储油罐的设计及焊接工艺1.docx
《储油罐的设计及焊接工艺1.docx》由会员分享,可在线阅读,更多相关《储油罐的设计及焊接工艺1.docx(47页珍藏版)》请在冰豆网上搜索。
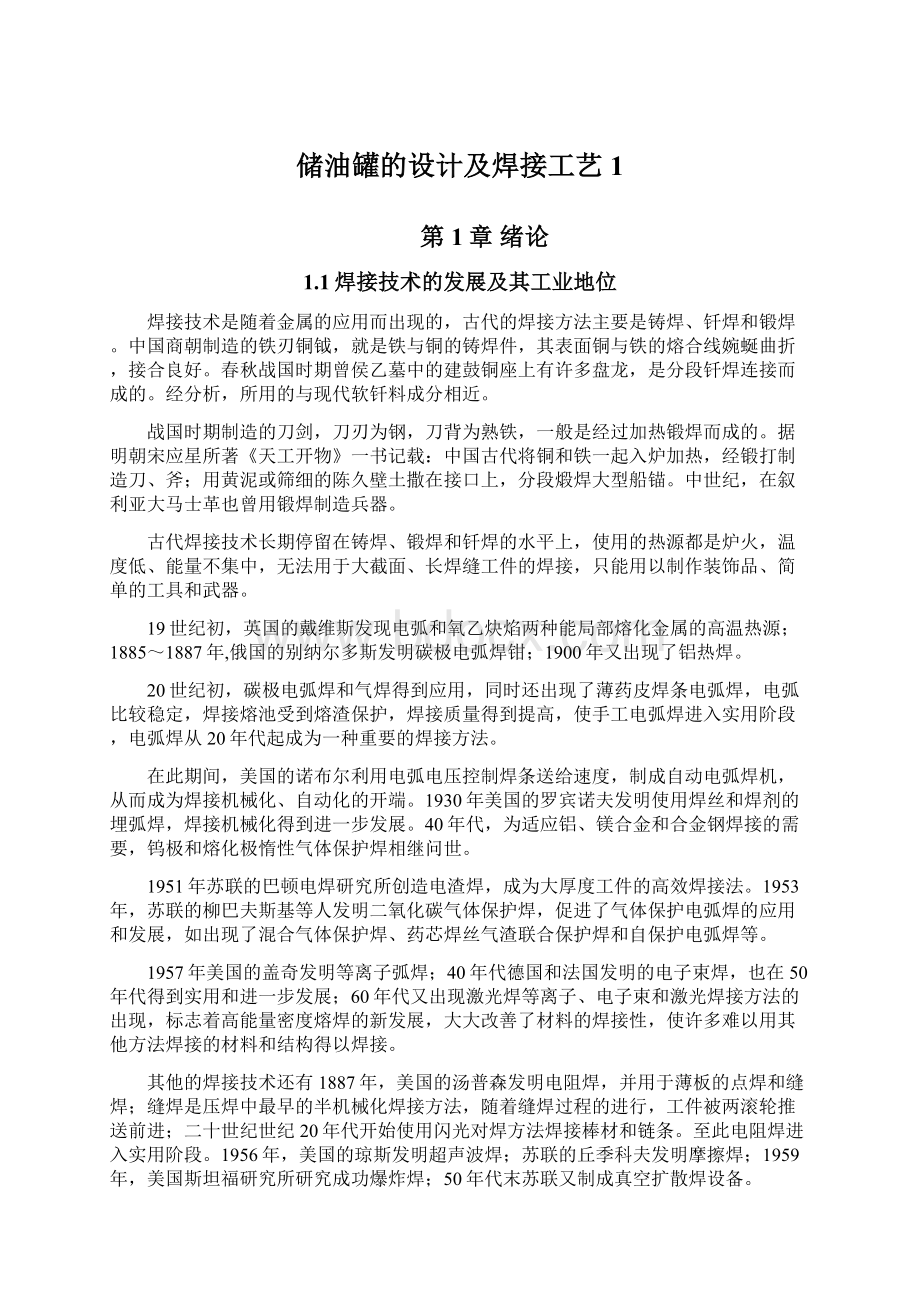
储油罐的设计及焊接工艺1
第1章绪论
1.1焊接技术的发展及其工业地位
焊接技术是随着金属的应用而出现的,古代的焊接方法主要是铸焊、钎焊和锻焊。
中国商朝制造的铁刃铜钺,就是铁与铜的铸焊件,其表面铜与铁的熔合线婉蜒曲折,接合良好。
春秋战国时期曾侯乙墓中的建鼓铜座上有许多盘龙,是分段钎焊连接而成的。
经分析,所用的与现代软钎料成分相近。
战国时期制造的刀剑,刀刃为钢,刀背为熟铁,一般是经过加热锻焊而成的。
据明朝宋应星所著《天工开物》一书记载:
中国古代将铜和铁一起入炉加热,经锻打制造刀、斧;用黄泥或筛细的陈久壁土撒在接口上,分段煅焊大型船锚。
中世纪,在叙利亚大马士革也曾用锻焊制造兵器。
古代焊接技术长期停留在铸焊、锻焊和钎焊的水平上,使用的热源都是炉火,温度低、能量不集中,无法用于大截面、长焊缝工件的焊接,只能用以制作装饰品、简单的工具和武器。
19世纪初,英国的戴维斯发现电弧和氧乙炔焰两种能局部熔化金属的高温热源;1885~1887年,俄国的别纳尔多斯发明碳极电弧焊钳;1900年又出现了铝热焊。
20世纪初,碳极电弧焊和气焊得到应用,同时还出现了薄药皮焊条电弧焊,电弧比较稳定,焊接熔池受到熔渣保护,焊接质量得到提高,使手工电弧焊进入实用阶段,电弧焊从20年代起成为一种重要的焊接方法。
在此期间,美国的诺布尔利用电弧电压控制焊条送给速度,制成自动电弧焊机,从而成为焊接机械化、自动化的开端。
1930年美国的罗宾诺夫发明使用焊丝和焊剂的埋弧焊,焊接机械化得到进一步发展。
40年代,为适应铝、镁合金和合金钢焊接的需要,钨极和熔化极惰性气体保护焊相继问世。
1951年苏联的巴顿电焊研究所创造电渣焊,成为大厚度工件的高效焊接法。
1953年,苏联的柳巴夫斯基等人发明二氧化碳气体保护焊,促进了气体保护电弧焊的应用和发展,如出现了混合气体保护焊、药芯焊丝气渣联合保护焊和自保护电弧焊等。
1957年美国的盖奇发明等离子弧焊;40年代德国和法国发明的电子束焊,也在50年代得到实用和进一步发展;60年代又出现激光焊等离子、电子束和激光焊接方法的出现,标志着高能量密度熔焊的新发展,大大改善了材料的焊接性,使许多难以用其他方法焊接的材料和结构得以焊接。
其他的焊接技术还有1887年,美国的汤普森发明电阻焊,并用于薄板的点焊和缝焊;缝焊是压焊中最早的半机械化焊接方法,随着缝焊过程的进行,工件被两滚轮推送前进;二十世纪世纪20年代开始使用闪光对焊方法焊接棒材和链条。
至此电阻焊进入实用阶段。
1956年,美国的琼斯发明超声波焊;苏联的丘季科夫发明摩擦焊;1959年,美国斯坦福研究所研究成功爆炸焊;50年代末苏联又制成真空扩散焊设备。
