大连100000m3罐施工技术方案.docx
《大连100000m3罐施工技术方案.docx》由会员分享,可在线阅读,更多相关《大连100000m3罐施工技术方案.docx(64页珍藏版)》请在冰豆网上搜索。
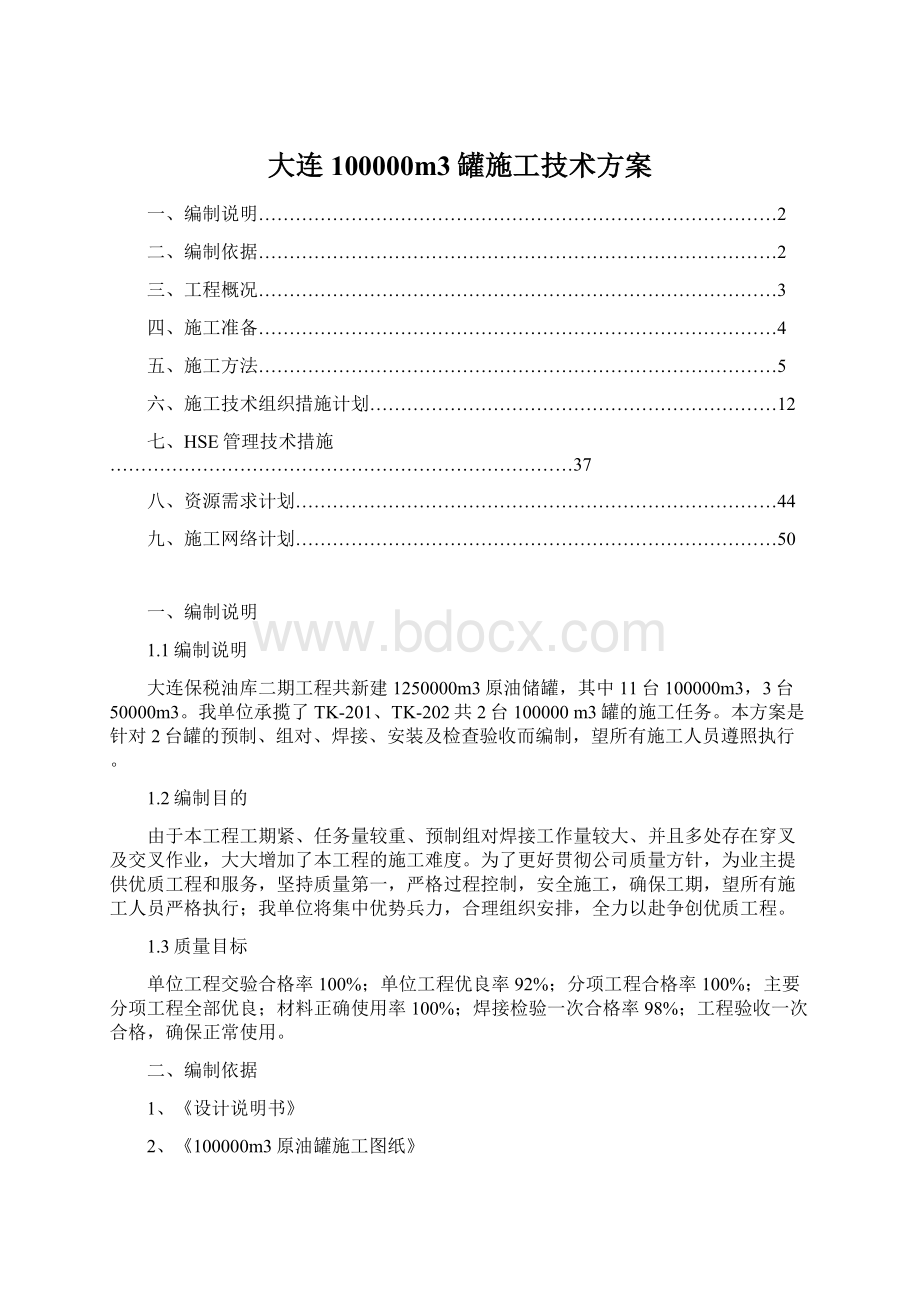
大连100000m3罐施工技术方案
一、编制说明…………………………………………………………………………2
二、编制依据…………………………………………………………………………2
三、工程概况…………………………………………………………………………3
四、施工准备…………………………………………………………………………4
五、施工方法…………………………………………………………………………5
六、施工技术组织措施计划…………………………………………………………12
七、HSE管理技术措施…………………………………………………………………37
八、资源需求计划……………………………………………………………………44
九、施工网络计划……………………………………………………………………50
一、编制说明
1.1编制说明
大连保税油库二期工程共新建1250000m3原油储罐,其中11台100000m3,3台50000m3。
我单位承揽了TK-201、TK-202共2台100000m3罐的施工任务。
本方案是针对2台罐的预制、组对、焊接、安装及检查验收而编制,望所有施工人员遵照执行。
1.2编制目的
由于本工程工期紧、任务量较重、预制组对焊接工作量较大、并且多处存在穿叉及交叉作业,大大增加了本工程的施工难度。
为了更好贯彻公司质量方针,为业主提供优质工程和服务,坚持质量第一,严格过程控制,安全施工,确保工期,望所有施工人员严格执行;我单位将集中优势兵力,合理组织安排,全力以赴争创优质工程。
1.3质量目标
单位工程交验合格率100%;单位工程优良率92%;分项工程合格率100%;主要分项工程全部优良;材料正确使用率100%;焊接检验一次合格率98%;工程验收一次合格,确保正常使用。
二、编制依据
1、《设计说明书》
2、《100000m3原油罐施工图纸》
3、《钢制焊接油罐》API650
3、《立式圆筒形钢制焊接储罐施工及验收规范》GB50128-2005
4、《立式圆筒形钢制焊接油罐设计规范》GB50341-2003
5、《现场设备、工业管道焊接工程施工及验收规范》GB50236-1998
6、《钢制压力容器焊接工艺评定》JB4708-2000
7、《钢制压力容器产品焊接试板的力学性能检验》JB4744-2000
8、《承压设备无损检测》JB/T4730-2005
9、《热轧钢板和钢带的尺寸、外形、重量及其允许偏差》GB/T709-2006
10、《气焊、手工电弧焊及气体保护焊焊缝坡口基本形式与尺寸》GB/T985-1998
11、《埋弧焊焊缝坡口的基本形式与尺寸》GB/T986-1998
12、《钢结构工程施工质量验收规范》GB50205-2001
13、《钢质石油储罐防腐蚀工程技术规范》GB50393-2008
14、《压力容器涂敷与运输包装》JB/T4711-2003
15、《安全技术操作规程》Q/JH121.11.004-92
