模糊控制配料系统论文.docx
《模糊控制配料系统论文.docx》由会员分享,可在线阅读,更多相关《模糊控制配料系统论文.docx(65页珍藏版)》请在冰豆网上搜索。
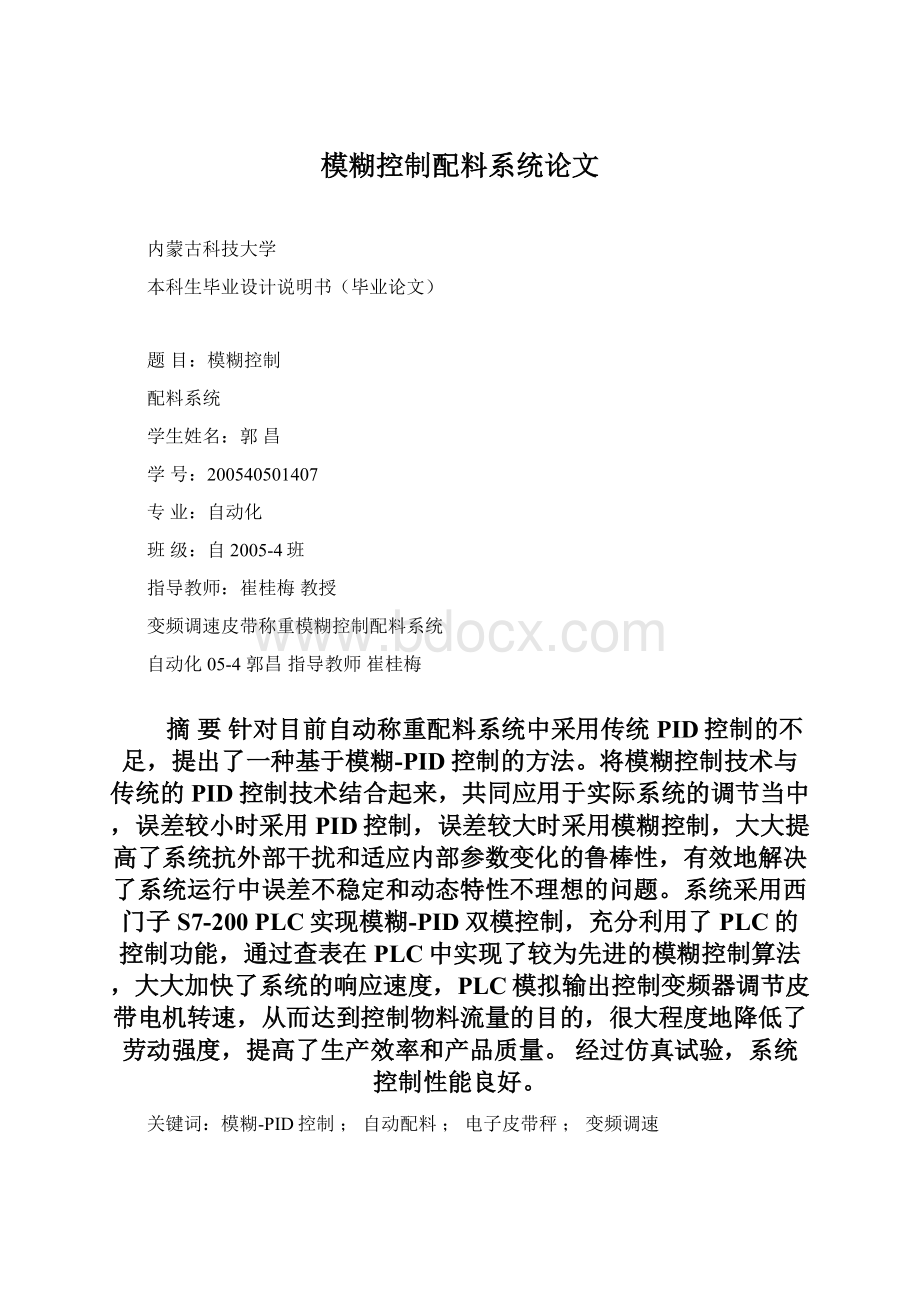
模糊控制配料系统论文
内蒙古科技大学
本科生毕业设计说明书(毕业论文)
题目:
模糊控制
配料系统
学生姓名:
郭昌
学号:
200540501407
专业:
自动化
班级:
自2005-4班
指导教师:
崔桂梅教授
变频调速皮带称重模糊控制配料系统
自动化05-4郭昌指导教师崔桂梅
摘要针对目前自动称重配料系统中采用传统PID控制的不足,提出了一种基于模糊-PID控制的方法。
将模糊控制技术与传统的PID控制技术结合起来,共同应用于实际系统的调节当中,误差较小时采用PID控制,误差较大时采用模糊控制,大大提高了系统抗外部干扰和适应内部参数变化的鲁棒性,有效地解决了系统运行中误差不稳定和动态特性不理想的问题。
系统采用西门子S7-200PLC实现模糊-PID双模控制,充分利用了PLC的控制功能,通过查表在PLC中实现了较为先进的模糊控制算法,大大加快了系统的响应速度,PLC模拟输出控制变频器调节皮带电机转速,从而达到控制物料流量的目的,很大程度地降低了劳动强度,提高了生产效率和产品质量。
经过仿真试验,系统控制性能良好。
关键词:
模糊-PID控制;自动配料;电子皮带秤;变频调速
Abstract
AutomaticweighingingredientsforthecurrentsystemusedintheinadequaciesoftraditionalPIDcontrol,afuzzy-PIDcontrol-basedapproach.ThefuzzycontroltechnologywiththetraditionalPIDcontroltechnologycombinedwithcommonregulationappliestotheactualsystem,theerrorwhenusingPIDcontrolofasmallermarginoferrorgreateruseoffuzzycontrolsystemgreatlyenhancedtheanti-interferenceandadapttoexternalchangesintheinternalparametersrobustandeffectivesolutiontoasystemerrordynamiccharacteristicsofinstabilityandtheproblemofunsatisfactory.
SystemusesaSiemensS7-200PLCtoachievedual-modefuzzy-PIDcontrol,makefulluseofthePLCcontrolfunctions,throughthelook-uptableinthePLCtoachieveamoreadvancedfuzzycontrolalgorithm,greatlyspeedingupthesystemresponsespeed,PLCanalogoutputinvertercontrolmotorspeedregulatingbelt,soastoachievethepurposeofcontrollingtheflowofmaterials,toalargeextentreducedthelaborintensityandimproveproductionefficiencyandproductquality.Aftersimulation,thesystemcontrolperformancegood.
Keywords:
Fuzzy-PIDcontrol;Automaticingredient;Electronicbeltscale;VVVF
目录
摘要I
AbstractII
第一章引言1
1.1设计背景及其意义1
1.2目前国内外的现状及存在的问题2
1.2.1电子皮带秤配料系统的现场工艺过程2
1.2.2国内外常用技术解决方案2
1.2.3现有控制系统存在的问题3
1.3本设计的主要研究内容和解决的问题5
第二章自动配料系统的总体结构设计7
2.1系统总体设计方案和基本组成7
2.2系统工作原理及控制模型9
2.3配料皮带秤的组成及原理10
2.3.1配料皮带秤的组成10
2.3.2配料皮带秤的工作原理10
2.4称重传感器11
2.4.1称重传感器的选择11
2.4.2称重信号的处理12
2.5测速传感器的选择14
2.6电机调速方式的选择15
2.6.1常用电机调速方式15
2.6.2配料系统电动机的调速控制策略16
2.7系统的抗干扰设计19
2.8接地措施20
第三章电气控制系统21
3.1配料过程的动力控制21
3.1.1可编程控制器的选用和配置21
3.1.2系统的输入输出量22
3.1.3动力控制部分的设计24
3.2称量落差补偿问题26
第四章模糊-PID复合控制系统的设计28
4.1系统的控制模型28
4.2控制思想与控制算法29
4.2.1PID控制器29
4.2.2模糊控制原理32
4.2.3Fuzzy控制器的结构及算法34
4.2.4模糊控制算法的PLC实现40
4.3变频调速皮带称重模糊控制配料系统的仿真试验42
4.3.1仿真分析43
4.3.2仿真试验43
4.3.3结论46
第五章系统通信与管理软件的设计47
5.1系统的通信设计47
5.1.1PROFIBUS-DP概述47
5.1.2PROFIBUS-DP系统的组成48
5.1.3PROFIBUS-DP系统工作过程49
5.1.4系统的PROFIBUS-DP通信52
5.2系统组态管理软件的选择与设计53
5.2.1组态软件的选择53
5.2.2上位机与PLC的通信组态设计55
5.2.3监控模块中变量组态57
5.2.4配料系统的软件功能模块57
第六章总结与展望59
参考文献60
附录62
致谢80
第一章引言
一.1设计背景及其意义
近年来,国内新建烧结机的配料方法均采用重量配料法,重量配料就是按原料的重量来配料,采用电子皮带秤对物料进行连续计量,通过调节圆盘给料机或皮带的速度来实现定量给料,重量配料易实现自动配料,配料精度较高。
烧结机的配料采用电子皮带秤定量给料,为提高皮带配料秤的计量精度和配料系统给料精度,所有给料机的皮带配料秤均采用变频调速的方式进行控制。
该自动称重配料控制由下列五大部分:
电子皮带称、称重控制PLC、变频控制柜、监控计算机及现场操作箱部分。
配料自动控制实现烧结用的原料如混匀矿、燃料、熔剂白云石、生石灰、冷返矿按照工艺要求的配比进行自动给料,能够判断下料堵料和失控故障、变频器故障,并报警。
电子皮带秤自动配料系统可以按照设定配比和流量控制各输入物料的瞬时流量,从而达到控制各种产品的质量和产量的目的,是实现生产过程自动化和智能化、企业的科学管理、安全稳定生产和节能降耗的重要技术手段[1]。
微机配料控制系统在生产中的应用不仅可以提高配料质量和产量,也大大减轻了岗位工人的劳动强度,提高了生产效率。
有些企业开发了一些基于皮带秤仪表和PID控制器的皮带秤配料系统,但控制精度不尽人意,易出故障,不能适应许多生产工艺过程中的恶劣环境,不能满足用户日益增长的设备需求。
因此,优化设计研制技术先进、设备成熟、经济实用的配料系统至关重要。
本课题设计开发的变频调速皮带称重模糊控制配料系统能有效解决动态皮带称重控制物料流量的精度问题,又因为采用先进的控制算法明显加快了系统响应速度,很大程度地降低劳动强度,提高生产效率和产品质量,带来可观的经济效益,推动国民经济的发展。
一.2目前国内外的现状及存在的问题
一.2.1电子皮带秤配料系统的现场工艺过程
企业内常见的皮带秤自动配料系统现场结构组成如图l-l所示,结构形式是一种最基本、使用最广泛的皮带配料系统。
由于每个称重单元的工作原理与控制方法是类似的,本系统以称重单元中的一个为例。
系统的每个物料仓装满物料压在皮带上,皮带电机拖动皮带转动,则物料被连续拉出,皮带电机的转速就决定了物料的流量。
皮带电机可采用多种调速方式,每个皮带下面有一自动称重皮带秤,通过皮带秤就可以称出下料的流量、累计量等数据;所有皮带的下面是一输送主皮带把混合好的原料送到下级容器中。
图1-1皮带秤自动配料系统现场示意图
一.2.2国内外常用技术解决方案
目前国内电子皮带秤自动配料系统的生产厂家主要有徐州拉姆齐、山西新元、济南金钟等,国外的生产厂家有德国申克、日本大和等。
某些厂家从成本考虑,采用单片机进行简单的称量积算和PID调节,功能简单,控制精度低,管理功能弱,可靠性不高。
规模较大的公司则通常采用基于调节器和Windows平台的皮带秤配料系统[2-3],该系统正常工作时,配料仪表接受来自秤体的称重信号和测速信号,经乘积算后显示瞬时流量和累计量,并将瞬时流量以4~20毫安模拟电流的形式送往PID调节器作为调节测量输入信号,调节器将该信号与机内设定值比较运算后输出4~20毫安模拟调节信号,控制皮带电机转速,从而进一步控制该种物料的下料流量,最终使几种物料的瞬时下料流量与阶段累计量都保持在用户要求的范围内。
要改变流量及配比可直接在调节器上进行设定操作,操作简单方便。
为便于集中控制,可以采用工控机作为上位机,通过串行接口与配料仪表和调节器进行通讯,对现场配料情况进行实时监控,并可直接在工控机上进行经验PID参数的设定[3],加上报警监测功能,整个系统实现了自动化,节省了劳力,提高了生产效率。
第i号皮带电机的传统控制方框图模型如图1-2所示。
图1-2常用系统控制方框图
一.2.3现有控制系统存在的问题
适用上述解决方案的工艺现场首先必须满足这样一个前提条件,那就是物料流出量必须与直拖皮带电机的转速成正比。