近年来,随着国民经济的飞速发展,我国重型机械金属结构制造业取得了令人瞩目的成就。
我国不仅是世界钢材消耗大国,也是一个世界机械制造业大国。
据国际钢铁协会(IISI)统计,2004年世界钢产量首次达到10.3亿t,用钢量为9.35亿t。
我国2004年钢产量为2.72亿t,约占全球钢产量的26%,全年用钢量为3.12亿t,占全球钢产量的33%,其中1.6亿t应用于焊接结构,约占用钢量的51%左右。
而欧美和原苏联焊接结构用钢占其用钢量的60%左右,日本超过70%。
由此可见,我们与工业发达国家相比还有一定差距。
根据有关调查,在1.6亿t焊接结构用钢中,机械制造业金属结构用钢量约占用钢量的45%,钢铁工业的快速发展,给我国焊接行业,尤其是重型机械金属结构行业焊接技术的可持续发展创造了很大的发展空间。
进入21世纪,我国重型机械行业面临新的挑战和机遇,应彻底改善耗能大、耗材高、效率低、工作环境差和自动化程度低的传统焊接产业,促进焊接技术与产业向着优质、高效、节能、低成本、环境友好方面和自动化方向发展,努力将相对人力资源优势转化为科技竞争优势,促进企业进步和产业升级。
1.2行业焊接技术现状
1.2.1中国大陆情况
发展至今,我国的重型机械焊接技术与美国(如P&H公司等)、德国(如西马克公司等)、法国(如奥钢联公司等)、日本(如三菱重工、小松株式会社等)等发达国家间存在很大的差距。
目前,这些国家及地区采用焊接结构件的比例日趋增大,其中自动化、机械化的气体保护焊及多丝埋弧焊等高效焊接工艺方法消耗的焊接金属材料约占全部焊材总量的50~70%,其焊接生产采用机械化、自动化、高效的焊接工艺方法,带来焊接生产效率高、焊接质量好的效果,国际竞争力强。
机械金属结构行业,气体保护焊、双丝埋弧自动焊、龙门焊机、电渣焊等高效焊接工艺方法在大型金属结构制造企业中的应用日趋增多,高效焊接方法完成的金属结构件已占其总重量的50~80%左右,在中小型企业中,CO2气体保护实芯焊丝、埋弧自动焊等方法也得到一定应用。
但总体来说,我国重型机械制造中劳动工资低廉的优势正在被生产效率低下、质量成本高昂的巨大差距所抵消,这应引起我们的足够重视。
1.2.2成就及产品情况
机械金属结构行业主要为国家大型骨干企业和国家重点工程项目提供重型机械装备。
行业制造骨干企业如第一重型机械集团有限公司、第二重型机械集团有限公司、太原重型机械集团有限公司、大连重工起重机集团有限公司、中信重型机械有限公司、郑州煤机厂、北京煤机厂、上海振华港口机械公司、齐齐哈尔第二机床厂等,主要制造大型桥式和门式起重机、4~35m3机械式挖掘机、1~6m3液压挖掘机、大型加压气化炉、加氢反应器、大型舞台设备、航天发射塔架、焦炉机械设备、螺旋焊管设备以及大型减速机、提升机、堆取料机、轧钢锻压设备、氧气瓶压机、水泥设备、粉磨、破碎机械、水利、工程机械、液压支柱、港口机械及环保设备等大型设备。
