高炉煤气提纯低燃值高炉煤气综合利用工程可行性研究报告.docx
《高炉煤气提纯低燃值高炉煤气综合利用工程可行性研究报告.docx》由会员分享,可在线阅读,更多相关《高炉煤气提纯低燃值高炉煤气综合利用工程可行性研究报告.docx(40页珍藏版)》请在冰豆网上搜索。
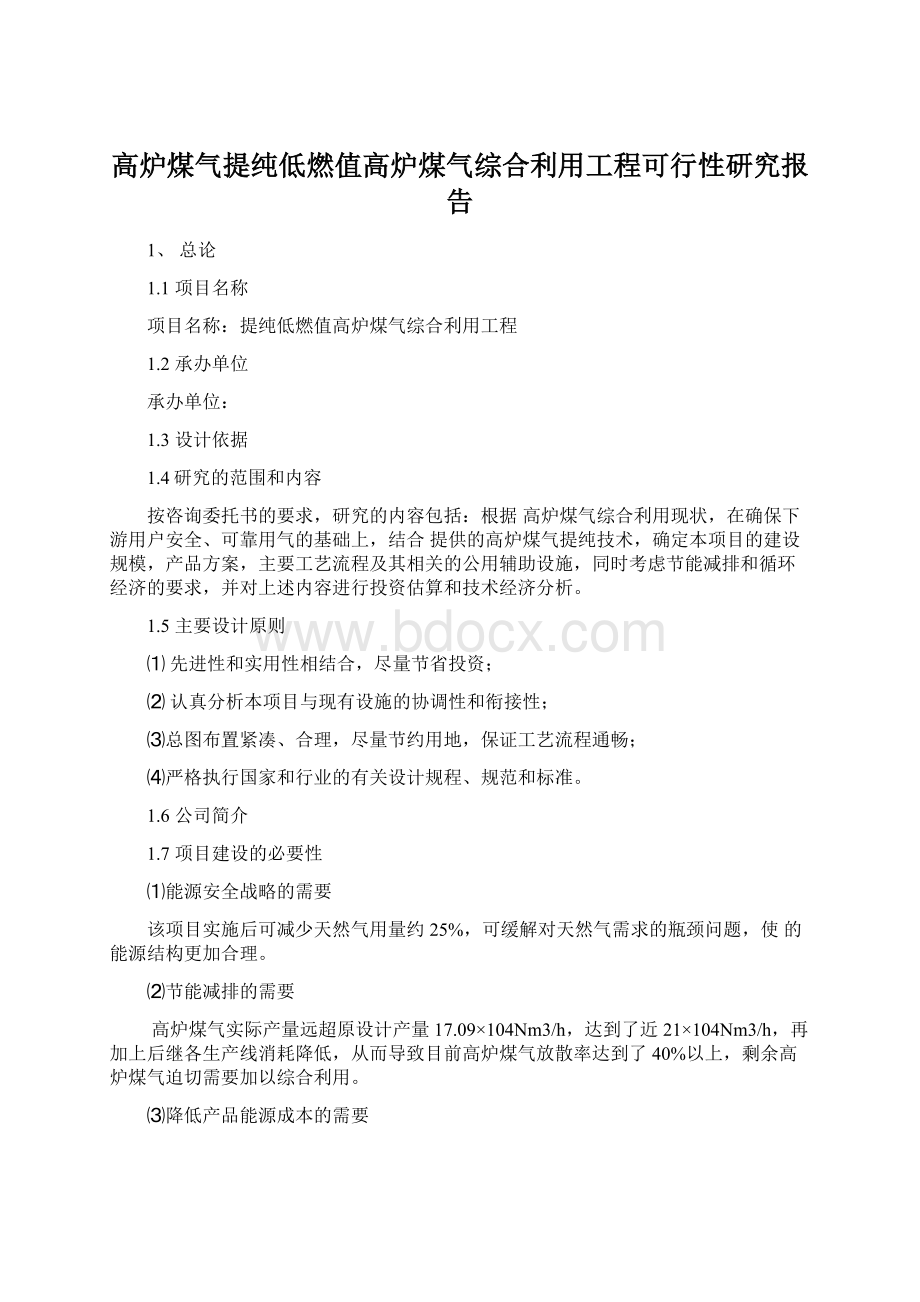
高炉煤气提纯低燃值高炉煤气综合利用工程可行性研究报告
1、总论
1.1项目名称
项目名称:
提纯低燃值高炉煤气综合利用工程
1.2承办单位
承办单位:
1.3设计依据
1.4研究的范围和内容
按咨询委托书的要求,研究的内容包括:
根据高炉煤气综合利用现状,在确保下游用户安全、可靠用气的基础上,结合提供的高炉煤气提纯技术,确定本项目的建设规模,产品方案,主要工艺流程及其相关的公用辅助设施,同时考虑节能减排和循环经济的要求,并对上述内容进行投资估算和技术经济分析。
1.5主要设计原则
⑴先进性和实用性相结合,尽量节省投资;
⑵认真分析本项目与现有设施的协调性和衔接性;
⑶总图布置紧凑、合理,尽量节约用地,保证工艺流程通畅;
⑷严格执行国家和行业的有关设计规程、规范和标准。
1.6公司简介
1.7项目建设的必要性
⑴能源安全战略的需要
该项目实施后可减少天然气用量约25%,可缓解对天然气需求的瓶颈问题,使的能源结构更加合理。
⑵节能减排的需要
高炉煤气实际产量远超原设计产量17.09×104Nm3/h,达到了近21×104Nm3/h,再加上后继各生产线消耗降低,从而导致目前高炉煤气放散率达到了40%以上,剩余高炉煤气迫切需要加以综合利用。
⑶降低产品能源成本的需要
一方面大量的高炉煤气在放散,另一方面天然气的价格仍在上涨(据有关资料介绍在2011年西气东输二线建成通气后,东亚天然气大量进入中国后,天然气价格还要上涨),这样产品单位能源成本还将增加。
⑷环境综合治理的需要
高炉煤气的大量放散,不仅浪费能源,而且严重污染环境,本项目的实施不仅能改善周围环境状况,而且还可通过节能,年实现节约标准煤2.9万t,给企业带来良好的社会效益和经济效益。
1.8项目建设的有利条件
⑴具有优越的自然条件
本项目建设地位于厂区内,区域内功能齐全,设施配套,工程所需的水、电、气等能源介质均可由综合管网供给。
⑵具有良好的工程建设管理经验
为适应市场变化,近几年不断加大工程项目投资力度,在项目实施的过程中,公司非常重视对工程项目的科学管理,并积累了丰富的工程建设组织管理经验,为本项目的实施打下了良好的基础。
⑶具有可靠的原料资源
具有稳定、可靠的高炉煤气资源,并迫切需要将其综合利用,因而为本项目的日常生产运行提供了可靠的原料保证。
⑷拥有先进、可靠的技术
已为用户设计建设了多套大型提纯CO装置。
⑸具有充足的资金保证
1.9主要研究结果概要
1.9.1项目建设条件
⑴选址
本项目建设地位于厂区现有煤气站南侧,占地约6000m2。
⑵供电
本项目2回路10KV电源从炼铁35KV变电站10KV配电室两段不同的母线引来。
系统高压部分装机容量为:
6310kW,工作容量为:
5955KW;低压部分装机容量为:
3390kW,工作容量为:
2419kW。