要使系统具有良好的调节品质,即有较高的稳定性、准确性和快速性,系统还必须具备两个条件[4]:
1)系统自身的结构性质稳定,这包括它的容量系数、阻力和传递距离等内容。
2)调节器有合理的PID参数。
只有将这三种作用的强度作适当的配合,才可以使调节器快速、平稳、准确地运行,从而获得满意的控制效果。
在这两者中,条件1)是条件2)的前提,因为PID参数取决于系统的动态特性,而影响系统动态特性的主要因素是系统本身的结构性质。
因为以往常用配料称重系统方案设计是基于普通的PID调节器,采用一般的PID控制算法,其参数一般是按阶跃响应的过渡过程时间来整定的,灵敏度较高,对于固定参数的系统有着较好的调节品质,从理论上讲能做到无误差调节,在误差较小的范围内确有其优越性。
在各设备运转正常、稳定的情况下,可以实现良好的控制效果。
同时,利用调节器的自整定功能可由调节器自动整定出一套合理的PID参数用于系统的正常运行。
但是,实际中电子皮带秤自动配煤系统的控制准确度会受到多个因素的影响[5]。
1)给料设备安装精度的影响
给料设备加工和安装精度对控制准确度也会发生影响。
例如:
采用圆盘给料机作为给料设备时,假如圆盘的水平精度不高,在给料圆盘旋转一周的时间内将会产生给料量的大小变化。
要害是周期性大小变化的干扰信号会引入到配料控制回路,对系统控制准确度产生影响,所以,给料设备的加工安装应最大限度地严格。
2)料仓结构形状的影响
实践证明:
料仓的形状以及料仓内壁的材料选用,都对物料均匀流线型下落有影响。
严重时会使物料积压在料仓中,产生所谓的“悬料”现象,物料时下时不下。
这些都会干扰配料系统正常工作。
3)物料物理特性的影响
物料流动性的好坏是影响配料系统的因素之一。
当物料的粒度、湿度、温度、灰分发生变化时,给料设备往往不能正常地供料,严重时配料系统无法工作。
如在我国南方,雨水较多,若对物料无保证措施,物料水分受天气的影响有时会粘成球团,在这种情况下,配料准确度是无法保证的,而在我国北方,冬天气温很低,若对物料无保护措施,物料可能结在一起,也同样不能保证准确度,所以,要达到控制准确度指标,物料应不结块、结球,粒度保持一致,水分适中,流动性好。
因此一般都在物料仓两边加两个电机作为振动器使用,以防止物料结块。
4)机械震动的影响
配料皮带秤检测出的物料瞬时流量是要参与控制量的输出运算的,是通过瞬时物料流量求出控制量。
如果瞬时物料流量不稳定,将直接影响系统的控制准确度。
安装时尽量避免将周围输送设备的振动引入到配料秤中。
5)现场环境较为复杂、恶劣,其他外界干扰频繁。
如:
秤体排列紧凑,秤体周围常安装有大功率给料电机;仪表附近装有大功率变频器,电机经常频繁启停,电磁波干扰大。
由于以上因素的存在,系统误差往往较大,其动态特性并不理想,超调量一般较大,因为不能及时地调整流量,造成系统自身的阻力和传递距离不稳定,设备运转不稳定,系统的结构性质不稳定,最终导致控制系统无法实现理想的控制效果,并调节器的自整定功能也失效[5]。
此时,通常只能由操作人员通过一定的经验方法了解系统的动态特性,人工整定出一套粗略的PID参数,使之能够在恶劣的环境条件下以适用于一个较宽的范围。
