石英陶瓷.docx
《石英陶瓷.docx》由会员分享,可在线阅读,更多相关《石英陶瓷.docx(15页珍藏版)》请在冰豆网上搜索。
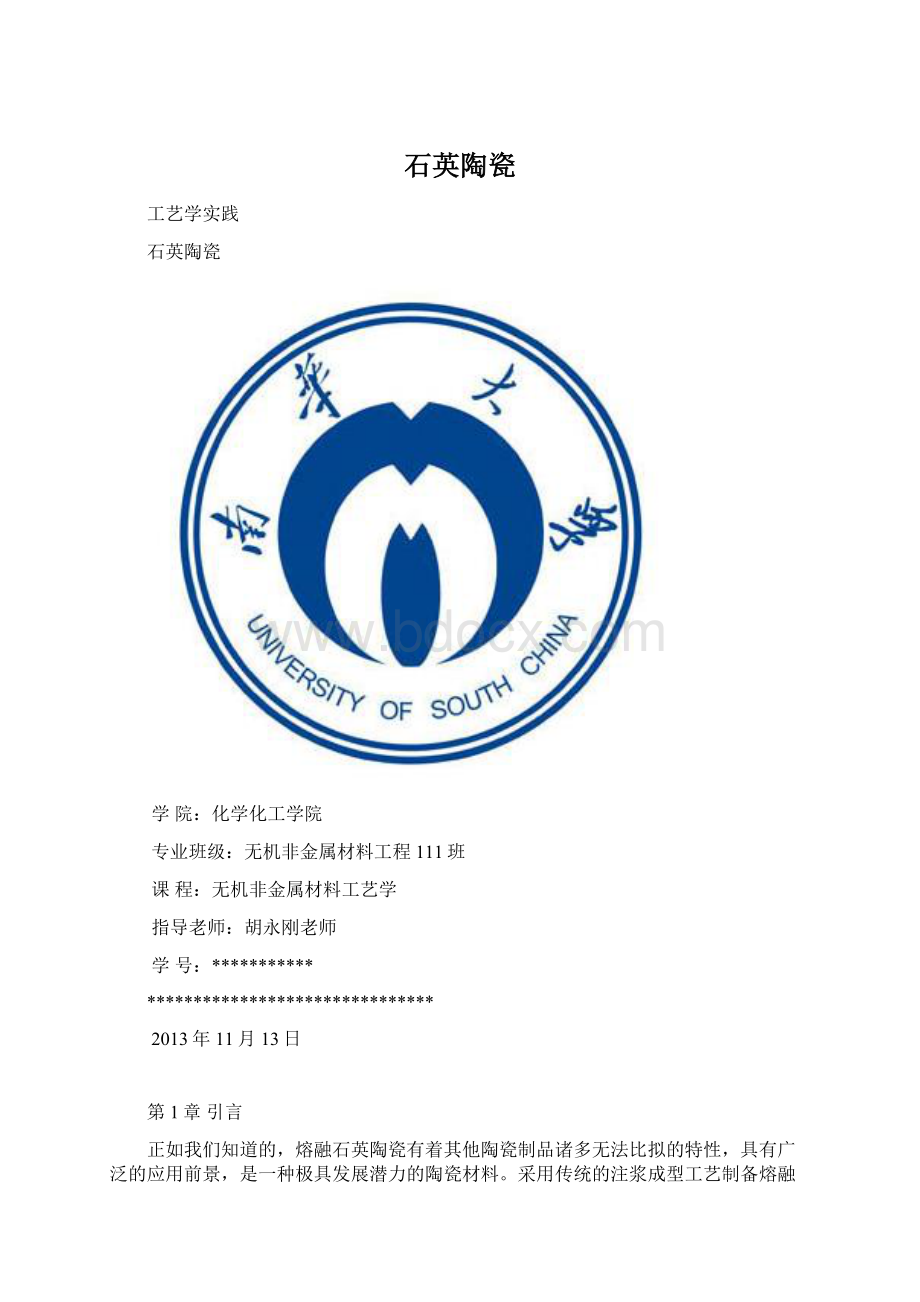
石英陶瓷
工艺学实践
石英陶瓷
学院:
化学化工学院
专业班级:
无机非金属材料工程111班
课程:
无机非金属材料工艺学
指导老师:
胡永刚老师
学号:
***********
*******************************
2013年11月13日
第1章引言
正如我们知道的,熔融石英陶瓷有着其他陶瓷制品诸多无法比拟的特性,具有广泛的应用前景,是一种极具发展潜力的陶瓷材料。
采用传统的注浆成型工艺制备熔融石英陶瓷时由于成型过程中固化时间较长,从而延长了生产周期,增加了生产成本;另一方面,注浆成型过程中容易造成坯体的颗粒偏析,坯体出现分层现象,特别是对大型、厚壁制品,会导致结构及性能上的不均匀。
因此,为满足一些特殊领域对熔融石英陶瓷制品的强度(弯曲强度大于40MPa)及整体均匀性的要求,必须对石英陶瓷的强度及均匀性予以改进提高,减少缺陷的产生,提高可靠性。
本课题设计是为满足高性能熔融石英陶瓷的制备而提出的。
本课程设计拟采用先进的注凝成型技术,通过对料浆引入复合添加剂,并对成型、烧成工艺参数进行调整和控制,制备出高强度、高密度和高可靠性的熔融石英陶瓷制品,拓宽熔融石英陶瓷的应用范围。
第2章概述
2.1石英陶瓷的简介
石英陶瓷是一种新型高纯耐高温石英材料,它既保留了石英玻璃的诸多优点,又可采用陶瓷的一系列生产艺。
它是以熔融石英或石英玻璃为原料,经破碎、成形、烧成等一系列工序制备而的产品。
由美国Georgia理工学院在20世纪60年代研制成功并于1963年投入批量生产。
石英陶瓷具有导热性低、膨胀系数小、耐高温、热稳定性好,以及与其它品种石英玻璃相比成本低等优点。
石英陶瓷还有一个最大的优点.就是在1100摄氏度以下,其强度随着温度的升高而大大增加。
从室温至1100℃,其强度可增加33%。
由于具有上述许多优良的性质,因此自问世以来,迅速得到了推广及应用.其应用领域也涉及到宇宙飞船、火箭、导弹、雷达、原子能、电子、钢铁、炼焦、有色金属、玻璃等工业领域。
2.2、石英陶瓷的发展现状
2.2.1国外发展现状
目前,美国、法国、德国、日本等国家具有较高的研制开发水平,石英陶瓷也得到了广泛应用。
主要用途是作为耐火材料及中等温度下的能抗拒温度剧变的结构材料。
根据使用条件的不同,研制开发的石英陶瓷制品具有不同的性能特点,既有高致密度、高强度的系列制品,也有低密度、高气孔的隔热保温制品和泡沫石英制品。
如美国的Ceradyne公司生产的熔融石英陶瓷导弹天线罩,法国的Vesuvius公司生产的玻璃水平钢化炉和金属带材热处理用棍棒等均代表了目前国际上熔融石英陶瓷研制生产的先进水平。
2.2.2国内发展现状
