固定板加工工艺规程设计.docx
《固定板加工工艺规程设计.docx》由会员分享,可在线阅读,更多相关《固定板加工工艺规程设计.docx(33页珍藏版)》请在冰豆网上搜索。
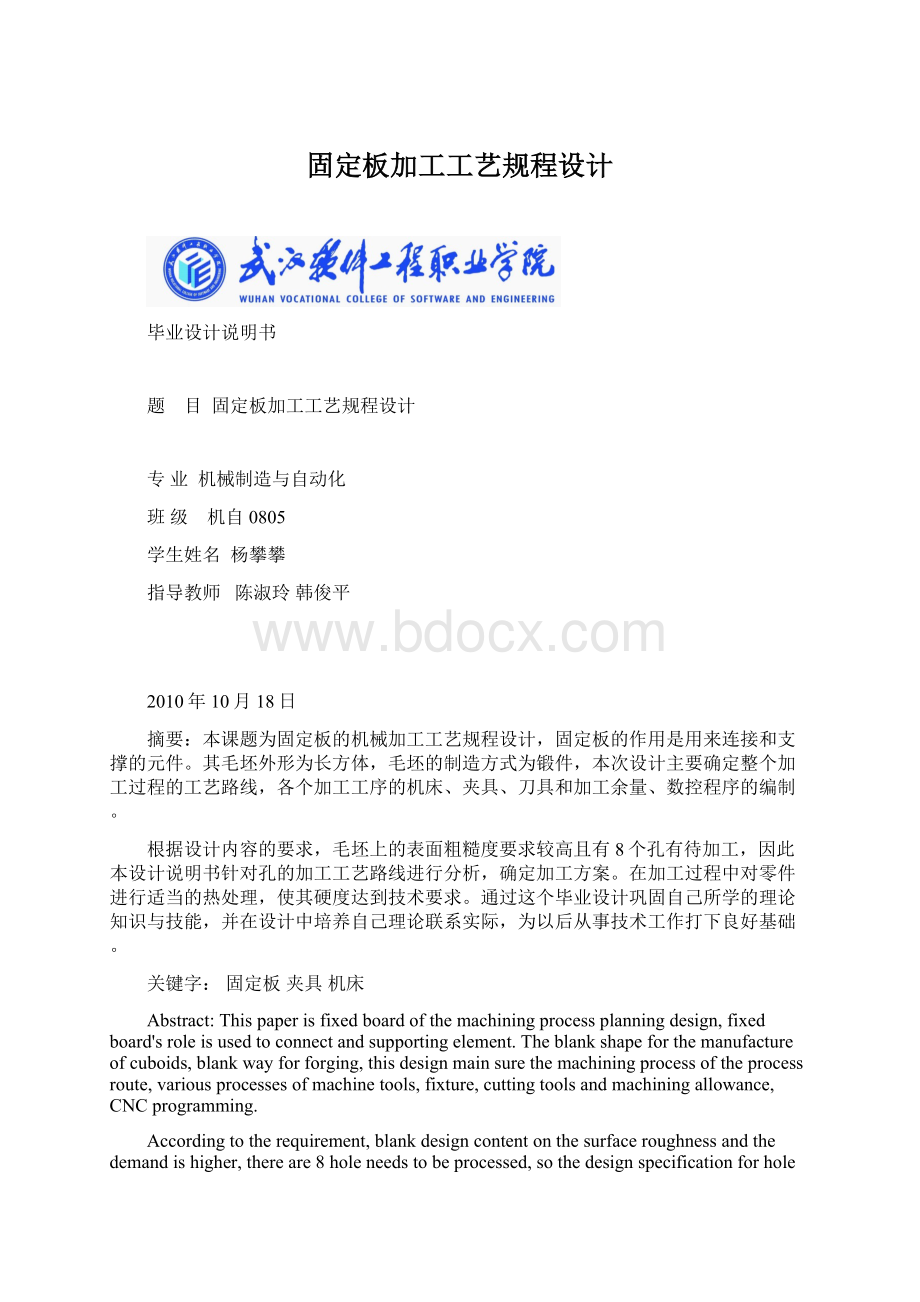
固定板加工工艺规程设计
毕业设计说明书
题目固定板加工工艺规程设计
专业机械制造与自动化
班级机自0805
学生姓名杨攀攀
指导教师陈淑玲韩俊平
2010年10月18日
摘要:
本课题为固定板的机械加工工艺规程设计,固定板的作用是用来连接和支撑的元件。
其毛坯外形为长方体,毛坯的制造方式为锻件,本次设计主要确定整个加工过程的工艺路线,各个加工工序的机床、夹具、刀具和加工余量、数控程序的编制。
根据设计内容的要求,毛坯上的表面粗糙度要求较高且有8个孔有待加工,因此本设计说明书针对孔的加工工艺路线进行分析,确定加工方案。
在加工过程中对零件进行适当的热处理,使其硬度达到技术要求。
通过这个毕业设计巩固自己所学的理论知识与技能,并在设计中培养自己理论联系实际,为以后从事技术工作打下良好基础。
关键字:
固定板夹具机床
Abstract:
Thispaperisfixedboardofthemachiningprocessplanningdesign,fixedboard'sroleisusedtoconnectandsupportingelement.Theblankshapeforthemanufactureofcuboids,blankwayforforging,thisdesignmainsurethemachiningprocessoftheprocessroute,variousprocessesofmachinetools,fixture,cuttingtoolsandmachiningallowance,CNCprogramming.
