设计支架的机械加工工艺规程及工艺装备课程设计论文.docx
《设计支架的机械加工工艺规程及工艺装备课程设计论文.docx》由会员分享,可在线阅读,更多相关《设计支架的机械加工工艺规程及工艺装备课程设计论文.docx(34页珍藏版)》请在冰豆网上搜索。
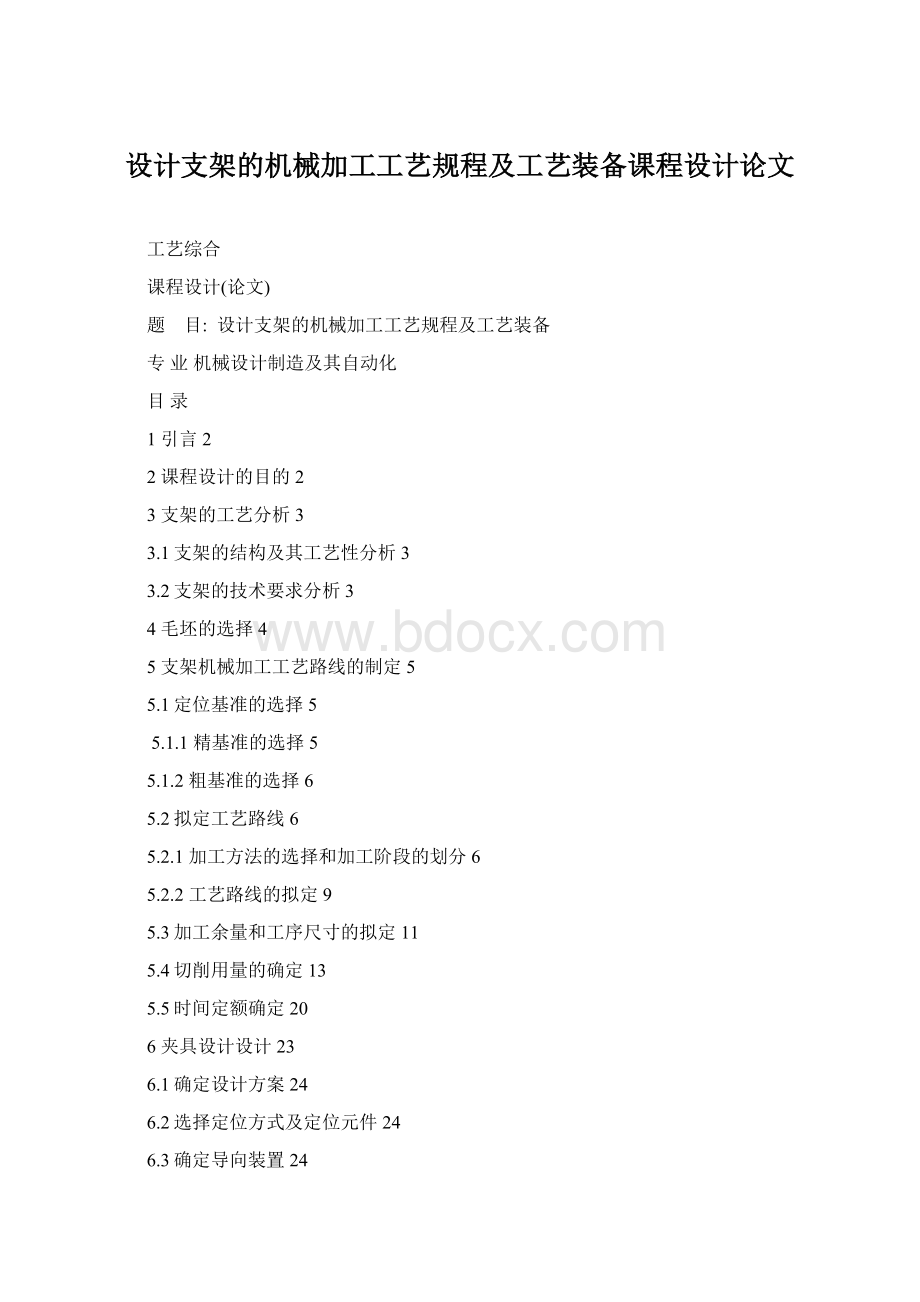
设计支架的机械加工工艺规程及工艺装备课程设计论文
工艺综合
课程设计(论文)
题 目:
设计支架的机械加工工艺规程及工艺装备
专业机械设计制造及其自动化
目录
1引言2
2课程设计的目的2
3支架的工艺分析3
3.1支架的结构及其工艺性分析3
3.2支架的技术要求分析3
4毛坯的选择4
5支架机械加工工艺路线的制定5
5.1定位基准的选择5
5.1.1精基准的选择5
5.1.2粗基准的选择6
5.2拟定工艺路线6
5.2.1加工方法的选择和加工阶段的划分6
5.2.2工艺路线的拟定9
5.3加工余量和工序尺寸的拟定11
5.4切削用量的确定13
5.5时间定额确定20
6夹具设计设计23
6.1确定设计方案24
6.2选择定位方式及定位元件24
6.3确定导向装置24
6.4设计夹紧机构25
7致谢25
参考文献26
设计支架的机械加工工艺规程及工艺装备
1引言
工艺综合课程设计是机械类专业的一门主干专业基础课,内容覆盖金属切削原理和刀具、机械加工方法及设备、互换性与测量技术、机械制造工艺学及工艺装备等,因而也是一门实践性和综合性很强的课程,必须通过实践性教学环节才能使我们对该课程的基础理论有更深刻的理解,也只有通过实践才能培养我们理论联系实际的能力和独立工作能力。
因此,工艺综合课程设计应运而生,也成为机械类专业的一门重要实践课程。
通过这次课程设计,对自己专业能力进行了一次适应性训练,从中锻炼了自己分析问题、解决问题的能力,同时,在课程设计过程中,我们通过认真查阅资料,切实地锻炼了我们自我学习的能力。
另外,在设计过程中,经过老师的悉心指导和同学们的热心帮助,我们小组三位成员顺利完成了本次设计任务。
由于能力所限,设计尚有许多不足之处,恳请各位老师给予批评指正。
