课程设计配有盘的热处理.docx
《课程设计配有盘的热处理.docx》由会员分享,可在线阅读,更多相关《课程设计配有盘的热处理.docx(23页珍藏版)》请在冰豆网上搜索。
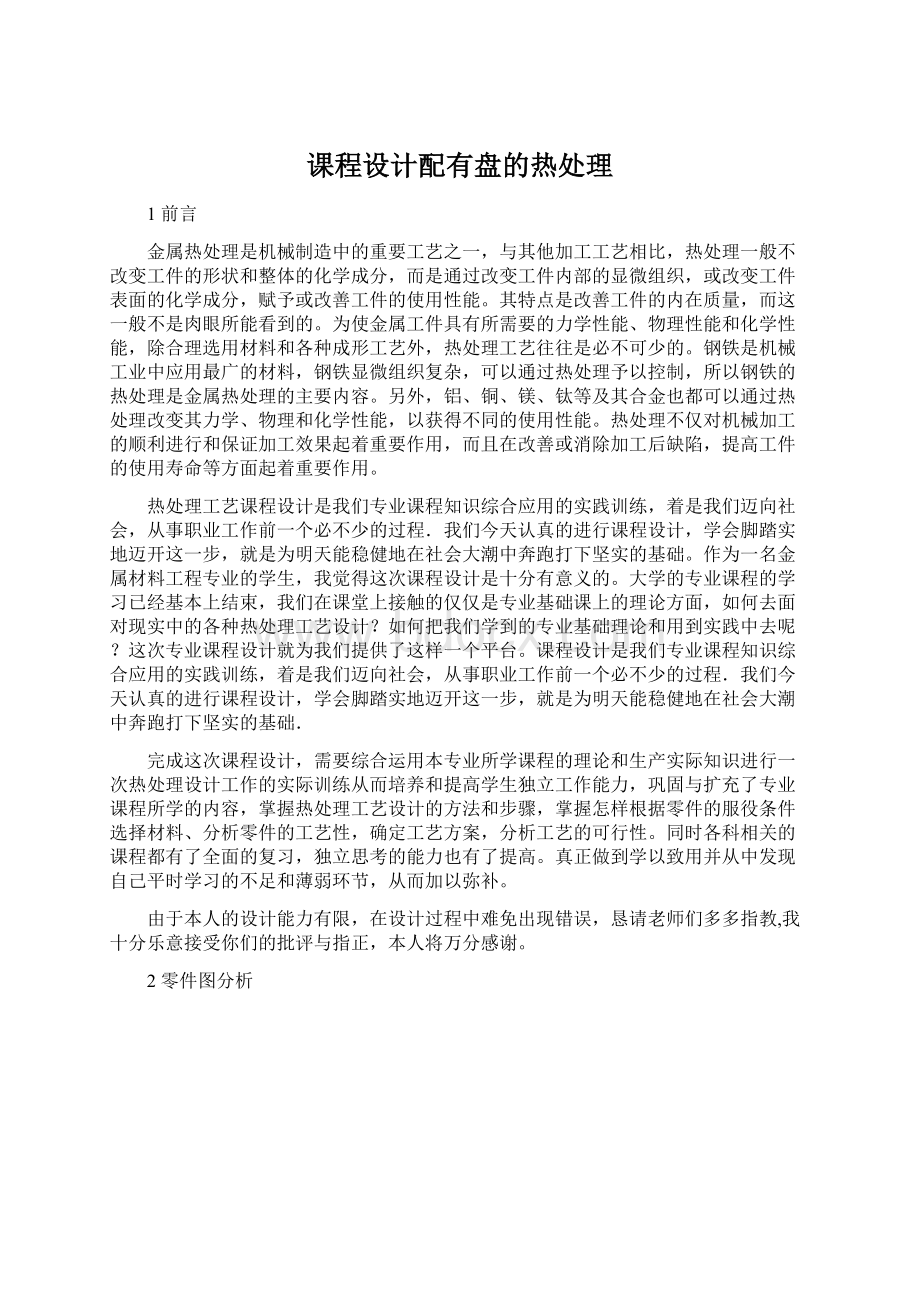
课程设计配有盘的热处理
1前言
金属热处理是机械制造中的重要工艺之一,与其他加工工艺相比,热处理一般不改变工件的形状和整体的化学成分,而是通过改变工件内部的显微组织,或改变工件表面的化学成分,赋予或改善工件的使用性能。
其特点是改善工件的内在质量,而这一般不是肉眼所能看到的。
为使金属工件具有所需要的力学性能、物理性能和化学性能,除合理选用材料和各种成形工艺外,热处理工艺往往是必不可少的。
钢铁是机械工业中应用最广的材料,钢铁显微组织复杂,可以通过热处理予以控制,所以钢铁的热处理是金属热处理的主要内容。
另外,铝、铜、镁、钛等及其合金也都可以通过热处理改变其力学、物理和化学性能,以获得不同的使用性能。
热处理不仅对机械加工的顺利进行和保证加工效果起着重要作用,而且在改善或消除加工后缺陷,提高工件的使用寿命等方面起着重要作用。
热处理工艺课程设计是我们专业课程知识综合应用的实践训练,着是我们迈向社会,从事职业工作前一个必不少的过程.我们今天认真的进行课程设计,学会脚踏实地迈开这一步,就是为明天能稳健地在社会大潮中奔跑打下坚实的基础。
作为一名金属材料工程专业的学生,我觉得这次课程设计是十分有意义的。
大学的专业课程的学习已经基本上结束,我们在课堂上接触的仅仅是专业基础课上的理论方面,如何去面对现实中的各种热处理工艺设计?
如何把我们学到的专业基础理论和用到实践中去呢?
这次专业课程设计就为我们提供了这样一个平台。
课程设计是我们专业课程知识综合应用的实践训练,着是我们迈向社会,从事职业工作前一个必不少的过程.我们今天认真的进行课程设计,学会脚踏实地迈开这一步,就是为明天能稳健地在社会大潮中奔跑打下坚实的基础.
完成这次课程设计,需要综合运用本专业所学课程的理论和生产实际知识进行一次热处理设计工作的实际训练从而培养和提高学生独立工作能力,巩固与扩充了专业课程所学的内容,掌握热处理工艺设计的方法和步骤,掌握怎样根据零件的服役条件选择材料、分析零件的工艺性,确定工艺方案,分析工艺的可行性。
同时各科相关的课程都有了全面的复习,独立思考的能力也有了提高。
真正做到学以致用并从中发现自己平时学习的不足和薄弱环节,从而加以弥补。
由于本人的设计能力有限,在设计过程中难免出现错误,恳请老师们多多指教,我十分乐意接受你们的批评与指正,本人将万分感谢。
2零件图分析
图1配油盘零件图[2]
2.1零件的总体分析
叶片泵是由转子,定子,叶片和配油盘相互形成封闭容积的体积变化来实现泵的吸油和压油。
叶片泵的结构紧凑,零件加工精度要求高。
叶片泵转子旋转时,叶片在离心力和压力油的作用下,尖部紧贴在定子内表面上。
