旋液式油水分离器的设计.docx
《旋液式油水分离器的设计.docx》由会员分享,可在线阅读,更多相关《旋液式油水分离器的设计.docx(19页珍藏版)》请在冰豆网上搜索。
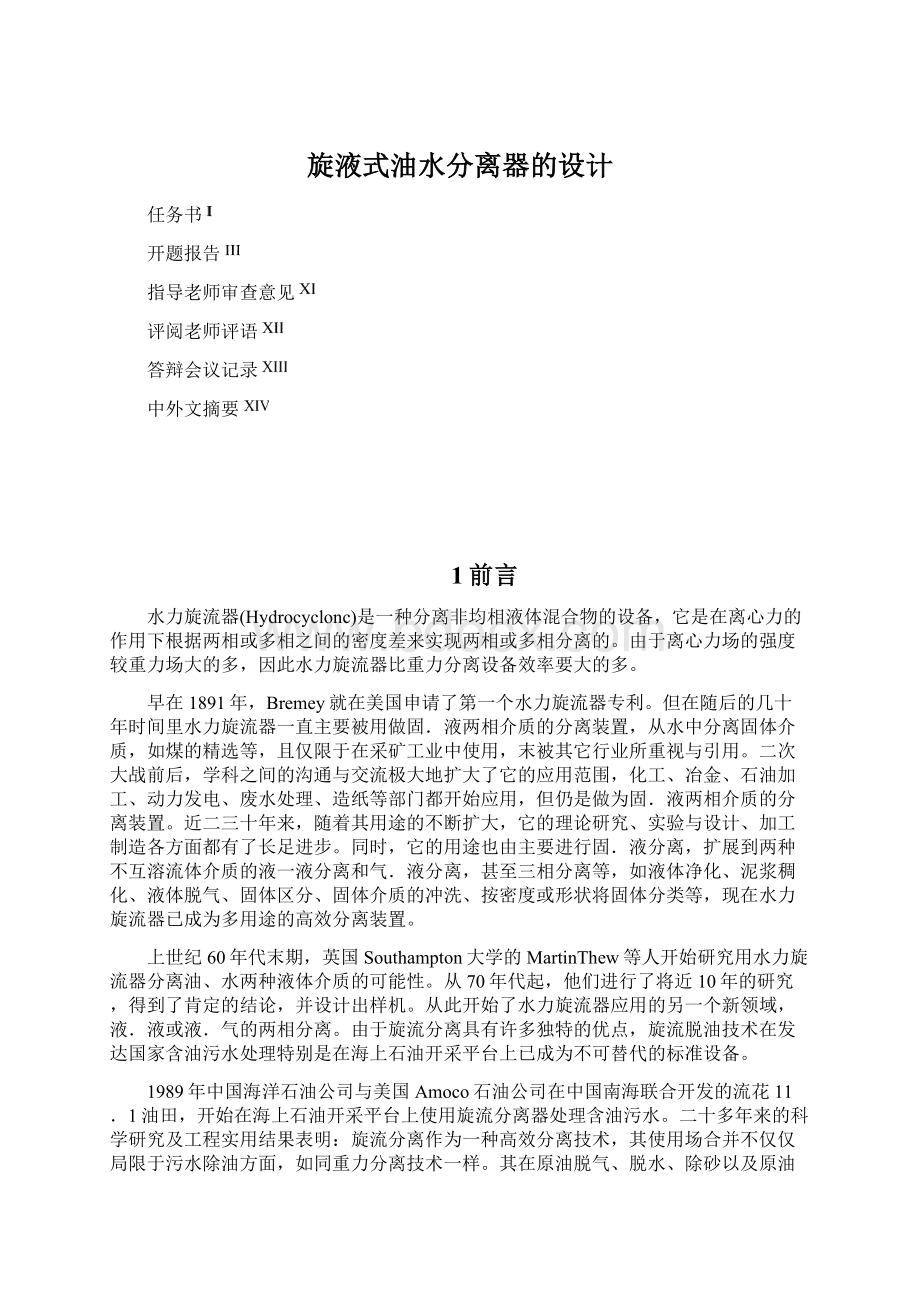
旋液式油水分离器的设计
任务书
开题报告
指导老师审查意见
评阅老师评语
答辩会议记录
中外文摘要
1前言
水力旋流器(Hydrocyclonc)是一种分离非均相液体混合物的设备,它是在离心力的作用下根据两相或多相之间的密度差来实现两相或多相分离的。
由于离心力场的强度较重力场大的多,因此水力旋流器比重力分离设备效率要大的多。
早在1891年,Bremey就在美国申请了第一个水力旋流器专利。
但在随后的几十年时间里水力旋流器一直主要被用做固.液两相介质的分离装置,从水中分离固体介质,如煤的精选等,且仅限于在采矿工业中使用,末被其它行业所重视与引用。
二次大战前后,学科之间的沟通与交流极大地扩大了它的应用范围,化工、冶金、石油加工、动力发电、废水处理、造纸等部门都开始应用,但仍是做为固.液两相介质的分离装置。
近二三十年来,随着其用途的不断扩大,它的理论研究、实验与设计、加工制造各方面都有了长足进步。
同时,它的用途也由主要进行固.液分离,扩展到两种不互溶流体介质的液一液分离和气.液分离,甚至三相分离等,如液体净化、泥浆稠化、液体脱气、固体区分、固体介质的冲洗、按密度或形状将固体分类等,现在水力旋流器已成为多用途的高效分离装置。
上世纪60年代末期,英国Southampton大学的MartinThew等人开始研究用水力旋流器分离油、水两种液体介质的可能性。
从70年代起,他们进行了将近10年的研究,得到了肯定的结论,并设计出样机。
从此开始了水力旋流器应用的另一个新领域,液.液或液.气的两相分离。
由于旋流分离具有许多独特的优点,旋流脱油技术在发达国家含油污水处理特别是在海上石油开采平台上已成为不可替代的标准设备。
1989年中国海洋石油公司与美国Amoco石油公司在中国南海联合开发的流花11.1油田,开始在海上石油开采平台上使用旋流分离器处理含油污水。
二十多年来的科学研究及工程实用结果表明:
旋流分离作为一种高效分离技术,其使用场合并不仅仅局限于污水除油方面,如同重力分离技术一样。
其在原油脱气、脱水、除砂以及原油和污水净化等方面都存在着技术上的可行性、经济上的必要性和工程应用上的广阔前景。
2.选题背景
它的应用领域已扩大到各行各业。
从其可分离的类型上看,除了对完全溶解于液体介质的物质不能分离(溶于液体中的气体,在水力旋流器中也可部分地分离),以及对乳化液难于分离(可加入破乳剂后再行分离)外,其它的两相或三相介质均可分离。
如液--固、气--固、液--气、液--液、液--气--固三相的分离,甚至密度不同,或形状不同的两种固体颗粒亦可用水力旋流器分离。
同时,对水力旋流器的操作特性许多学者作了专门研究,对它的应用场合,运转参数的选择与确定都有了合理的依据。
因此,水力旋流器在实际应用中大都取得了很好的分离效果,经济效益可观。
许多学者专门研究了水力旋流器各部分几何参数的合理确定的问题,研究了几何尺寸变化对分离性能的影响,如,溢流口径和底流口径的形状及大小的改变、圆锥角的变化、尾管长度等,从而逐渐得出了几组合理的几何尺寸。
