<0.05<0.01
铁水温度:
1250℃~1350℃
其中,新日铁广烟厂铁水经三脱处理后P、S含量都在O.005%以下。
2.1.2重轨钢的生产工艺
国外重轨生产厂的工艺流程主要有两种;
(1)LD-RH(个别也有采用VD或DH)-CCM
(2)电炉-CCM
2.1.3重轨钢的终点控制
磷、硫的去除通常比脱碳复杂,因此总是尽可能让磷、BX在前期去除到终点要求的范围。
终点控制只进行含碳量和温度的控制,使终点碳达到要求时,出钢温度也同时达到要求。
(1)碳的控制
转炉炼钢终点碳的控制,存在着两种不同的方法:
“拉碳法”和“增碳法’,日本是采用“拉碳法”的代表,即吠练终点时不但熔池的硫,磷和温度等符合出钢要求,而且熔池中的碳(包括铁合金带人钢水中的碳)也能符合所炼钢种的规格,不需再专门向钢水中追加增碳剂增碳。
吹炼过程中及时测定熔池温度和碳量,是提高“拉碳法”优越性的重要手段。
欧洲国家普通采用的是“增碳法”,即吹炼含碳量大于0.60%的钢种时,一般采取吹到0.04%~0.06%C或更低时停吹,然后按照所炼钢种的规格,再在钢包或RH装置中进行增碳。
“增碳法”则必须采用含硫低,灰份少和干燥的增碳剂。
(2)温度的控制
不论是从顺利连铸还是从铸坯质量来说,都必须把出钢温度控制在一个较窄的适宜范围内。
这就不仅要求各炉次间的钢水温度要稳定,而且要求同一钢水包中的钢水温度要相当均匀,在浇注过程中温度变化也要小,这是连铸对出钢温度要求不同于模铸的第一个特点,也是炼钢一连铸工艺的难点。
连铸时,由于增加了中间包内的热损失,加之浇注水口断面小,浇注时间长,因此,供连铸钢水的出钢温度要比模铸钢水高出20℃~50℃,这是连铸对出钢温度控制的第二个特点和难点。
基于以上两点,一般出钢温度应高于液相线80℃~100℃。
2.1.4重轨钢的脱氧制度
由A·伊凡诺夫等人研究发现,不同的脱氧方法对76kg/m重轨断裂韧性、疲劳性及抗裂纹性有显著影响,炉内用Si-Mn-Al合金而包内用Fe-Si-Ca-V合金脱氧,在-60℃~+40℃之间有最好的疲劳性和最大的断裂韧性,并且发现在-60℃时断裂韧性值K。
包内脱氧比炉内脱氧高7%,大于+20℃时高20%。
下塔吉尔钢铁公司在160t转炉里冶炼76kg/m重轨钢,终点采用“拉碳法”,出钢温度高于液相线80℃~100℃。
包内用Si-Mn或Si-Ca脱氧,同时吹氩10min以上。
此外,各种炉外精炼技术,都可看成是包内脱氧的继续和发展,它们能在一定程度上综
合地完成脱氧、脱碳(增碳)和合金化的任务。
2.2重轨钢的炉外精炼技术及其应用
德国蒂森克虏伯钢公司鲁尔区厂第三炼钢厂是世界上唯一一家可生产125m长度重轨的厂家,其炼钢厂有240t×3转炉,后面的RH循环脱气装置中,采用微合金化方法,使得同一炉或同一序号不同炉的钢水化学成分均匀。
可生产出氢含量极低,质量可靠的重轨。
在RH法真空处理过程中通过控制脱氧作用,可保证获得十分纯净的宏观和微观组织的重轨。
该公司的重轨钢是在RH装置中增碳,从0.3%C增至所要求的含碳量,增碳过程中开始氢含量有所增加,当连续地降低罐压时,氢含量随之降低,通过控制压力和脱气量,可使氢含量达到目标值。
经对成品轨的氢含量分析与钢水经RH处理后的含量大致相同,RH处理后还使重轨中氧化物夹杂含量降低。
因为这些夹杂是影响重轨机械性能、降低重轨寿命的主要原因之一,尤其是Al2O3夹杂,在距轨头踏面5mm~10mm处出现形状不定,呈链状含铝夹杂,会使轨头踏面出现疲劳断裂,导致过早的更换钢轨。
2.3重轨钢连铸