低压部分设630KVA、10/0.4KV干式变压器两台;配电系统采用单母线分段的接线方式;电源由10kV高压配电室两段不同的母线引来。
本项目高压配电室、低压配电室、变压器室等均设于控制楼内。
⑶供气
压缩空气:
从现有压缩空气管道上接出一根DN25管道,经缓冲、过滤、冷却和再过滤后,用作仪表气源。
压缩空气管道输送压力为:
0.8MPa。
⑷给排水
本项目供水就近从厂区内主供水管网上接入,供水压力为:
0.3~0.4MPa;排水系统就近排入厂区内的排水干管。
本系统界区内设950m3/h循环水冷却系统一套。
⑸通风空调
在压缩机主厂房、真空泵房及热值仪室等场所设置事故通风机;在高低压配电室、控制值班室、休息室和门卫等人员工作场所设置空调或通风设施。
⑹资金
本项目建设投资费用估算额为:
9300万元,
1.9.2建设规模和产品方案
本项目建设规模为提纯60000Nm3/h(干基)高炉煤气原料气。
本项目提纯产品气设计工况基准点为:
CO体积含量70vol%,产量17500Nm3/h,热值2200×4.18kJ/Nm3。
1.9.3主要工艺流程
从现有煤气柜后DN1800净高炉煤气总管上接出一根DN1400煤气管道,送至本项目界区内。
高炉煤气压缩至0.32MPa(G)后,进入预处理工序,在预处理工序中脱出大部分粉尘、全部无机硫和氧气后,气体温度降到70℃。
经上述处理后的合格原料气进入提纯装置,在CO提纯装置中,CO气体浓缩到70vol%,然后经产品气增压机压缩到35KPa(G)后出界区。
吸附尾气从吸附塔顶出来后由放散塔高空放散。
1.9.4能源、环保、安全及工业卫生与消防
⑴能源
本项目主要能源介质为电,主要耗电设备为煤气压缩机、罗茨风机和真空泵。
生产达设计规模后,年耗电量为:
4761.36×104kWh;年耗新水量为:
28×104t;年耗氮气量为:
10×104Nm3,共计折合标准煤:
1.93万t/a。
本项目提纯气生产工序能耗为0.1380kg标准煤/Nm3提纯气,设计中采取的节能措施符合国家能源政策。
本项目实施后,年可替代天然气3382×104Nm3,折合标准煤3.8万吨,采用提纯气替代混合气(高炉煤气与天然气混合)用于各工业炉燃烧,年可节约标准煤1.03万吨。
本项目综合能耗指标为:
年可节约标准煤2.9万吨,另外提纯气燃烧后烟气相比混合煤气燃烧后的烟气能提高各工业炉内的辐射换热效果,也具有一定的节能作用。
本项目实施符合国家能源政策,具有良好的经济效益和社会效益。
⑵环保、安全及工业卫生与消防
本设计按照国家有关标准、规程和规范对涉及环保、安全及工业卫生和消防等方面的问题,采取了多种必要的措施,能满足生产和国家有关标准要求,但有关CO的排放问题须与当地环保部门沟通。
1.9.5工程建设进度
工程建设期为一年
1.9.6技术经济分析
本工程项目主要技术经济指标如下:
项目建设总投资:
9300万元;投资利润率:
14.42%
财务内部收益率:
15.01%;投资回收期:
7.1年
1.9.7结论
本项目的建设从公司的客观实际情况来说是必要的,技术上从理论分析亦是可行的。
且本项目实施后具有良好的社会效益和一定的企业经济效益。
1.10需要说明的问题
