T6145镗床主轴套筒的加工工艺规程及铣齿夹具设计.docx
《T6145镗床主轴套筒的加工工艺规程及铣齿夹具设计.docx》由会员分享,可在线阅读,更多相关《T6145镗床主轴套筒的加工工艺规程及铣齿夹具设计.docx(60页珍藏版)》请在冰豆网上搜索。
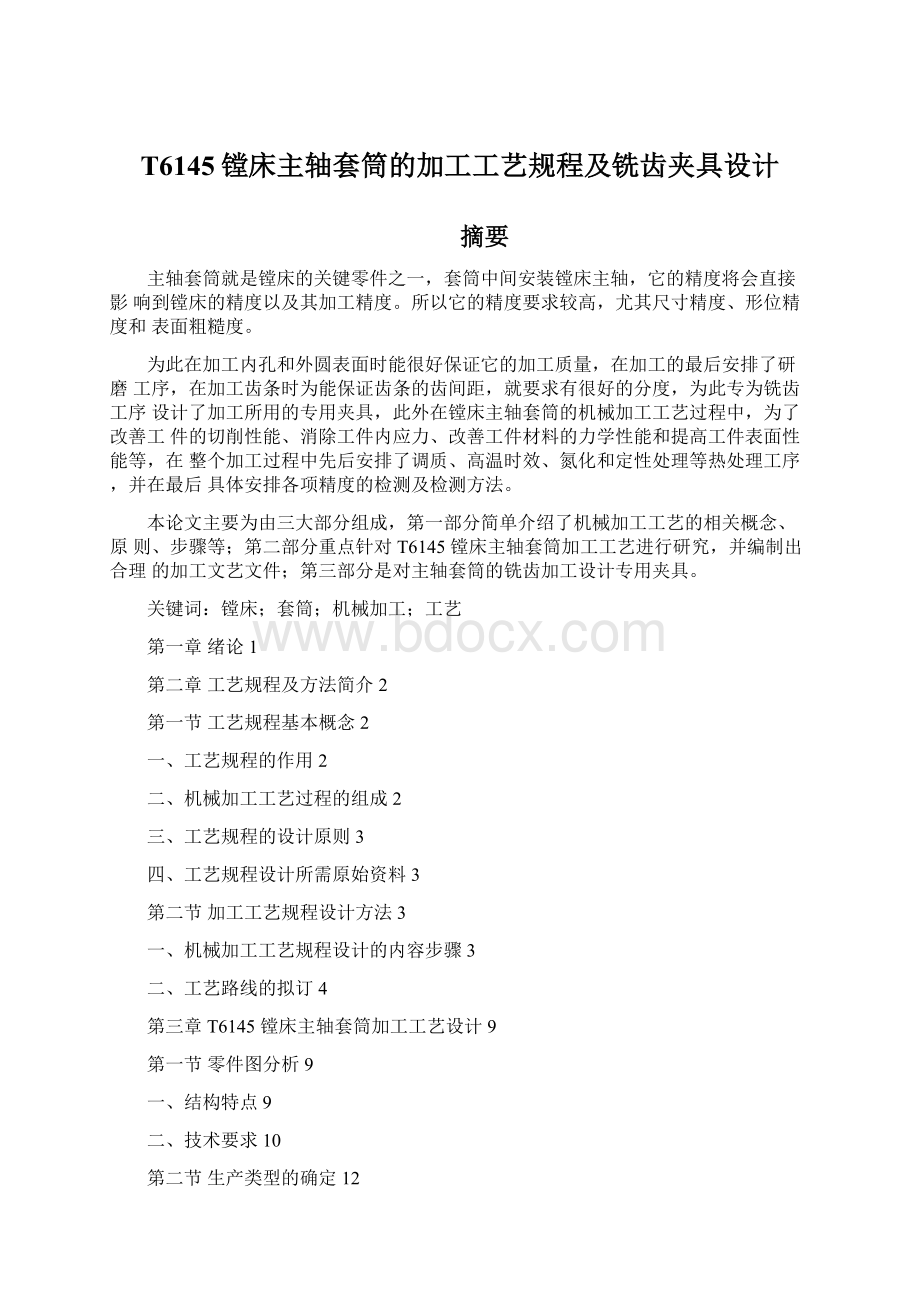
T6145镗床主轴套筒的加工工艺规程及铣齿夹具设计
摘要
主轴套筒就是镗床的关键零件之一,套筒中间安装镗床主轴,它的精度将会直接影响到镗床的精度以及其加工精度。
所以它的精度要求较高,尤其尺寸精度、形位精度和表面粗糙度。
为此在加工内孔和外圆表面时能很好保证它的加工质量,在加工的最后安排了研磨工序,在加工齿条时为能保证齿条的齿间距,就要求有很好的分度,为此专为铣齿工序设计了加工所用的专用夹具,此外在镗床主轴套筒的机械加工工艺过程中,为了改善工件的切削性能、消除工件内应力、改善工件材料的力学性能和提高工件表面性能等,在整个加工过程中先后安排了调质、高温时效、氮化和定性处理等热处理工序,并在最后具体安排各项精度的检测及检测方法。
本论文主要为由三大部分组成,第一部分简单介绍了机械加工工艺的相关概念、原则、步骤等;第二部分重点针对T6145镗床主轴套筒加工工艺进行研究,并编制出合理的加工文艺文件;第三部分是对主轴套筒的铣齿加工设计专用夹具。
关键词:
镗床;套筒;机械加工;工艺
第一章绪论1
第二章工艺规程及方法简介2
第一节工艺规程基本概念2
一、工艺规程的作用2
二、机械加工工艺过程的组成2
三、工艺规程的设计原则3
四、工艺规程设计所需原始资料3
第二节加工工艺规程设计方法3
一、机械加工工艺规程设计的内容步骤3
二、工艺路线的拟订4
第三章T6145镗床主轴套筒加工工艺设计9
第一节零件图分析9
一、结构特点9
二、技术要求10
第二节生产类型的确定12
第三节毛坯的选择13
第四节选择定位基准13
一、选择精基准和确定夹紧方案13
二、选择粗基准和确定夹紧方案15
第五节拟定套筒的工艺路线15
一、加工阶段的划分15
二、确定各表面的加工方法15
三、加工顺序安排19
四、热处理工序及表面处理工序的安排19
五、其他工序的安排21
六、工序过程安排21
七、确定套筒程工序加工余量及工序尺寸22
第六节机床设备和工艺装备的选择。
24
一、机床设备的选择24
二、刀具的选择26
三、夹具的选择27
第七节切削用量的选择28
一、切削用量的选择原则28
二、确定各工序的切削用量29
第八节精度检验35
第四章夹具设计37
第一节概述37
三、夹具的基本要求38
四、夹具设计的步骤38
第二节套筒铣齿夹具设计过程39
一、分析T6145镗床主轴套筒零件图39
二、夹具结构设计39
三、主要零件设计的说明43
四、使用说明43
第五章T6015镗床主轴套筒机械加工工艺规程卡45
结论69
致谢70
参考文献71
绪论