三、工程概况
3.1工程简介
本装置共有立式圆筒形钢制焊接储罐14台,我公司承揽施工其中两台。
设备名称:
原油罐;外形尺寸:
φ80290×21970mm;全容积为101536m3;设备总重为2025872kg,;罐体主要材质为Q235-B/16MnR/08MnNiVR。
其结构主要由罐底板、罐壁板、双浮盘、顶平台、盘梯、抗风圈及附件几大部份组成。
罐底边缘板采用了弓形板结构,中幅板为条形板结构。
弓形板间采用对接焊,弓形板与中幅板及中幅板与中幅板间采用对接焊;罐壁板为对接焊;双浮盘为搭接焊。
储罐主要技术参数
结构形式
双盘浮顶罐
执行标准
GB50128-2005
公称容积
100000m3
计算容积
101536m3
设计压力
正压0MPa
试验压力
正压充水试验
负压0MPa
负压0MPa
最高充水液位
20200mm
介质密度
860kg/m3
介质允许充装最高液位
20200mm
工作温度
常温
储存介质
原油
基本风压
650N/m2
设计温度
60℃
基本雪压
400N/m2
抗震设防烈度
7度
焊接接头系数
1.0
场地土类别
II类
腐蚀裕量
1.0mm
加热器加热面积
500m2
保温材料/厚度
超细玻璃棉/80mm
公称直径
80000mm
壁高
21870mm
罐底重
538589.7kg
罐底材质
08MnNiVR/Q235-B
罐壁重
804242kg
罐壁材质
08MnNiVR
16MnR/Q235-B
浮顶重
505456kg
浮顶材质
Q235-B
抗风圈
88295kg
抗风圈材质
Q235-B
加强圈
43163kg
加强圈材质
Q235-B
盘梯及平台
3966kg
盘梯及平台材质
Q235-B
保温结构
90000kg
保温结构材质
超细玻璃棉
各种板设计板厚及材质
板号
板厚(mm)
壁板高度(mm)
材质
第一带板
δ=32
H=2450
08MnNiVR
第二带板
δ=29
H=2450
08MnNiVR
第三带板
δ=22
H=2450
08MnNiVR
第四带板
δ=19
H=2450
08MnNiVR
第五带板
δ=15
H=2450
08MnNiVR
第六带板
δ=12
H=2450
08MnNiVR
第七带板
δ=12
H=2450
16MnR
第八带板
δ=12
H=2450
Q235-B
第九带板
δ=12
H=2450
Q235-B
罐底边缘板
δ=20
33块
08MnNiVR
罐底中幅板
δ=12
161张
Q235-B
浮顶底板
δ=5
322张
Q235-B
浮顶顶板
δ=5
338张
Q235-B
3.2工程特点
二期新增14座原油罐位于原一期西侧。
我单位承建的2台罐(TK-201、TK-202)紧邻一期,靠近路边,方便原材料运输。
由于施工现场没有多余场地,所以我单位只有在外围租赁预制场地,距离施工现场7公里,施工过程中原材料需要二次倒运。
2台罐除了一次密封、二次密封、刮蜡机构、加热器及阀类设备外,全部在预制场预制,通过二次倒运到现场进行组装、焊接。
此次工程工期紧,工程量较大;零部件繁多;施工工期又在夏季,天气炎热多雨,为了给用户提供满意的服务,要求我们必须克服任何困难,创造条件,高效的完成此工作。
3.3工程工期要求
