机械工艺夹具毕业设计96传动轴工艺规程设计内容.docx
《机械工艺夹具毕业设计96传动轴工艺规程设计内容.docx》由会员分享,可在线阅读,更多相关《机械工艺夹具毕业设计96传动轴工艺规程设计内容.docx(28页珍藏版)》请在冰豆网上搜索。
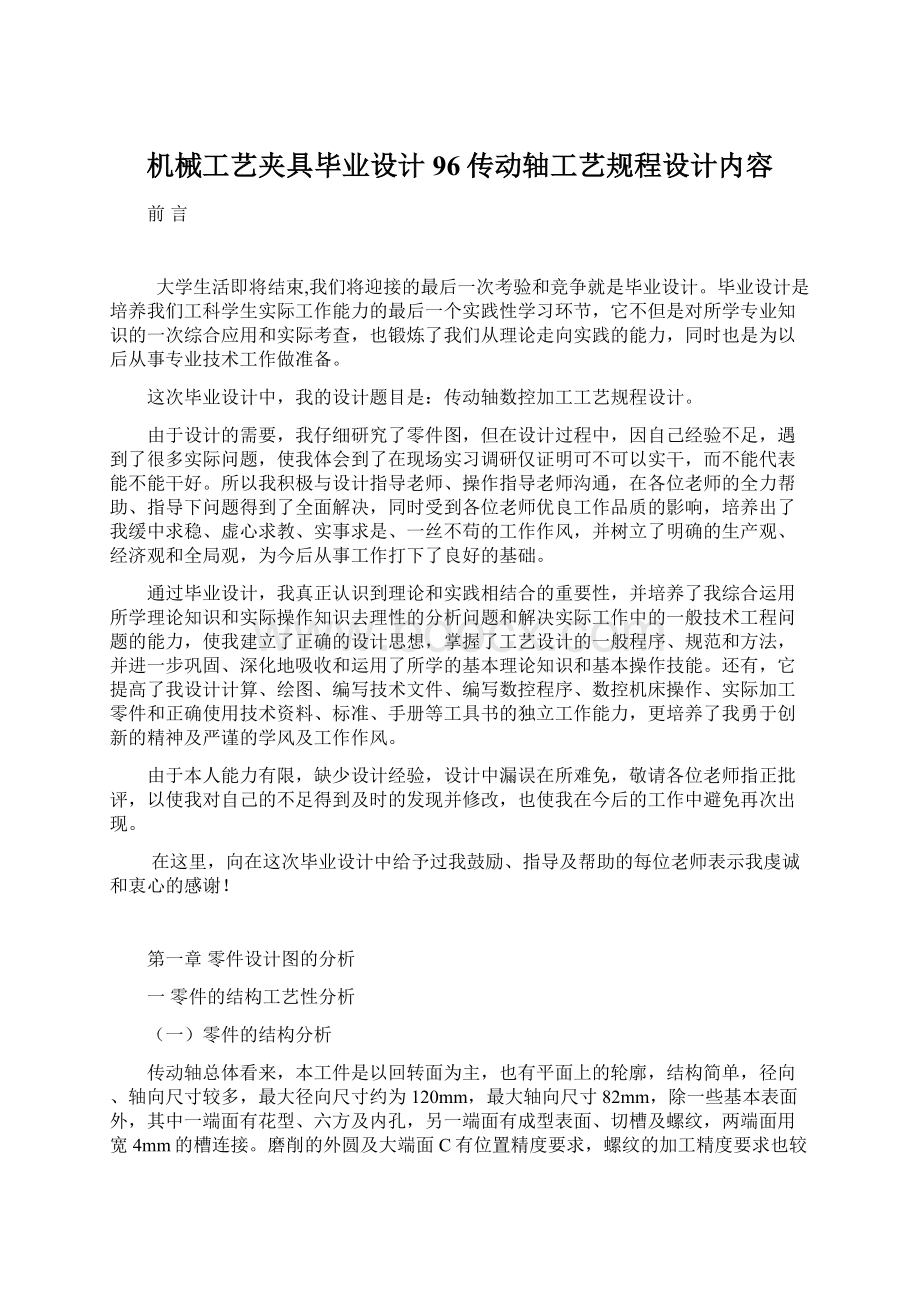
机械工艺夹具毕业设计96传动轴工艺规程设计内容
前言
大学生活即将结束,我们将迎接的最后一次考验和竞争就是毕业设计。
毕业设计是培养我们工科学生实际工作能力的最后一个实践性学习环节,它不但是对所学专业知识的一次综合应用和实际考查,也锻炼了我们从理论走向实践的能力,同时也是为以后从事专业技术工作做准备。
这次毕业设计中,我的设计题目是:
传动轴数控加工工艺规程设计。
由于设计的需要,我仔细研究了零件图,但在设计过程中,因自己经验不足,遇到了很多实际问题,使我体会到了在现场实习调研仅证明可不可以实干,而不能代表能不能干好。
所以我积极与设计指导老师、操作指导老师沟通,在各位老师的全力帮助、指导下问题得到了全面解决,同时受到各位老师优良工作品质的影响,培养出了我缓中求稳、虚心求教、实事求是、一丝不苟的工作作风,并树立了明确的生产观、经济观和全局观,为今后从事工作打下了良好的基础。
通过毕业设计,我真正认识到理论和实践相结合的重要性,并培养了我综合运用所学理论知识和实际操作知识去理性的分析问题和解决实际工作中的一般技术工程问题的能力,使我建立了正确的设计思想,掌握了工艺设计的一般程序、规范和方法,并进一步巩固、深化地吸收和运用了所学的基本理论知识和基本操作技能。
还有,它提高了我设计计算、绘图、编写技术文件、编写数控程序、数控机床操作、实际加工零件和正确使用技术资料、标准、手册等工具书的独立工作能力,更培养了我勇于创新的精神及严谨的学风及工作作风。
由于本人能力有限,缺少设计经验,设计中漏误在所难免,敬请各位老师指正批评,以使我对自己的不足得到及时的发现并修改,也使我在今后的工作中避免再次出现。
在这里,向在这次毕业设计中给予过我鼓励、指导及帮助的每位老师表示我虔诚和衷心的感谢!
第一章零件设计图的分析
一零件的结构工艺性分析
(一)零件的结构分析
传动轴总体看来,本工件是以回转面为主,也有平面上的轮廓,结构简单,径向、轴向尺寸较多,最大径向尺寸约为120mm,最大轴向尺寸82mm,除一些基本表面外,其中一端面有花型、六方及内孔,另一端面有成型表面、切槽及螺纹,两端面用宽4mm的槽连接。
磨削的外圆及大端面C有位置精度要求,螺纹的加工精度要求也较高。
由零件图样看,加工时除用外圆作基准外,可靠两顶尖夹紧定位,定心正确可靠,装夹方便,车削的各档表面之间同轴度好。
(二)零件的工艺性分析
1.主要加工表面的分析
根据零件图要求其主要加工表面为:
(1)φ
外圆,表面粗糙度Ra值0.4,并且需经过渗碳处理和保证渗碳层深度0.6-0.9mm硬度;