镗床是主要用镗刀对工件已有的孔进行镗削的机床,使用不同的刀具和附件还可进行钻削、铣削、切削,它的加工精度和表面质量要高于钻床。
镗床是大型箱体零件加工的主要设备,螺纹及加工外圆和端面等。
由于制造武器的需要,在15世纪就已经出现了水力驱动的炮筒镗床。
1769年J.瓦特取得实用蒸汽机专利后,汽缸的加工精度就成了蒸汽机的关键问题。
1774年英国人J.威尔金森发明炮筒镗床,次年用于为瓦特蒸汽机加工汽缸体。
1776年他又制造了一台较为精确的汽缸镗床。
1880年前后,在德国开始生产带前后立柱和工作台的卧式镗床。
为适应特大、特重工件的加工,20世纪30年代发展了落地镗床。
随着铣削工作量的增加,50年代出现了落地式镗铣床。
20世纪初,由于钟表仪器制造业的发展,需要加工孔距误差较小的设备,在瑞士出现了坐标镗床。
为了提高镗床的定位精度,已广泛采用光学读数头或数字显示装置。
有些镗床还采用数字控制系统实现坐标定位和加工过程自动化。
镗床分为卧式镗床、落地式镗铣床、金刚镗床和坐标镗床等类型。
①卧式镗床:
应用最多、性能最广的一种镗床,适用于单件小批生产和修理车间。
②落地镗床和落地镗铣床:
特点是工件固定在落地平台上,适宜于加工尺寸和重量较大的工件,用于重型机械制造厂。
③金刚镗床:
使用金刚石或硬质合金刀具,以很小的进给量和很高的切削速度镗削精度较高、表面粗糙度较小的孔,主要用于大批量生产中。
④坐标镗床:
具有精密的坐标定位装置,适于加工形状、尺寸和孔距精度要求都很高的孔,还可用以进行划线、坐标测量和刻度等工作,用于工具车间和中小批量生产中。
其他类型的镗床还有立式转塔镗铣床、深孔镗床和汽车、拖拉机修理用镗床等。
主轴套筒是镗床的关键零件之一,该零件质量直接影响机床的精度和镗床对工件的加工质量和精度,尤其尺寸精度、形位精度、表面粗糙度等的要求都较高,两端内孔表面的圆柱度公差、径向圆跳动公差≤0.02mm之内;镗床主轴套筒的主要表面粗糙度Ra数值是0.04和0.02,总之该零件是精密套筒,此外镗床主轴套筒属于长型薄壁套筒零件,其最薄处仅有4.5mm,零件的全长为476mm。
从零件的实际情况出发,安排好合理正确的加工方法,编制出正确可行的机械加工工艺文件是此次设计的主要任务。
工艺规程及方法简介
一台相同结构相同要求的机器或一个相同要求的机器零件,可以采用几种不同的工艺过程完成,但其中总有一种工艺过程在某一具体条件下是最合理的,人们把合理的工艺过程有关内容写在工艺文件中,用以指导生产,这些工艺文件就是工艺规程。
工艺规程是在总结工作及工程技术人员实践经验基础上,依据科学理论和必要的工艺试验制订的。
经审定批准的工艺规程是指导生产的工艺文件,企业有关人员须严格执行,不得有各行其是。
当然,工艺规程也不是一成不变的,随着科学技术的发展,一定会有新的更为合理的工艺规程代替旧的相对不合理的工艺规程。
但是,工艺规程的修订必须经过充分的试验认证,并须严格履行呈报审批手续。
第一节工艺规程基本概念