我国熔融石英陶瓷的生产基本是以钢铁冶炼用熔融石英水口以及玻璃窑炉用熔融石英耐火材料为主,多属中低档石英陶瓷制品。
20世纪90年代我国加强了熔融石英陶瓷的研制开发,目前我国的高档熔融石英陶瓷的研制也已达到了国际先进水平,山东中材高新材料股份公司研制开发的玻璃水平钢化炉用石英陶瓷辊、金属带材热处理炉用石英陶瓷空心辊,玻璃浮法窑用耐火材料等多种产品的质量在国内处于领先地位,得到了用户的认可,产品质量达到了国外同类产品的先进水平。
国内外石英陶瓷材料性能比较
2.3石英陶瓷的结构与性能
2.3.1热性能
与一般陶瓷和耐火材料相比,石英陶瓷的优良的物理性能是其特性之一。
它不仅线胀系数和高温蠕变小,而且热稳定性和耐老化性能好。
石英陶瓷的高温蠕变有一个剧增阶段和一个停止阶段,当温度一旦达到变形起始温度时,则变形量急速增加,基本呈线性正比关系。
石英陶瓷的导热系数低,接触热阻大。
其导热系数随温度的升高而相应增大,在温度低于1200℃范围内,导热系数增大速率较慢。
而当温度高于1200℃时,则成倍地增长。
正是由于石英陶瓷的低线胀系数,因而也具有相当好的热稳定性。
2.3.2化学稳定性
石英陶瓷具有良好的化学稳定性(除氢氟酸及300℃以上的热浓硫酸对其有侵蚀外),盐酸、硫酸、硝酸等对石英陶瓷几乎没有作用。
锂、钠、钾、铷、铯等等金属熔体对石英陶瓷也几乎没有作用。
而且其耐玻璃酸液侵蚀性也很好。
2.3.3电性能
石英陶瓷的电性质很好。
电阻也很大,其介电常数介远远低于电损耗角正切随温度的变化都氧化铝等其他高温陶瓷,可用于绝缘材料,也是导弹和雷达天线罩的良好材料。
2.3.4抗折、抗压性能
与其他陶瓷有所不同的是石英陶瓷的抗折强度、抗压强度是随着温度的升高而大大增加,这是因为熔融石英陶瓷随着温度升高其塑性增加,脆性减小。
例如:
从室温至1100℃时,刚玉陶瓷的抗折强度降低67%,高温陶瓷的抗折强度降低25%,而石英陶瓷反而增加33%,这一性能对熔融石英陶瓷在高温下使用很有利。
2.3.5核性能
石英陶瓷的核性能也很好。
由于一般晶体在重辐射下都将转变为非晶质相,而石英玻璃是非晶质结构。
热膨胀系数又很小,因此在辐射条件下与其他材料相比结构是稳定的。
此外,石英陶瓷的强度基本不受核辐射的影响,并具有低的热种族俘获截面,所以广泛应用于原子工业及辐射实验室。
由于辐射能够稳定非晶质结构,因此其工作温度可以超过一般使用时的界限,即发生大量结晶化的温度限。
2.4石英陶瓷的应用
2.4.1冶金行业
石英陶瓷制品以其极低的膨胀系数和较高的热稳定性,在有色冶金方面取得了广泛的应用。
在铸钢行业中,对浸入式水口的材质要求严格,既要热稳定性好、导热率低,又能经受钢水的冲刷和耐保护渣的侵蚀,因此石英陶瓷成为浸入式水口的首选材料之一。
2.4.2电工行业
石英陶瓷同时具有介电强度、耐火耐热的特点,从而可以应用到电热绝缘器和光波反射器。
