注塑模设计说明书塑料盒.docx
《注塑模设计说明书塑料盒.docx》由会员分享,可在线阅读,更多相关《注塑模设计说明书塑料盒.docx(20页珍藏版)》请在冰豆网上搜索。
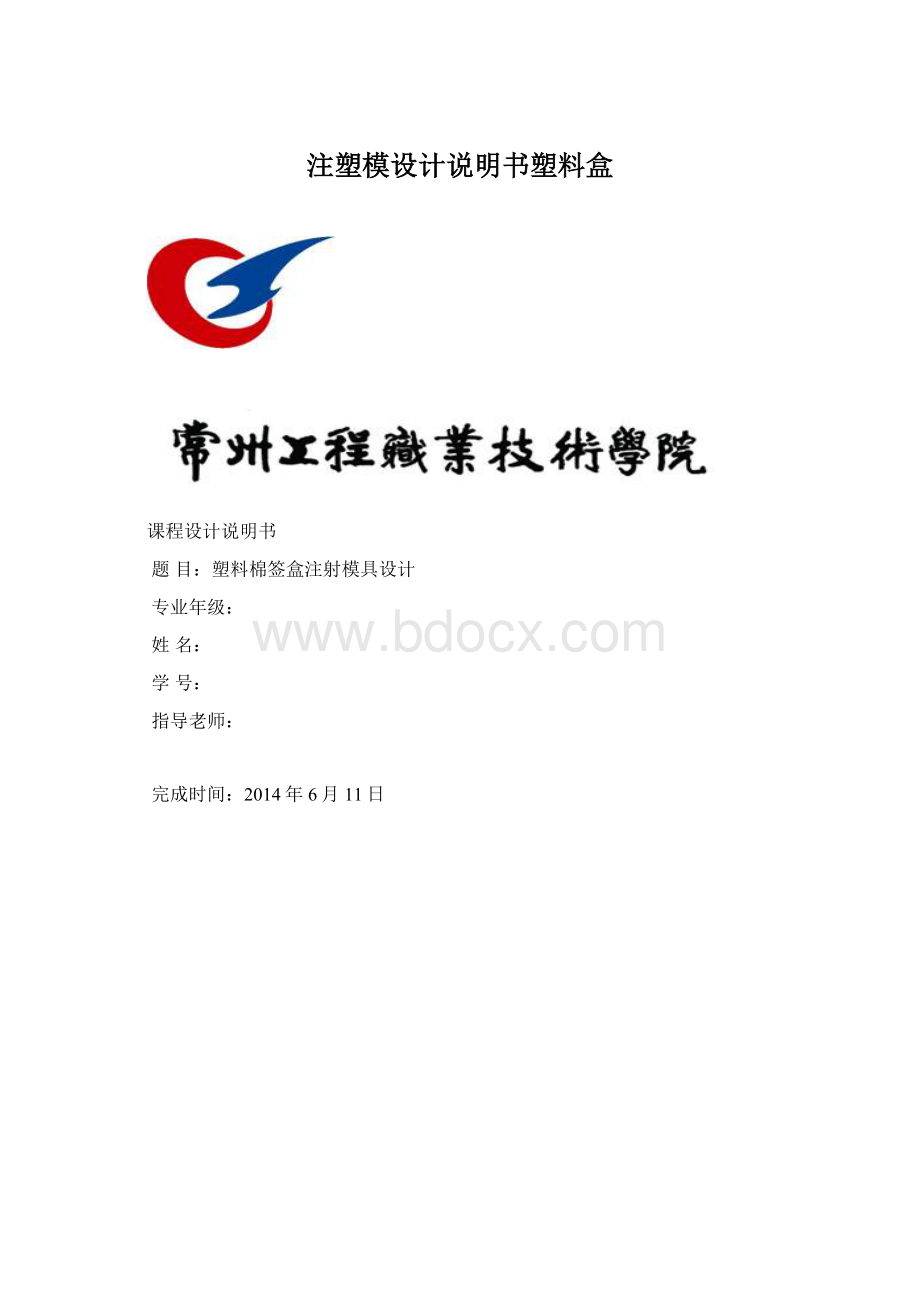
注塑模设计说明书塑料盒
课程设计说明书
题目:
塑料棉签盒注射模具设计
专业年级:
姓名:
学号:
指导老师:
完成时间:
2014年6月11日
1.塑件的工艺分析
1.1塑件的成型工艺性分析
塑件如图1、图2所示。
图一
图2
产品名称:
棉签盒盖
产品材料:
PS
产品数量:
大批量生产
塑件尺寸:
如图1所示
塑件重量:
V=35.735cm3m=ρV=1.05×35.735=37.521g
塑件颜色:
白色
塑件要求:
塑件外侧表面光滑,下端外沿不允许有浇口痕迹。
塑件允许最大脱模斜度0.5°
1.2.1塑件材料PS的使用性能
材料品种
结构特点
使用温度
化学稳定性
性能特点
成型特点
PS
由苯乙烯单体经自由基缩聚反应合成的聚合物
长期使用温度0~70℃
化学稳定性良好,不耐苯.汽油等有机溶剂.会被强酸强碱腐蚀在受到紫外光照射后易变色
电绝缘性(尤其高频绝缘性)优良,无色透明,透光率仅次于有机玻璃,强度一般,但质脆,易产生应力脆裂,着色性耐水性良好。
1.无定形料,吸湿小,不须充分干燥,不易分解,但热膨胀系数大,易产生内应力.流动性较好,可用螺杆或柱塞式注射机成型.
