管材生产工艺.docx
《管材生产工艺.docx》由会员分享,可在线阅读,更多相关《管材生产工艺.docx(11页珍藏版)》请在冰豆网上搜索。
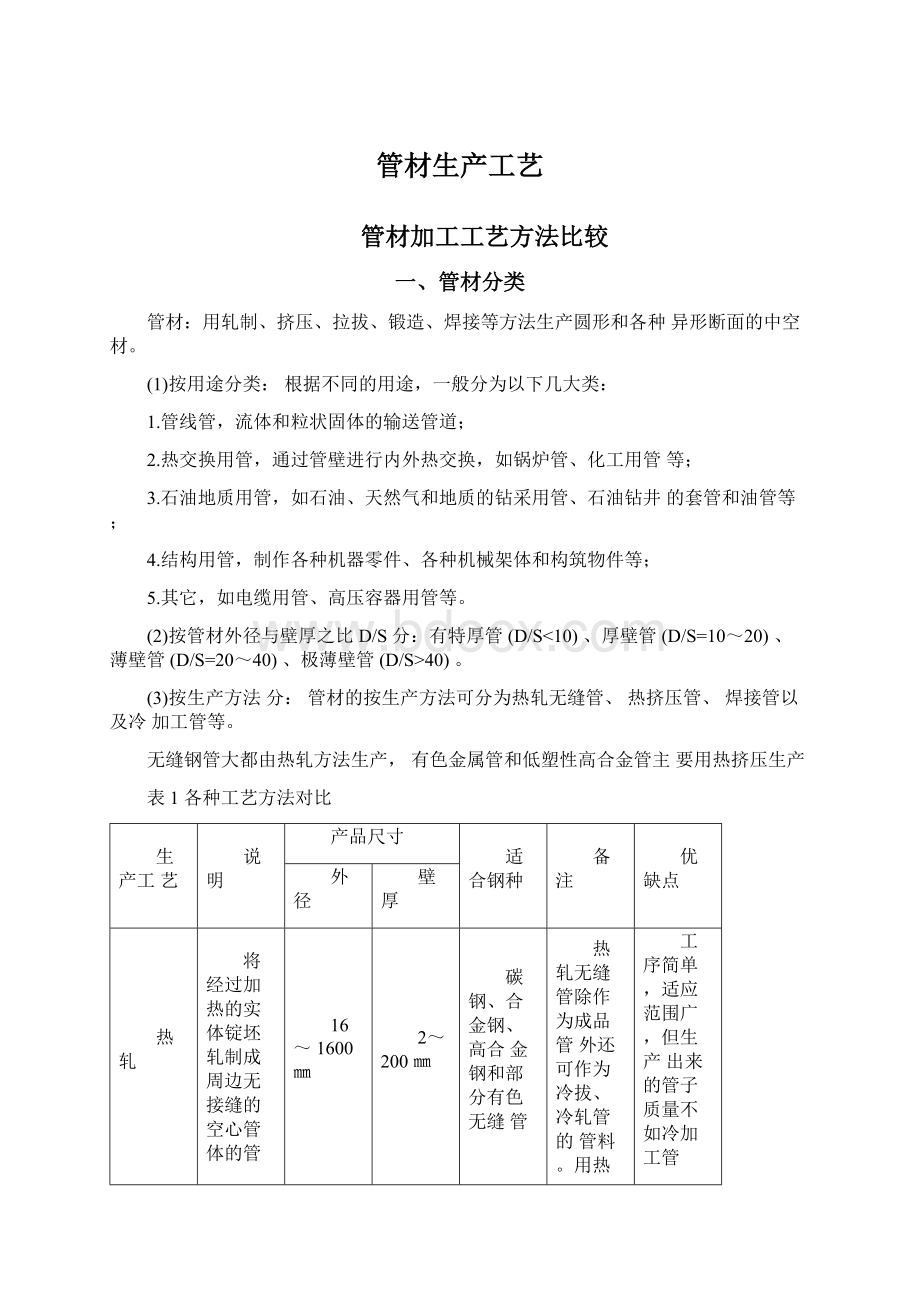
管材生产工艺
管材加工工艺方法比较
一、管材分类
管材:
用轧制、挤压、拉拔、锻造、焊接等方法生产圆形和各种异形断面的中空材。
(1)按用途分类:
根据不同的用途,一般分为以下几大类:
1.管线管,流体和粒状固体的输送管道;
2.热交换用管,通过管壁进行内外热交换,如锅炉管、化工用管等;
3.石油地质用管,如石油、天然气和地质的钻采用管、石油钻井的套管和油管等;
4.结构用管,制作各种机器零件、各种机械架体和构筑物件等;
5.其它,如电缆用管、高压容器用管等。
(2)按管材外径与壁厚之比D/S分:
有特厚管(D/S<10)、厚壁管(D/S=10~20)、薄壁管(D/S=20~40)、极薄壁管(D/S>40)。
(3)按生产方法分:
管材的按生产方法可分为热轧无缝管、热挤压管、焊接管以及冷加工管等。
无缝钢管大都由热轧方法生产,有色金属管和低塑性高合金管主要用热挤压生产
表1各种工艺方法对比
生产工艺
说明
产品尺寸
适合钢种
备注
优缺点
外径
壁厚
热轧
将经过加热的实体锭坯轧制成周边无接缝的空心管体的管材生产工艺
16~1600㎜
2~200㎜
碳钢、合金钢、高合金钢和部分有色无缝管
热轧无缝管除作为成品管外还可作为冷拔、冷轧管的管料。
用热轧法生产的无缝管占无缝管产量的80%~90%。
工序简单,适应范围广,但生产出来的管子质量不如冷加工管
热挤压
有色金属管和低塑性高合金管
冷拔或冷轧
在室温下用轧制和拉拔方式对管材进行的冷加工,属于热轧管(包括热挤压的管材)和焊接管的深度加工
冷拔法可生产直径0.2~765㎜和壁厚0.015~50㎜的各种管材,冷轧法可生产直径4~450㎜和壁厚0.03~
35㎜的各种管材。
适合于所有钢种,特别是不锈钢
可以得到尺寸精度高、表面粗糙度低、综合力学性能好的管材以及薄壁管材
工序多,生产周期长、金属消耗较大,生产效率较低,管子质量较高。
二、各种生产方法介绍
(一)热轧管
1.简介热轧无缝管是将经过加热的实体锭坯轧制成周边无接缝的空心管体的管材生产工艺。
用热轧方法可以生产碳钢、合金钢、高合金钢和部分有色无缝管,外径范围为16~1600㎜,壁厚为2~200㎜。
除圆断面管外还有各种异形断面管和变断面管。
热轧无缝管除作为成品管外还可作为冷拔、冷轧管的管料(见管材冷轧冷拔)。
用热轧法生产的无缝管占无缝管产量的80%~90%。
热轧无缝管的主要工序有管坯准备(包括切断和清理缺陷)、定心、管坯穿孔、毛管轧制、荒管精轧等。
石油地质管还要经过管端加工工序。