本项施工任务工期非常短,定于2009年5月3日开始施工,至2009年8月30日中交。
四、施工准备
4.1施工现场准备
4.1.1施工现场达到“四通一平”,水、电、气(汽)、通讯接通。
4.1.2土建基础施工完毕,基础交接合格,具备安装条件;罐基础周围回填、并夯实,具备站车条件。
4.1.3施工主要工种配备齐全,且经过一定的岗位培训,焊工应持有劳动局颁发的相应项目资格证书上岗。
4.1.4施工过程中所需的机具、卡具落实到位,运至现场。
4.1.5现场暂设布置整齐,预制场地平整完毕,预制平台铺设完成,一切准备就续,进料就可以进行预制工作。
4.2施工技术准备
4.2.1认真阅读各项施工技术文件。
4.2.2施工前组织工程技术人员审查图纸,熟悉图纸、设计资料及有关文件,并进行施工图纸会审。
4.2.3根据图纸要求和现场情况,编制可行的施工技术方案,并经各级主管部门审批合格。
4.2.4各专业工种经过技术培训,取得相应资格证书,施工前储罐排板图应绘制完成。
4.2.5施工前由工程技术人员进行技术交底,参加人员:
承包队长、安全员、检查员和全体施工人员。
五、施工方法
5.1施工程序
5.2施工方法
由于施工现场没有多余场地,所以只有在外围租赁预制场地,我单位将在这里完成施工的预制工作:
将罐壁板喷砂、下料、滚弧、油漆;罐底板、顶板的下料、喷砂、油漆;全部预制完后运输至安装现场;罐体附件也是如此。
此油罐安装方法采用正装自动焊法。
壁板的焊接:
环缝采用埋弧横焊自动焊,立缝采用气电立焊自动焊;罐底边缘板采用手工电弧焊、中幅板采用埋弧角焊自动焊;浮顶底板及顶板采用CO2气体保护焊加手工电弧焊;盘梯平台、抗风圈等采用手工电弧焊。
5.2.1预制平台的铺设
为了满足现场预制件的预制工作,在预制场内铺设预制平台两座,各300m2。
剪板机、数控切割机及罐底中幅板和边缘板的预制均要做砖石混凝土基础,各两组。
其中剪板机基础为7500×5000×3000mm,地下部分为2000mm深;数控切割机基础为16500×100×120mm,地下部分为60mm深;中幅板基础为20000×6000×1000,边缘板基础为9000×4000×1000mm。
地下部分均为500mm深。
5.2.2罐底的施工方法
5.2.2.1罐底板的铺设
基础验收合格后,进行罐底板的铺设,铺设时应按图纸先找好0º、90º、180º、270º中心位置,用拉线法划线,并用油漆标记。
利用盘尺由中心向圆周测量,划出边缘板外边缘线,并做好标记。
先铺设弓形边缘板,铺设前先将垫板点焊于两块边缘板任意1块下侧,间隙小于1mm。
铺设时可按中心线位置分四份对称组装;弓形边缘板全部铺完后再铺设中幅板,中辐板铺设时,先铺中幅板中心条板,然后再铺中心条板的两侧条板,直至整个中幅板铺成,中幅板铺设原则为先中间后两边。
铺设顺序如下图所示:
5.2.2.2罐底板的组对
(1)按施工图方位,划出底板在基础上的十字中心线和底板外边缘线。
(2)在基础上划出底板对接缝处垫板位置线。
在垫板铺设前,现场应根据边缘板间对接焊缝的位置,在环墙上开槽,深度6mm,以便能将边缘板连接垫板嵌入槽内,使整个边缘板与环墙保持良好接触。
示意图如下:
(3)铺设底板垫板。
垫板从油罐中心向外铺设。