(2)M24×1.75-5g6g外螺纹;
(3)大端面C,表面粗糙度Ra值1.6,并且圆柱面绕基准孔作无轴向移动回转时,在任一测量平面内的径向圆跳动不大于0.04mm。
2.次要加工表面的分析
因为次要加工表面没有配合进度要求,只要求在保证零件硬度,耐磨性等使用性能的前提下尽量采用一次加工达到图样要求尺寸。
3.技术要求
(1)渗碳φ
外圆,深度0.6-0.9mm;
(2)渗碳区硬度HRC55-60;
(3)非渗碳区硬度HRC35-40;
(4)未注圆角C0.3;
(5)未注倒角C0.5;
(6)未注公差按HB5800-82。
4.零件的设计基准与定位基准
通过对零件图的分析可以看出零件有如下几个基准:
(1)径向尺寸的设计基准为两中心孔。
(2)轴向尺寸设计基准为零件大端面C。
由以上分析可知本零件采用三种基准原则:
一是基准重合原则,它是以两中心孔为定位基准也是设计基准,适合用于零件的外圆、切槽、螺纹、以及内孔的定位;另一种是基准统一原则,它是多个加工表面都以一个基准作基准面加工定位的;最后一种是互为基准原则,为了使加工面间有较高的位置精度可采用反复加工。
5.工件加工保证方法
(1)保证工件的形状精度
工件的位置精度主要是通过在加工过程中,控制切削用量中的ap的大小和vc的大小及刀具、夹紧力等因素来保证。
(2)保证工件的表面质量
在设计工件的工艺规程时,本工件回转表面及各端面通过数控车加工保证表面粗糙度6.3。
通过以上分析,可以得出本零件结构较为简单,易于加工,各部分尺寸分布较为合理,具有一定的可行性。
二零件的材料分析
(一)零件的材料分析
1.零件的材料选择
机械零件选材的一般原则是:
首先满足使用性能要求,同时兼顾工艺性、经济性和环保性。
对于轴类零件应具有:
(1)优良的综合力学性能,即要求有高的强度和韧性,以防由于过载和冲击而引起的变形和断裂。
(2)高的疲劳极限,防止疲劳断裂。
(3)良好的耐磨性。
(4)在特殊条件工作时,还应有特殊要求。
本零件为传动轴,工作条件及要求的力学性能如表1-1所示:
表1-1零件的工作条件及要求的力学性能
零件名称
工作条件
常见的失效
形式
要求的主要力学性能
应力种类
载荷性质
受载状态
传动轴
弯应力、
扭应力
循环冲击
轴颈摩擦、
振动
疲劳断裂、
过量变形、
轴颈磨损
综合力学
性能
由上所述,本零件采用优质合金渗碳钢,牌号为12Cr2Ni4A。
这类钢的选用原因及特点如下:
(1)性能特点
经渗碳,淬火—低温回火后,钢的表面具有高的硬度和耐磨性,心部具有足够强度,塑性和韧性。
(2)成分特点
碳含量低(
<0.25%),以确保零件的心部具有足够的塑性和韧性,同时也是为了能进行表面渗碳。
加入的合金元素有Cr、Ni、Mn、B、W、Mo、V、Ti等,可提高钢的淬透性并起到细化晶粒的作用。
(3)热处理特点
预先热处理经常采用正火处理,最终热处理采用渗碳、淬火-低温回火工艺。
2.材料的切削加工性
