管道流量比值控制PLC系统设计.docx
《管道流量比值控制PLC系统设计.docx》由会员分享,可在线阅读,更多相关《管道流量比值控制PLC系统设计.docx(14页珍藏版)》请在冰豆网上搜索。
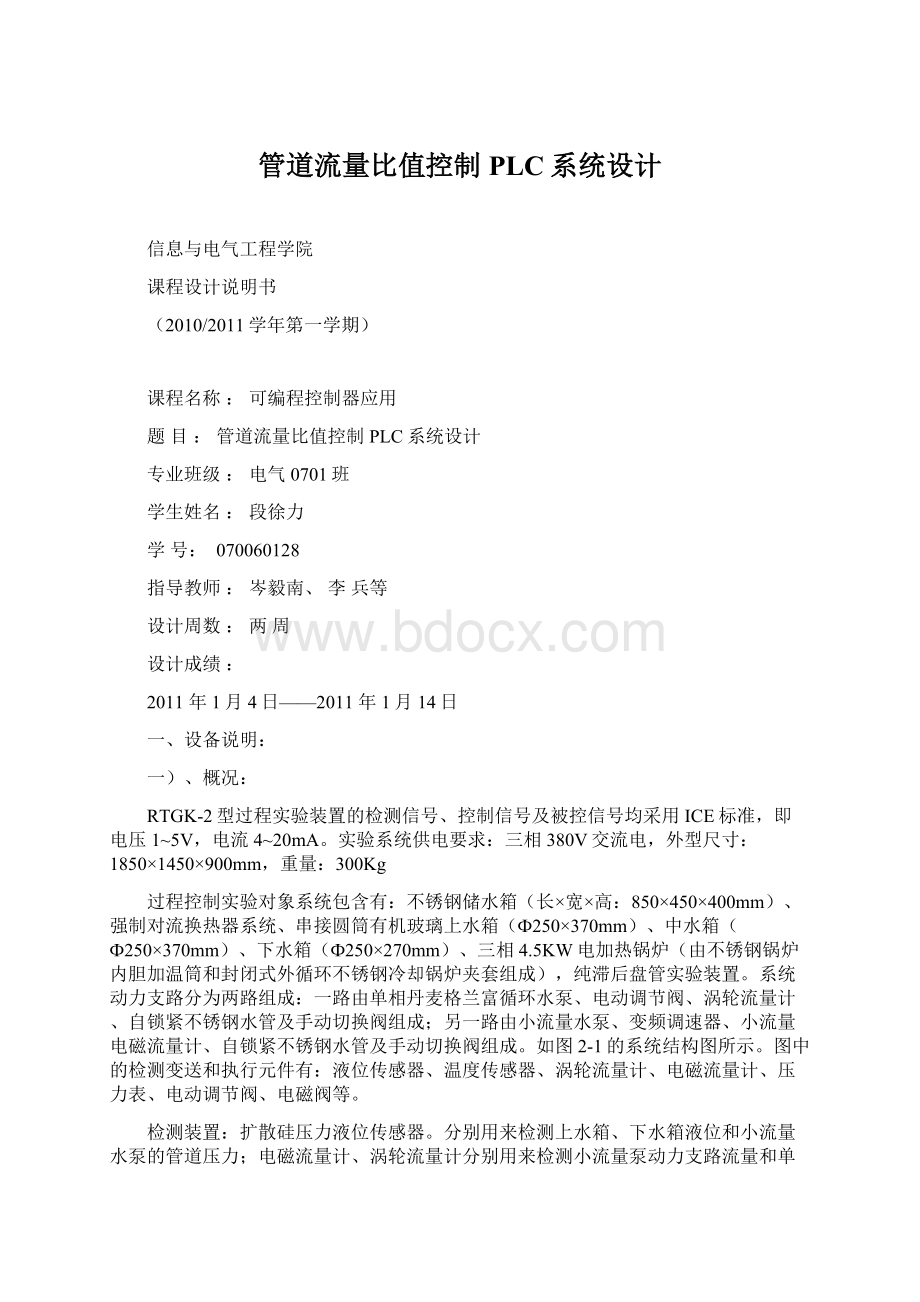
管道流量比值控制PLC系统设计
信息与电气工程学院
课程设计说明书
(2010/2011学年第一学期)
课程名称:
可编程控制器应用
题目:
管道流量比值控制PLC系统设计
专业班级:
电气0701班
学生姓名:
段徐力
学号:
070060128
指导教师:
岑毅南、李兵等
设计周数:
两周
设计成绩:
2011年1月4日——2011年1月14日
一、设备说明:
一)、概况:
RTGK-2型过程实验装置的检测信号、控制信号及被控信号均采用ICE标准,即电压1~5V,电流4~20mA。
实验系统供电要求:
三相380V交流电,外型尺寸:
1850×1450×900mm,重量:
300Kg
过程控制实验对象系统包含有:
不锈钢储水箱(长×宽×高:
850×450×400mm)、强制对流换热器系统、串接圆筒有机玻璃上水箱(Ф250×370mm)、中水箱(Ф250×370mm)、下水箱(Ф250×270mm)、三相4.5KW电加热锅炉(由不锈钢锅炉内胆加温筒和封闭式外循环不锈钢冷却锅炉夹套组成),纯滞后盘管实验装置。
系统动力支路分为两路组成:
一路由单相丹麦格兰富循环水泵、电动调节阀、涡轮流量计、自锁紧不锈钢水管及手动切换阀组成;另一路由小流量水泵、变频调速器、小流量电磁流量计、自锁紧不锈钢水管及手动切换阀组成。
如图2-1的系统结构图所示。
图中的检测变送和执行元件有:
液位传感器、温度传感器、涡轮流量计、电磁流量计、压力表、电动调节阀、电磁阀等。
检测装置:
扩散硅压力液位传感器。
分别用来检测上水箱、下水箱液位和小流量水泵的管道压力;电磁流量计、涡轮流量计分别用来检测小流量泵动力支路流量和单相格兰富水泵动力支路流量;Pt100热电阻温度传感器分别用来检测锅炉内胆、锅炉夹套和对流换热器冷水出口、热水出口、纯滞后盘管出口水温。
执行装置:
三相可控硅移相调压装置用来调节三相电加热管的工作电压;电动调节阀调节管道出水量;变频器调节小流量泵。
二)、涉及的设备单元部件:
1)、涡轮流量计:
输出信号:
频率,测量范围:
0~0.6m3/h
接线如图所示:
接线说明:
传感器的供电电源由24VDC开关电源提供,负载为流量积算变送仪。
注:
使用涡轮流量计时,必须将24VDC开关电源打开。
2)、电磁流量计:
输出信号:
4~20mA,测量范围:
0~0.4m3/h
接线说明:
转换器为交流220V供电,X、Y和A、B、C为传感器和转换器之间的连线,输出信号线直接接控制台上的电磁流量计信号输出端。
3)、电磁阀:
24V直流开关电源供电,电磁阀共两种状态:
上电时电磁阀阀门开,掉电时阀门关。
4)、变频器面板:
如图所示,变频器型号为三菱FR-S520S-0.4K型变频调速器,具体参数设置如下表:
名称
表示
设定范围
设定值
上限频率
P1
0-120Hz
60Hz
下限频率
P2
0-120Hz
20Hz
扩张功能显示选择