Accordingtotherequirement,blankdesigncontentonthesurfaceroughnessandthedemandishigher,thereare8holeneedstobeprocessed,sothedesignspecificationforholemachiningprocessoftherouteisanalyzed,anddeterminetheprocessingschemes.Inthemachiningprocessforpartsproperheattreatment,makeitshardnessoftechnicalrequirements.Throughthegraduationdesignconsolidatetheirtheoriesknowledgeandskills,andcultivatethemselvesinthedesigntheorywithpractice,isengagedintechnicalworkforlaterandlaythegoodfoundation.
Keywords:
Retainingplatefixturemachine
第一章:
零件的工艺审查
1.1零件图样的审查
本题图中尺寸都已给出,由图中给出的尺寸知道零件的形状,各个孔的尺寸和配合也都给出各个表面粗糙度也有要求,但形位公差要求给出不具体,因此综合分析后,应在φ16mm与φ12mm的孔之间加一个同轴度要求可取0.06μm,中心孔φ60mm与A面应该有一个垂直度要求取0.01μm,A、B面都要有平面度要求取0.04μm。
图1-1固定板
材料HT200。
硬度要求:
235-265HBS
1.2零件选材及技术条件的审查
题目中给出用HT200作为原材料,但硬度要求达到235~265HBS,查机械制造基础下表:
表1-1常用灰铸铁的牌号、力学性能及应用
类别
牌号
铸件壁厚
HBS
用途
铁素体
灰铸铁
HT100
2.5~10
10~20
20~30
30~50
110~166
93~140
87~131
82~122
适用于载荷小、对摩擦和磨损无特殊要求的不重要铸件,如防护罩、盖、油盘、手轮、支架、底板、重锤、小手柄等
铁素体—珠光体灰铸铁
HT150
2.5~10
10~20
20~30
30~50
137~205
119~179
110~166
105~157
承受中等载荷的铸件,如机座、支架、箱体、刀架、床身、轴承座、工作台、带轮、端盖、泵体、阀体、管路、电机座等
珠光体
灰铸铁
HT200
2.5~10
10~20
20~30
30~50
157~236
148~222
134~200
129~192
承受较大载荷和要求一定的气密性或耐蚀性等较重要铸件,如汽缸、齿轮、机座、飞轮、床身、气缸体、气缸套、活塞、齿轮箱、刹车轮、联轴器盘、中等压力阀体等
HT250
4.0~10
10~20
20~30
30~50
175~262
164~247
157~236
150~225
孕育铸铁
HT300
10~20
20~30
30~50
182~272
168~251
161~241
承受高载荷、耐磨和高气密性重要铸件,如重型机床、剪床、机座、机架,高压液压件,活塞环,受力较大的齿轮、凸轮、衬套,大型发动机的曲轴、气缸体、缸套、气缸盖等
HT350
10~20
20~30
30~50
199~298
182~272
171~257
为了满足所需要的硬度,材料换成HT350,其余技术要求都符合要
1.3零件图和零件的立体图
零件图如下:
用AutoCAD绘制零件的平面图,标注零件基本尺寸、表面粗糙度、形位公差。
图1-2零件图
零件立体图用Pro/E3.0绘制:
图1-3零件立体图第二章:
毛坯制造方法和尺寸的确定
第二章:
毛坯制造方法和尺寸的确定
2.1毛坯制造方法的确定