一、工艺规程的作用
1.工艺规程是工厂进行生产准备工作的主要依据产品在投入生产之前要作大量的生产准备工作,包括材料和毛坯的供应,机床的配
备和调理中,专用工艺装备的设计制造,核算生产成本以及配备人员等,所有这些工作都要根据工艺规程进行。
2.工艺规程是企业组织生产的指导性文件工厂管理人员根据工艺规程规定的要求,编制生产作业计划,组织工人进行生产,
并按照工艺规程要求验收产品。
3.工艺规程是新建和扩建机械制造厂(或车间)的重要文件新建和扩建机械制造厂(或车间)须根据工艺规程确定机床和其他辅助设备的种类、
型号规格和数量,厂房面积,设备布置,生产工人的工种、等级及数量等。
此外,先进的工艺规程还起着交流和推广先进制造技术的作用。
典型工艺规程可能
缩短工厂摸索和试制的过程。
二、机械加工工艺过程的组成
1.工艺过程:
改变生产对象的形状、尺寸、相对位置和性质等,使其成为成品或半成品的过程。
工艺过程又可分为铸造、锻造、冲压、焊接、机械加工、热处理、装配等工艺过程。
2.机械加工工艺过程:
用机械加工方法,改变毛坯形状、尺寸和表面质量,使其成为零件的过程。
零件的机械加工工艺过程由许多工序组合而成,每个工序又可分为若干个安装、工位、工步和走刀。
3.工序:
一个或一组工人,在一个工作地对同一个或同时对几个工件所连续完成的那一部分工艺过程。
4.安装:
工件经一次装夹(定位和夹紧)后所完成的那一部分工序。
5.工位:
为了完成一定的工序部分,一次装夹工件后,工件与夹具或设备的可动部分一起,相对刀具或设备的固定部分所占据的每一个位置。
6.工步:
当加工表面、加工刀具和切削用量中的转速和进给量均保持不变的情况下完成的那一部分工序。
三、工艺规程的设计原则
工艺规程设计必须遵循以下原则:
1.所设计的工艺规程必须保证机器零件的加工质量和机器的装配质量,达到设计图样上规定的各项技术要求;
2.工艺过程应具有较高的生产效率,使产品能尽快投放市场;
3.尽量降低制造成本;
4.注意减轻工人的劳动强度,保证生产安全。
四、工艺规程设计所需原始资料设计工艺规程必须具备以下原始资料:
1.产品装配图;
2.产品验收质量标准;
3.产品的年生产纲领;
4.毛坯材料与毛坯生产条件;
5.制造厂的生产条件,包括机床设备和工艺装备的规格、性能和当前的技术状态,工人的技术水平,工厂自制工艺装备的能力以及工厂供电、供气的能力等有关资料;
6.工艺规程设计所用设计手册和有关标准;
7.国内外有关制造技术资料等。
第二节加工工艺规程设计方法一、机械加工工艺规程设计的内容步骤
1.分析零件图和产品装配图设计工艺规程时,首先应分析零件图和该零件所在部件或总成的装配图,了解该零
件在部件或总成中的位置和功用以及部件或总成对该零件提出的技术要求,分析其主要技术关键和应相应采取的工艺措施,形成工艺规程设计总体构思。
2.对零件图和装配图进行工艺审查审查图样上的视图、尺寸公差和技术要求是否正确、统一、完整,对零件设计的结