在管坯穿孔工序中,由于穿孔方法的不同,穿孔分斜穿孔(见二辊斜轧穿孔和三辊斜轧穿孔)、菌式穿孔机穿孔、压力穿孔和推轧穿孔等。
穿孔后的毛管按轧管方法的不同分自动轧管机轧管、管材斜轧延伸、周期式轧管机轧管、连续轧管机轧管和顶管。
荒管通过精轧得到各种热成品管。
精轧的方式包括管材均整、管材定径、管材减径和管材热扩径等。
如需要获得尺寸精度高、表面粗糙度低、综合力学性能好的管材以及薄壁管材,则必须采用冷加工方法生产,管材冷加工有冷轧、冷拔、冷减径和冷旋压等。
2.现代热轧管的工艺流程:
合格管坯测长称重穿孔延伸轧管定心(或没有)高压水除鳞穿孔延伸轧管
定径
{再加热高压水除鳞张力减径}冷却精整检查
成品入库
3.基本工序:
热轧管用的管坯有铸锭、连铸坯、轧坯、锻坯和空心铸坯。
热轧管的基本工序是:
⑴.在穿孔机上将锭或坯穿成空心厚壁毛管。
管坯穿孔的方法又分二辊斜轧穿孔、压力穿孔、推轧穿孔、三辊斜轧穿孔等。
⑵.在延伸机上将毛管轧薄,延伸成为接近成品管壁厚的荒管。
毛管延伸即毛管轧制的方法有:
自动轧管机轧管、连续轧管机轧管、三辊和二辊轧管机斜轧、周期式轧管机轧管、顶管机顶管。
⑶.荒管在精轧机上精轧成成品管。
荒管精轧包括以改善质量为目的的管材均整和管材定径以及以扩大产品规格为目的的管材减径和管材热扩径。
4.各种热轧管机组比较
表2各种热轧管机组比较
机组名称
特征
产品尺寸/㎜
适合钢种
备注
外径
壁厚
碳钢
低合金钢
含铬9%的钢
不锈钢
自动轧管机组
1.产品范围广;2.生产效率中等;3.可生产低合金和部分不锈钢管;4.产品尺寸精度不高;5.使用的原料为圆坯,采用推轧穿孔时用方坯。
25~660(斜轧穿孔)165~440(推轧穿孔)
2~60
5.5~40.5
大量生产
大量生产
可以生产
不易生产
生产小口径管设减径机;生产
大口径管设二次穿孔机以及扩径机
连续轧管机组
1.生产效率很高;2.管子内表面质量好;3.壁厚不均小;
4.自动化程度高;5.使用圆坯或方坯;6.为大量发展的机组。
34~168
(斜轧穿孔)
48~426
(推轧穿孔)
2~25
3~35
大量生产
大量生产
可以生产
很少生产
带限动芯棒的连续轧管机组得到了大量发展
三辊斜轧管机组
1.适合制造高精度管,生产效率低;2.内外表面质量好;
3.壁厚不均小;4.采用特朗斯瓦轧机可生产较薄管,多为生产厚壁管。
21~240
10(3)~50
大量生产
大量生产
可以生产
可以生产
多设纵轧减径机和斜轧定径机,采取毛管尾端预先减薄,可轧制D/S>30的薄壁管
二辊斜轧机组
1.适合生产高尺寸精度管;2.生产效率较低;3.管子内表面质量好;4.壁厚不均小;4.使用圆坯
34~219
8~30
大量生产
大量生产
可以生产
