自行车辐条长度计算及编圈方法.docx
《自行车辐条长度计算及编圈方法.docx》由会员分享,可在线阅读,更多相关《自行车辐条长度计算及编圈方法.docx(29页珍藏版)》请在冰豆网上搜索。
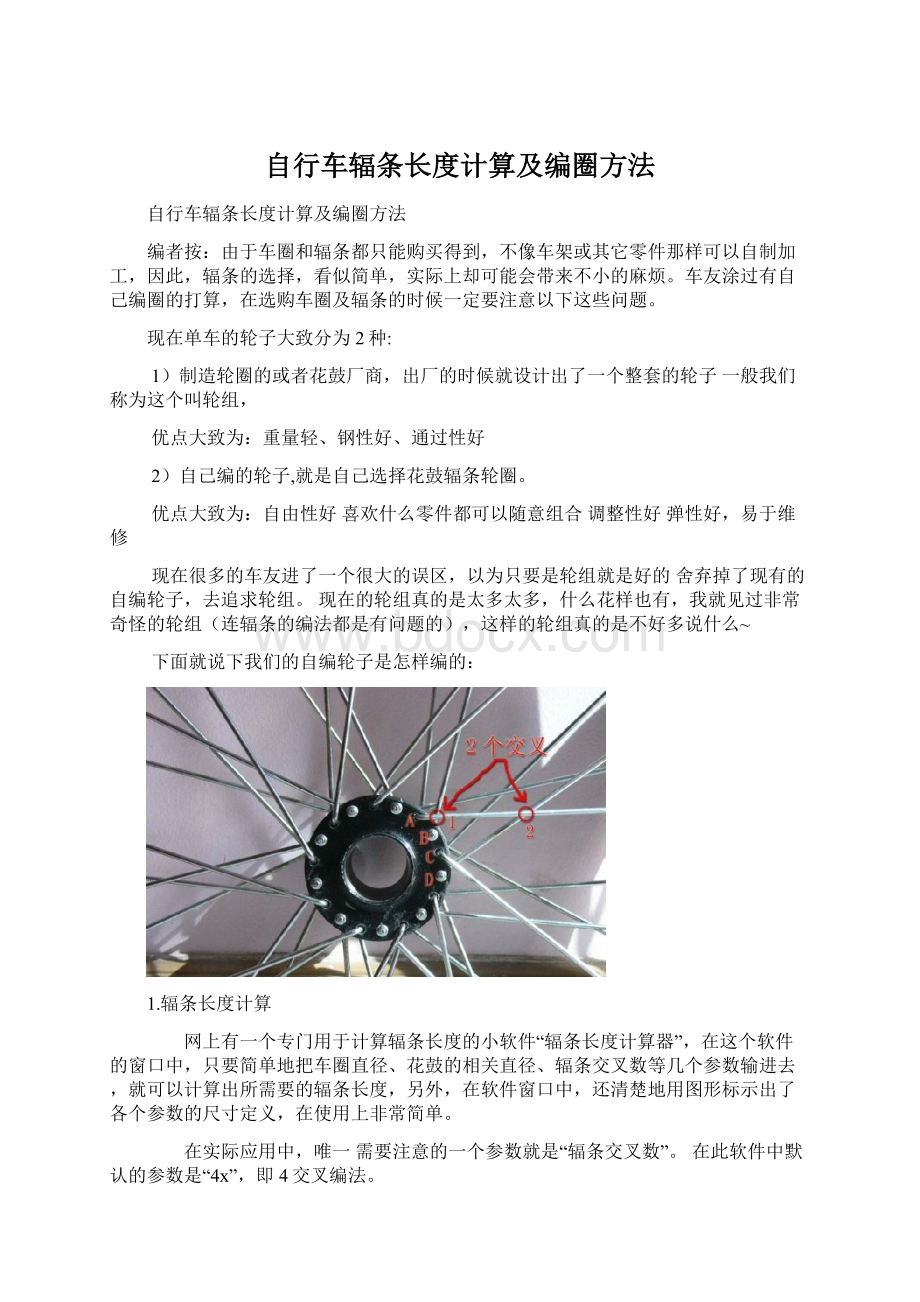
自行车辐条长度计算及编圈方法
自行车辐条长度计算及编圈方法
编者按:
由于车圈和辐条都只能购买得到,不像车架或其它零件那样可以自制加工,因此,辐条的选择,看似简单,实际上却可能会带来不小的麻烦。
车友涂过有自己编圈的打算,在选购车圈及辐条的时候一定要注意以下这些问题。
现在单车的轮子大致分为2种:
1)制造轮圈的或者花鼓厂商,出厂的时候就设计出了一个整套的轮子一般我们称为这个叫轮组,
优点大致为:
重量轻、钢性好、通过性好
2)自己编的轮子,就是自己选择花鼓辐条轮圈。
优点大致为:
自由性好喜欢什么零件都可以随意组合调整性好弹性好,易于维修
现在很多的车友进了一个很大的误区,以为只要是轮组就是好的舍弃掉了现有的自编轮子,去追求轮组。
现在的轮组真的是太多太多,什么花样也有,我就见过非常奇怪的轮组(连辐条的编法都是有问题的),这样的轮组真的是不好多说什么~
下面就说下我们的自编轮子是怎样编的:
1.辐条长度计算
网上有一个专门用于计算辐条长度的小软件“辐条长度计算器”,在这个软件的窗口中,只要简单地把车圈直径、花鼓的相关直径、辐条交叉数等几个参数输进去,就可以计算出所需要的辐条长度,另外,在软件窗口中,还清楚地用图形标示出了各个参数的尺寸定义,在使用上非常简单。
在实际应用中,唯一需要注意的一个参数就是“辐条交叉数”。
在此软件中默认的参数是“4x”,即4交叉编法。
我个人认为,这种4交叉的编法,比较适合于编制直径较大的车圈,比如26寸车圈,而对于躺车中较常用的20寸前轮,则4x的编法会使辐条倾斜过度,导致辐条根部在花鼓的一圈圆周孔上相互叠压,影响辐条的正常排列。
26寸车圈最常见的编法都是3交叉,即“3x”编法,这种编法,在花鼓的一圈圆周孔上,2根交叉的辐条孔,其中间夹着4个孔。