构工艺性进行评价,如发现有不合理之处应及时提出,并同有关设计人员商讨图样修改方案,报主管领导审批。
3.由产品的年生产纲领研究确定零件生产类型
4.确定毛坯提高毛坯制造质量,可以减少机械加工劳动量,降低机械加工成本,但同时可能会
增加毛坯的制造技术成本,得根据生产类型和毛坯制造的生产条件综合考虑。
应当指出,我国机械制造工厂的材料利用率较低,只要有可能,应提出采用精密铸造、精密锻造、冷轧、冷挤压、粉末冶金等先进制造方法来制造毛坯。
材料利用系数是衡量工艺规程是否合理的一个重要参数。
5.拟订工艺路线其主要内容包括:
选择定位基准,确定各表面加工方法,划分加工阶段,确定工序
集中和分散成度,确定工序顺序等。
在拟定工艺路线时,需同时提出几种可能的加工方法方案,然后通过技术、经济的对比分析,最后确定一种最为合理的工艺方案。
6.确定各工序所用机床设备和工艺装备(含刀具、夹具、辅具等),对需要改装或设计的专用工艺装备提出设计任务书。
7.确定各工序的加工余量,计算工序尺寸公差。
8.确定各工序的技术要求及检验方法。
9.确定各工序的切削用量和工时定额。
10.编制工艺文件。
二、工艺路线的拟订
拟订工艺路线是设计工艺规程最为关键的一步,需顺序完成以下几个方面的工作。
(一)选择定位基准
在工艺规程设计中,正确选择定位基准,对保证零件技术要求、确定加工先后顺序有着至关重要的影响。
定位基准有精基准与粗基准之分。
用毛坯未经加工的表面定位基准称为粗基准;用加工过的表面作定位基准称为精基准。
在选择定位基准时一般都是先根据零件的加工要求选择精基准,然后再考虑用那一组表面作粗基准才能把精基准加工出来。
1.精基准的选择原则
选择精基准一般应遵循以下几项原则:
(1)基准重合原则为了较容易地获得加工表面对其设计基准的相对位置精度要求,应选择加工表面的
设计基准为其定位基准。
这一原则称为基准重合原则。
如果加工表面的设计基准与定位基准不重合,则会增大定位误差,如果选择所加工表面的工序基准为精基准,这样可以避免由于基准一重合收起的定位误差。
(2)统一基准原则应尽可能选择用同一组精基准加工工序上尽可能多的表面,以保证所加工的各个表
面之间具有正确的相对位置关系。
例如,加工轴类零件时,一般都采用两个顶尖作为驻的精基准来加工轴类零件上的所有外圆表面和端面,这样可以保证各外圆表面间的同轴度和端面对轴心线的垂直度。
采用统一基准进行加工还有减少夹具种类、降低夹具设计制造费用的作用。
(3)互为基准原则当工件上两个加工表面之间的位置精度要比较高时,可以采用两个表面互为基准的
方法进行加工。
例如,车床主轴前后支承轴颈与主轴锥孔间有严格的同轴度要求,常先以主轴锥孔为定位基准磨主轴前、后支承轴颈表面,然后再以前、后支承轴颈表面为定位基准磨主轴锥孔,最后达到图样上规定的同轴度要求。
(4)自为基准原则一些表面的精加工工序,要求加工余量小而均匀,常以加工表面自身为精基准进行
