降低丁二烯装置能耗.docx
《降低丁二烯装置能耗.docx》由会员分享,可在线阅读,更多相关《降低丁二烯装置能耗.docx(11页珍藏版)》请在冰豆网上搜索。
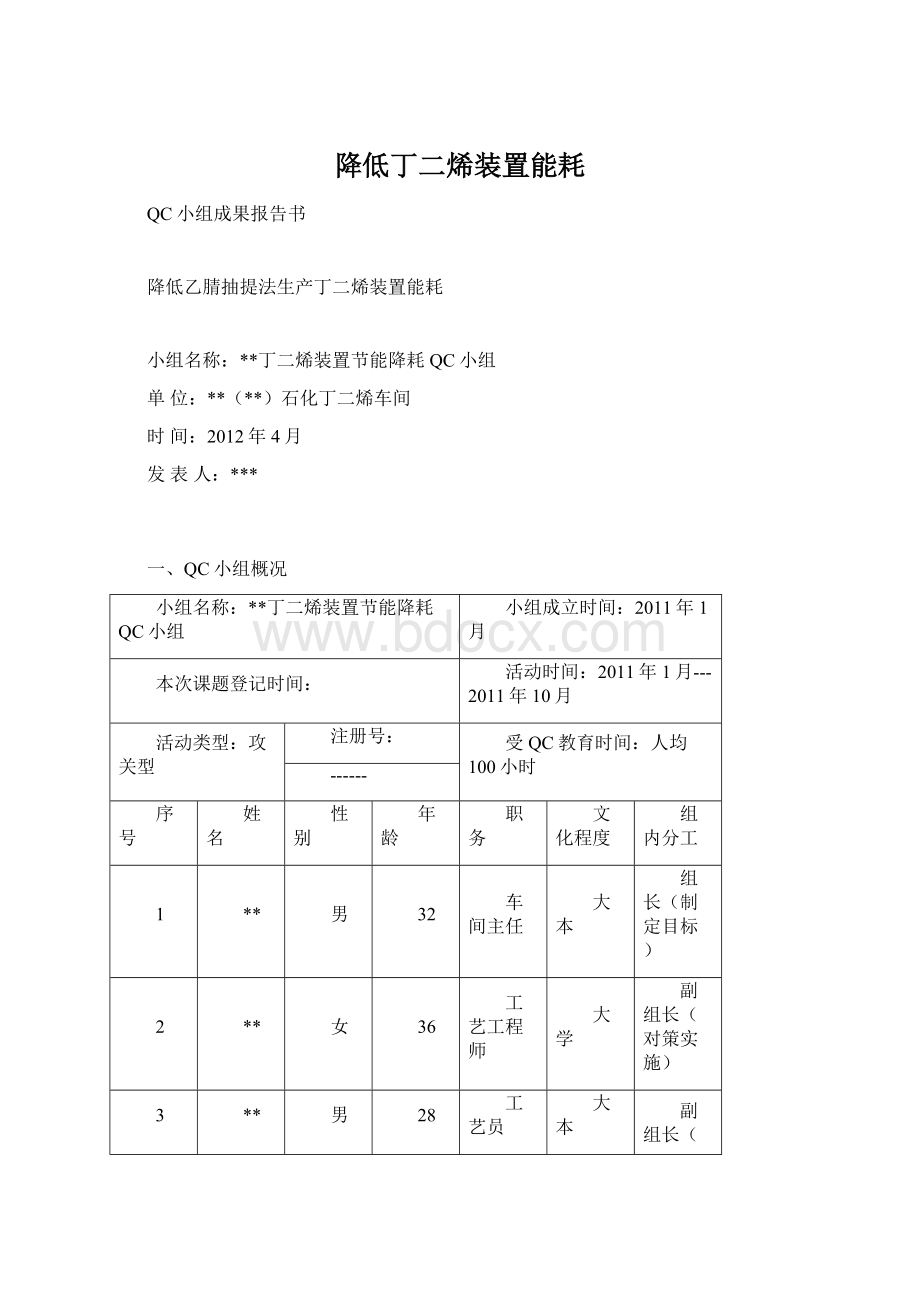
降低丁二烯装置能耗
QC小组成果报告书
降低乙腈抽提法生产丁二烯装置能耗
小组名称:
**丁二烯装置节能降耗QC小组
单位:
**(**)石化丁二烯车间
时间:
2012年4月
发表人:
***
一、QC小组概况
小组名称:
**丁二烯装置节能降耗QC小组
小组成立时间:
2011年1月
本次课题登记时间:
活动时间:
2011年1月---2011年10月
活动类型:
攻关型
注册号:
受QC教育时间:
人均100小时
------
序号
姓名
性别
年龄
职务
文化程度
组内分工
1
**
男
32
车间主任
大本
组长(制定目标)
2
**
女
36
工艺工程师
大学
副组长(对策实施)
3
**
男
28
工艺员
大本
副组长(对策实施)
4
**
男
42
安全员
大本
组员(对策实施)
5
**
男
28
工艺员
大本
组员(对策实施)
6
**
女
41
工艺员
大本
组员(资料整理)
7
**
男
27
设备员
大本
组员(对策实施)
二、选题理由
1、集团公司对装置能耗有创新性要求
2010年1月份**(**)丁二烯装置一次性开车成功,2010年丁二烯装置平均能耗260千克标油/吨丁二烯,2011年车间丁二烯能耗指标251千克标油/吨丁二烯,车间面临很大挑战。
2、国内同类装置横向对比表明我们在能耗优化方面有很大潜力
2010年国内其他乙腈抽提法生产丁二烯装置,能耗可以达到240~250千克标油/吨丁二烯,我们装置规模更大在节能降耗上更有优势。
三、现状调查
2010年丁二烯平均能耗260Kg标油/吨丁二烯,小组成员统计了2010年5到12月份丁二烯能耗分布情况,结果见下图。
从以上图表可以看出,2010年丁二烯平均能耗260Kg标油/吨,最小的10月份能耗只有246Kg标油/吨丁二烯,最大的6月份能耗为296Kg标油/吨丁二烯,能耗的分布差异很大。
四、确定目标及可行性分析
1.目标确定
根据我们装置的现状,及完成年度指标的要求,我们将小组活动目标订为:
2011年平均能耗250千克标油/吨丁二烯
2.可行性分析
从装置现状可以看出,我们在某些月份能耗可以达到目标值以下,表明装置具备达到目标值能耗的潜力,只是存在某些因素使装置的能耗不稳定,我们如果能够找出这些主要的影响因素,并且加以控制就可以完成目标。
五、原因分析
1.能耗计算公式说明
丁二烯装置能源包括以下种类:
蒸汽、电能、循环冷却水、氮气、仪表风、压缩空气。
计算能耗时用“单位时间内各种能源的消耗量”乘以“各类能源对应的系数”求和后除以“单位时间内丁二烯产量”。
2.先使用数学论证的方法进行初步原因分析
根据能耗公式,导致能耗大的原因:
①“公式分子”部分大,即蒸汽、循环水、氮气、仪表风消耗大。
②“公式分母”部分小,即当公用工程正常消耗时丁二烯产量小。
3.对公式的分子部分进行“分类分析”并使用头脑风暴法进行原因查找
①将分子部分能源按装置操作方式分为两类:
一是蒸汽(可以由操作人员主动控制,消耗量大且不稳定),二是电、水、氮气、仪表风(不受操作人员直接控制,消耗量小且使用量稳定)。
②头脑风暴法分析蒸汽用量大的原因
4.对公式的分母部分使用头脑风暴法进行原因查找。
5.并按照“5M1E”的原则对分析结果进行初步分类、筛选、汇总得到如下关系图
六、确定主要原因
确认一:
塔底再沸器换热效率低
在2010年11月中旬,先后对丁二烯一萃塔底蒸汽再沸器E-103和原料罐容剂再沸器E-101进行了切换,切换前后随即抽取10天装置能耗数据见右表。
对表中两组数据进行双总体T检验
①假设两总体平均数相同即:
μ1=μ2
②计算T值,T=0.2618
③查表T(9)0.05=2.62
④结论0.2618<2.62,故两组数据差异不显著,原假设成立。
结论一:
“塔底再沸器换热效率低”非要因。
确认二:
操作工水平参差不齐
对操作技能由高向低排列的四名内操A、B、C、D的操作能耗数据进行统计,平均差值在0.05%以内,没有明显。
统计数据见下表
结论二:
目前操作工技能水平差异对装置影响很小,非要因!
确认三:
操作参数未达到最优
2010年底开始,对装置的腈烃比、回流比、塔塔底操作温度等参数进行了一系列的优化,以下是优化前后装置能耗对比。
结论三:
经过优化调整后装置能耗有了较大幅度的下降。
因此,“操作参数未达到最优”是要因!