连铸与模铸生产重轨相比较,不仅机械性能,焊接性能有提高外,金属收得串增加11.6%,总轧制道次减少,大大地降低丁能耗,生产串大幅度提高。
因此,用连铸坯生产重轨钢的现代化工艺流程在欧洲、日本等国的先进企业中已普遍应用。
1970~1971年,谢尔顿厂用413mm×230mm连铸坯以13:
1的压缩比轧成65kg/m重轨,铺于铁路干线上迄今为止没有出现问题。
1976年瑞典也采用了该工艺批量生产60kg/m和65kg/m重轨。
1978年德国蒂森公司也采用了大方坯连铸工艺生产重轨。
目前,国外用于浇注轨钢的大方坯连铸机已有20余台,生产能力约1000万t/y左右,用连铸坯生产的重轨占全部重轨产量的90%以上。
连铸坯生产重轨的质量和性能:
(1)表面质量:
用连铸坯轧制的重轨,其表面缺陷比钢锭轧制的重轨减少55%,这是连铸坯轧制重轨的一个突出特点。
(2)内部质量:
由于连铸时采用严密的保护浇注,防止钢水二次氧化,钢包、中间包及结晶器中的夹杂进一步脱除,连铸坯中夹杂总量仅为模铸的55%,钢轨内部组织比较均匀、致密,偏析、疏松等缺陷明显减少。
(3)重轨的性能:
加拿大阿尔戈马钢公司用连铸坯轧制重轨的实践表明:
由于重轨表面质量及内部质量均得到明显改善,重轨的使用性能也明显提高。
在轮压试验机上施加22700kg轮压,交变500万次,试样未出现疤皮;在落锤试验中,承受高度为6.06m,支点距为1.212m的5次落锤冲击,而不产生裂纹,疲劳试验结果也优于钢锭轧制的重轨。
目前用连铸坯生产的重轨几乎满足所有重要铁路公司的标准,对使用寿命和质量要求高的重孰都采用连铸坯生产。
2.4重轨轧制
重轨轧制是重轨生产中的重要一环,直接影响着重轨产品质量和综合机械性能,目前重轨轧制主要有两种方法:
孔型轧制法和万能轧制法。
法国的阿央日厂首创了重轨万能轧制技术,该厂研制的万能轧制原理就是用万能轧机和轧边机交替地对金属进行加工成形。
在万能轧机上,从4个垂直方向上给轧件施加很大的压下量,同时控制轨腰、轨底和轨头厚度,延伸率相当大,每道次达到1.25~1.40,轨底、轨头翼缘部分尺寸由轧边机控制,最终由半万能精轧机轧成成品,其流程为:
连铸坯在由1340mm万能轧机和1036mm轧边机组成的可逆串列式机组中轧制5道次,最后在1280mm的万能精轧机上进行精轧。
主要设备包括:
两座950mm×2250mm租轧机架,一座1340mm的万能机架,水平辊1170mm,立辊900mm;一座1036mm轧边机,轧辊920mm,辊身长度为838mm;一座1280mm的半万能精轧机架,水平辊1100mm,立辊800mm。
重轨轧制道次为:
在粗轧机上轧10道次,随后在具有大压下量的万能轧机上轧制3道次.再在轧边机上轧3个道次,最后,在半万能轧机中轧一个道次,万能轧机的总延伸系数为2.5。
日本新日铁八幡厂也采用万能轧机轧制重轨,在原有技术的基础上开发了轧边机快速移位,带支撑辊的小直径立辊以及左右异径立辊技术。
快速移位可使从万能轧机出来的轧件准确对正轧边机孔型,提高轧辊的寿命,稳定形状和尺寸,小立辊可以防止轨腰和轨底产生偏差。
左右异径小立辊技术是用小直径辊轧制轨头,用大直径辊轧制轨底,使轨头轨底压缩均匀,提高断面形状及尺寸精度。
德国蒂森钢公司,美国的伯利恒钢公司,原苏联的下塔吉尔钢铁公司也在设备改造中采用了万能轧机轧制重轨,万能轧机的优越性已被国外各生产厂家所证实,因而国外大部分重轨生产厂都采用了此项技术。
2.5重轨余热淬火
2.5.1余热淬火工艺种类
余热淬火的特点是充分利用轧后余热,对重轨进行在线淬火,获得所希望的均匀珠光体组织。