垫板长度方向中心线应与罐底边缘板平行,平行度偏差应小于3mm;垫板长度方向中心线与罐底板对接焊缝长度方向中心线之间的距离偏差应小于3mm。
当垫板需对接时,应采用带垫板的结构,对接接头应全熔透。
中幅板铺设之前,从罐中心开始向外组焊连接。
(4)罐底板铺设前,每张底板下表面应涂刷两遍无机富锌防腐涂料。
(5)罐底中幅板应从油罐中心向外铺设,罐底边缘板的铺设在油罐中心附近的中幅板铺设完之后进行;垫板应与对接的两块底板紧贴,其间隙不得大于1mm。
罐底板与垫板点焊定位时,将相邻两张钢板的相邻边与垫板点焊,另外两边自由收缩。
(6)罐底边缘板对接接头采用不等间隙,外侧间隙6mm,内侧间隙10mm。
先焊边缘板外端400mm对接缝。
采用手工焊,焊后磨平。
5.2.2.3罐底板真空试漏方法
罐底铺设焊接完成后,应进行真空试漏。
试漏时,先在焊缝表面涂肥皂水,用长方形真空箱压在焊缝上,真空箱底部四周用玻璃高密度海绵密封,用胶管与真空箱泵相通,通过真空箱上盖装有的密封有机玻璃观察箱内渗漏情况,当箱内真空度达到0.053MPa时,若焊缝表面无气泡出现,证明焊缝无泄漏,即为合格,如发现气泡应立即作好标记,必须用砂轮将缺陷表面磨开,明确渗漏原因后方可修补,坚决不可在缺陷表面进行修补,修补后重新试漏。
5.2.3罐壁施工方法
壁板坡口采用自动坡口机进行加工,加工成型的壁板应用卷板机进行滚弧。
卷板前,应对卷板机滚辊进行清理,下上滚辊表面不得有可损伤钢板表面的硬物存在;卷板时应确保板长边与卷板机滚辊垂直,可利用特制样板检查;在滚弧过程中为了必免钢板回弹,应制作2具半弧形胎具配合卷板,卷板机一侧放置一具;滚弧后的壁板应放置在钢平台上检查弧度及垂直度,其偏差应在本方案要求内;检查合格后的壁板放置在弧形胎具上运至现场待用。
⑴第一带壁板的组装
壁板采用正装法组装。
第一带壁板在底板边缘板外侧300mm范围焊接、检测合格后即可进行,组装前应按排板图及施工图在罐底板上划出第一带壁板安装基准圆及单块壁板位置,并做出明显标记;在底板上沿内外安装线焊接定位挡板,内侧沿圆周线布置,间距500mm一块,挡板规格100mm×100mm×12mm;外侧挡板距外安装线30mm,可先按2m一块布置,等壁板就位调整时再加焊。
罐壁围板利用两台吊车进行。
吊装时,根据壁板排板图,从定位圆上一点开始,分成两组沿两个方向围板。
第一块壁板及第二块壁板安装时,可先对壁板进行粗找平,调整其安装位置,垂直度后,可用F型支撑临时固定。
整圈壁板直立后,利用外侧定位挡板及大头楔子调整安装位置,使每块板与安装基准圆和每块板位置线吻合;利用调整拉杆调整壁板垂直度,并做临时固定;采用正反螺栓调整立缝间隙,每条纵缝利用六组正反螺栓组件;采用大头楔子与龙门板板配合调节错边量;以上项目找正同时应对壁板上边缘板的水平度进行调整,当全部项目符合本方案要求时,用F型支撑焊接固定。
壁板组对合格以后进行纵向焊缝的焊接。
F型支撑如下图所示:
(2)第二层壁板安装
第二带壁板吊装前,应在壁板上焊接背杠龙门板,龙门板间距2m弧长一组,一组2块,位于壁板上下各200mm处并保证上下2块龙门板在同一垂直线上;在已安装完的第一带壁板上边缘内侧安装限位挡板,间距1m一个。
壁板按排板图顺序吊装,就位后立即用背杠进行固定。