石英陶瓷能制造出适合各种条件的绝缘结构,具有高的介电强度,在一般温度和高温下的击穿电压高,介电数值低,介电损失角正切值低和热绝缘性能好等特点,这就保证了该材料在电工行业中的广泛应用。
2.4.3浮法玻璃行业
石英陶瓷具有导热系数小、热震稳定性好、热膨胀系数小、不易沾附锡灰及杂物等优点,可以明显提高玻璃的表面质量。
因此很多大尺寸的石英陶瓷制品已经广泛的应用在浮法玻璃的生产中。
2.4.4玻璃深加工方面
目前,钢化玻璃在多方面得到了广泛的应用。
国内外现在广泛采用辊道式水平钢化炉玻璃炉取代了以前的垂直吊挂式玻璃钢化系统,生产出了高质量的钢化玻璃。
石英陶瓷的特点完全能够满足使用要求,因此从一开始就被熔融石英陶瓷辊棒就被应用到了钢化炉中,并取得了很好的效果。
2.4.5航空方面
石英陶瓷可用于火箭发动机的喷嘴、头部及前室等部位,是目前国内外广泛采用的导弹天线罩材料之一。
美国的爱国者导弹、潘兴II导弹、天弓III导弹、Sam-D导弹等均采用石英陶瓷天线罩,我国在石英陶瓷天线罩的研制方面已逐步赶上世界水平,并在多个型号导弹上得以应用在原子能工业中,作为在核燃料中的基质(Si02-U02)体系和辐射屏蔽材料,也广泛用来作为在射电望远镜中作光学反射器,也是红外线的高质量反射器。
2.4.6精密平台
由于石英陶瓷导热系数小、热量不易传递、升温缓慢、热膨胀系数小,可以使得精密平台热变形较小,同时石英由于热膨胀产生的内应力引起的变形远小于铝、钢和氧化铝,因此,石英陶瓷成为制作精密平台比较理想的陶瓷材料。
2.4.7坩埚
在太阳能行业,石英陶瓷坩埚是太阳能电池用多晶硅铸锭炉的关键部件,它作为装载多晶原料的容器。
由于其使用条件十分苛刻,对坩埚的纯度、强度、外观及内在质量、高温性能、尺寸精度等要求非常严格。
石英陶瓷坩埚是目前不可替代的关键性消耗材料,由于是一次性使用,所以需求量巨大。
2.5石英陶瓷的制备工艺
在国内外石英陶瓷的生产中,目前普遍采用的成型工艺是泥浆浇注成型(注浆成型),其次还有离心浇注成型、浇注成型,蜡注成型,半干法成型,等静压成型,在石墨模热压成型与捣打成型等。
上述这些成型工艺制备的制品普遍存在着显微结构不均匀、材料可靠性差、不适于制作形状复杂的制品、生产周期长、效率低、成本高等缺点,难以适应大批量工业化生产的需要。
特别是对于一些对材料性能要求特别高的石英陶瓷制品,传统的成型工艺己经远远不能满足各个领域对熔融石英陶瓷的要求。
随着现代技术的进步,新的陶瓷成型工艺得到的迅速的发展,尤其是新的成型方法的出现,为陶瓷工业的发展奠定了技术基础。
如注凝成型技术在近几年得到了较快的推广应用,已经功的应用于氧化铝、氮化硅等陶瓷的制备。
熔融石英陶瓷的成型也已经开始应用注凝成型技术,并取得了较好的效果。
本课程设计中主要说明注凝成型法
注凝成型工艺是20世纪90年代以来出现的一种新的胶态成型工艺,是美国橡树岭国家实验室M.A.Jammey等人首先发明的,是传统的胶态成型工艺与有机化学理论的理想结合。