1.2.3重型机械金属结构行业用钢
我国重型机械金属结构行业大多采用国内外成熟钢种,如Q235系列碳素钢,Q345、Q390系列低合金钢,20g、16MnR压力容器用钢等。
近年来,随着国家重点工程的发展和产品结构的调整,焊接用钢的种类品种大幅度提高,随着钢材种类和品种的不断增多,焊接件的年产量大幅度提高。
据不完全统计,2005年齐齐哈尔第二机床厂焊接件年产量约为1万吨;第二重型机械集团有限公司约为3万吨;太原重型机械集团有限公司为约5万吨;中信重型机械有限公司突破5万吨;上海振华港口机械公司焊接件年产量高达20万吨左右。
焊接结构件以其独特的优势,已取代了铆接结构,替代了铸造结构,成为重型机械行业金属结构设备的主导结构。
1.2.4焊接工艺方法
机械金属结构行业开始起步一般采用手工电弧焊工艺方法。
20世纪50年代开始使用埋弧自动焊和电渣焊工艺方法,主要用于一些厚板对接、工型梁及筒体焊接。
近年来,一些大型企业通过技术改造,相继应用双丝埋弧焊、双丝窄间隙埋弧自动焊、龙门式焊机、轧辊埋弧堆焊等先进的焊接工艺方法,以满足产品制造技术要求。
我国大型骨干企业焊接技术改造,气体保护焊工艺方法在重型机械金属结构行业得到广泛的应用。
可以说气体保护焊工艺方法伴随着重型机械金属结构行业焊接技术的发展而壮大。
在我国八十年代后期,为满足国家重点工程大型机械技术装备制造要求,引进国外先进的焊接技术和设备,对大型骨干重型机械企业进行技术改造,我国大型重型机械金属结构制造企业通过与美国、德国、日本等国家的跨国公司合作制造大型金属结构,批量购买国外气体保护焊设备、焊材等器材,并进行焊工培训。
我国借助国外气体保护焊成熟技术和生产工艺,形成了我国大型金属结构行业以气体保护焊为主的生产能力,从根本上改变了重型机械金属结构行业的制造技术水平,推动了我国气体保护焊技术的发展。
90年代初至今的近十几年时间,以第一届“全国CO2焊接技术推广应用交流会”为契机,我国又分别于2001年和2004年连续举行两届全国CO2焊接技术推广应用交流会,气体保护焊技术在重型机械金属结构行业中推广应用工作持续、稳定、蓬勃发展,气体保护焊技术开发应用能力增强,应用工作从大型机械企业推广到中小企业,而大型重型机械企业的气体保护焊应用也从合作制造产品的生产,推广到普通产品的生产中。
气体保护焊设备、焊材、辅件基本实现国内供给,逐渐形成了我国气体保护焊产业。
1.3储油罐
1.3.1储油罐的分类
储油罐是储存油品的容器,它是石油库的主要设备。
储油罐按材质可分金属油罐和非金属油罐;按所处位置可分地下油罐、半地下油罐和地上油罐;按安装形式可分立式、卧式;按形状可分圆柱形、方箱形和球形。
(1)金属油罐
金属油罐是采用钢板材料焊成的容器。
普通金属油罐采用的板材是一种代号叫A3F的平炉沸腾钢;寒冷地区采用的是A3平炉镇静钢;对于超过10000m3的大容积油罐采用的是高强度的低合金钢。