⑴从高炉煤气中提纯CO工艺尽管从理论上可行,并通过了实验室论证,但国内无该类项目实施先例,因而存在着一定的技术风险;
⑵本项目的关键设施→吸附剂对原料气的品质要求较高,尤其是粉尘和硫的含量,若原料气品质达不到要求,将可能造成催化剂中毒,对整个系统产生极大的影响,因而本项目必须保证原料气品质;
⑶由于现无适合的高炉煤气缓冲用户,本项目实施后,仍会有少量的高炉煤气放散;
从高炉煤气利用的角度来说,本项目的经济性较好。
2、项目分析与策划
2.1概况
高炉投用后,产生约21X104Nm3/h高炉煤气,目前利用率仅约60%,高炉煤气放散量达81000Nm3/h。
为充分利用高炉煤气化学能,减少高炉煤气放散对环境的影响,拟推动对高炉煤气进行提纯的综合应用项目。
2.2项目背景及煤气平衡
目前所采用的高炉煤气利用方式是在高炉煤气中掺入部分天然气提高其热值供用户使用,因为二种不同热值的燃气混合对高热值燃气要引起熵的损失,所以从能源利用角度来说不是最佳的利用方式。
根据的特殊情况,目前剩余高炉煤气利用方式主要有:
⑴直接送入锅炉生产蒸汽发电;
⑵适当掺烧一部分天然气,利用CCPP发电;
⑶把高炉煤气进行富化,提高其热值到2200X4.18KJ/Nm3左右直接进入工业炉内燃烧。
由于历史的原因,不能自供燃料,又由于各生产机组能力有限,不能将高炉煤气充分消化,一方面购入大量的天然气作燃料,另一方面多余的高炉煤气又在放散,这对资源的保障和成本的降低大大不利,因此,从资源保障方面考虑,用高炉煤气发电不是最佳选择;若通过变压吸附方式,把高炉煤气中的56vol%的氮气去除大部分,提高其中CO浓度,使热值达到2200X4.18KJ/Nm3,直接送入轧钢加热炉内使用,采用这种方式,既可解决高炉煤气放散问题,又可解决天然气供应紧缺问题,是目前最佳的选择。
一方面高炉煤气大量放散,另一方面还在大量使用天然气制备热值约为2100~2200X4.18KJ/Nm3的混合气(MG),其原因就是高炉煤气热值太低,未能将其合理利用。
据此,提出将高炉煤气进行变压吸附,使煤气中CO的体积含量提高至约70vol%,以提高高炉煤气单位热值,供现有轧钢工业炉使用,达到减少天然气使用量,逐步实现高炉煤气零放散的目的。
经多方论证,并对相关项目进行实地考察,现已证明采用变压吸附提纯CO的工艺方案在技术上是切实可行的。
根据“咨询委托书”的要求,本可行性研究报告将不对CO提纯的具体工艺方案进行论证,仅根据技术资料进行该项目整体工艺方案的可行性研究。
2.3生产规模与产品方案的确定
2.3.1基本思路
生产规模与产品方案的确定:
以实现混合煤气用户热值和压力最稳定,高炉煤气充分利用,浓缩成本最低,综合效益最大化为原则。
2.3.2高炉煤气使用现状分析
根据煤气使用情况分析资料可知:
⑴现有生产线均采用混合煤气(高炉煤气与天然气混合),混合煤气热值约为~2200X4.18KJ/Nm3,最大耗量:
65000Nm3/h。
⑵目前混合煤气根据生产情况使用的波动范围为20000~65000Nm3/h,且瞬时波动幅度大,可达100%~200%,波动方式呈不规则正弦波形。
⑶目前高炉煤气产量约210000Nm3/h,除热风炉、喷煤及烧结使用外,可外送高炉煤气量约为131700Nm3/h,高炉煤气放散量高达~81000Nm3/h;另一生产线投产后,若高炉煤气不加以合理利用,其放散量仍高达~49000Nm3/h。