注凝成型的原理是将陶瓷粉末颗粒分散于含有有机聚合物单体和交联剂的水溶液或非水溶液中,制成低粘度、高固相体积含量的浓悬浮体,然后加入引发剂及催化剂,将这种浓悬浮体(料浆)注入模型中,在一定的温度条件下,有机聚合物单体交联聚合成三维网络状聚合物凝胶,并将陶瓷颗粒原位粘结而固化形成的坯体,即原位固化。
所谓原位固化就是指颗粒在悬浮液中的位置不变,靠颗粒之间的作用力或者悬浮体内部的一些载体的性质的变化,使悬浮体从液态转变成固态。
在浓悬浮体从液态转变成固态的过程中,体积没有收缩,介质没有量的变化。
注凝成型技术首次使用较低含量的有机物使陶瓷料浆原位固化,大大提高了陶瓷部件显微结构的均匀性,增加了陶瓷材料的可靠性。
由于该工艺与其它传统的成型工艺相比具有许多优越的特点,引起陶瓷界内专家的普遍关注,使得该技术得到了很块的发展,并己经在实际中获得了推广应用。
注凝成型工艺流程
料浆加入引发剂混合均匀后,经真空除气后,注入模具内,浇注过程中,对注凝成型料浆或成型模具或者是两者一前一后并有重叠的施以物理场如机械振动、超声波振动等的作用,从而实现注凝成型过程的动态化。
在40-80℃温度下固化,固化时间因制品尺寸形状不同而不同,一般在20min以上,坯体固化后进行脱模干燥烧成。
2.6石英陶瓷制备中的影响因素
2.6.1动态作用对注凝成型的影响
浇注过程中对料浆和模具施加的动态作用,可使料浆中的陶瓷颗粒在机械波或其它物理场的作用下重新位移重排,形成均匀致密的显微结构,减少或消除由于气泡和搭桥等现象所导致的非均匀结构。
尤其是在料浆往模型中注人的过程中或注人后,对模型和料浆施以物理场。
并且在注凝料浆开始胶凝固化前适当时间停止这种物理场作用,可使料浆中的颗粒得以均匀地排列,形成均匀的显微结构,图a显示出采用振动波辅助注凝成型工艺中颗粒在振动波作用下通过位移消除搭桥现象,形成较紧密堆积的原理,因此可以有效地形成一个结构均匀、致密度高的陶瓷坯体,由这种坯体烧结的制品强度等性能明显改善,可靠性显著提高。
通过20-30min的机械振动可使生坯密度提高0.03-0.05g/cm3。
由图b的扫描电镜照片可以看出机械振动可使熔融石英陶瓷材料的显微结构更加均匀致密。
图a
图b
2.6.2固化温度对注凝成型的影响
在聚合过程中引发剂分解属于吸热反应,温度的提高有助于促进初级自由基的形成,提高引发效率而单体的聚合反应是放热反应,在反应引发之后,聚合过程中如果温度过高,聚合反应过程中会放出气体,聚合的速度非常快,气体来不及排除,被包裹在坯体中,形成气孔。
另外也会导致料浆中水分的汽化,在坯体中产生气孔。
为了提高坯体固化速度,成型可适当提高温度至50-80℃之间进行,温度低时固化时间长,温度高时固化时间短。
2.6.3有机单体、引发剂引入对注凝成型的影响
单体引人量与固化时间的关系见图c,由图可见有机单体的引人量越多,聚合速度越快,当料浆中有机单体的浓度大于某一范围后,加人引发剂后在极短的时间内发生聚合反应,料浆来不及浇注。