2.宜用高料温,高模温,低注射压力,延长注射时间有利于降低内应力,防止缩孔.变形.
3.可用各种形式浇口,浇口与塑件圆弧连接,以免去处浇口时损坏塑件.脱模斜度大,顶出均匀.塑件壁厚均匀,最好不带镶件,如有镶件应预热
1.、结构特点:
PS一般为头尾结构,主链为饱和碳链,侧基为共轭苯环,使分子结构不规整,增大了分子的刚性,使PS成为非结晶性的线型聚合物。
由于苯环存在,PS具有较高的Tg(80~82℃),所以在室温下是透明而坚硬的,由于分子链的刚性,易引起应力开裂。
聚苯乙烯无色透明,能自由着色,相对密度也仅次于PP、PE,具有优异的电性能
2、热性能:
最高工作温度为60~80℃。
当加热至Tg以上,PS转变为高弹态,且保持这种状态在较宽的范围内,这就使其热成型提供方便。
PS的热变形温度为70~80℃,脆化温度为-30℃,PS在高真PS的分子量过高,加工困难,所以通常聚苯乙烯的分子量为5~20万。
PS的机械性能,随温度升高,刚性(弹性模量、抗拉强度、冲击强度等下降,而断裂伸长率较大。
PS的透明性好,透光率达88~92%,仅次于丙烯酸类聚合物,折射率为1.59~1.60。
故可用作光学零件,但它受阳光作用后,易出现发黄和混浊。
PS有主要缺点是性脆和耐热性低。
空和330~380℃下剧烈降解。
3、机械性能:
PS的分子量过高,加工困难,所以通常聚苯乙烯的分子量为5~20万。
PS的机械性能,随温度升高,刚性(弹性模量、抗拉强度、冲击强度等下降,而断裂伸长率较大。
PS的透明性好,透光率达88~92%,仅次于丙烯酸类聚合物,折射率为1.59~1.60。
故可用作光学零件,但它受阳光作用后,易出现发黄和混浊。
PS有主要缺点是性脆和耐热性低。
4、优异、持久的隔热保温性:
挤塑板,导热系数为0.028w/mk,具有高热阻、低线性膨胀率的特性。
其导热系数远远低于其他的保温材料如:
EPS板、发泡聚氨酯、保温砂浆、水泥珍珠岩等。
同时由于本材料具有稳定的化学结构和物理结构,确保本材料保温性能的持久和稳定5、优越的抗水、防潮性:
挤塑板具有紧密的闭孔结构。
聚苯乙烯分子结构本身不吸水,板材的正反面又都没有缝隙,因此,吸水率极低,防潮和防渗透性能极佳。
5、高强度抗压性:
挤塑板由于发泡结构紧密相连且壁间无缝隙,所以其抗压强度极高,即使长时间水泡仍维持不变。
因此用作泊车平台、机场跑道、高速公路等领域能受到良好的抗冲击性。
6、防腐蚀、经久耐用性:
一般的硬质发泡保温材料使用几年后易产生老化,随之导致吸水造成性能下降。
而挤塑板因具有优异的防腐蚀、防老化性、保温性,在高水蒸汽压力下,仍能保持其优异性能,使用寿命可达到30-40年。
7、轻质、高硬度:
挤塑板完全的闭孔发泡结构形成轻质,而均匀的蜂窝结构造成高硬质,但又不像聚氨酯发泡、酚醛发泡那样发脆,因此不易破损,不仅搬运、安装轻便,切割容易,用作屋顶保温时不会影响结构的承受能力。
8、高质量环保型:
挤塑板不会发生分解和霉变,不会有有害物质挥发,化学性质稳定。
同时在生产过程中,利用环保型原料,不产生有害气体,没有废水产生,所形成的固体下脚料,可回收处理再利用,是高质量环保型产品。
1.2.2塑件材料PS的加工特性
(1)典型应用范围:
产品包装、家庭用品(餐具、托盘等)、电气(透明容器、光源散射器、绝缘薄膜等)。
(2)注塑工艺及模具条件
②干燥处理除非贮存不当,通常不需要干燥处理。
如需干燥,为80℃、2~3h。
②熔化温度180~280℃。
对于阻燃型材料其上限为250℃。
②模具温度40~50℃。
②注射压力20~60MPa。
②注射速度建议使用快速注射