常见的金属油罐形状,一般是立式圆柱形、卧式圆柱形、球形等几种。
立式圆柱形油罐根据顶的结构又可分为桁架顶罐、无力矩顶罐、梁柱式顶罐、拱顶式罐、套顶罐和浮顶罐等,其中最常用的是拱顶罐和浮顶罐。
拱顶罐结构比较简单,常用来储存原料油、成品油和芳烃产品。
浮顶罐又分内浮顶罐和外浮顶罐两种,罐内有钢浮顶浮在油面上,随着油面升降。
浮顶不仅降低了油品的消耗,而且减少了发生火灾的危险性和对大气的污染。
尤其是内浮顶罐,蒸发损耗较小,可以减少空气对油品的氧化,保证储存油品的质量,对消防比较有利。
目前内浮顶罐在国内外被广泛用于储存易挥发的轻质油品,是一种被推广应用的储油罐。
卧式圆柱形油罐应用也极为广泛。
由于它具有承受较高的正压和负压的能力,有利于减少油品的蒸发损耗,也减少了发生火灾的危险性。
它可在机械,一成批制造,然后运往工地安装,便于搬运和拆迁,机动性较好。
缺点是容量一般较小,用的数量多,占地面积大。
它适用于小型分配油库、农村油库、城市加油站、部队野战油库或企业附属油库。
在大型油库中也用来作为附属油罐使用,如放空罐和计量罐等。
球形油罐具有耐压、节约材料等特点,多用于石油液化气系统,也用做压力较高的溶剂储罐。
(2)非金属油罐
非金属油罐的种类很多,有土油罐、砖油罐、石砌油罐、钢筋混凝土油罐、玻璃钢油罐、耐油橡胶油罐等等。
石砌油罐和砖砌油罐应用较多,常用于储存原油和重油。
该类油罐最大的优点是节约钢材、耐腐蚀性好、使用年限长。
非金属材料导热系数小,当储存原油或轻质油品时,因罐内温度变化较小,可减少蒸发损耗,降低火灾危险性。
又由于非金属罐一般都具有较大的刚度,能承受较大的外压,适宜建造地下式或半地下式油罐,有利于隐蔽和保温。
但是一旦发生基础下陷,易使油罐破裂,难以修复。
它的另一大缺点是渗漏,虽然使用前经过防渗处理,但防渗技术还未完全解决。
(3)地下油罐
地下油罐指的是罐内最高油面液位低于相邻区域的最低标高0.2m,且罐顶上覆土厚度不小于0.5m的油罐。
这类油罐损耗低,着火的危险性小。
(4)半地下油罐
半地下油罐指的是油罐埋没深度超过罐高的一半,油罐内最高油面液位比相邻区域最低标高不高出2m的油罐。
(5)地上油罐
地上油罐指的是油罐基础高于或等于相邻区域最低标高的油罐,或油罐埋没深度小于本身高度一半的油罐。
地上油罐是目前炼油企业常见的一类油罐,它易于建造,便于管理和维修,但蒸发损耗大,着火危险性较大。
基本参数1、压力:
常压 温度:
-19℃~200℃介质:
燃料油(石油化工原料等)2、5m³~100m³卧式油罐基本参数和尺寸 3、安全:
储罐应有壁雷、防静电措施、消防措施,根据工程实际情况由选用单位与环卫措施等统一考虑。
4、防腐:
储罐内壁防腐措施应根据罐内贮存介质确定,外壁防腐措施根据罐土质确定。
5、根据现在容器所造材质及规格不同,主体材质可选用不锈钢、碳钢、低合金钢。
最后根据客户要求来设计制造、安装。
第2章25cm3储油罐结构的制造工艺