如果是2x的编法,则2根交叉的辐条孔(A和D)中间是夹着2个孔(B孔和C孔),参见照片。
照片中,A、B、C、D这4根辐条为一组,其中,在辐条A上共有2个交叉点:
与辐条B相交于1点处,与辐条D相交于2点处。
我的躺车前轮是20寸的,花鼓是本论坛的高手“狂野之驴”为我制作的碟刹花鼓,尺寸与标准的山地车碟刹花鼓相同,只是定制成36孔。
由于这种花鼓的直径较大,所用的辐条更短,由此,我采用了“2x”的编法,但因车圈是20寸,最终,2x编法的辐条倾斜角度与26寸圈3x编法的倾斜角度也基本相近。
经过实践验证,“辐条长度计算器”的计算结果还是很准确的,在车圈和花鼓尺寸已确定不变的情况下,可通过变更“交叉数”这个参数,计算出多个辐条长度值,这样,就比较容易购买到合适的辐条了。
个人建议:
尽量不要选择“4x”交叉编法。
另外,在购买辐条时,我是以辐条的直线段长度为计算值,辐条根部的弯钩部分不计入长度值。
实际购买时,如果实在没有合适的长度,辐条可以比计算值短2~3mm,但不能比计算值长,长了很难处理,得打磨修短。
2.辐条的编法与技巧
市面上常见的辐条按直径大多为10#、12#和13#这几种,10#条最粗,一般用于电动车,13#最细,普通自行车中用的都是13#条。
对于20寸车圈的辐条,一般可在电动车配件市场中买到,大多是12#条,其长度规格较多,但要买到刚好合适的,也不是一件容易的事情。
我最后买的是12#条长度175mm,用2x编法正好合适20寸车圈。
在编辐条时,应注意以下几点:
a.因12#条较粗较硬,长度又短,对于36孔的车圈,内层的9根条与外层的9根条不必绞绕(26寸车内外层辐条一般都是有一次相互绞绕),各走各的层面,这样可以使辐条挺直不打弯。
b.由于辐条不绞绕,就比较容易编了。
首先,把内圈的9根辐条依次穿圈,上条帽,然后再依次穿外层的9根辐条,上条帽。
一侧的18根辐条编好后,再编另一侧的18根辐条,也是先内层的9根,再外层的9根。
其间没有多少技巧,很容易编成。
为什么要先编内层的辐条呢?