(3)化学和物理性能大多数商业用的PS(聚苯乙烯)都是透明的非结晶材料。
PS据用非常好的几何稳定性、热稳定性、光学透过特性、电绝缘特性以及很微小的吸湿倾向。
它能够抵抗水、稀释的无机酸,但能够被强氧化物如浓硫酸所腐蚀,并且会在一些哟基溶剂中发生溶胀变形。
收缩率一般在0.4%~0.7%。
1.3塑件的成型工艺参数确定
材料名称
聚苯乙烯
纯
注射机类型
柱塞式
预热和干燥
温度t/℃
时间23
80~85
2~3
料筒温度t/℃
后段
中段
前段
140~160
170~190
喷嘴温度
模具温度t/℃
32~65
注射压力p/MPa
60~110
注射时间
高压时间
冷却时间
总周期
15~45
0~3
15~60
40~120
螺杆转速η/(r.min-1)
48
方法
温度t/℃
时间τ/h
红外线灯、烘箱
70
2~4
说明
丁苯橡胶改性的聚苯乙烯的成型条件与上相似
2模具的基本结构及模架选择
2.1模具的基本结构
2.1.1确定成型方法
塑件采用注射成型法生产。
为保证塑件表面质量,使用点浇口成型,因此模具应为双分型面注射模(三板式注射模)。
2.1.2型腔布置
塑件形状较简单,重量较轻,生产批量较大。
所以应使用多型腔注射模具。
考虑到塑件尺寸60x90mm,且较为规则,所以模具采用一模二腔、平衡布置。
这样模具尺寸较小,制造加工方便,生产效率高,塑件成本较低。
其布置如图2所示
图2型腔布置
2.1.3确定分型面
塑件分型面的选择应保证塑件的质量要求,本实例中塑件的分型面有多种选择,如图3所示。
图3(a)的分型面选择在轴线上,这种选择会使塑件表面留下分型面痕迹,影响塑件表面质量。
同时这种分型面也使侧向抽芯困难;图3(b)的分型面选择在下端面,这样的选择使塑件的外表面可以在整体凹模型腔内成型,塑件大部分外表面光滑,仅在侧向抽芯处留有分型面痕迹。
同时侧向抽芯容易,而且塑件脱模方便。
因此塑件选择如图3(b)所示的分型面。
图3分型面选择
2.1.4选择浇注系统
塑件采用点浇口成型,其浇注系统如图4所示。
点浇口直径为Φ1mm,点浇口长度为1mm,头部球R1mm。
分流道采用半圆截面流道,其半径R为3.8mm。
主流道为圆锥形,锥角α为8˚,上部直径与注射机喷嘴相配合,下部直径Φ8mm。
图4点浇口浇注系统
2.1.5确定推出方式
由于塑件形状为圆壳形而且壁厚较薄,使用推杆推出容易在塑件上留下推出痕迹,不宜采用。
所以选择推件板块出机构完成塑件的推出,这种方法结构简单、推出力均匀,塑件在推出时变形小,推出可靠。
2.1.6斜滑块机构
塑件的内侧面有0.3x1的长方体,因此模具应有斜滑块机构,由于抽出距离较短,抽出力较小,所以采用斜滑块机构,滑块装在推杆上。
2.1.7模具的结构形式
模具结构为双分型面注射模,如图5所示。
图5双分型面注射模模具结构
1—拉杆2—导套3—定模板(中间板)4—螺钉5—推件块
6—动模板7—支承板8—推杆固定板9—垫块10—动模座板
11—导柱12—导套13—导套14—定模座板15—导套
16—导柱17—限位螺钉
2.1.8选择成型设备
“注射机的选用”可参考《简明塑料模具设计手册》P133,P128表3-4
选用XS-Z-60型号注塑机,其有关参数为:
型号
标称注射量/㎝3
柱塞直径/mm
注射压力/Mpa
注射时间/s
注射方式
合模力/N
最大成型面积/cm2
模板最大行程/mm
XS-Z-60
60
38
122
0.7
柱塞式
5×105
130
180
模板最大厚度/mm
模板最小厚度/mm
模板尺寸/mm
合模方式