2.1储油罐的结构分析
本次设计的储油罐属于II类压力容器。
工业生产中具有特定的工艺功能并承受一定压力的密闭容器和分离容器均属压力容器。
它在石油化学工业、能源工业、科研和军工等国民经济设备,称压力容器。
目前压力容器在各行业中的应用已十分广泛。
贮运容器、反应容器、换热的各个部门都起着重要作用。
本储油罐的设计目的是储蓄和运输石油,石油是无毒易爆介质,每个焊缝都必须保证质量达到要求。
本产品主要是由筒体,封头,法兰所组成。
产品的简要数据如表2-1所示。
表2-1产品简要数据表
设计压力(MPa)
0.2
设计温度(℃)
100
工作压力(MPa)
0.1
全容积(m3)
25
物料名称
导热油,氮气
容器类型
II类
储油罐上还有支座、支架、支撑架、法兰等几个附件。
2.3产品制作工艺流程图
2.3.1筒节制作工艺流程图
此储油罐的筒体部分是由两节筒节焊接而成,筒节的制作工艺流程如图2-1所示。
图2-1筒节制作工艺流程图
2.3.2封头制作工艺流程图
本设计中有两个封头,它们的制作工艺是相同的,如图2-2所示。
图2-2头制作工封艺流程图
2.4筒节制作工艺
2.4.1钢材复检
压力容器是质量要求严格的重要焊接结构。
储油罐的厚度为8mm的Q235B钢板制作。
这两种钢材在使用前应进行必要的化学成分和力学性能复检,还应检验金属材料的表面及内部质量(如夹层、砂眼等)。
2.4.2钢材预处理
(1)矫正
钢材在轧制、运输、装卸和堆放过程中,表面常会出现凹凸不平或弯曲、扭曲、波浪变形等现象。
当这些变形超过一定程度时,会影响焊接结构件生产过程中各工序的正常进行,并将降低产品的质量。
按操作方法的不同对钢板的矫正可分为手工矫正、机械矫正和火焰矫正三种方法。
在本设计中对Q235B钢板的矫正选用的是机械矫正法。
(2)清理
钢材表面存在的铁锈、氧化皮及各种污物等,都将直接影响零件和产品的制造质量,焊前应进行清理的工作。
除锈的方法有种:
化学法和机械法。
本设计中对Q235B钢板清理选用的是机械法中的喷丸方法。
采用GYX-nM型钢材预处理装置,它是一种大型喷丸除锈设备,既可以用于钢板、型钢的表面处理,也可用于结构部件的表面处理。
钢材矫正后,利用电磁吊上料、辊道输送到加热室预热,再进入喷砂机中将铁锈及氧化皮除掉,清理掉丸料后,装置自动喷底漆并烘干,以防钢板在加工过程中再次生锈。
2.4.3划线、下料
(1)下料规范
筒体的排板下料应根据板材实际尺寸进行,绘制排板图时应遵循以下规定:
1最短筒节长度L≥300mm。
2同一筒节在下料时应尽量减少纵向拼接焊缝的数目,同一筒节相邻纵缝间的弧长距离L≥500mm。
3筒节与筒节之间,筒节与封头之间的焊缝不允许采用“+”字交叉焊缝,它们之间的焊缝必须错开,错开量应大于名义厚度的三倍,且不小于100mm。
4筒体内件与筒体焊接的焊缝边缘应尽量避开筒体环焊缝边缘。