这样两个叶片与转子和定子内表面所构成的工作容积,先由小到大吸油后再由大到小排油,叶片旋转一周时,完成两次吸油与排油。
配油盘又称侧盘。
配油盘和转子端面、叶片端面相对滑动而产生磨损,严重时间隙封破坏,泄漏量加大,泵的容积效率下降。
因此,配油盘应具有良好的耐磨性,是比较重要的叶片泵零件。
液压技术的广泛应用,对液压元件的性能上要求高压、大流量、高转速、高容积效率等方向发展,在结构上要求微型化,在质量上要求高的可靠性。
液压元件的零件特点是体积小而精度要求,在工作中承受复杂的服役条件。
因此,在选材上与热处理上应保证高的强度,良好的韧性,高的耐磨性和尺寸稳定性高。
2.2零件的结构形状分析
零件结构形状如图1所示
2.3零件的尺寸及技术要求分析
尺寸要求:
直径:
120mm厚:
14mm
技术要求:
碳氮共渗的化合物层深度5~10μm
2.4零件的服役条件及失效形式分析
2.4.1服役条件
叶片泵在运行过程中,配油盘与转子端面、叶片端面将发生相对滑动而产生磨损,这时接触部位将产生大量摩擦热,使局部温度升高。
2.4.2失效形式
叶片泵在运行过程中,配油盘与转子端面、叶片端面将发生相对滑动而易产生磨损;同时由滑动摩擦产生大量摩擦热,易造成热疲劳现象。
3材料选择
3.1配油盘的性能要求
根据配油盘的工作状况,可以初步得出其材料应满足的性能要求:
一是具有良好的热硬性和耐磨性,以保证配油盘满足液压元件在高压高速工作下具有足够好的耐磨性;二是具有良好的疲劳性能,使配油盘零件能够在良好的服役条件下长时间的工作。
因此,为满足配油盘使用性能的要求,其选择材料原则一般如下:
低中压泵一般采用青铜制造,而高压泵则采用HT300高强铸铁制造,并一般施以低温的化学热处理以提高其耐磨性。
为提高配油盘的耐磨性,在最后精加工前一般进行氮碳共渗。
由于液压元件一般要求尺寸精度高,所以配油盘加工精度要求也较高,为此,热处理过程中要严格控制器畸变。
其主要措施是铁丝捆扎、垂直吊挂加热等。
铸件有优良的机械、物理性能,它可以有各种不同的强度、硬度、韧性配合的综合性能,还可兼具一种或多种特殊性能,如耐磨、耐高温和低温、耐腐蚀等。
铸件的重量和尺寸范围都很宽,重量最轻的只有几克,最重的可达到400吨,壁厚最薄的只有0.5毫米,最厚可超过1米,长度可由几毫米到十几米,可满足不同工业部门的使用要求。
3.2灰口铸铁及铸青铜的性能特点
在铸铁中中,铸铁按在结晶过程中石墨化程度不同,可分为灰口铸铁、白口铸铁和马口铸铁,其中灰口铸铁是第一阶段石墨化过程充分进行而得到的铸铁,全部或大部分碳以片状石墨形态存在,断口呈灰暗色,因此得名,根据基体组织的不同,灰口铸铁分为铁素体灰口铸铁、铁素体+珠光体灰口铸铁、珠光体灰口铸铁及变质灰口铸铁,分别如图所示。
表1灰铸铁的化学成分范围(质量分数)(%)[1]
铸铁类型
C
Si