反之,有机单体的引人量越少,聚合速度越慢,固化时间越长,坯体强度也随之降低。
对于熔融石英料浆而言,适宜的有机单体引人量范围为0.5%-2.0%。
引发剂的作用是形成初级自由基,促进单体分子形成单体自由基,引发聚合反应。
随着引发剂加人量的增大,料浆中初级自由基浓度增大,引发速率增大,聚合反应速度加快。
引发剂用量较小时,聚合反应进行的缓慢,甚至不能进行反应,降低成型效率。
引发剂用量过大时,聚合反应剧烈,可能导致料浆不能完成浇注即凝固。
熔融石英陶瓷的注凝成型,引发剂用量与坯体固,由图d可见引发剂用量控制在每千克料浆的0.5-2.0ml范围内,聚合反应速度较为适宜。
c单体引入量与固化时间关系d引发剂用量与固化时间的关系
2.6.4石英陶瓷的相组成的变化与热稳定性
石英陶住相组成和热定性与烧结温度的关系
1000℃之前,坯体中主要发生了球磨时形成的硅溶胶的脱水与分解过程,分解的产物是无定形的二氧化硅。
由于原料中碱金属和碱土金属的氧化物、氧化铁等熔剂氧化物的含量极少,不可能形成足以影响坯体烧结的低共熔点的液相,这时侯玻璃态的石英原料颗粒还未参与烧结,坯体结构无明显变化。
这时坯体尺寸和吸水率均无大的变化,强度亦维持较低的水平。
坯体加热温度在1000一1200℃,尽管这时候仍不可能形成促进烧结的液相,二氧化硅在此温度下的蒸气压也很低,但是,无定形二氧化硅是一种热力学上的亚稳状态,扩散活化能低,通过扩散传质使坯体致密化和颗粒间形成牢固结合。
故坯体有明显的收缩,吸水率下降和强度上升。
坯体的烧结过程的物质迁移是靠扩散传质实现时,烧结有两个特征,其一,烧结速率与原料粒度的五分之三次方成正比,如图所示,在以扩散传质为主的烧结中,线收缩不会超过6%,这正好可以说明石英陶瓷烧成收缩小的原因。
扩散传质分为表面扩散和体扩散。
烧结初期以表面扩散为主,随温度升高,体扩散也活跃起来。
对非晶态的颗粒而言,表面扩散的结果在颗粒间形成颈部,不改变颗粒的非晶态,而体扩散则不同,它可以消除颗粒内部的结构缺陷和导致结构质点的有序化—从非晶态转变为晶体。
所以,在1000一1200℃的石英陶瓷的烧结仍保持非晶态的结构相组成。
在1200℃或略高一点的温度下方石英化过程即将开始。
1200一1400℃温度下,体扩散导致非晶态的二氧化硅形成方石英晶粒和方石英晶粒的生长是坯体烧结和结构改变的主要特征。
方石英化对坯体的显微结构和性能显示出两重性,一方面促进了坯体烧结—坯体的体密度增加,闭口气孔下降另一方面改变了坯体的相组成—由单一的非晶态转化成晶体与非晶态混杂的显微结构。
由于晶体与玻璃相在热性质上的巨大差异从而对材料的性能产生了不利的影响一强度下降和丧失优异的热稳定性。
石英陶瓷的强度在以后又开始随烧成温度的提高而有所提高,显然,1300℃可作为陶瓷结构和相组成变化的一个转折点,强度随晶相的增加而有所提高。