5卧式容器的环焊缝应尽可能布置在支座之外,纵焊缝的布置应在筒体下部140或170°范围之外。
6筒体的纵、环焊缝应尽可能避开开孔以及补强圈。
7排板图上必须按《产品标识和可追溯性管理规定》的规定进行标记绘制。
8根据排板图进行下料时,各块板料的材质标记、产品编号、件号、筒节号、板厚及几何尺寸、焊缝编号、坡口方向均应检查合格。
9排板图上应按选定的基准绘制装配基准线,装配基准线对于大直径的容器应间隔45°绘制一条,对于直径较小的容器至少应保证隔90°有一条。
装配基准线沿圆周用规定的标记表示。
10筒体周长一律按中径展开,并参照封头外周长尺寸加以确定。
11筒节下料划线时,板上应注明检查线、实际用料线和切割线。
12切割余量和边缘加工余量根据选定的加工方法或工艺文件要求确定。
13筒体展开长度应考虑纵焊缝收缩量,其数值按有关工艺文件规定。
(2)材划线及下料尺寸的计算和确定
选定钢板尺寸规格后,在板材上进行划线,所谓划线即按构件设计图样的图形与尺寸1:
1划在待下料的钢板上,随后按划线图形进行下料加工的工序。
下料是指将零件从金属材料上按划线标记切割下来的工序。
下料的方法可分为两类:
机械切割和热切割。
本设计中Q235B钢板选用的都是中等厚板的板材,对其下料均选用热切割的方法,采用的设备是CNC-4A型数控切割机,用氧乙炔火焰进行切割。
在划线下料前应先对制作筒节的板材进行选取,因为钢材在卷圆后,内层纤维受压而缩短,外层纤维被拉伸而伸长。
而在内层与外层之间存在着一层既不缩短也不伸长的纤维,该层即为中性层。
制作内筒筒节所用钢材的展开尺寸计算就是以中性层为依据的。
首先,按弯曲内径
与板厚
的比值确定中性层位置,
为中性层位置系数。
,所以
值取0.5。
故筒节的展开直径:
d=Dg+s=2200+8=2208(2-1)
筒节的展开长度:
L=πd=3.14*2208=6693(2-2)
筒节的展开长度即为选用板材的长度;再根据筒体的总长选择板材数量以及每块板材的宽度。
筒体总长5800mm,选取两块板材即可,宽度为2900mm。
采用数控切割机下料时,钢板边缘处厚度不均匀,影响焊接质量,因此,需预留出余边量为50mm。
根据国标709—88热轧钢板和钢带的尺寸、外形和重量。
钢板宽度可为50mm或者10mm倍数的任何尺寸。
钢板长度可为100mm或者50mm的任何尺寸,但厚度小于等于4mm钢板的最小长度不得小于1.2mm,厚度大于4mm钢板的最小长度不得小于2m。
根据以上计算和国标规定,选择制作筒节板材的尺寸为,8mm*6800mm*3000俩块;所选板材尺寸如图2-3所示
图2-3筒节板材尺寸
2.4.4边缘加工
边缘加工是按工艺要求采用一定的加工方法将工件的边缘或端面加工成符合工艺要求的形状、平直度和粗糙度的生产过程。
边缘加工可以消除前到工序加工所产生的加工硬化层和热影响区;根据工艺要求完成坡口加工;消除装配、焊接工件边缘或自由边的各类缺陷,以提高储油罐的整体质量;提高结构的表面质量,也可为产品的后期制作创造条件。