再次,水力旋流器的设计与制造方面,固一液水力旋流器已有几种定型的设计,其结构与参数经使用证明较为合理。
其中以Rietema,Bradley和Kelsall的三种设计结构应用最普遍,效果最好.他们的选择与比例放大也有自己的关系式,这些关系式都是通过试验推出的,具有半经验性。
液一液水力旋流器的结构与设计,最为合理的是Thew等人的设计,他们在这一领域进行了大量的试验研充。
其效果十分明显。
但液一液水力旋流器的选择与比例放大的理论工作。
目前还很不完善,没存提出什么合理的可供遵循约关系式。
水力旋流器的制造技术也大大提升了,在保证精度以确保水力旋流器的运转特性前提下,制造方法不断改善。
最明显的是液一液水力旋流器的制造,许多国家巳用非金属材料(如聚胺酯等)代替金属材料,用注塑方法加工生产.同时将几个水力旋流器制造在一个外壳内,加大了处理量,又降低了成本。
对于油中分散水进行处理的水力旋流器取得的成功较少。
一篇较早的论文采用了传统的几何结构,实验从水为连续相延续到油为连续相,而且实验采用的也是塑料颗粒,以免乳化。
实验没有得出合理的分离结果,即使是采用水-煤油混合液。
但是实验也的确给出结论认为壁面的润湿性是显著的。
对全锥角为60和具有低剪切扩大入口的旋流器进行水/煤油实验的结果全面总结,揭示出分流比和入口含水量对分离压降的影响,以及仅以水为介质时对轴向速度分布的影响。
一个关键参数是比值Rf/Cf(分流比与含水量之比),这个比值的理想值为当水刚刚发生突破进入溢流时的值1,实验中最小值为1.1。
对水滴的破碎情况与固体颗粒和类比液滴在同一旋流器内的结果进行了检查对比。
从油中分离水(或盐水),当油的粘度接近水的5倍时,很明显没有什么成功的先例,当然界面的自然性质也是极为重要。
最近的研究表明正确匹配的破乳剂可改善分离效率30%,这主要是增强了液滴的聚结。
这项研究也暗示了应当对几何尺寸进行修正,以便正确确定停留时间,使表面活性剂充分发挥作用,而且由于两个排出口停留时间分布(RTD)是不同的,因此也包括对分流比的调整。
我国在液-液旋流分离技术研究方面起步较晚。
80年代末,国内有关科研单位开始正式成立旋流器科研课题进行研究。
他们在引进成套旋流器的同时,根据国外文献资料中提供的液-液旋流器模型尺寸比例,结合自己的设计经验,设计出适合我国油田实际情况的液-液旋流器。
其中江汉石油机械研究所设计的XL-10型液-液旋流分离器,油田现场试验的分离效率为0.94;大庆油田设计院于1992年设计的双锥型旋流器的除油效率基本达到了国外同类产品的指标;胜利油田勘探设计院同沈阳新阳机器制造公司合作开发的预分离旋流器和污水处理旋流器的分离效率分别在80%以上,但在现场应用中性能还不稳定。
此外,石油大学(华东)油气集输教研室在开展液-液旋流分离技术研究以来,先后在结构选型试验研究、旋流管外特性研究、旋流管流场数值模拟方面取得了很大的进展。
开发出了35mm、28mm和20mm高效、低耗系列油水预分、污水除油旋流管,在压降小于0.3MPa时,处理量分别为6.2m3/h、4.1m3/h、2.2m3/h。
其中除油旋流管底流出口水中含油指标达到国外同类旋流器的性能指标。
并且开发出的部分旋流管已经推广应用到胜利油田和大港油田,目前正着手把初步的研究成果转向产品化。
尽管在理论分析方面和计算流体力学(CFD)方面水力旋流器研究稳步向前发展,但水力旋流器研究基本上仍以实验为基础。