确认四:
设备检维修消耗蒸汽多
对装置中大型换热器E-203C检修过程中消耗的蒸汽进行计算,结果如下表。
装置界区蒸汽总表读数
各个蒸汽再沸器消耗蒸汽总和
校正值
(校正系数-0.063)
检修蒸汽消耗
1672.4t
1685t
-106.16t
93.56t
计算检修蒸汽消耗对月能耗均值的贡献仅为0.43千克标油/吨丁二烯因此:
结论四:
设备检修消耗蒸汽多,非要因!
确认五:
防冻防凝蒸汽消耗量大
对2010年冬季伴热投用前后日蒸汽消耗量进行统计,见右图。
从图表可以看出,伴热投用前后日能耗消耗无明显上升。
结论五:
防冻防凝蒸汽消耗非要因!
确认六:
电能、循环水、仪表风消耗量大
计算各种能源在总能耗中所占比例见下图:
从图表可知,各能源中蒸汽所占比例最大,其次是循环水和电能,其余能源由于所占比例太小,对节能降耗意义不大,目前不做进一步研究。
由于蒸汽消耗受操作人员主动控制,电、水、氮气、仪表风不受操作人员直接控制,下面是电和循环水每月用量。
从图中可以看出循环水和电能的消耗在每个月中基本维持稳定。
因此:
结论六:
电能循环水、仪表风消耗大,非要因!
确认七:
现场跑冒滴漏
对2011年第一季度着重对现场跑冒滴漏进行了治理,治理后现场物料泄漏降至很低水平,现场基本闻不到物料的味道。
但是治理前后装置总物衡无明显变化,能耗也无明显降低,因此
结论七:
现场跑冒滴漏非要因!
确认八:
产品不合格切循环
丁二烯月切循环累计时间时见和当月能耗数据如下表:
以切循环时间为X轴,月平均能耗为Y轴建立直角坐标系,得到以下散点图;
由散点图可以看出:
产品切循环时间和月能耗存在明显的正相关,因此:
结论八:
产品不合格切循环,是要因!
七、制定对策
针对影响丁二烯能耗的主要因素,制定了以下对策
八、对策实施
实施一、装置参数优化
2011年4月开始对装置的操作参数进行了一些列的节能降耗优化,至2011年9月这些参数逐渐趋于稳定,优化前后对比见下表:
序号
优化指标
优化前
优化后
1
腈烃比
7:
1
6:
1
2
T-102釜温
(溶剂含水量)
139.3℃
138.5℃
3
T-203回流量
112t/h
104t/h
4
T-302釜温
108.1℃
107.5℃
5
T-302塔回流量
13.5t/h
11.2t/h
优化前后装置正常生产时能耗对比如下图
优化效果:
优化后蒸汽消耗比优化前降低了64吨/天,折合8千克标油/吨丁二烯。
效果检查:
经过参数优化降低了正常生产时的绝对蒸汽消耗,完成了活动目标。
实施二、精细化管理消除装置隐患延长装置平稳运行周期
1.加强重要设备监控
►完善机泵运行状态记录、定期切换备台、机泵清理记录、滤网自聚物称重记录
►一萃二萃及精制两塔压差、温度点跟踪记录
►丁二烯高浓度冷却器换热效率曲线监控、定期取样分析循环水中丁二烯
►塔釜再沸器壳程压力曲线监控
2.加强培训
►车间技术人员定期给操作人员讲课培训
►班组内部师带徒
►月岗位练兵在线答题、季度考试、年度技能比武
3.装置隐患排查
►技术人员定期对装置进行“体检”
►鼓励车间全体人员查找装置隐患,并及时整改
►对每周隐患发现及整改情况进行记录,并给予责任人加分奖励
3.系统“平稳”参数监控
►每周取溶剂留样,建立循环溶剂变化跟踪档案
►定期对过滤器进行清理,记录系统自聚物情况
►监控系统氧含量,并定期对管线死点、容易积聚氧的部位进行排放
效果检查:
经过车间精细化管理及隐患排除工作,装置月累计切循环时间明显降低,见下图:
对策实施后月累计切循环时间明显下降,2011年6月份以后,每个月累计切循环时间都小于3小时,完成了活动目标。
九、效果检查
经过小组活动后,丁二烯装置能耗变化见下图
2010年丁二烯装置平均能耗260千克标油/吨丁二烯,2011年丁二烯装置平均能耗244千克标油/吨丁二烯,完成了活动目标!
十、总结及下一步打算
1、小组活动总结
本次活动从优化工艺和精细管理两方面进行攻关,有效减少装置能耗取得了可观的经济效益,同时,积累了很多操作经验及管理经验。
2、下一步打算
进一步对装置进行优化及精细化管理,降低能耗的同时实现更长周期平稳的运行。