常用边缘加工的方法为刨削、铣削、车削等切削加工工艺。
2.4.5筒节卷制
钢板的弯曲加工,实际上是通过旋转的辊轴,使钢板在辊轴的作用力和摩擦力的作用下,自动向前推进产生塑性变形而弯曲。
本设计选用对称式三辊卷板机,钢板卷制的基本原理如图2-3所示。
图2-4三辊卷板机工作原理图
(1)使用对称式三辊卷板机进行钢板卷制时,在钢板的两端各存在一个平直段(约为两下辊中心距长度的一半)无法卷弯。
为此,在卷制之前,应采取的措施将钢板两端弯曲成所需要的曲率。
预弯的方法有以下两种:
模压预弯和弯胎预弯。
在此选择弯胎预弯的方法,即利用弯曲胎板在卷板机上进行的。
其原理如图2-5所示。
图2-5预弯胎板法工作原理图
预弯胎板一般用厚度大于筒体厚度两倍以上的板材制成。
在本设计中预弯胎板的厚度取20mm。
在冷变形时需考虑到回弹量,预弯胎板的曲率半径应略小于筒体的半径,所以取900mm。
预弯长度应大于两下辊中心距的一半,通常为(6~20)s,在此取240mm。
(2)为防止钢板在卷制过程中出现扭斜,产生轴线方向的错边,滚卷之前在卷板机上摆正钢板的过程为对中。
常用的方法有:
对中挡板对中法、倾斜进料对中法、辊上槽线对中法。
本设计所选用的是辊上槽线对中法,即先在钢板上划出中线,然后与下辊表面的槽线对正,即可对中。
(3)对中后可实施滚卷,使上辊下压,钢板产生一定曲率的弯曲。
卷制时应注意:
冷卷时,不超过材料允许的最大变形率;上辊下压产生的下压力保证辊子不打滑;根据板厚、材质,一次下压量不超过卷板机的额定功率;考虑冷卷时的回弹量,应过卷20~30mm,并随时用样板进行测量。
卷制达到要求曲率时,还应在此曲率下多卷几次,以使其变形均匀和释放内应力,减少回弹。
(4)在滚圆完毕并对纵缝进行装配焊接之后,应再次滚圆,以使筒节的圆度达到规定的范围。
步骤如下:
逐渐加载,达到最大矫正曲率;重点矫正焊缝区,经测量直到合格;逐渐卸载,至卷制过程结束。
2.5封头制作工艺
封头制作的钢材复检、预处理、边缘加工工艺与内筒筒节的钢材复检、预处理及边缘加工工艺相同。
下面介绍封头制作的其它工艺。
2.5.1封头部分的选料
封头在划线下料前应先对制作封头的坯料进行计算。
坯料直径(包括加工余量):
(2-11)
式中:
----毛坯料直径,mm;
----封头内径,mm;
----封头形状影响系数;
----板厚,mm;
----直边量,mm;
100----二次切割余量,mm。
所以,
筒=Dp=1.19*(2200+8)+2*40+100=2807.52mm
由于毛坯料直径过大,所以采用拼板的方法来制作毛坯料,为了避免焊缝十字交叉,压力容器的封头由两块或有左右对称的三块钢板且对接焊缝距封头中心≤1/4
。
内筒封头坯料由:
8mm*1100mm*2850mm和8mm*1750mm*2850mm的两块板材拼焊而成,封头拼板如图2-6所示。