若石英陶瓷在本设计的温度范围内不能得到吸水率低于2%的烧结体,可以解释为石英陶瓷的烧结是非晶态物质的固相烧结,二氧化硅的熔点为1713士5℃,完全致密烧结的温度应在1450℃左右,即材料完全方石英化并且方石英晶体得到良好的发育生长。
二氧化硅相变关系图
2.7石英陶瓷制备中可能出现的问题以及应对方法
2.7.1色斑
1)色斑产生的原因
色斑一般是内表面受到外来物质的污染而不是陶瓷本身的缺陷形成的。
石英陶瓷生产过程中要求内装硅胶干燥剂,是生产过程中石英陶瓷内表面唯一能接触到的物质。
接触变色硅胶水溶液的陶瓷,干燥后表面呈淡蓝色;接触无色硅胶水溶液的陶瓷,干燥后表面没有颜色变化。
石英陶瓷生产周期长,使用的变色干燥剂容易粉化,周转过程中由于变色硅胶干燥剂的摩擦、碰撞,容易产生粉末或小颗粒并透过纱布包装落到石英陶瓷内表面,在潮湿环境中吸收水分,使变色硅胶干燥剂中含有的氧化亚钴溶解到水分中,渗透污染到陶瓷内部。
同时陶瓷材料吸附力较强,使氧化亚钴能稳定地存在于陶瓷材料中,并随着环境温度的变化使石英陶瓷表现到蓝色的色斑变化。
2)色斑解决办法
a、硅胶干燥剂改为无色硅胶干燥剂(带致密且透气的无纺布包装);
b、硅胶干燥剂应在60-70ºC,30min条件下烘干后使用,最多烘干2次;
c、使用包装袋包装石英陶瓷时必须使用绳子扎紧,不允许开口存放;
d、在石英陶瓷生产过程定点烘干、更换干燥。
2.7.2裂纹和蚀坑
1)裂纹和蚀坑产生的原因
a、粉料中各组分的百分比、弹性性能、各相界面的相对断裂能、尺寸大小和强度等不匹配。
b、坯料配方不当。
坯料中挥发含量较高,灼碱量大;可塑性原料用量过少,坯料可塑性差,生坯强度低。
c、坯料颗粒过粗或过细。
粉料中有泥粒子、干硬块、湿块或过于致密的料块,水分不均匀,有过干、过湿现象或水分波动过大。
d、烧成时,预热阶段温度过高,升温过快,受热不均匀;制品形状复杂、薄厚区烧结收缩不一致;粉料中的各组成在烧结过程中发生的相变及反应造成了一定的体积变化。
2)、解决方法
a、配料时仔细筛选,使粉料颗粒尽量一致;水分分配均匀。
b、在坯料中相应增加可塑性原料,提高生坯的强度;减少挥发含量。
c、在烧成时升温不要太快,应缓慢升温,使水分充分蒸发;制品制作时保持壁薄厚程度一致,形状简单,不用太复杂。
2.8石英陶瓷的性能测定
2.8.1石英陶瓷的粒度测定
粒度分布是指某一粒径或某一粒径范围的颗粒在整个粉体中所占的比例。
粒径的大小和分布会影响成型和烧结。
粒度分布的测定方法有很多,常用的有筛分法、沉降法、激光法和吸附法。
本设计中采用激光法测试原料的粒度。
激光测试法是依据光的衍射和散射以及散射原理进行测试的。
用激光做光源,当光为波长一定的单色光后,衍射和散射的光能的空间(角度)分布就只与粒径有关。
对颗粒群的衍射,各颗粒级的多少决定着对应各特定角处获得的光能量的大小,各特定角光能量在总光能量中的比例,应反映着各颗粒级的分布丰度。
由特定角度测得的光能与总光能的比值推出颗粒群相应粒径级的丰度比例量。