LDA的出现使稳态和紊流情况下高涡旋速度场的无侵入式测量成为可能,而且该技术已从70年代早期的一维测量发展到今天的三维测量。
实验架设计的关键因素是独立控制流量和液滴粒径,结合利用等动量取样进行进出口液滴粒径测量。
尽管在线激光衰减散射法在含油浓度测量的精度上不如传统的溶解萃取红外线法,但激光在线法却远比萃取法方便得多。
虽然LDA是单点测量,但当使用染色剂或盐示踪剂时,停留时间的确定可以给出合成的图像,尽管只是针对连续相成份。
尽管Kimber和Thew用圆筒形水力旋流器分出了大约90%的油,但这是不适合于商业应用的。
在研究中,他们很看重多入口的重要性,认为多个入口可实现油核的线性,使油核具有最小的回旋。
他们还发现在底流端具有轴向出口而不是切向出口情况下具有最低的紊流强度。
然而,油芯向出口的流动对轴向出口设在入口端及底流端的两种情况都不能令人满意。
前者得不到稳定的反向流动的核芯,而后者会出现导致油被捕获的周期性的不稳定性,或者说已分开的油和水会发生片刻的混合。
(细小的聚丙烯粉用来模拟油滴,具有更高的摄像可视性,避免偶合和破碎现象)。
Colman和Thew发现增加非常小的锥角,如小到1°~2°全锥角,会导致径向流动的不同,特别是当为了降低剪切和压降而显著扩大入口截面时。
与长圆柱几何结构相比,锥管结构可以给出稳定的、直径细小的反向流核芯,而且允许在极小的溢流孔径下工作。
实验所得到的最好结果是在没有涡流探测管(Vortexfinder)的情况下。
长的圆柱尾管是构成旋流器整体所必须的部件,在圆柱尾管里小粒径的液滴移向轴线上的反向核芯。
发展的步伐逐渐加快。
1983年Colman和Thew发表文章公布了一些概括出的关系式和级效率曲线(粒径测试采用库尔特计数器,CoultreCounter),尽管这篇文献中优化的斯托克斯数St(StokesNum_ber)和雷诺数Re(ReynoldsNumber)之间的关系式被后来发现是错误的。
液-液水力旋流器装置的工作可采用计算机控制,例如,一个3段式水力旋流器装置采用计算机在线控制,如果超声探针探测到入口有一油流段塞,可自动控制将油流切换到污油罐去。
尽管计算机控制在操作上是令人满意的,但在旋流器本身仍没有被验证的情况下,该应用被油田所接受还需要很长时间。
八十年代中期以后,流场测试的结果开始出现。
然而,由于对实验室中的模拟感到怀疑,尤其是对界面的化学和物理性质感到怀疑,后来的工作变得迟缓了。
然而,对旋流器几何尺寸的影响的深入研究,尤其是对入口旋涡的检验,否认了斯托克斯数与欧拉数乘积为常数的说法,认为这很有可能是由于液滴的变形或破碎造成的,最近的一项实验理论研究证实尾直管是必须的。
这项研究还计算了液滴的轨迹,进而表明最近提出的除油水力旋流器理论分析模型需要改正,这个模型显示尾直管内的液滴没有经反向流到达溢流。
一篇关于CFD的论文展现了与实验对比的结果,特别是关于除油旋流器的情况。
文章表明这项工作还有很长的路要走。
总之.水力旋流器出于其特珠的分离机理及结构持证,使它成为独具一格的一种分离装置.在一定的应用场合它比任何其它的分离设备更便于使用。
特别是在石油工业.尤其是今后三次采油技术的全面推广后,水力旋流器的应用将更为广泛。
可以预见.今后若干年内,它必将发挥巨大的效益.在我国石油工业等部门中获得更广泛的应用。
3方案论证