立缝组对采用大头楔与龙门板配合调整焊缝错边量;用正反螺栓组件调整焊缝间隙,按规定调整后,在内侧点焊壁板。
由于壁板高度为2450mm,为了方便操作,现场制作组对平台,平台挂于壁板上方,通过滑轮可以行走,操作非常方便。
焊接方法及反变形措施同第一带板。
立纵组对平台每台罐制作4组,示意图如下:
(3)环缝的组对
将第一带壁板“F型支架”上铺跳板,施工人员站在跳板上组对第一带环缝。
环缝组对时,采用龙门板与大头楔配合调节错边量,具体方法将龙门板焊接于第一带壁板内侧距上边缘约50mm处,由上端向下楔入大头楔,用大锤不断楔入,直至错边量符合设计要求;错边量调节时宜从一点开始向两个不同方向进行调整。
间隙调节采用正反扣螺栓组件进行,具体方法为将正反螺栓两端分别焊于两带壁板上,通过杠杆旋转正反扣螺栓完成对板间隙的调节,每条立缝设置正反扣螺栓组件6组。
壁板的垂直度是通过背杠与龙门板配合完成的,将背杠穿入上下两带板预焊的龙门板内,楔入大头楔,使工字钢背杠与上下两层壁板充份接触,工字钢背杠间距2m设置一根。
工字钢背杠待环缝焊接完成后方可拆除并上移。
组对合格以后进行环缝的焊接。
(4)操作平台组装
操作平台主要用于壁板环缝的组对工作,第一、二层壁板纵、环缝焊接完毕后就应组装操作平台。
操作平台由三角架(角钢∠63×63×6制作,每个三角架自带可拆卸的防护栏杆33.5×3.25有缝管制作)沿罐内壁均布;在第一带环缝上端800mm高处,焊接挂钩板,把预制好的三角架联接销穿进挂钩板内,再在三角架上安装走道板,四块跳板并排摆放在三角架上,走道板搭头处用铁线捆绑牢固。
利用此脚手架做为操作平台,即可安装上一层壁板。
其余壁板安装按此顺序交替进行。
5.2.4浮顶的的施工方法
浮盘应在临时支架上组装,根据浮舱底板位置调整立柱高度,使立柱顶部在同一水平面上。
立柱间通过型钢连接,布满整个罐底。
组装施工程序为:
罐底板划临时支架线→安装临时平台→设置浮顶底板四中线标记→铺设浮顶底板→安装浮顶内桁架、隔板等件→铺设浮顶顶板
⑴划线
当中幅板搭接焊缝及第一层壁板纵向焊缝焊接完成后,进行临时支架组装;立柱位置的划线,应按中间条形底板的铺设方向为轴线,向两侧反线,立柱呈等腰三角形排列,底边长3000mm,腰边长2642mm,各立柱位置线标记清楚、牢固。
临时支柱布置图如下图所示:
⑵搭设临时平台
将立柱直立,粗调高度后,将连接工字钢梁安装,临时支架边搭设边利用水平仪将工字钢上表面找平,利用微调调整工字钢上表面。
临时支架安装完毕后,整个角钢上表面应在同一水平面上,相邻角钢水平度允许偏差≤2mm,任意角钢(10m距离内)水平度允许偏差≤5mm(可用拉线检查)。
⑶设置浮顶底板四中线标记
从罐底将浮舱底板四中线划到罐壁,罐壁上焊接临时挂线耳,拉十字细钢丝绳,作为控制铺板和检查的基准线,并在中心作出明显的标记。
⑷浮顶底板铺设
浮顶底板采用了条形板结构,安装时先铺设中心板条,再铺设两侧板条,直至整个底板铺设完。
浮顶底板边铺设边调整,同时将底板点焊焊牢,浮顶底板外边缘应在底板铺完后进行放样切割,并按焊接收缩量将直径放大,以确保与罐壁板的间距。
用拉线法放样,确定出桁架、支架、隔板、环板、边缘板等位置,底板被其覆盖的焊缝应先进行焊接500mm,并用真空箱法进行真空试漏,合格后才可组焊以上构件。