如果先编外层的辐条,等外层的辐条编好后,因内层的辐条活动空间不自由,经常会有别死的情况。
对于内层辐条与外层辐条要相互绞绕的情况,也就是普通车圈的编法,因我暂时还没编过,所以,也没有什么经验可谈了。
自行车圈的编法与调整
2013-08-0809:
08:
30| 分类:
自行车|举报|字号 订阅
一、轮圈的组装
1、基本工具与材料
(1)工具
l 辐条冒专用起子
l 辐条扳手
l 轮圈校正台
l 轮圈碟型对称规
l 辐条张力器
4、调整车圈工作原理
车手在踩踏时,不断地将压力施予轮组。
而定期的对轮组校正,可令轮框侧壁保持笔直运转。
转动“车辐条帽”,连接车辐条末端的一颗内牙螺母,可提高或降低车辐条张力。
虽然我们常说:
“拉紧车辐”,实际操作的却是车辐条帽,而非车辐。
转动辐条帽需要由辐条扳手。
调整轮组的偏摆,选择正确尺寸的辐条扳手尤为重要。
车辐条帽通常使用软质金属制成,例如铜和铝。
辐条帽通常是正方形,有着不同尺寸。
辐条扳手的尺寸即使是稍微过大,都不会轻易摧毁辐条帽,将四个角磨成圆边。
购买正确的扳手,尽量挑选套入辐条帽之后,间隙最小。
某些款式的车辐条有着特殊的造型或尺寸,需要从原厂获取。
如隐藏于轮框内部的辐条帽,有正方形或六角形。
观察轮框在旋转时的偏摆幅度,这时需要观察一支稳定的指示器作为参考点。
轮组校正台(平圈架)的触规犹如游标卡尺,使用更容易,是判断轮框摆幅的依据,能够提升调校轮框的工作效率。
若无平圈架,可以利用车架,以刹车皮作为参考点,进行轮框的调整,有四个基本面向:
侧向、径向、正心以及张力。
一个完善的调整轮组,必须四个面向都很平均的轮组,才能发挥最佳性能。
A、侧向偏摆的调整方法:
侧向(轴向)偏摆,也称轮圈偏摆,随着轮组的旋转,轮框会左右摇晃,是最常处理的轮组校正项目。
观察刹车皮与轮框的间隙,很容易判断轮框是否偏摆,拉紧或放松辐条,可以控制轮框区段的侧向摆幅。
一般来说,经验不足的技师在校正偏摆时,应该先紧辐条帽。
因为提升辐条张力,对控制轮框摆幅效果较为显著。
轮框侧壁的摆幅受质量因素的影响,不一定是完美笔直的保持零偏摆,一般常用的侧向摆幅在1mm以内,而且在用力踏蹬骑行时轮圈不会松散而摩擦车闸皮,即可属正常。
此类调整关乎刹车夹器的设定,严重的偏摆会磨到刹车皮,甚至外胎会磨到车架或前叉。
B、径向偏摆的调整方法:
即垂直误差,如果轮组的真圆度不够, 轮框旋转时,轮框与花鼓的距离从侧面观察,轮框会随着旋转而上下跳,骑行时轮组每转一圈跳动一下,高速度时震动的更加厉害,甚至无法扶住车把,严重地影响速度。
远离花鼓的轮框区域段称为“高点”,靠近花鼓的轮框区段称为“低点”。
拉紧来自花鼓耳两侧的辐条,能将高点的轮框区域段向花鼓拉近。
放松来自花鼓耳两侧的车辐条,能够让低点的轮框区段远离花鼓。
校正径向偏摆,高点与低点必须两者兼顾。
成对处理相邻的辐条,一支来自左耳花鼓耳,一支来自右花鼓耳,才能避免轮框的侧向精准度受影响。