余热淬火工艺对钢轨的材质提出了更为严格的要求。
近十年来,随着电子计算机技术的普及应用,使余热淬火技术取得了突破性的发展,国外目前主要采用的余热淬火工艺有以下几类。
(1)喷水淬火工艺
喷水余热淬火是利用水介质对轧后钢轨的头部底部及腰部进行喷水预冷,随后空冷,完成奥氏体向珠光体的转变.喷水冷却重轨的温度大于900℃,冷却终止温度一般控制在450℃~650℃,具体操作如下:
重轨从终轧机架出来.经热锯锯成预定长度,轨头向上立起,通过温度监视器,连续监测轨头温度并将测得数据送入计算机,由导向辊将重轨送入冷却装置,经一列喷嘴喷水进行淬火,冷却装置由计算机控制,喷嘴自动调整水量,自动定位。
经热处理后的重轨移至冷床,并在空气中静置完成相变,形成珠光体显微组织,然后进行中温矫直.再按常规精整。
英国的沃金顿厂、卢森堡罗舟—阿托斯、加拿大阿尔戈马公司,德国的蒂森钢公司,日本的NKK公司均采用该工艺,其区别在于英国沃金顿厂采用的是水雾冷却,卢森堡则采用的是常温水淬火,加拿大的阿尔戈马采用间隔式水冷却(中间喷吹压缩空气),德国蒂森公司则采用两段式冷却,日本NKK公司则采用热水淬火。
(2)浸水淬火
把轧后经热锯、打印的重轨从冷床取下,将轨头或整体浸入添加有合成缓冷剂的水溶液或沸水中快冷到一定温度取出,空冷至室温,从而使整个轨头得到所期望的微细珠光体组织和良好的硬度分布。
奥地利—阿尔卑斯钢铁矿山联合公司多纳维茨厂研制出一种聚合物缓冷剂,能溶于水,淬火中可在重轨表面形成一层坚固的薄膜,降低水的冷却强度。
调整这种物质在水中的含量,可保证重轨以适当的速度均匀快速冷却。
重轨在淬火槽内进行头部淬火,为保证淬火槽内冷却温度恒定,装有冷水和热水管道的循环系统,自动调节水温。
在轨头浸水的同时,轨底喷吹压缩空气冷却,以减少重轨弯曲。
此外该公司还研究出一种避免重轨向轨底弯曲的专用设备,确保重轨平直和顾利矫直,减少因矫直引起的残余应力。
德国克虏伯冶金公司波鸿厂采用沸水淬火工艺,重轨终轧温度约为1080℃。
在950℃左右将重轨切成定尺。
在重轨冷却到740℃~850℃时(最好在800℃~850℃)从冷床上取下,整体浸入温度不低于80℃的热水中,并保持重轨一直与水接触,直到珠光体完全转变温度470℃以上(实际生产中冷却到450℃),然后空冷。
目前,阿尔戈马公司正在开发一种采用循环水淬火的热处理工艺。
(3)喷吹压缩空气工艺
日本新日铁公司对水雾、压缩空气和盐浴淬火介质对重轨性能的影响进行了试验,结论是对低台金钢轨采用压缩空气淬火,适当调整空气压力即可得到希望的使用性能。
开发了压缩空气淬火工艺,在钢中加入微量Cr、Mn,使余热淬火轨(DHH)达到了离线淬火轨(NHH)的水平,井于1987年建成了在线淬火作业线,轧后钢轨空冷到670℃~770℃时,分批集中于淬火罩内进行处理。
2.5.2重轨余热淬火所达到的硬度
(1)新日铁在线余热淬火的情况
该公司的余热淬火生产线采用压缩空气和加速冷却,生产的余热淬火轨有三种:
DHH340,DHH370、DHH370s。
(2)NKK公司福山厂
主要有THH340、THH370,同时还开发了THH370N、THH370A用于出口的余热淬火轨,采用热水喷射冷却。
3国内重轨生产现状
目前,国内已形成50kg/m、60kg/m和75kg/m系列重轨生产线,产量达到了130万t/y,钢种由普碳钢扩大到中锰,高硅、稀土及含微量元素钒的低合金钢。
重轨的性能也有提高,抗拉强度由785N/mm2~850N/mm2提高到885N/mm2~1300N/mm2以上。
并采取了一系列措施,以提高重轨质量。