可以生产
有狄舍尔和改进型狄舍二辊轧机、拉力芯棒斜轧延伸机等
周期式轧管机组
1.适合制造大口径管;生产效率较低;2.能生产愤形管和长管;3.内表面质量较好;4.对管坯要求低,可使用钢锭直接轧成管
165~457
(700)
5.6~80
大量生产
大量生产
可以生产
很少生产
已少建设
顶管机组
1.一般用于制造中小直径管,有的国家用于制造大直径管;2.生产效率较高;3.新使用方坯或圆坯;4.机组使用圆坯(CPE机组)斜轧穿孔
17~219
210~1070
2.5~11
27~198
大量生产
大量生产
可以生产
很少生产
发展斜轧穿孔--延伸(CPE)机组
(二)热挤压(资料较少)空心锭正向挤压时,由于被挤压金属同穿孔针之间存在摩擦力,减少了内层金属的超前流动,金属流动比较均匀。
此外,锭坯中心为穿孔针占据,不会产生挤压缩尾。
在管材生产中,穿孔挤压仍存在较大的局限性,多适用于挤压管坯毛料和挤压熔点较低的合金管材,且只适用于短锭、高温、慢速挤压工艺。
(三)冷加工
1.简介在冷轧冷拔机组上在室温下用轧制和拉拔方式对管材进行的冷加工,属于热轧管(包括热挤压的管材)和焊接管的深度加工。
它可以获得直径更小、壁厚更薄、尺寸精度更高、表面粗糙度更低和恨不能更好以及多种断面形状的管材。
用冷拔法可生产直径0.2~765㎜和壁厚0.015~50㎜的各种管材,用冷轧法可生产直径4~450㎜和壁厚0.03~35㎜的各种管材。
2.基本工序
依据金属的加工性能、管材尺寸、质量要求以及投资和效益来选择不同的加工方法及相应的辅助工序,冷轧冷拔管的基本工序有:
⑴.管料供给,所用管料为热轧成品管或半成品管、挤压管以及焊接管;⑵.管料,包括检查、打捆、酸洗、清洗、冲洗、中和、烘干、涂润滑剂等;⑶.冷加工(冷轧或冷拔);4.成品精整包括成品热处理、矫直、取样、切头尾、检查(人工检查和各种探伤)、水压试验、涂油、包装、入库等。
不同的产品精整内容有所差异。
3.加工特点
冷加工的特点是管料从投入到加工成成品通常要经过多次冷并产生加工硬化,因而整个生产过程由多个准备工序和变形工序组成,且具有往复循环的特点,因而工序多,生产周期长、金属消耗较大,生产效率较低,一般生产规模均不大。
冷拔与冷轧相比较,冷轧的优点是道次变形量大,加工道次少,生产周期短和金属消耗小。
缺点是工具制造较多,变更规格不方便,生产灵活性差,设备投资高及维护较复杂;由于是周期轧制,轧制时间长,生产力较低,能耗高。
冷拔的优点是生产力较高,生产中变规格方便,灵活性大,设备和工具制造简单国;缺点是道次变形量小,加工道次多,生产周期长,金属消耗大。
4.管材冷拔的常规方法:
⑴.无芯棒拔管,用于只减小管子外径。