2课程设计的目的
机械制造技术基础是机械工程累本科专业的学科基础课,实践性强,应用范围广,内容涉及机械制造装备的选择或设计、机械工艺规程的制订。
工艺综合课程设计旨在继承前期先修基础课程的基础上,让我们完成一次机械零件的机械加工工艺规程和典型夹具设计的锻炼,其目的如下。
(1)在结束了机械制造基础等前期课程的学习后,通过本次设计使我们所学到的知识得到巩固和加深。
培养我们全面综合地应用所学知识去分析和解决机械制造中的问题的能力。
(2)通过设计提高我们的自学能力,使我们熟悉机械制造中的有关手册、图表和技术资料,特别是熟悉机械加工工艺规程设计和夹具设计方面的资料,并学会结合生产实际正确使用这些资料。
(3)通过设计使我们树立正确的设计理念,懂得合理的设计应该是技术上先进的,经济上合理的,并且在生产实践中是可行的。
(4)通过编写设计说明书,提高我们的技术文件整理、写作及组织编排能力,为我们将来撰写专业技术及科研论文打下基础。
3支架的工艺分析
3.1支架的结构及工艺性分析
支架是起支撑作用的构架,可以承受较大的力,也具有定位作用,使零件之间保证正确的位置。
支架的材料为HT200,灰铸铁生产工艺简单,铸造性能优良,但塑性较差、脆性高,切削性能良好。
由支架零件图(《机械制造技术基础课程设计》[1]图5-6)可知,该支架结构形状对称布置。
主要由底板、肋板和圆柱孔等部分构成。
支架的主要加工表面有:
支架底面、肋板孔与圆柱孔、肋板孔内端面及圆柱孔上端面等。
支架零件加工表面的加工要求如下:
1.支架底面与支架底板上端面距离25mm,未注公差尺寸,表面粗糙度
。
2.肋板孔孔径加工为
,孔轴线与支架底面距离为
,孔内壁表面粗糙度为
。
3.肋板内端面之间距离为
,内端面的表面粗糙度为
。
4.圆柱孔的孔径为
,外径为
,两圆柱孔之间距离为
,孔轴线与肋板孔的孔轴线之间距离为
,孔内壁的表面粗糙度为
。
5.圆柱孔上端面与支架底面的距离为
,未注公差尺寸,其中上端面的表面粗糙度为
。
3.2支架的技术要求分析
该支架零件的主要技术要求为:
1.未注明圆角半径R5;
2.