本设计采用湿法分析,机械搅拌使样品均匀散开在水中,超声震荡使团聚的颗粒充分分散,使大小颗粒在整个体系中均匀分布,再用激光照射,用计算机处理数据得出结果。
2.8.2物相分析
物相分析包括价态分析、结晶基本成分分析和晶体结构分析。
本文采用X射线衍射方法来进行结晶基本成分分析。
X射线衍射是利用X射线的波长较小,
穿透样品时在晶格之间产生衍射,再利用劳埃方程和布拉格定律以及衍射花纹,来计算晶体的晶格常数,推断结晶相的成分。
实际分析中常用X衍射图谱与已知的PDF卡片对照的简易方法来判断样品中的结晶相成分。
2.8.3微观形貌测试
本设计的微观形貌的测试是利用扫描电子显微镜(SEM)完成的。
扫描电镜通过用二次电子和背散射电子信号成像,研究样品表面的显微结构和断面形貌特征。
其优点是景深大,放大倍数大,图像分辨率高,不破坏样品。
2.8.4其它性能测定
对所制成的石英陶瓷制分别品进行抗压、抗折强度,PH值、密度的测定,并讨论所制作的石英制品是否符合课程设计的要求。
第3章石英陶瓷制作方案
方案中采取的石英陶瓷制备工艺为注凝成型法。
3.1原料
本方案中采用的主要原料为熔融石英粉料(江苏东海产的高纯度熔融石英粉料),要求其真比重为2.21g/com,玻璃相为100%,粒度240以目,莫氏硬度7,PH值6.0。
熔融石英粉料化学组成
化学组成
Si02
Al2O3
Fe2O3
Na2O
K2O
Li2O
含量
99.9-99.95%
20-30ppm
10-25ppm
10-20ppm
20-25ppm
1-2ppm
辅助原料及其功用
名称
分子式
品级
功用
丙烯酰胺
C2H2CONH2
工业纯
单体
N,N-亚甲基双丙烯酰胺
C7H10N2O2
化学纯
交联剂
过硫酸铵
(NH)4S2O
分析纯
引发剂
去离子水
H2O
工业纯
分散介质
乳酸
C3H5O3
化学纯
调节PH
聚乙烯醇
PVA
1600聚合度
粘合剂
3.2制备料浆
3.2.1配置单体预混液:
本方案为丙烯酰胺凝胶体系,将单体按一定配比溶于去离子水中,配置成预混液。
(适宜的有机单体的引入量范围为0.5%-2.0%)
3.2.2表面改性:
由于熔融石英属于脊性料,为了提高其塑性,加入熔融石英质量份量3%-7%体积的PVA(质量分数15%聚乙烯醇溶液)溶液进行表面改性,过改性后的熔融石英颗粒表面包覆了PVA,有利于提高生坯的强度和稳定性,且易于成型操作。
3.2.3制备浆体:
本方案采用二次加料法。
两步制浆法即为首先将50%-70%的熔融石英粉料、pH调节剂等添加剂、全部的去离子水加入球磨机中进行球磨至要求粒度,再加入剩余的30%-50%熔融石英粉料及剩余的添加剂,再进行球磨混浆,分两步完成料浆制备。
其特点是:
工艺比较复杂,但料浆的粒度分布合理可控,制成的制品性能相对较好。
3.3注凝成型
在已经制作好的料浆里加入每千克料浆的0.5-2.0ml范围内的引发剂过硫酸铵,并将其混合均匀。