⑵.不动短芯棒拔管,适用于同时减小管子外径和壁厚;这种方法由于芯棒固定,且使用固定外模,摩擦阻力大,拔制力大,道次变形量小;优点是拔制方法简单,故被广泛应用。
⑶.浮动芯棒拔管,常用于卷筒拔管,能生产很长的管子(100m以上)。
浮动芯棒拔制时拔制力较小,可提高道次变形量;由于不存在拉杆的限制,可带芯棒拔制直径很小的管子。
⑷.长芯棒拔管,拔管时由于芯棒同管子一起运动,基本上消除了芯棒上的摩擦阻力,因而可降低拔制力和增加道次变形量;芯棒运动还可降低管子内表面粗糙度;长芯棒拔管的缺点是对芯棒要求严
格,且拔后要脱棒。
⑸.扩径拔管,管子壁厚减小,直径增大,管长有些缩短;扩径拔管时,管子固定不动而拉杆带动芯棒从管内通过。
以上是常规冷拔管的方法,为了克服它们的缺点,不断研究出以下一些拔管方法:
⑹.圆锥芯棒拔管,同一般短芯棒相比拉打力小。
⑺.半连续和连续拔管。
各种直线式拔管机都是间歇工作的,拔完一根管后需要等待小车返回才能拔下一根管,因此研究出半连续和连续式拔管。
(四)焊接管
1.简介
焊接管是将金属板带先冷弯成要求的形状和尺寸,再以适当的焊接方法焊合接缝而成。
焊接管主要用于流体输送,常经镀锌。
与无缝管相比,焊管的壁厚均匀性好,表面粗糙度小,同样的规格和钢种,焊管的价格便宜。
但焊管的焊缝及其热影响区的力学性能和其它物理性能比本体差,致使其使用范围受到一定限制,一般主要用作流输送管和结构管等。
随着焊接技术和焊缝热处理技术的提高以及采用焊管机后再加热和张力减径工艺,基本上消除了焊缝和热影响区性能差的缺点并可扩大机组产品规格,现在焊接管已经部分取代无缝管,用作锅炉管和油井管等。
焊管的焊缝有直焊缝和螺旋焊缝两大类。
2.焊管的主要工艺方法
焊管按生产方法分有炉焊管、连续成形电焊管、UOE电焊管、辊式弯板电焊管、螺旋成形电焊管等。
连续炉焊是将带坯在管坯连续加热炉中加热,使其边缘加热到焊接温度,然后出炉在辊式连连续成形机中成形、对接焊缝、压焊成管。
主要用于生产低碳钢和低合金钢。
连续电焊是将板带在正常情况下冷状态下先卷成要求形状和尺寸的管筒,然后选用合适的电热源将管筒边缘加热到焊接温度,对接焊缝,施压力焊接成管。
连续电焊的焊接方法有:
高频电焊、埋弧焊、惰性气体保护电弧焊(主要用于高合金钢和合金材料管)、直流电焊和方波电焊(主要用于小口径薄壁)、电子束焊和等离子焊(适用于高熔点材料)等。
非连续电焊主要用于大口径厚壁管生产。
板、带坯用一定方法冷弯成管筒后,先在线用自动电焊或高频电阻焊预焊管缝定位,切成定长,再送往下工序用埋弧焊焊接内外焊缝本焊。
一般一条预焊线
与多条本焊线组合,采取流水作业以保持高生产率。
焊管的主要生产方法和产品规格范围见表3。
表3焊管的主要生产方法和产品规格范围
类别
生产方法
基本工序
产品规格范围
成形
焊接
外径/㎜
壁厚/㎜