固定板是连接件,要求有一定的硬度,零件的外形尺寸为正方体用于单件小批量生产,可选择自由锻的方法制造毛坯。
2.2毛坯机械加工余量的确定
2.2.1机械加工余量计算
灰铸铁自由锻件机械加工余量可用机械加工工艺手册表3.1-36所列计算公式计算。
灰铸铁毛坯铸造时中间可以有孔,与表3.1-36中所列图相近。
所以取其计算公式
A=0.18H0.8B0.55H为零件厚度B为零件宽度
A=0.18H0.8B0.55=0.18×150.8×1600.55=0.18×1.72×16.30≈5.046mm
0.5A=0.5×5=2.5mm
0.75A=0.75×5=3.85mm
2.2.2确定毛坯加工余量
根据以上计算毛坯宽、高方向尺寸都留有余量A,中间孔留有机械加工余量1.5A。
如下图所示:
图2-1毛坯余量图
2.2.3确定毛坯尺寸
灰铸铁锻件毛坯基本尺寸:
长160mm、宽160mm、高25mm中间孔直径
为52.5mm
图2-2毛坯图
2.3毛坯极限偏差确定
2.3.1质量m、复杂系数S、材质系数M的计算
铸件的质量:
m=[162-π62]×1.5×7.35=1576.13g=1.576kg
加工精度
零件表面的一般加工余量精度为F,即尺寸公差等级为IT7~IT9。
锻件形状复杂系数S=
=
≈0.798W1为锻件重量,W2为相应锻件外轮廓包容体的重量。
S=0.798查属于S1范围内,所以形状系数为S1
锻件材质系数:
灰铸铁含碳Vc=2.7%~3.6%,合金元素最高总的质量分数大于3%,属于M2级。
2.3.2确定毛坯各偏差
根据毛坯的质量m,材料系数M2,形状复杂S1查机械加工工艺手册表3.1-37如下图:
表2-1毛坯各尺寸的极限偏差
铸件尺寸(mm)
上下偏差(μm)
165
+1.5
-0.7
15
+1.4
-0.6
φ52.5
+1.5
-0.7
图2-3毛坯图
2.4确定毛坯的热处理
灰铸铁拥有高强度、高耐磨性,但铸造性能差,需进行加工前的退火处理,改善其加工性能和提高塑性、韧性。
毛坯在制造和切削加工的过程中会改变它的力学性能,而淬火可以获得需要的力学性能,淬火因其硬度高且不宜切削一般安排在精加工阶段的磨削加工之前,因此在粗加工后安排一次淬火。
加工前:
退火粗加工后:
淬火
第三章:
固定板工艺路线设计
3.1定位基准的选择
3.1.1设计基准的选择
零件的设计基准为中心孔的轴线,A面试B面对设计基准,或B面试A面的设计基准,他们互为基准。
3.1.2粗、精基准的选择
在选择定位基准时,从保证工件精度要求出发,选择定位基准的顺序是从精基准到粗基准。
零件为加工之前,只能以毛坯面作为定位基准,选择中心孔的中心线为精基准加工A、B面,孔的轴心线又为设计基准,符合基准重合原则。
加工各个孔的时候也是以中心孔的中心线为精基准,定位时也是用孔的中心线作为定位基准,避免因基准不重合引起的误差。
3.2工艺路线的拟定
3.2.1固定板A、B面加工方法的确定
固定板A、B面表面粗糙度为6.3μm,查下表壳选用第3个方案
表3-1平面加工方法适用范围
序号
加工方法
经济精度(IT)
表面粗糙度
Ra(μm)
1
粗铣
12~14
12.5~6.3
2
粗铣—半精铣
11~12
6.3~1.6
3
粗铣—精铣
7~9
6.3~1.6
3.2.2固定板上孔加工方法的确定
零件上孔的加工方法查下图:
表3-2内圆加工方法的适用范围
序号
加工方法
经济精度
表面粗糙度
Ra(μm)
适用范围
1
钻
12~13
12.5
孔径<15~20mm
2
钻—铰
8~10
3.2~1.6
3
钻—粗铰—精铰
7~8
1.6~0.8
4
钻—扩
10~11
12.5~6.3
孔径>15~20mm
5
钻—扩—粗铰—精铰
7~8
1.6~0.8
6
钻—扩—铰
8~9
3.2~1.6
7
粗扩—精扩
9~10
3.2~1.6
毛坯有铸孔或锻孔的未淬火钢及铸铁