3.1油水分离器的主要特点
围绕实现液—液旋流分离的问题,国内外研究者经过多年研究,在以下方面人们取得了共识:
(a)产生强烈的旋流,使分散相有足够的径向迁移:
(b)旋流腔径要小,要有足够大的长径比,以产生强烈的旋流。
避免过大压降,分散相有充裕的滞留时间;
(c)较轻的分散相总是趋向于流心,因此流心附近的液流层必须稳定,如果流心摇摆就会出现相的重混;
(d)旋流器有很小的圆锥角,导流口的形状和位置能使液流刚好旋转,旋转轴与几何轴线重合,避免分散相的剪切。
结合以上的基本要求,现在所研究的除油型水力旋流器(以下简称油水分离器)是一种较为理想的油水分离设备,它具有以下特点:
(1)结构紧凑,体积小,尤其适用于海上石油钻井平台等场合;
(2)分离效率高,对含油污水的浓度适用范围广;
(3)操作简单,设备的维修少,因为水力旋流器的结构简单,无运动部件,设备出现故障的机会少,可长期连续运行:
(4)对于有较大压力的含油污水(如油田注井水)可不需其他动力,对低压的进料经过加压也可较好的分离。
与其他处理方法相比,用水力旋流器处理处理含油污水可节省大量能源;
(5)由于依靠强大离心力场作用,油滴在设备中停留的时间短(2-3s),对含油污水的较大浓度波动或流量波动能很快地适应;
(6)对基础的运动不敏感。
3.2工作原理
将需要分离的两相混合液以一定的压力从旋流器圆筒体上部的切向进料口注入,从而在器内形成强烈的旋转运动,由于轻重两相的密度差异,重相沿锥体器壁向下,形成外旋流并在下部的底流口排出,而轻相则受流体的拽力向内部运动,并被向上的内旋流由溢流口带出从而完成两相液--液水力旋流器的分离原理,与固--液分离十分相似,它是利用两种混合在一起但不互溶的液体之间的密度差,在水力旋流器体内进行离心分离。
但液--液分离要比固一液分离困难得多,其主要原因是:
①一般两种液体之间的密度差较小,如油与水的密度差一般只有0.1至0.2g/cm3左右,而固--液两种介质之间的密度差常常较大,有时会有几倍的差别。
②分散相的液体介质,不论其密度较连续相液体介质大或小,都是以小滴的形式存在。
这些液滴没有固定不变的形状,在力的作用下极易变形,有时甚至会破裂。
因此.两种液体混合的介质在水力旋流器中分离时.既要求液流在水力旋流器体内形成高速旋转的涡流,以保证液滴有足够的力沿径向方向移动,又要防止液滴在高速旋转时,受到过大的切向剪应力致使液滴破碎,分裂成更细小的液滴,导致分离更加困难。
这都是液--液分离水力旋流器的应用较固--液水力旋流器晚了近一百年的原因。
下面进一步分析一下液--液分离的过程。
两种液体介质的混合物由入口切向进入旋流腔后,在内部产生强烈的涡流。
然后由旋流腔经过很短的大锥角段后,迅速过渡到锥角很小面长度较大的小锥角段,其后进入一个长度较大直径较小的圆拄状尾管内。
这种结构使进入旋流腔后高速旋转的液体很快收缩到细长的小锥角段内,这一段直径变化缓馒,旋转加速度的变化趋于缓和。
同时,液体涡流在细长的小锥角段及尾管中存留时间稍有增加,而液滴在小直径孔中沿径向向轴线移动的路径就短,液滴受到的切向力也减小。
因之,分散相液滴在连续相介质中的分离更平稳,分离的机率大大增加。
在保证液滴分离的同时,减少了其破碎的几率,即使部分液滴破碎成更小的尺寸,也会在长的小锥角段甚至在尾管中进一步分离出。