⑷随着高炉冶炼强度的提高,高炉煤气产量仍有增加的趋势。
2.3.3建设规模与产品方案
2.3.3.1建设规模
本项目的建设规模为:
提纯高炉煤气原料气60000Nm3/h(干基)。
2.3.3.2产品方案
本项目提纯装置设计工况基准点如下:
⑴提纯产品气成分(V%)
提纯产品气成分表(V%)
化学成份
CH4
CO
CO2
H2
N2
Σ
百分率/%(干基)
~0.22%
70.00%
~9.41%
~0.25%
~20.13%
100.00%
流量/Nm3/h
38.5
12250
1646.8
43.8
3522.7
17500
⑵提纯产品气热值:
2200X4.18KJ/Nm3
⑶提纯产品气压力:
≥35KPa
⑷提纯产品气温度:
常温
2.4提纯装置生产运行模式
本系统提纯产品气CO体积含量为70vol%,对应煤气热值为2200X4.18KJ/Nm3,可不掺混天然气,直接外送,此时提纯气产量为17500Nm3/h。
生产用气不足部分由高炉煤气掺混天然气补充,其控制热值与提纯产品气一致。
特殊情况下,可通过降压方式将提纯产品气CO体积含量降低10~20%(可调),以增大产量,系统以掺混天然气方式补充不足热值,使外送产品气热值稳定在2200X4.18KJ/Nm3。
该模式可保证用户生产用气安全、稳定。
2.5高炉煤气放散
采用变压吸附提纯装置后,还必须合理利用现有25t燃气锅炉(可考虑将多余蒸汽发电),将其作为缓冲用户,以适应并平衡用气负荷的波动,实现高炉煤气的零放散。
3、工艺方案
3.1原料气来源及技术参数
本提纯装置原料气利用1000m3级高炉生产的副产煤气,用量约60000Nm3/h(干基)。
高炉煤气从现有120000m3煤气柜后DN1800煤气总管上接出,其技术参数如下:
高炉煤气化学成份表
化学成份
CH4
CO
CO2
H2
N2
O2
H2O(气)
Σ
百分率/%(干基)
0.50%
24.0%
16.0%
1.0%
57.5%
≤1.0%
饱和
100.00%
流量(干基)/Nm3/h
335.0
16080.0
10720.0
670.0
38525.0
670.0
60000.0
⑴原料气压力:
8000±150Pa;
⑵原料气温度:
≤60℃;
⑶原料气SO2的浓度:
≤1ppm;
⑷原料气中H2S的浓度:
≤100ppm;
⑸原料气粉尘:
≤10mg/Nm3
3.2提纯产品气设计工况
提纯产品气设计工况表(提供)
化学成份
CH4
CO
CO2
H2
N2
Σ
百分率/%(干基)
~0.22%
70.00%
~9.41%
~0.25%
~20.13%
100.00%
流量/Nm3/h
38.5
12250
1646.8
43.8
3522.7
17500
⑴外送提纯产品气压力:
≥35KPa
⑵外送提纯产品气热值:
2200X4.18KJ/Nm3
3.3主要工艺流程
从现有12万m3煤气柜后DN1800净高炉煤气总管上接出一根DN1400煤气管道,将高炉煤气送至本项目界区内。
高炉煤气压缩至0.32MPa(G)后,进入预处理工序,在预处理工序中脱出大部分粉尘、全部无机硫和氧气后,气体温度降到70℃。