8
粗镗—精扩—精铰
7~8
1.6~0.8
由上表可知:
φ60的孔表面粗糙度为0.8μm,选用第8种方案
φ12的孔表面粗糙度为0.8μm,选用第3种方案
φ16的孔表面粗糙度为12.5μm,选用第4种方案
M16的螺纹孔表面粗糙度无具体要求加工路线为:
钻-攻螺纹
综上所述固定板的加工工艺过程:
1.备料—2.自由锻—3.退火—4.铣A、B面—5.时效—6.加工φ60的中心孔—7.加工φ12的中心孔—8.加工φ16的孔—9.加工M16螺纹孔—10.去毛刺—11.终检
3.3加工顺序的安排
表3-3零件加工工序
序号
加工部位
加工工艺路线
备注
1
备料
—
材料:
HT350
硬度:
235-265HBS
2
自由锻
—
长165mm
宽165mm
高15mm
3
退火
—
提高塑性、韧性
4
铣A、B面
粗铣—精铣
Ra≤6.3
5
时效
—
消除残余应力
6
加工φ60的孔
粗镗—精扩—精铰
Ra≤0.8
7
钻φ12的孔
钻—粗铰—精铰
Ra≤0.8
8
钻φ16的孔
钻—扩
Ra≤12.5
9
攻M16的螺纹孔
钻-攻螺纹
—
10
去毛刺
—
锉刀
11
终检
按图纸要求或检查卡检验
—
第四章:
机械工序设计
4.1机床的选择
工序4和6在同一个铣床上加工,零件最大外轮廓尺寸为165mm,A、B平面度要求0.04μm,表面粗超度值6.3μm,查机械加工工艺师手册11-4,可选择卧式升降台铣床X6025A
工序7、8和9在同一台机床上加工,因为φ12的孔精度要求较高,所以选择一台加工中心完成加工。
查机械加工工艺师手册表7-9可以选择MCV450型立式加工中心。
4.2工艺装配的选择
4.2.1夹具的选择
在铣床上加工选择通用夹具平口钳、固定板就可以满足加工要求。
图4-2平口钳图4-3固定板
在加工中心加工孔为通孔,定位基准为已经加工好的孔的轴心线,先择专用夹具定位,如下图所示:
图4-3专用夹具
4.2.2刀具的选择:
工序4选择可转位面铣刀6C2K。
工序6选择单刃镗刀、高速钢锥柄扩孔钻、镶齿套式机用铰刀。
工序7选择直柄麻花钻、锥柄机用铰刀。
工序8选用指柄麻花钻、整体高速刚锥柄扩孔钻。
工序9选择直柄麻花钻、丝锥。
表4-1各工序选择的刀具及直径
工序
加工部位
所选刀具
直径(mm)
4
铣A、B面
面铣刀6C2K
φ170
6
加工φ60孔
单刃镗刀
—
高速钢锥柄扩孔钻
φ59.5
镶齿套式铰刀
φ60
7
钻φ12的孔
直柄麻花钻
φ11
锥柄机用铰刀
φ11.95、φ12
8
钻φ16的孔
直柄麻花钻
φ15
整体高速钢锥柄扩孔钻
φ16
9
攻M16的螺纹孔
直柄麻花钻
φ14
丝锥
φ16
4.2.3量具的选择
量具的选择主要根据生产类型和加工精度来选择,在单件小批量生产时应尽量采用通用量具,本题选用游标卡尺测外轮廓尺寸,用粗糙度仪测A、B面表面粗糙度值,用量规测孔的直径。
图4-4游标卡尺
表4-2量规尺寸参照(mm)
基本尺寸
D1
H
B
φ60
116
100
10
φ16
132
114
10
φ12
138
122
10
4.2.4机械加工余量及工序尺寸的确定
零件多次加工的工序尺寸与加工余量有关,根据上述数据得出固定板上孔的总加工余量,应将总的加工余量分为各个工序的加工余量。
然后由后向前算出工序尺寸,中间工序的表面粗糙度按机械加工工艺手册表3.2-9查出。
加工φ60mm的孔粗镗到φ57mm加工余量为4.5mm,精扩到φ59.5mm加工余量2.5mm,最后精铰到φ60mm加工余量0.5mm。
加工φ12mm的孔先钻φ11mm,然后粗铰刀φ11.95mm加工余量0.95mm,再精铰到φ12mm加工余量0.5mm。
加工φ16mm的孔先钻到φ15mm,再扩孔道φ16mm加工余量1mm。
M16的螺纹孔钻到φ14mm在攻螺纹。
铣A、B面时先粗铣1.7mm,在精铣0.8mm。