根据结构上的这些要求,决定了液--液用水力旋流器比同直径的固--液水力旋流器的长径比大很多,因而总长度也大好几倍。
图1工作原理示意图
如图1,在液--液分离中,连续相介质可能比分散相介质重(如从水中分离出所含的少量油),也可能比分散相介质轻(如从油中分离所含的少量的水)。
以上两种不同的情况的分离,原理相似,但水力旋流器的结构会略有不同。
分散相介质较连续相介质轻时,两种介质混合物在水力旋流器体内分离时,轻质分散相向轴线附近移动,形成轻质分散相的核心,并向上从溢流口排出,而分散相介质较重时,它在水力旋流器体内旋转时,就会向器壁移动,并向下从底流口排出。
所以溢流口与底流口直径及水力旋流器的其它某些结构参数会根据分散相介质的浓度及性质而做相应的改变。
此外,由于液体在水力旋流器体内形成涡流.而涡流中心处的压力最低.溶于液体内的气体会分解出,在轴线附近形成一个“气核”。
不论固--液分离与液--液分离。
这个气核都是存在的。
实践证明.这个气核的存在不会影响分离过程.有时还对分离有利。
与固--液分离相同,用水力旋流器进行液一液分离也是不完全分离。
从溢流中排出的液体并不完全是轻质相介质,会同时排出少量重质相介质。
而从底流中排出的液体,不可避免地会含有少量轻质相介质。
但只要操作变量控制恰当,分离效率完全可达到90%-95%以上,有的液--液分离水力旋流器约分离效率高达98%,能满足一般分离要求。
4.旋液式油水分离器结构
图2southampton型水力旋流器结构示意图
水力旋流器是水力旋流法处理含油污水的核心设备。
目前国内外尽管有各种不同结构形式的水力旋流器,但内部结构却基本相同。
本文以较为典型的southampton双锥型水力旋流器为例简述其基本结构。
图2为southampton型水力旋流器结构示意图,它由以下几部分组成。
a入口:
由于液-液两相密度差较小,水力旋流器中必须形成一个大范围的高强度的旋流场,从而达到分离分散相的目的。
但为了防止分散相液滴的破碎,应使其内部具有最小的湍流剪切应力,通过切向进口使流体的线动量尽可能变为角动量。
b旋流腔:
旋流腔是一圆柱形空腔,对于旋流器液--液分离是很关键的部分之一。
从入口进入的油水混合物在这个直径较大的空腔内产生旋转涡流。
若没有旋流腔,则流体从直径较小的入口进入旋流器后会产生较大的压力损失,而且高强度的剪切应力也会增加分散相液滴破碎的几率。
实验表明这个较大直径的旋流腔可以减少压力损失15%-50%,同时还大大降低分散相液滴的破碎几率。
c大锥段:
又称收缩腔,根据角动量守恒原理,利用圆锥的收缩使流体旋转速度增大,强化离心力场。
d小锥段:
也称尾段,是液-液水力旋流器的主要分离段,流体以高强度旋流从大锥段进入小锥段后,尽管也存在壁面摩擦损失,但由于水力旋流器的进一步收缩,使得流体在其中的切向速度进一步加大,高强度旋流得到进一步加强。
同时细长的小锥段使流体在水力旋流器内停留时间增加,这样两相液滴能充分进行径向迁移,从而实现轻相液滴聚集在中心轴线区而重相在其外围。
e圆柱形尾管:
该部分主要用于收集更小的分散相液滴并保持中心油核的稳定性。
f溢流管:
通过溢流管将水力旋流器中心轴线区域的轻相及时排出,防止其在水力旋流器内重新混合。
水力旋流器作为分离分级设备的基本工作原理是基于离心沉降作用。
当待分离的两相混合物以一定的压力沿切线方向进入旋流腔后,由于流向改变,流体处于强烈的旋流状态。