2807
2850
图2-6封头拼板示意图
2.5.2加热
拉延前要对板材进行加热,这样可以提高板材的韧性,降低变形抗力,易于拉延成形。
采用室式加热炉加热。
筒封头材料为Q235B钢板,冲压的起始温度为900-1050℃左右,冲压结束温度不得低于700℃,如温度低于700℃冲压后必须进行回火处理。
温度过高,板材的结构组织将发生变化;温度过低,变形抗力大不易拉延。
2.5.3压制
压制封头的方法很多,可采用人工锤击法、冲压成形法及爆炸成形法等。
本设计采用的是冲压成形法。
整体封头压制属于拉延过程。
拉延也称为拉伸或压延,它是平板毛坯或空心半成品利用拉延模具拉延成一个开口零件的过程。
此加储油罐的封头设计为标准椭圆形。
首先,对冲压封头的压延力进行计算:
(2-12)
式中,
----压边力影响系数,有压边
;
----封头形状影响系数;
----毛坯直径,mm;
----封头内径,mm;
----板厚,mm;
----材料的高温抗拉强度,N/mm2。
根据上式计算出筒封头的压延力:
内筒
冲压设备采用水压机或油压机。
根据上述的延压力计算来选择压力机的吨位,并且需要考虑到冲压直径。
所以可选用500t的四柱式油压机。
在压制封头过程中,当
,需要采用压边圈。
内筒封头的
,所以要采用压边圈。
压边圈主要用来防止由于冲压力过大而产生起皱的现象。
压边圈应安装在下模上面,与下模表面之间应留有1.15~1.2倍板厚的间隙。
由于
,
。
因此,该产品的封头属于中壁封头,中壁封头可一次拉延成形。
2.5.4划线、切割
因考虑到在冲压成形加工工艺过程中存在不稳定因素,较难掌握封头的变形及准确形状,在封头毛坯下料时已预留出100mm修边余量,以便加工后进行修整。
因此,封头冲压成形后利用焊接回转台再按照内筒封头的展开尺寸,进行二次划线及二次切割。
为提高工作效率,可使钢板的二次切割和坡口加工同时进行。
将封头夹持于可旋转的回转平台上,开口朝上,而将割枪夹持于工作平台侧面的支架上,使之对准切割线,由电动机驱动回转平台旋转。
即可切出直边、V形或X形坡口。
切割时主要考虑封头的对中方法,本设计采用三角对中法,即将封头放在等边三角形支架上,找出最低点,装夹好即可。
另外,由于封头中心与回转台中心不同轴及封头高度差异造成封头边缘的径向跳动,使切割不稳定,为此,可采用与割嘴相连的导向滚轮,用弹簧压紧在封头壁进行切割。
2.6装配工艺
在焊接结构制造中,将组成结构的各个零件按照一定的位置、尺寸关系和精度要求组合起来的工序,称为装配。
装配在焊接结构制造工艺中占有很重要的地位,这不仅是由于装配工作的质量好坏直接影响着产品的最终质量,而且还因为装配工序的工作量大,约占整个产品制造的30%~40%。
因此,应正确的选用工装夹具定位并夹紧工件;选用适合的变位机调整焊件、焊机或焊工的位置,可提高装配工作的效率和质量,缩短产品制造工期、降低生产成本、