经真空除气后,注入模具内,浇注过程中,对注凝成型料浆或成型模具或者是两者一前一后并有重叠的施以物理场如机械振动作用,从而实现注凝成型过程的动态化。
3.4热固化
陶瓷料浆通过丙烯酰胺的聚合反应完成固化成型,成型的坯体以聚丙烯酰胺的网络结构为骨架,陶瓷颗粒固定其中,陶瓷颗粒与聚合物凝胶通过吸附作用,形成具有一定强度和柔韧性的坯体。
固化过程可在40-80℃之间进行,温度低时固化时间长,温度高时固化时间短。
40℃时固化时间为2h,80℃时固化时间为0.5h,我们可以根据制品的形状大小来选择确定合适的固化温度。
3.5坯体干燥
干燥的实质是水分扩散和溢出表面的过程。
为了避免坯体收缩不匀造成翘曲和开裂等现象,初期干燥须在低温和高湿度的条件下进行,一般控制湿度大于90%。
当坯体收缩至内部固相颗粒相互接触以后,收缩现象停止,这时可以提高温度或降低湿度继续干燥,以缩短干燥周期。
整个干燥周期中坯体的收缩率与固相含量有关,固相含量为50%(质量分数)时收缩率约3%。
更高固相含量下的收缩率很小甚至可以忽略,干燥后坯体中的粘合剂的质量分数不大于4%。
3.6烧成
待坯体烘干完成后,便可进行烧结过程。
烧结是石英陶瓷生产中很重要的一个环节,它对石英陶瓷的物理化学性能有很大的影响。
熔融石英陶瓷的烧结方法包括常压烧结、热压烧结和热等静压烧结等。
目前在实际生产中应用的大都是常压烧结。
常压烧结又称为普通烧结,指烧结过程中烧结坯体在无外加压力的常压下置于烧结炉中,在热能作用下坯体由粉末聚集体变成晶粒结合体,多孔体变成致密体。
它是烧结工艺中较传统、简单、广泛使用的一种方法。
为保证获得比较理想的致密程度,熔融石英陶瓷要采用低温慢烧、高温快烧的烧结技术。
一般石英陶瓷的最高烧成温度不宜超过1300ºC,为避免析晶,900ºC以上的高温阶段应快烧制度。
本设计的烧结过程中的烧结制度如下:
(1)坯体的水分蒸发期(室温-300ºC):
坯体在这一阶段主要是排除在干燥中所没有除掉的残余水分。
入窑水分控制在2%,主要是吸附水。
这是时坯体的气孔率较大,高达25%-40%,在这阶段可以稍微快速地升温不致于使产品开裂。
该阶段烧结时间为1.5h,并在300ºC这个温度点上持续烧结1h。
(2)氧化分解及晶型转化期(300-950ºC)在这一阶段,坯体内部发生了比较复杂的物理化学变化:
结构水的排除,碳酸盐分解;有机物、碳素和硫化物被氧化;石英晶型转化。
这个过程烧结时间为10h。
从300ºC逐渐提高温度至450ºC,在这个阶段有机高分子聚合物脱水分解过程,此过程烧结时间为1.5h
从450ºC逐渐提高温度到650ºC,在这个阶段主要进行的是硅溶胶的脱水,由于硅浴胶脱水很困难,脱水过快就直接导致坯体开裂,因此这个阶段一定要慢速升温,此过程烧结时间为5h。
并在650ºC这个温度点上持续烧结1h。
(3)玻化成瓷期(950-1250ºC):
该时期是烧成的关键,其最大特点是釉层玻化,