而由于轻相和重相存在密度差,所受的离心力、向心浮力、和流体曳力的大小不同,受离心沉降作用,大部分重相经底流口排出,大部分轻相经溢流口排出,从而达到分离目的。
5.旋液分离器尺寸的计算
液-液旋流器的选型设计方法与固-液旋流器相同,其设计方法有2种。
第1种是根据几何尺寸对压降、处理量、分离效率的影响情况,选择各部分几何尺寸。
这种设计方法需要掌握各设计变量与水力旋流器性能的定量关系。
当然,已有许多经验理论和模型可以利用,除特定的旋流器外,这些理论和模型只能给出近似估算。
第2种方法是选择标准的水力旋流器,按其相似准则和几何尺寸比例关系,进行计算和比例放大,这样能够得到较可靠的设计结果。
第2种设计方法实际是相似设计法,也就是按照设计参数处理量、压降"和粒径的要求,选择性能优良的旋流器,用其相似准数关系和几何尺寸比例关系,计算设计旋流器,在旋流器选型设计中常采用该方法。
5.1主直径的选取
参照文献[2],常用双锥油水分离器的主要结构参数如下表1,任务书中中的处理量600m3/h,可以并联几个此油水分离器共同处理完成
表1常规结构水力旋流器主要结构参数
a.取主直径Dn=28mm,旋流腔直径D=56mm
旋流器直径越大,分离性能越低。
对于油水分离用旋流器,由于油滴尺寸比较小,油水密度差比较小,因此属于难分离的料液,旋流器直径大约在20-70mm之间较为合适。
5.2旋流器其它结构参数的设计
M.Thew等人在1980年BHRA组织的旋流器国际学术会议上公布了他们的研究成果,经研究认为最佳的双锥旋流器尺寸比例为:
D/Dn=2,di/Dn=0.35,du/Dn=0.5,do/Dn<=0.14,L1/Dn=2,L3/Dn=15,大锥夹角为20°,小锥锥度为1.5°。
b.进料口直径di
最佳进料口直径di:
di=0.35*Dn=9.8mm,进料口的作用主要是将作直线运动的液流在柱段进口处转变为圆周运动。
在一定的流量条件下,减小进口面积,使进口速度过大,造成进口区域的湍流程度加大,容易造成液滴破碎、乳化,使分离效率下降。
因此,进口截面积不宜过小。
另外,为了减小进口液流的能量损失,进口形状通常采用摆线形和渐开线型等。
c.溢流口直径do
do=0.14Dn=0.14×28=4mm,对于油水分流器来说,分散相液滴通过短路流进入溢流管对分离性能反而有利,因此溢流管不插入旋流器内而仅仅与旋流器顶盖相接即可。
在一些经典设计中溢流口的直径为do<=0.14D,D为旋流腔直径。
d.底流口直径du
du=0.5*Dc=0.5×28=14mm,底流口与溢流口一样都是对旋流器的性能影响比较大的结构尺寸。
对于液液旋流器来说,底流口直接与尾管段相连接,尾管段的作用是保持旋流器内的内旋流能够保持一个稳定的形状、提高分离效率,通常尾管段的长度取为Lu=20D。
而尾管段直径(等于底流管直径)一般取值为du/D=0.25或du/D=0.33,两者的分离效率几乎一样,只是后者可在更宽的流量范围内提供较好的分离效率。
e.旋流器锥角a
α=20°,旋流器锥角的增大会引起其内流体阻力变大,因此在同一进口压力下其体积生产能力会有所减小,分离粒度随水力旋流器锥角的增大而变大,因此,固液分离用水力旋流器采用小锥角a≤15°。
,但若处理的料浆浓度大而又颗粒粗且不要求分离效率很高时,采用大锥角a>40°,以防底流口堵塞。