直缝焊管
连续炉焊机组
将带坯在管坯连续加热炉中加热,使其边缘加热
到焊接温度,然后出炉在辊式连连续成形机中成形、焊接
21.7~114.2
1.9~8.6
连续成形电焊机组
辊式连续成形机
高频电阻与感应焊惰性气体保护电弧焊
12.7~508
0.8~14.0
连续排辊成形机
高频电阻与感应焊、埋弧焊、惰性气体保护焊
400~1200
6.0~22.2
履带式连续菜机
高频电阻与感应焊、埋弧焊、惰性气体保护焊
20~150
0.5~3.5
UOE电焊机组
UO压力成形机
埋弧焊、惰性气体保护焊
400~1625
6.0~40.0
辊式弯板电焊机组
辊式弯板成形机
埋弧焊、惰性气体保护焊
300~4064
4.5~50.0
螺旋焊管
螺旋成形电焊机组
连续螺旋成形机
埋弧焊、惰性气体保护焊
300~3660
3.2~25.4
三、管材变径工艺方法简介
管材减径:
在多机架的减径机中对荒管进行的不带芯棒的连轧工序。
管材减径的目的在于减小管径、提高尺寸精度和扩大品种。
管材减径分热减径和冷减径两种,热减径分带张力减径和不带张力减径两种。
1.管材冷减径
室温下减小管材直径的工序,其变形过程与热减径类似。
冷减径的基本特点是变形时轧件横截面的稳定性好,不易出现轧折。
2.管材张力减径在多机架的减径机中对空心荒管进行的不带芯棒、带张力的热连轧工序,目的是获得既减径又减壁的成品管材。
因此,在热轧管机组后设置张力减径机,既可提高产品产量又可扩大产品规格范围。
张力减径的总壁厚变化量在-30%~+10%之间,这样完全可以用少数规格的管坯,通过张力减径机生产规格众多的管材。
3.管材无张力减径
在多机架的减径机中对空心荒管进行的不带芯棒、不带张力的连轧工序,目的是获得小直径的长管材,以扩大产品规格和提高机组生产能力。
无张力减径机和纵轧定径机(见管材定径)相同,但减径机的机架数目多达15~22架。
管材热扩径:
用斜轧法或拉拔法扩大管材直径的一种荒管轧制工序,用于大直径薄壁管的生产。
尽管大型周期式轧管机组与顶管机组可以生产一部分大直径管,但其设备庞大,一次性投资高,且生产大直径薄壁管有一定困难。
20世纪20年代末和30年代初,美国和德国研制出了辊式斜轧热扩管,德国又研制拉拔热扩管机,并都投入了工业生产。
斜轧热扩径在斜轧扩管机上进行。
其特点是一次变形量大、变形速度快、产量高,适于生产各种钢种的大直径和尺寸精度较高的中、薄壁厚无缝钢管;但机组设备庞大,投资高,且不能生产异形及变截面管。
拉拔热扩径在热拉扩管机上进行。
其特点是,扩管机既能热扩又能热拔,既能热扩圆管,也能拔异形及变截面管;拉拔扩管机设备重量轻,投资少,更换工具简便;但因拉拔扩管为自由变形,扩管产品的表面缺陷易暴露和扩大,壁厚精度和外径精度不高。