然而,我国重轨质量水平和品种,还不能全部满足铁路运轴的实际需要,这是由于我国地域宽广、南北温差大、地形复杂所造成,铁路运输是我国国民经济的大动脉,担负着全国运量的60%~70%。
铁路货运密度已超过2000万t/ykm,货运量已从80年代的2.5亿t,增加到3.0亿t,7万km运营铁路中,山区弯遭约占30%左右,而且,货物列车最大载重量由3500t~4000t提高到5000t~6000t或更大,行车密度从8min缩短到5min以下,旅客列车时速,从80km/h提高到140km/h,最高速度达200km/h。
轴重由25t提高到30t,在线无缝线路长度已达5km。
这些都对重轨的实物质量提出了越来越高的要求,为适应铁路发展这一需求,“八五”以来,我国的重轨生产厂家也进行了大规模的技术改造。
由原来的平炉炼钢改为转炉炼钢,增加了铁水预处理、钢包炉(LF)和真空脱气等装
置,用大方坯连铸机连铸重轨坯,实现了铁水脱硫、转炉炼钢、炉外精炼、连铸、余热淬火生产重轨的全新工艺。
3.1国内重轨钢的冶炼
重轨钢全部采用转炉冶炼,包钢80t×5座顶底复吹转炉。
攀钢120t×5座转炉,其中
2座用于提钒,3座用于炼钢。
鞍钢90t×3座转炉。
3.1.1重轨钢的冶炼条件
国内重轨钢的冶炼条件见表1。
表1国内重轨钢的冶炼条件
公司
名称
铁水
预处理
铁水成份(%)
铁水温度
(℃)
C
Si
Mn
P
S
鞍钢
无
3.8~4.2
0.3~0.8
0.5~1.0
<0.04
<0.03
1250~1300
攀钢
喷粉、脱硫
3.7~4.1
0.06~0.10
0.35~0.85
0.055~0.07
0.006~0.010
1300~1350
包钢
扒渣
4.2~4.5
0.45~0.80
0.6~0.8
0.12~0.22
0.03~0.05
1250~1300
国内转炉冶炼重轨钢的参数见表2。
表2国内转炉冶炼重轨钢的参数
公司
名称
炉容(t)座数
(个)
冶炼周期
(min)
装入量
(t)
氧枪
类型
喷头
氧气流量
(m3/h)
工作压力
(MPa)
孔数(个)
夹角(度)
鞍钢
903
402
100
4
13
17500
0.82
攀钢
1205
403
140
5
13
21300
0.88
包钢
805
352
90
拉瓦尔
3
12
15000
0.80
3.1.2重轨钢的生产工艺
鞍钢:
LD—吹Ar—模铸(下一步采用方坯连铸后,将增加LF和VD精炼装置)
攀钢:
LD—吹Ar—LF—RH—模铸(大方坯连铸很快投人生产)
包钢:
LD—吹Ar—LF—VD—CCM
3.1.3重轨钢的终点控制:
(1)碳和温度的控制
国内目前采用的终点[C]的控制有两种方法,鞍钢和攀钢都采用“拉碳法”,而包钢采
用“增碳法”。
a.攀钢对碳和温度的控制:
拉碳目标为:
C≥0.8%,P≤0.03%~0.04%,温度1600℃~1610℃
终点控制:
C≥0.65%,P≤0.02%,S≤0.01%,经RH处理的高速轨,温度控制在1630℃~1650℃,当终点碳达不到要求时不做重轨钢。
鞍钢碳的控制基本上同攀钢一样,出钢温度控制在1620℃~1640℃,当终点C<0.5%时不做U7lMn(重轨钢)。
b.包钢对碳和温度的控制:
包钢采用“增碳法”,重轨钢按板材钢吹炼及出钢.然后按照所炼钢种的规格再在钢包中进行增碳,达到重轨钢的要求,凡终点C<0.20%的炉次改钢。
(2)浇注工艺的控制
鞍钢采用7.51t和6.27t两种锭型,钢包水口45mm或50mm,浇注速度7.51t锭,本体8min~12min,6.27t锭本体6min~9min,帽部大于2min,保护渣采用吊包法加入,注温控制在1540℃~1550℃。