加工。
2.粗基准的选择原则
工件加工的第一道工序所用基准都是粗基准,粗基准选择得正与否,不但与第一道工序的加工有关,而且还将对该工件加工的全过程产生重大影响。
选择精基准,一般应遵循以下几项原则:
(1)保证零件表面相对于不加工表面具有一定位置精度的原则被加工零件上如有不加工表面应选不加工面作粗基准,这样可以保证不加工不表面
相对于加工表面具有一定的相对位置关系。
(2)合理分配加工余量的原则从保证重要表面加工余量均匀考虑,应选择重要表面作为粗基准。
(3)便于装夹的原则为使工件定位稳定,夹紧可靠,要求所选用的粗基准尽可能平整、光洁,不允许有
锻造飞边、铸造浇冒、切痕或其他缺陷,并有足够的支承面积。
(4)粗基准不重复使用原则粗基准通常只允许使用一次,这是因为粗基准一般都很粗糙,重复使用同一粗基准
所加工的两组表面之间的位置误差会相当大,所以,粗基准一般不得重复使用。
(二)表面加工方法的选择
机器零件的结构形状虽然多种多样,但它们都是由一些最基本的何表面组成的,机器零件的加工过程实际就是获得这些几何表面的过程。
同一种表面可以选用各种不同的加工方法加工,但每种方法的加工质量、加工时间和花费的费用却是各不相同的。
工程技术人员的任务,就是要根据具体加工条件选用最适当的加工方法,加工出合乎图样要求的机器零件。
(三)加工阶段的划分
当零件的质量要求较高时,一般都要经过粗加工,半精加工和精加工等三个阶段;如果零件的加工精度要求特别高、表面粗糙度要求特别小时,还要经过精整和光整加工阶段。
各个加工阶段的主要任务是:
1.粗加工阶段高效地切除加工表面上的大部分余量,使毛坯在形状和尺寸上接近成品零件。
2.半精加工阶段切除粗加工后留下的误差,全被加工工件达到一定精度,为精加工做准备,并完成
一些次要的加工,例如,钻孔、攻螺纹、铣键槽等。
3.精加工阶段保证主要表面达到零件图规定的质量要求。
4.精整和光整加工阶段
其主要任务是减小表面粗糙度和进一步提高尺寸精度和开状精度,但一般没有提高表面间位置精度的作用。
(四)工序集中与分散
确定加工方法后,就要按零件加工的生产类型和工厂具体条件确定工艺过程的工序数。
确定零件加工过程工序数有两种迥然不同的原则,一种是工序集中原则,另一种是工序分散原则。
按工序集中原则组织工艺过程,就是使每个工序包括的加工内容尽量些,组成一个集中工序;按工序分散就是使每个工序所包括的加工内容尽量少些。
(五)工序先后顺序的安排
1.机械加工工序的安排
机械加工工序先后顺序的安排,一般应遵循以下原则:
(1)先加工定位基面,再加工其他表面;
(2)先加工主要表面,后加工次要表面;
(3)先安排粗加工工序,后安排精加工工序;
(4)先加工平面,后加工孔。
2.热处理工序及表面处理工序的安排
为改善工件材料切削性能安排的热处理工序,例如退火、正火、调质等,应在切削加工前进行。
为消除工件内应力安排的热处理工序,例如人工时效、退火等,最好安排在粗加工阶段之后进行。