表4-3工序的余量及尺寸
加工部位
工序余量(mm)
工序尺寸(mm)
表面粗糙度Ra(μm)
扩
粗铰
精铰
扩
粗铰
精铰
扩
粗铰
精铰
φ12
—
—
0.95
0.05
φ11
—
φ11.95
φ12
25
—
6.3
0.8
φ16
4
1
—
—
φ15
φ16
—
—
25
12.5
—
—
φ60
6.5
0.5
—
0.5
φ59
φ59.5
—
φ60
12.5
6.3
—
0.8
A面
B面
粗铣
精铣
粗铣
精铣
粗铣
精铣
1.7
0.8
—
—
12.5
6.3
攻孔M16
钻
钻
钻
—
φ14
25
第五章:
确定切削用量
5.1确定A、B面的铣削用量
本工序A、B面的粗铣和精铣,选用铣床X6025A,工作台尺寸125×500(mm),主轴转速50~1250r/mm,电动机功率2.2KW。
铣刀选择面铣刀,直径φ100,中齿硬质合金刀,齿数为6。
由机床功率2.2KW,查表2.1-71(机械加工工艺手册第二版)的粗铣时每齿进给量af=0.15~0.30mm/齿,取af=0.2mm/齿。
精铣时根据表面粗超度Ra=6.3μm查的每圈进给量af=1.2~2.7mm/r。
5.1.1粗铣时铣削用量的计算
粗铣af=0.2mm/齿
铣刀磨钝标准查表2.1-75铣刀最大后刀面磨损为2mm,由铣刀直径D=100mm查的T=180min。
(1)铣刀速度V的确定
根据表2.1-77中公式:
V=
查表2.1-77得:
Cv=203,pv=0.2,xv=0.15,yv=0.35,uv=0.2,pv=0,af=0.2,m=0.32,d=100,aP=1.7,aW=100,z=6,kv=1
带入得V=76.8m/min
n=
=224.6r/min
取n=250r/min
实际切削速度V=
=78.5m/min
工作台进给速度Vf=fn=afzn=150mm/min
5.1.2机床功率校验
根据公式Pm=
,Fc=
查表2.1-78得CF=534,XF=0.9,yf=0.74,UF=1.1,WF=0,qF=1,
=1,d=100mm,n=250r/min,V=78.5m/min
带入Fc=182.9N,Pm=0.24KW
铣床主电动机功率为2.2KW,故所选切削用量可以采用,所确定粗铣A、B面对切削用量:
V=78.5m/min,n=250r/min
Vf=150mm/min,af=0.2mm/齿
5.1.3精铣时切削用量的计算
精铣时每转进给1.2mm,Z=6,所以每齿进给0.2mm。
与粗铣时af一样。
计算过程与粗铣时计算过程一样。
所以精铣时切削用量:
V=78.5m/min,n=250r/min
Vf=150mm/min,af=0.2mm/齿
5.2确定工序7、8、9中钻孔的钻削用量
加工中心MCV450主轴转速60~3000r/min,主电动机功率3.7KW,快速进给10m/min。
5.2.1确定进给量
工序7、8、9中都选用高速钢钻头,钻头直径分别φ1=11mm、φ2=15mmφ3=15mm,根据表3.4-1查出f1=0.31~0.39mm/rf2=f3=0.37~0.45mm/r。
由于孔深与孔径比I1=1.36I2=0.33I3=1
都取1,钻孔深度小于孔径的3倍。
根据表3.4-1钻孔强度所允许的进给量f1=1.0mm/rf2=1.22mm/r远远大于f1、f2、f3,故选f1、f2、f3可用,f1=0.35mm/rf2=f3=0.4mm/r。
5.2.2确定切削速度、V轴向力F、转矩T以及切削功率Pm
查表3.4-8得V=
Cv=9.4,xv=0.25,yv=0.4
uv=0.2,m=0.125,T=60min,kv=1
V1=15.6m/min,V2=V3=14.8m/min
查表3.4-10
F=
F1=1995N,F2=3032N
T1=10.8N·m,T2=T3=22.3N·m
P=