然而,每次校正径向偏摆之后,都要重新检查侧向。
(1)将触规紧贴轮框外缘;
(2)缓慢旋转轮组,观察轮框外缘,寻找触规稍微磨檫之处。
此即花鼓与轮框的最长半径,即最高点;
(3)将轮框停在磨檫磨擦处,来回转动,寻找高点的中心,此区段的车辐条需要缩短。
(4)在高点的中心,成对旋紧车辐条,从1/2圈开始,等量旋紧来自左右花鼓耳的辐条;
(5)来回转动轮组,检查调校过的轮框区段。
若有需要,重复调校;
(6)收窄触规,旋转轮组,寻找下一个高点。
成对旋紧车辐条,以缩短轮框到花鼓的距离;
(7)径向校正三处之后,检查侧向偏摆,先排除侧向偏摆,再继续校正径向;
(8)高点调校后,可能只剩低点。
排除低点,要防松车辐条。
旋转轮组,移动触规,令轮框轻松地连续磨檫,未磨檫之处,即为低点,此区段的车辐条需要拉长。
找出最低点的中心;
(9)在低点的中心,成对防松车辐条。
车辐条必须相邻,一左一右来自不同侧的花鼓耳;
(10)旋转轮组,处理其它的低点,偶尔检查、校正侧向偏摆;
(11)检查真圆度的容许值。
收窄触规至几乎磨檫轮框。
缓慢旋转轮组,观察触规与轮框的最大间隙,此即径向的最大偏摆。
如果摆幅小于1mm,可谓之正常;
(12)再次检查与校正侧向偏摆;
若轮框在骑行或运输过程,因撞击而损毁或变形,可能无法调校的得非常精准。
如果轮框某个区域段朝向花鼓凹陷,而该区段的车辐条呈现松弛的状态,说明轮框已经变形,不能修复,建议更换轮框或轮组。
C、正心的调整方法:
轮框中心线是否在前叉或车架后三角的中央,才能使前后轮沿着同一条直线前行。
如果轮框偏向前叉或车架的左或右,会造成骑行操控困难与骑行费力等问题。
改变车辐条张力,可令轮框重叠车架中心缘。
调校正心的原则是:
来自花鼓左耳的车辐条张力,轮框会拉向左侧。
来自花鼓右耳的车辐条张力,轮框会拉向右侧。
平均提升花鼓左耳的车辐条张力,正心会偏左。
平均提升花鼓右耳的车辐条张力,正心会偏右。
反过来说,平均降低花鼓左耳的车辐条张力,正心会偏右。
平均降低花鼓右耳的车辐条张力,正心会偏左。
检查正心最准确的方式是用轮组中心定位量规,来测量轮框到花鼓的距离。
(1)任选一侧作为基准,如测量右侧;
(2)将滑轨向下伸,直到末端抵住花鼓右端的防松螺母侧面,不要抵住轴心末端,因为轮组夹在车架时,是防松螺母的侧面接触勾爪;
(3)翻转轮组,测量左侧,将量规的两端紧压住轮框,观察滑规与防松螺母侧面的间隙。
有三种可能性:
1)量规的两端压住轮框,滑规稍微接触花鼓左端的防松螺母侧面,或是间隙小于1mm。
代表轮组正心在标准范围内,无需校正。
(4)在轮框与量规两端有间隙的同侧花鼓耳,平均提升车辐条张力1/4圈;
(5)再次检查与校正侧向偏摆,因为使用量规对于轮框无法测量侧向偏摆;
(6)用量规再次检查轮组正心,从步骤a开始。
注意:
原先的测量值已经无参考性,轮组与防松螺母的相对位置已改变,视需求继续校正。