P30
0,1
1
频率设定电流增益
P39
1-120Hz
60Hz
RH端子功能选择
P62
4
操作模式选择
P79
0-8
0
C5
C5
输出频率大小
25Hz
C6
C6
偏置
20%
A面板接线端子功能说明:
为了保护变频器各接线端子不因实验时经常装拆线而损坏或丢失,故将其常用的端子引到面板上。
(1)控制信号输入:
可输入外部0~5V电压,
或4~20mA电流控制信号。
(2)STF、STR:
电机的正、反转控制端,SD与STF相连为正转,SD与STR相连时为反转。
B变频器使用说明:
本装置中使用变频器时,主要有两种输出方式:
一种是直接调面板旋钮输出频率,另一种是用外部
输入控制信号改变变频器输出频率。
两种输出方式具体接线方法如下:
(1)变频器面板旋钮输出接线方法:
SD与STF(或STR)短接,当需要改变输出频率时,旋动面板上的旋钮,顺时针旋可增大输出频率,逆时针旋可减小输出频率。
待旋至所需要的频率时,按变频器上白色的SET键,即可选定所需的输出频率。
(2)变频器外部控制信号控制输出接线方法:
SD与STF(或STR)、RH两端都短接,在控制信号输入端接入控制信号(正极、负极应对应,不能接错),打开变频器的电源开关即可输出。
通过改变控制信号的大小来改变输出频率。
三)、PLC工作原理:
PLC是采用“顺序扫描,不断循环”的方式进行工作的。
即在PLC运行时,CPU根据用户按控制要求编制好并存于用户存储器中的程序,按指令步序号(或地址号)作周期性循环扫描,如无跳转指令,则从第一条指令开始逐条顺序执行用户程序,直至程序结束。
然后重新返回第一条指令,开始下一轮新的扫描。
在每次扫描过程中,还要完成对输入信号的采样和对输出状态的刷新等工作。
PLC扫描一个周期必经输入采样、程序执行和输出刷新三个阶段。
PLC在输入采样阶段:
首先以扫描方式按顺序将所有暂存在输入锁存器中的输入端子的通断状态或输入数据读入,并将其写入各对应的输入状态寄存器中,即刷新输入。
随即关闭输入端口,进入程序执行阶段。
PLC在程序执行阶段:
按用户程序指令存放的先后顺序扫描执行每条指令,经相应的运算和处理后,其结果再写入输出状态寄存器中,输出状态寄存器中所有的内容随着程序的执行而改变。
输出刷新阶段:
当所有指令执行完毕,输出状态寄存器的通断状态在输出刷新阶段送至输出锁存器中,并通过一定的方式(继电器、晶体管或晶闸管)输出,驱动相应输出设备工作。
四)、电磁和涡轮流量计流量比值控制说明:
1)、比值系统组成原理:
在各种生产过程中,需要使两种物料的流量保持严格的比例关系是常见的,例如,在锅炉的燃烧系统中,要保持燃料和空气量的一定比例,以保证燃烧的经济性。
而且往往其中一个流量随外界负荷需要而变,另一个流量则应由调节器控制,使之成比例地改变,保证二者之比值不变。
否则,如果比例严重失调,就可能造成生产事故,或发生危险。
又如,以重油为原料生产合成氨时,在造气工段应该保持一定的氧气和重油比率,在合成工段则应保持氢和氮的比值一定。
这些比值调节的目的是使生产能在最佳的工况下进行。
本实验比值调节系统的组成原理如下图所示:
图8-1、比值控制系统原理图
2)、原理:
对于节流元件来说,压差与流量的平方成正比,即