f.小锥角为β
β=1.5°,其他尺寸不变时,旋流器的锥角越大,料液在旋流器内的停留时间越短,因此分离能力越低,同时旋流器内的流体阻力随着锥角的增大而变大。
实践证明,对于用于油水分离的水力旋流器,其锥角为1.5°较为理想,因而这种旋流器一般很长,对制造加工提出了更高的要求。
g.圆柱段长度Ll
L1=2*Dn=2×28=56mm,旋流腔是一圆柱形空腔,对于旋流器液—液分离是很关键的部分之一。
从双切向入口进入的油水混合物在这个直径较大的空腔内产生旋转涡流。
若没有旋流腔,则流体从直径较小的入口进入旋流器后会产生较大的压力损失,而且高强度的剪切应力也会增加分散相液滴破碎的几率。
实验表明这个较大直径的旋流腔可以减少压力损失15%—50%,同时还大大降低分散相液滴的破碎几率。
h.后管的长度L3
L3=20*Dn=20×28=560mm,尾管是一个长圆柱形管,内径用Du表示。
它的顶端与水力旋沈器体小锥角圆锥段的内径相连,其长度用L3表示。
该部分主要用于收集更小的分散相液滴并保持中心油核的稳定性。
i.溢流管伸出长度L2
L2=0.5*Dn=0.5×28=14mm
j.溢流管壁厚s
溢流管壁厚的增加,可以提高旋流器的分离效率,并能降低其内部的损失,且
还能略镦提高旋流器的生产能力,所以,设计时可适当加大溢流管壁厚,且溢流管外壁做成环齿形有助于提高旋流器的分离精度.根据文献[3]:
di<=(Dn-do-2*S)/2,即9.8<=(28-4-2*S)/2,取S=2.2;
5.3法兰和法兰垫片的选择
由于油水分离器工作压力在0.1—0.6MPa之间,分别根据GB/T9119—2000和GB/T9126—2003,选择法兰和垫片的工程压力为PN0.6,选择的法兰是平面板式平焊钢制管法兰,其示意图如下图3:
图3平面板式平焊钢制管法兰示意图
旋流腔总直径60.4mm,查表得公称直径为DN50,法兰外径D=140mm,螺栓孔中心圆直径K=110mm,螺栓孔径L=14mm,螺栓数量N=4,螺纹规格M12,法兰厚度C=16mm。
小锥段大端总直径32.4mm,查表得公称直径为DN25,法兰外径D=100,螺栓孔中心圆直径K=75mm,螺栓孔径L=11mm,螺栓数量N=4,螺纹规格M10,法兰厚度C=12mm。
圆柱尾管部分总直径18.4mm,查表得公称直径为DN10,法兰外径D=75mm,螺栓孔中心圆直径K=50mm,螺栓孔径L=11mm,螺栓数量N=4,螺纹规格M10,法兰厚度C=12mm。
然后根据各个公称压力和公称直径选择对应的法兰垫片。
5.4溢流口流量和底流口流量的计算
对于脱油型水力旋流器而言,分流比F即水力旋流器出油口(溢流口)流量与入口总流量的比值。
单纯从净化的角度考虑,分流比适当加大时有利于底流水的净化,即水力旋流器的分离效率会有所提高。
随着分流比的增大分离效率和溢流口液体流速也增大,即在单位时间内其他边界条件不变的情况下随着分流比的增加底流口含油量减小、溢流口流量增大、溢流口含油量减小、分离效率增加。
同时,随分流比的减小,溢流口液体的平均速度也减小,但溢流口液体中含油体积比例增加,这说明分流比的减小使得溢流口流速降低,而溢流口流速对溢流口(出油口)的出油率影响很大。
如果希望出油口出油浓度较高时,降低旋流器的分流比较好,但随之带来的影响是底流口(排水口)的含油量增加了。
所以,在实际应用中应该