Mn
P
S
灰铸铁
2.5~4.0
1.0~3.0
0.2~1.0
0.002~1.0
0.02~0.25
表2HT300灰铸铁件的特点及应用范围[1][9]
牌号
铸铁级别
主要特点
工作条件
应用举例
HT300
高强度、高耐磨性铸件
集体组织为100%珠光体,属于需要孕育处理的铸件
强度高,耐磨性好;白口倾向大,铸造性能差,需要人工时效处理
1)承受高弯曲力(<50MPa)及抗拉应力
2)摩擦面间的单位压力≥2Mpa
3)要求保持高度气密性
1)机械制造中重要的铸件,如:
车床、床身导轨、压力机等;
2)高压的液压缸、水缸、泵体、阀体
3)镦锻、热锻锻模、冷冲模
4)须经表面淬火的零件
铸铁按在结晶过程中石墨化程度不同,可分为灰口铸铁、白口铸铁和马口铸铁,其中灰口铸铁是第一阶段石墨化过程充分进行而得到的铸铁,全部或大部分碳以片状石墨形态存在,断口呈灰暗色,因此得名,根据基体组织的不同,灰口铸铁分为铁素体灰口铸铁、铁素体+珠光体灰口铸铁、珠光体灰口铸铁及变质灰口铸铁。
分别如图所示。
铁素体+粗大石墨片铁素体+珠光体+粗大石墨片
珠光体+粗大石墨片均匀细小石墨片
图2灰铸铁组织图
变质灰口铸铁在灰铸铁基础上经变质处理后,灰色的条状石墨片变得细小和均匀分布,铸铁性能得到很大的改善其强度、塑性和韧性均比一般灰铸铁好得多,组织也较均匀。
主要用于制造力学性能要求较高铸件
青铜它是红铜和锡、铅的合金,也是金属治铸史上最早的合金。
青铜和锡的比例变化范围很大(从残存人工制品中测得,铜含量为67~95%)青铜具有熔点低、硬度大、可塑性强、耐磨、耐腐蚀、色泽光亮等特点,适用于铸造各种器具、机械零件、轴承、齿轮等。
因为锡青铜结晶温度范围较宽,流动性差,不易形成集中缩孔,而易形成枝晶偏析和分散缩孔,铸造收缩率小,有利于得尺寸极接近于铸型的铸件,所以适于铸造形状复杂,壁厚较大的条件,而不适宜铸造要求致密度高和密封性好的铸件。
由于配油盘需要很好的耐磨性及工作在高温高压的条件下,而且要求密封性良好,由以上分析可以看出经孕育处理后的HT300与青铜相比,能更好的满足零件的性能要求,所以,高压泵的配油盘尺寸精度高,采用HT300高强铸铁制造,并一般施以低温的化学热处理以提高其耐磨性。
4确定加工路线(冷、热加工)
加工工艺主要包括机加工和热处理工艺。
机加工是指通过加工机械精确去除材料的加工工艺。
它直接改变毛坯的形状、尺寸和表面质量等,使其成为零件的过程称为机械加工工艺过程。
热处理是将金属材料放在一定的介质内加热、保温、冷却,通过改变材料表面或内部的金相组织结构,来控制其性能的一种金属热加工工艺。
该零件结构简单,可以通过铸造铸出毛坯,通过机加工使其成型;之后进行去应力退火,消除残余内应力。
改善其切削性能然后经过机加工使其复合尺寸要求;再经过化学热处理(氮碳共渗)使表面获得一层化合物渗层,提高零件表面耐磨性和抗疲劳性能;最后经过研磨,以满足尺寸精度,即可得到所需的零件。