经上述处理后的合格原料气进入提纯装置,在CO提纯装置中,CO气体浓缩到70vol%,然后经产品气增压机压缩到35KPa后出界区。
吸附尾气从吸附塔顶出来后高空放散。
进入变压吸附提纯装置前,应满足:
粉尘含量≤10mg/Nm3,同时没有有机硫,保证无机硫含量≤100PPm,氧气含量≤1v%。
预处理工序分为脱硫和除氧两部分。
在此工序中原料气中的无机硫和氧气被除去。
保证进入PSA-CO工序中的原料气中不含无机硫、氧气含量小于0.01%。
3.4项目技术方案简介------变压吸附(PSA)技术
变压吸附(PSA)技术是近30多年来发展起来的一项新型气体分离与净化技术。
1942年德国发表了第一篇无热吸附净化空气的专利文献。
60年代初,美国联合碳化物公司首次实现了变压吸附四床工艺技术的工业化。
由于变压吸附技术投资少、运行费用低、产品纯度高、操作简单、灵活、环境污染小、原料气源适应范围宽,因此,进入70年代后,这项技术被广泛应用于石油化工、冶金(焦化)、轻工及环保等领域,特别在国内化工行业近十多年里得到了较快的发展,主要用于气体分离,制氧、提取氢、提取CO2、提取CO等等。
变压吸附气体分离工艺过程是吸附剂在物理吸附中所具有的两个基本性质:
一是对不同组分的吸附能力不同,二是吸附质在吸附剂上的吸附容量随吸附质的分压上升而增加,随吸附温度的上升而下降。
利用吸附剂的第一个性质,可实现对混合气体中某些组分的优先吸附而使其它组分得以提纯;利用吸附剂的第二个性质,可实现吸附剂在低温、高压下吸附而在高温、低压下解吸再生,从而构成吸附剂的吸附与再生循环,达到连续分离气体的目的。
本项目PSA工序简述如下:
⑴PSA-1工序简述
PSA-1工序的作用是分离原料气中的无机硫和水等杂质。
进入界区的原料气,首先由煤气压缩机增压到0.32MPa(G),同时温度控制在70℃左右,再由原料气进口阀从塔底进入PSA-1工序吸附塔,半成品气从吸附塔顶部排出。
经过一定循环步骤后,吸附塔内的杂质气体通过冲洗方式排出吸附塔,送出界区。
为了保证半成品气的连续输出和适应今后工况变化而灵活调节产量,PSA-1工序由二套装置组成。
每套装置有2台吸附塔,任何时刻均有1台吸附塔处于吸附步骤,其余各塔处于吸附剂再生过程,2台塔交替工作从而达到连续分离杂质的目的。
在一个周期中每个吸附塔均经历:
吸附、冲洗再生两个工艺过程。
具体步骤如下:
a.吸附
增压的原料气从吸附塔底部进入PSA-1工序的吸附塔中,在预定的吸附压力下,混合气中的有害杂质被专用吸附剂吸附下来,CO、N2、CH4等未被吸附的组份作为吸附尾气从吸附塔顶流出吸附塔,送到后工序。
当吸附塔中的杂质吸附前沿到达吸附塔的预定位置后,关闭吸附塔的原料气进口阀门和吸附尾气出口阀门,吸附塔停止吸附步骤,开始转入冲洗再生过程。
b.冲洗再生
结束吸附步骤后,将PSA-CO的尾气从吸附塔的塔顶送入吸附塔对吸附剂进行冲洗再生,再生过程中吸附塔压力保持不变。
至此,吸附塔完成了一个完整的吸附-再生循环过程,并为下一个循环过程做好了准备。
装置中9台吸附塔交替进行以上各个步骤的操作,从而得到满足产品规格要求的半成品气。
⑵除氧工序简述