推出形式两侧推出时中心距/mm
电动机功率/KW
喷嘴
定位圈尺寸/mm
机器外形尺寸/m
球半径/mm
孔直径/mm
200
70
200×315
液压-机械
两侧推出
11
12
4
55
4.0×1.4×1.6
2.2选择模架
2.2.1模架的结构
可参考《简明塑料模具设计手册》P418表10-1—10-6
模架的结构如图6所示。
图6模架
2.2.2模架安装尺寸校核
模具外型尺寸为,长301mm、宽260mm、高216mm,小于注射机拉杆间距和最大模具厚度,可以方便地安装在注射机上。
3模具结构、尺寸的设计计算
3.1模具结构设计计算
3.1.1型腔结构
见装配图所示,由中间板所构成,便于脱掉废料
3.1.2型芯结构。
见装配图所示,型芯由顶块和斜型芯组成,便于组装和脱离,侧边有滑套,便于配合。
型芯中心开有冷却水孔,用来强制冷却型芯。
3.1.3滑块结构
见装配图。
3.1.4模具的导向结构
为了保证模具的闭合精度,模具的定模部分与动模部分之间采用导柱1和导套2导向定位。
推件块18上装有滑套6,推出时,滑套6在导柱1上运动,保证了推件块的运动精度。
定模座板上装有导柱30,为点浇口凝料推板24和定模板4的运动导向。
3.1.5脱模力计算F=【8δ2ESlcosφ(f-tanφ)】/(1-u)k2
δ=δ2=1S收缩率=0.6%E模量=3000Mpal=90f静摩擦系数=0.2
φ脱模斜度=0.5°u泊松比=0.35
F脱模力=3813N
3.2模具成型尺寸设计计算
可参考《简明塑料模具设计手册》P110表2-55
取PS的平均成型收缩率为0.6%,塑件未注公差按照SJ1372中4级精度公差值选取。
塑件尺寸如图1所示。
3.2.1型腔径向尺寸
模具最大磨损量取塑件公差的1/6;模具的制造公差δz=Δ/3;取x=0.75。
1)
→
2)
→
3.2.2型腔深度尺寸
模具最大磨损量取塑件公差的1/6;模具的制造公差δz=Δ/3;取x=0.5。
1)
→
3.2.3型芯径向尺寸
模具最大磨损量取塑件公差的1/6;模具的制造公差δz=Δ/3;取x=0.75。
1)
→
2)
→
3.2.4型芯高度尺寸
模具最大磨损量取塑件公差的1/6;模具的制造公差δz=Δ/3;取x=0.5。
1)
→
3.3模具加热、冷却系统的计算
3.3.1模具加热
一般生产ABS材料塑件的注射模具不需要外加热。
3.3.2模具冷却
模具的冷却分为两部分,一部分是型腔的冷却,另一部分是型芯的冷却。
型腔的冷却是由在定模板(中间板)上的两条ф10mm的冷却水道完成
图7定模板冷却水道
型芯的冷却如图8所示,在型芯内部开有ф16mm的冷却水孔,中间用隔水板2隔开,冷却水由支承板5上的ф10mm冷却水孔进入,沿着隔水板的一侧上升到型芯的上部,翻过隔水板,流入另一侧,再流回支承板上的冷却水孔。
然后继续冷却第二个型芯,最后由支承板上的冷却水孔流出模具。
型芯1与支承板5之间用密封圈3密封。
图8型芯的冷却
1—型芯2—隔水板3—密封圈4—动模板(型芯固定板)5—支承板
4.模具主要零件图
4.1模具定模板(中间板)零件图
定模板(中间板)零件图如图9所示。
图9定模板(中间板)零件图
4.2模具动模板(型芯固定板)零件图
动模板(型芯固定板)零件图如图11所示。
5模具总装图及模具的装配、试模
5.1模具总装图
图12为模具的总体装配图。
图12模具图
5.2模具的安装试模
试模是模具制造中的一个重要环节,试模中的修改、补充和调整是对于模具设计的补充。
5.2.1试模前的准备
试模前要对模具及试模用的设备进行检验。