可采用的工艺流程:
配油盘的整体加工工艺流程:
铸出毛坯→一次机加工(粗加工)→去应力退火→二次机加工(精加工)→氮碳共渗→研磨。
5热处理工艺方法选择
5.1退火工艺的选择
铸铁经过铸造及粗加工后组织不均匀内应力较大,易变形开裂,所以在精加工前需施以消除内应力稳定组织为目的的去应力退火。
铸铁的内应力主要产生在有塑性到弹性变形的过渡阶段,这也就是在620~400℃之间,因此在这个温度区间内,冷却速度愈慢,内应力就愈小。
消除内应力的退火应该是将粗加工后铸件缓慢加热到高于铸铁塑性变形的温度范围内,然后保温,使铸件各部分组织均匀,内应力减小。
故一般在选用低温去应力退火。
5.2表面处理工艺的选择
由于叶片泵工作时配油盘和转子端面、叶片端面发生相对滑动而产生磨损,严重时间隙封破坏,泄漏量加大,泵的容积效率下降,将影响叶片泵进而整个系统的正常工作,故配油盘零件表面要求要有良好的耐磨性,以保证它能长时间的良好工作。
HT300表面硬度不够高,耐磨性较差,不能满足零件的性能要求。
故一般在最后精加工之前要对其进行表面处理,以达到其工作性能的要求。
灰铸铁中石墨片呈片状,是影响其机械性能的主要矛盾,用普通热处理改善它的机械性能效果不太显著,故一般不采用表面淬火工艺,而采用表面化学处理,这里选用氮碳共渗工艺。
经过处理后,在表面形成氮碳共渗化合物层,该渗层硬度高,耐磨性好,而且极大的改善了铸铁的疲劳性能。
6制订热处理工艺制度
6.1灰铸铁的热处理基础
铸铁是一种以铁、碳、硅为基础的复杂的多元合金,其含碳量(质量分数)一般在2.0%4.0%的范围。
除碳、硅外,铸铁中还存在锰、磷、硫等元素。
图3普通铸铁的碳、硅成分范围[1]
图4Fe-C-Si三元稳定系相图[1]
表3灰铸铁的临界温度范围[1]
铸铁类型
化学成分(质量分数)(%)
临界温度/℃
C
Si
Mn
P
S
Cu
Mo
Mg
Ce
Ac1下限
Ac1上限
Ar1上限
Ar1下限
灰铸铁
3.15
2.2
0.67
0.24
0.11
–
–
–
–
770
830
–
–
2.83
2.17
0.5
0.13
0.09
–
–
–
–
775
830
765
723
铸铁的热处理工艺方法和钢的热处理基本相似,但由于铸铁中石墨的存在以及化学成分等方面的差异,其热处理又有其特殊性:
①控制不同的加热温度和时间,可获得不同比例的F和P组织,在较大幅度内调整其力学性能;
②与钢相比,铸铁通过合适的热处理,可分别获得相当于高、中、低碳钢的性能;
③控制奥氏体温度和加热、保温、冷却条件,可使铸铁的性能在较大范围内调整;
④碳集中于石墨中,相变过程中碳长做远距离扩散,受到温度和化学成分等因素很大影响;
⑤热处理一般不能改变石墨的形状和分布特性,铸铁的各项性能指标与基体中的石墨形态有很大关系,故热处理对铸铁有一定的局限性。