如果轮框与量规的间隙不足1mm,可谓正常。
(7)若无其它校正项目,用酒精或玻璃清洁剂擦拭轮框的刹车磨擦面;
(8)调整正心时,总体张力值会随着改变,提升单侧的车辐条张力,会导致两侧的张力都升高。
降低单侧的车辐条张力,会导致两侧的张力都下降。
D、张力的调整方法:
车辐张力,就是辐条产生的拉力松紧程度。
测量辐条张力的工具是辐条张力计,由校准过程的弹簧对辐条施压,将辐条的侧向弯曲值换算为力的单位。
有经验的技师凭经验握捏成对的同侧辐条,感受变形量,可以粗估张力。
调整辐条张力之前,先用稀薄的油品任何辐条的螺牙,以及辐条帽和轮框之间的缝隙,降低辐条转动时的摩擦力。
旋紧左花鼓耳上的辐条帽,提升辐条张力,轮框就会偏左。
旋紧右花鼓耳上的辐条帽,就会提升右侧辐条张力,轮框就会偏右。
左侧的辐条将轮框拉向左,右侧的辐条则控制住的左侧的张力,每根辐条的影响对轮框都有区域段的距离。
若旋松左侧辐条张力,因为受右侧辐条的牵引,轮框就会向右侧偏。
5、调整轮圈的过程步骤
(1)初步调整:
初步调整时,旋紧时必须保持相同的圈数。
例如:
第一次旋紧设定为两圈,每根辐条都要旋紧两圈。
作歪斜调整时若以四只辐条为单位调整1/2圈,则四根辐条都需要相同,随着调整幅度的缩小,旋紧的调整幅度逐渐减少。
若以一紧一松的方式同时调整两侧,则旋进旋出的圈数也要相同。
(2)初步检测:
把正心检测弓放在花鼓中心点,检查轮圈是否在中心;
(3)将轮子架在调整台上,调整触规,令末端稍微触及轮框侧壁,先任挑左侧或右侧完成;并将触规移向轮框。
根据正心检测弓工具的初步检测,做初步调整。
将轮组停在轮框摩擦触规,或是距离触规的最近处。
此区域的侧向摆幅最大,应先调整。
(8)初步调整后,持续校正侧向偏摆。
调整触规,令末端几乎摩擦轮框侧壁。
由此点开始,缓慢旋转轮组,观察触规与轮框的最大间隙,此即侧向的最大摆幅。
(9)若左右偏摆1mm左右时,需要作左右辐条一松一紧的调整。
旋紧辐条帽1/4到1/2圈,1/4圈是90度,1/2圈是180度。
再次旋转轮组,检查偏摆。
通常一个偏摆区域需要微调多次。
辐条帽的单次调整幅度不要超过1/2圈。
分次微调,每次调整之后都要旋转轮组,检查摆幅。
调整1/2或1/4圈旋松,相对另一侧旋紧。
(11)观察圆度的差距,进行两只以上辐条为单位的调整。
如果跳动小于1mm甚至校正更精准。
(12)完成圆度的调整后,用检测弓再次车圈的中心检测,若有偏离中心,还必须再次做调整。
轮框制造商已制定了不同的建议张力值,低至60kgf,高至100kgf.200kgf是常见的建议张力,张力的极限值由轮框决定,而非车辐条种类或粗细。
越重的轮框越强壮,也越能承受高张力值。
轻量的轮框大约是280g到350g,重的轮框大约是450g或更高。
此外,轮框的眼孔协助了负荷的传导。
无眼孔的轻量框不能承受高张力。
张力的变化范围非常广,最好按照制造商建议值操作。