但此时皮带秤的计量性能和配料精度都会受到影响。
目前,该问题一直困扰着许多用户,尚没有较为成熟的方法来解决这一问题。
还有其他如:
称重传感器、测速传感器的选择;电机调速方式的选择;系统抗干扰设计;动力联锁控制;系统调试;称重管理软件的设计等问题都有待于进一步改进[13]。
一.3本设计的主要研究内容和解决的问题
本课题针对以上现有皮带配料系统中存在的问题,设计开发了一套合理高效的变频调速皮带称重模糊控制配料系统以解决皮带输送过程中的,系统响应速度与控制精度的问题。
本设计主要研究内容是针对自动配料环节,采用模糊-PID复合控制技术、将模糊控制技术结合传统的PID控制策略应用在自动配料系统的调节中。
论文详细阐述了模糊-PID复合控制系统具体的实现,即通过对自动配料系统的分析,建立合理的控制系统模型,根据模糊控制原理,提出自动配料系统的模糊控制结构和算法,以改进电子皮带秤自动配料系统的控制调节效果,解决了原系统存在的误差较大时,动态特性不理想,超调量较大的问题,从而进一步提高了系统的配料精度和配料速度[6]。
论文第二章阐述了皮带秤配料系统的总体结构设计,第三章说明了电气控制系统的配置实现,第二章和第三章属于系统的硬件设计部分;第四章对模糊-PID复合控制系统进行了详细研究以及部分仿真试验,第五章介绍了系统通信与管理软件的设计思路,第四章和第五章属于系统的软件设计部分;第六章是设计所得出的结论部分。
第二章自动配料系统的总体结构设计
二.1系统总体设计方案和基本组成
以4台皮带秤组成的配料系统为例。
本系统主要由配料电子皮带秤、仪表控制柜、动力控制柜、低压开关柜、变频器柜、现场操作盘、工业控制微型计算机、及监控管理软件几部分组成[7]。
1)配料电子皮带秤
配料电子皮带秤对经过皮带的散装物料进行自动地连续称量和累计,具有运输和计量两种功能。
称重部分采用电阻应变式工作原理,多托辊杠杆式结构,实际工作时,皮带秤采用恒速计量方式[1],通过调节上级给料速度来改变物料流量,本类型皮带秤多用于企业内部生产的工艺控制。
2)仪表控制柜
仪表控制柜主要包括4台皮带秤仪表。
每台皮带秤仪表接受来自称重传感器的重量毫伏信号和来自测速传感器的带速脉冲信号,计算出流量和累计量,并将流量信号以4~20毫安模拟电流的形式送给工控机,工控机将流量信号与机内设定值比较后,根据一定的控制规则输出4~20毫安调节信号,控制现场给料电机的转速,从而构成单机闭环系统,达到控制某种物料流量的目的。
皮带秤仪表通过RS-485通讯接口与工控机进行通讯。
3)动力控制柜
动力控制柜是动力部分的中央控制部件,安装有电流表、控制按钮、指示灯、可编程控制器(以下称PLC)及电机保护电路,用于监控现场皮带机电流、对现场皮带机和给料设备的启停进行控制、指示电机运行状态、联锁控制及打滑跑偏报警。
PLC通过扩展EM277通讯模块,用PROFIBUS_DP的通讯接口与工控机进行通讯。
4)低压开关柜
低压开关柜配置有刀开关、断路器、电压表、电流表、电流互感器、隔离变压器等器件为各控制柜和配煤系统动力部分提供电源,同时检测动力电源部分的相间电压和线电流。
5)变频器柜
柜中的变频器,接受来自动力控制柜的开关信号控制上级给料电机的启停,同时亦接受来自工控机的4~20毫安调节信号,来改变输出动力电源的频率,从而控制现场7台给料机的转速。