经过脱硫工序的原料气自上而下的通过脱氧塔。
在脱氧塔内,原料气中的氧在催化剂的作用下与原料气中的氢和一氧化碳发生反应,生成水和二氧化碳而被除去。
在这一过程中,根据反应原理,需要消耗一部分原料气中的氢和一氧化碳。
⑶PSA-CO工序简述
PSA-CO工序的作用是使CO与其它组份如CO2、N2、CH4等杂质组份分离,得到CO产品。
从预处理工序来的半成品气,经进口阀从塔底进入PSA-CO工序吸附塔,吸附尾气从吸附塔顶部排出。
经过一定循环步骤后,吸附塔内合格的CO通过抽真空方式排出吸附塔,进入CO产品气罐。
为了保证CO产品的连续性和适应今后工况变化而灵活调节产量,PSA-CO工序由两套装置组成。
每套装置有8台吸附塔,任何时刻均有3台吸附塔处于吸附步骤,其余各塔处于吸附剂再生过程的不同阶段,8台塔交替工作从而达到连续分离CO的目的。
在一个周期中每个吸附塔均经历吸附、均压降压、抽空、均压充压、(终)充压等工艺过程。
具体步骤如下:
a.吸附
半成品气从吸附塔底部进入PSA-CO工序的吸附塔中,在预定的吸附压力下,混合气中的CO被专用吸附剂PU-1吸附下来,CO2、N2、CH4等未被吸附的组份作为吸附尾气从吸附塔顶流出吸附塔送出界区。
当吸附塔中的CO吸附前沿到达吸附塔的预定位置后,关闭吸附塔的原料气进口阀门和吸附尾气出口阀门,吸附塔停止吸附步骤,开始转入再生过程。
b.吸附塔均压降压
结束吸附步骤后,将吸附塔与处于低压状态的吸附塔连通,对吸附塔进行降压,对塔内死空间的气体和解吸下来的气体中的有用组分进行回收。
c.抽真空
均压降压结束后,为得到产品CO并使吸附剂得到彻底地再生,用真空泵逆着吸附方向对吸附塔进行抽真空,使被吸附的CO解吸,解吸下来的CO流入产品气罐。
d.吸附塔的均压升压
抽真空步骤结束后,吸附塔与处于高压状态的吸附塔连通进行均压升压。
均压升压气体从吸附塔的顶部逆着吸附方向导入吸附塔,达到升压的目的并且回收均压罐中的有用组分。
e.吸附尾气对吸附塔终升压
均压升压步骤后的吸附塔内压力还未达到预定的吸附压力,为了使吸附塔可以平稳地切换到下一次吸附并保证吸附塔中的CO浓度前沿在终充过程中平稳移动,需要通过相应的升压调节阀缓慢而又平稳地用另一处于吸附步骤的吸附塔的吸附尾气将吸附塔压力升至预定的吸附压力。
至此,吸附塔完成了一个完整的吸附-再生循环过程,并为下一个循环过程做好了准备。
每套装置中8个吸附塔交替进行以上各个步骤的操作,从而得到满足产品规格要求的产品一氧化碳。
3.5系统整体调配方案
⑴当用气负荷大于系统出力(超过17500Nm3/h,热值:
2200X4.18KJ/Nm3)时,利用现有煤气加压及混合站,以同热值的高炉煤气混天然气补充不足气量,但小流量时须靠高炉煤气提纯系统自带的高炉煤气混天然气设施补充;
⑵当用气负荷小于系统出力(低于17500Nm3/h,热值:
2200X4.18KJ/Nm3)时,须及时调整提纯装置负荷,紧急状态时,采取事故回流放散措施。
根据目前生产情况,该工况出现的概率较低;
⑶为保证用户热值稳定,在提纯气出口及混合气出口采用在线热值跟踪控制方式;
⑷提纯装置故障时,可切换至现有系统,保证生产正常运行;