12Cr2Ni4A的切削加工性较差,切削时刀具易磨损,加工硬化现象严重,切削温度高,切削力大,切屑不易切断,容易损伤加工表面,易产生积屑瘤,降低表面质量。
因此在切削加工前需进行正火的预先热处理。
(二)零件的加工过程
首先对锻件毛坯进行正火的预先热处理,因为材料12Cr2Ni4A的硬度达不到技术要求硬度HRC35-40,所以要经正火处理提高硬度。
其次进行数控车削和渗碳处理。
渗碳是在工件表面形成渗碳层,提高工件表面硬度,耐磨性疲劳强度及抗蚀能力。
除渗碳表面外的非渗碳区域需保持原低碳硬度状态,不允许渗碳的区域采取防渗碳处理。
根据生产条件,生产经济等综合考虑,采用余量保护防渗法。
但螺纹不在此时车削,为后序的淬火做防变形保护。
如果在此时加工螺纹,淬火后要磨削修正螺纹,这样则会提高加工成本。
在数控铣床上铣轮廓至图样要求。
进行淬火+低温回火的最终热处理。
淬火后中心孔会随工件产生氧化变形,且表面形成较厚的氧化层,所以要对中心孔进行研磨修正,以保证其硬度、耐磨性、支承能力等使用性能。
前面以中心孔作基准车削外圆,此处以外圆作基准研修中心孔,符合互为基准原则。
热处理后按零件图样要求车削螺纹。
由于渗碳表面为工作表面,尺寸精度和表面粗糙度要求较高,所以还要对渗碳区进行磨削加工。
外圆的磨削余量一般为0.3-0.5mm,用查表法确定为0.3mm。
注:
未注圆角R0.3及未注倒角C0.5的作用:
为防止加工过程中引起应力集中使连接处产生微裂痕。
第二章零件毛坯的确定
一确定零件的生产纲领及生产类型
生产纲领是指企业在计划期内应当生产的产品产量和进度计划。
计划期常定为1年,所以也称年产量。
生产类型由生产纲领和零件型别决定。
它对零件工艺规程有重要影响,所以编制工艺规程之前必须先确定生产类型。
根据指导老师要求和零件生产类型设计任务书,生产类型为中批生产。
二确定零件的毛坯类型
在确定零件机械加工之前,还要确定毛坯。
毛坯是根据零件所要求的形状、工艺尺寸等方面而制成的供进一步加工使用的生产对象。
正确选择毛坯的制造形式具有重大的技术经济意义,选择不同类型的毛坯不仅影响毛坯的制造工艺设备,对零件的机械性能及工时定额计算也有影响。
在选择毛坯种类时应考虑的因素如下:
(1)零件材料及其力学性能;
(2)零件的形状和尺寸;
(3)生产类型;
(4)具体生产条件;
(5)充分考虑利用新工艺、新技术和新材料的可能性。
1.毛坯的种类
(1)铸件:
成本低。
铸件用于受力不大或以承压为主的零件或要求减振耐磨的零件。
铸钢件用于承受重载而形状复杂的零件,以砂型铸造时表面质量差。
通常用于机架、床身、底座、工作台、导轨、齿轮等。
(2)锻件:
成本较低。
用于承受重载,动载或复合载荷的重要零件,用自由锻单件
小批量生产时表面质量较低,用模锻大批量生产时表面质量较好。
通常用于连杆、螺栓、弹簧、模具、轴类零件等。
(3)焊接件:
生产成本中等。
用于制造金属结构件或组合件和零件的修补。
精度较