如果变频器功率较大,则必须在柜体中配置散热风扇,以保证变频器能正常工作。
6)现场操作盘
配煤系统电机的现场控制部件,装有控制按钮、指示灯,可在机旁对现场皮带机和给料设备的启停进行控制、指示PLC对电机的命令状态。
7)工业控制微型计算机及软件
工控机作为上位机,通过PROFIBUS双向通讯接口与动力控制柜中的PLC联机,控制PLC的运行方式,输出开关量量控制信号控制主皮带电机的启停,从而构成完整的配料系统。
工控机另留有一个RS485双向通讯接口,以备与全厂的上位工控机通讯。
监控软件的主要功能有:
根据生产配方和产量目标对称重过程进行自动控制,对称重数据进行统计管理并实现打印,包括对变频器进行调节控制的运算。
系统软件有多种现场监控方式和配方输入方式,以适应不同的工程要求,用户可设定报警打印时间等参数。
界面采用菜单方式,使用方便,用户可通过鼠标或键盘进行操作,对整个配料系统进行控制和管理。
二.2系统工作原理及控制模型
系统开始工作时,工控机首先根据本次生产任务首先进行各种初始化,包括各成分的名称、仓号、产量、标准配比、标准流量等,然后按一定时序控制各给料机和皮带秤的启动,各给料机按一定流量给料,同时工控机读取皮带称重仪的重量信号和累计量数据,根据各成分的累积量值计算当前的实际配比,通过与标准配比的比较修正各给料机的给定量,使系统工作在最佳配比状态,当达到预定产量时,再按一定时序停止各给料机。
该系统的特点是由一台上位机来控制多台给料机,为了实现一定的配比,各给料机之间的工作又是相互联系的,而且给定量要随当前的实际配比进行修改,因此其控制结构是较为复杂的。
第i号给料机的控制方框图模型如图2-1所示。
图2-1第i号皮带电机的控制方框图模型
从图2-1中可以看出,该系统属于一个多闭环有关联控制结构。
就第i号给料仓而言,有两个闭环和一个前馈,内环是一个FUZZY-PID控制器,据给定流量Fgi去控制调速给料机,使其给料流量Fi控制在理想的给定值Fgi附近。
外环根据当前的累积值和希望产量之差△P以及前馈环节的给料机当前流量来修正内环的给定值。
控制器采用FUZZY-PID复合控制方式,当偏差较大时采用模糊控制,当偏差减小到较小范围时采用PID控制方式。
这样就可以解决系统误差较大,其动态特性不理想,超调量较大的控制难题。
具体实现见第四章。
二.3配料皮带秤的组成及原理
二.3.1配料皮带秤的组成
配料皮带秤的结构组成,主要由输送机架、称重传感器、测速传感器、秤架、主动滚筒、从动滚筒、输送带、张紧装置、拖动装置、清扫器、调偏装置等组成。
当散落在输送皮带机上的物料通过秤体时,秤体中的称重传感器和测速传感器分别把重量毫伏信号和带速脉冲信号通过接线盒送往皮带秤仪表。
二.3.2配料皮带秤的工作原理
皮带秤是自动衡器,与人们熟悉的非自动秤比较,前者是物料在输送过程中连续自动地完成称重任务,后者是物料在静止状态下断续地进行称重。
所以连续、自动称重是皮带秤的主要特点。
运动皮带上单位长度的瞬时流量,某一段距离的物料重量,或一段时间和一段距离的累积重量,这些量可以用积分法来演算。