为了改善工件材料力学性能的热处理工序,例如淬火、渗碳淬火等,一般都安排在半精加工和精加工之间进行,这是因为淬火处理后尤其是渗碳淬火后工件会有加较大的变形产生,为了修正渗碳、淬火处理产生和变形,热处理后需要安排精加工工序。
在淬火处理进行之前,需将铣槽、钻孔、攻螺纹、去行刺等次要表面的加工进行完毕。
当工件需要淬火处理时,由于渗碳过程工件会有较大的变形产生,常将渗碳过程放在次要表面加工之前进行,这样可以减少次要表面与淬硬表面间的位置误差。
为提高工件表面耐磨性、耐蚀性安排的热处理工序以及装饰旷目的而安排的热处理工序,例如镀铬、镀锌、发兰等,一般都安排在工艺过程最后阶段进行。
3.其他工序的安排
为保证零件制造质量,防止产生废品,需在下列场合安排检验工序:
(1)粗加工全部结束之后;
(2)送往外车间加工的前后;
(3)工时较长工序和重要工序的前后来;
(4)最终加工后。
除了安排几何尺寸检验工序外,有的零件还要安排擦伤、密封、稳重、平衡等检验
工序。
零件表层或内腔的毛刺对机器装配质量影响甚大,切削加工之后,应安排去毛刺工
序。
零件在进入装配之前,一般都应安排清洗工序。
在用磁力夹紧的工序之后,要安排
去磁工序,不让带有剩磁的工件进入装配线。
(六)机床设备与工艺装备的选择
正确选择机床设备是一件很重要的工作,它不但直接影响工作的质量,而且还影响
工件的加工效率和制造成本。
所选机床设备的尺寸规格应与工件的加工质量相适应,机床精度等级应与本工序加工要求相适应,电动机功率应与本工序加工所需功率适应,机床设备的自动化程度和生产效率应与工件类型相适应。
工艺装备的选择将直接影响工件的加工精度、生产效率和制造成本,应根据不同情况适当选择。
在中小批生产条件下,应首先考虑选用通用工艺装备(包括夹具、夹具、量具和辅具);在大批量生产中,可根据加工要求设计制造专用工艺装备。
(七)切削用量的选择
切削用量是指在切削过程中,选取的切削速度、进给量和被吃刀量的具体数值。
合理选择切削用量,对于保证质量、提高生产率和降低成本具有重要作用。
提高切削速度、加大进给量和被吃刀量,都使得单位时间内金属的切除增多,因而都有利于生产率的提高。
但实际上它们受工作材料、加工要求、刀具耐用度、机床动力、机床和工件的刚性等因素限制,不可能任意选取。
合理选择切削用量,就是在一定条件下选择的切削用量三要素的最佳组合。
其基本原则是:
应首先选择一个尽可能大的切削深度,其次选择一个较大的进给量,最后,在刀具耐用度和机床功率允许条件下选择一个合理的切削速度。
T6145镗床主轴套筒加工工艺设计
第一节零件图分析
一、结构特点
主轴套筒是镗床的关键零件之一,它的质量直接影响机床的精度和镗床对工件的加工质量和精度,所以它的精度要求较高,尤其尺寸精度、形位精度和表面粗糙度等。
技术要求:
1、材料为38CrMoAlA;
2、氮化深度0.5,硬度HV900;
3、其它棱角倒角;
4、齿顶棱边倒角R.