攀钢采用11.25t和9.51t两种锭型,每盘4个锭,每炉钢约浇注13~14个锭,浇注速度为11.25t锭,本体8min~11min,9.51t锭本体6min~9min,帽部大于3min,钢包水口60mm,模内吊保护渣20kg,帽部加覆盖剂15kg,注温控制在1535℃~1545℃。
包钢采用大方坯连铸机,连铸的规格为230mm×325mm,280mm×380mm,319mm×410mm,中间包过热度20℃~25℃,钢水从钢包到中间包的温降为35℃,所以正常开浇温度为:
1536℃~1541℃。
这里未考虑钢包到达回转台后待注时的温降,一般应为5min,连浇期的第一炉或新中间包的第一炉,开浇温度应提高10℃。
3.1.4重轨钢的脱氧制度
攀钢用P1做终脱氧剂,加入量为80kg/炉,用低铝硅铁和硅锰合金脱氧合金化。
加入量为硅铁800kg/炉,硅锰合金1.5t/炉,高速轨加钒铁75kg/炉。
必须挡渣出钢,要求红包出钢,出完钢后加入120kg/炉盖包材料,出钢后喂人复合硅钙包芯线13mm,300m/炉,喂线后吹氩时间保证大于5min。
鞍钢采用复合脱氧剂(Si-Ba-Al和Si-Ca),出钢1/3时加入,50kg/炉,同时加入Si-Al-Fe终脱氧,50kg/炉,吹Ar5min。
包钢采用硅锰合金和硅铁脱氧,以利于脱氧产物的上浮和减少包内合金加入量,终脱氧剂为硅钙合金,力口入量1kg/t。
3.2国内重轨钢炉外精炼技术的应用
国内主要重轨钢生产厂家,全部应用了LF炉和真空处理相配合的炉处精炼技术。
鞍钢和包钢都是由平炉车间改造而来的小型转炉(<100t),且以碳累钢为主要产品的钢厂,在钢包吹氩或喂丝技术不能满足连铸工艺和铸坯质量要求的基础上增加了LF炉和VD装置。
攀钢为中型转炉(120t),采用了LF炉和RH法。
选择LF炉与真空处理并用,既能适应大生产,高质量的要求,又不致于使成本增加过多,还可得到最佳的精炼效果。
这种组合可生产超低碳(C≤100×10-6)或超低硫(S≤5×10-6)的钢种。
攀钢LF炉处理要点:
就位后取样测温,加入顶渣600kg/炉,渣层厚度控制在50mm~
80mm,顶渣成份;CaO:
60%~66%,Al2O3≤8%,SiO2:
4%~6%,MgO:
5%~7%,H2O≤
2%,CaF2:
12%~16%,P、S≤0.08%,升温速度3℃/min,没有脱硫和微调成份的任务,离
位温度1590℃~1610℃。
在RH工位进行成份微调,浸入管插入深度为550mm~650mm,吹Ar流量为1200NL/min,处理时间要求大于18min,真空度小于5mbar,离位温度控制在1560℃~1580℃。
包钢两台LF炉,处理能力100万t/y。
VD处理能力70万t/y,抽气能力250kg/h,工
作真空度6.7Pa,氢含量处理到2×10-6时需20min,氢含量达到1.5×10-6需24min。
温降
1.5℃/min~2.0℃/min。
VD工位设有两流喂丝机可进行喂丝处理。
LF炉最高升温速度可达4℃/min,脱硫效率可达70%。
3.3重轨钢的连铸
国内三家重轨生产厂家,只有包钢对重轨钢冶炼部分进行了全面改造,实现了转炉炼钢、炉外精炼、连铸生产重轨钢的全部工艺。
包钢采用一台四流大方坯连铸机和一台四流方圆兼用型连铸机.连铸坯产量方坯68万t/y,圆坯52万t/y。
铸机机型为全弧三点矫直,弧形半径为12m,流间距:
1.65m。
大方坯的规格和产量:
280mm×325mm,10万t/v;280mm×380mm,50万t/v;319mm×410mm,8万t/y。
大方坯的钢种主要是重轨钢。
连铸钢水中要求:
S<0.01%,P<0.020%。
鞍钢和攀钢正加快大方坯连铸机的建设,预计在近一、二年内就可以采用连铸坯轧
制重轨。
3.4重轨的轧制工艺
(1)攀钢
钢锭送初轧厂加热到1280℃、开轧温度≥1150℃,轧制道次9.51t锭:
6-7-4-2-1,11.25t锭:
6-10-4-2-1,钢坯截面为280mm×325mm,280mm×372mm,堆垛缓冷后经火焰清理,清理温度冬季≥200℃,夏季≥150℃。
钢坯冷送轨梁厂,在加热炉中加热3h~4h,出加热炉后采用高压水除鳞:
出炉温度1180℃,开轧温度1150℃,孔型系统由二个箱型,一个梯型、三个帽型、五个轨型孔组成共轧12道次。
950mm轧制5道次,800mm/850mm轧制道次为3-3-1,终轧温度为920℃~950℃。
压缩比不小于13.8:
1。
然后重轨入缓冷坑,出坑后经1300mm型八辊辊式矫直机矫直,重轨硬弯较小,矫直时经常修磨矫直辊,重轨矫痕较轻,100%在线超声波探伤。
加工用西德WHCB1000/S锯钻联合机床,落锤试验采用热锯样,不做矫后落锤试验。
(2)包钢
连铸坯出加热炉温度1150℃~1180℃,出炉后高压水除鳞,开轧温度1120℃~1160℃,终轧温度850℃~950℃。
采用950mm~800mmm/850mm二列式轧机,孔型系统:
二个箱型,一个梯型,三个帽型和五个轨型,共轧制14~16道次,轧后缓冷,六辊悬臂式矫直机矫直,WHCB1000/S型锯钻联合机床进行加工,螺栓孔倒棱,100%在线超声波探伤。
3.5重轨余热淬火
我国三家重轨生产厂.目前只有攀钢轨梁厂建设了全长余热淬火生产线,采用对轧后标准碳索钢轨的4个侧面喷水淬火的方式进行热处理,通过对轨头、轨底及轨腰部的喷水预冷,随后空冷,完成奥氏体向珠光体转变,通过控制水温和喷水强度来调整重轨硬度。
包钢、鞍钢余热淬火生产线还没有上,只能采用简单的轨端淬火。
4国内外重轨生产技术的差距
4.1重轨冶炼条件的差距
国外冶炼重轨钢的转炉大多数为大、中型转炉,都配有副枪测温定碳,自动化程度较高。
入炉铁水经三脱(脱硅、脱磷、脱硫)后磷,硫含量低,重轨化学成分的控制范围很窄,各主要成份的波动范围:
C<0.05%,Mn<0.1%,Si<0.07%,P<0.009%,S<0.006%。
国内的转炉为中、小型,都没有副枪,自动化程度低,人炉铁水只进行脱硫扒渣,所以磷含量较高,影响终点控制,重轨化学成分的控制范围较宽,各主要成份的坡动范围:
C<0.13%,Mn<0.3%,Si<0.15%,P<0.017%,S<0.021%。
4.2生产工艺的差距
国外重轨生产工艺为:
高炉铁水→铁水“三脱”→顶底复合吹炼转炉→RH真空脱气→连铸(大方坯)→步进式加热炉(保温隧道)→高压水除鳞→万能轧机→热锯定尺→在线余热淬火生产线→自动打印→带预弯装置的步进式冷床→双向平立可变辊距10辊矫直机→轨端四面压力矫→在线超声波探伤(16个探头)→联合锯钻机床→成品检查入库。
国内重轨生产工艺为:
高炉铁水→铁水脱硫处理→转炉炼钢→钢包吹氧、喂复合线→LF炉→真空脱气→模铸或连铸→初轧开坯→推钢式加热炉→横列式轧机→热锯定尺→自动打印机→拉钢式冷床→坑缓冷→平立联合6辊或8辊矫直机→四面液压矫直机→联合锯钻机床→轨端帽形淬火→在线三探头超声波探伤→人工检查入库。
与国外生产工艺相比,我国重轨生产的总体装备及技术水平虽有所改进,但还存在着不同