输送机输送物料时,皮带秤仪表连续测量皮带上每单位长度的载荷值q(kg/m),并与皮带在同一时刻的速度v(m/s)相乘,测得结果为物料的瞬时流量,q*v(kg/s)。
因物料输送的不均匀性和皮带速度随时间变化,所以在T时间间隔的累积流量可以用以下积分式(2-1)表示:
式(2-1)
W——T时间间隔的物料累积量kg或t;
T——物料通过秤的时间S或h;
q(t)——皮带单位长度上的物料重量kg/m;
v(t)——物料在皮带上的运行速度m/s。
二.4称重传感器
称重传感器作为衡器的关键部件,其应用已经很普及了,但是称重传感器的选型,尤其是动态称重传感器的选型,还有很多要点需要注意。
配料皮带秤传感器选型时应着重考虑称重传感器的量程、灵敏度、结构材质等方面[8-9]。
二.4.1称重传感器的选择
l)量程的选择
皮带秤称重传感器的受力包括杠杆结构秤体的自重、物料流量作用力以及称量段内输送皮带的自重,因此量程选择要考虑这几项内容。
物料流量作用力Fl的计算方法见式(2-2)。
式(2-2)
式(2-2)中,Fi—物料额定流量;
L—称量段长度;
R—杠杆比,R=传感器受力/实际称量段受力(一般取R=0.5);
V(t)—物料在皮带上的运行速度。
考虑到皮带秤的使用环境较恶劣,经常遇到震动、冲击、过载等情况,为提高皮带秤可靠性,选择量程时,常取1.5的安全系数。
为解决这些问题,同时还要考虑机械限位的设计,称重传感器的材质尽量选用抗冲击、抗过载能力强且输出稳定的钢制传感器,而尽量不选取铝制材料。
2)灵敏度的选择
一台衡器是否能正常工作,必须考虑这个系统中各个部件的技术参数能否匹配[19]。
对衡器来讲,也就是称重传感器所选用最大秤量值,灵敏度值;称重仪表所选用的供桥电压值、最高灵敏度值等数最终必须满足这个系统的整体指标要求。
3)称重传感器结构类型的选择
电阻应变式称重传感器的结构类型较多,按照弹性体结构区分,主要有以下几种类型。
a)悬臂梁式称重传感器
悬臂梁式称重传感器结构简单,灵敏度高,便于制作加工,但对立的作用点较敏感,对于震动大的场合,其输出信号不稳定。
b)剪切梁式称重传感器
该类型传感器的弹性体截面形式多为工字形,电阻应变片贴在中性层位置上,对受力点的变化不敏感,但结构简单,灵敏度高,线形好,但弹性体贴片困难,加工不易。
所用材质多为铝制,稳定性差,而钢质的多为大量程,不适合皮带秤使用。
c)S型称重传感器
该类型传感器应变输出大、线性好,主要有平行梁和剪切梁两种类型。
剪切梁式的剪切力与梁弯距无关,消除了受力点移动所引起的输出灵敏度变化,对侧向载荷也有较大的抵抗能力,而且结构紧凑小巧。
其不足之处在于,用于小量程时,贴片处的腹板太薄,不易加工制作,且不易做到较高的灵敏度。
平行梁式有较大的刚度,对载荷的偏移不敏感,有较高的输出灵敏度,可用于小量程称重传感器。
通过以上分析可知,对于配料皮带秤,可选用钢质的S型称重器,其连接方式采用关节轴承,处于受拉状态,其抗侧向力的能力可安装于密封的梁内,结构紧凑。
二.4.2称重信号的处理
该测控系统中,采集的信号是来自各皮带秤上压力传感器输出的mV级小信号。
设计选用的皮带秤远传来的动态称重信号是0~30mV范围,不能直接被PLC读取,需要经过外加放大电路处理,将其转化为0~10V的标准电压信号。
为了实现电压放大,采用LM324系列器件为