以上构件边组装边将其与底板点焊,用来增加底板的钢性固定。
(5)浮顶顶板的组装
浮顶顶板采用了条形板结构,其铺设顺序与浮顶底板相同,浮顶顶板边组装边与桁架、环形隔板、径向隔板等点焊好,但与外边缘板相连的小块条形边缘板,应在其它条形板焊接完毕后,放样下料铺设。
六、施工技术组织措施计划
6.1质量要求及保证质量的措施
6.1.1材料验收
6.1.1.1储罐用的板材、型材和附件应符合设计要求,并应有质量证明书,质量证明书中应标明钢号、规格、化学成份、力学性能、供货状态及材料的标准。
其机械性能参数符合现行的国家或行业标准,并满足设计图纸要求。
6.1.1.2焊接材料(焊条、焊丝、焊剂及气体)应具有质量合格证明书,焊条质量合格证明书应包括熔敷金属的化学成分和机械性能;低氢型焊条还应包括熔敷金属的扩散氢含量。
当无质量证明书或对质量证明书有疑问时,应对焊接材料进行复验。
6.1.1.3焊条应符合《碳钢焊条》GB/T5117和《低合金钢用焊条》GB/T5118的规定;药芯焊丝应符合《碳钢药芯焊丝》GB/T10045的规定;埋弧焊用焊丝应符合《熔化焊用钢丝》GB/T14957和《气体保护焊用碳钢、低合金钢焊丝》GB/T8110的规定。
焊剂应符合《埋弧焊用碳钢焊丝和焊剂》HG/T5293和《低合金钢埋弧焊用焊剂》GB/T12470的规定。
二氧化碳气体应符合《焊接用二氧化碳》HG/T2537的规定,氩气应符合《纯氩》GB4842的规定。
6.1.1.4现场到货的钢板,必须逐张进行外观检查,钢板表面不得有气孔、结疤、拉裂、折叠、夹渣和压入的氧化皮,且不得有分层现象,其表面质量应符合现行的钢板标准的规定。
6.1.1.5钢板表面锈蚀减薄量、划痕深度与钢板实际负偏差之和,不应大于相应钢板板允许负偏差值。
6.1.1.6不允许使用由于运输、倒运而造成不可矫正变形的材料。
6.1.1.7各种板材、型材、焊材、紧固件等应按材质、规格等分别存放,并设置好标记,材料存放整齐、平稳。
6.1.1.8所有的预制构件在保管、运输及现场堆放时应防止变形、损伤和锈蚀。
6.1.1.908MnNiVR钢板应满足下列要求:
⑴每张板进行超声波复验,探伤方法按JB/T4730-2005《承压设备无损检测》,质量等级不低于I级。
⑵必须按炉号对其化学成份进行复验,每炉号且每台罐至少复验一张。
⑶厚度为32mm、29mm的钢板要求逐张进行力学性能检验,其他厚度的钢板每台罐至少复验一张。
(4)厚度应逐张复验,其结果应符合GB19189-2003《压力容器用调质高强度钢板》中的有关要求。
6.1.1.10碳素钢钢板应满足GB700-88《碳素结构钢》、GB3274-88《碳素结构钢和低合金钢结构钢热轧厚钢板及钢带》的要求。
6.1.2预制要求
一般要求:
油罐在预制加工过程中,所采用的加工方法不得影响材料的机械性能和化学成份。
(1)坡口加工及检查
焊接接头的坡口加工采用气割或机械切割,气割坡口表面粗糙Ra≤50μm;平面度B≤0.04t(t为板厚,mm),且小于1mm,坡口处的熔渣、氧化皮、硬化层应清除干净,坡口表面不得有夹渣、分层、裂纹等缺陷存在。
罐底边缘板应在下料后的两侧坡口100mm范围内进行超声检测,检测结果应符合JB/T4730-2005《承压设备无损检测》中规定的Ⅰ级合格。