6.2退火工艺的制定
6.2.1退火方式的确定
铸铁的内应力主要产生在有塑性到弹性变形的过渡阶段,这也就是在620~400℃之间,为消除铸件的残余应力及稳定其几何尺寸,减小或消除切削加工后产生的畸变,需对铸件进行去应力退火。
消除内应力的退火应该是将粗加工后铸件缓慢加热到高于铸铁塑性变形的温度范围内,为使铸件各部分温度均匀而予以保温,使铸件各部分组织均匀,然后再缓慢冷却到弹性变形温度范围内,出炉空冷,故对于本零件需要选用稍微高于塑性变形温度范围内的低温去应力退火。
6.2.2去应力退火工艺规范的确定
图5灰铸铁退火温度与内应力消除程度的关系[1]
1——变形减小程度;2——残留内应力
表4灰铸铁去应力退火规范[1]
6.2.2.1退火温度的确定
去应力退火温度的确定,必须考虑铸铁的化学成分。
去应力退火温度一般稍高于材料的再结晶温度。
铸件的内应力主要产生在620~400℃之间由塑性变形到弹性变形的温度范围内,要想消除内应力,必须加热到塑性变形温度以上,使其从重新冷却,在620~400℃冷却速度要慢,已达到消除内应力的目的。
提高加热温度可缩短保温时间,但普通灰铸铁当温度超过550℃(当含有合金元素时,渗碳体开始分解的温度将提高到600℃左右),即可发生部分渗碳体的石墨化和粒化,使强度和硬度降低,并伴随有组织转变。
T再结晶≈0.4TmTm为金属的熔点[14]
6.2.2.2退火时间的确定
HT300的退火保温时间选择相当重要,虽不必像淬火加热时间那样精确计算,但也应该适当选择。
时间太长,既影响生产效率(如灰铸铁可经过1~1.5年的自然时效达到去应力退火的目的),而且会可能造成工件的严重的氧化脱碳,使性能恶化;时间太短,则很难使铸件组织完成均匀化,达不到消除内应力和降低硬度的目的,失去退火的意义。
具体加热时间的确定应考虑装炉量和装炉方式及工件大小,以保证工件透烧和组织转变。
对于单个灰铸铁件,保温时间的前2~3小时内消除内应力的效果最显著。
保温时间取决于加热温度和铸件的大小和复杂程度,必须保证铸件的各部分均匀加热到所需的温度,一般为2~8小时,对于HT300为2~4小时。
加热速度一般为100~150℃/h,在塑性变形与弹性变形的温度范围内,冷却速度要慢,根据零件的复杂程度选择20~50℃/h,为了不致使去应力退火后冷却时再发生附加的残余应力,对于大截面工件需要冷却至300℃以下出炉空气中快冷
6.2.2.3退火冷却方式的确定
冷却方式需要根据冷却速度选择,为了达到消除内应力的目的在塑性变形与弹性变形的温度范围内(620~400℃),在这个范围内,冷却速度越慢内应力越小,所以冷却速度要慢,根据零件的复杂程度选择20~50℃/h,所以随炉冷却是合适的。
为了不致使去应力退火后冷却时再发生附加的残余应力,所以铸件冷却至弹性变形温度范围内出炉空冷,对于大截面工件需要冷却至300℃以下出炉在空气中冷却至室温。