低,接头处表面质量很差。
一般用作锅炉、车身、飞机、管道、支架、压力容器、工作台等。
(4)冲压件:
生产批量越大,成本越低,用于板料成型的型件。
精度高,表面质量好。
通常用于汽车车身覆盖件、仪表、电器以及仪器、外壳及零件、油箱、水箱等各种薄金属件。
(5)型材:
成本较低。
一般用于中、小型简单件。
由于此材料适用于多种加工方法,
所以表面质量跨越很大。
通常用于制造光轴、螺母、销子等。
从零件图中可以看出零件形状并不复杂,各表面间直径尺寸相差较大,生产类型为中批生产,考虑到工厂的设备和技术水平等各方面还不能制成模锻件,而自由锻件是在各种锻锤和压力机上由手工操作而锻出的毛坯,这种锻件尺寸精度低,加工余量大,生产率低,工艺灵活,所用工具、设备简单,通用性大不需专用模具,成本低。
所以本零件的毛坯采用自由锻件毛坯。
2.毛坯形状,尺寸其公差的选择
(1)确定毛坯形状:
由于零件各加工表面间直径尺寸相差较大,所以毛坯形状要采用台阶状。
(2)确定毛坯尺寸及其公差:
首先选取毛坯加工余量和毛坯公差,其次将毛坯加工余量叠加在零件的相应加工表面上,从而计算出毛坯尺寸,最后标注毛坯尺寸及其公差。
毛坯形状和尺寸越接近成品零件,即毛坯精度越高,则零件的机械加工劳动量越少。
第三章零件工艺规程的设计
工艺规程是规定产品或零部件制造工艺过程和操作方法等的工艺文件。
它一般应包括下列内容:
零件的加工基准、加工工艺路线、各工序的具体加工内容及所用的设备和工艺装备等。
它是指导工人操作和用于生产、工艺管理工件的主要技术文件,是新产品投产前进行生产准备和技术准备的依据,是新建、扩建车间或工厂的原始材料,是交流和推广先进经验的重要手段。
它也是生产中的工艺纪律,必须严格执行。
制订零件工艺规程的基本要求是,在保证产品质量的前提下,尽可能提高劳动生产率和降低加工成本,并在充分利用企业现有的生产条件的基础上,尽可能采用国内外先进工艺技术和经验,还应保证操作者具有良好的劳动条件。
一定位基准的选择
定位基准分为工艺基准和设计基准。
其中,工艺基准又分为:
(1)工序基准;
(2)定位基准;(3)测量基准;(4)装配基准。
我们应尽量采用设计基准为定位基准。
定位基准的选择直接影响零件加工精度、能否保证其加工顺序的安排以及夹具结构的复杂程度等,所以它是在制定工艺规程中的一个十分关键的问题。
各工序定位基准的选择,应先根据工件定位基准能保证,再按基准选择原则来选定每个定位基准。
为使所选的定位基准能保证整个机械加工工艺过程顺利的进行,通常应先考虑如何选择精基准加工各个表面,然后考虑如何选择粗基准,把它作为精基准先加工出来。
基准的选择是否合理直接影响工件的位置精度,换言之,基准的选择主要是研究加工过程中表面的相对位置,精度及其保证方法。
所以,选择定们基准应遵循以下原则:
1.精基准的选择原则
(1)基准重合原则;
(2)基准统一原则;
(3)自为基准原则;
(4)互为基准原则;
(5)保证工件定位准确、夹紧可靠