图2.1镗床主轴套筒
图2.1为镗床主轴套筒零件图。
其结构特点如下:
主轴套筒中间安装镗床主轴,在两端φ90mm与φ85mm孔内安装轴承,轴承内孔与主轴轴颈相配合用来支承主轴并保证主轴的回转精度;在套筒的圆表面上铣出齿条与主轴箱中的齿轮相啮合,由齿轮带动
齿条,使主轴套筒与主轴实现进给运动;主轴套筒外圆与抽轴承相配合,要求主轴套筒既能在横向运动时无阻滞,以要求在主轴旋转时不产生晃动,以保证主轴的回转精度。
所以φ90mm与φ85mm孔和φ105mm的外圆是该零件的主要加工的表面。
此外,该零件全长476mm,两端内孔的形状和位置公差是不易掌握的,并且其最薄处仅有4.5mm,工序安排不易会产生变形,将直接影响到零件的加工精度,套筒的主要面的粗糙度0.8和1.6,加工表面全部需要磨削,并在磨削前必须要安排合理的热处理,总之该零件的主要加工表面必须经过多道加工,才能逐步提高精度以达到要求。
二、技术要求
镗床主轴套筒的技术要求见表2.1:
表2.1镗床主轴套筒的技术要求
项目
说明
φ90mm内孔轴线对φ105mm外圆轴线的同轴度公差为φ0.01mm。
φ90mm内孔表面圆柱度公差0.002mm;
φ90mm内孔表面对φ105mm外圆轴线的
径向圆中跳动公差为0.002mm。
55±0.1长度的左端面对φ90mm内孔和φ85mm内孔的公共轴线端面圆跳动公差为0.002mm。
55±0.1长度的左右端面任选基准的平等度公差为0.01mm。
项目
说明
φ105mm外圆表面圆柱度公差为
0.002mm。
齿条齿形中心平面对φ105mm外圆轴线的垂直度公差为0.02mm。
φ85mm内孔表面圆柱度公差为0.002mm;
φ85mm内孔表面对φ105mm外圆轴线的
径向圆跳动公差为0.002mm。
32长度右端面对φ90mm和φ85mm内孔的公共轴线端面圆跳动公差为0.002mm。
氮化深度0.5,HV900
热处理氮化工艺后,工件的氮化层深
0.5mm,维氏硬度在900左右。
38CrMoAlA
含碳为0.38%的中碳优质合金结构钢
1.φ105mm外圆表面的轴线是设计基准,其尺寸公差等级很高为IT4级,表面粗糙度为Ra0.04μm,这些技术条件都是为了保证与抽轴承的配合精度和运动的平稳。
2.两端φ85mm和φ90mm内孔表面对φ105mm外圆轴线的径向圆跳动公差为
0.002mm,圆柱度为0.002mm,其表面粗糙度值为Ra0.32mm,这些技术条件都是为了满足与轴承配合的要求,以保证主轴的回转精度;φ90mm和φ85mm孔的内端面对φ90mm和φ85mm内孔的公共轴线端面圆跳动公差为0.002mm,这是因为这两处端面都
是推力轴承的安装基准,它的精度直接影响轴向窜动。
3.中间的60○倒角是工艺基准,专为精磨φ105mm外圆时用顶尖式心轴而设计的,
以保证两端内孔与外圆有很高的同轴度。
4.齿条齿形中心平面对φ105mm外圆轴线的垂直度公差为0.02mm,这项技术条件是保证齿轮与齿条啮合时接触良好,传动平稳。
第二节生产类型的确定
生产类型是企业生产专业化程度的分类,一般分为大量生产、成批生产和单件生产,其中成批生产又分为小批生产、中批生产和大批生产。
由于该T6145镗床主轴套筒的年产量定为100件/年,查表2.2可知,该生产类型属于小批生产。
表2.2机械加工各种生产类型
生产类型
生产纲领
单件生产
成批生产
大量生产
小批
中批
大批
产品类型
重型机械
<5
5~100
100~300
300~1000
>1000
中型机械
<20
20~200
200~500
500~5000
>5000
轻型机械
<100
100~500
500~5000
5000~50000
>50000
小批量生产纲领的工艺特点如下:
1.毛坯的制造方法及加工余量:
自由锻、木模手工造型;毛坯精度低余量大。
2.机床设备及机床布置:
通用机床按机群式排列;部分采用数控机床及柔性制造单元。
3.夹具及尺寸保证:
通用夹具、标准附件或组合夹具;划线试切保证尺寸。
4.刀具及量具:
通用刀具,标准量具。
5.零件互换性:
配对制造,互换性低,多采用钳工修配。
6.工序集中成度:
工序集中,加工工序少,每工序加工内容多。
7.工艺文件的要求:
编制简单的工艺过程卡片。
8.生产率:
用传统加工方法,生产率低,用数控机床可提高生产率。
9.成本:
较高。
10.对工人的技术要求:
需要技术熟练地工人。
10.发展趋势:
采用成组工艺、数控机床、加工中心及柔性制造系统。
第三节毛坯的选择
T6145镗床主轴套筒的材料为38CrMoAlA,所以选择毛坯类型为圆钢,成品外形尺寸为φ105mm×476mm,所以参考表2.3外圆表面加工余量表,