ΔP∝Q2
对于图13-1单闭环比值调节系统,A,B两个管路上的ΔP可分别写为
ΔPA=KAQA2
ΔPB=KBQB2
其中,KA、KB为放大系数。
变送器送出的信号为4-20mA电流信号,那么F1,FA有如下关系:
F1-4=CAΔPA
FA-4=CBΔPB
式中CA、CB是变送器的放大系数,F1,FA是变送器的输出信号电流。
比值器的输出关系为:
F2-4=KC(F1-4)
KC为比值器的放大系数。
则有:
F2-4=KCCAKAQA2
FA-4=CBKBQB2
由于调节器为比例积分调节,在稳态下它可保持FA=F2,故有
KCCAKAQA2=CBKBQB2
即(QA/QB)2=KCCBKB/CAKA
从上式可知,为使流量QA、QB的比值满足工艺要求,只要适当地调整比值器的放大系数KC即可。
3)、pid控制算法说明:
S7-200能够进行PID控制。
S7-200CPU最多可以支持8个PID控制回路(8个PID指令功能块)。
PID是闭环控制系统的比例-积分-微分控制算法。
PID控制器根据设定值(给定)与被控对象的实际值(反馈)的差值,按照PID算法计算出控制器的输出量,控制执行机构去影响被控对象的变化。
PID控制是负反馈闭环控制,能够抑制系统闭环内的各种因素所引起的扰动,使反馈跟随给定变化。
根据具体项目的控制要求,在实际应用中有可能用到其中的一部分,比如常用的是PI(比例-积分)控制,这时没有微分控制部分。
4)、PID算法在S7-200中的实现:
PID控制最初在模拟量控制系统中实现,随着离散控制理论的发展,PID也在计算机化控制系统中实现。
为便于实现,S7-200中的PID控制采用了迭代算法。
详细的计算方法请参考《S7-200系统手册》中PID指令部分的相关内容。
计算机化的PID控制算法有几个关键的参数Kc(Gain,增益),Ti(积分时间常数),Td(微分时间常数),Ts(采样时间)。
在S7-200中PID功能是通过PID指令功能块实现。
通过定时(按照采样时间)执行PID功能块,按照PID运算规律,根据当时的给定、反馈、比例-积分-微分数据,计算出控制量。
PID功能块通过一个PID回路表交换数据,这个表是在V数据存储区中的开辟,长度为36字节。
因此每个PID功能块在调用时需要指定两个要素:
PID控制回路号,以及控制回路表的起始地址(以VB表示)。
由于PID可以控制温度、压力等等许多对象,它们各自都是由工程量表示,因此有一种通用的数据表示方法才能被PID功能块识别。
S7-200中的PID功能使用占调节范围的百分比的方法抽象地表示被控对象的数值大小。
在实际工程中,这个调节范围往往被认为与被控对象(反馈)的测量范围(量程)一致。
PID功能块只接受0.0-1.0之间的实数(实际上就是百分比)作为反馈、给定与控制输出的有效数值,如果是直接使用PID功能块编程,必须保证数据在这个范围之内,否则会出错。
其他如增益、采样时间、积分时间、微分时间都是实数。
因此,必须把外围实际的物理量与PID功能块需要的(或者输出的)数据之间进行转换。
这就是所谓输入/输出的转换与标准化处理。
《S7-200系统手册》上有详细的介绍。