6.2.2.4退火工艺参数的确定
据计算,工件的质量<0.3吨,壁厚为14mm∈(10~40mm),铸铁熔点Tm≈1500℃,尺寸如图1。
故其工艺参数为去应力退火:
加热到(590±10)℃,保温3小时,炉冷到300℃以下出炉空冷
6.3氮碳共渗化学处理工艺的制定
6.3.1表面处理工艺的选择
配油盘零件工作环境要求零件应具有的性能为:
表面硬度高,耐磨性好,疲劳性能优良。
灰铸铁中石墨片呈片状,是影响其机械性能的主要矛盾,用普通热处理改善它的机械性能效果不太显著,故一般不采用表面淬火工艺,而采用表面化学处理。
金属表面化学热处理是利用元素的扩散性能,使合金元素渗入金属表层的一种热处理技术。
基本工艺过程:
①将工件置于含有渗入元素的活性介质中加热到一定温度,使活性介质通过分解并释放出欲渗入元素的活性原子;
②活性原子被工件吸附并溶入表面;
③溶入表面的原子向金属表层扩散渗入形成一定厚度的扩散层,从而改变工件表层的成分、组织和性能。
渗氮工艺特点:
可以使金属表面硬度达到950~1200HV,使工件具有极高的耐磨性;可以使表面产生很大的残余压应力,从而提高疲劳强度;此外还可以提高工件的耐蚀性能。
渗氮能形成优越性能的渗氮层,但由于工艺时间较长(氮化物形成温度低,扩散较慢,工艺时间较长,如获得0.5mm的渗氮层,约需要40~50h),使得生产率太低,成本高,应尽量少用。
渗碳工艺特点:
渗碳也可以使工件表面获得高硬度、耐磨性、耐侵蚀磨损性及接触疲劳强度等,但其也存在许多不足:
①工艺过程繁琐,渗碳后还要进行淬火加回火处理,工件变形大,一般不用于高几何尺寸精度要求的零件的处理;②与高频淬火相比,生产成本高;渗碳层硬度和耐磨性不如渗氮层好。
碳氮共渗工艺特点:
碳氮共渗是在渗碳和渗氮工艺基础上发展起来的,其具有前者的优点,同时还具有自己的特点:
①与渗碳相比,处理温度低,晶粒不易长大,变形开裂倾向小,能源消耗低;②与渗氮相比,工艺周期大大缩短,对材料适用范围广。
但也有其不足,渗后需进行渗后处理,渗后直接淬火或渗后淬火加回火,虽然变形小,但也要产生变形。
氮碳共渗的工艺特点:
热处理温度低,一般在500~600℃,过程以渗氮为主,渗碳为辅,渗碳量很小。
其有很多优点,应用范围较广:
①氮碳共渗层有优良的性能,渗层硬度高,脆性低,有优良的耐磨性、耐疲劳性能、抗咬合性、热稳定性和抗腐蚀性;②工艺温度低,且不淬火,工件变形小;③处理时间短,经济性好;设备简单,工艺易掌握。
适用于渗层浅且不承受重载的零件。
通过比较以上四种工艺的特点,结合配油盘性能要求,经济性,我们选用氮碳共渗工艺。
6.3.2氮碳共渗工艺规范的确定
6.3.2.1氮碳共渗方式的确定
因为这里需要在较低温度下进行共渗,所以我们需要在固体渗氮、液体渗氮及气体渗氮中选择。
盐浴氮碳共渗是最早采用的氮碳共渗方式,按盐浴中CN-含量可将氮碳共渗分为低氰、中氰和高氰型。