模具的闭合高度,安装与、于注射机的各个配合尺寸、推出形式、开模距、模具工作要求等要符合所选设备的技术条件。
检查模具各滑动零件配合间隙适当,无卡住及紧涩现象。
活动要灵活、可靠,起止位置的定位要正确。
各镶嵌件、紧固件要牢固,无松动现象。
各种水管接头、阀门、附件、备件要齐全。
对于试模设备也要进行全面检查,即对设备的油路、水路、电路、机械运动部位、各操纵件和显示信号要检查、调整,使之处于正常运转状态。
5.2.2模具的安装及调试
模具的安装是指将模具从制造地点运至注射机所在地,并安装在指定注射机的全过程。
模具安装在注射机上要注意以下方面:
1)模具的安装方位要满足设计图样的要求。
2)模具中有侧向滑动结构时,尽量使其运动方向为水平方向。
3)当模具长度与宽度尺寸相差较大时,应尽可能使较长的边与水平方向平行。
4)模具带有液压油路接头、气路接头、热流道元件接线板时,尽可能放置在非操作一侧,以免操作不方便。
模具在注射机上的固定多采用螺钉、压板的形式,如图13所示。
一般采用4-8块压板,对称布置。
图13模具固定
1—压板2—螺钉3—模具4—注射机模板
模具安装于注射机上之后,要进行空循环调整。
其目的在于检验模具上各运动机构是否可靠、灵活,定位装置是否能够有效作用,要注意以下方面:
1)合模后分型面不得有间隙,要有足够的合模力。
2)活动型芯、推出及导向部位运动及滑动要平稳、无干涉现象,定位要正确、可靠。
3)开模时,推出要平稳,保证将塑件及浇注系统凝料推出模具。
4)冷却水要畅通,不漏水,阀门控制正常。
5.2.3试模
模具安装调整后即可以进行试模。
1)加入原料原料的品种、规格、牌号应符合产品图样中的要求,成型性能应符合有关标准的规定。
原料一般要预先进行干燥。
2)调整设备按照工艺条件要求调整注射压力、注射速度、注射量、成型时间、成型温度等工艺参数。
3)试模采用手动操作,试模注射出样件。
5.2.4检验
通过试模可以检验出模具结构是否合理;所提供的样件是否符合用户的要求;模具能否完成批量生产。
针对试模中发现的问题,对模具进行修改、调整、再试模,使模具和生产出的样件满足客户的要求,即可交付生产使用。
XS-1780D型注塑机主要参数如表3-1:
参数名称
参数值
参数名称
参数值
额定注射量
499cm3
螺杆直径
55mm
最大开模行程S
435mm
注射压力
133Mpa
最大装模厚度Hmax
500mm
锁模力
1780kN
最小装模厚度Hmin
190mm
喷嘴圆弧半径
15mm
模板最大安装尺寸
470×470mm
喷嘴孔直径
6mm
表3-1XS-1780D型注塑机主要参数
1、注射量的校核
如前所述,塑件和浇注系统的总体积为V=24657.65mm3,远远小于注射机的标称注射量499
。
2、模具闭合高度的校核
由装配图可知模具的闭合高度为H闭=235mm。
最小装模高度为Hmin=190mm,最大装模高度为Hmax=500mm,能满足Hmin≤H闭≤Hmax的安装条件。
3、模具安装部分的校核
该模具的外形尺寸为250×250mm,注塑机模板最大安装尺寸为470×470mm,故能满足安装要求。
模具定位圈的直径为
50.46mm<注塑机定位孔的直径
160mm,符合安装要求。
浇口套主流道球面半径R=16mm大于注射机喷嘴圆弧半径R15mm,符合安装要求。
浇口套小端孔径
7mm大于喷嘴孔直径
6mm,符合要求。
4、模具开模行程的校核
模具的开模行程S模=塑件的高度+浇注系统的高度+推出距离+(5~10)=30+40+35+10=115mm
注塑机的最大开模行程S=435>115mm,符合要求。