S7-200的编程软件Micro/WIN提供了PID指令向导,以方便地完成这些转换/标准化处理。
除此之外,PID指令也同时会被自动调用。
5)、调试PID控制器:
PID控制的效果就是看反馈(也就是控制对象)是否跟随设定值(给定),是否响应快速、稳定,是否能够抑制闭环中的各种扰动而回复稳定。
要衡量PID参数是否合适,必须能够连续观察反馈对于给定变化的响应曲线;而实际上PID的参数也是通过观察反馈波形而调试的。
因此,没有能够观察反馈的连续变化波形曲线的有效手段,就谈不上调试PID参数。
观察反馈量的连续波形,可以使用带慢扫描记忆功能的示波器(如数字示波器),波形记录仪,或者在PC机上做的趋势曲线监控画面等。
新版编程软件STEP7-Micro/WINV4.0内置了一个PID调试控制面板工具,具有图形化的给定、反馈、调节器输出波形显示,可以用于手动调试PID参数。
对于没有“自整定PID”功能的老版CPU,也能实现PID手动调节。
PID参数的取值,以及它们之间的配合,对PID控制是否稳定具有重要的意义。
这些主要参数是:
•采样时间:
计算机必须按照一定的时间间隔对反馈进行采样,才能进行PID控制的计算。
采样时间就是对反馈进行采样的间隔。
短于采样时间间隔的信号变化是不能测量到的。
过短的采样时间没有必要,过长的采样间隔显然不能满足扰动变化比较快、或者速度响应要求高的场合。
编程时指定的PID控制器采样时间必须与实际的采样时间一致。
S7-200中PID的采样时间精度用定时中断来保证。
•增益:
(Gain,放大系数,比例常数)增益与偏差(给定与反馈的差值)的乘积作为控制器输出中的比例部分。
过大的增益会造成反馈的振荡。
•积分时间(IntegralTime)偏差值恒定时,积分时间决定了控制器输出的变化速率。
积分时间越短,偏差得到的修正越快。
过短的积分时间有可能造成不稳定。
积分时间的长度相当于在阶跃给定下,增益为“1”的时候,输出的变化量与偏差值相等所需要的时间,也就是输出变化到二倍于初始阶跃偏差的时间。
如果将积分时间设为最大值,则相当于没有积分作用。
•微分时间:
(DerivativeTime)偏差值发生改变时,微分作用将增加一个尖峰到输出中,随着时间流逝减小。
微分时间越长,输出的变化越大。
微分使控制对扰动的敏感度增加,也就是偏差的变化率越大,微分控制作用越强。
微分相当于对反馈变化趋势的预测性调整。
如果将微分时间设置为0就不起作用,控制器将作为PI调节器工作。
6)、PID算法:
在稳定状态操作中,PID控制器管理输出数值,以便将错误(e)驱动为零。
错误测量由设定值(所需的操作点)和进程变量(实际操作点)之间的差别决定。
PID控制原则基于以下公式,其中将输出M(t)表示为比例项、积分项和微分项的函数:
其中:
M(t):
作为时间函数的回路输出
Td:
回路增益
E:
回路错误(设定值和进程变量之间的差别)
Minitial:
回路输出的初始值
为了在数字计算机中运行该控制函数,必须将连续函数量化为错误值的定期样本,并随后计算输出。
数字计算机运算以下列相应的公式为基础:
其中:
Mn:
采样时间n的回路输出计算值
Kc:
回路增益
En:
采样时间n的回路错误值
En-1:
回路错误的前一个数值(在采样时间n?