由于环保的原因,中、高氰盐浴已经逐渐被淘汰。
低氰盐浴与氧化配合,排放的废气、废水、废盐中CN-量应符合国家规定标准。
根据工件的尺寸要求与性能要求,可选择盐浴氮碳共渗方式进行处理。
相比气体氮碳共渗与固体氮碳共渗,盐浴氮碳共渗具有提高耐磨性、抗疲劳性和耐蚀性等优点,而且经过盐浴氮碳共渗后,工件尺寸及精度变化极小,对工件的安装、使用等影响甚微。
因此选择盐浴氮碳共渗方式处理。
由于尿素型原料无毒,液体流动性能很好,渗入速度快,低成本等优点,盐浴类型可选尿素型。
盐浴质量百分比为:
尿素︰碳酸钠︰氯化钾=3︰2︰2,使用温度为550℃~580℃。
但在共渗之前还需进行以下操作:
(1)表面处理:
清理表面,彻底去除表面油污及铁锈;
(2)预热:
进行氮碳共渗前将工件在电炉中预热至400℃~500℃,以防止工件放入坩埚中使盐浴温度降低过多。
6.3.2.2氮碳共渗温度的确定
氮碳共渗温度的选择要考虑到渗层形成质量,同时考虑渗速,一般选在Fe-N共析温度附近,多数钢的共渗温度在560~580℃,同时温度应低于调质回火温度以不降低基体的强度,碳钢、低合金钢和铸铁一般选择为(570±10)℃,在此温度下可获得足够厚的化合物层和较高的硬度。
6.3.2.3氮碳共渗时间的确定
如图6所示化合物层厚度,渗层硬度在0~4h内增加很快,随后随时间延长变化变得缓慢,在2~3小时之间达到最大值,过长时间则硬度下降。
6.3.2.4氮碳共渗冷却方式的确定
共渗温度高于共析温度565℃,共渗组织会有ε、r相共存,缓慢冷却时发生
转变,硬度下降,当快冷时ε相析出r,同时共析反应受阻生成马氏体,使硬度提高,所以液体氮碳共渗后一般采用快冷,铸铁采用先空冷以使组织均匀,后用水快冷以析出马氏体。
图6软氮化时间对硬度与深度的影响[6]
6.3.2.5氮碳共渗工艺参数的确定
综上所述,氮碳共渗处理工艺可制定为:
装炉前应先对工件表面进行清理,去除油污及铁锈。
装炉后先预热至400℃~500℃,再加热至570℃并保温,在尿素型盐浴中进行氮碳共渗。
氮碳共渗过程应进行约3h,共渗后先在空气中预冷至350℃附近,然后水冷。
7热处理组织与性能分析
去应力退火一般在A1以下进行,组织并未发生变化,同铸铁的原始组织,在缓慢冷却的过程中,工件各部分均匀冷却和收缩,消除了铸造和机加工的残余内应力,并使其稳定化,避免在使用或随后的加工过程中产生变形或开裂,为后续加工做好准备。
氮碳共渗,又称软氮化或低温碳氮共渗,即在铁-氮共析转变温度以下,在工件表面同时渗入氮、碳元素,且使工件表面在主要渗入氮的同时也渗入碳。
碳渗入后形成的微细碳化物能促进氮的扩散,加快高氮化合物的形成,这些高氮化合物反过来又能提高碳的溶解度,碳氮原子相互促进便加快了渗入速度。
表面氮浓度不断增加,形成白亮层及扩散层。
碳在氮化物中还能降低脆性。