P1=0.51km,P2=P3=0.72km
由于实际加工条件与上表给出的条件不完全相同,故应对结果进行修正,由表3.4-9,切削速度的修正系数Kmv=0.7。
V1=11m/min,V2=V3=10.6m/min
公式n=
n1=320r/min,n2=n3=225r/min
实际切削速度V1=11m/min,V2=V3=10.6m/min
由表3.4-11切削力及转矩的修正系数KmF=Kmm=1
因此切削力:
F1=1995N,F2=F3=3026N
5.2.3校验机床功率
Pm=Pm×(V实/V)KMM
P1=0.51KW,P2=P3=0.73KW
P1、P2、P3、都小于机床电动机功率,故选用的切削用量可用,即:
工序7中:
f1=0.35mm/r,n1=320r/min,V1=15.6m/min
工序8、9中:
f2=f3=0.4mm/r,n2=n3=225r/min
V2=V3=14.8m/min
5.3确定工序6工序8中扩孔的切削用量
工序中都选用高速钢扩孔钻,直径分别是φ59.5mmφ16mm
5.3.1确定进给量f
根据表3.4-5取f1=0.7×(1.3-1.5)=0.91-1.05mm/r
f2取0.5mm/r
f1=1mm/r,f2=0.5mm/r
5.3.2确定切削速度V及N
查表3.4-7刀具寿命T1=170min,T2=60min
V=
查表计算得:
V1=18.1m/min,V2=10.3m/min
又n=
带入V1、V2得
n1=96.9r/min,n2=205r/min
查机床手册n1取100r/min,n2取275r/min
实际扩孔速度V1=18.7m/min,V2=10.3m/min
即工序6的扩孔用量:
f1=1mm/r,V1=18.1m/min,n1=96.9r/min
工序8的扩孔用量:
f2=0.5mm/r,V2=10.3m/min,n2=205r/min
5.4确定工序6工序7铰孔切削用量
工序6中选镶齿套式铰刀φ60mm
工序中选镶齿锥柄机用铰刀φ11.95mm和φ12mm
5.4.1确定进给量f
根据表3.4-6查出
f1=2.6~5mm/r,f2=f3=1~2mm/r
由表下注2注3取:
f1=4mm/r,f2=2mm/r,f3=1.5mm/r
5.4.2确定切削速度V及N
查表3.4-40取
V1=4.8m/min,V2=6.3m/min,V3=10m/min
切削速度修正系数查表3.4-9
KMv=0.7,Ktv=1
V=V·KMv·Ktv
故V1=3.4m/min,V2=6.23m/min,V3=7m/min
又n=
带入V1、V2、V3得
n1=18r/min,n2=165.3r/min,n3=185.7r/min
取n1=60r/min,n2=170r/min,n3=200r/min
实际切削速度
V1=11.3m/min,V2=6.4m/min,V3=7.5m/min
即确定的铰孔用量:
工序6:
f1=4mm/r,V1=11.3m/min,n1=60r/min
工序7粗铰:
f2=2mm/r,V2=6.4m/min,n2=170r/min
工序7精铰:
f3=1.5mm/r,V3=7.5m/min,n3=200r/min
5.5各工序的切削用量
表6-1各工序切削用量
工序
加工方法
切削用量
4
粗铣A、B面
V=78.5m/minn=250r/min
Vf=150mm/minaf=0.2mm/齿
4
精铣A、B面
V=78.5m/minn=250r/min
Vf=150mm/minaf=0.2mm/齿
6
扩φ60孔
f=1mm/rV=18.1m/minn=96.9r/min
6
精铰φ60孔
f=4mm/rV=11.3m/minn=60r/min
7
钻φ12的孔
f=0.35mm/rV=15.6m/minn=320r/min
7
粗铰φ12的孔
f=2mm/rV=6