1)
Ki:
积分项的比例常数
Minitial:
微分项的比例常数
Kd:
微分项的比例常数
在该公式中,积分项被显示为全部错误项的函数,从第一个样本至当前样本。
微分项是当前样本和前一个样本的函数,而比例项仅是当前样本的函数。
在数字计算机中,既不可能也没有必要存储所有的错误项样本。
因为从第一个样本开始,每次对错误采样时数字计算机都必须计算输出值,因此仅需存储前一个错误值和前一个积分项数值。
由于数字计算机计算结果的重复性,可在任何采样时间对公式进行简化。
简化后的公式为:
其中:
MX:
积分项的前一个数值(采样时间n?
1)
计算回路输出值时,CPU使用对上述简化公式的修改格式。
修改后的公式为:
其中:
Mn:
采样时间n的回路输出计算值
MPn:
采样时间n的回路输出比例项数值
Min:
采样时间n的回路输出积分项数值
MDn:
采样时间n的回路输出微分项数值
比例项
比例项MP是增益和错误(e)的乘积,其中增益控制输出计算的敏感度,错误是在某一特定采样时间设定值(SP)和进程变量(PV)之间的差别。
CPU采用的计算比例项的公式为:
其中:
MPn:
采样时间n的回路输出比例项数值
Kc:
回路增益
SPn:
采样时间n的设定值数值
SPv:
采样时间n的进程变量数值
积分项
积分项MI在时间上与错误(e)和成比例。
CPU采用的积分项公式为:
其中:
MNi:
采样时间n的回路输出积分项数值
Kc:
回路增益
Ts:
回路采样时间
Ti:
积分时间(亦称为积分时间或复原)
SPn:
采样时间n的设定值数值
PVn:
采样时间n的进程变量数值
MX:
采样时间n-1的积分项数值(亦称为积分和或偏差)
积分和或偏差(MX)是积分项所有先前数值的运行和。
每次计算后,根据的数值更新偏差,该数值可能被调节或截取(详情请参阅"
变量和范围"一节)。
偏差的初始值通常被设为第一次回路输出计算之前的输出值。
其他几个常数也是积分项的一部分,例如增益、采样时间(即PID回路重新计算输出值的循环时间)以及积分时间或复原(即用于控制积分项对输出计算影响的时间)。
微分项
微分项MD与错误变化成比例。
计算微分项的公式为:
为了避免步骤改变或由于对设定值变化求导带来的输出变化,对该公式进行修改,假定设定值为常数=。
如下所示,会导致计算进程变量的变化,而不计算错误的变化:
或:
其中:
MDn:
采样时间n的回路输出微分项数值
Kc:
回路增益
Ts:
回路采样时间
Td:
回路微分阶段(亦称为微分时间或速率)
SPn:
采样时间n的设定值数值
SPn-1:
采样时间n-1的设定值数值
PVn:
采样时间n-1的进程变量数值
PVn-1:
采样时间n-1的进程变量数值
必须保存进程变量,而不必保存错误,用于下一次微分项计算。
第一次采样时,数值被初始化,等于。
回路控制选项在很多控制系统中,可能有必要仅采用一种或两种回路控制方法。
例如,可能只要求比例控制或比例和积分控制。
通过设置常数参数值对所需的回路控制类型进行选择。
如果您不需要积分运算(即在PID计算中无"I"),则应将积分时间(复原)指定为"INF"(无限大)。
由于积分和MX的初始值,即使没有积分运算,积分项的数值也可能不为零。
如果您不需要求导数运算(即在PID计算中无"D"),则应将求微分时间(速率)指定为0.0。