氮碳共渗后得到的化合物层韧性好,硬度高,耐磨,耐蚀,抗咬合。
8热处理设备选择
热处理常用的加热设备按能源分有燃料加热设备和电加热设备;按工作温度可分为高温炉(>1000℃)、中温炉(650℃~1000℃)和低温炉(≤650℃)。
生产上常用的加热设备有电阻炉、浴炉、气体渗碳炉、高频感应加热设备等。
炉型的选择应依据不同的工艺要求及工件的类型来决定。
热处理设备的选择要从多方面来考虑,包括:
经济性、可靠性、配套性、安全性、以及工厂的实际情况等。
8.1去应力退火加热炉的选择
表5热处理炉的分类[3]
分类原则
炉膛形式
工艺用途
炉型
箱式炉
井式炉
罩式炉
贯通式炉
转底式炉
管式炉
退火炉
淬火炉
回火炉
渗碳炉
渗氮炉
实验炉
盐浴炉不能用于退火,感应热处理炉只用于表面热处理,可控气氛热处理炉一般用于气体渗碳、渗氮、碳氮共渗等工艺,真空热处理设备一般用于处理零件性能、精度要求非常高的零件,成本较高,应用范围受到限制。
故我们在这里选用电阻炉,箱式电阻炉该类热处理电阻炉是以电为能源的,通过炉内电热元件将电能转化为热能而加热工件的炉子,是一种造价相对便宜的炉子,以降低成本。
鉴于所需要的加热温度,选择中温箱式电阻炉进行加热。
中温箱式电阻炉可用于退火、正火、回火或固体渗碳等。
表为中温热处理电阻炉的型号。
配油盘尺寸为Φ120mm,厚度为14mm,为小批量生产,考虑经济性和实用性,故选用RX3-60-9型的热处理电阻炉。
表6中温箱式电阻炉产品规格及技术参数[3]
型号
功率/KW
电压
/V
相数
最高工作温度℃
炉膛尺寸(长×宽×高)/(mm×mm×mm)
炉温850℃时的指标
空载耗能/KW
空炉升温时间/h
最大装载量/kg
RX3-15-9
15
380
1
950
600×300×250
5
2.5
80
RX3-30-9
30
380
3
950
950×450×350
7
2.5
200
RX3-45-9
45
380
3
950
1200×600×400
9
2.5
400
RX3-60-9
60
380
3
950
1500×750×450
12
3
700
RX3-75-9
75
380
3
950
1800×900×550
16
3.5
1200
8.2氮碳共渗用炉的选择
由于氮碳共渗处理采用盐浴式,因此处理设备可选择盐浴炉。
盐浴炉按温度划分为低、中、高温浴炉。
盐浴炉的品种和代号见下表。
表7盐浴炉的品种和代号[3]
品种代号
结构形式
最高工作温度/℃
RYN3
矩形浴槽,内部管状加热元件加热
300
RYN4
400
RYW5
矩形浴槽,外部电加热
550
RYW8
圆形浴槽,外部电加热
850
RYD6
矩形或圆形浴槽,内部电极加热
650
RYD8
850
RYD9
950
RYD13
1300
根据上表和工件生产的实际情况,可选择RYD6式盐浴炉。
8.3热处理冷却设备的选择
热