⑸以现有25t燃气锅炉作为高炉煤气缓冲用户,实现高炉煤气零放散。
3.5主要设备表
3.5.1主要非标设备
主要非标设备表
序号
非标设备名称
技术规格
材质
数量(台)
1
预处理塔1
Φ3600
Q345R
2
2
预处理塔2
Φ3400
Q345R
4
3
预处理塔3
Φ3400
Q345R
8
4
吸附塔
Φ3600
Q345R
16
5
吸附尾气缓冲罐
Φ3200
Q345R
2
6
置换气缓冲罐
Φ3200
Q345R
2
7
产品气缓冲罐
Φ3500
Q345R
6
8
喷淋塔
Φ2600
Q345R
1
9
汽水分离器
Φ1800
Q345R
1
10
离心机增压后汽水分离器
Φ1200
Q345R
2
11
仪表空气缓冲罐
Φ1200
Q345R
1
12
离心机后冷却器
Q235
2
13
除氧后冷却器
Q235
2
14
真空泵前冷却器
Q235
4
15
真空泵后冷却器
Q235
2
16
提纯尾气放散塔
1
小计
56
3.5.2主要动力设备
主要动力设备表
序号
设备名称
技术规格
单位
数量
1
原料气离心压缩机
进口压力:
3KPa;出口压力:
0.32MPa(G);流量:
715m3/min;2800KW
套
2
2
置换气罗茨鼓风机
进口压力:
4KPa;出口压力:
39.2KPa;流量:
28m3/min;37KW
套
2
3
产品气增压机
进口压力:
4KPa;出口压力:
39.2KPa;流量:
407.5m3/min;355KW
套
2
4
真空泵
W1200型;1.2m3/s;110KW
套
4
5
真空泵
W2400型;2.4m3/s;220KW
套
12
6
液压站
套
1
7
防爆单梁起重机
起吊重量:
10t
套
2
8
冷却水泵
(见水道专业)
1000t/h;扬程:
32m
台
2
9
冷却塔
(见水道专业)
600t/h
台
2
10
仪表气冷干机
(见热力专业)
5m3/min
台
2
合计
26
3.5.3主要程控阀门
主要程控阀门表
序号
技术规格
单套数量
装置套数
总数
备注
1
DN200
10
2
20
2
DN250
8
2
16
3
DN300
24
2
48
4
DN350
8
2
16
5
DN400
8
2
16
小计
58
116
3.5.4吸附剂用量
序号
填料
总量/吨
消耗/年
1
P-14
305
305
2
P-14B
127
25
3
P-5A
30
4
P-1
388
5
P-9
50
6
瓷球
274
小计
1174
3.6工艺平面布置
本项目布置在现有煤气站区域南侧的空地上,占地面积约6000m2。
各工艺设备按工艺流程顺序布置。
站区内主要建、构筑物有:
煤气压缩机主厂房,煤气鼓风机、真空泵房,循环水泵房,冷却塔及控制楼等辅助用房。
本系统为独立站房,四周设有防护围墙,站内设有4m宽消防通路。
煤气压缩机主厂房采用双层结构,煤气压缩机呈单列布置,运转层设在二层,冷却器及油站等设于一层,压缩机室外阀门操作平台与二层相连,主厂房内二层设有10t电动单梁防爆起重机一台,LK=10.5m。
各种吸附塔及储罐等设施均露天布置。
3.7工艺技术特点
⑴主要工艺设备按先进、可靠和适用的原则选取;
⑵尽量利用现有设施,以节省投资;