如果您不需要比例运算(即在PID计算中无"P"),并且您需要I或ID控制,则应将增益值指定为0.0。
因为回路增益是计算积分和微分项公式中的系数,将回路增益设为0.0会导致在积分和微分项计算中使用的回路增益值为1.0。
从您在PID指令框中输入的表格(TBL)起始地址为回路表分配八十(80)个字节。
S7-200的PID指令引用一个包含回路参数的回路表。
此表起初的长度为36个字节。
在增加了PID自动调谐后,回路表现已扩展到80个字节。
如果使用PID调谐控制面板,与PID回路表的全部相互作用将由此控制面板代您完成。
如果需要由操作员板提供自动调谐能力,您的程序必须提供操作员和PID回路表之间的相互作用,以发起和监视此自动调谐进程,以及随后套用建议的调谐数值。
7)、回路表:
偏移量域格式类型说明
0进程变量双字.实数入包含进程变量,必须在0.0至1.0范围内。
4设定值双字.实数入包含设定值,必须在0.0至1.0范围内。
8输出双字.实数入/出包含计算输出,在0.0至1.0范围内。
12增益双字.实数入包含增益,此为比例常数,可为正数或负数。
16采样时间双字.实数入包含采样时间,以秒为单位,必须为正数。
20积分时间双字.实数入包含积分时间,以分钟为单位,必须为正数。
24微分时间双字.实数入包含微分时间,以分钟为单位,必须为正数。
28偏差双字.实数入/出包含0.0和1.0之间的偏差或积分和数值。
32以前的进程变量双字.实数入/出包含最后一次执行PID指令存储的进程变量以前的数值。
8)、Plc程序:
五)、设计总结或结论:
这是这学期最后的课设,也是大学阶段课设的结点,所以我们组员加倍珍惜这次也是最后一次课设机会,运用进实验室时间,对所要涉及的题目认真了解学习,对硬件系统结构学习,对系统所涉及到的检测元件了解,对操作台注意事项进行学习,对所运用的plc扩展模块了解,通过借阅图书对所涉及内容细节进行了解。
在设计过程中,结合硬件实验,对过程中所出现的问题认真分析,对程序中不妥之处进行改进,通过硬软联合试验,使得对plc的pid控制有进一步了解。
在设计之初我们对所要实现的控制方法在软件中一向导方式建立pid控制,实现控制策略。
并且对向导设置有一定的了解,而且对设计思路想法有进一步的确信,是对思考方法的一种快速验证方法,在设计中同样遇见了不少的问题,如s7-200扩展模块em235模拟量输入输出的设置,其采集范围应与传感器采集输出范围相配合。
按比例控制副管流量,确保主管流量乘以比例倍数作为副管给定不超过副管流量最大值(以传感器量程范围考虑)。
再者就是回路表中注意过程量、给定量、输出量都在标准化实数范围0~1之间,注意采集数据,和输出控制数据的正确转换。
设计的还不是很完善,还需要再进一步修改调整,对系统抗扰还需进一步考虑,系统的可靠性还需进一步考虑。
最后,感谢同组组员的不懈努力思考与团队配合,感谢指导老师的认真指导与实验硬件的提供。
六)、考文献:
[1]殷洪义.可编程控制器选择设计与维护.北京:
机械工业出版社,1994
[2]张万忠.可编程控制器应用技术.北京:
化学工业出版社,2001.12
[3]曾庆波、孙华、周卫宏.监控组态软件及其应用技术.哈尔滨:
哈尔滨工业大学出版社.2005
七)、
课程设计
评语
课程设计
成绩
指导教师
(签字)
年月日