孔的同轴度允许误差为0.01;
3.
孔与C面的平行度允许误差为0.02;
4.
孔与C面垂直度允许误差为0.01;
5.
孔与
孔的垂直度公差为0.02;
6.零件加工表面相交所形成的棱边去毛刺。
7.未注尺寸公差按GB/T1804—c,未注几何公差按GB/T1184—l。
4毛坯的选择
4.1毛坯的制造形式
任务设计书给定的是支架零件,该零件年产量为50000件,设其备品率
,机械加工废品率
,则该零件的年生产纲领为:
(4-1)
其中N——零件的年产量(件/年);
Q——产品的年产量(台/年);
n——每台产品中该零件的数量(件/台);
a——该零件的倍频率(备品百分率%);
b——该零件的废品率(废品百分率%)
查《机械制造技术基础课程设计》[1](表2-3)可知该产品为大量生产。
一般大批大量生产采用机器造型、模锻等高效率的毛坯制造方法,毛坯精度高,加工余量小采用高效率的专用机床、夹具、量具等工艺装备,工艺规程要求详细。
结合支架零件特点,设计采用先进铸造方法、自动机床与专用机床、高效专用夹具、刀具量具以提高生产率和加工质量,降低生产成本。
由于该支架零件的结构形状较复杂并是大批生产,查《机械制造技术基础课程设计》[1](表2-5)我们可确定采用熔模铸造方式生产,其加工余量小,因此毛坯形状可以与零件的形状尽量接近,可锻造出圆柱孔和肋板孔(减少加工余量和材料损耗)。
毛坯材料可采用HT200。
4.2毛坯尺寸的初步确定
铸件的尺寸公差及加工余量有材料、铸造方法和生产类型决定。
查阅支架的零件图,其所用材料为HT200,大批量生产时采用熔模铸造方式生产。
根据《机械制造技术基础课程设计》[1]表5-7至5-11。
由表5-9可知,灰铸铁在熔模铸造下粘结剂使用水玻璃,毛坯铸件的公差等级为CT7~CT9,取CT8。
由表5-11可知,灰铸铁在熔模铸造下机械加工余量等级为E级。
具体尺寸通过对加工余量的计算后得到。
5支架机械加工工艺路线的制定
支架的工艺特点是:
外形较复杂,尺寸精度、形状精度、和位置精度及表面粗糙度要求较高。
上诉工艺特点决定了支架在机械加工时存在一定的困难,因此在确定支架的工艺过程时应注意定位基准的选择,以减少定位误差;夹紧力方向和夹紧点的选择要尽量减少夹紧变形;对于主要表面,应粗、精加工分阶段进行,以减少变形对加工精度的影响。
5.1定位基准的选择
基面选择是工艺规程中的重要工作之一。
在工艺规程设计中,正确选择定位基准,对零件技术要求、确定加工先后顺序有着至关重要的影响。
定位基准有精基准和粗基准之分。
在选择定位基准时一般都是现根据零件的加工要求选择精基准,然后再考虑用哪一组表面做粗基准才能把在加工出来。
5.1.1精基准的选择
精基准的选择一般遵守以下原则:
1.基准重合原则。
应尽可能选择所加工表面的设计基准为精基准,这样可以避免由于基准不重合度引起的误差。
2.统一基准原则。
应尽可能选择用同一组精基准加工工件上尽可能多的表面,以保证所加工的各个表面之间具有正确的相对位置关系。
3.自为基准原则。
一些表面的精加工工序,要求加工余量小而均匀,常以加工表面自身为精基准进行加工。
4.互为基准原则。
当工件上两个加工表面之间的位置精度要求比较高时,可以此采用两个加工表面互为基准的方法进行加工。
根据精基准的选择原则,选择精基面时,首先应考虑基准重合和基准统一的问题。
本支架零件将经过粗加工的支架底面作为精基准,它既是设计基准又是定位基准,基准重合,它还是后续工序如铣圆柱孔上端面、镗肋板孔等工序的基准。
5.1.2粗基准的选择
粗基准的选择一般遵守以下原则:
1.保证零件加工表面相对于不加工表面具有一定位置精度德尔原则。
选择不加工的表面作为粗基准,尤其应选与加工表面有位置要求的不加工表面,这样可以保证加工面的位置精度;
2.合理分配加工余量的原则。
选重要表面作为粗基准,这样可以保证重要表面的加工余量,加工精度较高;
3.选加工余量较小的表面作为粗基准,这样可以保证加工表面都有足够的加工余量;
4.便于装夹的原则。
选平整、光洁、无飞边、浇冒口等缺陷的表面作为粗基准,这样可以使定位可靠、加紧方便;
5.在同一尺寸方向上粗基准一般不得重复使用的原则。
粗基准只选用一次,应避免重复使用,这样可以避免较大定位误差。
因此选用圆柱孔上端面作为粗基准。
5.2拟定工艺路线
5.2.1加工方法的选择和加工阶段的划分
根据各种加工方法的经济精度和表面粗糙度、已确定的生产纲领、零件的结构形状和尺寸大小等因素来选择各表面的加工方法。
1.支架底面的表面粗糙度要求较高为
,所以确定最终加工方法为精铣。
加工路线为粗铣→半精铣→精铣。
2.肋板内表面与圆柱孔上端面的表面粗糙度要求较高为
,所以确定最终加工方法为精铣。
加工路线为粗铣→半精铣。
3.肋板上的孔与圆柱孔的表面粗糙度为
,
孔的公差等级要求7级,
孔的公差等级要求8级,表面粗糙度和位置精度都要求较高,所以确定最终加工方法为精铰。
加工路线为粗镗→扩孔→粗铰→精铰。
加工路线为粗镗→精铰。
4.支架地板上的两个装配孔为
,精度要求较高,最终加工方法为精铰。
加工路线为钻孔→扩孔→精铰。
5.沉头孔表面粗糙度为
,位置精度和表面粗糙度要求较低,故采用钻孔、锪孔就能达到图纸上的设计要求。
表1支架零件加工方法的选择
加工面
尺寸精度和几何精度要求
表面质量要求
加工方法选择
支架底面
圆柱孔上端面与支架底面的距离为
,底面为精基准、
粗铣→半精铣→精铣
圆柱孔上端面
圆柱孔上端面与支架底面的距离为
,上端面为粗基准。
粗铣→半精铣
肋板内表面
两肋板之间距离为
粗铣→半精铣
肋板上的孔
直径
,孔轴线与支架地面之间的距离为
粗镗→扩孔→粗铰→精铰
圆柱孔
直径
,孔轴线与肋板孔的孔轴线之间距离为
粗镗→精铰
装配孔
直径为
,两孔之间距离为
钻孔→扩孔→精铰。
沉头孔
直径为
,孔深
钻孔→锪孔
辅助工序
孔口及锐边
去毛刺
图1零件三维图
图2零件主视图
图3零件左视图
图4零件俯视图
5.2.2工艺路线的拟定
在工艺路线的拟定过程中要遵循机械加工工序顺序的安排原则。
即:
1.划线工序。
对于形状复杂、尺寸较大的毛坯或尺寸偏差较大的毛坯,应先安排划线工序,为精基准提供找正基准。
2.基准先行。
按照“先基面后其它”的顺序,先加工精基准面,再以加工出的精基准面为定位基准,安排其它表面的加工。
3.先粗后精。
按先粗后精的顺序,对精度要求高的各主要表面进行粗加工、半精加工和精加工。
4.先主后次。
先考虑主要表面加工,再考虑次要表面加工。
次要表面的加工,通常从加工方便与经济角度出发进行安排。
次要表面和主要表面之间往往有相互位置要求,常常要求在主要表面加工后,以主要表面定位加工主要表面。
5.先面后孔。
当零件有较大的平面可以作定位基准时,先将其加工出来,再以面定位孔加工,这样可以保证定位准确、稳定。
6.关键工序。
对易出现废品的工序,精加工或光整加工可适当提前。
在一般情况下,主要表面的精加工和光整加工应放在最后阶段进行。
制定工艺路线的出发点,应当是使零件的几何形状,尺寸精度及位置精度等技术要求能得到合理保证。
在生产纲领已经确定为大批生产的条件下,可以考虑采用万能机床配以专用夹具,并尽量使工序分散来提高生产效率。
除此之外,还应该考虑经济效果,