罐底边缘板之间对接焊缝坡口表面、底层罐壁和第二层罐壁的坡口表面应进行磁粉检测,检测结果应符合JB/T4730-2005《承压设备无损检测》中规定的Ⅰ级合格。
坡口检查合格之后,在表面涂刷可焊性防锈漆进行临时保护。
钢板表面局部减薄量、划痕深度与钢板实际负偏差之和,不应大于相应钢板标准允许负偏差值。
所有的预制构件在保管、运输及现场堆放时应采取防变形、损伤和锈蚀措施。
罐底板、壁板、浮顶等,划线后应使用白油漆按排板图在指定位置做好标记。
下料后剩余材料按规定做好标记移植。
所有预制件应做好施工记录或填写检查验收表格。
(2)罐底板的预制
根据设计图纸绘制罐底板排板图。
其要求如下:
●罐底板直径放大0.1~0.15/100;
●与罐底边缘板相邻的中幅板在径向上适当放大;
●边缘板沿罐壁半径方向的最小尺寸不得小于700mm;
●底板任意相邻焊缝之间的距离不得小于300mm。
●弓形边缘板的对接接头,外测间隙e1应为6-7mm,内测间隙e2应为8-12mm。
●中副板的宽度不得小于1000mm;长度不得小于2000mm;
弓形边缘板尺寸允许偏差应符合下表:
表1弓形边缘板尺寸允许偏差
测量部位
允许偏差(mm)
长度AB、CD
±1.5
宽度AC、BD、EF
±1.5
对角线之差|AD-BC|
≤3
坡口角度
±2.5°
罐底板边缘板坡口形式如下图:
罐底边缘板应在下料后两侧100mm范围内进行超声波检测。
储罐底板中幅板安装前应进行预制,其几何尺寸允许偏差应符合下列规定:
表2中幅板下料的允许偏差
测量部位
允许偏差(mm)
宽度AC、BD、EF
±1.5
长度AB、CD
±2
对角线之差|AD-BC|
≤3
直线度
宽度方向AC、BD、
≤1
长度方向AB、CD
≤1.5
坡口角度
±2.5°
中幅板坡口形式
(3)罐壁板预制
根据施工图绘制排板图,其要求如下:
●各圈壁板的纵向焊缝沿同一方向逐层错开,底层壁板纵向焊缝间距按设计文件规定,其他各层壁板之间,相邻纵缝间距宜为板长的1/3,且不小于600mm;
●第一圈壁板的纵向焊缝与罐底边缘板对接缝之间的距离不得小于300mm;
●包边角钢的对接焊缝与顶层罐壁纵缝之间距离不得小于300mm;
●除设计文件规定者外,罐壁开口接管或开口接管补强板边缘与罐壁纵缝之间距离不得小于300mm;与罐壁环缝之间距离不得小于200mm;
壁板加工工艺流程:
标记
划线
尺寸检查
坡口切割
防腐
滚弧
样板检查
修整
放入弧形支架
壁板下料的允许偏差,应符合下表规定
表3壁板下料的允许偏差
测量部位
允许偏差(mm)
板长≥10m
板长<10m
宽度AC、BD、EF
±1.5
±1.0
长度AB、CD
±2.0
±1.5
对角线之差|AD-BC|
≤3.0
≤2.0
直线度
宽度方向AC、BD
≤1.0
≤1.0
长度方向AB、CD
≤2.0
≤2.0
坡口角度
环向焊接接头
±2.5°
纵向焊接接头
±1.25°
因为壁板对尺寸要求精度高,所以壁板的下料形式全部采用机械切割。
壁板卷弧
●卷板前,应对卷板机滚辊进行清理,下上滚辊表不得有可损伤钢板表面的硬物存在;
●卷板时卷板机进出板侧应设置弧形支架,以防板变形;
●卷板时